
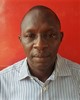
- Open Access
- Authors : S. O Alebiosu , J. O. Odubunmi , A. Muhammed Raji , T. F Samson
- Paper ID : IJERTV10IS120159
- Volume & Issue : Volume 10, Issue 12 (December 2021)
- Published (First Online): 04-01-2022
- ISSN (Online) : 2278-0181
- Publisher Name : IJERT
- License:
This work is licensed under a Creative Commons Attribution 4.0 International License
Evaluation of Physical and Mechanical Properties of Polypropylene and Cockle Seashell Composite
S.O Alebiosu, J. O. Odubunmi, A. Muhammed Raji, T.F Samson
Department of Polymer and Textile Technology,
Yaba College of Technology, P.M.B 2011, Yaba, Lagos, Nigeria.
Abstract:- Calcium carbonate is one of the most common fillers used in compounding of Polypropylene.Cockle seashell, a bioresource rich in calcium carbonate and readily found along the seacoast wasgrounded to fine particle size and sieved to obtain a mesh size of 150micrometer. Cockle seashell powder was compounded with polypropylene keeping the weight of polypropylene constant at 50gwhile increasing the filler loading of seashell. Seashell powder was added to the polypropylene matrix ranging from 5g – 50g. The samples were prepared using a compression molding machine. Ten samples were prepared without compatibilizer and another ten samples were prepared with Maleic Anhydride as a compatibilizer. A control sample of pure polypropylene was also prepared. The mechanical properties such as tensile strength, flexural strength, hardness and elongation at break of the samples were analyzed. Tensile strength of PP/SS samples with Maleic anhydride increased steadily and at PP/SS (50/30) had the highest tensile strength of while PP/SS samples without Maleic Anhydride had better elongation at break.PPcomposite incorporated with compatibilizer had low flexural values compared to PPcomposite without compatibilizer. However, there was no significant difference in the hardness property of the compositeswith and without compatibilizers.
1.0 INTRODUCTION
Polypropylene (PP) is a polymer obtained from the polymerization of propylene and regarded as one of the commodity polymers in high demand. It has found application both in technological and domestic end use. Technological reasons are often the basis for using particulate fillers in Polypropylene which gives a new material with enhanced properties such as improved stiffness and higher heat deflection temperature.[1]Fillers used in polypropylene are glass fibre, talc or magnesium and calcium carbonate. [1].Calcium carbonate (CaCO3) is the utmostplentiful white mineral in the earth's crust. It's white, odorless, nontoxic, soft and has a low refractive index, and ittemperature is stable across a wide temperature range.CaCO3is a mineral filler which is formed in rock types such as limestone and chalk.[2]. Calcium carbonate from biological wastes such as sea shells, (cockles, scallops, marine mollusks, mussels, shellfish, oysters) and egg shellscan be alternativefillers for polymer composites. They are discarded in large quantities by food processing companies. [3]. Cockle is an edible marine bivalve mollusk which belong to the family of Cardiidae. They are found in sandy sheltered beaches throughout the world. [4]. Cockle seashell (SS)is found on the beaches across the world and contain a significant amount of bio-Calcium carbonate. The amount of calcium Carbonate present in cockle shell has been estimated to range from 92% – 98%. [5 9].Some researchers have employed bio calcium carbonate as fillers for thermoplastics such as polyethylene and polypropylene. Seashell treated with NaOH was used as a filler for polypropylene. The tensile strengths of the composites were compared with composites filled with mineral CaCO3. The PP/SS composite showed better tensile strength than the PP/ Calcium carbonate. [10]. Low Density Polyethylene (LDPE) composites were prepared using cockle shell as fillers. The LDPE composites with cockle shell had higher Young Modulus value than the pure LDPE. [11].Improved tensile strength and hardness was reported for natural rubber filled with bio-CaCO3by Norazlina et.al. [12]. This work aims to examine the properties of using CaCO3 from sea waste (designated as bio-CaCO3) as a replacement for synthetic CaCO3 to be incorporated into PP and evaluate the physical and mechanical performance of the bio- composites. The mechanical properties evaluated concentrated on the tensile strength, flexural strength, hardness and elongation at break of the bio-composites.
-
MATERIALS AND METHODOLOGY.
-
Materials
Cockle shells were obtained from Sultan Beach, Badagry, Lagos state, Nigeria. Polypropylene pellets obtained from a chemical company in Lagos was used. Maleic Anhydride (MA) of analytical grade was gotten from a chemical company in Lagos.
-
Methodology
-
Preparation of the Cockle shell particulate filler.
The cockle shells were washed thoroughly with water to get rid of dirt, and oven dry at a temperature of 100°C over 2 hours. It wasat that point taken to a grinding mill to be milled into small particles. The amount of cockle shell obtained was 20kg and after milling, it reduced to 19.5kg. The milled cockle shell was then sieved with a British standard sieve mesh to obtaina particle size of 150µm.
-
Preparation of the composite
The polypropylene pellets were first masticated with a two-roll mill for about 5 minutes at a temperature of 110OC after which the cockle shell particulate filler was added and also masticated together for another 5 minutes.The temperature was kept constant until a fine homogenous mixture was obtained. The mixture was allowed to cool for 24 hours. The mixture was then compression molded in a hydraulic press at a temperature of 160OC for about 5 minutes. paraffin wax was added to the mould
before placing the mixture in the hydraulic press.Ten samples of compatibilized composites and ten samples of composites without compatibilizerwere produced in a dumbbell shape. The samples mechanical properties were analyzed.
Table 1: Formulation for Polypropylene/Cockle Shell Composite without compatibilizer
SAMPLE
POLYPROPYLENE(g)
COCKLE SEASHELL(g)
A1
50
5
B1
50
10
C1
50
15
D1
50
20
E1
50
25
F1
50
30
G1
50
35
H1
50
40
I1
50
45
J1
50
50
-
-
Tensile Strength and Flexural strength
Mechanical properties of the blends wereinvestigated using computerized universal testing machine (Instron series 3369) with a load cell 50KN. ASTM D680/ASTMD 790 three point bending test was used to determine the flexural strength. The span length was 65mm. The dimension of the specimen for the tensile strength was 70mm by 5mm by 15mm.
Table 2:Formulation for Polypropylene/Cockle Shell Composite with compatibilizer
SAMPLE CODE
POLYPROPYLENE(g)
COCKLE SHELL PARTICULATE (g)
MALEIC ANYHYDRIDE(2g)
A2
50
5
2
B2
50
10
2
C2
50
15
2
D2
50
20
2
E2
50
25
2
F2
50
30
2
G2
50
35
2
H2
50
40
2
I2
50
45
2
J2
50
50
2
-
Hardness Test
The Durometer OS2H 04081401 was used to determine the hardness properties of the blends.The durometer's indentor pin was placed very close to the sample on a metallic base. The durometer's load was pulled down to allow the indentor pin to penetrate the sample. On the display screen, the sample's resistance to indentation was measured, and the value was recorded. This was repeated three times for each sample, with the average value taken.
3.0 RESULTS AND DISCUSSION
16
TENSILE STRENGHT OF COMPOSITES MPA
TENSILE STRENGHT OF COMPOSITES MPA
14
12
10
8
6
4
2
0
A B C D E F G H I J K SAMPLES
S-S & PPE Compactibilizer (S-S & PPE) Control Sample
Figure 1: Tensile strength of pristine PP, PP/SS and PP/SS/MA Composites
From Figure 1, it can be observed that the tensile strength of the composites is lower at smaller filler concentrations. There was a gradual increase in the tensile strength values of the composites as the filler loading increased to 15g relative to pristine PP. Optimal tensile strength (14.64MPa) was observed with the incorporation of 2g of MA into the composite PP: SS (50:30), after which there was a decrease in the tensile property of the composites. Maleic anhydride addition to the composites increased the interaction between the polymer matrix and the particulate filler. Similar trend was observed by Mumusamil et al. [11]. In this study, the tensile strength was significantly better than the control sample, (pristine PP).
30
Flexural strenght (MPa)
Flexural strenght (MPa)
25
20
15
10
5
0
A B C D E F G H I J K
Axis Title
Sea-Shell & PPE Compactibilizer (S-S & PPE) Control Sample
Figure 2: Flexural Strength of Composite samples
Figure 2 shows the flexural strength of the pristine PP and its composites. At 30% SS loading, composites without Maleic anhydride had better flexural strength, (25.3MPa). Increasing the filler loading above 30%, the flexural strength of the composites decreased. PP/SS/MA composites had low flexural strength at lower filler loading, but at 60% filler loading, the
flexural strength was optimal after which a gradual decline was observed in the flexural strength. Sakahara et al,[13], reported similar findings where the flexural strength of their composites was higher than that of isotactic polypropylene. This the authors attributed to the particle size of the filler. The higher filler loadings might have reduced the interaction of the maleic anhydride with the hydrophilic polymer and hydrophobic filler thereby causing a decline in the flexural strength.
96
94
92
90
Hardness
Hardness
88
86
84
82
80
78
A B C D E F G H I J K
samples
S-S & PPE Compactibilizer(S-S & PPE) Control Sample
Figure 3: Hardness of Composites Samples
From Figure 3, the hardness of the composites both compatibilized and un-compatibilized steadily increased with increase in filler loading. The presence of bio-CaCO3increased the stiffness of the polymer matrix. An opposite trend is observed in the elongation of break of thecomposites in Figure 4. The un-compatibilized compositeshad higher elongation at break percentage compared to the compatibilized composites.This indicates that the un-compatibilized composites had better ductility. This might be attributed to the dispersion of the filler within the polymer matrix.Salmah et al,[13] reported that the elongation at break reduced with increase in filler loading in EPDM/PP/CaCO3 composites.
3.5
elongation at break of samples
elongation at break of samples
3
2.5
2
1.5
1
0.5
0
A B C D E F G H I J K
samples
S-S & PPE Compactibilizer (S-S & PPE) Control Sample
Figure 4: Elongation at break of samples
4.0 CONCLUSION
Particulate fillers such as CaCO3 is used extensively in polypropylene to improve its mechanical properties as well as reduce the production costs. Cockle shell, a bioresource with high CaCO3 deposits has been used in this study in place of mineral CaCO3 and the mechanical and physical properties were observed to be better than the pure polypropylene. Incorporating Maleic anhydride into the composites of polypropylene/cockle shell boosted the tensile strength and flexural strength, as the interfacial adhesion amid the polymer matrix and the filler was improved. Though at higher filler add-ons, there was a decline in these values. Cockle shell/polypropylene compositesis proposed to be used for automobile interior and exterior application and any other suitable applications..
REFERENCES
-
Bela Pukanszky(1999), Polypropylene: An A- Z Reference, published by Kluwer publishers
-
M.M.H. Al Omari, I.S. Rashid, N.A. Qinna, A.M. Jaber and A.A. Badwan, (2016) Calcium Carbonate. In: Harry G. Brittain, editor, Profiles of Drug Substances, Excipients and Related Methodology, Vol. 41, Burlington: Academic Press, 2016, pp. 31-132.
-
Stephen Owuamanam and Duncan Cree, 2020, Progress of Bio-Calcium Carbonate Waste Eggshell and Seashell Fillers in Polymer Composites: A Review, journal of composite science. Volume 4, Pg 70.
-
Jung, J.H.; Shon, B.H.; Yoo, K.S.; Oh, K.J. Physicochemical characteristics of waste sea shells for acid gascleaning absorbent. Korean J. Chem. Eng.
2000, 17, 585592.
-
Lertwattanaruk, P.; Makul, N.; Siripattarapravat, C. Utilization of ground waste seashells in cementmortarsfor masonry and plastering. J. Environ.
Manag. 2012, 111, 133141
-
Olivia, M.; Oktaviani, R. Properties of concrete containing ground waste cockle and clam seashells.Procedia Eng2017, 171, 658663.
-
Mohamed, M.; Yusup, S.; Maitra, S. Decomposition study of calcium carbonate in cockle shell. J. Eng. Sci.Technol. 2012, 7, 110.
-
Olivia, M.; Mifshella, A.A.; Darmayanti, L. Mechanical properties of seashell concrete. Procedia Eng. 2015,125, 760764.
-
Li, H.Y.; Tan, Y.Q.; Zhang, L.; Zhang, Y.X.; Song, Y.H.; Ye, Y.; Xia, M.S. Bio-filler from waste shellfish shell:Preparation, characterization, and its effect on the mechanical properties on polypropylene composites. J.
-
Munusamil, Y.; Sumathi, S.; Chi, H.C. Potential use of waste cockle shell as filler for thermoplasticcomposite. J. Mater. Cycles Waste Manag. 2019, 21, 10631074, doi:10.1007/s10163-019-00867-9.
-
H. Salmapa, A. Siti Rohana2b, H. Kamarudin, 2014. Effect Maleic Anhydride Polypropylene on Properties of Calcium Carbonate Filled Polypropylene/Ethylene Propylene Diene Terpolymer Composites. Key Engineering Materials Vols. 594-595 (2014) pp 770-774
-
H. Norazlina, R.M. Firdaus andW.M. Hafizuddin, 2015,CaCO3 from seashell as a reinforcement for natural rubber. J. Mech. Eng. and Sci. 8, 1481 1488.
-
Rogerio Sakahara, Aurianny Lima and Shu Hui Wang, 2014. Influence of the Beta Crystalline Phase Fraction on the Mechanical Behavior of Polypropylene/calcium Carbonate/ polypropylenegraftmaleic Anhydride Composites