
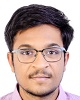
- Open Access
- Authors : Yashkumar Patel , Nikhil Jakka , Pratham Patel , Vatsal Patel
- Paper ID : IJERTV11IS030091
- Volume & Issue : Volume 11, Issue 03 (March 2022)
- Published (First Online): 28-03-2022
- ISSN (Online) : 2278-0181
- Publisher Name : IJERT
- License:
This work is licensed under a Creative Commons Attribution 4.0 International License
Solid Modelling and CFD Analysis of Venturi Wind Turbine
Yashkumar Patel1
Department of Mechanical Engineering LDRP-ITR, Gandhinagar, India
Nikhil Jakka2
Department of Mechanical Engineering LDRP-ITR, Gandhinagar, India
Pratham Patel3 Vatsal Patel4
Department of Mechanical Engineering Department of Mechanical Engineering LDRP-ITR, Gandhinagar, India LDRP-ITR, Gandhinagar, India
Abstractwind energy is a clean and renewable source of energy which can be used to increase the demand for electricity. In ancient time wind energy is utilized in different types of forms such as lifting the water, transfer any object to one place to another place. conventional wind turbine uses wind as an input and produce electricity as an output using generator. This paper highlights new innovative concept in sustainable energy. Presented Idea derived from INVELOX wind turbine which is a type of horizontal wind turbine. The proposed form of wind turbine is a vertical wind turbine which gives more output than conventional windmills. The main feature of Venturi wind turbine is that it captures wind flow through an omnidirectional intake and provides higher wind velocity in the venturi portion. The CFD analysis result shows that Venturi wind turbine increased the wind velocity to 8 m/s to 28 m/s.
Keywords Venturi wind turbine, CFD, Venturi Effect, CAD, Renewable Energy, Wind Energy, Clean and Green Energy, Wind mill, Sustainable Energy, ANSYS.
-
INTRODUCTION
Initial use of wind power goes back as far as 3000 years ago. The conversion of wind energy to electrical power marked a turning point for the wind power industry in the late 1800s. While the wind turbine industry has made major advances in increasing the power capacity by increasing the rotor diameters and the tower heights, the low-capacity factors, excessive downtime, and O&M costs have been major challenges in making wind affordable and reliable. These issues have slowed wind power from reaching its full potential. In addition, people and end-users are more aware of the negative impact of the large turbines on wildlife, farm animals, and human. The latter has resulted in the rapid increase in complaints that continue to plague the industry.
The principle of a wind turbine is to convert the kinetic energy of wind into electrical energy. The presented concept of the Venturi wind turbine is basically a vertical type of wind turbine. It is working on principle as same as conventional wind turbine, but the main difference is the addition of venturi effect at the outlet to increase the velocity of the wind. The fundamental characteristic of the system is that it captures a large portion of free stream airflow through the convergence and concentrates the wind towards the venturi section where a certain turbine system is located which will
capture the wind for power generation; subsequently, the wind will flow through the divergence, thereafter a special arrangement of a diffuser is implanted to ensure proper wind flow and avoidance of wind vortexes. This innovative idea is to develop a wind delivery system for wind power harnessing.
-
LITERATURE REVIEW
[1] The INVELOX technology captures wind with a funnel and directs it through at a peering passageway that passively and naturally accelerates its flow. This stream of wind energy then drives a generator that's put in safely and economically at ground or sub-ground levels. The performance of the system was valid by recent measured field information. Turbines within INVELOX, or any ducted turbine, have the next power constant than those put in Associate in Nursing open-flow setting. Normal horizontal or vertical turbines will be put within INVELOX and generate considerably additional energy compared with open-flow systems. In future, INVELOX windmill is exclusive innovation in wind business with multiple turbines will be at the same time use to grant massive output in small area. [2] In this study, the performance of the INVELOX system was investigated by analyzing the changes of the nozzle-diffuser section. Some geometrical changes were applied, as well as changes within the nozzle length, diffuser length, diffuser gap angle, and additionally exchange conic nozzle by the perfect one and adding the exit projection. Increasing the nozzle and diffuser length or the diffuser angle, as long because the separation within the channel flow is avoided, will increase the channel efficiency. Replacing the conic nozzle by the perfect nozzle considerably affects the rate and flow stream through the channel.[3] The operation of INVELOX and its performance with 3 wind turbines put in within the Venturi section. The extraction ofenergy depends on the enlarged mass rate through the system controlled by the omni-directional intake and therefore the external flow that sets up the rear pressure. This advantage comes as an on the spot, results of its omni-radial asymmetry, that decouples the intake from the turbine. The intake will capture wind flowing from any direction whereas the rotary engine is stationary, mounted on a close to ground position. Yaw management isn't needed as a result of intake is intended to capture wind from 360.[4] The objective of this work is to report on measured performance of the system once single, double and triple turbines are placed within the Venturi section. In Multiple wind turbines INVELOX technology on the market mass rate at second and third turbine is way lower as compared to initial turbine in venturi section. The extracted wind generation will increase by increasing the mass rate or total pressure drop across the turbine.[5] The review provides an entire image of turbine blade style and shows the dominance of contemporary turbines nearly exclusive use of horizontal windmill. The optimum economical form is complicated consisting of airfoil sections of skyrocketing dimension, thickness, and twist angle towards the hub. This general form is affected by physical laws and is unlikely to alter. A basic load analysis reveals that the blade may be modelled as an easy beam with a in-built support at the hub finish. A uniformly distributed load may be wont to represent lift throughout operation.
-
METHODOLOGY
-
Design of Venturi Wind Turbine
Venturi Wind Turbine consists of 8 different parts which are as:
-
Upper Funnel Portion
-
Fins
-
Lower Funnel Portion
-
Travelling Tube
-
Convergent Section
-
Venturi Section
-
Divergent Section
-
Diffuser
-
The above-mentioned components are shown in the 3D model as follows:
(Isometric View)
(Sectional View)
-
Upper Funnel Portion
Upper Funnel is used for the supporting of the parts which are attached underneath it. Also, it ensures the smooth flow of wind towards the tube without any deviations by possessing a gradually radial surface. Furthermore, the upper funnel guides the air towards the inner part of the turbine. It is designed to capture wind from omni-direction which means from all the directions, increase its speed and concentrate the moving flow of air before passing it further as shown in the picture.
-
Fins
The prime concept of Fins is to divert the wind into the turbine, they basically act like guide vanes which collects wind and direct the wind to pass further to the duct in a proper flow without minimal turbulence. The air will strike the Upper Funnel(a) and then will move downwards simultaneously following the funnel. There are 8 fins provided in this modl which ensures the proper wind flow entering the turbine.
-
Lower Funnel Portion
Lower funnel portion is used to concentrate the wind, which is collected through the fins, it also acts like a guide vane which will further direct the air towards the elongated pipe (tube), it will possess two radial surfaces at front and end portion of the funnel gradually decreasing the radius from front to the end. The end radius will be same as the starting of the travelling tube (concentrating tube) further.
-
Travelling Tube
The travelling tube is the outlet of the nested funnel structure which is connected to the inlet of the elongated pipe referred as the Travelling tube as shown in the model. This type of structure causes
the difference in height () from the top till the
end of the tube and through this, acceleration of
wind flow is gained.
-
Convergent section
The convergent is placed to increase the flow rate of wind. Its sole purpose is to increase the wind velocity and decrease the wind pressure. The accelerated wind flow achieved in the travelling tube (d) creates a dynamic environment for the passing wind towards the convergence section. The wind will start getting concentrated and hence it will help in attaining increment in wind velocity and decrement in wind pressure.
-
Venturi section
Venturi meter works on the principle of Bernoullis effect. The venturi measures the fluids flow rate by reducing a cross sectional flow area in the flow path and generating a pressure difference and eventually rises the velocity of the fluid (wind or liquid). This is the portion where the maximum wind velocity is obtained by creating a pressure difference and the measurement of that pressure difference allows the determination of discharge through the pipe.
-
Divergent section
Divergent cone of the venturi meter is made to minimize the flow separation and resulting energy losses, the flow retards in the diverging portion and pressure increases towards the downward direction. Indirectly the divergent acts as a diffuser, which gives the surety.
-
Diffuser
The prime function of establishing a Diffuser structure is to minimize the vortexes or turbulence effects of downstream wind, a diffuser is basically a device which is used for reducing the velocity and increasing the static pressure of a fluid flowing through a system. The fluid's static pressure rises as it passes through a duct is commonly referred to as pressure recovery.
-
-
ANALYSIS & RESULTS
Analysis
-
Geometry- During pre-processing in ANSYS Workbench The geometry of the model will be describe in the finest possible way by unifying the all-different parts of the model and creating single ideal body.
-
Meshing- It is an important step to acquire the ideal meshing and its dimension to adopt precise results, with minimal computational time and appropriate outcome with least amount of error in the solution.
-
Boundary conditions- In modelling it will create prismatic structural geometry around the model which create a complete boundary condition, for this model the boundary area is available in all direction X, Y & Z and in each
direction, it is expanded up to 300 meters to – 300 meter. Here the pressure and temperature during analysis is 1atm & 25°C respectively. And the turbulence intensity of fluid is medium.
-
Solver- Ansys CFD analysis solver it is used to identify the fluids and models materials and its properties, and it also calculate all constrain and physics which defined to the model. The solver will calculate the temperature, pressure, boundary condition, and kind of turbulence model. Here the model has contained the K- epsilon (k-) turbulence model.
RESULTS
(Figure 1)
(Figure 2)
The streamline allows to track the flow lines of fluid around the model, figure 1 shows the streamline illustration according to the fluid flow, The fluid will first approach the omnidirectional inlet section and passes through the funnel for convergence and then at venturi section the fluid will compress and increases its velocity, then to avoid the recirculation or back flow of fluid it will interact with diffuser and released out in atmosphere.
The velocity contour of model is developed by the velocity of fluid in each section of the model, Here the inlet wind speed is 8 m/s and the results shows the maximum wind speed at venturi section is 28.36 m/s which is indicated by the red dark portion in velocity contour at venturi section figure 2.
-
-
CONCLUSION
The current project is completely based on Clean and Green Energy which is currently in the utmost need of the world and possesses a bright future.
After understanding the concept of Venturi Wind Turbine and gathering all the required information; proposed various models designed, generated in Solid Works CAD Software, and performed CFX flow simulation in Ansys Simulation Software.
During the analysis phase, the drawbacks of Horizontal Venturi Wind Turbine (HVWT) are identified which is a major drawback of INVELOX for its discontinuity. The concept of Venturi Wind Turbine is very useful in the future as a power generation; so, to utilize this concept we designed our model which overcomes all the drawbacks of Horizontal Venturi Wind Turbine (HVWT) with the tremendous increment in wind velocity at the venturi section from 8 m/s to 28.36 m/s.
V. REFERENCES
[1] INVELOX Windmill [Dhananjay Kadlag, Bhor Sushma, Bangar Vishal,Rajgude Bhagyashri,Doke PrafullAssistant Professor, Department of Mechanical Engineering, JCOE Kuran, Maharashtra, India.U.G. Student, Department of Mechanical Engineering, JCOE Kuran, Maharashtra, India.] [2] A novel design of nozzle-diffuser to enhance performance of INVELOX wind turbine [S. Rasoul Hosseini, Davoud Domiri Ganji, Faculty of Mechanical Engineering, Babol Noshirvani University of Technology, Babol, Iran] [3] INVELOX with multiple wind turbine generator systems [Daryoush Allaei, David Tarnowski, Yiannis, Andreopoulos; SheerWind, Inc., Chaska, MN 55318, USA; QRDC, Inc., Chaska, MN 55318, USA; Department of Mechanical Engineering, City College of New York, New York, NY 10031, USA] [4] Design Modification & Analysis for Venturi Section of INVELOX System to Maximize Power using Multiple Wind Turbine [AnandL. Solanki Prof. Brijesh D. Kayasth, M.E. Student Assistant Professor, Department of Mechanical Engineering Department of Mechanical Engineering, SAL College of Engineering, Ahmedabad, India SAL College of Engineering, Ahmedabad, India; Prof. Hardik Bhatt, Assistant Professor, Department of Mechanical Engineering, SAL College of Engineering, Ahmedabad, India] [5] Wind Turbine Blade Design [Peter J. Schubel * and Richard J. Crossley; Faculty of Engineering, Division of Materials, Mechanics and Structures, University of Nottingham, University Park, Nottingham NG7 2RD, UK] [6] https://www.jetir.org/papers/JETIRAE06019.pdf
[7] https://en.wikipedia.org/wiki/Diffuser_(thermodynamics) [8] https://www.sciencedirect.com/science/article/abs/pii/S03605442 15012864?via%3Dihub