
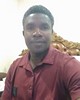
- Open Access
- Authors : Jerry M. Asuo , Barinaadaa T. Lebele-Alawa , Barinyima Nkoi
- Paper ID : IJERTV10IS110149
- Volume & Issue : Volume 10, Issue 11 (November 2021)
- Published (First Online): 03-12-2021
- ISSN (Online) : 2278-0181
- Publisher Name : IJERT
- License:
This work is licensed under a Creative Commons Attribution 4.0 International License
Exergo-Economic Analysis of 180MW Gas Turbine in the Niger Delta
Jerry M. Asuo 1, Barinaadaa T. Lebele-Alawa 2 and Barinyima Nkoi 3
Department of Mechanical Engineering, Rivers State University, Port Harcourt, 5080, Rivers State, Nigeria
Abstract:- Using exergy and exergo-economic techniques, this paper investigates the rate of exergy destruction of a 180MW gas turbine in the Niger Delta (Nigeria). The method entailed simplifying the plant components into control volumes and analyzing each flow using exergy, economic, and exergy cost principles. The combustion chamber had the highest efficiency destruction (79.15 percent) at 114.55MW, while the turbine had the lowest at 15.01MW (10.46 percent). The air compressor has the highest capital investment, operation, and maintenance costs (240.59 $/h), as well as the highest exergo-economic factor (67.78 percent). Lowering the pressure ratio and/or compressor isentropic efficiency can lower the plant's overall cost effectiveness. Exergy destruction in the combustion chamber can be significantly reduced by increasing the turbine inlet temperature or introducing a pre-heater after the compression process. The overall exergy efficiency was 28.28%, with the first law efficiency at 32.27%.
Keywords – Cost, exergy, exergetic efficiency, exergy destruction, exergo-economic, irreversibility, turbine
-
INTRODUCTION
The use of petroleum and other fossil fuels has steadily increased since the invention of the Internal Combustion Engine in the 17th century, and their continued use at the current rate is thought to increase global warming and cause more climate change. The combustion of fossil fuels is responsible for approximately 98 percent of CO2 emissions (Demirbas, 2008). Furthermore, man's pursuit of a higher standard of living, industrialization, and population growth have all put a strain on available fossil energy resources. Gas turbines are more cost-effective. Due to their low capital cost, high power-to-size ratio, high reliability, and flexibility in using a variety of fuels, gas turbines are more economically appealing than other forms of power generation (Raja et al., 2006). They have become one of the most widely used technologies in power generation, and natural gas has become the primary operating fuel associated with their use, due to their numerous advantages over other sources of power generation. With diminishing fossil energy resources, rising energy demands, and rising environmental concerns, it's more important than ever to understand the mechanisms that degrade energy quality (ability to do work) and energy resources, as well as how to improve the efficiencies of existing power plants by utilizing energy more efficiently. The first law of thermodynamics was previously used to evaluate system performance. It is concerned with energy quantity and asserts that energy cannot be created or destroyed. Recently, there has been a growing interest in exergy and exergetic efficiency as a more realistic way of
assessing thermodynamic process performance in terms of energy utilization. Exergy analysis uses thermodynamics'
first and second laws to analyze and provide information to optimize and improve thermodynamic processes. Exergy analysis provides a quantitative and illustrative description of the energy forms' convertibility. It asserts that while energy cannot be destroyed, its quality can be degraded, reducing its ability to do useful work (Obodeh and Ugbokwe, 2017). Exergy analysis allows for the evaluation of energy degradation during a process, entropy degradation, and lost opportunities to do work, and thus provides an alternative approach to power plant improvement. Exergy can be lost because of a process' irreversibilities, and this provides a measure of the system's thermodynamic losses, as well to locate and quantify wasteful energy usage (Wark and Richard, 1988). Exergy analysis gives a clearer picture of a process's true efficiency and is particularly useful for identifying the unit operations where efficiency improvements are most needed. Exergy losses refer to exergy that is lost to the environment, whereas exergy destruction refers to exergy that is lost within the system boundary due to irreversibility (Eke et al., 2018). Several researchers have spent a significant amount of time using energy and exergy to improve existing power plants. Eke et al., 2018 compared the energetic and exergetic performances of individual components of a 220MW power plant and identified each component's deficiencies. The boiler, according to the authors' findings, is the major contributor to overall exergy destruction, with an exergy destruction rate of 87 percent. Increasing the High-Pressure Turbine (HPT) inlet temperature at constant boiler pressure increases the component's exergy efficiency as well as the power plant's second law efficiency, reducing the component's exergy destruction. Osueke et al. (2015) conducted an energy and exergy analysis for the various components of the Sapele steam power plant. According to their findings, the boiler contributes the most energy loss, with 105 KW lost to the environment and only 15.7 KW lost from the condenser system. Their findings also revealed that the boiler system had the highest rate of exergy destruction at 105.9 percent, followed by the turbine and condenser at 86.53 percent and
62 percent, respectively. Kwambai (2005) examines the electricity generation process at a geothermal power plant in Kenya. The results show that Olkaria I Power Plant has a
34.6 percent overall second law of efficiency and a 15 percent overall first law of efficiency. According to the analysis, 6MW of exergy is lost in the separated brine, while 11MW is lost in the steam transmission system. Turbines,
condensers, and the GES system are all found to have significant losses. Lebele-Alawa and Asuo (2013) used Energy and Exergy methods to analyze the performance of a 20MW gas turbine. Their report shows that the combustion chamber contributes to the maximum exergy loss of 38.62 percent, while the second law efficiency was 16.39 percent. The component(s) of the power system responsible for irreversibility or lost work were identified for improvement and applied to improve operational performance using the exergy analysis. The goal of this research was to use exergy and thermo-economics to determine the rate of entropy generation and cost of thermo-economic variables of a gas turbine and to provide information on how to improve and optimize the system based on exergy destruction reduction and wastage.
Figure 2: Control Volume for a Typical System Component
-
MATERIALS AND METHODS
Where
Qcv ,W cv , hin and
hout
are heat supplied, ideal
-
Description of Plant Investigated
Figure 1 shows a schematic diagram of the system under
work, enthalpy at inlet and enthalpy at outlet. The first law efficiency of the system component is thus given as:
investigation. A 180MW single shaft ALSTOM GT-13E2 unit gas turbine power plant located in Afam, Rivers State, Nigeria. A 5-stage turbine and a 21-stage axial compressor
Energydesired
s Energyinput
(3)
installed on the same shaft serve as the primary mechanical components, as does a combustion chamber between the compressor and the turbine. At a rotor speed of 3000 rpm, it has a maximum combustor temperature of 1368K, a pressure
In this study, the exergy of a material stream was simplified
into physical and chemical exergy and an entropy-production flow; For a strea of matter, the total exergy flow total was
expressed as:
ratio of 16:1, and an exhaust flow of 528 kg/s.
total
ke
-
pe
-
ph
-
f
(4)
Where
ke , pe , ph
and
f are kinetic exergy, potential
exergy, physical exergy and chemical (fuel exergy) respectively. At steady state, the effects of kinetic and potential exergy were neglected, and the processes involved are of fixed composition, hence exergy was expressed as the maximum work extracted from the stream as it is brought to
equilibrium with environment P0 ,T0 by physical and
chemical exergy.
Figure 1: Schematic Diagram of a Sigle Shaft Gas Turbine
-
-
Equations and Analysis
The methodology employed consisted of simplifying the plant components into control volumes of energy and exergy flows and analyzing each flow based on first law of thermodynamics and exergy principles. A typical plant component is shown in figure 2 depicting energy and mass flow across the system boundary.
Figure 3: Control Volume for Generalized Exergy Balance
min hin
mout hout
(1)
From figure 2, an exergy balance equation according to Wark
From steady flow energy equation and neglecting influence
and Richards (1988) was employed as state below:
of potential and kinetic energy, equation (1) becomes:
Wcv Qcv out in d
(5)
Qcv min hin W cv mout hout
(2)
in out
Where Qcv , W cv , in , out
and d are
sum of heat supplied, sum of ideal work input, sum of exergy
inflow, sum of exergy outflow and sum of exergy lost within
the system due to irreversibility.
mg ma m f
-
Exergy Analysis
The exergetic efficiency of the ith component was
cc,in cc, f
cc,out
cc,d
(16)
expressed as:
0 0 P3 (17)
cc,out mg p h0 T0 s3 s0 Rg ln
,i
1
i,d
(6)
P0
i,in
P
The overall exergetic efficiency of the entire plant was
T S mg T s 0 s 0 R ln 3
g
g
(18)
expressed according to Martin et al. (2016) as follows:
cc,d 0
0 3 2
P2
W net
(7)
1 cc,d
(19)
cc,out
,cc
cc,in
-
cc, f
The exergetic performance coefficient is an important parameter in exergy analysis because it represents the amount of exergy loss rate per unit of power output and is expressed as the ratio of total exergy destruction to net power output.
Turbine Analysis
From figure 3, the energy input and exergy input/output, exergy destroyed and exergetic efficiency were expressed according to Lebele-Alawa and Asuo, 2013.
d ,total
(8)
Et mg (p h4 )
(20)
W net
0 0 P4
(21)
Plant improvement potential indicates the possibility that
t ,out mg h4 h0 T0 s4 s0 Rg ln
irreversibilities in the plant can be reduced and efficiency improved. The improvement potential of the component was expressed according to (9):
t ,d
P0
0 mg 0 4 3 g
0 mg 0 4 3 g
T S T (s 0 s 0 ) R ln P4
P
(22)
i (1i, ) i,d
(9)
,t
1 t ,d
3
(23)
The efficiency defect is a critical parameter. It was expressed as the ratio of component exergy destruction to rate of exergy input.
t ,in
-
-
Economic Analysis
The cost of the various components of the gas turbine was assessed in terms of investment, operation and
i ,d
i ,in
Compressor Analysis
(10)
maintenance, and fuel cost, and the annualization cost method proposed by Moran and Schuibba (1994) was used in this study. The Purchase equipment cost for the compressor, combustion chamber and turbine were expressed according to
From figure 3, the balance equations for specific ideal work input, exergy input/output, exergy destroyed and exergetic efficiency in the compressor were expressed as
Aliu and Ochornma (2018); Oyedepo et al. (2015).
Compressor Economic Analysis
follows:
PEC
71.1ma
P2 ln P2
(24)
-
ac
0.9
P
P
W ac
ma (p p ) ac,in
(11)
ac 1
1
h h T s 0 s 0 R
P
ln 2
(12)
ac,out ma 2 0
0 2 0
a P
SVac 0.1 PECac
(25)
0
P
PWac PECac (SVac )PWF
(26)
ma T (s0 s0 ) R ln 2
a
a
(13)
ac,d
0 2 1
P1
PWF (1 r)n
,ac
1 ac,d
(14)
Cac PWac CRF
(27)
W ac
Combustion Chamber Analysis
From figure 3, the energy input and exergy input, output
Z ac
Cac
3600 N
(28)
and loses were expressed according to Lebele-Alawa and Asuo, 2013.
Combustion Chamber Economic Analysis
Ecc mg (p p )
(15)
46.08
PEC
ma 1 exp0.018T3 26.4 (29)
cc 0.995 P P
3 2
SVcc 0.1 PECcc
(30)
PWcc PECcc (SVcc )PWF
PWF (1 r)n
Ccc PWcc CRF
(31)
(32)
Zcc
Ccc
3600 N
(33)
Figure 4: Control Volume for Generalized Cost Balance
Turbine Economic Analysis
479.34 P
Compressor Cost Flow Analysis
PEC
mg ln 3 1 exp0.036T3 54.4
(34)
Z
(39)
t 0.92
gt
P4
C 2 C1 C 6 ac
SVt
0.1 PECt
(35)
cac ,in
C 1 C 6
E1 E6
(40)
PWt
PECt
-
(SVt )PWF
(36)
cac,out
C 2 C1
E2 E1
(41)
PWF (1 r)n
cac ,out cac ,in ac c
(42)
Ct PWt CRF
(37)
ac ,in
ac cac,in ac,d
(43)
Zt
Ct
3600 N
(38)
f ac Z
Z ac
ac ac
(44)
Combustion Chamber Cost Flow Analysis
-
-
-
Exergy Cost Flow Analysis
C 3 C 2 C 7 Zcc
(45)
From Figure 4, three sets of non-linear equations were
formulated and solved using Specific-Exergy Costing
c C1 C 6
(46)
(SPECO) as proposed by Benjan et al. (1996) and Lazzareto and Tsatsaronis (2006) to analyze cost flow rates per unit
cc,in
E1 E6
energy of all plant components.
c C 2 C1
(47)
cc,out
E2 E1
cout ,cc cin ,cc cc c
(48)
in ,cc
cc ccc,in cc,d
(49)
fcc Z
Zcc
cc cc
(50)
Turbine Cost Flow Analysis
C 4 C 5 C 6 C 3 Zt
(51)
c C 1 C 6
(52)
t ,in
E1 E6
c C 2 C1
(53)
t ,out
E2 E1
ct ,out ct ,in t c
(54)
t ,in
t ct ,in t ,d
(55)
Z
Z
ft
t
Zt
-
t
(56)
Figure 6. Graph of Exegetic/Thermal Efficiency Vs Turbine Inlet Temperature
-
RESULTS AND DISCUSSIONS
p>A graph of exegetic and thermal efficiency versus ambient temperature is shown in Figure 5. The specific work of the compressor increases as the ambient temperature rises, reducing the amount of flow exergy and exegetic efficiency. Power output, thermal efficiency, air mass flow rate, exergy destroyed, and exergy efficiency all decrease as ambient temperature rises, according to Saleh et al. (2016). Exergy efficiency decreases by 1.4 percent as the ambient temperature rises from 300 K to 302 K, while thermal efficiency decreases by about 0.6 percent for the same range of ambient temperature increase, according to Figure 4.
Figure 5: Graph of Exergetic/Thermal Efficiency Vs Ambient Temperature
A graph of exegetic/thermal efficiency versus turbine inlet temperature is shown in Figure 6. When the turbine inlet temperature is raised from 1320K to 1340K, the exegetic and thermal efficiencies both increase by 0.15 percent. Rahman et al. (2011) found that as the turbine inlet temperature rises, the thermal efficiency rises linearly until a certain compression ratio is reached. The gas turbine specific work increases as TIT increases, while the compressor specific work remains constant. As a result, cycle efficiency and exergetic efficiency increase.
Exergy destruction/plant improvement potential is plotted against ambient temperature in Figure 7 More work is required as the ambient temperature rises during compression, resulting in an increase in irreversibilities and exergy destruction. According to Arvind et al. (2013), as ambient temperature rises, more fuel is required in the combustion chamber, resulting in a faster rate of exergy destruction. Figure 7 shows that as ambient temperature rises from 299 K to 302 K, exergy destruction increases by 2.87 percent while plant improvement potential increases by 3.4 percent.
Figure 7: Graph of Exergy Destruction/PIP Vs Ambient Temperature
Rate of exergy destruction and plant improvement potential against turbine inlet temperature is shown in figure
8. As turbine inlet temperature increase from 1320 K to 1340 K total exergy destruction increase by 6.65 percent while for the same range of turbine inlet temperature increase, plant improvement potential increases by 4.72 percent
Figure 8: Graph of Exergy Destruction/PIP Vs Turbine Inlet Temperature
inlet temperature rises by 1.59 percent from 1322 K to 1343
K. As the temperature of the air rises, more work is required during the compression process, which increases the rate of exergy destruction, resulting in a decrease in compressor work input and an increase in efficiency defect. According to Oydedepo et al. (2015), as the temperature of the turbine inlet rises, the rate of entropy generation decreases while network power output increases, resulting in a reduction in efficiency defect. Figure 12 depicts the contribution of each system component to the efficiency defect, with the combustion chamber contributing the most (21.24MW).
Figure 9 depicts the relationship between ambient and turbine inlet temperature against exergy performance coefficient. With a rise in turbine inlet temperature, rate of entropy generation decreases, and network power output rises. Thamir et al. (2016) found that increasing the turbine inlet temperature leads to a linear increase in power output because the average temperature at which heat is supplied rises as the inlet temperature rises. As shown in figure 8, the exergy performance coefficient decreases by 3.22 percent as the turbine's inlet temperature rises from 1319 K to 1337 K. The rate of entropy generation and irreversibilities increases as ambient temperature rises, resulting in a reduction in power output and, as a result, an increase in plant improvement potential. Figure 9 shows how plant improvement potential increases by 4.2 percent as ambient temperature rises from 300.8 K to 301 K. Figure 11 is a representation of the contributions of each system component to overall exergy destruction. The combustion chamber with
-
percent has the highest rate of exergy destruction. This was attributed to the chemical reaction as well as the large temperature difference between the burners and the working fluid (Oyedepo et al., 2015).
Figure 9: Graph of Ambient/Turbine Inlet Temperature Vs Performance Coefficient
Figure 10 depicts ambient/turbine inlet temperature versus efficiency defect. When the air ambient temperature drops from 33.5 K to 32 K, the efficiency defect increases by 4.47 percent, while it decreases by 4.69 percent when the turbine
Figure 10: Graph of Ambient/Turbine inlet temperature Vs Efficiency Defect
Figure 11: Exergy Destroyed and Exergetic Efficiency for System Components
Figure 12: Improvement Potential and Efficiency Defect for System Components
Component
Z ($/h)
cin ($/h)
cout ($/h)
d ($/h)
(%)
f (%)
Compressor
240.59
7.56
8.67
113.85
14.68
67.78
Combustion Chamber
11.81
5.58
7.14
639.19
27.87
1.81
Turbine
83.91
7.14
7.56
107.17
5.88
43.72
Component
Z ($/h)
cin ($/h)
cout ($/h)
d ($/h)
(%)
f (%)
Compressor
240.59
7.56
8.67
113.85
14.68
67.78
Combustion Chamber
11.81
5.58
7.14
639.19
27.87
1.81
Turbine
83.91
7.14
7.56
107.17
5.88
43.72
Table 1: Summary of thermo-economic variables for each component
Table 1 summarizes the values of exergo-economic variables for the plant's components. The combustion chamber has the highest exergy loss among the plant's components.
-
-
CONCLUSION
The compressor, combustion chamber, and turbine each contributed 10.39%, 79.15%, and 10.46% of the total exergy destroyed, respectively. The air compressor has the highest capital investment, operation and maintenance costs, and exergo-economic factor (f). The overall cost effectiveness of the plant, according to Bejan et al. (1996), is determined by the capital investment, operation, and maintenance costs of the air compressor, which can be reduced by lowering the pressure ratio and/or compressor isentropic efficiency. The combustion chamber's high value of the relative cost index (27.87%) and low value of the exergo-economic factor (1.81%) indicate the high rate of exergy destruction associated with this component. By increasing the compressor outlet temperature and turbine inlet temperature, the cost of exergy destruction of the combustion chamber and other components is reduced. This, however, results in a slight increase in capital investment, operation, and maintenance costs. Increased turbine inlet temperature improves turbine exergetic efficiency and net power output while lowering combustion chamber exergy destruction. However, lowering any of the turbine inlet temperature, P3/P4 value, or turbine isentropic efficiency is recommended to lower the capital investment, operation, and maintenance cost of the gas turbine. By installing a preheater after the compression process, the exergy destruction within the combustion chamber can be reduced as well. This will increase the exergetic efficiency of the combustion chamber and reduce irreversibilites.
ACKNOWLEDGEMENT
The authors would like to express their gratitude to First Independent Power Limited (FIPL), Afam, for providing the necessary materials for this study.
REFERENCES
-
Aliu, S.A., & Ochornma, P.I. (2018). Exergoeconomic Analysis of Ihovbor Gas Power Plant. Nigerian Journal of Technology, 37(4), 927-935.
-
Eke, M.N., Onyejekwe, D.C., Iloeje. O.C., Ezekwe, C.I., & Akpan, P.U. (2018). Energy and Exergy Analysis of a 220MW Power Plant. Nigerian Journal of Technology, 37(1), 115- 123.
-
Kwambai, B.C. (2005). Exergy Analysis of Olkaria I Geothermal Power Plant, Kenya. A Report on the Geothermal Training Programme, United Nation University. Retrieved:
http:// www.os.is/gogn/Unu-gtp-report/UNU-GTP-2005-05. pd.
-
Lazzaretto, A., & Tsatsaronis, G. (2006). SPECO: A Systematic and General Methodology for Calculating Efficiencies and Costs in Thermal Systems. Energy,32, 1257-1289.
-
Lebele-Alawa, B.T. & Asuo, J.M. (2013). Performance Analysis of 20MW Gas Turbine Power Plant by Energy and Exergy Methods. International Journal of Applied Science and Technology, 18(1-2), 20-26.
-
Martin, A., Adhy, P., Miswandi, M. & Iwan, K. (2016). Exergy Analysis of Gas Turbine Power Plant 20MW in Perkanbaru- Indonesia. International Journal of Technology, 7(5), 921-927.
-
Moran, M. J. & Schiubba, E. (1994) Exergy Analysis: Principles and Practice. Journal of Engineering Gas Turbines Power, 116(2), 285-290.
-
Obodeh, O. & Ugbokew, P.E. (2017). Optimal Operating Parameters of 100MW Delta IV Ughelli Gas Turbine Power Plant. International Journal of Energy and Power Engineering, 6(5), 68-74.
-
Osueke, C.O., Onokwai, A.O., & Adeoye, A.O. (2015). Energy and Exergy Analysis of a 75MW Steam Power Plant in Sapele (Nigeria). International Journal of Innovative Research in Advanced Engineering, 2(6), 2349-2163.
-
Oyedepo, S.O., Richard, O.F., Samuel, S. A. & Mahbub, A. (2015). Thermo-economic and Thermo-environomic Modelling and Analysis of Selected Gas Turbine Power Plants in Nigeria. Jurnal of Science and Engineering, 3(5), 423-442.
-
Rahman, M.M., Thamir, K.I., Kadirgama, K. & Bakar, R.A. (2011). Influence of Operation Conditions and Ambient Temperature on Performance of Gas Turbine Power Plant. Journal of Advanced Material Research, 189(193), 3007-3013.
-
Raja, A. K., Srivastava, A. P., & Dwivedi, M., (2006). Power Plant Engineering. Delhi: New Age International Publications.
-
Saleh, S. M, Ali, K., Omid, M. & Somchai W. (2016). Second Law Analysis of a Nonofluid-Based Solar Collector Using Experimental Data. Journal of Thermal Analysis and Calorimetry, 126, 617-625.
-
Thamir, K. I., Rahman, M. M., Obed, M. A., Firdaus,
B.& Rizalman, M. (2016). Optimum Performance Enhancing Strategies of the Gas Turbine Based on the Effective Temperatures. Journal of Thermal Engineering and Energy Conversion, 30, 1-9.
-
Wark, K. & Richards, D.E. (1998). Thermodynamics (6th ed.). London: Pearson Publishing.
NOMENCLATURE
Symbols
T Temperature (K)
s 0
s 0
-
Arvind, T., Mohd, M.H. & Mohd, I. (2013). Effect of ambient
temperature on the performance of a combined cycle power
Specific entropy (kJ/kg K)
plant. Transactions-Canadian Society of Mechanical Engineers,
37(4), 1177-1188.
-
Bejan, A., Tsatsaronis G., & Moran M. (1996). Thermal Design and Optimization, John Wiley & Sons, Inc. USA.
-
Demirbas, A. (2008). Carbon Dioxide Emission and Carbonation Sensors Turkey. Energy Sources, Part A, 30, 70-78.
h Specific enthalpy (kJ/kg)
m Mass flow rate (kg/s)
R Gas constant (kJ/kg K)
Exergetic efficiency
Q Heat supply (kJ/kg)
th Thermal efficiency
Relative cost difference
W ac
W net
Compressor ideal work (kJ/kg)
Power output (kJ/kg)
Exergo-economic factor
Cost of exergy destruction
Maintenance factor
P Pressure (bar)
PEC Purchase equipment cost ($)
SV Salvage value ($)
PW Present worth ($) CRF Capital recovery factor C Annualized cost ($/yr)
C Cost rate ($/h)
c Annualized cost ($/yr
Z Total capital investment, operation, and maintenance cost ($/h)
n Total operating period (yr)
N Number of running hours (h)
Greek Symbols
Exergy (kJ/kg)
Efficiency defect
Exergetic performance coefficient
Plant improvement potential
Subscript
-
Compressor inlet condition
-
Compressor outlet and combustion chamber inlet condition
-
Combustion chamber outlet and turbine inlet condition
-
Turbine outlet condition
in Inflows
out Outflows
ac Input/output from compressor
cc Input/output from combustion chamber
t Input/output from turbine
d Destruction
f Fuel
a Air
g Gas
cv Control volume
i Component
0 Reference condition
Abbreviations and Notations
TIT Turbine inlet temperature
HPT High Pressure turbine
PIP Plant improvement potential
Appendix A: Summary of Average Operating Data for 180MW ALSTOM GT13-E2 Gas Turbine Power Plant (Source: FIPL, 2018)
Parameter |
Value |
Unit |
Compressor inlet temperature, T1 |
27.73 |
0C |
Compressor inlet pressure, P1 |
1.008 |
Bar |
Compressor outlet temperature, T2 |
389.36 |
0C |
Compressor outlet pressure, P2 |
11.75 |
Bar |
Air mass flow rate, ma |
487.76 |
kg/s |
Fuel gas (natural gas) mass flow rate, mf |
7.60 |
kg/s |
Turbine inlet temperature, T3 |
1040.65 |
0C |
Turbine outlet temperature, T4 |
508.38 |
0C |
Power output |
116.38 |
MW |