
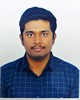
- Open Access
- Authors : V. Naveen
- Paper ID : IJERTV10IS110170
- Volume & Issue : Volume 10, Issue 11 (November 2021)
- Published (First Online): 03-12-2021
- ISSN (Online) : 2278-0181
- Publisher Name : IJERT
- License:
This work is licensed under a Creative Commons Attribution 4.0 International License
Evaluation of Braking Performance of Disc Brake Rotor with different Pillar Ventilation Structures
V Naveen
B. Tech. Mechanical Engineering, Karunya Institute of Technology and Sciences,
Coimbatore, India.
Abstract The aim of this study was to analyze the structural integrity and heat dissipation characteristics of disc brake rotor with different pillar ventilation structures. In case of a single stop braking scenario, the entire kinetic energy of the vehicle gets converted into an equivalent amount of thermal energy. Under the heaviest of the braking applications, the brake rotor must be very efficient in dissipating the heat it gathers. Modern disc brake rotors with suitable material properties are necessary to improve the cooling performance of the braking system. SOLIDWORKS 2020 was used to model the disc brake rotors and the finite element analysis was conducted using ANSYS 2020 R1. Static structural analysis was performed to evaluate the total deformation and equivalent stress. Static thermal analysis was performed to evaluate the temperature distribution and heat dissipation capacity of each type of disc brake rotor. The results give a detailed description of how the brake performance varies with the structure.
Keywords ANSYS; Disc Brake Rotor Design; Pillar Venting Technology; Aluminium Metal Matrix Composite; FEA; Thermo- Mechanical analysis
pillars sandwiched between two discs manages to create air circulation inside the ventilation chamber, which allows for greater heat removal. The pillars are placed in such a way as to create a good barrier against formation and propagation of cracks. This allows the heat generated by the contact surfaces to escape out easily by radiation. The only drawback of a vented disc is that there is a slight increase in weight of the disc but improving the cooling performance of the system. This type of disc brake rotor is designed to achieve the optimum benefit from the dynamic flow of air. Table I shows the different variations in the pillar vented brake rotor design.
Sl. No |
Types of Pillar vented disc brake rotor |
|
Type |
Advantages |
|
1 |
Diamond and Tear Drop Pillared |
Better heat dissipation |
2 |
Star Pillared |
Improved resistance to cracks |
3 |
T-Pillared |
Inhibits ingression of foreign particles |
4 |
Circular Pillared |
Uniform cooling |
Sl. No |
Types of Pillar vented disc brake rotor |
|
Type |
Advantages |
|
1 |
Diamond and Tear Drop Pillared |
Better heat dissipation |
2 |
Star Pillared |
Improved resistance to cracks |
3 |
T-Pillared |
Inhibits ingression of foreign particles |
4 |
Circular Pillared |
Uniform cooling |
TABLE I. TYPES AND ADVANTAGES OF EACH PILLAR DESIGN
-
INTRODUCTION
Braking system is the most prominent component of any automobile in terms of safety and reliability. They must be engineered with utmost attention to make them structurally strong, light in weight, durable and dissipate the generated heat effectively. The material of the brakes should be carefully selected so that it satisfies the sole purpose. The brake rotor must be resistant to distortion, corrosion, cracks, wear, fading, warping and ingression of foreign particles. The principle used by every brake is friction. Friction helps in converting the kinetic energy into heat energy thus effectively reducing the velocity of the car. The braking system incorporates a stationary part which when comes in contact with a moving one develops friction. In case of disc brakes, when the brake pedal is pressed, brake fluid is forced into the caliper moving the piston and brake pads against the rotor. The clamping force applied by the brake pads against the disc rotor creates the necessary friction to stop the spinning of the rotor. [3] Disc brakes are extensively used in all varieties of cars and two wheelers. The frictional surfaces of the disc brakes are exposed to atmospheric air at all times thus enabling it to reject the generated heat quickly than the other types of brakes.
There are different types of disc brake rotors such as flat brake, vented, drilled, slotted or grooved, dimpled and waved. The vented brake disc rotors are the best solution to increase the heat exchange surface with the air, with appropriate width of ventilation channels and efficient ventilation shapes. In Pillar Venting Technology, the shape and distribution of
-
Types of Pillar vented Disc Brake Rotors
Diamond and tear drop pillared structure of ventilation have the capability of keeping the rotors cool even during the heaviest of braking applications which minimizes the risk of brake fade. The cooling efficiency of this design increases by up to 20% when compared with conventional ventilated disc brake rotors. The diamond and tear drop patterned pillars are evenly spread across the disc face and make the rotor stronger, more stable and more consistent in operation. The increased surface area results in greater heat dissipation.
Fig. 1. Section View of Diamond and Tear Drop Pillared Brake Rotor
Star pillar ventilation employs star-shaped pillars to disperse the heat better, reducing the risk of thermal shock of the disc and ultimately guaranteeing longer pad life. The type of disc brake rotor offers enhanced resistance to thermal cracks.
Fig. 2. Section View of Star Pillared Brake Rotor
T-Pillar ventilation employs T-shaped pillars near the outer diameter of the disc brake rotor to avoid particles infiltrating the ventilation chamber of the rotors.
Fig. 3. Section View of T-Pillared Brake Rotor
Circular Pillar ventilation structure enables uniform velocity and pressure distribution around the pillars. The uniform velocity distribution will result in even cooling of pillars. The uniform pressure distribution of circular pillars helps in uniform cooling of rotor pillars and more uniform distribution of mass flow around the pillars.
Fig. 4. Section View of Circular Pillared Brake Rotor
-
Problems with other disc brake rotors
In Flat disc rotors, the surface area of contact with the brake pads are maximum and so it has a better braking power. The disadvantage of this type of rotor is that during braking the built-up gas finds it difficult to escape out which
ultimately causes brake fade and pad glazing. At times the disc tends to warp and causes the rotor to wear when excessive heat generated isnt dissipated effectively.
In Drilled disc rotors, the overall surface area increases due to the presence of drilled holes thus increasing its heat dissipation capability. [2] The problem of trapping of built-up gas between the rotor and the pads doesnt occur and also the drilled holes make it easy for water to move away from the rotor surface during rainy seasons. The only problem with the drilled disc rotor is that the drilled holes tend to weaken the rotor which can make the rotor susceptible to cracks during stressful driving conditions.
Adding slots or grooves to a disc rotor works in a similar way as drilled disc rotors which remove the excess heat, gas and particles from the friction surface thus allowing better braking. The grooves on the disc radiate out from the center of the disc at a particular angle to vent out the waste away with the rotation of the disc. The main problem occurring in grooved disc rotors is that they have a tendency to be noisier when the brakes are applied because the groves scrub the pads. They tend to wear down the brake pads quickly.
-
Material Selection
The desirable properties of any automotive disc brake rotor must include optimum hardness, stiffness, wear resistance, coefficient of thermal expansion, thermal conductivity and friction properties. The most commonly used material for disc brake rotor is particularly gray cast iron because of its good friction properties, strength, low cost, relative ease of manufacturing and thermal stability. This material has been the choice for almost all automotive disc brakes.
The best possible alternative to gray cast iron is Aluminium metal matrix composites (AMMC) with Silicon carbide (SiC) reinforcement. SiC increases the strength and hardness of AMMC and also improves the thermal shock resistance of the material. Considerable weight reduction is possible with this material. However, this material is costlier than cast iron. The thermal conductivity of Al-SiC is about two to three times higher than cast iron. For an equivalent cast iron disc, the weight of the disc made of Al-SiC is very much lower. The material chosen for study is Al-25%SiC and its properties are listed in the table II below.
TABLE II. MATERIAL PROPERTIES
Properties
Material
Al-25%SiC
Youngs Modulus, E
115 Gpa
Poissons Ratio,
0.27
Shear Modulus, G
452.75 Gpa
Mass Density,
2800 kg/m3
Yield Strength, y
178 Mpa
Tensile Strength, T
186.21 Mpa
Compressive Strength
390 Mpa
Coefficient of Friction,
0.4
Thermal Conductivity
145 W/mK
Coefficient of thermal expansion
1.5 x 10-5 K-1
Specific Heat Capacity
0.919 kJ/kgK
Some of the other materials used in automotive disc brake rotor manufacturing include Galvanized cast iron, Titanium
alloys like Ti-6Al-4V and Ti-C reinforced composite (TMC) and ceramic and carbon-carbon composites. [2] Carbon fibre reinforced silicon carbide composites like C/SiC and C/C-SiC used in high performance vehicles can withstand high temperatures and possess great strength.
-
-
METHODOLOGY
In this study, a single stop braking scenario is taken into consideration in which the vehicle is traveling at a speed of 120 km/hr (33.33 m/s) and is brought to rest by the application of brakes. This scenario is analyzed for each type of disc brake rotor by using static structural and static thermal analysis. [2] The specifications of the vehicle chosen for study is given in below table III.
TABLE III. VEHICLE SPECIFICATIONS
Sl. No
Light weight commercial vehicle
Parameters
Magnitude
1
Mass of the vehicle, M (kg)
1400
2
Velocity of the vehicle, V (km/hr, m/s)
120, 33.33
3
Force applied on the brake pedal (N)
350
4
Pedal ratio
5:1
5
Pedal Effort (N)
1750
6
Master Cylinder Bore Diameter (mm)
25
7
Disc Effective Radius (mm)
110
8
Caliper Piston Diameter, DP (mm)
44
9
Friction between Rotor and Pad
0.4
10
Friction between Road and Tyre
0.7
11
Wheel Diameter, DR (mm/in)
406.4/16
12
Radius of Tire, RT (mm)
310.45
The methodology followed for the evaluation of braking performance includes:
-
Design of Disc Brake Rotor
-
Analysis of disc brake rotors
-
Static Structural Analysis
-
Static Thermal Analysis
-
-
Evaluating the results obtained from the analysis
-
Comparing the results of each rotor and selecting the best suitable one for manufacturing.
-
Design of disc brake rotor
The design of pillar ventilated disc brake rotors is done using SOLIDWORKS 2020 according to standard dimensions. The only variation in each rotor design is the structure of the pillars. All other dimensions arent altered so as to perform a best comparison between the disc brake rotors. The magnitude of outer diameter of the rotor determines how fast the rotor moves through the pads, thereby generating the necessary friction for a better braking power. More the surface area of the disc, more is the heat dissipation. The maximum temperature attained during braking is determined by the thickness of the rotor. The effective radius and the thickness of the rotors are kept same to avoid the changes in the braking torque. The specifications of the brake rotor are provided in the below table IV.
TABLE IV. BRAKE ROTOR SPECIFICATIONS
Sl. No
Rotor Dimensions
Specification
Value
1
Inner Diameter (mm)
160
2
Outer Diameter (mm)
280
3
Height (mm)
56
4
Nominal Thickness (mm)
30
5
Minimum Thickness (mm)
10
6
Number of Pillar elements
108
7
Hub Register (mm)
68
8
Bolt Circle (mm)
105
9
Bolt Bore (mm)
15.3
10
Weight (kg)
2.95
Fig. 5. Front-View Dimensions of Disc Brake Rotor
Fig. 6. Side View Dimensions of Disc Brake Rotor
-
Numerical Calculations to find out heat flux
-
Kinetic Energy of the vehicle:
K.E = (M*V2) / 2 = (1400 * 33.332) / 2
= 777622.23 J
-
Stopping distance of the vehicle: Maximum frictional force, F = *M*g
= 0.7*1400*9.81
= 9613.8 N
Considering the coefficient of friction () for all materials as 0.7
Deceleration of the vehicle, a = F/M = 9613.8/1400
= 6.86 m/s2
Time taken to stop the vehicle, t = V/a = 33.33/6.86
= 4.85 s
Maximum speed attained by the vehicle is 33.33 m/s. So, the distance travelled by the vehicle in 4.85 s is
161.65 m.
Now, due to reflex delay the reaction time of the driver to apply brakes is considered as 1.5 seconds,
Total stopping distance, Sd = (V*reaction time) +
(V2/(2**g))
= (33.33*1.5) + (33.332/ (2*0.7*9.81))
Angular velocity, = (2**N)
= (2*3.14*1025.73)/60
= 107.35 rad/s
f) Heat flux:
The heat generated when applying braking action on the disc brake = Kinetic eergy [3]
Hg = Kinetic energy = 777622.23 J
On converting the kinetic energy for 4.85 seconds, the power produced will be,
Sd = 131 m
-
Braking torque on the wheel:
Braking force in other words is also known as braking power of the vehicle.
The following calculations below tells the exact force required to stop the vehicle within the minimum stopping distance or minimum stopping time. [4]
Tangential braking force, Fb = K.E/Sd
= 777622.23/131
= 5936.04 N
Tangential force on each wheel, Ft = Fb/4
= 4883.44/4
= 1484.01 N
Braking torque on wheel, Tw = Ft * R
= 1484.01*0.31045
= 460.71 Nm
-
Clamping force:
R and r corresponds to the radius of the tire and radius of disc brake rotor respectively.
Effective rotor radius, Reff = r – (Dp/2)
= 0.140 (0.044/2)
= 0.118 m
Braking torque on disc, Tb = Tw*(R/r)
= 460.71*(0.31045/0.140)
= 1021.62 Nm
Clamping force, C = Tb / (2**Reff)
= 1021.62 / (2*0.4*0.118)
= 10822.31 N
-
Angular velocity of the rotor:
The maximum speed at which the vehicle is traveling is 120 km/hr or 33.33 m/s.
Velocity, V = *D*N
33.33 = 3.14*0.6209*N
N = 17.09 rps or 1025.73 rpm
P = KE/t = 777622.23/4.85 = 160334.48 W
The dynamic weight transfer during braking on the front and rear axle is 60:40 percent of the total vehicle weight respectively. [2]
P = (160334.48*0.6)/2 = 48100.34 W
So, the power on each front rotor will be, P = 48100.34/2 = 24050.17 W
Heat flux, q = (P/t)/A
where, A = 2*(/4) *((Dr)2 – (Dr Dp)2)
= 2*3.14*((0.2802 – (0.280 0.044)2)
= 0.1425 m2
Therefore, Heat flux, q = (24050.17/4.85)/0.1425
= 35 kW/m2
-
-
Geometry
The CAD model of the disc brake rotor designed using SOLIDWORKS 2020 is imported into ANSYS workbench. The geometry of the rotor is sliced into three parts to easily differentiate the area of the disc in contact with the brake pads. The area in green is where the brake pads come in contact with the disc upon application of the brake.
Fig. 7. Sliced geometry
The mass of each rotor varies due to different types of pillar structures taken into consideration.
TABLE V. MASS PROPERTY
Type of disc brake rotor
Mass
Diamond and Tear drop pillared
2.9545 kg
Star pillared
2.9591 kg
T-pillared
2.9552 kg
Circular pillared
2.8953 kg
-
Meshing
Finite element analysis consists of the following steps: [4]
-
Preprocessing
-
Discretization
-
Apply constraints
-
-
Solving
-
Postprocessing
The foremost step in FEA preprocessing is the discretization. Discretization is the process of dividing up the model into smaller number of elements consisting of nodes. The processing phase solves equations for these nodes and obtains results. Discretization is done using the meshing. It is a very important part of an analysis which can determine the efficiency and effectiveness of an analysis. The accuracy of the results depends on the density of the meshing. The details of the meshing done on the disc brake rotor is shown in below figures.
Fig. 8. Details of Mesh
The mesh resolution is a scale varying from 0 (Coarse mesh) to 7 (Fine Mesh). The resolution has been set as 4. The span angle center has been set to medium for this model. Span angle center is a feature for curvature based local refinement of mesh. In the curved regions, the boundaries of the mesh will be subdivided until individual element span an angle between 75 and 24 degrees. Tetrahedral element meshing is preferred because the model consists of intricate geometries.
Fig. 9. Details of Mesh method
Fig. 10. Details of Sizing
Fig. 11. Meshed Model
-
-
Boundary Conditions
The boundary conditions applied on the model are given below.
-
Clamping force, C = 10822.31 N
-
Moment, M = 224 Nm
-
Rotational velocity, = 107.65 rad/s
-
Heat flux, q = 35 kW/m2
-
Convection (Heat transfer coefficient) h = 80 W/m2ºC
-
Ambient temperature = 25ºC
The regions where the boundary conditions are applied on the model are shown in the below figures. The results obtained from the static structural and static thermal analysis are purely dependent on the applied boundary conditions. The boundary conditions applied are same for all the disc brake rotors.
Fig. 12. Boundary Conditions for Static Structural Analysis
On the basis of the calculations performed, the clamping force of 18546 N is applied on both contact faces of the rotor. Braking torque in the form of moment is applied on the rotor. The magnitude of braking torque (T) was derived using the formula P = T, where P is the power on each front rotor in watts (W) and is the angular velocity in rad/s. The representation of torque is in the form of moment. The rotational velocity has also been imparted to the whole model.
Fig. 13. Boundary conditions for Static Thermal Analysis
The boundary conditions for static thermal analysis have been applied as shown in the above Fig. 13. All the surfaces of the disc brake rotor are subjected to forced convective heat transfer because it is exposed to the atmosphere for heat dissipation. [1] The faces where the brake pads are in contact with the disc is the region where radiation occurs predominantly. The ambient temperature is considered as 25ºC.
Fig. 15. Equivalent Stress Diamond and Tear drop pillared rotor
Fig. 16. Temperature distribution – Diamond and Tear drop pillared rotor
-
-
RESULTS
The next step in the FEA is to evaluate the model for total deformation, equivalent (von-Mises) stress, temperature distribution and total heat flux.
-
Diamond and tear drop pillar ventilated brake rotor
Fig. 14. Total deformation Diamond and Tear drop pillared rotor
Fig. 17. Total Heat Flux – Diamond and Tear drop pillared rotor
-
Star pillar ventilated brake rotor
Fig. 18. Total deformation Star pillared rotor
Fig. 19. Equivalent Stress Star pillared rotor
Fig. 20. Temperature distribution – Star pillared rotor
Fig. 21. Total Heat Flux Star pillared rotor
-
T-pillar ventilated brake rotor
Fig. 22. Total deformation T-pillared rotor
Fig. 23. Equivalent Stress T-pillared rotor
Fig. 24. Temperature distribution T-pillared rotor
Fig. 25. Total Heat Flux T-pillared rotor
-
Circular pillar ventilated brake rotor
Fig. 26. Total deformation Circular pillared rotor
Fig. 27. Equivalent Stress Circular pillared rotor
Fig. 28. Temperature distribution Circular pillared rotor
Fig. 29. Total Heat Flux Circular pillared rotor
The results obtained through the analysis are summarized in the below table VI.
TABLE VI. SUMMARIZED ANALYSIS RESULTS
Type of Disc brake rotor
Static Structural analysis
Static Thermal analysis
Total Deformation (mm)
Equivalent Stress (Mpa)
Temperature (ºC)
Total Heat Flux (W/m2)
Diamond and Tear drop pillared
0.022805
41.12
94.752
1.4805e5
Star pillared
0.022868
43.23
95.046
1.4531e5
T-pillared
0.022878
41.61
95.005
1.3712e5
p>Circular pillared 0.022856
42.88
98.013
1.0447e5
Based on the results it is clear that the variations in pillar ventilated structures have an impact in the braking performance of the vehicle. Due to the changes in surface area of each disc brake rotor, it is observed that the heat dissipation capabilities are different for each type. The maximum deformation occurred in the regions close to the circumference of the disc brake rotor. The fixed support of the rotor is subjected to the maximum equivalent (von-Mises) stress. The least temperature is observed at the fixed support. It can be observed that the diamond and tear drop pillared rotor is said
to exhibit the best heat dissipation as compared to the other rotors while maintaining its structural integrity.
-
-
DISCUSSION
In the static structural analysis, on applying a clamping force of 10822.31 N, maximum total deformation of magnitude 0.022878 mm is observed in case of T-pillared disc brake rotor. Both the total deformation and equivalent (von-Mises) stress is minimum for diamond and tear drop pillared rotor.
In the static structural analysis, on applying a clamping force of 10822.31 N, maximum total deformation of magnitude 0.022878 mm is observed in case of T-pillared disc brake rotor. Both the total deformation and equivalent (von-Mises) stress is minimum for diamond and tear drop pillared rotor. The maximum equivalent stress of magnitude 43.23 Mpa is observed in the disc brake rotor with star pillars. In static thermal analysis, the heat generated should be dissipated at a faster rate. On comparing all the disc brake rotors, the rotor with diamond and tear drop pillars generates the least temperature of 94.752 ºC and the highest total heat flux of 1.4805e5 W/m2. Higher the total surface area of the disc brake rotor, higher will be the heat transfer to the atmosphere and lesser will be the heat generated in the rotor. The heat dissipation capability and temperature distribution in the diamond and tear drop pillar ventilated rotor is better than any other type of rotors. Hence, the rotors with this type of pillars have better braking performance when compared with the star, T, circular pillared disc brake rotors.
-
CONCLUSION
The design calculations to find out the clamping force on the disc brake rotor and heat flux were performed. Based on the calculations, FEA analysis was performed considering four different types of pillar ventilated discs with similar boundary conditions and material. Among the four disc brake rotors, the rotor offering the best braking performance is finally identified. It is concluded from this study that the braking performance is purely dependent on the material of construction and the geometry of the rotor.
-
FUTURE SCOPE
This paper presents the advantages and disadvantages of each type of pillar ventilated disc brake rotor. The braking performance of the disc brake rotor can be further improved by altering the pillar shapes, arrangement of the pillars, dimensions and so on. The rotor can also be tested for its performance using different cost-effective materials. The alteration can be done in such a way that the pillar ventilated rotor can be manufactured easily.
REFERENCES
- [1] Ali Belhocine, Mostefa Bouchetara, Thermal analysis of solid brake disc, Elsevier, Applied Thermal Engineering 32 (2012)59- 67, 2012. doi.org/10.1016/j.applthermaleng.2011.08.029.
-
Atharva Kulkarni, Rohan Mahale, Impact of Design Factors of Disc Brake Rotor on Braking Performance, IJERT Vol. 9 Issue 06, June 2020, ISSN: 2278-0181.
-
Amrish PN (2016) Computer Aided Design and Analysis of Disc Brake Rotors. Adv Automob Eng 5: 144. doi: 10.4172/2167- 7670.1000144
-
Praharsha Gurram, Shravan Anand Komakula, G. Vinod Kumar, Design and Analysis of Vented Disc Brake Rotor, International Journal of Applied Engineering Research ISSN 0973-4562 Volume 14, Number 9 (2019) pp. 2228-2233