
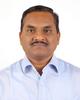
- Open Access
- Authors : Dr. Namdeo A. Hedaoo
- Paper ID : IJERTV10IS100114
- Volume & Issue : Volume 10, Issue 10 (October 2021)
- Published (First Online): 25-10-2021
- ISSN (Online) : 2278-0181
- Publisher Name : IJERT
- License:
This work is licensed under a Creative Commons Attribution 4.0 International License
Subcontracting Management Issues and Challenges facing the Residential Projects in Pune City (India)
Dr. Namdeo A. Hedaoo
Associate Professor, Department of Civil Engineering,
Government College of Engineering Pune, India.
AbstractFor efficient construction projects, subcontractors are essential, but various problems arise in subcontracting management. This paper aims to examine and study issues in subcontracting management in residential projects in Pune. After an extensive literature study, a research gap was identified through various journals, research papers, and books. A suitable research problem has been formulated based on the findings of the research gap. The research design includes collecting primary data, i.e., by floating a questionnaire and secondary data, i.e., the literature study. The primary data was gathered by distributing a questionnaire to businesses involved in residential construction in Pune. At first, for checking data reliability, the Alpha test by Cronbach was performed in the Statistical Package for Social Science (SPSS). The responses were collected according to the Likert scale by conducting a site visit on various residential projects in Pune. The contribution of each factor related to issues and challenges in subcontracting management was examined, and the criticality rating of the qualities was considered as described by the Relative Importance Index (RII) and TOPSIS. Based on the findings, necessary conclusions and recommendations have been drawn, highlighting the factors that have a crucial impact on the selection and engagement of subcontractors in residential projects.
KeywordsCronbach's Alpha (CA), Subcontractors, Statistical Package for Social Sciences (SPSS), Relative Importance Index (RII), TOPSIS.
-
INTRODUCTION
Every Construction project has various complexity, mainly human resources, raw materials, equipment, technology, finance, and most notably. Many parties, including clients, builders, vendors, manufacturers, subcontractors, and others, are involved in construction projects. The contractors are usually subcontracted to work to turn the risks. Subcontractors work with core competencies, efficiency, and completion in timely execution, supplying human resources, tools, equipment, and designs. India is going ahead with many residential projects for development in that subcontractors constitute the majority of the construction and installation activities and play an extremely crucial role in completing the residential projects. Whatever the General Contractor, parts of almost any residential project are subcontracted to companies with specialized resources, advanced technology, and engagement with the project [1, 23]. Subcontracting is how cost minimization, completion of projects within a time frame, and performance of the specific work increase. Specialized residential developments can also be procured, but different
kinds of complications can also occur. These may come from various factors, but some primary reasons are characteristics of different types of work, coordination between contractor and sub-contractor, litigation, poor operation, finance, unavailability of resources, and most importantly, health safety-related issues [14]. The subcontractor's work constitutes most of the construction activities and plays a significant role in project success. Regardless of the expertise of the general contractor, parts of almost any undertaking are licensed to specialist companies. It is observed that More and more specialist work is expected to be employed to improve production and sustainability. Subcontracting is an affordable way to provide specialized services but can lead to many issues. Such issues can derive from specialist works characteristics and subcontracting procurement methods [7]. Project claims are always ongoing issues that entail much care documentation keeping. When contested claims are sent, the sub-contractor is entangled with the primary contractor or customer. The subject matter studied consists of payable timeliness for the selection process of a subcontractor, the general contractor, bonding of the sub-contractor, building insurance, construction site security, partnership with different parties, and problems with productivity. This study mainly deals with the issues in subcontracting management. A detailed understanding of each function is required to coordinate between the contractors and subcontractors and provide the best techniques for subcontractor management functions to work efficiently and effectively.
Problems with Subcontractor Management:
The two major problems occurred in subcontractor management
-
Managing the Work
-
Managing people.
Along with the significant problems, some of the critical problems in subcontracting management are as follows:[5]
-
Issues associated with payment
-
Issues associated with tendering
-
Issues associated with the communication
-
Issues associated with insurance
-
Issues associated with safety
-
Issues associated with partnership
-
Issues associated with productivity
-
Withheld retaining by general contractor
Objectives of the Study:
The study aims to identify to conduct a study on the subcontracting management affecting the residential project performance, safety, productivity, and quality to determine the responsibilities of each party and allocation of risk.
The specific objectives are:
-
To study the importance of subcontracting in residential projects.
-
To identify the various factors that cause issues in subcontracting management.
-
To analyze the data and list the most serve factors.
-
To suggest recommendations to reduce the number of issues in managing subcontractors.
-
-
LITERATURE REVIEW
Proper planning and risk management are necessary for smooth operational activities and effective supply chain management in residential projects. Subcontractors and suppliers play a critical role in delivering projects to the customers with a high level of safety, quality, and ethics due to the many problems found with subcontracting, which is rarely acknowledged [9]. Subcontracting is a common strategy adopted in many business sectors. Sub-contracting has benefited considerably in the construction industry worldwide, but the process is not prevention-oriented. Conflicts and disputes often occur between the main contractor and subcontractor, which has impaired the method's overall effectiveness [3].
Lew Yoke-Lian (2012) states that subcontractors are specialists for executing a particular job, supplying materials, human resources, machinery, instruments, or designs as agents of the company's manufacturing chain. Subcontractors employed for specialized job assignments play a crucial part in most construction projects. Usually, the General Contractor carries out the fundamental activities and subcontracts the rest to different specialist contractors [16].
According to Francis Yik (2006), Subcontracting, shown as an economical means of delivering projects, is a long- standing procedure in the construction industry. However, issues such as conflicts and disputes between contracting parties, lack of service standards, delays in project work, pay disputes, and others that occur from time to time in the local construction industry can be caused by specialized work or unsatisfactory work subcontracting activities. These challenges have to be tackled because they undermine the indutry's productivity and competitiveness [8].
David Arditi and Ranon Chotibongs (2005) stated that the concerns include the General Contractors' payments, the procedure for subcontractor's selection, bonding with subcontractors, construction insurance, building site security issues, partnerships with different parties, and competitiveness issues [6].
Caroline T W Chan (2006) stated that Subcontracting is a common strategy in many business sectors. It gives enterprises greater flexibility, allowing them to spend less on staffing and associated costs such as insurance premiums and pensions. More importantly, various contract forms can incorporate expert knowledge from different external parties into the business process. Although subcontracting is perceived as an effective and competitive tool to procure necessary skills for
the project work, success relies heavily on selecting suitable subcontractors. Conflicts and disagreements between the principal contractor and the subcontractor often affect work efficiency. As a result, the main contractor must monitor the subcontractor's performance, increasing the overall production cost. Subcontractor evaluation is an effective process to determine which subcontractor is to be appointed in future projects. Experts have recommended a simulation model to identify which subcontractor best fits a work item using the lowest total project cost as the objective function. However, other essential factors such as quality control and safety performance were not considered in the Probabilistic neural network (PNN) model. Twelve evaluation factors were used as the input variables for PNN. Finally, subcontractor performance is assessed in the range of 1 to 5 (very poor to very good) given in the calibration chart [4].
Othman (2002) stated that Receiving payment on time is one of the most severe problems in establishing a long-lasting connection between the contractor and the subscriber. There is a lack of confidence between them, and all sides in all commercial transactions are suspect. In some situations, the employer is seen as a lousy payee, complicating the relationship further [19].
S. A. Assaf (2005) identified the main reason was the delay in the contractor's payment to subcontractors, material shortage in construction, change in material, the weather condition, shortage in human resources (unskilled, semiskilled, and skilled human resources). Costs overrun, rescheduled, rearrangement, litigation, dispute, and arbitration were the six principal consequences of the delay [20].
Ndekugri, I. (2008) found that Delays and disruptions to the contractor's progress are a significant cause of the construction sector disputes and conflicts. Sometimes in question, the dichotomy responsible for delays (project owner or his contractors) is partially due to the many causes of the possible delays and interruptions. The settlement of such disputes and claims has been a matter of uppermost challenge with increasing project scope and specifications combined with various stakeholders, all subject to their performance requirements. Furthermore, conflicts between the project participants are a factor that adversely affects cost efficiency, ignorance and lack of expertise, the presence of inadequate characteristics of the project and lack of cooperation, hostile social, economic, and climate conditions, reticence to make timely decisions, aggressive tender competitiveness and a short bidding period [18].
Shash (1998) stated that Contractors and subcontractors cannot collabourate strongly on a regular schedule but maintain long-term business relationships. The statistics provided in this publication show that for an average of 21.1 years, 76 % of industrial subcontractors maintained their partnerships with the contractors. He outlined the four 'C' for the contractor general and subcontractor: communication, consideration, compensation, and cooperation, saying that "the sole responsibility for the project performance rests with the general contractor" [21].
According to Hsieh (1998), under the instruction of the general contractor, the subcontractors deliver a significant amount of construction work. The efficient activity of sub- contractors is intended to benefit all involved parties,
including the owners, general contractors, and sub-contractors. In reality, a sub-contractor can be an intermediary individual to provide the general contractor with various construction and installation-related services. In particular, in labour relations, management, equipment maintenance, material supplies, prefabrication, staff recruitment, standardization, quality control, and use, sub-procured companies have a critical influence on on-site efficiency. According to him, most contractors' efficiency, schedule management, and worker preparation are the main areas for enhancing subcontractors' productivity [12].
Alinitwe (2007) found that ten major issue areas in the building's construction include lack of supplies, preliminary drawings, incompetent managers and supervisors, poor site layout, lack of equipment and tools, absenteeism, poor site layout, weak coordination, instruction time, inspection delay, and rework [2].
Daniel (2000), in this paper the ability of subcontractors to strengthen contracts and commercial ties between contractor and sub-contractor in the competition of construction firms and their value chains. He also defined issues that made subcontracting policy an exciting theme for construction firms and focused on contracts and mutual ties between developers and subcontractors. The aspects such as the decrease in material prices, the rise in labour costs, and market opening to the international competition were necessary for the subject [5].
Jill Wells (2000) stated that the employment by sub- contractors is just outsourcing labour and is a long known and common phenomenon in construction industries of developed countries. In this article, he discussed the impacts on construction industry growth, workers' well-being, and the fulfilment of larger development goals. It is concluded that some of the negative repercussions may be unavoidable but must consider existing procedures to improve them [13].
Hinze and Wilson (2000) said that Subcontractors should maintain a healthy working atmosphere while at the same time providing enough safety personnel at the facility. The owner and developers of the project affect the safety protocol at the workplace. Moreover, engineers must take protection, health, and health care into account in their technical and moral tasks. While there has been much improvement in safety measures, the industry still lags as to protection. Safety rules are applied in developing countries, but construction firms are generally fragile in successfully applying such rules. In general, they lack safety dedication because of a limited budget, time, and resources [11].
Kumaraswamy, M. M. (2000) stated that adopting partnering arrangements between the main contractor and subcontractors help manage the quality, coordination, and scheduling of subcontracted works more effectively [15].
After carrying out a literature review, primary data was collected. Factors were listed out causing issues in subcontracting management, and depending upon the factors, a questionnaire was framed.
-
RESEARCH METHODOLOGY
The questionnaire was prepared, conducted among the professionals like Assistant managers, Managers, Dy Manager, Senior Engineer, and Engineers by a pilot study on
various residential projects. As the outcome of this phase, 39 factors causing issues in subcontracting management in residential construction projects were identified. The data was collected by conducting site visits on various residential projects in Pune (Aundh, Baner, Hadapsar, Kharadi, Pashan, Pimple-gurav, Pimpri, Wagholi and Wakad); almost all the areas were covered under this study to give better. A total of
40 site visits were conducted. This survey covered all residential projects, such as high-rise structures, apartment blocks, bungalows, townships, and villas. These projects were almost completed. Cronbach's alpha (CA) test was initially performed to verify the reliability of data. Data analysis is done using Statistic Package for Social Science SPSS (v17.0) software; this analysis included the results assigned by the respondents per factor, which led to a comparative analysis of the responses made in the 40 sites. In engaging subcontractors, the contribution of each factors related issues & challenges was examined; the attributes were described by the Relative Importance Index (RII) and TOPSIS in terms of criticality perceived by the respondents.
In the present study, a questionnaire survey was administered to people engaged in residential projects to investigate the issues and determine the differences in perception between the contractors and subcontractors. Our primary source of collecting data is by conducting site visits on various residential projects in Pune. All questions in the questionnaire mainly deal with issues between subcontractors and main contractors. The questionnaire also seeks general information about the respondents, as shown in Table 1.
TABLE I. GENERAL INFORMATION ABOUT THE RESPONDENTS
Name of the respondent:
Name of the organization
Location of project
Position of Respondent
Qualification
Contact No.
Email ID
Experience
Date of visit
In achieving the objectives of this study, the information regarding different types of issues and challenges in engaging subcontractors in residential projects was obtained from various sources, i.e., international journals, international conferences, and published books. As shown in Table 2, these issues and challenges were used to develop the questionnaire [22].
Factors
Not a factor 1
Minor factor 2
Moderate Factor
3
Serious Factor 4
Major Factor 5
A time period of the project
Accident on site
Neglecting the safety measures
Factors
Not a factor 1
Minor factor 2
Moderate Factor
3
Serious Factor 4
Major Factor 5
A time period of the project
Accident on site
Neglecting the safety measures
TABLE II. LIST OF FACTORS
Factors
Not a factor 1
Minor factor 2
Moderate Factor
3
Serious Factor 4
Major Factor 5
spare parts
Contractual disputes due to poor framing of contract document
Factors
Not a factor 1
Minor factor 2
Moderate Factor
3
Serious Factor 4
Major Factor 5
Improper supervision of work
Lack of knowledge/ experience
Not following the construction schedule
Unavailability of funds
Mistakes and omissions in the bills
Delay in payment of progress work
Slow mobilization of resources
Material wastage
Delay of works
Absence of labour at the site
Lack of proper communications with the subcontractor
Scope of Work not defined properly
Drawing is not precise before starting the work
Shortage of equipment and machinery of the subcontractor
Decision pending from owner/client
Regular changes in drawings and design
Not maintain cash flow in time
Efficiency in Time management of the subcontractor
Unavailability of machinery
Payment system
Shortage of skilled labour with subcontractor
Variations in the Scope of work and changes in specifications.
Frequent equipment breakdown
Equipment allocation problem
Change in cost of resources (labour and material)
Low labour productivity
Not following the contractual conditions
Unavailability of material
Idle human resources
Simultaneous involvement of the subcontractor in various projects
Late involvement of the subcontractor in the project
Low bid
Idle material
Idle machinery
Shortage in supply of labour, equipment, and
Factors
Not a factor 1
Minor factor 2
Moderate Factor
3
Serious Factor 4
Major Factor 5
Improper supervision of work
Lack of knowledge/ experience
Not following the construction schedule
Unavailability of funds
Mistakes and omissions in the bills
Delay in payment of progress work
Slow mobilization of resources
Material wastage
Delay of works
Absence of labour at the site
Lack of proper communications with the subcontractor
Scope of Work not defined properly
Drawing is not precise before starting the work
Shortage of equipment and machinery of the subcontractor
Decision pending from owner/client
Regular changes in drawings and design
Not maintain cash flow in time
Efficiency in Time management of the subcontractor
Unavailability of machinery
Payment system
Shortage of skilled labour with subcontractor
Variations in the Scope of work and changes in specifications.
Frequent equipment breakdown
Equipment allocation problem
Change in cost of resources (labour and material)
Low labour productivity
Not following the contractual conditions
Unavailability of material
Idle human resources
Simultaneous involvement of the subcontractor in various projects
Late involvement of the subcontractor in the project
Low bid
Idle material
Idle machinery
Shortage in supply of labour, equipment, and
In this analysis, to assess the relative value of the different variables that causes subcontract management problems, the same approach would be used. Table 3 shows that the questionnaire is based on a scale of five ordinal actions of one scale (1) to five (5).
TABLE III. LIKERT'S SCALE
Option
Scale of measure
Major Factor
5
Serious Factor
4
Moderate Factor
3
Minor Factor
2
Not a factor
1
-
Cronbach's alpha:
In 1951 Lee Cronbach developed the Cronbach's alpha or coefficient alpha, which is signified by ''. Cronbach's alpha may be used to test the reliability or internal consistency of a series of scale or test objects. It is used to check if multiple Likert scale tests are reliable. The help of Cronbach's alpha shows you whether the variable of interest is measured correctly in the test you designed. It is used under the assumption that you have various elements that measure the same base structure.
Where N is the total number of items, c is the average covariance between item pairs, and v is an average variance.
It ranges from 0 to 1.
= 0: If all of the scale items are entirely independent of one another (i.e., are not correlated);
= 1: If all of the items have high covariances, as the number of items in the scale approaches infinity
Theoretically, the findings from Cronbach alpha can send you a number between 0 and 1, and negative numbers can also be obtained; if you get a negative number, it indicates that the data you have entered has some error or there is something wrong with it the data.
Throughout the evaluation of assessments and questionnaires, alpha is an essential component. Assessors and investigators must measure this quantity to provide an understanding of their data authenticity and accuracy. The values of alpha are between 0 and 1 since it is the ratio of two variances. However, alpha estimates take any value less than or equal to 1, even negative value based on the estimate process. Whereas only positive values make sense, higher alpha values are more desirable. According to A rule of thumb, some practitioners need 0.70 or better reliability (obtained on a significant sample) before using an instrument.
For dichotomous questions, a rule of thumb for the interpretation of alpha (i.e., questions with two possible answers) or questions on the Likert scale is as follows:
-
If the CA Value is 0.9, then the IC is Excellent.
-
If the CA Value is 0.9 > 0.8, then the IC is Good.
-
If the CA Value is 0.8 > 0.7, then the IC is Acceptable.
-
If the CA Value is 0.7 > 0.6, then the IC is Questionable.
-
If the CA Value is 0.6 > 0.5, then the IC is Poor.
-
If the CA Value is 0.5 > , then the IC is Unacceptable.
-
-
Ranking for Factors
Ranking for the factors is performed to rank each factor according to their impact on the project objectives. Two methods are used: Relative importance index (RII) and another is TOPSIS.
-
Relative Importance Index
After carrying out the Reliability Analysis, it is essential to carry out the Relative Importance Index (RII) to prioritize the factors.
W is the respondents' weighting to each element (ranging from 1 to 5), N is the total number of respondents, and A is the significant weight (i.e., 5 in this case). There were 1 to 5 RIIs, which were higher and more significant than subcontracting management. Every RII seen by all respondents must show a general picture of the Pune residential construction project's time and costs to determine the overall and general rankings.
-
Topsis
Hwang and Yoon created TOPSIS; a MADM technique Alternative is chosen for the smallest Euclidean distance from the optimal solution in this technique. A perfect approach is to match all solutions with importance for attributes to the maximum values, and the least attribute values in the database are negative-ideal solutions. Therefore, TOPSIS selects the solution close to the positive solution and far from the ideal negative solution. If there are alternatives in the MCDM (A1, A2, A3…, Am) and m criteria (C1, C2, C3…, Cn) problems, all alternatives are assessed by m.
Using the following steps for TOPSIS:
-
Get the decision matrix using an intangible numerical scale
-
Get structured decision matrix R through the relation
-
Build the standard structured decision matrix
-
Identify ideal and harmful ideal solutions
-
For each alternative, evaluate the separation measures
-
SPSS Analysis for Development of Correlation
Using SPSS, the distinction between variables was achieved through data analysis. The SPSS spreadsheet has included all 39 variables. The findings from SPSS were shown to correlate between different variables. All this relationship between -1 and +1 was established. In addition to a positive value, extreme negative implies more significant correlations between factors. While values near zero indicate that the correlation between those respective factors is very weak, and zero indicates no correlation. +1 indicates that the strongest positive correlation suggests that if there is +1 between any two factors, then there is a positive correlation of the highest
degree; if one factor increases, the other also increases with the same intensity and level. 1 indicates the strongest negative correlation, meaning that if there is a value near this, there is an inverse correlation stating that others decrease with the same intensity if one risk tends to increase. They are inversely proportional. Every value from 0 to 1 indicates a positive correlation, but the rate at which one factor differs is different, and they are going in the same direction. Similarly, every value from 0 to -1 indicates a negative correlation differing only in intensity; hence if one increases other decreases depending upon the rate.
-
-
DATA ANALYSIS
The designed questionnaire was distributed, and responses were collected based on the five-point Liker scale by conducting site visits on various residential projects in Pune. Based on their experiences, the respondents were asked to rate the factors. The respondents' profiles have been analyzed based upon the data collection and are shown in fig. 1. Most of the respondents were Assistant managers (42%), Managers (26%), Dy Manager (11%), Senior Engineers (13%), and
Engineers (8%).
Fig. 1. The respondent's profile.
Following figure 2 indicates the respondent's experience and average experience, which is 12 years. Mainly the responses were collected from the respondents of experience above 5 years to find the best results. All the respondents were experts in their field.
Fig. 2. The experience of the respondents.
Chart 1 shows the response recorded from 40 sites through various respondents, and chart 2 shows Iter-Item Correlation Matrix obtained from SPSS.
Sr.
no.
Factors
RII
Ranking
25
Variations in Scope of work and changes in specifications.
0.745
25
26
Frequent equipment breakdown
0.744
26
27
Equipment allocation problem
0.74
27
28
Change in cost of resources (labour and material)
0.736
28
29
Low labour productivity
0.735
29
30
Not following the contractual conditions
0.732
30
31
Unavailability of material
0.73
31
32
Idle manpower
0.725
32
33
Simultaneous involvement of the subcontractor in various projects
0.721
33
34
Late involvement of the subcontractor in the project
0.72
34
35
Low bid
0.7
35
36
Idle material
0.691
36
37
Idle machineries
0.688
37
38
Shortage in supply of labour, equipment, and spare parts
0.68
38
39
Contractual disputes due to poor framing of contract document
0.63
39
Sr.
no.
Factors
RII
Ranking
25
Variations in Scope of work and changes in specifications.
0.745
25
26
Frequent equipment breakdown
0.744
26
27
Equipment allocation problem
0.74
27
28
Change in cost of resources (labour and material)
0.736
28
29
Low labour productivity
0.735
29
30
Not following the contractual conditions
0.732
30
31
Unavailability of material
0.73
31
32
Idle manpower
0.725
32
33
Simultaneous involvement of the subcontractor in various projects
0.721
33
34
Late involvement of the subcontractor in the project
0.72
34
35
Low bid
0.7
35
36
Idle material
0.691
36
37
Idle machineries
0.688
37
38
Shortage in supply of labour, equipment, and spare parts
0.68
38
39
Contractual disputes due to poor framing of contract document
0.63
39
The reliability of data supplied in an exam or research report must be evaluated with high-quality assessments. Alpha is a frequently used research reliability measure. The length and dimensionality of the test were affected by alpha. If those assumptions are not fulfilled, a low alpha emerges. Alpha does not simply assess test homogeneity or uniqueness since test reliability depends on the length of the test. A lengthy test enhances the reliability of a test, whether or not it is homogenous. A high alpha value (> 0.90) indicates redundancies and shorter test lengths.
TABLE IV. CRONBACH'S ALPHA (CA) ANALYSIS
CA
CA (Based on Standardized Items)
Number of Factors
0.871
0.862
39
Thus, the Cronbach Alpha's value after carrying out the reliability analysis can be found out to be 0.871. The alpha values mentioned in Table 4 show that the value falling in the range of 0.8-0.9 is considered good.
-
Relative Importance Index (RII)
After carrying out the Reliability Analysis, it is essential to carry out the Relative Importance Index (RII) to prioritize the factors; This has been computed using the Microsoft Excel Package and represented in Table 5
TABLE V. RELATIVE IMPORTANCE INDEX ANALYSIS
-
TOPSIS
From the questionnaire, the rating of all factors is calculated with the help of TOPSIS.
Sr.
no.
Factors
Relative closeness values
Ranking
1
A time period of the project
0.737655204
1
2
Accident on site
0.673207201
2
3
Neglecting the safety measures
0.665023391
3
4
Improper supervision of work
0.664637318
4
5
Lack of knowledge/ experience
0.659441017
5
6
Not following the construction schedule
0.654188296
6
7
Unavailability of funds
0.651721947
7
8
Mistakes and omissions in the bills
0.640946214
8
9
Delay in payment of progress work
0.637707636
9
10
Slow mobilization of resources
0.634411366
10
11
Material wastage
0.630639124
11
12
Delay of works
0.630239977
12
13
Absence of labour at site
0.618740107
13
14
Lack of proper communications with the subcontractor
0.615070286
14
15
Scope of Work not defined properly
0.607488478
15
16
Drawing is not precise before starting the work
0.60530847
16
17
Shortage of equipment and machinery of the subcontractor
0.596841238
17
18
Decision pending from owner/client
0.582085572
18
19
Regular changes in drawings and design
0.576925583
19
20
Not maintain cash flow in time
0.575013224
20
21
Efficiency in Time management of the subcontractor
0.570901025
21
22
Unviability of machineries
0.570203507
22
23
Payment system
0.570153878
23
24
Shortage of skilled labour with subcontractor
0.569708149
24
25
Variations in Scope of work and changes in specifications.
0.569195429
25
26
Frequent equipment breakdown
0.567477042
26
27
Equipment allocation problem
0.552129696
27
28
Change in cost of resources (labour and material)
0.540628623
28
29
Low labour productivity
0.530710875
29
Sr.
no.
Factors
Relative closeness values
Ranking
1
A time period of the project
0.737655204
1
2
Accident on site
0.673207201
2
3
Neglecting the safety measures
0.665023391
3
4
Improper supervision of work
0.664637318
4
5
Lack of knowledge/ experience
0.659441017
5
6
Not following the construction schedule
0.654188296
6
7
Unavailability of funds
0.651721947
7
8
Mistakes and omissions in the bills
0.640946214
8
9
Delay in payment of progress work
0.637707636
9
10
Slow mobilization of resources
0.634411366
10
11
Material wastage
0.630639124
11
12
Delay of works
0.630239977
12
13
Absence of labour at site
0.618740107
13
14
Lack of proper communications with the subcontractor
0.615070286
14
15
Scope of Work not defined properly
0.607488478
15
16
Drawing is not precise before starting the work
0.60530847
16
17
Shortage of equipment and machinery of the subcontractor
0.596841238
17
18
Decision pending from owner/client
0.582085572
18
19
Regular changes in drawings and design
0.576925583
19
20
Not maintain cash flow in time
0.575013224
20
21
Efficiency in Time management of the subcontractor
0.570901025
21
22
Unviability of machineries
0.570203507
22
23
Payment system
0.570153878
23
24
Shortage of skilled labour with subcontractor
0.569708149
24
25
Variations in Scope of work and changes in specifications.
0.569195429
25
26
Frequent equipment breakdown
0.567477042
26
27
Equipment allocation problem
0.552129696
27
28
Change in cost of resources (labour and material)
0.540628623
28
29
Low labour productivity
0.530710875
29
TABLE VI. RELATIVE IMPORTANCE INDEX ANALYSIS
Sr.
no.
Factors
RII
Ranking
1
A time period of the project
0.91
1
2
Accident on site
0.89
2
3
Neglecting the safety measures
0.885
3
4
Improper supervision of work
0.87
4
5
Lack of knowledge/ experience
0.855
5
6
Not following the construction schedule
0.835
6
7
Unavailability of funds
0.83
7
8
Mistakes and omissions in the bills
0.815
8
9
Delay in payment of progress work
0.81
9
10
Slow mobilization of resources
0.805
10
11
Material wastage
0.8
11
12
Delay of works
0.795
12
13
Absence of labour at site
0.793
13
14
Lack of proper communications with the subcontractor
0.792
14
15
Scope of Work not defined properly
0.791
15
16
Drawing is not precise before starting the work
0.79
16
17
Shortage of equipment and machinery of the subcontractor
0.784
17
18
Decision pending from owner/client
0.782
18
19
Regular changes in drawings and design
0.781
19
20
Not maintain cash flow in time
0.78
20
21
Efficiency in Time management of the subcontractor
0.775
21
22
Unviability of machineries
0.77
22
23
Payment system
0.765
23
24
Shortage of skilled labour with subcontractor
0.76
24
Sr.
no.
Factors
Relative closeness values
Ranking
30
Not following the contractual conditions
0.529168321
30
31
Unavailability of material
0.524026306
31
32
Idle manpower
0.520138225
32
33
Simultaneous involvement of the subcontractor in various projects
0.516494297
33
34
Late involvement of the subcontractor in the project
0.498936229
34
35
Low bid
0.488811485
35
36
Idle material
0.485820652
36
37
Idle machineries
0.463497425
37
38
Shortage in supply of labour, equipment, and spare parts
0.459786721
38
39
Contractual disputes due to poor framing of contract document
0.43140489
39
-
-
CONCLUSION & RECOMMENDATIONS
After studying the literature, the data was collected using the primary (questionnaire) and secondary (literature) methods. The questionnaire was prepared by carrying out a literature study and conducting site visits on residential projects in Pune. The factors causing issues in subcontracting management were identified, and a questionnaire was prepared based on the Likert scale (five-point scale). At first, the reliability of the data collected was found by Cronbach's Alpha Test in SPSS, which was 0.871; hence the data was reliable. Relative Importance Index and TOPSIS ranking of the factors were done to determine the factors that mainly contribute to subcontracting management issues.
The time period of the project: The interest in the on-time performance and on-time payment is vested by all involved parties in the construction process (i.e., builders, operators, suppliers, subcontractors). Because of the high cost of early success, contractors and owners generally need well-planned and often complex schedules. Contractors use completion date, bar chart, and completion schedule percentage to follow up, manage subcontractors and track delays. The main contractor can control the schedule of sub-contractors by developing a system or using advanced technology tools to track reasons for the time variances like Microsoft project, CPM (Critical Path Method), ZOHO Projects, Primavera P6. To enhance coordination and communication with subcontractors, the main contractor can hold evaluation sessions. There should be a penalty clause included in the specialized subcontract agreement for delay and damages so that the subcontractor complete the work on time
Payment provisions: In almost any sub-contract, as in most purchase contracts, there are two simple payments, firstly the advance payment in respect of which the contractor typically makes payment depending on the completion percentage, and secondly the final payment. The contractor usually makes payment after completion and acceptance of the work. Payment disputes constitute a substantial proportion of all disputes over construction in practice.
Usually, for one of three reasons, contractors withhold payment:
-
They claim that the performance of the subcontractor is somehow inadequate.
-
They don't have any funds (in which case the subcontractor is in an adamant position).
-
The owner did not pay the contractor.
A policy "pay if paid" (often referred to as a " pay until paid" clause or a conditional payment clause) requires the ability of the subcontractor after the same payment has been made by the owner to accept a progress payment.
Scope of work: The changing project scope is known as the "scope creep," which means that the project is changing, over and beyond its original intent Managers of all building companies face this challenge every time a client demands it. This Scope creeps many times leads to double or triple the workload of the contractor. The Scope of work is an essential aspect of every subcontract. There must be plenty of time and effort to review the nature of work ensure that all issues and omissions are addressed as far as possible before beginning. Two-way lead times have often been adopted in subcontracts. Two ways to ensure were the primary contractors and subcontractors intending to notify the subcontractor when to commence work and to inform the subcontractor about any modification in the work to prevent disputes on a reasonable basis; For this, a written instruction should invoke the subcontractor's obligation to undertake extra work arising from modifications. Subcontractors can achieve a fair raise in the amount of the subcontract plus overhead percent and profit percent. If the contractor and subcontractor cannot agree on the price change, it shall be appropriate to proceed with and negotiate on prices later, as long as the Contractor, Owner or Architect is not a final price arbiter. If possible, settle a matter; litigation or arbitration may be available.
Safety measures: The main contractor should appoint a safety officer. Promote the proper use of adequate personal protective equipment (PPE): Providing PPE in various sizes and preferences so that workers can select equipment that can give them freedom of mobility, convenience, and fitness. Workers' rewards for safe behaviour: Create exciting activities for the length of time between work crews or workplaces without an injury or OSHA violation by treating yourself to a success award, sports event, or a great meal at the office. Try an awards scheme where employees can receive several recognition points for their safety behaviour, for example, wearing high-visibility clothing, safety lenses, and preparation relevant to security. Penalize inappropriate worker performance: provide a scheme of penalties for employees, including probation or removal of repeated offences or severe violations of their corporation's safety standards; This encourages employees to do what they can to prevent problems that can lead to the first place to accidents. Train and prepare on all job levels to react to accidents: Details about how to contact in the case of an injury, getting immediate assistance and prevention certified, and the like ensures that the injured person is taken care of instantly in a possible way if an accident occurs, in place of the best measures.
Quality of work by subcontractor: Formal procurement standards for subcontractors are necessary. It allows
significant contractors to easily and quickly decide whether the subcontractors are eligible to handle the main contractor. The main contractor understands more about subcontractors by setting up a subcontractor database. It allows main contractors to understand the reliability of subcontractors better. Top management should play a leading role in quality engagement. For the quality strategy, quality policies and practices should be carried out. The subcontractor shall recognize and adopt the quality policies as a standard for work. The poor-quality complaints should be prevented. The owner approves any deal between the general contractor and subcontractor, so Subcontractors should comply and review in compliance with the modifications rendered to the prime contract during the process to comply with the prime contract between the contractor and the project owner.
REFERENCES
-
Adnan Enshassi, Rafiq M. Choudhry, Peter E. Mayer, and Younis Shoman, Safety Performance of Subcontractors in the Palestinian Construction Industry, Journal of Construction in Developing Countries, Vol. 13. 1, 2008.
-
Alinaitwe, H. M., Mwakali, J. A. and Hansson, B. (2007) Factors affecting the Productivity of Building Craftsmen Studies of Uganda. Journal of Civil Engineering and Management ISSN 1392 3730, 13(3), 169 176.
-
Brad C. Parrott, Esq., "Construction Subcontracts: An Exercise in Risk Management"
-
Caroline T W Chan "Decision Support for Subcontractor Selection by Probabilistic Neural Network Model" 2006.
-
Daniel K O., Sergio R. P., and FE Cardoso, (2000) "The role of subcontractors in the competitiveness of building companies and the integration of value chains, information and communication in construction projects."
-
David Arditi, Ranon Chotibhongs. (2005), "Issues in subcontracting practice," Journal of Construction Engineering and Management, ASCE.
-
David. E Gunderson "General Contractors Perceptions of Subcontractors' Competencies and Attributes: A Pacific Northwest Study," 48th ASC Annual International Conference Proceedings, ASC,2012.
-
Francis W.H. Yik, Joseph H.K. Lai, and Jones, P. (2006), "Critical contractual issues of outsourced operation and maintenance service for commercial buildings," International Journal of Service Industry Management, Vol. 17 No. 4, pp. 320-343.
-
Gerald I. Katz, Stone L.L.P., "Contract risk allocation" Contractual risk transfer seminar International Risk Management Institute, Inc.
-
Harold Kerzner, Project Management, New Delhi, CBS Publication and Distributors.
-
Hinze J and Wilson G, (2000), "Moving towards a zero-injury objective. Journal of construction engineering and management", (ASCE).
-
Hseih T, "Impact of subcontracting on-site productivity." Journal of construction engineering and management, 1998.
-
Jill Wells. Construction industries of developing countries." An assessment from two perspectives," 2001.
-
Jimmie Hinze and Andrew Tracey, "The Contractor-Subcontractor Relationship: The Subcontractor's View" Journal of Construction Engineering and Management, Vol. 120, No. 2, June 1994.
-
Kumaraswamy, M. M., & Matthews, J. D. (2000). Improved Subcontractor Selection Employing Partnering Principles. Journal of Management in Engineering, 16(3), 4757.
-
Lew Yoke-Lian, S. Hassim, R. Muniandy, and Law Teik-Hua, "Review of Subcontracting Practice in Construction Industry," IACSIT International Journal of Engineering and Technology, Vol. 4, No. 4, August 2012.
-
Mohd Rosazuwad, Mohamad (2010) The factors and effect of delay in a government construction project (case study in Kuantan). Faculty of Civil Engineering & Earth Resources, University Malaysia Pahang.
-
Ndekugri, I., Braimah, N., & Gameson, R. (2008). Delay Analysis within Construction Contracting Organizations. Journal of Construction Engineering and Management, 134(9), 692700.
-
Othman J. (2002), Household Preferences for Solid Waste Management in Malaysia.
-
Sadi A. Assaf, Sadiq Al-Hejji-22 October 2004-"Causes of Delay in Large Construction Projects."
-
Shash A., Ganiyu A. A. (2010), Factors Affecting Subcontracting Strategy.
-
Subcontractor assessment form of LONG CROSS COMPANY. (Annexure 3).
-
United Nations Industrial Development Organization, "Transfer of Technology in Subcontracting," Component 4, ODG/R.10,27 October 1999.
-
William R. Mincks and Hai Johnston, Construction Jobsite Management Delmar Publishers.
-
http://cpwd.gov.in/Publication/manualvolume2.pdf (Central Public Works Department (CPWD) Works Manual)