
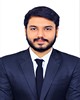
- Open Access
- Authors : Jeet Shah , Ashutosh Chowdhary , Deep Patel , Dhruv Thakker, Umang Talaviya, Pavit Shah
- Paper ID : IJERTV11IS010204
- Volume & Issue : Volume 11, Issue 01 (January 2022)
- Published (First Online): 04-02-2022
- ISSN (Online) : 2278-0181
- Publisher Name : IJERT
- License:
This work is licensed under a Creative Commons Attribution 4.0 International License
Cooling Techniques of Solar Photovoltaic Panels: A Critical Review
Jeet Shap
Student
Dept. of Mechanical Engineering L.D.R.P- I.T.R Gandhinagar, India.
Ashutosh Chowdhary2
Student
Dept. of Mechanical Engineering L.D.R.P- I.T.R Gandhinagar, India.
Deep Patel3
Student
Dept. of Mechanical Engineering L.D.R.P- I.T.R Gandhinagar, India.
Dhruv Thakker4
Student
Dept. of Mechanical Engineering L.D.R.P- I.T.R Gandhinagar, India.
Umang Talaviya5
Student
Dept. of Mechanical Engineering L.D.R.P- I.T.R Gandhinagar, India.
Pavit Shap
Student
Dept. of Mechanical Engineering L.D.R.P- I.T.R Gandhinagar, India.
Abstract:- Photovoltaic Technology seems to be one of the fastest- growing technologies on a global scale to solve the energy crisis. To improve photovoltaic (PV) panels' efficiency, one of the ways to do so is to maintain the correct working temperature for maximum yield of energy. This paper involves discussion of newly developed cooling methods such as cooling by nanofluids, heat sink by thermoelectric modules and radiative cooling methods which are very efficient for cooling. Moreover, the techniques which require more research and adaptivity like radiative cooling and methods of cooling for Floating PV panels are discussed. This paper comprises the classification, construction, working, brief representation of these cooling systems, readings of efficiency, maximum power outputs for a range of temperatures, factors affecting the output power of PV, and the conclusions to help choose the correct cooling technology for novel PV, ultra-high concentrated PV panels as well as for Floating PV panels.
Keywords: PV panel cooling, Water cooling techniques,
Active and Passive cooling, PCM cooling, Floating PV method, Cooling by Nanofluids.
Abbreviations: Photovoltaic- (PV), Computational Fluid Dynamics- (CFD), Phase Change materials- (PCM), Earth Tube Heat Exchanger- (ETHE), High concentrator photovoltaic- (HCPV), Ultra high concentrator photovoltaic- (UHCPV), Low pressure- (LP), High pressure- (HP), Photovoltaic Thermal system (PVT), Floating photovoltaic panel- (FPV), Membrane Distillation- (MD), Vapor Compression refrigeration- (VCR), Concentrated photovoltaic system- (CPV), Thermoelectric module- (TEM), maximum power point tracking- (MPPT), Watts- (W).
-
INTRODUCTION
In today's world, the energy crisis and pollution caused by decades of usage of fossil fuels have become a global issue and to solve this issue, the world needs adaptivity towards more safe, clean, and renewable energy sources. Amongst these renewable energy sources, Solar energy is a well organized and most used renewable power source which harnesses power
from the radiations of the Sun with the help of a solar cell. This solar cell or photovoltaic cell directly converts light radiation into electricity with the help of semiconductor materials by the principle of photovoltaics [01]. Solar cells can be made up of many materials and Silicon is the most abundantly used material for its manufacturing.
There are two types of energy that can be produced from solar energy: electrical energy and thermal energy. The electrical energy can be produced by using photovoltaic (PV) cells. The PV cell directly converts the incident solar irradiance to electricity. The most efficient, sustainable, and eco-friendly systems are the PV modules which convert small parts of the solar irradiance to electricity. The remaining part of the excessive solar irradiance and high ambient temperature overheats the PV panel and this heat is waste heat which proportionally decreases the working efficiency, maximum power output, and also the working life of solar cells [10],[27]. It is demonstrated that an increase of temperature by 1°C can decrease the efficiency of a silicon-based PV panel by 0.5% [19]. The efficiency of PV panels in certain conditions is the most efficient around 25°C surface temperature [20]. Hence, it becomes a necessity to control the working temperature range by the effective cooling of PV panels. Therefore, choosing a cooling solution could increase the life of solar cells as well as increase the working efficiency and power output of solar cells. These cooling techniques are mainly classified as active cooling methods and passive cooling methods.[13]. All such cooling methodologies have been critically reviewed and analyzed in this paper.
-
CLASSIFICATION OF COOLING TECHNIQUES AND METHODOLOGY
These PV panel cooling techniques have been classified mainly on the basis of Active cooling techniques and Passive cooling techniques. The representation below shows a brief classification of various other techniques categorized under Active and Passive methods.
Figure 1. Classification of Cooling Techniques.
-
Active air-cooled PV panels:
The cooling of PV panels by the techniques with air as cooling medium using power for fans or blowers are categorized under active cooling of PVs by air. Such techniques are discussed below:
-
Active air-cooling using fans:
Erhan Arslan et al. [12] conducted an energy and exergy analysis of a novel PV panel was done by Computational Fluid Dynamics testing (CFD) on a monocrystalline Photovoltaic Thermal collector panel and using air as cooling media through the newly designed copper fins structure. The air is drawn at different mass flow rates adjusting the radial speed of fans and the outlet is provided at the upper side of the tilted PV panel. The testing was done at two variable speeds of fans achieving the mass flow rates of 0.031087 kg/s and 0.04553 kg/s respectively. According to the laws of conduction and heat transfer, higher mass flow rates resulted in more heat transfer rate. Thus, cooling the panel more efficiently. The setup of such an air-cooled system is represented in figure 2.
Figure 2. Setup of cooling of PV panel using fan. [12] Therefore increasing the fan speed showed a more efficiently cooled system in CFD analysis. These CFD results display a temperature gradient through which the cooling and temperature drop can be easily observed. It was concluded that as the mass flow rates increased, the surface temperature of PV panels decreased and hence the efficiency increased by 0.42% in practice, whereas the numeric results by CFD showed an increase of 0.63%, calculating the data for the given
comparison of working environment for the above stated mass flow rates.
-
Cooling of Photovoltaic roof tile by air ducts:
The air passes through the cross-sectional area of the air ducts made in a wood casing just fixed below the solar PV tile for the experimental setup. The air flows through the duct size with various volumetric ranges by flow of air through the blower.
Figure 3. Design of PV roof tile ducts. [14]
The air circulates and conducts heat which is entrapped on the backside of such roof tiles used in buildings. By the laws of heat transfer, the air dissipates the heat through and out of the air duct path, which in turn results in the cooling of tiles. Furthermore, by varying the cross section of the air inlet opening of the duct, more or less air can be transferred through varying duct depths which provides varying mass flow rates for the duct system.
Results for this experiment were based on parameters like Various Volumetric ranges (V) were considered with respect to different solar irradiances and the readings of temperatures taken were in account of 3 conditions:
-
Without cooling.
-
Drawing and circulating air from a depth of 51mm air duct
-
Drawing and circulating air from an air duct of 25mm depth.
Figure 4. Graph of PV roof tile temperature – solar irradiance. [14]
Increase in mass flow rate of air can increase Thermal efficiency from 28% to 55% and Electrical efficiency from
10.6% to 12.2% approximately. Increasing mass flow rate of air and decreasing the depth of air duct size can result in better overall efficiency which is stated by Equation of Continuity.
-
-
Cooling of PV panel by an Earth tube heat exchanger: A heat exchanger is used to transfer heat between two fluids and used in both heating and cooling applications. It was observed by Nethra MR et al. [20] that the temperature of the soil at 10 m depth of earths crust remains at higher temperature than the ambient temperature during winter and at lower temperature during summer.
The Earth Tube Heat Exchanger (ETHE) uses the geothermal source to cool the working fluid air. This heat exchanger works on a simple setup with a pipe surrounded by the ground soil at a certain depth of around 10 m. As the temperature below the surface is low, a blower is used to circulate air through the air duct/ pipe which carries the relatively cool air from the depth below the ground level further delivering it out to the backside of the PV panel. This flow of cooled air is used to drop the temperature of PV panels in the working range. The setup of such ETHE is represented below in figure 5.
Figure 5. Design of earth tube heat exchanger for PV panel cooling. [20]
For this heat exchanger design, efficiency of the pipe increases for the cooling of the PV panel which increases the power output proportionally and with the addition of the fins, the convective heat transfer rate also increases with lower pressure drop.
-
-
Active water cooling of PV panels:
The cooling of PV panels by the techniques using water as cooling medium using power for water springs and pumps are categorized under active cooling of PVs by water. Such techniques are discussed as follows:
-
Active cooling of PV panel using water cooling tower: This research by Zhijun Peng et al. [31] is aiming to investigate practical effects of solar PV surface temperature on output performance, in particular efficiency. The setup for this experiment comprises the solar PV panel setup with a cooling water channel on the backside. This cooling water is pumped from the lower side of the channel and this absorbs heat as the water acts as the cooling media. Further, this water gets heated and is collected in the hot water tank which can be either recirculated through the cooling tower or also could be used
for household purposes. This hot water can be cooled in the cooling tower using the ventilated outlets and inlets for cool air. This setup is discussed below in figure 6.
Figure 6. Setup of PV panel cooled by cooling channel connected to cooling tower. [31]
Experimental works were carried out under different radiation conditions for exploring the variation of the output voltage, current, output power and efficiency in real time conditions. As test results show the efficiency of solar PV can have an increasing rate of 47% with the cooled condition, a cooling system is proposed for possible system setup of residential solar PV application. The system performance and life cycle assessment suggest that the annual PV electric output efficiencies can increase up to 35%, and the annual total system energy efficiency including electric output and hot water output can increase. The cost payback time can be reduced to 12.1 years, compared to 15 years of the baseline of a similar system without a cooling sub-system.
-
Active cooling of PV panel using multiple cooling techniques with water as cooling medium:
Most of the researches widely use two techniques; one is to enhance the efficiency of the solar PV cell and another to ensure a longer life span at the same time. The work carried out by Shrey Verma et al. [26] explains the cooling methods i.e., heat sink, heat pipe, PCM material based, microchannel, thermoelectric (Peltier). The setup of this experiment comprises an aluminum plate integrated on the backside of a PV panel. The microchannels with V ribs are integrated on this aluminum sheet with a coating of Thermal silica gel (PCM). The water is circulated in these microchannels from upper liquid headers and it dissipates heat from the backside of PV panels integrated with an Aluminum plate and flows to the lower liquid header. The Aluminum plate helps to conduct more heat transfer between the channels and the PV panel. The microchannels have a thermal silica gel coating acting as a phase change material. The setup of the microchannel is represented in figure 7.
Figure 7. Setup of cooling of PV panel with multiple techniques with water as cooling medium. [26]
The finding of the review reveals that water-based microchannel gives efficient cooling besides hot water for various applications and combination with PCM make it more efficient in both electrical and thermal aspects.
-
Active cooling of multiple PV panels using cooling kit:
This experiment by André F.A. Castanheiraa et al. [07] presents the design and characterization of a water-cooling kit system specifically conducted for already existing and operating PV plants, but also takes into account various aspects of its potential as a commercial-scale product. In this experimental setup, the water is pumped through multiple paths which circulate water to sprinklers through control valves to sprinkle water on the upper side of PV panels, this water is further collected and circulated back to the water tank after filtration of water to remove particulate matter and impurities. Chlorine is also added in water tanks to avoid fouling of water. This setup is represented in figure 8.
Figure 8. Cooling of multiple PV panels using a cooling kit. [07]
Experiments showed how cooling/ heating thermal time constants of the PV panels and water ON/OFF time cycles affect PVs efficiency. A large amount of test data was produced and analyzed, showing how the cooling kit can increase annual energy production up to 12%.
-
Active cooling of HCPV and UHCPV using water with heat sinking fins and channels:
HCPV (high concentrator photovoltaic) and UHCPV (Ultra high concentrator photovoltaic) systems with high Solar concentration ratio are used to increase cell efficiency dramatically and it is needed to spend less in the highly expensive semiconductor materials used in cells. The cooling of HCPVs is very challenging as it attains high temperature during usage at high concentration of direct solar irradiance. Hence, Heat sink can be developed at the backside of the PV panel with this following setup presented by Woei-Chong Tan et al. [30].
Fins and channel spaces 3D design is shown in figure in which the water inlet flows with a high mass flow rate through the cross-sectional area formed by channels. This fins structure can be fabricated forming a casing of fins and when the water flows out, its temperature is elevated. Hence, by designing fins of optimum length, more contact surface area between the water and backside of the PV panel can be obtained resulting in a good cooling technology. Also, the substrate region can be added at the backside of PV panels with Al2O3 powder which can provide cooling.
Figure 9. Structural design of multiple fins channel for mass flow rate of water attached under PV panel. [30]
Use of this cooling method from this experiment showed that, by a feasible setting of thickness of fins, water velocity of inlet and outlet and fin height, the desired results can be attained. High number of fins can give more surface area to flowing water and can dissipate heat in larger amounts.
-
Active cooling using water spray technique on front and backside of PVs:
Direct surface cooling of PV panels using water is proven efficient for a single side. Thiseffectiveness and efficiency can be increased by cooling PV panels on both; front and back sides simultaneously. A cooling technique experiment by S. Nizetic et al. [22] was conducted to investigate the total water spray cooling effect on the PV panel performance in circumstances of peak solar irradiation levels. A specific experimental setup was elaborated in detail and developed as shown in figure in which water is sprayed on both the sides by a simple layout of water tubes kept on the periphery of the solar panel. Water can be regulated by controlling solenoid water
valves. This pulse sprayed water is heated and can be reused by collecting it.
Figure 10. Setup of PV panel cooling by water spray system on both sides. [22]
The experimental result shows that it is possible to achieve a maximal total increase of 16.3% in electric power output and a total increase of 14.1% in PV panel electrical efficiency by using the proposed cooling technique in circumstances of peak solar irradiation. Furthermore, it was also possible to decrease panel temperature from an average 54°C (non-cooled PV panel) to 24°C in the case of simultaneous front and backside PV panel cooling. Economic feasibility was also determined for the proposed water spray cooling technique, where the main advantage of the analyzed cooling technique is regarding the cooling of the PV panel's surface and its self-cleaning effect.
-
-
Cooling of PV panels by multipurpose hybridized plants: The techniques which have a secondary purpose other than cooling of PV panels are called hybridized cooling techniques. These techniques can use water or air as the cooling medium. Such techniques are explained below:
-
Desalination of seawater and cooling of PV by seawater:
There is a development of hybrid power plants which serves multiple purposes; in this power plant design by Alireza Abbassi Monjezi et al. [04], the desalination is the main purpose. But, also the cooling necessary for better performance of PV panels is done by the sea water. The visual setup is represented below in figure 11.
Figure 11. Hybrid setup of seawater desalination and PV panel cooling by sea water. [04]
A low-pressure (LP) pump is used to feed the seawater and is pumped to a sand lter providing an initial stage of ltration to remove the larger particles. The high pressure (HP) pump is then connected to the RO unit to provide the pressure driving force required to facilitate desalination through the semipermeable membrane elements. Both the LP and HP pumps are powered by the PV panel unit during day-time. The surplus electricity supplied by the PV panels during day-time is stored in the battery unit which supplies the LP and HP pumps during night-time.
Major outcome from this experimental study is, if the temperature of the feed water is raised by 5°C due to undergoing PV cooling, the specific energy consumption of the desalination unit is reduced by 0.12 kWh/m3 of desalinated water. Hence, providing an effective solution of increasing the overall efficiency of the plant.
-
Hybrid technique for cooling of building walls and PV panel by water:
An experiment was conducted by Albert Al Touma et al. [03] to cool down the room in a building from the water also cooling the PV panel, which in turn could increase the efficiency of the PV panel and decrease the energy load on the building.
Figure 12. Design of a hybrid system for cooling PV panels and building walls. [03]
The experimental study investigated the performance of hybrid passive cooling on fully glazed building walls of typical office specs for reducing temperature and the space thermal loads. This system as shown in figure below consists of a PV panel, evaporative cooler, evaporatively cooled building wall, a fan and a pump for cool outdoor air by force and reduces the surface temperature.
Readings are taken on model and experiment both and also applied in Doha Qatar for case study in real life condition, good result was found between the model and experiment as the maximum decrement in the hourly wall surface temperatures and space loads were 6.0% and 12.2%. In Qatar, with very hot and humid weather during summer, the result was the system is capable enough to save 14.5% building wall temperature and space load in a day to the total thermal energy demand.
-
Hybrid PV cooling and water heating system for domestic purposes:
In this system designed by Ahmad Zareia et al. [02], a Vapor compression refrigeration (VCR) system with a refrigerant is used with a heating system of water which also cools the PV panel. As shown in the figure, the water is first used to cool the PV panel, then the outlet water is used to sub-cool the refrigerant coming out of the condenser, and further the same outlet water cools the refrigerant in the condenser working as heat exchanger. Then as the water gets heated, it's further more heated in the auxiliary heater to a desired temperature and it can be used, whereas the refrigerant will be ready to be circulated through the evaporators and cool the room.
Figure 13. Block representation of proposed hybrid PV collector system for domestic solar cooling and heating. [02]
This system does 3 tasks: heating of water, cooling of PVs, cooling of a closed space room with refrigerant. The major figurative conclusions from this experiment were that Module temperature is decreased by 20% which increases its efficiency around 9% and exergy is increased by 5.17%.
-
-
Cooling of PV panels by nanofluids:
Graphene nanoparticles in fluid medium can act as a good cooling media on the back side (in contact) of PV panels. An experimental study by cooling PV panels circulating water around it showed results by increasing its effective efficiency by 50%. Another approach was to place a PV panel inside a pool like a small tank with cooling media at a depth which could decrease temperature from 65°C to 45°C. Nanoparticles have a large surface area to volume ratio as their size varies between 1-100 nm. These nanoparticles suspended in the water can increase the heat carrying capacity of water, thereby increasing heat transfer rate. Hence, the cooling could enhance as the concentration of nanoparticles would be high.
The setup for the experiment by T.S.Y. Moh et al. [28] is as follows: Fabrication of micro sized channels is done by molding using Poly-dimethyl siloxane (PDMS) with ratio 1:10. The experimental study was carried out and by comparing the results with water as cooling media, it was concluded that GNP nanofluids cooling shows highest effective efficiency gauged at roughly 42% compared to water cooling with solution being flown at 1.11 L/min flow rate and 54% increase if compared to non-cooling while operating temperature is less than 45°C.
For knowing the efficiency of the nanofluids available in market, experimental study was conducted by Ashij K. Suresha et al. [08] and the following results are discussed:
1. Al2O3 (0.2% wt.),
-
TiO2,
-
ZnO in deionized water,
4. MgO/water (0.1,0.2,0.6% wt.),
-
Polypyrrole,
-
Al2O3/water (0.3% wt.) in water as nanofluid at weight fraction of 0.2%,
-
Al2O3, CuO with water and Ethylene Glycol (0.1, 0.2, 0.4% wt.).
The best results were obtained by Al2O3, CuO with water and Ethylene Glycol (0.1, 0.2, 0.4% wt.) with 76.8% increase in thermal efficiency.
-
-
Active Heat Sink using Thermoelectric Module (TEM): As it is examined, the working of PV panels is suitable in the direct solar radiance but, electrical efficiency of PV panels is undesirably influenced by the rise in the panel temperature and accelerates cell degradation which leads to reduction of life expectancy of PV modules. Hence, the reduction of maximum power output is observed as the temperature of PV panels rises. Therefore, an effective solution to such an undesirable problem is to transfer the waste heat which would not nly decrease the temperature of PV panels but also use the waste heat effectively.
For cooling such systems, thermoelectric technology is appropriate for its integration adjacent to the PV module. Thermoelectric module (TEM) is attached at the back side of the PV module for absorption of the heat generated in the PV module by the infrared spectrum. Mathematical models for TEM are developed by consideration of temperature dependence of material properties. The setup is quite simple. The backside of the panel is attached to a conducting material sheet which absorbs excess heat from the PV panel through
conduction heat transfer and that heat is transferred for its application by the Thermoelectric module.
A temperature based maximum power point tracking (MPPT) scheme is presented for operating TEM at optimal temperature of a PV system. Analysis and design of MPPT scheme, current controller and converter are also discussed. The performance improvement of PV systems with thermoelectric cooling is presented through simulated results under the MATLAB environment to compute the adequate heat sinking from the PV system exposed to a wide spectrum other than visible light. The readings are taken based on isolation and varying temperature conditions with the help of the MPPT algorithm. Observing the power output results conclude that with 1 kW.m-
2 solar irradiance at 25°C surface temperature, the power output is 60W under cooling conditions. Whereas, without cooling it reaches 55°C for the same condition and power output drops to 52W. Also, between 38°C to 40°C, maximum power output observed is 54W.
-
Passive air cooling of PV panels:
The cooling of PV panels by the techniques with air as cooling medium and no need for power input for its working are categorized under passive cooling of PVs by air. A widely used technique using fin's structure to circulate air and passively cool PV panel is explained below:
-
Passive cooling of PV panels by fins:
Fins are extended surfaces on the cooling surface which can increase the heat transfer rate. If the backside of PV panels is integrated with fins made from conducting materials like Aluminum; the fins will increase the heat transfer rate by providing a deep channel for air flow. This increase in surface area for the volume of air proportionally will increase the rate of convection and heat dissipation with the help of natural air flow will be more.
Such fins integrating methods are not very useful as the rate of flow of natural air cannot be determined or maintained. Hence, the conclusion of results of cooling completely depends on the natural mass flow rate and geographic location where the PV panel is kept.
-
-
Passive water cooling of PV panels:
The cooling of PV panels by the techniques with water as cooling medium and no need for power input for its working are categorized under passive cooling of PVs by water. Such techniques are explained below:
-
Passive cooling of PV panel and domestic water heating:
Leonardo Jonas Piotrowskia et al. [16] observed that the Voltage and Power outputs decreased gradually with the increase in PV temperature. To maintain the working temperature of PV panels without input of any pump work for circulation of water, this technique is developed. In this method, cooling is done by conductive heat transfer on the backside of PV panels by using metal channels like Copper or Aluminum through a continuous water running jacket that can harness the heat and help heating the water for domestic use and also cool down the PV panels for better overall efficiency. Moreover, this method can be operated completely without the use of a pump if the water supplied to the water jacket is
supplied through a specific potential head height. This setup is represented below in figure 14.
Figure 14. Setup of passively cooled PV panel and water heating configuration. [16]
Further, experimental values with this setup could be obtained by calculating the Temperature of Module:
Tm = Ta + [(N-20)/800] * G
where,
Tm = Temperature of Module, Ta = Ambient temp,
N = normal working temp. of the cell, G = Solar irradiance value in W.m-2
As the setup discusses the flow of water on the backside in the water jacket, this heated water can be used for domestic purposes and the heat is not dissipated to the surroundings. Regarding the life of PV panels, if considered 25 years, the degradation rates of cells were decreased from 29.8% to 26.8% by this cooling technology in comparison to no cooling. Improvement of 3% in cell efficiencies by cooling which is a huge energy saving and lower degrading solution for a long- term life of PVs. Moreover, a technology to harness waste heat to heat domestic water.
-
Passive cooling of Concentrated Photovoltaic systems (CPVs) using water:
Concentrated Photovoltaic systems keep solar irradiance concentrated on polycrystalline silicon cells by solar tracking. Its water cooled in this system to achieve better performance. CPVs can use mirrors or lenses to concentrate solar radiations collectively incident on the face of PVs. Therefore, attaining more solar irradiance on a focal point heats the solar cells to a greater extent and hence arises a need for a better low power consuming cooling system. This CPV setup by Bin Du et al.
[10] with the visual representation of its CPV water tube is discussed in figures 15 and 16.Figure 15. Setup of passively cooled CPV using water. [10]
Figure 16. Water channel used for CPV cooling. [10]
This setup comprises water channels acting as heat pipes specially fabricated for CPVs. These water channels are arranged on the backside in a tilted manner to provide flow of water from an overhead water supply without needing any power supply for pumping. A drastic change in the temperature difference was observed under different temperature conditions that heat pipe cooling can give double outputs of overall efficiency than at no cooling of cells to ambient temperature rise of 46°C. And using parabolic reflectors show an overall efficiency of about 69% with 11% electrical efficiency, 58% thermal efficiency and an increased cell life for CPVs. Water cooled CPVs can give encouraging results with parabolic reflectors which are just a bit lower than the results given by Heat pipe cooled CPVs with parabolic reflectors.
-
Passive cooling of PV panel using gas expansion and rainwater:
For the cooling of PV panels, many different methods are available as per the purpose of use of panels. This is a technique fabricated by Shenyi Wu and Chenguang Xiong [25] in which the resin water and gas expansion device which distributes the rain water to the panel was used for the cooling of PV panels. Gas expansion devices expand the gas by using the solar radiations and give a flow to the rain water for spray on panel. The relationship of gas expansion chamber dimension, solar radiation and gas expansion volume established with respect to the variation of gas temperature and rain water sprayed through water spray pipes and nozzles was used for cooling solar panels. The block representation of setup is discussed below in figure 17.
Figure 17. Design of PV panel using gas expansion technique and rain water. [25]
This gas expansion technique was proven very effective to work passively with rain water usage. Maximum power output obtained with cooling was 215W compared to 192W without cooling. Also, the overall efficiency was achieved around 14.75% with cooling which was 13.5% without cooling. Readings show that by passive cooling the temperature decreases and efficiency is increased drastically and the payback period of the system is less than 14 years.
-
Passive evaporative cooling of PV panel and distillation of seawater by hybridized plant:
-
-
The Cogeneration of electricity and water distillation is done simultaneously by evaporative cooling in this technique by L. Huang et al. [15]. In the Membrane Distillation (MD) process, water evaporates at the warmer feed-side and condenses at the cooler permeate-side, during which the vapor will release latent heat at the cold side. Recovering the latent heat for further vapor generation is a very effective way to improve thermal efficiency. Furthermore, combining the interfacial heating design and multistage latent recovery have shown great promise for enhancing the overall water yield of the passive MD systems. In this experimental study, a compact and efficient solar thermal MD system, which obtained water productivity as high as 1.02 kg m2 hr1 with a solar efficiency of 72% under 1 sun illumination by recycling the latent heat. The panel functions under the solar irradiance throughout the day and produces electrical potential and heat energy. This heat energy is wasted, therefore by this method, it can be recovered and used for distillation. As shown in figure, the seawater drives into the evaporator placed right below the aluminum plate by the capillary force in the hydrophilic cotton layer. A thermal gradient is generated from the top to the bottom in the multistage MD by the heat from the PV panel. The condensate water will be drained to the freshwater basin by capillary force and gravity, And the remaining salt in the evaporator could be discharged by diffusion and gravity. while the released latent heat becomes available to drive additional evaporation in the next stage. At the bottom of the multistage MD, the evaporation cooler can remove waste heat of the entire system by evaporation cooling.
Figure 18. Setup of evaporating cooling of PV panel. [15]
By coupling the passively functioning multistage MD to the backside of the PV panel, the working temperature can be effectively reduced due to the cooling effect of evaporation. The temperature of the PV panel with 1-stage distiller was only
47.1 °C under one sun, which was largely lower than 63.5 °C without evaporation cooling. With the addition of the stage, the
temperature increased gradually to 54.3 °C at five stages, still
9.2 °C lower than the value without evaporation cooling.
-
Passive cooled PV panels by Phase change materials: Photovoltaic thermal systems (PVT) equipped with phase- change materials (PCM) are capable of benefiting from the storage when phase change happens. Phase change materials (PCM) like Paraffin wax have also been considered in PV- PCM passive based cooling applications besides air and water as the assumed coolants for the cooling application. Experimentally, the effect of PCMs deployment on the performance of an air-cooled photovoltaic system were investigated. Using these Phase change materials can help absorb heat from the air channel covered with an absorber plate. Effects of PCM were deliberated in a setup provided in which the PVT is equipped with a sheet of PCM.
Figure 19. Schematics of PV panel cooling using phase change materials and its components.[19]
The setup comprises: 1. Air channel, 2. PCM, 3. Absorber plate, 4. Aluminum oxide layer, 5. Photovoltaic panel, 6. Outlet air temperature sensors, 7. Inlet air temperature sensors,
8. Temperature sensors on the absorber plate, 9. Data logger,
-
Pyranometer, 11. Thermometer, 12. Positions of sensors on the absorber plate.
The experimental results by Müslüm Arici et al. [18] and Negin Choubineh et al. [19] indicate that using PCM sheets of six milli-meters thick leads to reducing the panel temperature to 4.3, 3.4, 3.6 and 3.7 °C in average in a natural flow mode, forcing high-velocity, medium and low velocity, respectively. Moreover, decreasing the temperature results in increasing the outlet power and electrical efficiency. Accordingly, it can be concluded that using PCMs leads to a significant increase in natural and forced convection situations. In general, PCMs that are used for latent heat storage have become a commonly used method in many applications, due to their ability to store significant amounts of thermal energy in comparatively small volumes. Comparing a PV-only system to a PV system incorporating a PCM, with thermophysical properties suitable to the PVs heat rejection, an increase of the PVs output by 9% was achieved.
-
-
Radiative cooling using emitter:
Radiative cooling (RC) is a renewable method of cooling objects passively and relies on a special channel called atmospheric window that has high transparency for thermal radiation, especially at the wavelength range of 814 m mid infrared wavelength. This RC cooling technology designed by
B. Zhao et al. [09] can be used for any sky facing object in
open air without any energy supply. The emitter for RC needs to face the sky, the emitter inevitably faces the sun. Unfortunately, the magnitude of solar radiation power is much larger than the emitter's net RC power. Thus, most emitters are heated up by the sun enough to completely counteract the emitters cooling effect. The key solution to achieve daytime RC is to maximally reduce the solar absorption of the emitter while maintaining its strong thermal emission. The experimental setup consists of a solar PV panel, an emitter, thermocouple and copper tubes.
Figure 20. Design of nighttime radiative cooling system. [09]
Figure 21. Setup of nighttime radiative cooling system. [09]
At daytime, electricity can be generated by the PV conversion process due to the intrinsic characteristic of the solar cell. Solar radiation is a collection of photons with different energies, and the electron will be freed if the energy of the absorbed photon is higher than the bandgap of the solar cell (e.g., semiconductor material-based solar cell). At nighttime, cooling energy and/or space cooling can be obtained by the nighttime RC method. This passive cooling phenomenon is essentially due to energy balance in accordance with the first law of thermodynamics. The sky, which is also called atmosphere, can be equivalently regarded as an object that is much colder than terrestrial ambient air. Hence, a sky-faced terrestrial object will be passively cooled down by sending heat to the colder sky by infrared thermal radiation. This cooled object can be used as a local cold source for various utilizations, including space cooling. PV-RC system carries out two functions with a PV conversion efficiency of 14.9% at daytime and net RC power of 72.94 W·m2 when the temperature of the PV-RC panel was equal to the ambient air temperature at nighttime. Using this, electricity can be produced in daytime and at night radiative cooling happens which reduces the temperature and other cooling systems such as air conditioners are not required.
-
Design of FPVs (Floating Photovoltaics panels) and their cooling techniques:
Floating PVs is an emerging technology of PV panels which float on water with its floating mechanism. This technology is
still in a developing stage and they have specially designed cooling systems to increase the efficiency.
Floating system comprises a Pontoon (a floating device with buoyancy which can help a heavy load to float with it) or separate floats (multiple hollow plastic or fiber structures which has their own buoyancy to make the load float), mooring system (to keep the floating load in its area; commonly works as the anchor for a ship), solar panels and water-resistant power cables. It cannot acquire land as they are placed on water, which can save the evaporation of water up to 40% for a freshwater reservoir storing water for needs all over the year. The floating system can be selected by factors like: The layout of the pond, lake or other water reservoirs. Commercial designs for floating PVs are kept on a raft-like structure which is close to water for cooling and it can move around to track the solar radiance. The basic design of the pontoon and solar floating panel is represented in figures 22 and 23.
Figure 22. Basic design of a pontoon. [05]
Figure 23. Floating PV panel. [05]
-
Active Water veil cooling system:
Water veil cooling system is a system of cooling of PV panels, as the water has a reflective index of 1.33 which is between that of glass and air, it doesn't block the solar radiance and allows solar radiations to reach the active cells. Hence, using water can be a good solution for cooling on its front face. In the water veil system, the water pipes are kept surrounding on the perimeter of the PV panel in such a way that water gets dripping out of the pipes through holes of small cross sections which cool the PV panel to a good extent. This system is represented below in figure 24.
Figure 24. Setup of active water veil cooling system.[21]
-
Active water sprinkler system:
Another method to cool PV panels on the face using water is a sprinkler system which pretty much uses garden sprinklers placed between panels and it sprinkles water on the face of PV panels keeping the surface temperature low and the cells actively intact working through solar radiation. This method is represented in the figure below and the working effects and the performance of this cooling technique is similar to water veil systems.
Figure 25. Setup of water sprinkler cooling system [21]
-
Passive evaporative cooling from backside of FPVs by water:
In this passive cooling technique, there is a simple black colored aluminum sheet attached at the backside of the FPV. As the water heats below the FPV and attains evaporation temperature, the vapors rise up and they form droplets on the aluminum plate. These droplets help cooling of FPVs maintaining moisture content.
Studying these methods, it can be concluded from these 3 techniques specially designed for FPVs; water veil system and sprinkler system could also be used for cooling of normal PVs. Although, the efficiency shows a high increase by water veil system and water sprinkler system; the passive evaporative cooling method operates only in a limited amount of time and its proven very less effective.
-
-
Improving efficiency of PV panels by passive oil coating:
M.M. Fouad et al. [17] studied by an experimental study that a new passive technique for cooling was observed recently which uses Oil as the cooling medium. This technique works by coating the front surface of the PV panel by a fine layer of oil in order to increase the amount of light transmitted to the panel, and consequently its efficiency.
Different types of oils are examined, including both mineral oils and natural oils. In the case of mineral oils; vacuum pump oil (Labovac oil), engine oil (Mobil oil) and brake oil (Abro oil) are examined, while in the case of natural oils; olive and sunflower oils are examined. An experimental setup was developed to examine the performance of the PV panels as a function of oil coatings. Oils generally increase the solar transmissivity but also in turn increases the temperature of the PV panel, hence it was not found that effective from a cooling perspective. It was observed that the output power was increased by 20% if the temperature and solar irradiance are maintained constantly with relation to solar transmissivity.
Therefore, it can be derived that for increasing the efficiency of PV panels using oil on the surface, it is required to also use a secondary system to cool the PV panel and maintain optimum temperature preventing cell degradation.
3. CONCLUSION
From various active and passive air- and water-cooling systems, it is observed that water absorbs and dissipates more amount of waste heat than air. Active water-cooling techniques require more power input than the air-cooling systems. But the water-cooled PV panels seem to maintain the working temperature of PV panels and give more power output as compared to air cooled PVs.
It is also observed that direct water spraying cooling systems are more efficient and require less water than the systems used to circulate and drain water through channels on the backside of PV panels. The heat transfer rate is much higher as the water droplets spread on the front surface evenly and directly conduct heat from the front surface of PV panels cooling the solar cells.
Hybridized cooling techniques which perform a secondary task using the waste heat other than cooling PV panels are found to be very efficient but also expensive. These systems can heat the room or provide air conditioning using a VCR system by the water used for cooling of PV panels. Hybridized cooling and distillation methods can also passively cool the PV panels from seawater by evaporative cooling and further provide distilled desalinated water. This method could be very useful in remote coastal areas where there is undersupply of power and a scarcity of potable water.
It is derived that the efficiency of water-cooled systems could be drastically improved by adding substances like Al2O3 in water substituting it as a nanofluid. This kind of nanofluids show more heat transfer rate and can cool the PV panels quickly and more efficiently.
Radiative cooling of PV panels is an emerging technology to cool down the PV panels during the daytime and this technology also cools down the room below the ambient temperature. This method is a next generation cooling method and it requires more research and adaptivity.
In the areas where the requirement of power is more and the area for PV panels is less like in multistorey buildings, solar roof tiles can be used on the building walls. These solar roof tiles are placed on the building walls and are cooled using the air ducts. This solar tile with air ducts can provide more energy efficiently for tall buildings keeping the inside temperature of the building low.
ACKNOWLEDGEMENT
We would like to express our sincere gratitude to Prof. Pavit Shah for sharing his experience with us and for giving his invaluable guidance and suggestions. We would also like to thank our parents and friends for continuously motivating us.
REFERENCES
-
A. Shukla, Karunesh Kant, Atul Sharma and Pascal Henry Biwole, Cooling methodologies of photovoltaic module for enhancing electrical efficiency: A review, Solar Energy Materials and Solar Cells, Volume 160, February 2017, 275-286.
-
Ahmad Zareia, Mohammad Liravi, Marzie Babaie Rabiee and Maryam Ghodrat A Novel, eco-friendly combined solar cooling and heating system, powered by hybrid Photovoltaic thermal (PVT) collector for domestic application, Energy Conversion and Management, Volume 222, 15 October 2020, 113198
-
Albert Al Touma and Djamel Ouahrani. Evaporative-cooled façade integrated with photovoltaic thermal panel applied in hot and humid climates, Energy, Volume 172, 1 April 2019, Pages 409-422
-
Alireza Abbassi Monjezi et al., Development of an off-grid solar energy powered reverse osmosis desalination system for continuous production of freshwater with integrated photovoltaic thermal (PVT) cooling , Desalination, Volume 495, 1 December 2020, 114679
-
Alok Sahu, Neha Yadav and K. Sudhakar, Floating photovoltaic power plant: A review, Renewable and Sustainable Energy Reviews,
Volume 66, December 2016, Pages 815-824
-
Amel F. Boudjabi, Djallel Abada, Nour El Houda Benbghila and RoumaissaGhoul, Experimental study of a hybridized photovoltaic panel, Energy Procedia, Volume 115, June 2017, Pages 290-297
-
André F.A. Castanheiraa, João F.P.Fernandes and P.J. CostaBranco, Demonstration project of a cooling system for existing PV power plants in Portugal, Applied Energy, Volume 211, 1 February 2018,
Pages 1297-1307
-
Ashij K. Suresha, Sahil Khurana, Gopal Nandan, Gaura Dwivedi and Satish Kumar, Role on nanofluids in cooling solar photovoltaic cell to enhance overall efficiency, MaterialsToday: Proceedings, Volume 5,
Issue 9, Part 3, 2018, Pages 20614-20620
-
B. zhao et al., Performance analysis of a hybrid system combining photovoltaic and nighttime radiative cooling, Applied Energy,
Volume 252, 15 October 2019, 113432
-
Eric Hu and Mohan Kolhe, Performance analysis of water cooled concentrated photovoltaic (CPV) system, Renewable and Sustainable Energy Reviews, Volume 16, Issue 9, December 2012, Pages 6732- 6736
-
Dirk Goossensa, Rickard Lundholm, Hans Goverde and Jonathan Govaerts, Effect of soiling on wind-induced cooling of photovoltaic modules and consequences for electrical performance, Sustainable Energy Technologies and Assessments, Volume 34, August 2019,
Pages 116-125
-
Erhan Arslan, Mustafa Akta and Ömer Faruk Can, Experimental and numerical investigation of a novel photovoltaic thermal (PV/T) collector with the energy and exergy analysis, Journal of Cleaner Production, Volume 276, 10 December 2020, 123255
-
H. M. Nguyen et al., Innovative methods of cooling solar panel: A concise review, (2019)
-
Jan Wajs et al., Air-cooled photovoltaic roof tile as an example of the BIPVT system. An experimental study on the energy and exergy performance, Energy, Volume 197, 15 April 2020, 117255
-
L. Huang et al., Solar-driven co-generation of electricity and water by evaporation cooling, Desalination, Volume 488, 15 August 2020, 114533
-
Leonardo Jonas Piotrowskia, Marcelo Godoy Simões, Felix Alberto Farret, Feasibility of water-cooled photovoltaic panels under the efficiency and durability aspects, Solar Energy, Volume 207, 1 September 2020, Pages 103-109
-
M.M. Fouad, M.M.Fouad and T.Khalil, Improving the efficiency of photovoltaic (PV) panels by oil coating, Energy Conversion and Management, Volume 115, 1 May 2016, Pages 1-7
-
Müslüm Arc, Feyza Bilgin, Sandro Nieti and Agis M.Papadopoulos, Phase change material based cooling of photovoltaic panel: A simplified numerical model for the optimization of the phase change material layer and general economic evaluation, Journal of Cleaner Production, Volume 189, 10 July 2018,
Pages 738-745
-
Negin Choubineh, Hamid Jannesari and Alibakhsh Kasaeian, Experimental study of the effect of using phase change materials on the performance of an air-cooled photovoltaic system, Renewable and Sustainable Energy Reviews, Volume 101, March 2019, Pages 103- 111
-
Nethra MR and Kalidasan B, Earth tube heat exchanger design for efficiency enhancement of PV panel, MaterialsToday: Proceedings,
Volume 45, Part 2, 2021, Pages 587-591
-
R. Cazzanigaa, M.Cicu, M.Rosa-Clot, P.Rosa-Clot, G.M.Tina and C.Ventura, Floating photovoltaic plant: Performance analysis and design solutions, Renewable and Sustainable Energy Reviews,
Volume 81, Part 2, January 2018, Pages 1730-1741
-
S. Nizetic et al, D.oko, A.Yadav, F.Grubii-abo, Water spray cooling technique applied on a photovoltaic panel, Energy Conversion and Management, Volume 108, 15 January 2016, Pages 287-296
-
S. Rashidi, Mehran Rajabi Zargarabadi and Saman Rashidi, An efficient pulsed- spray water cooling system for photovoltaic panels: Experimental study and cost analysis, Renewable Energy, Volume 164, February 2021, Pages 867-875
-
Sam Joseph Paul, Uddeshya Kumar and Siddharth Jain, Photovoltaic cells cooling techniques for energy efficiency optimization, MaterialsToday: Proceedings, Volume 46, Part 11, 2021, Pages 5458- 5463
-
Shenyi Wu and Chenguang Xiong,Passive cooling technology for photovoltaic panels for domestic houses, International Journal of Low-Carbon Technologies, Volume 9, Issue 2, June 2014, Pages 118 126
-
Shrey Verma, Subhashree Mohapatra, Subhankar Chowdhury and Gaurav Dwivedi, Cooling techniques of the PV module: A review, MaterialsToday: Proceedings, Volume 38, Part 1, 2021, Pages 253- 258
-
Swar A. Zubeer, H.A. Mohammed and Mustafa Ilkan A review of photovoltaic cells cooling techniques, Issue: E3S Web Conf. Volume 22, 2017, International Conference on Advances in Energy Systems and Environmental Engineering (ASEE17), Article number: 00205, Pages: 11.
-
T.S.Y. Moh, T.W.Ting and A.H.Y. Lau, Graphene Nanoparticles (GNP) nanofluids as key cooling media on a flat solar panel through micro-sized channels, Energy Reports, Volume 6, Supplement 2,
February 2020, Pages 282-286
-
Vishal Verma, Aarti Kane and Bhim Singh, Renewable and Sustainable Energy Reviews, Renewable and Sustainable Energy Reviews, Volume 75, August 2017, Pages 1295-1305
-
Woei-Chong Tan, Kok-Keong Chong and Ming-Hui Tan, Performance study of water-cooled multiple-channel heat sinks in the application of ultra-high concentrator photovoltaic system, Solar Energy, Volume 147, 1 May 2017, Pages 314-327
-
Zhijun Peng, Mohammad R.Herfatmanesh and Yiming Liu, Cooled solar PV panels for output energy efficiency optimisation, Energy Conversion and Management, Volume 150, 15 October 2017, Pages 949-955