
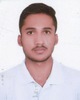
- Open Access
- [post-views]
- Authors : Vivek Kumar , Vinamra Purwar , Yajurved Gupta , Dr. Suvandan Saraswat
- Paper ID : IJERTV10IS080211
- Volume & Issue : Volume 10, Issue 08 (August 2021)
- Published (First Online): 04-09-2021
- ISSN (Online) : 2278-0181
- Publisher Name : IJERT
- License:
This work is licensed under a Creative Commons Attribution 4.0 International License
Reliability, Availability, Maintainability & Supportability Analysis of a Boiler
Vivek Kumar (Student)
Mechanical Engineering
JSS Academy of Technical Education Noida, India
Vinamra Purwar (Student) Mechanical Engineering
JSS Academy of Technical Education Noida, India
Yajurved Gupta (Student) Mechanical Engineering
JSS Academy of Technical Education Noida, India
Dr. Suvandan Saraswat (Associate Professor) Mechanical Engineering
JSS Academy of Technical Education Noida, India
Abstract – Sudden failures of any power plant boiler component lead to, loss of production and high maintenance cost due to unplanned and irregular maintenance. This unnecessarily increases the production cost of electricity. This study is focused at examining & analysing the failure times of boiler at thermal power plant identify its critical failure expectancy & system reliability. Method to choose best analysis mode has been discussed here. Reliability and maintainability analysis was carried out using Weibull probability plot & statistical analysis and the results being presented in charts. Achieved results & conclusions drawn shows the need & way to improvement.
Keywords :- Reliability, Maintainability, Availability, Hazard plot, Probability Distribution Function, Industrial processes, Production instability, industrial organization, defect, failure, maintenance costs, Weibull Distribution, failure data sorting.
-
INTRODUCTION
India as one of the largest electricity consumption country produces 65% of its power from thermal power plant with 85% being coal based. The boiler used in power plant extracts energy from fuel (such as coal etc.) to produce highly pressurized steam. This highly pressurized steam produced every hour is used to generate power with turbine, compressor and other mechanical devices.
The constant working of boiler for long hours can cause failure in the boiler unit like super-heater tube leakage, economizer tube leakage, water wall tube leakage etc. The main/sub-reason of these failures are thermal fatigue, creep, thermal stress, corrosion, cavitation, over-heating, high pressure, low pressure etc. That's why periodically maintenance of boiler is necessary as it may result in loss of hundreds of megawatt and also decline its revenue. Sometimes it may cause big explosion or disaster which can cost many lives.
The RAM analysis helps in analysing the reliability (which tells about the probability of working efficiently under stated condition), availability (which gives a measure of boiler to be available at any given time to work in the stated condition) and maintainability (which tells about the
probability of maintenance time of a boiler to work again in its stated condition). This analysis helps in deeply analysing how much work should be taken or can take from the boiler before shutting down for maintenance. This helps in reducing the number of failures and hence estimating the maintenance time / outage time required for the unit.
The RAM analysis can be done with different methods and different probability distribution but the most used and accurate method is 3-parameter Weibull distribution. The curves helps in understanding the nature of reliability and maintainability and find its value at any given time t in period T. The 3-parameter in Weibull distribution indicates scale parameter, shape meter and location parameter of the given failure data.
-
LITERATURE REVIEW :
There are various method to analyze the performance of system using RAMS.
RAMS is a logistic tool that estimate the performance of equipment at different levels. It directs safety and operation problems and find the area in the system where refinement work should be done. Certain key performance parameters such as Mean Time To Failure (MTTF), Mean Time Between Failure (MTBF), Mean Down Time (MDT), Mean Time To Repair (MTTR) and Availability (A) values can be determined to perform the analysis. The result gained from the statistics analysis of these values help in the assessment of the RAMS need of systems.
-
Discrete Analysis
MTBF = Total System Operating Hours / Number of Failures
MTTR = Forced outage hour / Total number of failure Availability = System Uptime / System Uptime +
System Downtime
-
Continuous Analysis
-
Goodness of fit
An applied mathematics model's goodness of work (GOF) refers to how well it fits a group of information. The distinction between actual values and foretold values beneath applied mathematics model is summarized by the
GOF indices. GOF statistics or GOF indices with better- known sample distributions that are utilized in applied mathematics hypothesis testing. Theyre typically made mistreatment straight line techniques.
-
Anderson Darling test
-
Correlation coefficient test Anderson Darling test:-
Anderson Darling test is a hypothesis test which is based on limited data. It is a statistical determination of data which helps in selecting the particular distribution. It tells how effectively data can be fitted on the particular curve from the previous studies it has been known that the lower the AD value better is the curve fitting.
The statistical output of Anderson Darling includes a p- value which allows whether to reject or approve the distribution. It is computed by statistical software.
Correlation Coefficient test:-
Correlation coefficient is the specific statistical measure to determine the strength of the relationship between the movements of two variables on the graph. It ranges from – 1.0 to 1.0.
Values other than this range means there is an error in correlation. A correlation coefficient closer than 0 consider as weak and greater than 0.9 shows the strong relationship between the two variables.
-
-
Common Life Distribution
The reliability of repairable equipment may be increased or decreased after repair, thus analysis of equipment reliability is required for maintenance management to meet maintenance needs.
These distributions include:
-
Exponential distribution
-
Log-normal distribution
-
Gamma distribution
-
Normal distribution
-
Weibull distribution
-
-
Weibull Distribution
One of the most used common life distribution in reliability analysis is Weibull distribution. The 2-parameter Weibull and 3-parameter Weibull differ only by location parameter which has just the significance of shifting of origin. Weibull can be easily applied to large number of situations and small data sets. It can also be used to model both increasing and decreasing failure rates. The main advantage of it is its ability to handle small samples and flexibility to fit different failure modes.
The three-parameter Weibull probability density function (PDF) is expressed by:
Where:
: Location parameter : Shape parameter
: Scale parameter,
-
-
METHODOLOGY
-
Discrete analysis
For performing discrete analysis the failure data is studied on monthly basis and outage frequency, forced outage hour, service hour and period hour are calculated for each month. Further
MTBF, MTTR, repair rate, failure rate, reliability and availability are calculated and noted in different columns.
Reliability: The failure rate remain constant for each month thus reliability is calculated using exponential distribution.
The formula for reliability is given below: R(t=et
Where t = time taken for each month
Maintainability: For calculating the Maintainability the Mean time between failure (MTBF) and Mean time to repair (MTTR) is calculated for each month.
Availability: The availability is calculated using the uptime (service hour) and downtime (forced outage hour). It can also be calculated using MTBF and MTTR.
-
Continuous Analysis
Under this distribution analysis, we are analyzing system reliability. The system which is comprised of various components is considered to be dependent on each individual component as well various components taken together. Thus failure of any component is the failure of system itself. Thus Time to failure for each failure through cumulative approach with respect to 1 JAN is calculated.
Significance of sorting of data this way is that it will show us reliability & failure results when the system is assumed to be started working from 1 JAN to a time period t.
Sr. No.
Failure Data
Sr. No.
Failure data
Sr. No.
Failure Data
1
2227.83
15
2593.30
29
2755.90
2
2988.33
16
3516.41
30
3573.03
3
3584.36
17
4154.96
31
4307.83
4
4599.6
18
4651.0
32
4801.55
5
5030.00
19
5270.30
33
5341.08
6
5379.41
20
5399.16
34
5541.00
7
5498.73
21
5535.00
35
5684.75
8
5547.00
22
5613.52
36
5900.86
9
5688.00
23
5751.51
37
6811.00
10
6448.50
24
6804.95
38
7215.51
11
7051.45
25
7125.96
39
7468.00
12
7429.38
26
7462.00
40
8100.88
13
7810.95
27
8007.26
41
8437.83
14
8166.30
28
8341.26
The arbitrary data thus obtained was than arranged in ascending order of failures (as shown above).
Distribution
Anderson-Darling
(adj)
Correlation Coefficient
Weibull
0.679
0.990
Log normal
1.226
0.963
Exponential
18.890
*
Log-logistic
1.249
0.961
3-Parameter Weibull
0.680
0.990
3-Parameter Log-normal
0.720
0.986
2-Parameter Exponential
9.824
*
3-Parameter Log-logistic
0.833
0.980
Smallest Extreme Value
1.329
0.976
Normal
0.720
0.986
Logistic
0.832
0.980
For estimation we are using LSXY (least square method) which is used for small & moderate data. The following equations are used to determine the mean time to failure (MTTF) and reliability of two parameter Weibull distribution.
The mean time to failure (MTTF) is obtained using:
by:
The reliability function of the Weibull distribution is given
The CDF or unreliability function of the two-parameter
This is also called Expected time of Failure free operations or expected time to collapse of whole system.
The failure rate function (also known as the hazard rate)
is:
Weibull distribution is given by equation:
Where , , t > 0
Where (x) = Gamma Function
Shape parameter
Scale parameter
Correlation coefficient
Anderson darling
3.63014
6318.29
0.990
0.679
-
-
RESULT & DISCUSSION
In this approach, we sorted the sample random failure data of boiler into month-wise failures. Number of outages (failures), mean time between two successive failures, total time for which the system was down, total hours for which the system was actually working & total period hour of respective month were listed. Then MTTR (Maintainability), MTBF, Failure Rate Repair Rate, Reliability & Availability was calculated.
In this study, the two-parameter Weibull distribution using the Least square (LSXY) estimation method is used to analyse the failure times of boiler system used in power generation in coal based power plant
Probability Curve:
From the plot, it is obvious that the Weibull distribution function F (t) is a nearly linear function of t. This means that our data was adequately described by the two- parameter Weibull distribution.
Reliability Curve:
Reliability (%) V/S Time plot
In plot, the reliability plot of the two-parameter Weibull distribution is shown. From the plot, a gradual drop in reliability is observed as the time to failure increases. It is a fact that no matter how well a component or system is designed or manufactured; it will fail after a considerable time during its operating life. The drop in the reliability of the boiler system is therefore expected as they have been in operation for a long time and ageing is beginning to occur.
The estimates of the two-parameter Weibull distribution, namely the shape and scale parameter ( & ) and the correlation coefficient (), were determined using reliability software. The following results were obtained; = 3.63014, = 6318.29 and = 0.990. The value of correlation coefficient= 0.990, shows that there is a good linear fit for the Weibull distribution.
Unreliability Curve:
Unreliability V/S Time Curve
From Plot, cumulative failure plot, it is evident that the probability function increases steadily till it reaches 65% failures almost after which it increases with a decreasing rate.
Hazard Plot:
Failure Rate V/S Time
Hazard curve (failure rate v/s time) is also known as Bath tub curve due to its shape. Here it is evident that no major early wear were observed thus the curve starts with almost constant failure rate to increasing failure rates at a steadily increasing rate of slope. Such increase in failure rate is observed due to aging & corrosion etc.
Probability Distribution Function:
PDF V/S Time
PDF Plot is used to define the shape of failure distribution. The median value obtained from the Weibull function is used to draw reference line. This line divides the plot into two halves with 50% of the failures occurring before the median time to failure & 50% occurring after the median time. The PDF graph shows the curve fit of the data. It answers the question, "Based on the curve fit, what is the proability that failure will occur below or above a certain value?" The graph is a graphical representation of the data that displays the variance or spread of the data. The probability that the random variable x is in the range and
is one; i.e.
The area under the PDF curve is, therefore, always unity.
Discrete Analysis
In this approach, we sorted the sample random failure data of boiler into month-wise failures. Number of outages (failures), mean time between two successive failures, total time for which the system was down, total hours for which the system was actually working & total period hour of respective month were listed.
Reliability:
Reliability
1.5
1
0.5
0
In this plot, January shows an early (infant) failure. Such kind of failures may occur commonly due to manual errors or accidental errors. Lower rank components are the major cause of such failures. Then the graph shows 100% reliability for Feb & March which is because the system has been under reduced loads. Then coming to April & May, no. of failures as well as the load on system had steep increase & thus a high fall in reliability. Such type of changes are shown due to longer working of system without fail previously & thus no maintenance. So a number of parts start to fail one after another due to seasonal variation in electricity requirement. To avoid such failures, scheduled inspections (not more than 2 weeks to 500 hours) are necessary.
Availability
1.5
1
0.5
0
Availability
1.5
1
0.5
0
Availability:
As evident from plot, the system has been available for more than 70% of the time throughout. In the month of Feb & March, availability of system has increased from 92% in Jan to 100%, as the system had failed & repaired thus unavailable for some time in Jan. Then due to increased number of failures in April & May, availability again decreased & was further got high in June when scheduled maintenance was carried out. Thus making the system function smoothly. After showing sudden decrease in August & steep increase in October, availability of system started to decrease & got to the lowest of 68% in December.
Maintainability
MTTR
80
60
40
20
0
MTTR
80
60
40
20
0
Maintainability of a system is directly derived & interpreted from Mean time required for Repairs.
As evident from Fig, Maintainability of system in Feb & March is 0 as there were no significant failures & no scheduled maintenance was carried out. Highest maintenance period was observed in Jan & Dec, which shows that some not so rare & ordinary components were failed. Maintainability tells about which components should be kept in extra quantity to reduce the time required for searching & placing order of failed rare components.
Supportability:
Supportability is not a statistical or analytical measure. Instead its a theoretical study of the support system required to keep the system functioning. Supportability includes the skilled & unskilled labour required to maintain, repair, carryout daily processes & to assist timely functioning of the boiler system. Various type of workforce, skilled, semi- skilled, unskilled, different equipment, and continuous supply of raw material as well as repairable materials is required to keep a unit functioning. Raw material in this case is Coal & Water (for cooling purposes).
-
Conclusion
January
February March April May June July August
Septe October Novem
Decem
January
February March April May June July August
Septe October Novem
Decem
This research project was based on applying discrete & continuous (lifetime) analysis using Weibull function distribution. The study involves analysis of failure times of a boiler system of a power generation plant using the Least Square estimation method. The failure times were rank- ordered and estimates of the two-parameter Weibull distribution; shape and scale parameters were determined using software. This method of estimation was found to be very fast and more accurate than the manual approach. Using the sorted data, survival, CDF failure, PDF failure, hazard curve & Probability density function curve were obtained. These plots were used to derive key results & interpretation of the data plots. Thus making it possible to predict future tendency of failures.
Discrete analysis was carried out to find out month-wise effect of failures so that proper time bound plan can be formed & required actions can be taken to improve the reliability, availability & maintainability of the system.
Calculations using the values of shape & scale parameters were carried out & resulted in an overall failure rate of (t) = 0.000437 & overall reliability = 50.3% throughout. Our study concludes that an yearly maintenance as well as timely inspection (not more than 500 hours) of components & system required. Moreover a proper estimation of load supply is to be made for the period of July-September as most of the failures occurred in between these months.
-
REFERENCES
-
Baradady, J., Improvement of System Availability: Using Reliability and Maintainability Analysis, PhD thesis of Luleâ University of Technology, 2005.
-
Barringer, P., Introduction and Evaluation of Reliability, International Mechanical Engineering Conference, Kuwait, 2004.
-
Junrong Du, Evaluation of equipment reliability,availability and maintainability in an oil sands processing plant, Vancouver, 2008
-
Lewis, N., Reliability through the Ages, Society for Maintenance & Reliability Professionals, 2002.
-
C. Ebeling, An Introduction to Reliability and Maintainability Engineering, Boston: McGraw Hill publication, 1997.
-
Saraswat Suvandan, and G. S. Yadava. "An overview on reliability, availability, maintainability and supportability (RAMS) engineering." International Journal of Quality & Reliability Management (2008).
-
B.M. Alkali, T. Bedford, J. Quigley and J. Gaw, Failure and maintenance data extraction from power plant maintenance management databases, Journal of Statistical Planning and Inference, vol. 139, no. 5, pp. 1766-1776, May 2009
-
Tsarouhas, Panagiotis. "Reliability, Availability, and Maintainability (RAM) Study of an Ice Cream Industry." Applied Sciences 10, no. 12 (2020).
-
Malik, Anees, Abdelkader Meroufel, and Saleh Al-Fozan. "Boiler tubes failures: a compendium of case studies." Journal of Failure Analysis and Prevention 15, no. 2 (2015).
-
Adarsh kumar & Pawan kumar sapra, Boiler Tubes Failure: Causes and Remedies a Case Study of a Fertilizer Plant, International Journal on Emerging Technologies 4(2): 2013
-
J.B. Kitto "Developments in Pulverized Coal-Fired Boiler Technology" Babcock & Wilcox Alliance, Ohio, U.S.A.
-
National Capital PowerStation, Technical Diary.
-
Kolawole, Adekunle, Olayinka Oluwole Agboola, Peter Pelumi Ikubanni, Olakunle Ganiyu Raji, and Christian Okechukwu Osueke. "Reliability and power loss analysis: A case study of a power plant in Nigeria." Cogent Engineering 6, no. 1 (2019).
-
Idoniboyeobu, Dikio, and Joshua Ojeleye. "MAINTENANCE AND MANAGEMENT OF THERMAL POWER STATIONS."
-
Kalaba, Dragan V., Milan Lj orevi, and Sneana D. Kirin. "Determining the reliability function of the thermal power system in power plant" Nikola Tesla, Block B1"." Thermal Science 19, no. 3 (2015).
-
Adhikary, D. D., G. K. Bose, S. Mitra, and D. Bose. "Reliability, Maintainability & Availability analysis of a coal fired power plant in eastern region of India." In Proceedings of the 2nd International Conference on Production and Industrial Engineering (CPIE 2010), pp. 1505-1513. 2010.
-
Adoh, Justin O., Barinyima Nkoi, and Anthony K. Le-ol. "Cost Reduction in a Brewery Boiler Operation Using Reliability Centered Maintenance: A Case Study." Journal of Newviews in Engineering and Technology (JNET) 1, no. 1 (2019).
-
Dewangan, D. N., Manoj Kumar Jha, and Y. P. Banjare. "Reliability investigation of steam turbine used in thermal power plant." International Journal of Innovative Research in Science, Engineering and Technology 3, no. 7 (2014).
-
Reliability & Life Testing Handbook, Volume 1 Dimitri B. Kececioglu, Ph.D., P.E., Professor of Aerospace and Mechanical Engineering, The University of Arizona
-
Hafaifa, Ahmed, Kouzou Abdellah, Guemana Mouloud, and Nadji Hadroug. "Reliability analysis using Weibull distribution applied to a booster pump used in oil drilling installations." Journal of the Technical University Sofia, Branch Plovdiv, Bulgaria, Fundamental Sciences and Applications 22 (2016).
-
Rachid, Belhadef, Hafaifa Ahmed, and Kouzou Abdallah. "Reliability modelling based on Weibull distribution to improve the pump availability control parameters."
-
Kumar, A. Ramesh, and V. Krishnan. "A Study on System Reliability in Weibull Distribution." Methods 5, no. 3 (2017).
-
Adoh, Justin O., Barinyima Nkoi, and Anthony K. Le-ol. "Cost Reduction in a Brewery Boiler Operation Using Reliability Centered Maintenance: A Case Study." Journal of Newviews in Engineering and Technology (JNET) (2019).
-
Jagtap, Hanumant, Anand Bewoor, Ravinder Kumar, Mohammad Hossein Ahmadi, and Giulio Lorenzini. "Markov-based performance evaluation and availability optimization of the boiler furnace system in coal-fired thermal power plant using PSO." Energy Reports 6 (2020).
-
Eti, M. C., S. O. T. Ogaji, and S. D. Probert. "Integrating reliability, availability, maintainability and supportability with risk analysis for improved operation of the Afam thermal power- station." Applied Energy 84, no. 2 (2007).
-
Sharma, Kapil Dev, and Shobhit Srivastava. "Failure Mode and Effect Analysis (FMEA) for Enhancing Reliability of Water Tube Boiler in Thermal Power Plant." SAMRIDDHI: A Journal of Physical Sciences, Engineering and Technology 8, no. 02 (2016).
-
Alazemi, Ahmed S. Kh RQ, Mohammad Yeakub Ali, and Mohd Radzi Che Daud. "Preventive Maintenance of Boiler: A Case of Kuwait Industry." International Journal of Engineering Materials and Manufacture 4, no. 2 (2019).
-
Patil, Suyog Subhash, and Anand K. Bewoor. "Reliability analysis of a steam boiler system by expert judgment method and best-fit failure model method: a new approach." International Journal of Quality & Reliability Management (2020).
-
Purbolaksono, J., J. Ahmad, A. Khinani, A. A. Ali, and A. Z. Rashid. "Failure case studies of SA213-T22 steel tubes of boiler through computer simulations." Journal of Loss Prevention in the Process Industries 23, no. 1 (2010).
-
Chaudhuri, S., and Raghubir Singh. "High temperature boiler tube failures: case studies." (1997).
-
Chaudhuri, Satyabrata. "Some aspects of metallurgical assessment of boiler tubesBasic principles and case studies." Materials Science and Engineering: A 432, no. 1-2 (2006).
-
Stapelberg, Rudolph Frederick. Handbook of reliability, availability, maintainability and safety in engineering design. Springer Science & Business Media, 2009.
-
Tsarouhas, Panagiotis. "Reliability, availability and maintainability analysis in food production lines: a review." International Journal of Food Science & Technology 47, no. 11 (2012).
-
Tsarouhas, Panagiotis. "Reliability, availability and maintainability analysis of a bag production industry based on the six sigma DMAIC approach." International Journal of Lean Six Sigma (2020).
-
Hoque, Khaza Anuarul, Otmane Ait Mohamed, and Yvon Savaria. "Towards an accurate reliability, availability and maintainability analysis approach for satellite systems based on probabilistic model checking." In 2015 Design, Automation & Test in Europe Conference & Exhibition (DATE), pp. 1635-1640. IEEE, 2015.