
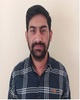
- Open Access
- Authors : Sucharu Sharma , Jainender Sharma
- Paper ID : IJERTV10IS090147
- Volume & Issue : Volume 10, Issue 09 (September 2021)
- Published (First Online): 27-09-2021
- ISSN (Online) : 2278-0181
- Publisher Name : IJERT
- License:
This work is licensed under a Creative Commons Attribution 4.0 International License
Alteration In The Properties of M35 Grade Concrete with Addition of GGBS and Jute Fiber
Sucharu Sharma
M.Tech. Scholar, Department of Civil Engineering, Sri Sai University, Palampur, H.P.,India
Jainender Sharma
Assistant Prof., Department of Civil Engineering, Sri Sai University, Palampur,H.P.,India
Abstract In India there is huge demand of construction materials, out of which cement is one of the important material used in the constructions. Due to large utilization of cement in the construction industry, the manufacturing of cement has to be increased. While production of cement the harmful gases exerted out from the cement kiln which is quite harmful to the health of living beings. To get rid off from such health causing issues either it is need to stop the usage of such toxic materials or replacing such materials with eco-friendly material which posses similar properties to the cement. In this paper M 35 grade concrete is manipulate with some proportion of GGBS which is replaced with cement and further addition of jute fiber at different proportions. The results shows that GGBS and jute fiber helps to improve the properties of concrete and make the concrete comparatively economical.
Keywords Jute Fiber, Ground Granulated Blast Slag (GGBS), Slump of Mix Concrete, Compressive Strength, Tensile Strength, Flexural Strength.
INTRODUCTION
The global usage of concrete is second to water. Annual worldwide production of concrete is estimated to be around one cubic meter for every person on earth. The increased demand for concrete calls for increased production of cement, undisputedly the most widely used single binder ingredient of traditional concrete. The annual rate of increase of cement production is about 3%. The world cement production was about 1 billion tonnes in 1990, 1.5 billion tonnes in 1995, 1.7 billion tonnes in 2003, 2.6 billion tonnes in 2008 it as against the estimated 2.2 billion tonnes in 2010. By 2020, cement requirement is estimated to be around 3.5 billion tonnes. It is estimated that with the demographic growth and industrialization, the pollution generated by cement production could reach an alarming 17 % of global CO2 emissions which is currently about 7 %.
In view of this, with an interest in minimizing the overall CO2 emissions associated with OPC composites to the extent technically and economically feasible, and sustainability in concrete construction, blended cements were introduced by partially replacing OPC by supplementary cementitious materials (SCM). In this work, M35 grade concrete is experimentally chosen in which cement is to be replaced with GGBS at different percentage of 12%, 22%, 32%, 42% and 52%, the jute fiber is added at percentage 0.12%, 0.22%, 0.32%, 0.42% and 0.52%.
LITERATURE REVIEW
Vijayalakshmi R (2021) investigated mechanical properties and crack arresting mechanism of natural jute fiber used as reinforcement for light weight concrete masonry prism. To
study the load deformation pattern, jute fiber reinforced masonry prism were subjected to axial compression load. from the stress strain behavior it can be concluded that jute fiber reinforcement in foam concrete helps to improve the pre-cracking behavior and prevents the formation of major crack plane in masonry units. From the study it can be concluded the light weight foam concrete with fiber reinforcement can be used as better alternative to clay bricks and aerated concrete blocks.
Pramodini Sahu et al. (2020) proposed study on effect of jute fiber orientation and percentage on strength of jute fiber reinforced concrete. In this research, the experiments related to jute fiber reinforced concrete are done by taking different fiber percentage and the compressive strength and modulus of rupture value observed. This work concluded that with jute fiber the compressive strength value more or less changed with respect to Plain cement concrete.
S.Tiwari et. al. (2020) studied mechanical properties and durability study of jute fiber reinforced concrete. The results shows that the workability indicated that the slump value reduced as an increased amount of jute fiber in the concrete specimen. Also compressive strength reduced in the acid curing as compared to normal curing. Additionally jute fiber increased the compressive and tensile strength of every concrete mix.
Peiyuan Chen et al. (2019) worked on ecological upgrade of normal strength of mortar by using high volume of GGBS. The ecological upgrade of GGBS like materials is more meaningful for the sustainable development in the greener way. Comprehensive experiments were conducted to investigate the influence of experimental variables such as content of cement, curing temperature and mass ratio of water to binder on the fresh properties, compressive strength, hydration products, micro structures and pore structures of normal strength mortar. The results shows that the ecological upgrade of normal strength mortar is feasible. Ashish kumar dash et al. (2018) researched on different materials like rice husk ash, GGBS, silica fume to obtain the desired needs. Higgins discussed on the effect of addition of a small percentage of calcium carbonate or calcium sulfate on the sulfate resistance of concrete containing GGBS. Shariq Prasad et al. (2018) studied the effect of curing procedure on the compressive strength development of cement mortar and concrete incorporating ground granulated blast furnace slag is studied. The compressive strength of OPC concrete shows higher strength as compare to the GGBFS based concrete for all percent replacement and at all ages. Incorporating 40% GGBFS is highly significant to increase the compressive strength of concrete after 56 days
than the 20 and 60% replacement. Among GGBFS based concrete 40% replacement is found to be optimum.
Valeti Ravikumar et al. (2018) studied the behavior of M 40 concrete after addition of banana fiber and jute fiber in it. The author found that the compressive strength and split tensile strength increases with the percentage of banana fiber at 0.5% and jute fiber at 0.2% and GGBS at 40%.. The flexural strength also increases gradually with banana fiber at 0.075% and jute fiber at 0.2% and GGBS at 40%.
EXPERIMENTAL WORK
The composition of slag essentially depends on the raw materials used in the iron production process.
Chemical components |
%age of chemical components |
MgO |
0.8868 |
Al2O3 |
8.6925 |
SiO2 |
33.6942 |
P2O5 |
0.4752 |
SO3 |
0.9498 |
K2O |
0.8946 |
CaO |
21.9869 |
MnO |
2.4709 |
Fe2O3 |
23.7346 |
NiO |
6.2144 |
Chemical components |
%age of chemical components |
MgO |
0.8868 |
Al2O3 |
8.6925 |
SiO2 |
33.6942 |
P2O5 |
0.4752 |
SO3 |
0.9498 |
K2O |
0.8946 |
CaO |
21.9869 |
MnO |
2.4709 |
Fe2O3 |
23.7346 |
NiO |
6.2144 |
Table 3.1: Chemical Properties of GGBS (Source:Indian- mart)
Methodology
To achieve the objectives of the work various experiments are performed are:
-
Slump Test for Workability
-
Compressive Strength Test for Concrete
-
Split Tensile Strength Test for Concrete
-
Flexural Strength Test for Concrete
The test results of M35 grade concrete were obtained by replacing cement with GGBS in various percentages of 0%, 12%, 22%, 32%, 42% and 52% and also Jute fiber is added
Slump Test
Results and Discussion
in various percentages of 0%, 0.12%, 0.22%, 0.32%, 0.42% and 0.52%. All specimens were cured for 7days and 28 days before testing.
Materials Required
1. Jute fiber
Jute with the highest production volume is the cheapest natural fibers. These fibers are extracted from the ribbon of the stem. Jute fibers are composed mainly of the plant materials cellulose and lignin. Recent studies have shown that jute fiber delays the hardening of concrete and improves the resistance of concrete against cracking. Workability of jute fiber reinforced concrete mix is improved by using an admixture called tannin.
Properties of Jute Fiber
-
Jute fiber is 100% bio-degradable and recyclable and thus environmentally friendly.
-
Jute is a natural fiber with golden and silky shine and hence called The Golden Fiber.
-
Jute is the cheapest vegetable fiber procured from the blast or skin of the plant's stem.
-
It is the second most important vegetable fiber after cotton, in terms of usage, global consumption, production, and availability.
-
It has high tensile strength, low extensibility, and ensures better breathability of fabrics. Therefore, jute is very suitable in agricultural commodity bulk packaging.
-
It helps to make best quality industrial yarn, fabric, net, and sacks.
It is one of the most versatile natural fibers that has been used in raw materials for packaging, textiles, non-textile, construction, and agricultural sectors.
Bulking of yarn results in a reduced breaking tenacity and an increased breaking extensibility when blended as a ternary blend.
2. Ground Granulated Blast Furnace Slag
Also known as GGBS. It is obtained during the manufacturing process of iron in blast furnace. The slag is a mixture of lime, silica and alumina and some oxides that make up Portland cement but not in the same proportion.
Table 4.1: Slump values of concrete using jute fiber and
GGBS
Concrete mix |
Slump Value in mm |
||
Jute fiber |
GGBS |
||
0 |
0 |
128 |
|
0.12 |
12 |
131 |
|
0.22 |
22 |
140 |
|
0.32 |
32 |
144 |
|
0.42 |
42 |
150 |
|
0.52 |
52 |
155 |
|
Slump Value (mm) 18 16 14 14 15 15 Sl u 14 12 13 m p 12 Va lue10 ( m 8 m 6 4 2 0 0 1 2 3 4 5 0 0.1 0.2 0. 0.4 0.5 Replacement(%) oGf GBS and Jute Fiber |
The graph shows the result of slump values which indicate that the slump value of concrete goes on increasing after the relacement and addition of GGBS and jute fiber respectively.
Compressive Strength Test
Table 4.2: Compressive Strength of Concrete Cubes Using GGBS and Jute Fiber after 7 days and 28 days of Curing
Concrete mix |
Compressive Strength @ 7 Days |
Compressive Strength @ 28 Days |
|
Jute fiber |
GGBS |
||
0 |
0 |
21.75 |
42.1 |
0.12 |
12 |
22.10 |
44.30 |
0.22 |
22 |
22.85 |
45.85 |
0.32 |
32 |
23.15 |
47.72 |
0.42 |
42 |
25.96 |
48.50 |
0.52 |
52 |
24.10 |
46.80 |
The graphs shows the result of compressive strength at 7days and 28 days, indicate the values of mix goes on increasing the maximum value at 7 days is 25.96 kN/mm2 at 0.42% of Jute Fiber and 42% of GGBS whereas at 28 days the maximum compressive strength value is 48.5 kN/mm2
Split Tensile Test
Table 4.3: Split Tensile Strength of Concrete using GGBS and Jute Fiber after 7 days and 28 days of curing
Concrete Mix |
Split Tensile Strength @ 7 Days |
Split Tensile Strength @ 28 Days |
|
Jute Fiber |
GGBS |
||
0 |
0 |
2.05 |
4.85 |
0.12 |
12 |
2.62 |
5.22 |
0.22 |
22 |
3.15 |
5.83 |
0.32 |
32 |
3.45 |
6.12 |
0.42 |
42 |
4.49 |
6.91 |
0.52 |
52 |
3.82 |
5.42 |
Split Tensile strength of
cylinder 28 days
10
Split Tensile strength of
cylinder 28 days
10
4.85
4.85
5.22
5.22
5.83
5.83
6.12
6.12
6.91
6.91
5.42
5.42
5
0
5
0
M1 0,0 M2 M3 M4 M5 M6
12, 0.1222, 0.2232, 0.3242, 0.4252, 0.52
Replacement % GGBS&JUIT FIBER
Split Tensile strength of cylinder 28 days
M1 0,0 M2 M3 M4 M5 M6
12, 0.1222, 0.2232, 0.3242, 0.4252, 0.52
Replacement % GGBS&JUIT FIBER
Split Tensile strength of cylinder 28 days
Strength kN/mm2
Strength kN/mm2
The graphs shows the result of split tensile strength at 7days and 28 days, indicate the values of mix goes on increasing, the maximum value at 7 days is 4.49 kN/mm2 at 0.42% of Jute Fiber and 42% of GGBS whereas at 28 days the maximum value is 6.91 kN/mm2
Flexural Strength Test
Table 4.4 : Flexural Strength of Concrete using GGBS and Jute Fiber after 7 days and 28 days of Curing
Concrete Mix |
Flexural Strength @ 7 Days |
Flexural Strength @ 28 Days |
|
Jute Fiber |
GGBS |
||
0 |
0 |
2.85 |
4.86 |
0.12 |
12 |
2.96 |
5.26 |
0.22 |
22 |
3.59 |
6.09 |
0.32 |
32 |
4.50 |
8.11 |
0.42 |
42 |
4.98 |
9.24 |
0.52 |
52 |
3.12 |
8.93 |
The graphs shows the result of flexural strength at 7days and 28 days, indicate the values of mix goes on increasing the maximum value at 7 days is 4.98 kN/mm2 at 0.42% of Jute Fiber and 42% of GGBS whereas at 28 days the maximum flexural strength value is 9.24 kN/mm2 .
CONCLUSION
-
The slump value increases 131 mm to 155 mm due to jute fiber percentage ranging from 0 to 0.52%. Maximum slump 155 mm is observed at 0.52% jute fiber in concrete mix due to the reason that heavy reinforcement of jute is added.
-
The compressive strength of concrete after 28days curing increases gradually by replacement of cement with GGBS percentage and addition of jute fiber.
-
The split tensile strength achieves maximum position of 6.91 N/m2 when 0.42% and 42% of jute fiber and GGBS is added to concrete mix after curing 28days
-
The ultimate flexural strength observed maximum with 42% GGBS and 0.42% of jute fiber i,e 9.24 N/m2 of mix after curing 28days.
REFERENCES
-
Vijaylakshmi R " Investigation on the Mechanical Property and Crack Arresting Mechanism of Natural Jute Fiber used as Reinforcement for Lightweight concrete Masonry Prism" IOP Conf. Series: Materials Science and Engineering Vol. 1126 (2021) 012064 DOI
:10.1088/1757899X/1126/1/0120654
-
Pramodini Sahu "Effect of Jute Fiber Orientation and percentage on Strength of Jute Fiber Reinforced Concrete" International Journal of Engineering and Advanced Technology(IJEAT) ISSN:2020-8958 Volume-9 Issue-3, February,2020
-
S.Tiwari "Properties and Durability Study of Jute Fiber Reinforced Concrete" IOP Conf. Series:Material Science and Engineering Vol. 961(2020)012009 DOI:10.1088/1757899X/961/1/012009
-
Peiyuan Chen "Ecological Upgrade of Normal-Strength Mortars by Using High Volume of GGBS" Hindawi Advances in Civil Engineering Volume 2020, Article ID 72101469, 13 Pages https://doi.org/10.1155/2020/7101469.
-
Ashish Kumar dash "Effect of pozzolanas on fiber Reinforced concrete " 2018 [11]. Higgins, D. D.
-
M. Shariq, J. Prasad "Strength development of cement mortar and concrete incorporating GGBFS " Asian journal of civil engineering
-
VenuMalagavelliet. "High performance concrete with GGBS and robo sand" International Journal of Engineering Science and Technology Vol. 2(10), 2014, 5107-5113.
-
Luo, R., Cai, Y., Wang, C., and Huang, X. "Study of chloride binding and diffusion in GGBS concrete" Cement Concrete. Res., 17.
-
C. A. Clear, "Formwork striking time for Ground Granulated Blast Furnace Slag concrete: test and site result" Building Board Structural and Structural Panel Paper l0517 Nov..441-448 Bldgs. 2015, 104,
-
A.Oner,S.Akyuz, "An experimental study on optimum usage of GGBS for the compressive strength of concrete Cement & Concrete Composites" 29 (2017) 505514 SSRG International Journal of Civil Engineering (SSRG-IJCE) volume 2 Issue 10 October 2015 ISSN: 2348 8352 www.internationaljournalssrg.org Page 41
-
Ganesh Babu, K., and Sree Rama Kumar, V. "Efficiency of GGBS in concrete Cement. Concrete" Res., 2017, 1031 1036.
-
P.J. Wainwright, N. Rey "The influence of ground granulated blast furnace slag (GGBS) additions and time delay on the bleeding of concrete" Cement and Concrete Composites 22, (2017), 253-257
-
M.N. Soutsos, S.J. Barnett et al, "Fast track construction with high- strength concrete mixes containing Ground Granulated Blast Furnace Slag", High-Strength/High Performance Concrete 255-263
-
. Pavia and E. Condren "Study of the Durability of OPC versus GGBS Concrete on Exposure to Silage Effluent" Journal of Materials in Civil Engineering ASCE / April 2008 / 313-319 15. Increased sulfate resistance of GGBS concrete in the presence of carbonate. Cement. Concrete. Composites, (2018), 913919.
-