
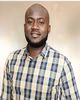
- Open Access
- Authors : Christian N. Kiyanga , Terence Malama , Kondwani Simukonda
- Paper ID : IJERTV10IS110159
- Volume & Issue : Volume 10, Issue 11 (November 2021)
- Published (First Online): 04-12-2021
- ISSN (Online) : 2278-0181
- Publisher Name : IJERT
- License:
This work is licensed under a Creative Commons Attribution 4.0 International License
Investigation into the Effects of Daily Planning and Scheduling in Electrical Engineering within Mining Companies, case of Anvil Mining Congo SA
Christian N. Kiyanga
Department of Agricultural Engineering, School of Engineering, University of Zambia, Lusaka, Zambia
Terence Malama
Kondwani Simukonda
Department of Agricultural Engineering, School of Engineering, University of Zambia, Lusaka, Zambia
Department of Mechanical Engineering, School of Engineering, University of Zambia, Lusaka, Zambia
Abstract The planning and scheduling process is an inevitable step in any organization. This research investigated its effects in the electrical section of Anvil Mining Congo SA. In this company, planning, and scheduling, especially on equipment, focuses on preventive maintenance and not on activities related to repair, replacement and installation works. This research aimed to evaluate the changes in the performance of the electrical engineering section which currently lacks the daily planning and scheduling process. A quantitative approach with observations and desk study as instruments for data collection was used. The collected data included the duration (time) and the human resources allocated to particular activities. Data with and without daily planning and scheduling were compared to evaluate the changes in the sections performance over a study period of 30 months. After implementing the daily planning and scheduling process, the total duration to complete works of the analyzed activities was reduced by 45% while the human resources allocated to the activities were reduced by 46%. The efficiency of the section increased from 74% in August 2019 and 82% in August 2020 to 95% in August 2021. The preventive maintenance backlog reduced from 76% in January 2021 to 7% in August 2021. The companys electrical section is currently implementing a pilot planning and scheduling process after which a full-scale is envisaged to be implemented.
Keywords Backlog; Efficiency; Human Resources; Planning; Scheduling;
INTRODUCTION
Planning and scheduling are important in the whole industrial world. They are among the first steps taken when it comes to performing activities such as maintenance, investment, recruitment, and so forth.
Planning involves establishing the organizational objectives and deciding what actions need to be taken to achieve them [1]. After establishing the organizational objectives, the scheduling step follows. Scheduling is the allocation of resources to tasks over given periods to optimize one or more objectives [2]. It is a decision-making process that is used regularly in many manufacturing and service industries.
The planning and scheduling process reduces or eliminates uncertainties, improves efficiency, facilitates process control, and puts focus on objectives by providing a better understanding [3]. Concerning the mining industry, planning and scheduling improve resource utilization to ensure resources are used effectively [4]. Planning and scheduling can be short, medium, or long-term. In the literature, limited research has been done on a daily (short-term) as compared to medium and long-term planning and scheduling [5] [6]. The existing literature also focuses on preventive maintenance (PM) and not on daily activities such as breakdown maintenance (BM).
Using a priority function, [7] developed a planning and control system for use in a foundry. They stated that the PM capacity (workforce) available the next day was the difference between the total maintenance capacity and the BM required workforce. Reference [8] noted that schedules depend on plans and that in dynamic environments such as the ones presented by daily operations in the mining industry, rather than software tools, human beings develop schedules using their knowledge and experience in the particular domain. In the literature review on trends in turnaround (planned shutdown) maintenance planning, [9] defined short-term planning as one with a period of four to ten weeks. Reference [5] restricted the literature review on short-term planning of open-pit mines activities to periods of at least one week to at most one to two years. Daily planning involving equipment selection and truck dispatch was outside the scope of the review. These studies show the lack of research not only on short-term planning and scheduling in general but also on the daily planning and scheduling of activities in the mining industry.
This study investigated the daily planning and scheduling process in the electrical engineering section of Anvil Mining Congo SA in the Democratic Republic of Congo (DRC). This is because the planning and scheduling process has fundamental effects on the performance indicators of the section. Only 4 of the indicators were considered in the study. These were the completion duration of activities (jobs), the efficiency of the section, the human resources allocated to activities, and the preventive maintenance compliance.
The study aimed to assess the effects of daily planning and scheduling in the electrical engineering section within a mining company. This was to be attained by reviewing the maintenance planning and scheduling approaches used in the mining industry, evaluating the planning and scheduling system of the electrical engineering section of Anvil Mining Congo SA and comparing it to the approaches previously identified, and evaluating the effects of daily planning and scheduling process on the performances of the electrical engineering section.
BACKGROUND
-
Planning
Planning is an important concept in any organization and it has been defined by different authors. Planning is the process of setting objectives and determining how to accomplish them and it involves deciding exactly what needs to be accomplished and how best to go about it [11]. Planning is the determination of what needs to be done, by whom, and by when should ones assigned responsibility be fulfilled [12]. It is looking ahead and drawing future courses of action to be followed. It is a systematic activity that determines when, how, and who is going to perform a specific job [13].
Planning is important because it helps organizations to achieve their objectives; it is a prerequisite not only for achieving success but also for surviving in a complex and competitive world [14]. The planning process has an impact on the company which is doing it in the way that it affects the performance, facilitates control, and helps the company in the decision-making process [13].
Planning is done in 9 different steps as stated by [3]; (1) Clear definition of the objectives, (2) Establishment of the project scope, (3) Dividing and subdividing of the project scope into major pieces and work packages (Work Breakdown Structures), (4) Definition of specific activities that need to be performed for each work package to accomplish the project objectives, (5) Graphically portraying of activities in the form of network diagrams showing sequences and interdependencies,
(6) Making time estimate for each activity, (7) Estimation of other resources for each activity, (8) Calculation of the project schedule and budget to determine whether the project can be completed within the required time, with the allocated funds and other resources, and (9) Adjustment of the project scope, activity time estimates, and resource estimate till a realistic baseline plan is achieved.
There are four types of planning which include strategic planning, tactical planning, operational planning, and functional planning [11]. Daily planning (which is at the centre of this study) falls undr operational planning.
-
Scheduling
Scheduling is a concept that is most of the time attached to planning. It is the establishing of times at which to begin and complete each event or operation comprising a procedure [15]. It can also be defined as the determination of the timing and sequence of operations in the project and their assembly to give the overall completion time [16] or the process of describing in detail which activities must be performed and how the organizations resources should be utilized to satisfy a given plan [17].
According to the size of the company and the business it is involved in, 5 types of scheduling have been enumerated: baseline schedules, detailed schedules, master production schedules, look ahead schedules, and weekly schedules [18].
Scheduling is done in 6 different steps as stated in [19]: (1) Planning and schedule management, (2) Definition of activities,
(3) Sequencing of activities, (4) Estimation of activity resources, (5) Estimation of activity duration, and (6) Development of schedules.
-
Planning and scheduling in the mining industry
This research focused on the planning and scheduling process in the electrical engineering section which falls under the maintenance department as far as the mining industry is concerned. In this regard, maintenance is an act that includes keeping, preserving, and protecting a machine [20]. It is defined as efforts taken to keep the condition and performance of a machine always like its condition and performance when it is new [21].
Different approaches have been developed to know how maintenance can be performed to ensure equipment reach or exceed its design life [10]. These approaches include reactive maintenance, preventive maintenance, predictive maintenance, and reliability-centred maintenance [15]. Besides these, modern approaches are also used nowadays which include lean maintenance and six sigma maintenance. Six sigma maintenance is the application of six sigma principles in maintenance that focuses on reducing the variation in production while the application of the lean principle in a maintenance environment is called lean maintenance [15].
For a production-based company such as a mining company, 6 steps are necessary to plan and schedule an activity [10], (1) Knowledge base, (2) Job investigation at the site, (3) Identification and documentation of the work, (4) Development of the repair plan, (5) Preparation of tools and facilities list, and
(6) Estimation of the time required to do the job. For Tenke Fungurume Mining, only 5 steps are included in the planning and scheduling process [22]: (1) Understanding of the job, (2) Area of work, (3) Proposition of techniques, (4) Time and resources, and (5) safety and permission. Concerning the mining industry in general, 6 steps are enough according to [18]: (1) Equipment identification work, (2) Presence of a support network, (3) Definition of an effective program, (4) Use of information efficiently, (5) Establishment of organization levels, and (6) Taking of measurements and evaluation.
METHODOLOGY
-
Definition of the case study
Anvil Mining Congo SA is found in the Pweto district in the DRC. The company is mainly involved in copper mining. For the company, the planning and scheduling process is the responsibility of the maintenance department which is one of the companys most important departments. The department has the role of ensuring that all sets of equipment are in good working conditions always to allow smooth mining operations. The maintenance department of Anvil Mining Congo SA is organized as shown in Fig. 1.
Figure 1. Organization chart of the maintenance department
Here only the planning and electrical engineering sections were considered. The electrical engineering section is important because it is responsible for generating electricity for the company which does not have any other external source of electrical power. The power that supplies the whole plant is produced by the electrical section through diesel generators.
The role of the planning section is to plan and schedule all the activities concerning maintenance, from the stock management to the work plans and schedules. This section comprises 3 people. 1 person from the electrical section, 1 from the mechanical section, and 1 data clerk. For maintenance management, the company uses PRONTO XI as the computerized maintenance management system.
The planning section gathers daily equipment function information to generate the monthly PM activities. The information includes electric current and temperature for motors and ball mills, running hours, oil and fuel consumption for the generators, and temperature for transformers, etc. Designed checklists are used to collect these data based on the parameters to measure for each piece of equipment.
The maintenance activities undertaken by the electrical section are supposed to come from the planning section. After the reception of a job request, the planning section generates a work order using PRONTO XI software so that the job is recorded in the system. This makes it easy to evaluate the performance of the section based on the work performed against the planned or scheduled work. However, in the current practice, some of the job requests are given directly to the electrical section. These jobs are only taken to the planning section, from the electrical engineering section, after execution. In some cases, the planning section is not even informed about the jobs. This makes the job of the planning section hard because it is difficult to evaluate the performance of the section in particular and the maintenance department in general.
In the electrical engineering section, the planning and scheduling process ends with a list of activities to be done per day which includes neither availability of human resources nor the preparation of tools, equipment, or time estimation for the activities. A comparison of Anvil Mining Congo SA and other production-based industries is shown in Table 1.
TABLE 1. COMPARISON OF THE PLANNING AND SCHEDULING APPROACHES USED IN PRODUCTION AND MINING INDUSTRIES
Production- based company (Kumar & Suresh, 2008)
Tenke Fungurume Mining (Christian, 2017)
Mining industries (Frieser, 2020)
Anvil Mining Congo SA
PM
activities
Daily activities
1
Knowledge base
Understanding of the job
Equipment identification
Area identification
Equipment/ machine identification
2
Job investigation at the site
Area of work
Have a support work
Equipment identification
Execution
3
Identification and documentation of the work
Proposition of techniques
Define an effective program
Generation of PM task
4
Development of repair plan
Estimation of time and resources
Use past information efficiently
Techniques proposition
5
Tools and facilities list
Safety and permission
Establish organization levels
Safety considerations
6
Estimation of time required
Execution
Execution
Execution
7
Execution
Evaluate and perform measurements
Table 1 shows that for Anvil Mining Congo SA, concerning the PM activities which are planned by the planning section, the planning and scheduling process involves five steps before te execution of the activities. But for the electrical engineering section, only the identification of the machine/ equipment is required before the execution of the activities. Therefore, activities are executed without any prior planning.
This lack of daily planning and scheduling affects firstly, the PM compliance which showed 59% of backlogs in April 2021 (Table 4) the month at the end of which the pilot planning and scheduling was implemented. This level of backlogs is against the maintenance standard which requires that backlogs should not exceed 10% [10]. Secondly, the activities take more time and require a lot of human resources to be completed compared to the case if there was prior planning and scheduling. Lastly, the efficiency of the section is also affected by the lack of planning and scheduling. The section report showed the highest efficiency of 83% in April 2021 (Table 4).
The research used a quantitative approach to achieve its objectives. It used observation and desk study as instruments for data collection. Interviews were used for information clarification.
-
Data collection process
The data collection procedure, as shown in Fig. 2, started with the job requests received at the section per day. For a given job request, the first step was to know if the job has been done before. If the job has never been done before, the second step was to apply the planning and scheduling process. If the job has been done before, not only was the planning and scheduling process implemented on it but also the recorded data (time spent and human resources allocated when the job was done) were collected through document review.
DATA ANALYSIS AND RESULTS
-
The efficiency of the section
The efficiency of the section is computed as a ratio of the number of activities done over the number of activities that were supposed to be done, expressed as a percentage, as shown in (1):
=
: efficiency of the section
n: number of activities done
N: number of activities issued
(1)
Figure 2. Data collection procedure
Having two collected data sets, respectively from the document review (without any prior planning and scheduling) and the records for jobs done after the planning and scheduling process, the next step was the comparison of these data sets to deduce the difference and highlight the effects of the planning and scheduling process.
Based on the emergency and the availability of the human resources, the activity (job) was either planned to be executed or scheduled for a suitable day. Then after the execution of the activity, the time spent and the human resources allocated to the activity were recorded.
-
-
The suggested planning and scheduling process
The research idea was based on the theory of planning and scheduling which states that planning improves efficiency and scheduling is well done if realistic estimates are applied [24]. This is because proper planning reduces the risk of time overruns, enhances outcome quality, and improves operational safety [9].
The planning and scheduling process suggested to the electrical engineering section was the one established by [15] for a production-based company with an aspect of scheduling and safety. This process includes 9 steps: (1) Knowledge base, (2) Job investigation at the site, (3) Emergency assessment, (4) Identification and documentation of the work, (5) Resources availability assessment, (6) Development of repair plan, (7) Tool and facilities list, (8) Estimation of time required, and (9) Safety considerations.
The efficiency of the electrical engineering section was computed for the years 2019, 2020, and from January to August 2021 to compare the figures within the period with and without the planning and scheduling process. The electrical engineering section monthly efficiencies for 2019 are shown in Table 2. The table shows that for the year 2019, the maximum efficiency was 83% and it occurred in April while the minimum was 69%. This occurred in October. For the year 2020, the monthly efficiencies were collected from reports and are shown in Table 3.
TABLE 2. SECTION MONTHLY EFFICIENCIES FOR 2019
Number of activities done (n) |
Number of activities issued (N) |
Efficiency (%) |
|
January |
49 |
61 |
80 |
February |
48 |
59 |
81 |
March |
45 |
58 |
78 |
April |
59 |
71 |
83 |
May |
51 |
69 |
74 |
June |
53 |
70 |
76 |
July |
40 |
51 |
78 |
August |
39 |
53 |
74 |
September |
47 |
65 |
72 |
October |
37 |
54 |
69 |
November |
49 |
60 |
82 |
December |
49 |
67 |
73 |
TABLE 3. SECTION MONTHLY EFFICIENCIES FOR 2020
Number of activities done (n) |
Number of activities issued (N) |
Efficiency (%) |
|
January |
37 |
50 |
74 |
February |
50 |
61 |
82 |
March |
51 |
63 |
81 |
April |
49 |
60 |
82 |
May |
40 |
56 |
71 |
June |
48 |
59 |
81 |
July |
47 |
57 |
82 |
August |
59 |
72 |
82 |
September |
60 |
81 |
74 |
October |
57 |
77 |
74 |
November |
61 |
79 |
77 |
December |
59 |
71 |
83 |
For the year 2020, the maximum efficiency of 83% occurred in December, while the minimum efficiency of 71% occurred in May as shown in Table 3.
The monthly efficiencies for the year 2021 are sown in Table 4. For the first time since 2019, the efficiency of the electrical engineering section reached 92% in May 2021. This increase in efficiency was attributed to the effect of the implemented daily planning and scheduling process which began in May 2021 because that is the only parameter that changed. This increase in the sections efficiency verifies the theory (discussed earlier) which says planning and scheduling improve efficiency.
-
Duration and human resources
The collected data sets were analyzed to compare the duration and human resources allocated to different activities under both planned and unplanned conditions. Fig. 3 shows that 41.5 hours were required to perform certain activities with 39 workers when they were not planned. However, 23 hours and 21 workers were required to do the same activities when they were planned and scheduled. This represents savings of 45% in the duration and 46% in human resources.
TABLE 4. SECTION MONTHLY EFFICIENCIES FOR 2021
Number of activities done (n)
Number of activities issued (N)
Efficiency (%)
January
47
56
84
February
75
89
84
March
46
57
81
April
69
83
83
May
58
63
92
June
64
67
96
July
74
79
94
August
78
82
95
UNPLANNED VS PLANNED
ACTIVITIES
Time Resources
UNPLANNED VS PLANNED
ACTIVITIES
Time Resources
41.5
39
41.5
39
23
21
23
21
U N P L A N N E D
P L A N N E D
U N P L A N N E D
P L A N N E D
Figure 3. Unplanned activities vs planned activities
-
PM Compliance
PM compliance is monitored in terms of the backlog, which is the percentage of the unexecuted PM activities against the issued (planned) PM activities. It is computed using (2):
= 1 ( ) (2)
B: Backlog
R: PM Activities executed
I: PM activities issued
PM compliance information in reports from the year 2019 to 2021 was collected. Table 5 presents the electrical engineering section PM monthly compliance levels for the year 2019. Table 5 shows that for July and August, backlogs were 100%. This happened because the section was working on a project of adding a new unit in the plant and during this same period, more than 2 planned shutdowns were supposed to be done. Therefore, the section did not have enough time for the PM activities (shutdowns). For the year 2020, the PM monthly compliance levels are shown in Table 6.
TABLE 5. PM MONTHLY COMPLIANCE LEVELS FOR 2019
Month
Number of PM activities issued (I)
Number of PM activities executed (R)
Backlog (B) (%)
January
248
107
57
February
135
57
58
March
44
23
48
April
104
78
25
May
192
140
27
June
192
98
49
July
135
0
100
August
112
0
100
September
181
16
91
October
386
356
8
November
438
306
30
December
429
309
28
TABLE 6. PM MONTHLY COMPLIANCE LEVELS FOR 2020
Month
Number of PM activities issued (I)
Number of PM activities executed (R)
Backlog (B) (%)
January
345
158
54
February
270
21
92
March
335
5
99
April
244
139
43
May
373
63
83
June
352
14
96
July
329
207
37
August
383
261
32
September
380
276
27
October
293
199
32
November
284
282
1
December
419
395
6
Table 6 shows that in November and December 2020, the section performed very well in terms of backlogs as shown in Table 6. Planners explanations for these exceptionally high compliance levels were that there were low workloads during the period covering those months.
The PM compliance levels for 2021 (Table 7), show an improvement in terms of backlogs. After the implementation of the planning and scheduling process in May 2021, for the first time since 2019, the backlog percentage did not go above 25% for 4 consecutive months.
TABLE 7. PM MONTHLY COMPLIANCE LEVELS FOR 2021
Month
Number of PM activities issued (I)
Number of PM activities executed (R)
Backlog (B) (%)
January
341
82
76
February
325
284
13
March
423
279
34
April
364
149
59
May
300
286
5
June
398
300
25
July
316
286
9
August
385
359
7
CONCLUSION
The study investigated the daily planning and scheduling process of Anvil Mining Congo SA and the effects of this process on the complete duration of activities (jobs), the efficiency of the section, the human resources allocated to activities and the preventive maintenance compliance. For the investigation, only the planning and scheduling process constituted a change in the daily maintenance approach of the electrical engineering section of Anvil Mining Congo SA.
The study showed, as predicted in the literature, that with the planning and scheduling process, being the only variable parameter, the performance of the electrical engineering section was greatly affected. Within two months, after implementing the planning and scheduling process, the total duration to complete works of the analyzed activities was reduced by 45% while the human resources allocated to the activities were reduced by 46%. The efficiency of the section increased from 74% in August 2019 and 82% in August 2020 to 95% in August 2021. The preventive maintenance backlog reduced from 76% in January 2021 to 7% in August 2021. The companys electrical engineering section is currently implementing a pilot planning and scheduling process after which a decision will be made on whether to switch to full scale or not.
ACKNOWLEDGEMENT
The researchers are thankful to the company Anvil Mining Congo SAs maintenance department for providing the necessary data for this research. This research was funded by the first author.
REFERENCES
-
U. Gündüz, I. Or and S. Nezih, "Design and Implementation of a Maintenance Planning System," International Journal of Production Economics, 2018.
-
J. Sauer, "Planning and Scheduling: An Overview," 2014. [Online]. [Accessed 26 October 2019].
-
A.-T. Umar, D. Salih and B. M., "Trends in turnaround Maintenance planning: literature review," Journal of Quality in Maintenance Engineering, vol. XXV, pp. 253-271, 2019.
-
A. Weber and R. Thomas, "Key performance indicators," Ivara corporation, Ontario, 2005.
-
J. John R. Schermerhorn, Management, 12th ed., New Jerey: Wiley, 2013.
-
P. Harold Kerzner, Project management: A systems approach to planning, scheduling and controlling, 10th ed., New Jersey: John Wiley & Sons, Inc., 2009.
-
A. Sarker, "Planning function management," Anupam publications, Bangladesh, 2019.
-
Tamanna, "Business Management ideas," 2007. [Online]. Available: https://www.businessmanagementideas.com/planning/importance- of-planning/importance-of-planning-in-management/19286. [Accessed 5 November 2020].
-
S. A. Kumar and N. Suresh, Production and Operations Management, 2nd ed., Bangalore: New Age International, 2008.
-
S. A. Mubarak, "Construction Project Scheduling and Control," Wiley, New Jersey, 2010.
-
M. Fera, F. Fruggiero, A. Lambiase, G. Martino, and M. E. Nenni, "Production Scheduling Approaches for Operations Management," Intechopen, 2013.
-
E. Bjarnason, "Critical Success Factors for Planning, Scheduling, and Control in Design and Construction," ReykjavÃk University, ReykjavÃk, 2015.
-
B. Roseke, "Project Engineer," October 2017. [Online]. Available: https://www.projectengineer.net/steps-in-project-scheduling/. [Accessed 20 April 2021].
-
R. Smith and M. R. Keith, Rules of thumb for maintenance and reliability engineers, 2007.
-
Sivaranjith, "AutomationForum.co," 2019. [Online]. Available: https://automationforum.co/what-is-maintenance-types-of- maintenance/. [Accessed 6 October 2021].
-
K. Christian, "Rapport de stage effectué au sein de l'entreprise Tenke Fungurume Mining," 2017.
[1] D. A. Desenzo, S. P. Robbins and S. L. Verhulst, Fundamentals of Human Resource Management, 12th ed., New Jersey: Wiley, 2016.
[2] M. L. Pinedo, Scheduling: Theory, Algorithms & Systems, 3rd ed., New York: Springer, 2008.
[3] Project Management Institute, Inc., A guide to the project management body of knowledge, 4th ed., Pennsylvania: Project Management Institute, Inc., 2008.
[4] J. Bruton and L. Lumen, "Lumen," 2017. [Online]. Available: https://courses.lumenlearning.com/wm- principlesofmanagement/chapter/reading-pros-and-cons-of- planning/. [Accessed 14 April 2021].
[5] B. Michelle, P. Adrian R., and S. Peter J., "Short term Planning for Open Pits Mines: A Review," International Journal of Mining, Reclamation, and Environment, 2018.
[6] C. Hon Huin, V. Petar Sabev, and K. Jià JaromÃr, "Short Term Maintenance Tasks Scheduling with Pinch Methodology," Chemical Engineering Transactions, Vols. VOL. 78, 2020, 2019.
[1] D. A. Desenzo, S. P. Robbins and S. L. Verhulst, Fundamentals of Human Resource Management, 12th ed., New Jersey: Wiley, 2016.
[2] M. L. Pinedo, Scheduling: Theory, Algorithms & Systems, 3rd ed., New York: Springer, 2008.
[3] Project Management Institute, Inc., A guide to the project management body of knowledge, 4th ed., Pennsylvania: Project Management Institute, Inc., 2008.
[4] J. Bruton and L. Lumen, "Lumen," 2017. [Online]. Available: https://courses.lumenlearning.com/wm- principlesofmanagement/chapter/reading-pros-and-cons-of- planning/. [Accessed 14 April 2021].
[5] B. Michelle, P. Adrian R., and S. Peter J., "Short term Planning for Open Pits Mines: A Review," International Journal of Mining, Reclamation, and Environment, 2018.
[6] C. Hon Huin, V. Petar Sabev, and K. Jià JaromÃr, "Short Term Maintenance Tasks Scheduling with Pinch Methodology," Chemical Engineering Transactions, Vols. VOL. 78, 2020, 2019.
-
A. Frieser, "Data Scope," 2020. [Online]. Available: https://datascope.io/en/blog/mining-maintenance-plan-how-to-do- it-step-by-step/. [Accessed 28 September 2021].
-
P. D. Harold Kerzner, Project planning: A systems approach to planning, scheduling and controlling, 11th ed., New Jersey: Wiley, 2013.
-