
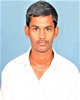
- Open Access
- Authors : Jyothi Prasad Gandreddi , Artis Kromanis , Andra Vamsi, Janis Lungevics, Krists Petersons , Diana Pukite, Kristine Viktorija Kule, Janis Kubulins, Igors Kristians Medvedevs
- Paper ID : IJERTV11IS030012
- Volume & Issue : Volume 11, Issue 03 (March 2022)
- Published (First Online): 08-03-2022
- ISSN (Online) : 2278-0181
- Publisher Name : IJERT
- License:
This work is licensed under a Creative Commons Attribution 4.0 International License
Surface Roughness Technological Assurance in Slot Milling
Jyothi Prasad Gandreddi, Artis Kromanis, Andra Vamsi, Janis Lungevics, Krists Petersons, Diana Pukite, Kristine Viktorija Kule, Janis Kubulins, Igors Kristians Medvedevs
Riga Technical University (RTU), Faculty of Mechanical Engineering, Transport and Aeronautics, Institute of Mechanical Engineering and Mechanical Engineering, Riga, Latvia
Abstract:- The research aims at investigation of surface roughness technological assurance in slot milling using various toolpath strategies. Surface roughness is one of the main quality assurance parameters and essential for surfaces that interact with each other during exploitation of any mechanism. In this study technological assurance was investigated on carbon steel material (C45) which has found wide use in mechanical engineering. Technological assurance involves adjustment of slot milling strategy and cutting parameters. Milling strategy involves a choose between different toolpaths: one-way slotting, two-way slotting and adaptive/trochoidal cutting. Cutting parameters to be adjusted are cutting speed, feed rate and depth of cut. Experiments were conducted on 3-axis CNC machine. The relation between the toolpaths, cutting parameters and surface roughness were analysed. From experimental results, it was concluded that the best surface roughness was obtained under increased cutting speed and low feed. This research identifies that the cutting parameters influence surface roughness and better surface roughness can be obtained at the proper cutting conditions. This study focuses on quality assurance and machine tool dynamics.
Keywords: Surface roughness; Slot milling; Feed rate; Cutting speed; Depth of cut; C45.
-
INTRODUCTION
CNC milling has become one of the most productive and flexible manufacturing methods, for complicated or sculptured surfaces. To design, optimize, built up to sophisticated, multi-axis milling centres, their expected manufacturing output is at least beneficial. Therefore, data, such as the surface roughness, cutting parameters and dynamic cutting behaviour are very helpful, especially when they are computationally produced, by artificial intelligent techniques. Predicting of surface roughness is very difficult using mathematical equations [1]. But it is possible to perform an experiment to evaluate. In milling, the most influential cutting parameters on Surface roughness (Ra) are cutting speed, feed rate and depth of cut [2].
Selecting the Variables
The dependant variable is the surface roughness (Ra), and the independent variables are the cutting speed, feed rate and depth of cut. Because these variables are controllable machining parameters, they can be used to calculate the surface roughness in vertical milling which will then improve the product quality. The variables are defined as follows:
-
Surface Roughness (Ra)
Surface roughness is one of the most important parameters to determine the quality of product. The mechanism behind the formation of surface roughness is very dynamic, complicated, and process dependent. Several factors will influence the final surface roughness in a CNC milling operations such as controllable factors (spindle speed, feed rate and depth of cut) and uncontrollable factors (tool geometry and material properties of both tool and workpiece) [3]. The surface roughness plays a great part in fatigue strength and corrosion resistance, surface friction, light reflection, ability of holding a lubricant, electrical and thermal contact resistance, appearance, cost, etc [4,5]. High quality of the surface after end milling makes further machining of the surface not necessary, which brings about decreased power consumption and environment load. However, optimization of surface roughness is consistently challenged by its uncertainty of prediction model as well as various influencing parameters, which can be divided into controlled and non-controlled parameters [6].
-
Cutting Speed
Metal cutting is one of the most significant manufacturing processes in material removal. Defined metal cutting is as the removal of metal chips from a workpiece to obtain a finished product with desired attributes of size, shape, and surface roughness [7]. Cutting speed of a milling cutter is its peripheral linear speed resulting from the operation. It is expressed in meters per minute. Spindle speed of a milling machine is selected to give the desired peripheral speed of cutter.
-
Feed Rate
It is the relative velocity at which the cutter is advanced along the workpiece. Feed rate is measured in mm/min [3]. The rate with which the workpiece under process advances under the revolving milling cutter. It is known that revolving cutter remains stationery and feed is given to the workpiece through worktable. Generally, feed is expressed in three ways[8].
-
Feed per Tooth
It is the distance travelled by the workpiece (its advance) between engagements by the two successive teeth. It is expressed as mm/tooth (ft).
-
Depth of Cut
Depth of cut in milling operation is the measure of penetration of cutter into the workpiece. It is thickness of the material removed in one pair of cutters under process. One pairs of cutter means when cutter completes the milling operation from one end of the workpiece to another end. In other words, it is the perpendicular distance measured between the original and final surface
of workpiece. It is measured in mm[8]. One reason for the popularity of the slot milling process is that it can be used for both rough and finish machining of components.
The second major problem which may result from the slot milling process is the generation of a finished part surface which does not satisfy product design specifications. A completed part surface may be excessively harsh or poor measurement precision. An unfortunate part surface may require extra machining, along these lines bringing down efficiency and expanding the expense of the generation. To produce parts which, conform to design specifications, proper machining conditions such as spindle speed, feed rate, depth of cut, cutter diameter, number of cutting flutes, and tool geometry must be selected.
The theory says that surface roughness generally increases with the increase of feed, concavity, and axial relief angles, while concavity angle is more than 2.5° [9].
-
-
SET UP OF EXPERIMENTS
Preparing the CNC milling machine system ready for performing the machining operation, milling of the work piece should be held properly in machine to hold strongly. The machine used for the milling process is a vertical machining centre GENOS M460-VE-e, which is specifically designed to manufacture high precision parts and deliver impressive metal removal rates in a compact design. Its solid double-column structure, full simultaneous control and thermal stability performance give it the ability to easily cut a variety of materials.
The work piece material used for the study is a rectangular C45 steel blocks. It is one of the main structural steels in circulation due to the excellent compromise between the characteristics of resistance and the toughness. It is a type of steel supplied to the natural, generally destined to reclamation treatment, a quenching followed by tempering at 600 ° C. The C45 is well suited for applications such as the construction of mechanical hard and tough as shafts, bolts, gears, bolsters, and under- molds.
The high-speed milling cutter of 8mm diameter is selected on the tool holder of the machine for milling.
The tool. The machining tool T13 is selected for the outcome of experimental work to study range of spindle speed, depth of cut and feed rate etc. This experiment gives the effect of different machining parameters (spindle speed, feed, and depth of cut) in slot milling.
CNC part program has been created on CNC professional software for tool paths, with specific commands using different levels of spindle speed, feed rate,
axial depth of cut and radial depth of cut, taking reference for Y axis, and Z axis then performing a slot milling operation.
For the machining process there are three different types of tool path programs has been created on CNC software program for slot milling. These tool paths involve in the machining process to observe the effects of cutting parameters on the work piece of the material. There are:
-
One-way slot milling the material removal takes place only in one direction. This type is the basic of all and can be used in machining of all types of materials. Tool movement in air is observed between every tool passes. This type is not suitable for mass production.
-
Two-way slot milling it is a continuous machining process and known as Zigzag. The material removal takes place continuously in two directions. No tool movement in air can be observed. This type is suitable for mass production.
-
Adaptive/Trochoidal slot milling it is a circular milling that includes simultaneous forward movements[12]. A wider slots than the diameter of tool[13] can be made by using this type.
For each tool path there was 15 experimental runs.
-
After each machining the surface roughness of the work piece being measured with the Mitutoyo surface tester. Surface tester. After the completion of machining process, the surface roughness of the workpieces is measured for further analysis. There are various surface roughness measurement techniques, by which in-process and post- process measurements can be taken. This is a measuring instrument that allows you to measure surface roughness easily and accurately.
The instrument used for present work was Mitutoyo Surf test SJ-2100. The measurements were obtained with the help of movement of stylus with diamond tip over the surface. The surf test SJ-2100 (Mitutoyo) is a shopfloor type surface- roughness measuring instrument, which measures the surfaces of various machine parts and calculates the surface roughness based on roughness standards and displays the results.
-
-
DESIGN OF EXPERIMENTS
The following table 1. shows all the methodologies and machining parameters used in this research.
Workpiece material
C45 (DIN)
Toolpath strategies
Two-way, One-way, Adaptive/Trochoidal
Feed rate (mm/tooth)
0.01, 0.02, 0.04, 0.06, 0.07
Cutting speed (m/min)
120, 170, 220
Axial depth of cut (mm)
1
Radial depth of cut (mm)
4
Cutting fluid
Air
Cutting tool
8mm carbide tool
CNC Vertical milling machine
OKUMA GENOS M460-VE-e
Surface measuring instrument
Mitutoyo Surf test SJ-2100
Table 1. List of parameters used in the experiments
For each tool path there was 15 experimental runs which all together makes 45 experimental runs.
-
RESULTS AND ANALYSIS
After conducting all the experiments, the results of it were explained below. The following Fig. 1. shows the measurement scheme of Ra, where arrows indicate the surface roughness profile measurement paths.
Fig. 1. Measurement scheme of surface roughness where arrows indicated surface roughness profile measurement paths. A indicates measurement scheme for adaptive/ trochoidal milling. O indicates a measurement scheme for one-way milling. T indicates a measurement scheme for two-way milling.
Cutting speed(v) m/min
Feed (ft) mm/ tooth
Surface roughness Ra along toolpath (One-way)
m
Surface roughness Ra along toolpath (Two-way)
m
Surface roughness Ra along toolpath overlapping (Two-way) m
Surface roughness Ra along toolpath (Adaptive) m
120
0.01
0.66
0.62
0.77
0.76
120
0.02
0.67
0.63
0.67
0.59
120
0.04
0.85
0.84
0.68
0.78
120
0.06
1.12
1.09
0.81
0.98
120
0.07
1.53
1.46
0.82
1.17
170
0.01
0.27
0.29
0.43
0.39
170
0.02
0.46
0.44
0.46
0.49
170
0.04
0.64
0.66
0.55
0.63
170
0.06
1.10
1.02
0.64
0.70
170
0.07
1.55
1.50
0.79
1.27
220
0.01
0.15
0.22
0.3
0.22
220
0.02
0.49
0.48
0.41
0.48
220
0.04
0.79
0.56
0.65
1.12
220
0.06
1.14
1.11
0.73
1.00
220
0.07
1.56
1.56
0.76
1.01
Table 2. Results of all the experiments.
From studying results of experiments (Table 2) it was concluded that
-
In all toolpath strategies which were used in this research, the lowest value (better) of Ra was obtained at a feed rate of
-
mm/tooth at respective cutting speeds.
-
-
At cutting speed of 120 m/min, the lowest (better) surface roughness value Ra 0.62 m was obtained in two-way toolpath strategy, the highest (poorest) surface roughness value Ra 1.53 m was obtained in one-way toolpath strategy and with increase in feed rate the Ra also increased gradually. The results obtained were almost identical up to a feed rate of 0.04 mm/tooth. The variation of results between the toolpath strategies was noticed at feed rate 0.06mm/tooth and above, the adaptive toolpath strategy resulted in better surface finish low surfaces roughness value Ra.
-
At cutting speed of 170 m/min, the lowest (better) surface roughness value Ra 0.27 m was obtained by means of a one- way toolpath strategy, the highest (poorest) surface roughness value Ra 1.55 m was also obtained by using a one-way toolpath strategy and with increase in feed rate the Ra also increased gradually. The results obtained were almost identical up to a feed rate of 0.04 mm/tooth. The variation of results between the toolpath strategies was noticed at feed rate 0.06mm/tooth and above, the adaptive toolpath strategy resulted in better surface roughness value Ra.
-
At cutting speed of 220 m/min, the lowest (better) surface roughness value Ra 0.15 m was obtained in one-way toolpath strategy, the highest (poorest) surface roughness value Ra 1.56 m was obtained in both one-way and two-way toolpath strategy and with increase in feed the Ra also increased gradually. The results obtained were almost identical up to a feed rate of 0.04 mm/tooth. The variation of results between the toolpath strategies was noticed at feed rate 0.06mm/tooth and above, the adaptive toolpath strategy resulted in better surface roughness value Ra.
Ra (m)
Ra (m)
Ra (m)
Ra (m)
-
The overall better surface roughness value Ra 0.15 m was obtained in one-way toolpath strategy at a cutting speed of 220 m/min and feed rate of 0.01 mm/tooth. The overall poor surface roughness value Ra 1.56 m was obtained in one- way toolpath strategy at a cutting speed of 220 m/min and feed rate of 0.07 mm/tooth. At low feed rates, the surface roughness value become better with increase in cutting speeds resulting in better surface.
1.6
1.2
0.8
0.4
0
1.6
1.2
0.8
0.4
0
1.6
1.2
0.8
0.4
0
1.6
1.2
0.8
0.4
0
0.01 0.02 0.04 0.06 0.07
Feed Rate (mm/tooth)
0.01 0.02 0.04 0.06 0.07
Feed Rate (mm/tooth)
0.01 0.02 0.04 0.06 0.07
Feed Rate (mm/tooth)
0.01 0.02 0.04 0.06 0.07
Feed Rate (mm/tooth)
One-way
Two-way
Adaptive
One-way
Two-way
Adaptive
One-way
Two-way
Adaptive
One-way
Two-way
Adaptive
-
(b)
1.6
1.2
Ra (m)
Ra (m)
0.8
0.4
0
0.01 0.02 0.04 0.06 0.07
Feed Rate (mm/tooth)
One-way Two-way Adaptive
(c)
Fig. 2. Comparison of surface roughness value with feed rate. (a) at cutting speed v=120m/min (b) at cutting speed v=170m/min (c) at cutting speed v=220m/min, X-axis refers to Ra m and Y-axis refers to feed rate (mm/tooth).
From Fig. 2. It is noticed that the surface roughness is gradually increased with increase in feed rate in all the toolpath strategies irrespective of cutting speeds except in adaptive toolpath strategy at cutting speed 220 m/min where Ra noticed at feed rate 0.04 mm/tooth is bigger than Ra at 0.05mm/tooth.
-
-
-
CONCLUSIONS
-
Surface roughness in slot milling is affected by technological parameters such as cutting speed, feed as well as toolpath strategy.
-
In slot milling of C45 using one-way toolpath strategy, the best surface roughness Ra 0.15 m was obtained using a cutting speed of 220 m/min and a feed of 0.01 mm/tooth (350 mm/min). The worst surface roughness Ra 1.56 m was obtained using a cutting speed of 220 m/min and a feed of 0.07 mm/tooth (2452 mm/min). In the result we may conclude that the most influential technological parameter on the surface roughness (Ra) is the feed.
-
In slot milling of C45 using two-way toolpath strategy, the best surface roughness Ra 0.22 m (along the toolpath), Ra
0.30 (orthogonal to the toolpaths) was obtained using a cutting speed of 220 m/min and a feed of 0.01 mm/tooth (350 mm/min). The worst surface roughness Ra 1.55 m (along the toolpath), Ra 0.76 (orthogonal to the toolpaths) was obtained using a a cutting speed of 220 m/min and a feed of 0.07 mm/tooth (2452 mm/min). Hence, the most influential technological parameter on the surface roughness (Ra) is the feed.
-
In slot milling of C45 using adaptive toolpath strategy, the best surface roughness Ra 0.22 m was obtained using a cutting speed of 220 m/min and a feed of 0.01 mm/tooth (350 mm/min). The worst surface roughness Ra 1.27 m was obtained using a cutting speed of 170 m/min and a feed of 0.07 mm/tooth (1895 mm/min). It can be concluded that the most influential technological parameter on the surface roughness (Ra) is the feed.
-
The lowest value of Ra was achieved in machining with low feed rate (0,01 mm/tooth) and at a speed range 220 and 170 m/min.
-
The difference of Ra because of toolpath strategy was not observed, so two-way toolpath and adaptive toolpath strategies can prefer over one-way toolpath strategy by considering the productivity. In one-way toolpath strategy, the tool moves in air between the two tool passes which results in high machining time.
-
For slightly rougher operations, the combination of high feed rates, high speeds, and the adaptive toolpath strategy could be preferred.
-
The combination of low feed and high-speed results in better surface roughness within the envelope of experiments.
-
Obtained results may be used for design of adaptive control CNC manufacturing cells were based on surface roughness measurements the cutting parameters may be adjusted to obtains the necessary surface roughness.
-
-
FURTHER RESEARCH
This research can be continued by evaluating waviness of the surface, because in certain applications waviness also plays an important role and by varying depth of cut. In future, there must be this kind of an experiment done using different CNC milling machines (also the horizontal ones) – knee-type, ram-type, producing or bed sort, and planer-type -, as all of them mill different. Most edge machines have self-contained electrical drive motors, fluid systems, variable spindle speeds, and power-operated table feeds. Also, there can be more different and interesting experiment results in other types of milling such as end milling, face milling, plain milling, profile milling, Helical milling (inward and outward), cam milling, and thread milling.
ACKNOWLEDGEMENT
The authors acknowledge Riga technical university for their support and for granting access to their manufacturing research facilities.
-
REFERENCES
-
Z.Zhang, J., C.Chen, J., Daniel Kirby, E. Surface roughness optimization in an end-milling operation using the Taguchi design method [online]. Iowa: University of Northern Iowa, 2006 [viewed 12 April 2020]. Available from: http://ariefsuwandi.weblog.esaunggul.ac.id/wp- content/uploads/sites/2412/2016/05/Mtb-Smaller.pdf
-
Gandreddi, Jyothi & Gerins, Eriks & Kromanis, Artis & Lungevics, Janis. (2020). Technological Assurance of Surface Roughness in Pocket Milling. 10.2507/31st.daaam.proceedings.080.
-
Agarwal, N. Surface Roughness Modeling with Machining Parameters (Speed, Feed & Depth of Cut) in CNC Milling [online]. MIT International Journal of Mechanical Engineering, 2015 [viewed 10 April 2020]. Available from: http://www.mitpublications.org/yellow_images/1347430634_logo_8.pdf
-
Shi-Jer, L. Development of four in-process surface recognition systems to predict surface roughness in end milling [online]. Iowa: Iowa State University, 1997 [viewed 11 April 2020]. Available from: https://lib.dr.iastate.edu/rtd/12004/
-
Lou, M. S., Chen, J.C., Li, C.M. Surface Roughness Prediction Technique for CNC End-Milling [online]. Journal of Industrial Technology, 1998 [viewed 8 April 2020]. Available from: https://link.springer.com/article/10.1007/s00170-008-1440-6
-
Yang, Y., Xinyu, L., Ping, J., Liping, Zh. Prediction of Surface Roughness in End Milling with Gene [online]. International Conference on Computers & Industrial Engineering, 2009 [viewed 10 April 2020]. Available from: https://pdfs.semanticscholar.org/efec/4e080d8930ccd5a8f96cefd85fa c9eac9e8f.pdf
-
Hayajneh, M. T., Tahat, M. S., Bluhm, J. A Study of the Effects of Machining Parameters on the Surface Roughness in the End-Milling Process [online]. 2007 [viewed 10 April 2020]. Available from: http://jjmie.hu.edu.jo/files/001.pdf
-
Thompson, R. Manufacturing Processes for Design Professionals [online]. 2007 [viewed 9 April 2020]. Available from: https://trove.nla.gov.au/work/8386587?q&versionId=9672250
-
Ming-Yung, W., Hung-Yen, Ch. Experimentalstudy of surface roughness in slot end milling [online]. International Journal of Machine Tools and Manufacture, 2004 [viewed 10 April 2020]. Available from: https://www.sciencedirect.com/science/article/abs/pii/S0890695503002335
-
Basil, A. A Study of the Effect of (Cutting Speed, Feed Rate, and depth of cut) on Surface Roughness in the Milling Machining [online]. Iraq: University of Technology, 2015 [viewed 10 April 2020]. Available from: https://www.researchgate.net/publication/314229791_A_Study_of_the_Effect_of_Cutting_Speed_Feed_Rate_and_depth_of_cut_on_Surface_Ro ughness_in_the_Milling_Machining.
-
Korkut, I., Donertas, M. A. The influence of feed rate and cutting speed on the cutting forces, surface roughness and toolchip contact length during face milling [online]. Turkey: Materials & Design, 2007 [viewed 9 April 2020]. Available from: https://www.researchgate.net/publication/248465003_The_influence
_of_feed_rate_and_cutting_speed_on_the_cutting_forces_surface_roughness_and_tool-chip_contact_length_during_face_milling.
-
Gosiger, Why you should consider Trochoidal Milling. Available from: https://www.gosiger.com/news/bid/152475/Why-You-Should-Consider-
Trochoidal-Milling
-
Harvey, Intro to Trochoidal Milling. Available from: https://www.harveyperformance.com/in-the-loupe/introduction-trochoidal-milling/