
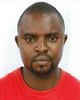
- Open Access
- Authors : Edeh . O. Edward , Job . O. Frederick , Anowai . I. Solomon , Shittu . N. Olawale
- Paper ID : IJERTV10IS080158
- Volume & Issue : Volume 10, Issue 08 (August 2021)
- Published (First Online): 30-08-2021
- ISSN (Online) : 2278-0181
- Publisher Name : IJERT
- License:
This work is licensed under a Creative Commons Attribution 4.0 International License
Effect of Nano Iron Oxide (Fe2O3) on Concrete Subjected to Physical Sulphate Attack (PSA)
Edeh.O. Edward1, Job. O. Fredrick2, 3 Shittu .N. Olawale, Anowai. I. Solomon
Department of Building,
1,2,3,4 Department of Building, University of Jos Nigeria
Abstract:- The use of nano iron oxide ( Fe2O3 ) powder as an admixture in concrete has a lot of benefits in reducing the amount of waste requiring disposal and also provides construction materials with significant savings over new materials. Field experience have shown that concrete exposed to sulphate usually suffer from sulphate scaling above the ground level which was caused by physical sulphate attack. This physical sulphate attack over time have been confused and ignore as chemical attack. The research work presents the results of laboratory evaluation on the effect of iron powder (Fe2O3) as an additives, water to binder ratio (w/b) ratio along with various curing conditions on the performance of concrete exposed physical sulphate attack and also the performance of concrete prone environment exposed to physical sulphate attack was evaluated on the compressive strength, tensile strength, workability, and porosity of the binary blended concrete and the physical properties (visual appearance and mass loss) were experimentally investigated. The blended nano iron oxide waste were exposed to sulphate solution and the cement properties were examined. Prepared mortar specimens were cured under water for 28 days and then they were exposed to sodium sulphate solution for this purpose, Portland cement was partially replaced by 0%, 2%, 3%, and 5% by weighing of iron powder. The amount of water-binder-ratio was considered constant. The workability of the fresh composite concrete was determined using mechanical properties were determined included compressive and tensile strengths at 7, 14, and 28 days and durability evaluated by water absorption and permeable porosity. It was observed that the compressive and tensile strengths change with the replacement of iron powder by up to 5%. However, the maximum improvement was gained at 3wt% for compressive strength and 5 wt% for tensile strength. The workability of the fresh mixtures decreased when iron powder amount increased. Moreover, this present study shows the importance and benefits to improve concrete properties by using micro-particles materials.
Keyword: Nano iron oxide, workability, Compressive Strength, Split Tensile Strength, Flexural Strength Test, the Porosity of Concrete and visual appearance and mass loss.
1.0 INTRODUCTION
The new order experienced in the field of Nano iron oxide has opened the eyes of researchers to explore other means in which Nano sized acted as a filler, admixtures which can improve the microstructure of Cementous composite and reduced its total porosity, then it increase the density of the composite. This improvement is attributed to the unique properties of nanomaterials, such as their high strength, high Youngs modulus, high surface area, electrical conductivity and certain chemical activity. The industrial production and incorporation of nanomaterials into concrete is undoubtedly the future of modern concrete technology. Nano materials are not only environmentally friendly, they can also help to create novel, sustainable and advanced concrete structures, resulting in lowering the use of cement and decreasing project costs.
In the recent pasted, the deterioration of stone in historical monuments was as a result of salt crystallization which have been a subject of investigation (Goudie and Viles, 1997). A lot of studies have been carried out as related to deterioration mechanisms and how such a problem can be mitigated, since it is considered as a major threat to historical monuments and building stones. Whereas, concrete deterioration due to salt crystallization, or the so called physical sulphate attack on concrete, has been ignored and confused in some occasions with chemical sulphate attack (Haynes et al., 1996; Haynes et al., 2008; Mehta, 2000). According to Scherer (2004), concrete can be vulnerable to damage when salt crystals grow from a supersaturated solution in its pores. This process was described as physical attack on concrete since, unlike chemical sulphate attack, it does not involve any chemical interaction between the sulphate ions and the concrete hydration products (Haynes et al., 1996).
However, the consequences of physical sulphate attack are different from those of chemical sulphate attack since it leads to surface degradation similar to that caused by cycles of freezing and thawing, while chemical sulphate attack results in expansion and cracks due to the formation of ettringite (Ca6Al2(SO4)3(OH)12·26H2O) and gypsum (CaSO4·2H2O) (Mehta, 2000). Using the sulphate attack terminology in-situ to describe concrete deterioration due to sulphates may lead to confusion between physical and chemical attack (Haynes et al., 1996).
Field experience regarding concrete exposed to sulphates has shown that concrete often suffers from surface scaling caused by physical sulphate attack, which is limited to the above-ground portion, while the portion embedded in sulphate rich soil (exposed to chemical sulphate attack) has mostly been found in intact condition (Yoshida et al., 2010; Stark, 1989; Irassar et al., 1995). The damaging process involves capillary rise and evaporation of ground water containing sulphates at the above ground concrete surface, resulting in crystal growth in concrete pores and damage (Irassar et al., 1995; Haynes et al., 1996).
In any case, the recent standards that evaluate the performance of concrete under sulphate attack, such as ASTM C1012 (Standard Test Method for Length Change of Hydraulic-Cement Mortars Exposed to a Sulphate Solution), only cover the chemical aspects of sulphate attack and ignore physical attack, since it evaluates the concrete performance when it is fully immersed in a sulphate
solution (Aye and Oguchi, 2011; Santhanam et al., 2001). This may serve to more confusion in assessing the deterioration of concrete due to sulphates under field exposure.
2.0 LITERATURE REVIEW
The previous studies showed that external sulfate attack due to interactions with calcium, sodium, and magnesium sulfate resulted in chemical alterations of the hydrated cement paste, for instance leading to the formation of gypsum or ettringite or to the decalcification of C-S-H. However, damage activated by external sulfates may also be physical in nature, without any such chemical alterations. A common form of physical salt attack in concrete occurs when sodium sulfate penetrates into concrete and phase changes occur between anhydrous sodium sulfate (thenardite) and decahydrate sodium sulfate (mirabilite). These phase changes, typically triggered by changes in temperature, lead to significant crystallization pressures that can impart stresses and cracking in concrete. Neville (2004) reported that this transformation of thenardite to mirabilite can result in tensile hoop stresses stressing the range of 1450-2900 psi (10-20 MPa). This stress is quite high and could easily damage concrete (Neville 2004).
-
MATERIALS AND METHODS
-
Nano Iron Oxide
The Nano Fe3O4 used in this study was sourced locally and sieved with 75m sieve in building department Laboratory of the University of Jos .The cement used for this study was manufactured from the Okpella factory of Bua Cement whose properties conform to the requirements of BS EN 197-1:2000 (which replaces BS 12 (1991)) for Ordinary Portland Cement. Cement has important property that when mixed with water, a chemica reaction (hydration) take place, which with time produces a very hard and strong binding medium for aggregate particles (Neville, 1981).
-
Sulphate Concentration, Exposure, and Testing
The specimen was cured for 28 days, the specimen were divided into two groups, the first group of specimens was continuously cured under water while the second group was placed in the second tank with the sulphate concentration 300 g NaSO4, the exposure condition represent very severe sulphate exposure conditions according to ACI 318-11 [21]. Solutions were renewed in periods of 14 days and mass changes were determined at the same periods. Second group specimens were left for 28 days of the sodium sulphate exposure at the end of the 27 days of water curing before the determination of mass change, the length change, and the compressive and flexural strengths tests. The effect of sulphate concentration on the performance of plain and blended cements was evaluated by visual examination and measuring the reduction in compressive strength. Mass changes were calculated as the difference between the mass of saturated-surface dry specimen at any time and just before the sulphate exposure.
-
LABORATORY PROCEDURES
The following OPC: Nano iron oxide proportions (%) were used for the study and investigation. See Table 1.
Table 1: the OPC: Nano iron oxide proportion composition of mix concrete
S/NO
OPC: Nano iron oxide (%)
1
98:2
2 97:3
3 95:5
-
MIXING PROCESSES AND PRODUCTION OF TEST CUBES
The mixing and batching adopted in research are manual mixing method was adopted in preparing the concrete for placement. First the sand was measured, followed by the measurement OPC and Nano iron oxide which were thoroughly mixed until uniform colour was obtained. It was followed with the measurement of crushed granite until its mixes are uniform, water was next measured, in order to achieve the required W/C ratio and the ratio used 0.55. The process is in accordance with B.S 1881: Part 125: (1986). Plate in appendix.
3.4.1 Batching Calculation
Absolute volume method was adopted for measurements of the volume of materials used in mixing the concrete. This method has the assumption that the volume of compacted concrete is equal to the sum of absolute volumes of all the ingredients (Neville and Brooks, 2002).
i.e Absolute Volume= Weight of Materials
Material Specific Gravity The batching result is shown in Table 2
Table 2: Val |
ues used for Absolute Volume Method |
Bulk Density of Materials |
|
Cement |
1440kg/m3 (obtained from literature) |
Fine Aggregate (sand) |
1454.3kg/m3 |
Coarse Aggregate (gravel) Nano iron oxide (N.F) |
1488.6kg/m3 1320kg/m3 |
Specific Gravity of Materials |
|
Cement |
3.15 (obtained from literature) |
Fine Aggregate (sand) |
2.58 |
Coarse Aggregate (gravel) Nano iron oxide (N.F) |
2.92 4.52 |
Batching Calculation |
|
Cement |
0.46m3 |
Fine Aggregate (sand) |
1.06m3 |
Coarse Aggregate (gravel) |
2.30m3 |
Water |
0.94 m |
Total Absolute Volume |
4.76m3 |
Quantities of Materials per cubic meter of concrete |
|
Cement |
376.96kg |
Fine Aggregate (sand) |
790.05kg |
Coarse Aggregate (gravel) |
1515.18kg |
Water |
188.48kg |
Table 3: Quantities of Materials Used for all Batches-Total Absolute Volume of 0.066m3
Materials |
Quantity |
|
Cement |
25kg |
|
Fine Aggregate (sand) |
52kg |
|
Coarse Aggregate (gravel) |
100kg |
|
Water |
12.4kg |
|
Quantities of Cement required for 0.066m3 Batch |
||
Control |
No replacement |
25kg |
20% (VA) |
5kg |
20kg |
-
RESULT AND DISCUSSION
This research present, the experimental results of nano iron oxide mixes on workability, visual appearance and mass loss, Mechanical Properties, Compressive Strength, Tensile Strength, the Porosity of Concrete are discussed. The workability tests performed in this research were ordinary slump,
The result of the workability test carried out in the laboratory 2%, 3% and 5% of nano iron oxide was replaced with cement. See below.
Table 4 : Workability Test Result
Batch No
Partial Replacement ( %)
Cement (kg)
(Fe2O3) (Kg)
Water Required (Kg)
Slump
Compacting
1
2
26.2
0.3
14.41
10
0.75
2
3
25.7
0.76
14.14
10.5
0.78
3
5
25.1
1.3
13.8
17
0.85
-
COMPRESSIVE STRENGTH
The result of the compressive strength test carried out on the 0% and concrete cubes incorporated with Nano iron oxide at various range of 2%, 3% and 5% respectively control is as presented in Table 5 revealing average compressive strength values
. this table shows the compressive strength of cubes with and without nano iron oxide.
Table 5: Average Com
pressive strength of
Cubes.
S/N
Mix Id ( % )
Compressive strength (N/mm2)
3 Days
Compressive strength (N/mm2)
7 Days
Compressive strength (N/mm2)
14 Days
Compressive strength (N/mm2)
28 Days
1
CC
19.5
26.8
26.3
28.8
2
2% Nf
19.0
21.8
26.0
28.0
3
3% Nf
16.5
23.0
26.0
28.8
4
5% Nf
18.5
25.0
19.0
27.0
35
30
25
20 19.5 19 18.5
16.5
15
26.8
25
21.8 23
26.3 26 26
19
28.8 28 28.8 27
10
5
0
3 Days 7 Days 14 days 28 Days
Curing Age (Days)
CC % 2% Nf 3 % Nf 5 % Nf
Figure 1. Chart of Compressive Strength/ Curing Age of Sample
-
Split Tensile Strength Test.
The Split tensile strength of concrete cylinders were found for the control concrete and concretes incorporated with Nano iron oxide at various range of 2%, 3% and 5% accordingly. (See Table 6)
Table 6: Average Split tensile strength test of concrete cylinders in 28 days curing.
S/N
Mix Id (%)
Split tensile strength (N/mm2)
1
CC
4.08
2
2%
4.08
3
3%
3.97
4
5%
4.93
-
Flexural Strength Test
The flexural strength of concrete beams were found for the control concrete and concrete beams incorporated with Nano iron oxide at different doses of 2%, 3% and 5% accordingly . Table 7 shows the flexural strength of concrete beams with and without nano iron oxide.
Table 7: Average Flexural strength test of concrete beams in 28 days curing.
S/N
Mix Id (%)
Flexural strength (N/mm2)
1
CC
6.00
2
2%
4.10
3
3%
6.25
4
5%
5.25
-
Visual Inspection
Figure 1 shows salt crystals on concrete surface. During the first week, salt precipitation (efflorescence) appeared above the solution level (30% of sodium sulphate) on the drying surface of the concrete cylinders when exposed to a temperature of 20°C [68°F] and RH of 82%. According to previous studies (Thaulow and Sahu, 2004; Haynes et al. 2008), this exposure condition can lead to mirabilite formation. In the second week, the exposure was altered to a temperature = 40°C [104°F] and RH = 31%, a condition conducive to thenardite formation. It was observed that the volume of the precipitated salt on the concrete surface decreased compared to that in the first exposure. This is due to the conversion of mirabilite to thenardite, which results in a volume reduction of about 314% according to Tsui et al. (2003).
Inspect|ion and mass loss Specimens partially immersed in sodium solution were monitored for over 10 cycles (approximately 1 month) of exposure. Excessive efflorescence of salts was progressively deposited on the evaporation surfaces of the specimen especially during the hot/dry period of the exposure cycles displaying the efflorescence on the surface of specimens at the end of the hot/dry ambient period, shows that the efflorescence accumulated to cover the whole specimen at the end of the period between readings and efflorescence removal solution evaporation was observed even with tight lids that act as vapor barrier. This was observed through the rapid reduction of the solution level in the containers periods between specimens inspection and solution typical examples of the surface damage occurred tested specimens at different exposure of exposure indicated remarkable visual deterioration on the surface of the specimen above the solution level.mid-third of the specimens send of exposure, some signs of immersed portions of the specimens. In specimens with severe damage, transverse or slightly inclined surface cracks could be noticed at the end of the exposure. However, these cracks did not seem to continue through the whole cross section as the specimens remained sound and rigid. The most severe scaling was observed in specimens from mixture A-0 from Group A and all of Group B specimen. The mass of each specimen was then measured to the nearest 0.01g and the specimens were visually inspected and photographed as shown in figure 1.
Table 8: Visual |
rating of Da |
mage at differen |
t ages of expo |
sure |
||||
Mixture Id |
0 Days |
10 Days |
20 Days |
30 Days |
40 Days |
50 Days |
60 Days |
|
0% |
0 |
1 |
2 |
3 |
4 |
5 |
5 |
|
2% |
0 |
0 |
1 |
2 |
4 |
5 |
5 |
|
4% |
0 |
0 |
1 |
2 |
3 |
4 |
5 |
|
6% |
0 |
0 |
1 |
1 |
2 |
4 |
5 |
4.4.1 Mass Loss
The average mass loss recorded over the PSA exposure was determined at different curing ages of exposure. for specimens from Groups 0%, 2%, 3% and 5% are shown in table 4 respectively, The table indicate faster rate of mass loss in some mixtures (especially for Group 2% specimens) during the first 20 cycles, followed by lower rates after that. For instance, specimens 2% experienced considerable mass loss during the first few cycles of exposure which may be attributed to the insufficient degree of hydration of the matrix at the beginning of exposure (28 days after mixing). . It can be noted that the specimens without Nf had higher surface scaling compared to those specimens incorporated with Nf Addition. At 60 days exposure, specimens containing 5% NS had better resistance to PSA (mass loss of 10%), relative to specimens from the control mixture (mass loss of 25.3%). All the specimens comprising Nf had comparable mass loss (average of 15%) after 60 days. However, the highest percentage of mass loss (22.3%) was recorded for specimens with 2% Nf dosage.
Generally, the mass loss values complied with the visual inspection the surface damage as the highest mass loss. For specimens, table 4 indicates notable reduction in mass loss associated with increasing the dosage of nano iron oxide from 0 to 5%. On the other hand, 2% mixtures (Table 9), the effect of nano iron oxide addition was less significant in terms of mass loss reduction as the variation in mass loss values between the three mixtures was considerably low.
Table 9: % Mass Loss of Specimens at different ages of PSA exposure
Mixture Id |
Percentage Mass Loss (%) |
||||||
1 Day |
10 Days |
20 Days |
30 Days |
40 Days |
50 Days |
60 Days |
|
0% |
0 |
2.6 |
3.5 |
6.6 |
13.7 |
20.4 |
25.3 |
2% |
0 |
2.1 |
2.9 |
5.1 |
10.5 |
16.3 |
22.3 |
3% |
0 |
1.9 |
2.6 |
4.3 |
8.9 |
10.7 |
13.3 |
5% |
0 |
1.7 |
2.5 |
3.8 |
6.6 |
8.4 |
10.3 |
-
CONCLUSION AND RECOMMENDATIONS
From the summary of findings, the study reviewed that the concrete mixtures incorporating nano iron oxide with different range of nano iron oxide exposed to PSA and the durability of concrete exposed to an environment prone to physical sulphate attack and the partial replacement of the cement by iron powder improved significantly the compressive strength in comparison of the concrete without iron powder (Fe2O3) particles. It was found that it is advantageous if cement is replaced by iron powder up to a maximum limit of 3% with predominant particles of 75 nm. The Split tensile strength was improved especially for concrete mixtures containing 5% nano iron oxide (i.e. 4.93N/mm2).The flexural strength was also improved particularly for the concrete mixtures containing 3% nano iron oxide (6.25 N/mm2) and also The slump of the fresh concrete decreased with the increase of the amount of the iron powder particles.Damage caused by crystallization of salt in concrete pores should be considered as an important cause f damage in areas with salt-rich soils. This type of environmental attack should be taken into account during the concrete mixture design especially in regions with hot and dry seasons.The rate of PSA deterioration depends on the pore microstructure and transport properties of cementitious materials. Thus, the transport of sulfates is the primary mechanism controlling the rate of PSA damage. From microscopic analysis, it can be concluded that there is an optimal amount of the nanomaterials which can be successfully applied in a cementitious composite to improve its final properties. PSA on concrete is linked to the crystallization of salts in pores near the drying surfaces, which leads to progressive surface scaling and flaking of concrete.
Surface scaling frequently occurs when the evaporation rate from the exposed surface of concrete is higher than the rate of solution uptake through capillarity, resulting in efflorescence (not harmful) on the surface, and subflorescence underneath the surface which is the main cause for scaling. Growth of salt crystals in the confined pore space is accompanied by crystallization pressure.
This can be concluded that the partial replacement of the cement by iron powder improved significantly the concrete with nano iron powder (Fe2O3) particles incorporated into various range of concrete mixtures which have better resistance in PSA exposure than ordinary Portland cement concrete.
-
RECOMMENDATIONS FOR FURTHER STUDIES
The results and discussion presented in this study provide many useful insights for the extension of this research work.
The following are recommendations for further investigations:
-
Ingress of chloride ions in conjunction with sulfate ions from de-icing salts, groundwater and seawater is a natural phenomenon, which may lead to combined chloride-sulfate attack. Hence, future research on nano-modified iron oxide concrete might include this aspect.
-
Verifying the effect of nano iron oxide at different dosages with PSA on the resistance to external sulfate attack.
-
To Investigate the effect of silica fume, slag and natural pozzolans alone or their combine effect with nano iron oxide on the resistance of concrete to PSA, conventional sulfate attack and TSA.
REFERENCES
-
Goudie, A., and Viles, H., (1997), Salt Weathering Hazards, John Wiley & Sons, England, 241 p.
-
Haynes, H., ONeill, R., and Mehta, P. K. (1996), Concrete deterioration from physical attack by salts, Concrete International, Vol. 18, No. 1, pp. 63- 68.
-
Haynes, H., ONeill, R., Neff, M. and Mehta, P. K. (2008), Salt weathering distress on concrete exposed to sodium sulfate environment, ACI Materials Journal, Vol. 105, No. 1, pp. 35-43.
-
Haynes, H., and Bassuoni, M. T., (2011), Physical salt attack on concrete, Concrete International, Vol. 33, No. 11, pp. 38 42.
-
Mehta, P. K., (2000), Sulfate attack on concrete: Separating myths from reality, Concrete International, Vol. 22, No. 8, pp. 57-61.
-
Mehta, P. K., and Monteiro, P. J. M., (2006), Concrete microstructure, properties, and materials, The McGraw-Hill, Third edition, 659 p.
-
Scherer, G. W., (2004), Stress from crystallization of salt, Cement and Concrete Research, Vol. 34, No. 9, pp.1613 1624.
-
Yoshida, N., Matsunami, Y., Nagayama, M., and Sakai, E., (2010), Salt weathering in residential concrete foundation exposed to sulfate-bearing ground, Journal of Advanced Concrete Technology, Vol. 8, No. 2, pp. 121-134.
-
Stark, D., (1989), Durability of concrete in sulfate-rich soils, Research and Development Bulletin, Portland Cement Association, Vol. RD097.
-
Irassar, E. F., Di Maio, A., and Batic, O. R., (1995), Sulfate attack on concrete with mineral admixtures, Cement and Concrete Research, Vol. 26, No. 1, pp. 113123.
-
Neville, A. M. & Brooks J. J. (2002), Concrete Technology, (2nd Edition). London, Longman Publishers.
-
Neville, A. (2004). The confused world of sulfate attack on concrete. Cement and Concrete Research, 34(8), 1275-1296.
-
Niville, A.M. (1981). Properties of Concrete, 3rd Edition. London, Pitman Publishing Limited :779
-
Aye, T., Oguchi, C. T., (2011), Resistance of plain and blended cement mortars exposed to severe sulfate attacks, Construction and Building Materials, Vol. 25, No. 6, pp. 2988-2996.
-
Santhanam, M., Cohen, MD., Olek, J., (2001), Sulfate attack research whither now? Cement and Concrete Research, Vol. 31, No. 6, pp. 845-51.
-
Thaulow, N., Sahu, S., (2004), Mechanism of concrete deterioration due to salt crystallization, Materials Characterization, Vol. 53, No. 2-4, pp. 123- 127.
-
ACI 318 (2008). Building Code Requirements for Structural Concrete and Commentary. Reported by ACI Committee 318, Farmington Hills, MI: American Concrete Institute.
-
Tsui, N., Flatt, R. J., and Scherer, G. W., (2003), Crystallization damage by sodium sulfate, Journal of Cultural Heritage, Vol. 4, No. 2, pp. 109-115.
-
British Standards Institute. (1986). B.S 1881: Part 125: (1986). Testing concrete. Methods for mixing and sampling fresh concrete in the laboratory
-
BS EN 197-1 (2000). Cement Composition, specifications and conformity criteria for common cements.
-