
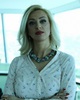
- Open Access
- Authors : Zlata Jelacic
- Paper ID : IJERTV10IS120056
- Volume & Issue : Volume 10, Issue 12 (December 2021)
- Published (First Online): 31-12-2021
- ISSN (Online) : 2278-0181
- Publisher Name : IJERT
- License:
This work is licensed under a Creative Commons Attribution 4.0 International License
Best Practices in Domestic Service Robot Design
Zlata Jelacic Department of Mechanics University of Sarajevo
Sarajevo, Bosnia and Herzegovina
Abstract Before service robots will be part of our daily lives, large-scale developments on both hardware and software are required. Nevertheless, service robots are currently only available to large research institutions that have the resources to develop one. The service robots that are available are usually far too expensive. Furthermore, the available service robots are not modular, and their designs are closed-source, hampering further development. Therefore, a modular service robot is required with standardized interfaces. Furthermore, it must be open hardware so that it can act as a reference implementation for future developments.
Keywords Service robots, mobile robots, algorithm classes, domestic robots, open-spource hardware
-
INTRODUCTION
Robots are expected to play an increasing role in society over the next number of years. They can, e.g., reduce the pressure on the home care system by assisting people with mobility impairments so that they can live independently at home for a longer time. Furthermore, robots will also increasingly work alongside people in industry. This illustrates the need for the development of versatile, reliable, robust and affordable robots.
As is mentioned in Weisshardt et al (2010), it is expensive and time consuming to develop these robots. Nevertheless, many service robots have been developed over the past ten years.
The development of the PR2 (based on the design in Wyrobek et al (2008)) has concentrated on the design and implementation of a fully integrated development platform that is designed to be safe and capable in human environments. The long-term goal of the Care-O-bot project (Graf et al, 2004, 2009) is to develop a mobile robot able to assist people in their homes and combines the technological aspects with a user-friendly design. The two-arm system in reference Ott et al (2006) is developed as a research platform to contribute to the manipulation skills of humanoid robots. Together with the platform introduced in Fuchs et al (2009), it also forms the mobile service robot Rollin' Justin. More humanoid research platforms are ARMAR-III (Asfour et al, 2006), Dynamaid (Stückler and Behnke, 2009), TWENDY- ONE (Iwata and Sugano, 2009) and HoLLiE (Hermann et al, 2013).
-
MODULARITY
Similar to the computer industry, which quickly gained momentum after a standardized, open PC architecture was introduced, the development of service robots can greatly benefit from standardized interfaces that allow modular substitution of components. Modular components with standardized interfaces i) allow the use of hardware
components for a specific task, ii) allow a robot to be assembled from components of multiple developers and iii) eases maintenance of the robots.
Modularity has been an important issue in a number of these designs. In Wyrobek et al (2008) it is recognized that a modular approach makes it possible to add specialized hardware and end-effectors. The Care-O-bot 3 also has a modular setup (Weisshardt et al, 2010) and has a modified, existing manipulator connected to an existing end-effector. Rollin' Justin (Ott et al, 2006; Fuchs et al, 2009) also has a separately designed base, torso and arms. Similarly, ARMAR-III (Asfour et al, 2006) and HoLLiE (Hermann et al, 2013) have been designed as a mobile platform with a modular upper body. However, only the PR2 contains open interfaces to use different grippers, arms or sensors and the designs in Stückler and Behnke (2009); Iwata and Sugano (2009) are in general less modular.
-
OPEN-SOURCE SOFTWARE
As is argued in Reynolds and Wyatt (2011), open-source software implementations of a standard means that the standard is more likely to be of high quality, since these implementations act as reference implementations, and that the standard is more likely to be adopted. Unfortunately, most of these robots are unique research platforms that are not available to other research institutions (Fuchs et al, 2009; Weisshardt et al, 2010). The platforms that are available such as the PR2 (Wyrobek et al, 2008) and the Care-O-bot 3 (Graf et al, 2009) are too expensive for many research institutions. In the field of humanoid, walking robots, the importance of open-hardware has long been recognized, with the iCub (Metta et al, 2008), DARwIn-OP (Ha et al, 2011) and NimbRo-OP (Schwarz et al, 2014) as well-known examples. These robots, however, are not suitable as service robots.
In the next section, the design principles of the base platforms, upper bodies and manipulators of current domestic service robots are discussed. In this section, various possibilities for base platforms, torsos and manipulators are discussed.
-
BASE PLATFORMS
Most of the robots consist of a moving base, a torso with one or more degrees of freedom and one or two manipulators. Although many of the tasks that are currently demonstrated using service robots can be performed with only one manipulator, an anthropomorphic robot with two manipulators and a moving torso has the advantage that it can also perform bimanual manipulation. Therefore, focus will lie on these anthropomorphic robots.
Base platforms for service robots can be divided in three categories: non-holonomic, semi-holonomic and fully holonomic platforms. A holonomic robot can drive in any direction without having to turn beforehand. Hence, both the number of controllable DoFs and the total number of DoFs equal 3 (two translations and one rotation). A non-holonomic robot has fewer controllable DoFs than the total number of DoFs. For example, a car is non-holonomic: it cannot drive sideways. A semi-holonomic platform is able to drive sideways. However, it first has to turn its wheels.
Non-holonomic robots have two differentially driven wheels and one or two passive caster wheels, e.g., the Pioneer P3- DX, or four or more differentially driven wheels, e.g., the Pioneer P3-AT. As is recognized, however, in Asfour et al (2006); Fuchs et al (2009); St uckler and Behnke (2009), this is not very beneficial for manipulation and maneuvering in tight spaces.
The semi-omnidirectionality of the robots in Wyrobek et al (2008); Fuchs et al (2009); Stückler and Behnke (2009) is obtained using steering wheels, i.e., four individually driven steerable drives. Each drive has either one or two wheels, hence the total number of motors required for a platform is either eight or twelve. This large number of actuators is the main drawback of these platforms.
Therefore, a base using either Mecanum wheels or omni wheels is an interesting alternative.
These wheels have small rolls on their circumference, allowing the wheels to move freely in axial direction (in case of omni-wheels) or under an angle (in case of Mecanum wheels). In Wyrobek et al (2008), it was argued that these fully holonomic platforms did not perform sufficiently robust in the presence of doorway thresholds, curbs and extension cords. Nevertheless, fully holonomic platforms are also successfully used in Iwata and Sugano (2009) and Hermann et al (2013).
As is mentioned in Fuchs et al (2009), platforms with more than three wheels are statically overdetermined and hence require some form of suspension in order to maintain good ground contact. Wheel suspension is not specifically addressed in Iwata and Sugano (2009); Stückler and Behnke (2009); Hermann et al (2013). Rollin' Justin (Fuchs et al, 2009) has an independent wheel suspension system. An example of addingcompliance using a rotational degree of freedom between the front and rear axis can be found in, e.g., Bischoff et al (2011).
-
UPPER BODIES
The successor of the design in Wyrobek et al (2008) and the robot in Stückler and Behnke (2009) are equipped with telescopic spines. This results in a large vertical motion while keeping the center of gravity (CoG) in the middle of the robot. On the other hand, the robots in Asfour et al (2006); Ott et al (2006); Iwata and Sugano (2009); Hermann et al (2013) have rotational DoFs. The upper bodies in Asfour et al (2006); Iwata and Sugano (2009); Hermann et al (2013) each have one actuator per joint, whereas one of the DoFs in Ott et al (2006) is passive, i.e., the tilt of the chest is coupled to the base via tendons. The main advantage of having a pitch joint is that the robot can move its shoulders further forward, as is indicated in Ott et al (2006). In our experiences with
AMIGO, the absence of a pitch joint is indeed a drawback: the robot needs to be positioned very accurately with respect to an object to allow a feasible grasping motion.
For large tilt motions, however, care has to be taken to prevent the robot from tipping over. In Fuchs et al (2009), this is solved by using a variable footprint, increasing the required number of actuators and the complexity and therewith the costs of the system. An alternative approach is presented in Hermann et al (2013), where a stability measure is optimized in motion planning. However, the safety of the robot preferably does not depend on software.
-
MANIPULATORS
One of the key abilities of a service robot is the ability to transport objects. Hereto, the robots are all equipped with manipulators. These manipulators typically have up to seven degrees of freedom and most manipulators are either mechanically compliant or have torque sensors so that the controllers enable compliant control.
The robots in Ott et al (2006); Weisshardt et al (2010) have industrial robot arms with seven DoFs and harmonic drives. The arms in Ott et al (2006) are equipped with torque sensors to allow compliant control. Both arms, however, are too large and too heavy for a dual arm domestic robot. The robot in Hermann et al (2013) has arms with six DoFs using three Schunk Powerballs, lacking the possibility to do compliant control. The arms of the robot in Stückler and Behnke (2009) are actuated by Dynamixel servo actuators. Although these have a compliant mode in which they are backdrivable, true impedance control is not possible. The robots in Wyrobek et al (2008) and Iwata and Sugano (2009) also have seven DoFs but are mechanically compliant.
Although recent developments show that variable-stiffness actuation is a promising research direction, it is concluded that a rigid arm with torque sensors leads to a simpler design of both hardware and controllers. To keep the compact design and anthropomorphic appearance, a design with differential joints similar to, e.g., Le Tien et al (2007); Rijs et al (2010) is desired.
Compared to the current manipulators, a number of possible improvements is identified: i) reduce the backlash in the differential joints, ii) improve the absolute position sensors and iii) redesign the I/O to be compatible with the rest of the robot.
-
MECHANICAL PLATFORM BASE
To design a domestic service robot the following requirements need to be fulfilled:
-
To minimize the number of required actuators for an omnidirectional platform, the base is fully holonomic, i.e., it has either omni wheels or Mecanum wheels. With respect to costs, it is furthermore desired to i) use o
-the-shelf parts whenever possible and ii) design parts in such a way that production costs decrease with increasing production volumes.
-
Since the robot is supposed to operate in domestic and care environments, it must be able to match human walking velocities up to v = 2.0 m/s = 7.2 km/h. To come to a timely stop in case of unexpected events, the robot must be able to accelerate to this velocity in 0.5 s, hence a = 4.0 m/s2. To
compute the required motor torques, the weight budget in Table 1 has been used.
-
The width of the robot is limited to 600 mm to easily fit through doors.
-
The robot must be able to drive through wheelchair- accessible areas. This implies that a vertical edge may up to 6 mm and a beveled edge with a slope up to 1 : 2 with a height up to 13 mm are allowed.
-
To keep traction even at rigid, uneven surfaces, the wheels must be compliantly suspended.
Table 1: Estimated mass of the various body parts.
-
-
MECHANICS
The difference between omni wheels and Mecanum wheels is the angle on which the rollers are placed on the wheel. Compared to omni wheels, Mecanum wheels have a number of advantages. With the same total width and wheel size, a Mecanum wheel platform has a wider track and a longer wheelbase (0.55 m) compared to an omni wheel platform (0.46 m), resulting in a more stable platform (see Figure 1).
Figure 1: Schematic layout of an omni-wheel and an Mecanum wheel platform. As is indicated by the red dashed lines, the Mecanum wheel platform is more stable and has more space available for peripheral equipment compared to the omni wheel platform.
Together with a more favorable position of the motors this also results in more space for peripheral equipment. Finally, driving over doorway thresholds is smoother because the wheels roll along their circumference instead of the circumference of the small rollers.
Although some of the robots are equipped with a spring damper system to handle uneven floors, no specific attention has been paid to the resulting driving characteristics.
Nevertheless, as is well-known in the automotive industry, suspension design has a great influence on, e.g., the camber and castor angles over the wheel travel, the roll center height and dive and squat properties.
Therefore, various suspension concepts have been considered, with one or both axles mounted to the chassis with a rotational DoF, crossed bars and an independent
suspension. Of these concepts, the independent multi-link suspension was selected. The main advantage of this concept is that the wheels will always be perpendicular to the surface, i.e., when the robot is accelerating in any direction as well as when driving over obstacles (see Figure 2). This prevents vibrations that are otherwise introduced. A second advantage is that the center of the base platform is not occupied by suspension parts.
The suspension geometry has been optimized using extensive dynamic simulations of the robot accelerating and driving over doorsteps of 15 mm. During the doorstep simulations, both compression and rebound of the wheels reached 20 mm but the camber angles remained below 0.3 degrees. During normal use, i.e., driving over a smooth floor with a maximum acceleration of 2.5 m/s2, wheel compression and rebound are around 5 mm and as a result the camber angle stays below 0.1 degree.
Figure 2: Rear view of the base: the multi-link suspension is designed to keep the wheels perpendicular to the ground in all three situations.
XI. CONCLUSION
A lot of knowledge about the service robots is already available. The main problem is that it is concentrated in research institutions and not shared as open-source hardware. That leads to slower development and optimization and higher cost. The goal in service robots for domestic use should be open-source development.
REFERENCES
-
Asfour T, Regenstein K, Azad P, Schröder J, Bierbaum A, Vahrenkamp N, Dillmann R (2006) ARMAR-III: An integrated humanoid platform for sensory-motor control. In: Proceedings of the IEEE-RAS International Conference on Humanoid Robots, pp 169-175
-
Bischoff R, Huggenberger U, Prassler E (2011) Kuka youbot – a mobile manipulator for research and education. In: IEEE International Conference on Robotics and Automation, pp 1-4
-
Fuchs M, Borst C, Giordano P, Baumann A, Kraemer E, Langwald J, Gruber R, Seitz N, Plank G, Kunze K, Burger R, Schmidt F, Wimböck T, Hirzinger G (2009) Rollin' Justin- design considerations and realization of a mobile platform for a humanoid upper body. In: Proceedings of the IEEE International Conference on Robotics and Automation, pp 4131-4137
-
Graf B, Hans M, Schraft R (2004) Care-O-bot II – development of a next generation robotic home assistant. Advanced Robotics 16(2):193-205
-
Ha I, Tamura Y, Asama H (2013) Development of open platform humanoid robot DARwIn-OP. Advanced Robotics
-
Hermann A, Sun J, Xue Z, Ruehl S, Oberlaender J, Roennau A, Zoellner J, Dillmann R (2013) Hardware and software architecture of the bimanual mobile manipulation robot hollie and its actuated upper body. In: IEEE/ASME International Conference on Advanced Intelligent Mechatronics, pp 286-292
-
Iwata H, Sugano S (2009) Design of human symbiotic robot TWENDY-ONE. In: IEEE International Conference on Robotics and Automation, pp 580-586
-
Le Tien L, Schaffer A, Hirzinger G (2007) Mimo state feedback controller for a flexible joint robot with strong joint coupling. In: Proceedings of the 2007 IEEE International Conference on Robotics and Automation, pp 3824-3830
-
Metta G, Sandini G, Vernon D, Natale L, Nori F (2008) The icub humanoid robot: An open platform for research in embodied cognition. In: Workshop on Performance Metrics for Intelligent Systems, pp 50-56
-
Ott C, Eiberger O, Friedl W, Bäuml B, Hillenbrand U, Borst C, Albu-Schäffer A, Brunner B, Hirschmüler H, Kielhöfer S, Konietschke R, Suppa M, Wimblöck T, Zacharias F, Hirzinger G (2006) A humanoid two-arm system for dexterous manipulation. In: Proceedings of the IEEE-RAS International Conference on Humanoid Robots, pp 276-283
-
Reynolds C, Wyatt J (2011) Open source, open standards, and health care information systems 13(1), URL http://www.ncbi.nlm.nih.gov/pmc/articles/PMC3221346/
-
Rijs R, Beekmans R, Izmit S, Bemelmans D (2010) Philips experimental robot arm, user instruction manual v1.1. Tech. Rep.
APT536-09-9962, Philips Applied Technologies
-
Schwarz M, Schreiber M, Schueller S, Missura M, Behnke S (2012) NimbRo-OP humanoid teensize open platform. In: Proceedings of the IEEE-RAS International Conference on Humanoid Robots
-
Stückler J, Behnke S (2009) Integrating indoor mobility, object manipulation, and intuitive interaction for domestic service tasks. In: Proceedings of the IEEE-RAS International Conference on Humanoid Robots, pp 506-513
-
Weisshardt F, Reiser U, Parlitz C, Verl A (2010) Making high- tech service robot platforms available. In: Joint International Symposium on Robotics and German Conference on Robotics, vol 2, pp 1115-1120
-
Wyrobek K, Berger E, Van Der Loos H, Salisbury J (2008) Towards a personal robotics development platform: Rationale and design of an intrinsically safe personal robot. In: Proceedings of the IEEE International Conference on Robotics and Automation, pp 2165-2170
AUTHORS BIOGRAPHY
Zlata Jelai is Assistant Professor in Department of Mechanics at the Faculty of Mechanical Engineering, University of Sarajevo, Bosnia and Herzegovina. PhD thesis was in the field of rehabilitation robotics, namely the development of an active above-knee prosthesis with actuated knee and ankle joints.