
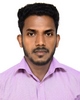
- Open Access
- Authors : Ramdas E R , Dileep Kumar K B
- Paper ID : IJERTV10IS090079
- Volume & Issue : Volume 10, Issue 09 (September 2021)
- Published (First Online): 18-09-2021
- ISSN (Online) : 2278-0181
- Publisher Name : IJERT
- License:
This work is licensed under a Creative Commons Attribution 4.0 International License
Surface Roughness Prediction for Cylindrical Grinding Process using Regression and Artificial Neural Model
Ramdas E R
Assistant Professor
Kelappaji College of Agricultural Engineering and Technology
Tavanur, Malappuram, India
Dileep Kumar K B Assistant Engineer Kerala Water Authority Wayanad, India
Abstract- Cylindrical grinding is one of the important metal cutting processes used extensively in the finishing operations. Surface finish is the important output responses in the production with respect to quantity and quality respectively. The purpose for this work is to develop mathematical model using regression and artificial neural network model for artificial intelligent method. Experiments have been conducted in MILANO RICEN RUM 1 cylindrical grinding machine based on Design of Experiment with input machining variables as work speed, feed rate and depth of cut. Surface roughness is measured using MITUTOYO Surf test SJ-400 surface roughness tester. The mathematical regression model has been developed using Minitab 16 software. The regression coefficient developed using Minitab 16 have been used for the development of mathematical model for surface roughness. The actual values are used to develop feed forward back propagation Artificial Neural Network (ANN) model using Matlab 7.1. The simulated user interface has been used to predict the surface roughness from ANN model. The error percentages in predicting surface roughness by two models have been determined. The average percentage of error is found to be 1.25 % in Ann model and 3.98 % in regression model. It is found that developed Neural Network model is more accurate, faster and effective in predicting surface roughness than regression model.
Keywords-Cylindrical grinding machine; surface roughness; regression; artificial neural network
-
INTRODUCTION
The challenge of modern machining industries is mainly focused on the achievement of high quality, in term of work piece dimensional accuracy, surface finish, high production rate, less wear on the cutting tools, economy of machining in terms of cost saving and increase of the performance of the product with reduced environmental impact. Cylindrical grinding is a very commonly used machining process in industry. The ability to control the process for better quality of the final product is paramount importance. The mechanism behind the formation of surfac roughness in cylindrical grinding process is very dynamic, complicated, and process dependent [7]. Several factors will influence the final surface roughness in cylindrical grinding operations such as speed, feed rate, depth of cut, material hardness, grain size and abrasive type. Some of the machine operator using trial and error method to set- up grinding machine conditions [1]. This method is not effective and efficient and the achievement of a desirable
value is a repetitive and empirical process that can be very time consuming.
Thus, a mathematical model using statistical method provides a better solution. Regression analysis is suitable to find the best combination of independent variables which is speed, feed rate, and the depth of cut in order to achieve desired surface roughness. Unfortunately, regression model is obtained from a statistical analysis which has to collect large sample of data. Realizing that matter, Artificial Neural Network (ANN) is state of the art artificial intelligent method that has possibility to enhance the prediction of surface roughness [5]. This paper will present the application of regression and ANN to predict surface roughness for cylindrical grinding process [2]. The accuracy of ANN to predict surface roughness will be compared with mathematical model that built using multiple regression analysis.
-
OBJECTIVES
To understand the cutting mechanisms involved in cylindrical grinding. To study the effect of cutting speed, feed rate& depth of cut on surface roughness with other parameters set constant. Using the cutting parameters speed, feed rate and depth of cut predict the surface roughness using regression mathematical tool and artificial neural network. To compare the obtained from regression and artificial neural model.
-
METHODOLOGY
-
Regression Analysis
After the surface roughness is obtained for all experiments, a table needs to be filled in order to obtain several values for the analysis. In order to obtain regression coefficient estimates0, 1, 2, and 3, it is necessary to solve the given simultaneous system of linear equations
-
Calculation of the coefficients of the regression model
This step deals with development of mathematical model. A mathematical model is the one which shows the relationship between the input and output variables. In the process model it relates the input process variables to the response variable of the process. Hence it is able to predict the response of the process for input variable considered.
In man problem there are two or more variables that are related and its important to model and explore this relationship. In general if there is a single dependent
variable or response Y which depends on K independent variables such as x1 x2..xk , the relationship between these variables are characterized by a mathematical model called regression equation. The regression model is obtained using a set of experimental data. In some instance the experimenter knows the exact form of true relationship between y and x1 x2..xk i.e. y
= f (x1 x2..xk) but in most cases the true functional relationships is unknown and the experimenter chooses an appropriate function.
The equation for Regression is Y = 0+ 1X1+ 2X2+ 3X3
Where, Y represents the response, X1, X2, X3 represents the coded values of process parameters and 0, 1, 2, 3 represents the regression coefficient to be determined.
In this work the input process variables are speed feed and depth of cut. The output response is surface roughness. Hence the relationship between these inputs and response variable are to be found out by developing a regression based mathematical model. Hence X1, X2 and X3 represents coded values of speed, feed and depth of cut respectively.Y1 surface roughness
The coefficient such as 0, 1, 2, and 3, have to be determined for the development of regression based mathematical model. Once the model is formed, the coded values of the actual process variables have to be substituted in the equation to get the predicted response of the process. In this work the values of regression coefficient are calculated using MINITAB 16 software statistical analysis software that can be used to create statistical mathematical model.
-
Artificial Neural Network (ANN)
Artificial Neural Network is an adaptable system that can learn relationships through repeated presentation of data and is capable of generalizing to new, previously unseen data. Some networks are supervised, in that a human determines what the network should learn from the data. For this study, the network is given a set of inputs and corresponding desired outputs, and the network tries to learn the input-output relationship by adapting its free parameters.
In back-propagation neural network, the learning algorithm has two phases. First, a training input pattern is presented to the network input layer. The network then propagates the input pattern from layer to layer until the output pattern is generated by the output layer. If this pattern is different from the desired output, an error is calculated and then propagated backwards through the netwrk from the output layer to the input layer. The weights are modified as the error is propagated. As with any other neural network, a back-propagation one is determined by the connections between the neuron (the networks architecture), the activation function used by the neurons, and the learning algorithm (or the learning law) that specifies the procedures for adjusting weights. Typically, a back-propagation network is multi layer network that has three or four layers. The layers are fully connected, that is, every neuron in each layer is connected to every other neuron in the adjacent forward layer. Figure
-
shows the neural network computational model. The neural network computational model coding is built using MATLAB software.
Fig.1. A simplified model of a neuron
-
-
ANN model development methodology
The following steps describe the methodology in developing the ANN model:
Step1. Create network and input values of hidden neurons and
desired output.
Step2. Initialize the weights and bias term Step3. Calculate net input to hidden layer units Step4. Calculate net input to each output unit
Step5. Calculate the output, error term and RMS value
Step6. If RMS value is not equal to desired value update the
weights between input and hidden layer and between
hidden and output layer.
Continue training until the desired accuracy is reached
-
-
EXPERIMENTAL DESIGN
Based on the literature survey it was observed that the process parameters have a significant effect on the surface roughness. Important process parameters are material hardness, speed, and feed, depth of cut, grain size and abrasive type. In present study, takes the following processes parameters selected are speed, feed rate and depth of cut. The other parameters are kept constant.
Upper and lower limits of the identified process parameters were fixed by conducting trial runs. This was carried out by varying one of the parameters while keeping the rest of them at constant values. The working range of each process parameter was decided upon by inspecting the bead for a smooth appearance without any visible defects
TABLE I. THE LEVELS OF EACH PARAMETER
Level
Low
Medium
High
Speed (rpm)
120
140
180
Feed rate (mm/sec)
2.5
3.5
5.5
Depth of cut (mm)
0.2
0.4
0.8
The present problem is a three factor three level problem. Full Factorial Experiment (FUFE) is applied. Full Factorial Experiment is the experiment where all the possible combinations levels of factors are realized. The design matrix chosen to conduct the experiment, which is suitable for a 3 factor 3 level problem. The parameters considered are Speed, Feed, and Depth of Cut. Thus, the numbers of experiment need to be executed are N = 3 = 33= 27 experiments. Thus 27 experiments have to be done to estimation of effects of the process parameters on the surface roughness.
The experiments were conducted according to the design matrix. As per the Design, 27 experiments is done
.EN8 is the grade of alloy steel used as work piece. EN8 is a very popular grade of through-hardening medium carbon steel, which is readily machinable in any condition. Work piece is 300 mm long and is diameter is 35 mm. Work piece are center drilled and turned in a universal lathe machine. After turning, work pieces are grinded in MILANO RICEN RUM 1 cylindrical grinding machine. A silicon carbide grinding wheel A60 L5 V10 and die coat is cutting fluid.
TABLE II. EN8 STEEL COMPOSITIONS
C
Si
Mn
S
P
0.40%
0.25%
0.80%
0.015%
0.015%
-
RESULTS & DISCUSSIONS
Surface roughness values are obtained from MITUTOYO Surftest SJ-400 surface roughness tester for each experiment. All the data taken from the experiment are shown in Table 3.
Job no
Speed in RPM
Feed rate in mm/sec
DOC in mm
Ra in
µm
1
120
2.5
0.2
0.47
2
120
2.5
0.4
0.40
3
120
2.5
0.8
0.34
4
120
3.5
0.2
0.49
5
120
3.5
0.4
0.41
6
120
3.5
0.8
0.35
7
120
5.5
0.2
0.48
8
120
5.5
0.4
0.42
9
120
5.5
0.8
0.35
10
140
2.5
0.2
0.55
11
140
2.5
0.4
0.49
12
140
2.5
0.8
0.41
13
140
3.5
0.2
0.59
14
140
3.5
0.4
0.52
15
140
3.5
0.8
0.46
16
140
5.5
0.2
0.61
17
140
5.5
0.4
0.57
18
140
5.5
0.8
0.49
19
180
2.5
0.2
0.65
20
180
2.5
0.4
0.59
Job No
Speed in RPM
Feed rate in mm/sec
DOC in mm
Ra in
µm
21
180
2.5
0.8
0.52
22
180
3.5
0.2
0.67
23
180
3.5
0.4
0.61
24
180
3.5
0.8
0.54
25
180
5.5
0.2
0.69
26
180
5.5
0.4
0.62
27
180
5.5
0.8
0.56
Job no
Speed in RPM
Feed rate in mm/sec
DOC in mm
Ra in
µm
1
120
2.5
0.2
0.47
2
120
2.5
0.4
0.40
3
120
2.5
0.8
0.34
4
120
3.5
0.2
0.49
5
120
3.5
0.4
0.41
/td>
6
120
3.5
0.8
0.35
7
120
5.5
0.2
0.48
8
120
5.5
0.4
0.42
9
120
5.5
0.8
0.35
10
140
2.5
0.2
0.55
11
140
2.5
0.4
0.49
12
140
2.5
0.8
0.41
13
140
3.5
0.2
0.59
14
140
3.5
0.4
0.52
15
140
3.5
0.8
0.46
16
140
5.5
0.2
0.61
17
140
5.5
0.4
0.57
18
140
5.5
0.8
0.49
19
180
2.5
0.2
0.65
20
180
2.5
0.4
0.59
Job No
Speed in RPM
Feed rate in mm/sec
DOC in mm
Ra in
µm
21
180
2.5
0.8
0.52
22
180
3.5
0.2
0.67
23
180
3.5
0.4
0.61
24
180
3.5
0.8
0.54
25
180
5.5
0.2
0.69
26
180
5.5
0.4
0.62
27
180
5.5
0.8
0.56
TABLE III. SURFACE ROUGHNESS OBTAINED FROM THE EXPERIMENTS
-
Regression Analysis Model
Since the surface roughness from the experiment has been established, the analysis for regression using Equation xx above is done to obtain regression coefficient 0, 1, 2, and 3.
-
Calculation of the coefficient of the regression model
In this work the values of regression coefficient are calculated using MINITAB 16 software statistical analysis software that can be used to create statistical mathematical model. The coefficient values for surface roughness from MINITAB 16 software are shown in Table 4.
TABLE IV. COEFFICIENT VALUES OF REGRESSION MODEL
Coefficients
Surface roughness model values
0
0.116
1
0.00307
2
0.0114
3
– 0.211
-
Predict the surface roughness using regression
-
Mathematical model for surface roughness:
The regression mathematical model for surface roughness by substituting the regression coefficients obtained from MINITAB 16 software is given as
Surface Roughness = 0.116 + 0.00307 X1 + 0.0114 X2 –
0.211 X3.
Where, X1 represents coded values of cutting speed in RPM, X2 represents coded values of feed in mm/sec, X3 represents coded values for depth of cut in mm. The predicted values of surface roughness using regression are shown in table 5.
TABLE V. PREDICTED SURFACE ROUGHNESS VALUES FOR REGRESSION
Job No
Speed in RPM
Feed rate in mm/sec
DOC in mm
Predicted Ra
1
120
2.5
0.2
0.4707
2
120
2.5
0.4
0.4285
3
120
2.5
0.8
0.3441
4
120
3.5
0.2
0.4821
5
120
3.5
0.4
0.4399
6
120
3.5
0.8
0.3555
7
120
5.5
0.2
0.5049
8
120
5.5
0.4
0.4627
9
120
5.5
0.8
0.3783
10
140
2.5
0.2
0.5321
11
140
2.5
0.4
0.4899
12
140
2.5
0.8
0.4055
13
140
3.5
0.2
0.5435
14
140
3.5
0.4
0.5013
15
140
3.5
0.8
0.4169
16
140
5.5
0.2
0.5663
17
140
5.5
0.4
0.5241
18
140
5.5
0.8
0.4397
19
180
2.5
0.2
0.6549
20
180
2.5
0.4
0.6127
21
180
2.5
0.8
0.5283
22
180
3.5
0.2
0.6663
23
180
3.5
0.4
0.6241
24
180
3.5
0.8
0.5397
25
180
5.5
0.2
0.6891
26
180
5.5
0.4
0.6469
27
180
5.5
0.8
0.5625
-
-
Coefficient of correlation of regression model
R2 value as obtained for the model is 93.8.it implies that the correlation between the actual values and predicted values of surface roughness from mathematical model develop is quite good. Finally the developed mathematical model can be checked by substituting the input process parameter to find output of model. The predicted values of the model have to be compared with the actual experimental values to find the error percentage. The validation of the model is done by substituting the input variable of experiments and verifying the model results with actual results.
The percentage error of the model value can be found by equation
% Error = Actual Value Predicted value × 100
Actual value
The Predicted values by regression model are
compared with actual values and their percentage of error is calculated. The Predicted values by regression model are compared with actual values and their percentageof error is calculated. The mean percentage error for regression is
3.98. The obtained result show that the predicted values of regression model come close to actual experimental values. The coefficient of correlation is found to be quite good. Hence the developed model is adequate and can be used to predict the surface roughness.
-
-
ANN Model
Besides using regression in surface roughness prediction, artificial neural network a branch of artificial intelligent has been implemented as an alternative approach. The predicted surface roughness has been performing using artificial neural network code in MATLAB® 2011. The input data for three independent variables spindle speed, feed rate, and depth of cut while actual surface roughness acted as target. The network propagates the input pattern from layer to layer until the output is generated. Then the result output will be compared with the target which is actual surface roughness in this study. The error is calculated and propagated back through network. Then, the weight will be changed and the same process repeated until the smallest error is achieved. In this project work a multi-layer feed forward back propagation neural network is employed as tool to predict the surface roughness.
-
Training the network
Once the network weights and biases have been initialized the network is ready for training .During training the weights and baises of network are iteratively adjusted to minimize the network performance error. ANN model structure and training parameters are as shown below Number of input node: 3 nodes
Number of hidden node (feed forward): 4 Number of output nodes: 1 node
Type of learning method: Supervised learning Algorithm: Feed forward back propagation Learning rule: Gradient descent rule
Number of learning Pattern used 20
The leaning parameter used : 0.5
Number of epochs 1000
The number of input parameter in the work was three namely speed, feed and depth of cut. Hence they were three input nodes used and the number of output node is one namely the surface roughness. In present work number of neurons in hidden layer was increased from one at the start .The best performance graph was obtained when the number of neurons was taken as four and is shown in figure 2.
-
Predicted output from ANN
The training, testing and validation set datas are simulated by different verity of hidden nodes. The network pattern which gives the closest value to original experimental values is 3-4-1 model.
Fig.2. Neural Network
The surface roughness is simulated using feed rate forward back propagation algorithm with tan-sigmoid function. The network is trained and simulated with the help of MATLAB software by setting target goal zero. The plot of predicted surface roughness (output) against the actual surface roughness (target) in Figure 3 below shown that both are correlated. This is because the predicted surface roughness is approaching towards the actual surface roughness with the coefficient of determination R is 0.99912.
-
ANN simulation by simulink
The ANN simulation was done using simulink tool in MATLAB software. The ANN simulation can be done by entering the input variables in developed user interface. Running the simulation gives the predicted results of developed ANN model for corresponding input entered. The figure 4 shows the user interface which is used to run the simulation of developed ANN model.
It shows the input and output variables associated with model. A combination of input variables can be entered in user interface to get their output by running the simulation. The predicted values of each model can be obtained by running simulation. The predicted results of surface roughness are given in table 6.
TABLE VI. PREDICTED SURFACE ROUGHNESS VALUE FROM ANN
Job No
Speed in RPM
Feed rate in mm/sec
DOC in mm
Predicted ANN Ra
1
120
2.5
0.2
0.4707
2
120
2.5
0.4
0.3957
3
120
2.5
0.8
0.3432
4
120
3.5
0.2
0.4759
5
120
3.5
0.4
0.3981
6
120
3.5
0.8
0.3481
7
120
5.5
0.2
0.4805
8
120
5.5
0.4
0.4201
9
120
5.5
0.8
0.3529
10
140
2.5
0.2
0.5562
11
140
2.5
0.4
0.4941
12
140
2.5
0.8
0.4208
13
140
3.5
0.2
0.5736
14
140
3.5
0.4
0.5219
15
140
3.5
0.8
0.4544
16
140
5.5
0.2
0.5983
17
140
5.5
0.4
0.5617
18
140
5.5
0.8
0.49
19
180
2.5
0.2
0.6473
20
180
2.5
0.4
0.589
21
180
2.5
0.8
0.5253
22
180
3.5
0.2
0.6605
23
180
3.5
0.4
0.614
24
180
3.5
0.8
0.5367
25
180
5.5
0.2
0.6512
26
180
5.5
0.4
0.6093
27
180
5.5
0.8
0.5572
The Predicted values by ANN model are compared with actual values and their percentage of error is calculated. The mean percentage error for ANN is 1.25.The obtained result show that the predicted values of ANN model come close to actual experimental values. The R values obtained is .999 is very good as it is very close to actual value and mean percentage error is very small so it is quite good. Hence the developed model is adequate and can be used to predict the surface roughness.
Fig.3. Plot of predicted surface roughness (output) against the actual surface roughness (target)
Fig.4. User interface used to run simulation of developed ANN model
-
-
Comparison of ANN and Regression models
The developed ANN model and regression model are compared for their predicted capabilities and error percentage of ANN model is compared with that of the regression model for corresponding surface roughness values. The predicted values of both the regression and ANN model come close to actual value. The predicted values of ANN model is found to be more accurate of two models The average percentage of error in predicted surface roughness is found to b 3.98% in the regression model and 1.25% in ANN model. However the ANN model is found to be better model for predicting the surface roughness. Graph is plotted between percentage error of regression and ANN model which is shown in figure 5.
Fig. 5. Graph between percentage error regression and percentage error ANN
-
-
CONCLUSIONS
The main purpose of this work is to provide an effective and accurate way to predict surface roughness in cylindrical grinding process.
Regression analysis had been applied to develop a mathematical model for surface roughness prediction method. The result of average percentage error is 3.98%, showing that the prediction accuracy is about 96%. That means the model developed is reliable to predict surface roughness with accepting accuracy range based on previous research.
Artificial neural network is a feasible technique and has been used quite often in recent researches in engineering field. The adaptation of this technique provides a brand new perspective in this field and in surface roughness prediction to be precise. Back-propagation neural network had been implemented to achieve the goal which is to minimize the error during surface roughness prediction. The result of the prediction is favorable with 1.25% average percentage of error, meaning that neural network is capable to predict the surface roughness up to 98% accurate. As a conclusion, artificial neural network provided better accuracy to predict surface roughness in cylindrical grinding process.
REFERENCES
-
J.Z. Zhang, J.C. Chen & E.D. Kirby, 2006, Surface Roughness optimization in an end milling operation using the Taguchi design method.
-
M.F.F. Ab. Rashid and M.R. Abdul Lani, Surface Roughness Prediction for CNC Milling Process using Artificial Neural Network Proceedings of the World Congress on Engineering, 2010 Vol III.
-
Advances in Modeling and Simulation of Grinding Processes, 2006 Keynote paper- E. Brinksmeier J. C. Aurich , E. Govekar , C. Heinzel1, H.-W. Hoffmeister, F. Klocke , J. Peters, R. Rentsch, D. J. Stephenson, E. Uhlmann,
K. Weinert, M. Wittmann.
-
E.Brinksmeimer, H.K.Tonshoff, C.Czenkusch and C.Heinzel(1998) Modelling and Optimization of grinding process. Journal of Intelligent Manufacturing pp 303-314.
-
S. Tasdemir, S. Neseli, S. Sartas, S. Yaldz. 2008. Prediction of surface roughness using artificial neural network in lathe, ACM International Conference Proceeding Series; Vol. 374, Proceedings of the 9th International Conference on Computer Systems and Technologies and Workshop for PhD Students in Computing.
-
Chang H.K., Kim J.H., Kim I.H., Jang D.Y. and Han D.C., 2007, In process surface roughness prediction using displacement signals from spindle motion, International Journal of Machine Tools and Manufacture Volume 47, Issue 6,
-
Users Manual, MITUTOYO Surftest SJ-400
-
Deepak Pal, Ajay Bangar, Rajan Sharma, AshishYadav, Optimization of tool and cutter. Grinder Parameters for Minimum Surface Roughness by Taguchi Parametric Optimization Technique, International Journal of Mechanical and Industrial Engineering (IJMIE), 2012.