
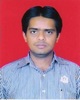
- Open Access
- Authors : Abdul Mateen , D Shaik Meera
- Paper ID : IJERTV11IS010007
- Volume & Issue : Volume 11, Issue 01 (January 2022)
- Published (First Online): 07-01-2022
- ISSN (Online) : 2278-0181
- Publisher Name : IJERT
- License:
This work is licensed under a Creative Commons Attribution 4.0 International License
Unsteady Flow and Heat Transfer of Viscous Immiscible Fluids Between Two Parallel Plates
Abdul Mateen*
Department of UG & PG Studies in Mathematics Government Womens First Grade College, Gulbarga, Karnataka, India
D Shaik Meera
Department of Mathematics
Bellari Institute of Technology and Management Bellari, Karnataka, India
AbstractThis paper studies the unsteady flow and heat transfer of two viscous immiscible fluids between two parallel plates. The partial differential equations governing the flow and heat transfer are solved analytically using two-term harmonic and non-harmonic functions in both fluid regions of the channel. Effects of physical parameters such as height ratio, viscosity ratio, conductivity ratio, Prandtl number, Eckert number, periodic frequency parameter and pressure on the velocity and temperature distributions are given and illustrated graphically
KeywordsUnsteady flow, heat transfer, immiscible fluids, oscillatory pressure gradient
NOMENCLATURE
A real positive constant
CP specific heat at constant pressure
g gravitational acceleration
K thermal conductivity
P pressure
Ec Eckert number
Pr Prandtl number
T temperature
Tw wall temperature
-
time
-
velocity components of velocity along the plate.
U0 average velocity
Greek letters
fluid density
vis cosity of fluid
coeffiecient of periodic parameter
frequency parameter
-
INTRODUCTION
Problems involving immiscible multi-phase flow and heat transfer and multi-component mass transfer arise in a number of scientific and engineering disciplines. Important applications include petroleum industry, geophysics and plasma physics. In modeling such problems, the presence of a second immiscible fluid phase adds a number of complexities as to the nature of interacting transport phenomena and interface conditions between the phases. In general, multi- phase flows are driven by gravitational and viscous forces. There has been some theoretical and experimental work on stratified laminar flow of two immiscible fluids in a horizontal pipe ,[1,2]. [3] studied two-phase MHD flow and heat transfer in a parallel plate channel, with one of the fluids being electrically conducting. Two-phase MHD flow and heat transfer in an inclined channel was investigated by [4]. Later on convective magnetohydrodynamic two-fluid flow and convective flow and heat transfer in composite porous medium was analysed by [5,6]. Fully developed flow and heat transfer in horizontal channel consisting of an electrically conducting fluid layer sandwiched between two fluids layers is studied analytically by [7]
All the above studies pertain to steady flow. [8-11] have presented analytical solutions for unsteady/oscillatory two-fluid and three-fluid flow and heat transfer in a horizontal channel. However, most problems of practical interest is unsteady. Keeping in view the wide area of practical importance of unsteady multi-fluid flows as mentioned above, it is the objective of the present study to investigate unsteady flow and heat transfer of twofluid model in a horizontal channel.
-
MATHEMATICALFORMULATION
Consider a two dimensional unsteady flow of two immiscible fluids in a horizontal parallel permeable plates, extending in the Z and X direction. The region 0 y h
t periodic frequency parameter
kinematic viscosity
nondimensional tempeaure
(Region-I) is filled with a viscous fluid having density , dynamic viscosity , specific heat at constant pressure
1
1
1
1
C thermal conductivity K and the region h y 0
P1 1
Subscripts
1,2 quantities for Region-I and Region-II respectively
(Region-II) is filled with a different viscous fluid having density 2 , dynamic viscosity 2 , specific heat at constant
pressure CP2 and thermal conductivity K 2 .
The flow of both regions is assumed to be fully developed and fluid properties are constant and driven by a
P
h
h 2
P
2
2
common pressure gradient 1 in region-I and by pressure
u U u *
y hy *
t t * P i
x
i 0 i
i U x
P
T T C
1 0
U 2
(7)
gradient 2 in region-II . The two plates are maintained
w2
Pr 1 p
Ec 0
p
p
w1
w1
x
Tw1
Tw2 K1
C T
Tw2
at constant temperatures Tw at y h and Tw
at y h.
1 2
1
1
Under these assumptions and taking
2 0
and for simplicity dropping the asterisks, equations (1) to (6) becomes
and
Cp1
Cp Cp the governing equations of motion and
2
2
energy (Loharsbi and Sahai, 1988) are given by:
Region-I
u 2u
1 1 P
(8)
Region-I
t y 2 1
u 2 u p
1 2
u
2
2
1
1 1
(1)
1 1 Ec 1
(9)
0 t
1 y 2 x
t Pr y2
y
T 2T
u 2
Region-II
Cp 1 K
1 1
(2)
0 t
1 y 2
2 y
u 2u
2 m 2 P
(10)
Region-II
t y2 2
2
2
b 2 u
u 2 u p
2 2 Ec m 2
(11)
2
2 2
(3)
t Pr y2
y
0 t
2 y 2 x
K
T 2T
u 2
where
m 2
is the ratio of viscosities and
b 2
is the
Cp 2 K
2 2
(4) 1 K1
0 t
2 y 2
2 y
ratio of thermal conductivities.
The hydrodynamic and thermal boundary and
where u is the x-component of fluid velocity, v is the y- component of fluid velocity and T is the fluid temperature. The subscripts 1 and 2 correspond to region-I and region-II, respectively. The boundary conditions on velocity are the no- slip boundary conditions which required that the x-component of velocity must vanish at the wall. The boundary conditions
interface conditions for both fluids in non-dimensional form become
1
1
u 1 0
2
2
u 1 0
u 0 u 0
(12)
on temperature are isothermal conditions. We also assume the 1 2
continuity of velocity, shear stress, temperature and heat flux
u1 m u2
at y 0
at the interface between the two fluid layers at y=0.
The hydrodynamic boundary and interface conditions for the two fluids can then be written as
y y
1
1
1 1
1
1
u h 0
2
2
u h 0
u1 0 u2 0
(5)
1 0
2
2
1 2
1 2
0 0
1 2
1 2
b
at y 0
(13)
u1
1 y 2
u2
y
at y 0
y y
-
SOLUTIONS
The thermal boundary and interface conditions on temperature for both fluids are given by
T h T
The governing equations (8) to (11) are solved subject to the boundary and interface conditions (12) and (13) for the velocity and temperature distributions in both regions.
1
2
2
T h
w1
Tw2
Thee equations are partial differential equations that cannot
be solved in closed form. However, it can be reduced to
T 0 T 0
(6)
ordinary differential equations by assuming
1 2
K T1 K
1 y 2
T2
y
at y 0
u y,t u
j
j
j
j
y,t
y eit u
j 0
j 0
j 0
j 0
y eit
j1
ji1
y
y
(14)
(15)
P y,t P y eit P y
(16)
j j 0 j1
By use of the following non-dimensional quantities:
where j-1,2 for region-I and region-II respectively.
By substitution of equation (14) to (16) into Non-periodic coefficients
equations (8) to (13), one obtains the following pairs of equations:
Region-I
Non-periodic coefficients
1 1
10
10
20
20
1 0
20
20
10
10
0
0
(28)
d 2 u
b
at y 0
10 P
(17)
10 20
10 20
y y
dy 2
d 2
10
u 2
Periodic coefficients
10 Pr Ec 10 0
(18)
dy 2
Periodic coefficients
d 2u
y
(19)
1 0
11
11
21
21
1 0
21
21
11
11
0
0
(29)
11 iu P
(20)
dy2
11 11
11 b 21
at y 0
d 2
du du
y y
11 i Pr u
2Ec 10 11 0
(21)
dy2
Region -II
11 dy dy
Equations (17) to (25) along with boundary and interface conditions (26) to (29) represent a system of ordinary differential equations and conditions that can be solved in
Non-periodic coefficients
d 2u P
closed form. Since the solutions can be obtained directly, the expressions are not presented. The results are depicted
20 20
(22)
graphically and are discussed in the next section.
dy2 m
2
2
d 2 m du
-
RESULTS AND DISCUSSION
-
20 Pr Ec 20 0
(23)
b
b
dy2
Periodic coefficients
dy
In this section representative, flow results for oscillatory flow and heat transfer of two immiscible fluids between two parallel plates are presented and discussed for various
d 2u
21 i
dy2
d 2
u
u
m 21
Pr
P21
m
2 Pr Ec du
du
(24)
parametric conditions. The flow governing equations cannot be solved exactly. However the closed form solutions were found considering the cosine function for frequency parameter
21 i
20 21 0
(25)
on velocity and pressure is assumed. The solutions are
dy2
b 21
b dy dy
depicted graphically in Figs. 1 to 7 for different values of viscosity ratio, periodic frequency parameter and pressure on
The corresponding boundary and interface conditions become
as follows:
Non-periodic coefficients
10
10
u 1 0
20
20
20
20
u 1 0
the flow and thermal conductivity ratio, Prandtl number and Eckert number on temperature field. The parameters are fixed as 1 except the varying one, Pr=0.7, Ec=0.5 and t =450.
Figure 1 shows that velocity profiles are suppressed for large values of viscosity ratios. The flow profile is large in region-II compare to region-I, and the similar effect observed for different values of viscosity ratio on temperature profile as
u10
0 u
0
(26)
shown in Fig. 2.
u10 m u20
at y 0
Figure 3 and 4 observed that the variation of periodic
y y
frequency parameter t on velocity and temperature profiles
respectively, as t increases the flow increases, the
Periodic coefficients
t increases temperature profiles is also increases in both the
u11 u21 u11
1 0
1 0
21
21
0 u
0
(27)
regions, since the solutions are approximated by function of since the solutions are approximated by exponential function of t .
u u
Keeping in view the physical model of the flow of two
11 m 21
at y 0
immiscible fluids such as water and oil in petroleum
y y
industries, a study is made to know the effect of pressure on the flow as shown Fig.5. We have considered different values of pressure for two fluids separately. For positive values of pressure on upper and lower fluids, the flow is promoting. For positive values of pressure in the lower region and negative values of pressure in the upper region display the effect of
1.0
1.0
Region-II
Region-II
2.0
2.0
1.0
1.0
m=0.5
m=0.5
0.5
0.5
maximum velocity in region-I. On the other hand if we take negative values of pressure in lower region and positive values of pressure in the upper region also show the maximum velocity in region-I itself but the flow direction is opposite. Assigning negative values of pressure also show the similar effect to that for positive values of pressure except in opposite direction. It is observed that controlling the pressure parameter one can also control the direction of flow, which has immense applications in flow reversal problems.
y 0.0
y 0.0
Region-I
Region-I
-0.5
-0.5
The effect of thermal conductivity ratio is depicted in Fig. 6. As the ratio increases the magnitude of suppression is large in region-I compared to region-II. This is obvious because the upper plate is maintained at a low temperature compared to region-I.
-1.0
-1.0
0.0
0.0
0.7
0.7
1.4
1.4
2.1
2.1
2.8
2.8
3.5
3.5
u
Fig.1 Velocity profiles for different values of viscosity ratio m
u
Fig.1 Velocity profiles for different values of viscosity ratio m
Figures 7 and 8 display the effect of Prandtl number and Eckert number respectively on temperature filed. It is seen that temperature is increases with increase in Prandtl number as well as Eckert number. Since the values of Prandtl number are very small for liquid and metals and it is very high for highly viscous fluid.
Thus one can conclude that the flow can be controlled by considering different fluids having different viscosities, periodic frequency and applying different pressures.
REFERENCES
-
Alireza Setayesh and V. Sahai, Heat transfer in developing magnetohydrodynamic poiseuille flow and variable transport properties, Int. J. Heat Mass Transfer, 33, 1711-1720, 1990.
-
M.S. Malashetty, and V. Leela, Magnetohydrodynamic heat transfer in two phase flow, Int. J. Engg. Sci., 30, 371-377, 1992.
1.0
1.0
-
J. Lohrasbi, and V. Sahai, Magnetohydrodynamic heat transfer in two phase flow between parallel plates, Appl. Sci, Res, 45, 53-66, 1988.
Region-II
Region-II
-
M.S. Malashetty, and J.C. Umavathi, Two phase Magnetohydrodynamic flow and heat transfer in annclined channel, Int. J. Multiphase flow, 23, 545-560, 1997.
0.5
0.5
-
Malashetty M.S., Umavathi J.C. and Prathpkumar J, Two fluid magnetoconvection flow in an inclined channel. Int. J. Transport Phenomena, 3, 73-84. 2001.
y 0.0
y 0.0
-
Malashetty M.S., Umavathi J.C. and Prathpkumr J., Convective magnetohydrodynamic two fluid flow and heat transfer in an inclined channel. Heat and Mass Transfer, 37, 259-264, 2001.
Region-I
Region-I
m=0.5
m=0.5
1.0
1.0
2.0
2.0
-0.5
-0.5
-
Umavathi, J. C., Malashetty. M.S. and Abdul Mateen, Fully developed flow and heat transfer in a horizontal channel containing electrically conducting fluid sandwiched between two fluid layer, Int. J. Applied Mechanical Engineering, 9, 781-794, 2004.
-
Umavathi, J.C., Chamkha, A.J., Abdul Mateen, Mudhaf, A.A., Unsteady two-fluid flow and heat transfer in a horizontal channel, Heat Mass Transfer, 42, 8190, 2005.
-1.0
-1.0
0
0
1
1
2
2
3
3
4
4
Fig.2 Temperature profiles for different values of viscosity ratio m
Fig.2 Temperature profiles for different values of viscosity ratio m
-
Umavathi, J.C., Abdul Mateen, Chamkha, A.J. and Mudhaf, A.A., Oscillatory Hartmann two fluid flow and heat transfer in a horizontal channel, International Journal of Applied Mechanics and Engineering, 11(1), 155178, 2006.
-
Umavathi., J.C., Shaik Meera. D. and Liu IC., Unsteady flow and heat transfer of three immiscible fluids, International Journal of Applied Mechanics and Engineering, 13(4), 1079-1100, 2008.
-
Umavathi, J.C., Chamkha, A.J., Mateen, A., Mudhaf, A.A., Unsteady oscillatory flow and heat transfer in a horizontal composite porous medium channel, Nonlinear Analysis: Modelling and Control, 14(3), 397415, 2009.
45, 135
90
0
1
2
3
4
5
u
Fig.3 Velocity profiles for different values of periodic frequency parameter t
10 11
20 21
P =P =-1.0
P =P =-1.0
20 21
10 11
20 21
P =P =-1.0
0.0
0.5
1.0
1.5
2.0
2.5
u
Fig.5 Velocity profiles for different values of pressure P
0.0
0.7
1.4
2.1
2.8
3.5
u
Fig.4 Temperature profiles for different values of periodic frequency parameter t
1.0
-1.0
0
1
2
3
4
5
Fig.6 Temperatur profiles for different values of conductivity ratio b
Fig.6 Temperatur profiles for different values of conductivity ratio b
5
4
3
2
1
0
-1.0
1.0
u
Fig.4 Temperature profiles for different values of periodic frequency parameter t
3.5
2.8
2.1
1.4
0.7
0.0
u
Fig.5 Velocity profiles for different values of pressure P
2.5
2.0
1.5
1.0
0.5
0.0
P =P =-1.0
20 21
10 11
20 21
P =P =-1.0
P =P =-1.0
20 21
10 11
u
Fig.3 Velocity profiles for different values of periodic frequency parameter t
5
4
3
2
1
0
90
45, 135
1.0
1.0
1.0
1.0
Region-II
Region-II
Region-II
Region-II
P =P =-1.0
P =P =-1.0
P =P =1.0
P =P =1.0
0.5
0.5
0.5
0.5
t=0, 180
10 11
t=0, 180
10 11
y 0.0
y 0.0
y 0.0
y 0.0
Region-I
Region-I
Region-I
Region-I
P =P =1.0
P =P =1.0
P =P =1.0
P =P =1.0
-0.5
-0.5
P =P =1.0
10 11
-0.5
-0.5
P =P =1.0
10 11
20 21
20 21
-1.0
-1.0
-1.0
-1.0
1.0
1.0
1.0
1.0
Region-II
Region-II
Region-II
Region-II
0.5
0.5
2.0
b=0.5
0.5
0.5
2.0
b=0.5
t=0, 180
45, 135
90
t=0, 180
45, 135
90
y 0.0
y 0.0
y 0.0
y 0.0
Region-I
Region-I
Region-I
Region-I
-0.5
-0.5
-0.5
-0.5
-1.0
-1.0
1.0
1.0
1.0
1.0
Region-II
Region-II
Region-II
Region-II
Pr=0.0001
Pr=0.0001
0.5
0.5
0.5
0.5
0.4
0.7
0.4
0.7
Ec=0.1
0.2
0.3
Ec=0.1
0.2
0.3
y 0.0
y 0.0
y 0.0
y 0.0
Region-I
Region-I
Region-I
Region-I
-0.5
-0.5
-0.5
-0.5
-1.0
-1.0
-1.0
-1.0
0.0
0.0
0.5
0.5
1.0
1.0
1.5
1.5
2.0
2.0
2.5
2.5
3.0
3.0
3.5 4.0
3.5 4.0
Fig.7 Temperatur profiles for different values of Prandtl number Pr
Fig.7 Temperatur profiles for different values of Prandtl number Pr
0
0
2
2
4
4
6
6
8
8
10
10
Fig.8 Temperatur profiles for different values of Eckert number Ec
Fig.8 Temperatur profiles for different values of Eckert number Ec
.