
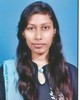
- Open Access
- Authors : Manju Singh , Harinder Pal , Kalesh Nath Chatterjee
- Paper ID : IJERTV10IS120078
- Volume & Issue : Volume 10, Issue 12 (December 2021)
- Published (First Online): 18-12-2021
- ISSN (Online) : 2278-0181
- Publisher Name : IJERT
- License:
This work is licensed under a Creative Commons Attribution 4.0 International License
A Comparative Study of Handloom Denim using Bamboo and Cotton Yarn
Manju Singh* Harinder Pal
Department of Fashion Technology, BPS Women University, Sonipat, Haryana, India
Kalesh Nath Chatterjee
Design Department, Netaji Subhas University of Technology, Delhi
Abstract:- Nowadays, sustainability plays a leading role in the textile and fashion industry due to the huge amount of consumption of energy, hazardous chemicals, and water being used in the above industries. Many textile and fashion industries are focusing more on eco-friendly products which help to meet the environmental and social aspects. From the last few decades, denim has become the most preferable product in the fashion industry adopted by all gender and age groups but at the same time, denim manufacturing has caused a huge environmental hazardous impact in terms of water and carbon footprints. Moreover, cotton is the main constituent of denim products which is also responsible for environmental hazardous impact as cotton production uses 25 % of insecticides and 12% pesticides which causes a concern for human health. In this study, an attempt has been made to reduce environmental hazardous impact by developing sustainable textile material made from bio-based renewable resources in the form of bamboo fibres. In this research study, Denim fabric samples are developed using ring yarn of 100% bamboo fibre with 2/20 Ne in a weft way and 100% cotton fibre with 2/20 Ne in the warp way on handloom frame with 2/1 and 3/1 twill weave. It is observed that lesser crease recovery, lower flexural rigidity, higher elongation % and tear strength using bamboo than cotton yarn. It is also found that better flexibility, higher air permeability, higher tensile and tearing strength in 3/1 twill weave as compared to 2/1 twill woven fabrics.
Keywords: Bamboo, Denim, Handloom, Sustainable
-
INTRODUCTION
Textile manufacturing industries are responsible for destroying the environment in different ways, for example, high consumption of water, harmful chemicals, and energy for cultivation and other processes [1]. Total of 15% of fertilizers are used to grow cotton crops which cause a serious impact on the environment [2]. Globally, Denim is a unique textile material that is mostly preferred by all gender and age groups for daily life [3]. Nowadays, many consumers are interested in apparel not only for its looks but also for the result of different comfort, psychological, sensorial activities, and thermo physiological comfort [4]. The denim manufacturing industry is one of the most polluting industries which is responsible for the ill impact on the environment and human health in the fashion world [5]. Further, the physiological comfort included by important fabric properties such as air permeability, moisture management properties, UV protection is influenced by various constructional parameters of the fabric such as weave, thread density, count, type of fibres, and their blend ratio [6]. Denim products consume about 2 kg of CO2 per functional unit and water footprints from raw material extraction to the disposable phase [7]. According to a Greenpeace report, two billion pairs of jeans are
manufactured every year, it may take 1.7 million tons of chemicals to produce them and water consumption can go as high as 7,000 litres per pair [8]. Cotton is a natural fibre and has a big market share in textile products worldwide, but its cultivation involves the extensive use of pesticides, fertilizers, insecticides, and large amounts of water that gives rise to environmental and economic distress [1]. About
1.5 pounds of cotton is needed to produce one pair of jeans which consumes about 1500 gallons of water [9].
With the challenging demand for more comfortable, healthier, and environment-friendly products, we have opted for bamboo which is a renewable, regenerated cellulosic, biodegradable fibre that will help to achieve sustainability in the products [10]. Bamboo fibre grows naturally without any herbicides, pesticides, fertilizers, and irrigation, it grows in natural rainfall [11]. Regenerated bamboo fibres have more characteristics such as superior tensile strength, excellent UV protection, antibacterial, biodegradable, high moisture absorption, softness, brightness, and high flexibility under flexible and compressive loads. bamboo [12]. Another consideration for sustainability in our research is given to the handloom sector, which is a traditional industry of India and provides opportunities for employment to millions of people in the rural and urban areas in our country [13]. The handloom sector has the advantage of being less capital intensive, no use of energy power, eco-friendly than power loom [14].
Literature reveals a very limited research work on handloom denim but until now, there is no research work on handloom denim using bamboo fibre. In this research work, two denim fabric samples were developed on a handloom frame using the same construction parameters such as thread density, yarn count and then compared between 2/1 and 3/1 twill weave denim based on Handle, Mechanical, and Comfort properties. Both samples are constructed using 100% grey cotton yarn in the warp direction and 100% bamboo yarn in the weft direction. The handloom denim samples developed using bamboo yarn are evaluated in terms of construction parameters like thread density and GSM. The handle properties in terms of crease recovery, bending length, flexural rigidity, and mechanical properties like tensile strength, tear strength, and Comfort properties such as air permeability are evaluated and compared between 2/1 and 3/1 twill weave denim in both directions.
-
MATERIALS AND METHODS
In this research work, two denim samples were developed on a handloom frame using bamboo and cotton yarn of 2/20 Ne. 100% bamboo yarn was used in the weft direction and 2/20 Ne 100% cotton yarn was used in the warp direction.
The reed size of 27 dents per inch with two ends per reed dent was used to produce the handloom twill denim sample. The fabric GSM was maintained between 256-269 g/m2.100% bamboo yarn was manufactured on ring spinning system with 17 TPI, Z twist in single-ply yarn and 11 TPI, S twist in double-ply yarn.
-
Test Methods
The properties and the test methods are shown in Table 2.1.
Properties
Standard Methods
Instruments
Thread Density
ISO 7211/2-1984.
Pick Glass
GSM
ISO 3801-1977
GSM Cutter
Bending Length & Flexural rigidity
ASTM D1388-08
Shirley Stiffness Tester
Crease recovery
AATCC 66
Shirley Crease Recovery Tester
Breaking Load & Elongation%
ASTM D5034- 09(2013)
CRE Tensile Testing Machine
Tearing Strength
ASTM D1424:09(2013)
Elmendorf Tear Tester
Air Permeability
ASTM D737
Air Permeability Tester
Table 2.1: Properties and Test method
-
Fabric weight in GSM (g/m2)
ISO 3801-1977 standard test method was used for measuring the gram per metre square of handloom denim fabrics. Five samples of each denim fabric were tested by using GSM circular cutter and weighing machine.
-
Thread Density
Thread density was measured by using a pick glass as per ISO7211/2-1984 standard test method. Ten samples were taken, five samples in the warp way and five samples in the weft way of each weave structure.
-
Breaking Load & Breaking Elongation %
The CRE based grab method (ASTM D5034-09, 2013) was used for the breaking strength and elongation % of the fabric. The specimens size was cut 6-inch x 4-inch where five samples were in the warp way and five in the weft way of each sample. In this tensile instrument, the initial length was
-
-
inch and the speed of the machine was adjusted for breaking the sample in 20±3 seconds.
-
Tearing Strength
The testing method ASTM D 1424:09, 2013) was used for the tear strength of the specimen. In this research work, the type of the falling Pendulum Elmendorf equipment was used to determine the tear strength of the denim. The specimens size was cut 7.5 cm x 10 cm and the numbers of samples taken were five warp way and five weft ways for each twill weave. The pendulum weight was 12.8 kilograms.
-
Bending length & Flexural Rigidity
Testing method ASTM D1388-08 was used for the stiffness of the fabric. Bending length and flexural rigidity was measured on the cantilever principle. In this experiment, the stiffness of the fabric was determined by using a Shirley Stiffness tester. The sample size was taken 6-inch x 1-inch. Total six specimens were taken of each twill weave, three in warp way and three samples in weft way.
Flexural rigidity (G) = W X C3 mg.cm
Where W is the weight per unit area in mg/cm2 and C is bending length in cm.
-
Crease Recovery
The crease recovery of the fabric was carried out on the Shirley crease recovery tester. Crease recovery depends upon the construction, twist of yarn, pressure, and time. Total twenty specimens were taken of each twill weave, where ten samples were in the warp way, and ten samples in the weft way. 500-gram load was applied for creasing and 5 min was taken for creasing and then the same time was taken for recovery.
-
Air Permeability
Testing method ASTM D737 was used to determine the air permeability of each twill weave sample. Air permeability was measured on the Air Permeability testing instrument (TEXTEST), and the device was FX 33000-IV. In this experiment, air permeability was evaluated in 2/1 and 3/1 twill weave. Total ten numbers of samples were taken of each twill weave and air permeability was measured with 125 Pa (air pressure) and 38 cm2 test area.
-
-
-
RESULTS & DISCUSSION
The denim samples were conditioned in the testing atmosphere of 65±2% RH and temperature of 27±20C to get reliability in the results. Following results have been obtained while testing of handloom twill denim fabric.
Table 3.1
Handloom Sample
Yarn count (Ne)
Thread Density per Inch
GSM
(g/m2)
Breaking Load (Kg)
Elongation%
Tearing Strength (Kgf)
Warp
Weft
EPI
PPI
Warp
Weft
Warp
Weft
Warp
Weft
2/1 Twill
2/20
2/20
60
34
256
57.1
45.9
24.9
37.5
5.9
10.2
3/1 Twill
2/20
2/20
62
36
269
54.6
49.7
22.3
37.2
6.7
11
Table 3.2
Handloom Sample
Bending Length (cm)
Flexural Rigidity mg.cm
Crease Recovery Angle
Air Permeability (cm3/cm2/sec.)
Warp
Weft
EPI
PPI
Warp
Weft
2/1 Twill
2.5
1.8
400
149
134
105
20.45
3/1 Twill
2.5
1.6
420
110
117
110
27.78
3.1 Fabric weight per unit area (g/m2)
Weight per unit area (g/m2) was measured by using a GSM circular cutter instrument of 100 cm2 area and a weighing machine. Fabric weight depends upon some characteristics such as yarn count, thread density, fibre density, crimp %.
Fabric weight per unit area
270
265
260
255
Breaking Elongation %
40
20
0
2/1 Twill Weave 3/1 Twill Weave Warp Weft
Figure 3.3: Breaking Elongation %
250
245
2/1 Twill Weave 3/1 Twill Weave
Results are indicated in Table 3.1 and Fig. 3.3. no significant difference in breaking elongation was observed among the denim samples. It was that breaking elongation was higher
Figure 3.1: Fabric weight per unit area (g/m2)
In this experiment, fabric weight for all the samples ranges from 256 g/m2 to 269 g/m2. Results are indicated in Table
-
and Fig. 3.1. no significant difference in fabric weight was observed among the denim samples.
-
Breaking Load (Kg.)
Tensile strength is the ability to measure the breaking strength and elongation of the textile material under the maximum stretching load and their results depend on some factors such as fibre type, specimen geometry, arrangement, and as well as the weave structure.
in a weft direction as compared to warp direction due to the use of bamboo yarn in the weft way. It is attributed to the smooth surface structure and lower resistance to bending and recovery of the bamboo fibers.
3.4 Tear strength (Kgf.)
The behaviour of the woven fabric under impact load is different from that under tension load. In tearing testing, only a few yarns share the breaking load, whereas in tensile strength all the yarns share the load in the directions. Denim fabric was constructed with the same construction parameters in 2/1 and 3/1 twill weave.
Tear strength (Kgf.)
Breaking Load
60
40
20
0
2/1 Twill Weave 3/1 Twill Weave Warp Weft
Figure 3.2: Breaking Load (Kg)
Table 3.1 and Fig.3.2 shows the comparison of tensile strength with 2/1 and 3/1 twill weave in both directions. It was observed that the tensile strength of the 2/1 twill weave was more than 3/1 twill weave which is due to the less porous, less float length and higher number of interlacements between warp and weft, providing higher contact area and hence leading to greater friction force and resistance to slippage of yarn in fabric. It was also observed that the tensile strength is less in the weft way when compared to the warp way because of the lesser pick density in a sample.
3.3 Breaking Elongation %
Breaking elongation was found to be more in the weft direction as compared to the warp direction.
15
10
5
0
2/1 Twill Weave 3/1 Twill Weave Warp Weft
Figure 3.4: Tear strength
Table 3.1 and Fig.3.4 shows the comparison of tear strength with each wave in both directions. It was observed that tear strength is higher in 3/1 as compared to 2/1 twill weave due to loosening structure (long floats), the fewer number of interlacements between warp and weft where the yarn can easily move, thus result in higher tear resistance. 2/1 twill weave has more binding points to resist the thread movement thus results in decreased tear strength. It was also observed that higher tear strength in weft way as compared to warp way due to more strength of bamboo yarn than cotton yarn.
-
Bending Length and Flexural Rigidity
Bending length and flexural rigidity is the measure of fabric stiffness. A higher bending length and flexural rigidity are considered to be stiffer and less draping of the fabric. The stiffness properties of fabric affect drapeability performance. The stiffer fabric may not be comfortable to wear. The bending length is also known as drape stiffness.
Bending Length
3
2
1
0
2/1 Twill Weave 3/1 Twill Weave Warp Weft
Bending Length
3
2
1
0
2/1 Twill Weave 3/1 Twill Weave Warp Weft
feeling and usage of the fabric depends upon climate conditions for example high air permeability is required for clothing in a hot climate, however, it may be a positive effect in a cold climate.
Flexural Rigidity
500
400
300
200
100
0
2/1 Twill Weave 3/1 Twill Weave Warp Weft
Flexural Rigidity
500
400
300
200
100
0
2/1 Twill Weave 3/1 Twill Weave Warp Weft
Figure 3.5: Bending Length (cm)
+
Figure 3.6: Flexural Rigidity
In this experiment, Table 3.2 and Fig.3.5 and 3.6 shows the comparison of bending length and flexural rigidity between 2/1 and 3/1 twill weave in both directions. It was found that the stiffness of 3/1 twill is less than 2/1 twill weave because it contains less interlacement point, high float length, more porous and flexible. It was also observed that flexibility is higher the weft wise which may be due to the prominence of bamboo yarn (more flexible than cotton) in the weft direction.
-
Crease Recovery
The effect of the weave and type of yarn on the crease recovery of the denim fabrics is shown in Table 3.2 and Fig. 3.7.
Crease Recovery
200
100
0
2/1 Twill Weave 3/1 Twill Weave Warp Weft
Figure 3.7: Crease Recovery
It can be observed that the higher crease recovery 2/1 twill weave in warp way when compared with the 3/1 twill weave, the reason may be attributed to 2/1 twill weave is made up with higher no. of intersection per repeat and more stretching of fibers and yarns on creasing than 3/1 twill weave. It was also observed that the higher crease recovery in warp way than weft way with both twill weave, which may be due to more ends per inch than picks per inch.
-
Air permeability
The air permeability of the textile material indicates the ability of the fabric to allow atmospheric air through the fabric. The purpose of this property is to reduce the damp
Air permeability
30
25
20
15
10
5
0
2/1 Twill Weave 3/1 Twill Weave Figure 3.8: Air permeability
Table 3.2 and Fig. 3.8 show the air permeability of 2/1 and 3/1 twill weave. In this experiment, it was observed that higher air permeability in 3/1 twill weave as compared to 2/1 twill weave which may be due to increasing float length which further makes the fabric, a loose structure.
-
-
CONCLUSION:
In this research work, denim fabrics were developed on handloom made from 2/20 Ne bamboo yarn in the weft way and 2/20 Ne cotton yarn in the warp way. The effect of weave in denim fabric using bamboo and the cotton yarns were critically analysed for their Handle, Mechanical and Comfort properties. The results indicate lesser tensile strength, better elongation %, higher tearing strength, better flexibility, and lesser crease recovery in the weft way using bamboo yarn as compared to using the cotton yarn in the warp way. It was also found that higher tensile strength, higher tearing strength, better flexibility, and higher air permeability but lesser crease recovery in a 3/1 twill weave sample using bamboo yarn as compared to 2/1 twill weave in the weft way. It is concluded that bamboo fibre has a better elongation %, tearing strength, better flexibility, but lesser crease recovery as compared to cotton fibre.
REFERENCES:
-
Ali A. M., Sarwar I. M., Sustainable and environmentally friendly fibres in textile fashion: A study of organic cotton and bamboo fibres, Master Thesis, Applied Textile Management, University of Baros, Boras, Sweden, (2010).
-
Prendergast J., Venkatraman P. D., A study on the development of sustainable organic clothing for womens wear using natural fibres with a specific focus on product serviceability. In: 14th Annual conference of the International Fashion Foundation Institute, (2012).
-
Gokarneshan N., Sandip K. R., Malathi R., Aathira, Advances in denim research, Research and Development Material Science, 3(1), 1-7, (2018).
-
Mahish S. S., Patra A. K., and Thakur R., Functional properties of bamboo/polyester blended knitted apparel fabrics, Indian Journal of Fibre and Textile Research, Vol.37, 231-237, (2012).
-
Csanák, E., Sustainable concepts and eco-friendly technologies in the denim industry, In International Conference on Design and Light Industry Technologies, Óbuda University, Budapest, Hungary, (2014).
-
Nagarajan G., Ramachandran T., A comparative study of denim fabrics developed using ring and rotor bamboo/cotton yarns, International Research Journal of Pharmacy, 9(4), 35-41, (2018).
-
Chatterjee K. N., Sharma D., Pal H, Quality aspects of sustainable handloom denim fabrics made of hand-spun and machine-spun cotton
yarn, Journal of Textile and Apparel, Technology and Management,11(2), 1-7, (2020).
-
Jiby J. B., The Indian denim industry in a market-driven environment,
International Journal of Advanced Research,5(5), 1189-1196, (2017).
-
Periyasamy P. A., Ramamoorthy K. S., Lavate S. S., Eco-friendly denim processing, Handbook of Eco materials, Springer Switzerland, pp 1559-1579, (2019).
-
Erdumlu N., Ozipek B., Investigation of regenerated bamboo fibre and yarn characteristics, Fibres & Textiles in Eastern Europe, 16(4), 43-47, (2008).
-
https://www.fibre2fashion.com/industry-article/3842/benefits-of- bamboo-fabric# (2008)
-
Rathod A., Kolhatkar A., Analysis of physical characteristics of bamboo fabrics, International Journal of Research in Engineering and Technology, 3(8), 21-25, (2014).
-
Tanusree S., A study of the present situation of the traditional handloom weavers of Varanasi, International Research Journal of Social Sciences, 4(3), 48-53, (2015).
-
Jain C. D., Gera R., An analytical study of handloom industry of India, International Journal of Science Technology and Management, 6(1), 663-669, (2017).