
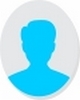
- Open Access
- Authors : Surachai Hemhirun , Kittikom Nontprasat
- Paper ID : IJERTV11IS030157
- Volume & Issue : Volume 11, Issue 03 (March 2022)
- Published (First Online): 13-04-2022
- ISSN (Online) : 2278-0181
- Publisher Name : IJERT
- License:
This work is licensed under a Creative Commons Attribution 4.0 International License
Performance Study of Thermo-Electric Generator by Heat Exhaust with Two Wheels Motorcycle
Surachai Hemhirun
Department of Mechanical Engineering, Rajamangala University of Technology Krungthep, Nang linchi road, Sathorn,
Bangkok, Thailand.
Kittikom Nontprasat
Department of Mechanical Engineering, Rajamangala University of Technology Krungthep, Nang linchi road, Sathorn,
Bangkok, Thailand.
Abstract This work was the studying of recharge the electric of two wheels exhausts gas by the thermo-electric system. The evaluation was 35°C and 42°C of environment temperature with load/unload at 1400 rpm used two speeds for 2 to 30 minutes. The result showed that at the 60 km/hour speed generated voltage average 21.86 volts, 0.55 Amp, it can be charged to 12 VDC battery by-charger controllers for the preventive reverse to the thermos-electric plate. As the idle speed of both environment temperatures have lowest, and not enough to charge the battery. The error of thermos-electric power generator must to a constant temperature and heat transfer system is low performed.
Keywords Two-wheel motorcycle, Exhaust Gas Recirculation, Thermo-electric, Heat exchanger, DC generator
-
INTRODUCTION
The estimation of total energy input in internal combustion engines was about 20 to 50% and loosed by the exhaust waste heat. As more of the researcher has been recovered from heat of exhaust to achieved electrical requirements of a car and the thermoelectric technology (TET) was used the electrical generator with heat surface [1, 2]. The heat of exhaust gases was high temperature compared to the heat of coolant and lubricant oil. As high temperatures shows the possibility of conventional energy by thermoelectric generator (TEG) to attach to the exhaust heat energy. It's converted a heat engine into electric energy and the principle of the Seebeck effect generated electric power [3, 4, 5]. Thermoelectric (TE) energy converted is fabricated by coupling two conjugate p-type and n-type doped semiconductors like in solid-state devices can transform heat given off sources into electric power and considered as an alternative and the familiar technology of environment of obtaining and recovering heat which is directly converted [2,4,5,6]. The working was the temperature differences at the junction to make an electrical current. For the circuit configuration, the knowledge that the series connecting got encourage to not only immediately voltage but also current, and the parallel connectors gave a solely of power [4]. The improvement of semiconductor materials can be the best combination of performance such feedback coefficient, electrical resistivity, and thermal conductivity, and the other benefit are the ability to used electron to conduct current [7]. On the cold side and a hot side of the thermoelectric modules, the heat is absorbed by electrons as it gives a high energy level in the n-type element of semiconductor at the hot side. The electrons are moved into the system by the energy of the power supply. The high
energy level element (n-type) is banished by the heat sink as electron movement to a lower level element (p-type) [8]. The main design of thermoelectric modules is bismuth telluride material base for cooling or integrate cooling and heating used while electric power is built by a temperature difference of thermoelectric module. The reverse behavior used the temperature differential of the surface of the module and generated electric power caused [9]. Thermoelectric devices are evident advantages and environments family feature. The weak benefit, it has low efficiency [10, 11]. The other distinct advantages of this technology were involving no moving parts or bulk fluids, low maintenance, lightweight, no vibration, no optics, and sonic signal, and flexibility on heat source [12]. Also, its easy availability, low cost, and low operating temperature range with considerable efficiency make the use of bismuth telluride an effective module. This work was studying the thermos-electric power generator (TEG) apply to the exhaust heat of a motorcycle at 125cc with 95% gasohol fuel, and 12VDC battery charging.
-
EXPERIMENTAL
-
Experimental Setup
As the single thermos-electric create low voltage and to achieve high voltage, the connection electrical technique was selected in mixing as series and parallel form to a module. The one end of the hot side was heated and the temperature gradient is maintained concerning the other end of the cold side [13]. As thermos-electric specification, was power generator TEG Peltier type model SP1848-27145, dimension is 4.0 (w) x 4.0 (L) x 3.4 (T) mm, material is ceramic / bismuth telluride, working environment: -60 – 125°C, Temperature electromotive force (a): >190x uV/°C, conductivity: 850-1250 -1cm-1, Thermal conductivity (K): 15 – 16×10-3 W/°C cm. The thermos-electric was working by the different temperature of both sides, heat side attached into the exhaust pipe and cooling plate is mounted on a cold side. The cooling plate circulated and transferred heat into the system by water and cool down by radiator. Figure 1 (a) shows the arrangement of n and p type material in a TEG module and (b) installing with an exhaust pipe.
-
(b)
Figure 1 (a) Thermo-electric of N and P type and (b)preparing the installation of thermo-electric into the exhaust pipe of motorcycle
All most thermoelectric generators comprise several individual modules that may be electrically connected in either series, parallel, or series/parallel arrangement. This generator has an NT (Total number of modules) with NS (Number of modules connected in series) and NP (Number of modules connected in parallel). The total number of modules in the system is:
NT = Ns * Np (1)
-
-
Design of Themo-Electric Generator
The thermo-electric cell is low generated voltage and low output power [6]. The design of the connective is served need the battery of two wheels motorcycle. Base on the additional current of electric is series connecting and parallel is voltage increased. Both of them are mixing as design and modify it.
Figure 2 Diagram of current and voltage increasing for thermo-electric
generators
When ITA is the total voltage of group A.I1A, I2A, I3A,, I10A are the voltage of each thermoelectric device in group A. ITB is the total voltage of group B.I1B, I2B, I3B, , I10B is the voltage of each thermoelectric device in group B. ITotal is total of voltage.
P = I * V (8)
When P is power (Watt), I is current (Amp), V is voltage (V)
-
Tester Instrument
Figure 3 (a) the measurement tool for the voltage and current output by multi-meter, which Kyoritsu digital millimeters model 1009, DC measure is 400mV- 600V (input Impedance 10M) ± 0.6%rdg±4Dgt, and input/output of the cooling system is measured by digital temperature controller model TTM-J4. The calculation of cooling is a difference between the input (cold water) and output (hot water).
-
(b)
-
VTA = V1A+V2A+V3A+V4A+V5A+V6A+V7A+V8A+V9A+V10A VTB = V1B+V2B+V3B+V4B+V5B+V6B+V7B+V8B+V9B+V10B
(2)
(3)
Figure 3 (a) multi-meter for voltage and ampere measurement and (b) digital temperature controller for input/output for cooling system
-
-
RESULTS AND DISCUSSION
A. Study of Perfomance for Mixing Conneted with A Thermo- Electric Generator
VTotal = VTA+VTB (4)
When VTA is the total voltage of group A, V1A, V2A, V3A,
, V10A is the voltage of each thermoelectric device in group
A. VTB is the total voltage ofgroup B, V1B, V2B, V3B, , V10B is the voltage of each thermoelectric device in group B. V Total is total of voltage.
ITA = I1A=I2A=I3A=I4A=I5A=I6A=I7A=I8A=I9A=I10A (5)
ITA = I1A=I2A=I3A=I4A=I5A=I6A=I7A=I8A=I9A=I10A (6)
ITotal = ITA+ITB (7)
The voltage and current are the output type of the main device of the performance system, and also the heat source in the exhaust of two wheels motorcycle. The experimental thermoelectric generator is testing each mixed connecting for basting performance by an average of two-wheel motorcycle, at 40 km/hour, the difference of both sides is 55 degrees centigrade of hot side and cooling side, the thermoelectric generated 1.34 voltage and 0.16 ampere by each. This battery is 12 VDC capacities and item 3 is connecting selected. Table 1 thermoelectric performance of generator connecting.
Table 1 Performance of the thermoelectric generator by the connecting method.
Item
description
Resistant
Voltage (V)
Ampere (A)
Power (W)
1
20 pieces with series
46.0
26.8
0.16
4.288
2
20 pieces with parallel
0.115
1.34
3.2
4.288
3
10 pcs./set with series and 2 sets with a parallel
11.5
13.4
0.32
4.288
4
10 pcs/set with parallel and 2 sets with series
0.46
2.68
1.6
4.288
5
5 pcs./set with series and 4 sets with a parallel
2.875
6.7
0.64
4.288
6
5 pcs./set with parallel and 4 sets with series
1.84
5.36
0.80
4.288
7
4 pcs./set with series and 5 sets with a parallel
1.84
5.36
0.80
4.288
8
4 pcs./set with parallel and 5 sets with series
2.875
6.70
0.64
4.288
9
2 pcs./set with series and 10 sets with a parallel
0.46
2.68
1.60
4.288
10
2 pcs./set with parallel and 10 sets with series
11.50
13.4
0.32
4.288
-
Temperature of Themo-Electric in Idel Speed with No Loaded
As the environment temperature is 35°C with no loaded at
Voltage of thermo-electric generator (V)
Voltage generating of thermo-electric with no loaded at idle speed
idle speed observed the start engine has 2°C difference
temperature until 10 minutes increased to 10°C difference. At 20 minute testing time, the difference temperature is 16°C and 18°C in 30 minutes. While, 42°C of environment temperature shows the different temperature is 2°C, at start engine until 10 minutes, the difference temperature increased to 11°C then continuous to 16°C at 20 minutes and 24°C at 30 minutes, shown in Figure 4. The comparison at 35°C and 42°C of environment, at 42°C has higher than 35°C but they are the lowest difference temperature.
Difference temperature of thermo-electric with no loaded at idle speed
4.0
3.5
3.0
2.5
2.0
1.5
1.0
0.5
0.0
35°C environment 42°C environment
0 2 4 6 8 10 12 14 16 18 20 22 24 26 28 30
Time (Minute)
Temperature difference of thermo-electric (°C)
30
25
20
15
10 35°C environment
5 42°C environment
0
0 2 4 6 8 10 12 14 16 18 20 22 24 26 28 30
Time (Minute)
Figure 4 the difference of temperature for thermo-electric at idle speed
with no loaded
-
Voltage Generating of Thermo-Electric in Idle Speed with No Loaded
Base on the idle speed test, the thermoelectric generator must to higher difference temperature so; the idle speed has the lowest difference temperature. They are generating the lowest voltage about 3.3 voltages at 30 minutes with a 0.07- ampere current show in Figure 5. It cannot be charging to battery 12 VDC both of them.
Figure 5 Generating voltage of thermo-electric at idle speed with no
loaded
-
Temperature of Thermo-Electric at a Differenct Speed with Loaded
Figure 6 shows the difference of temperature of thermo- electric of both speeds within 150 kg loaded at 42°C environments, at 40km/hour speed, the difference of temperature is 5°C at start point until at 10 minutes increased to 41°C, 57°C at 20 minutes, and 56°C at 30 minutes. While, at 60 km/hour speed, 6°C at start point the difference temperature increased to 72°C at 10 minutes, 87°C at 20 minutes, and 89°C at 30 minutes. The comparison to difference temperature, 60 km/hour speed is better than 40 km/hour speed and the 40 km/hour speed is better than idle speed.
Temperature difference of thermo-electric (°C)
100
90
80
70
60
50
40
30
20
10
0
Difference temperature of thermo-electric at difference speeds with 150kg loading and 42°C environment
40Km/hour 60Km/hour
0 2 4 6 8 10 12 14 16 18 20 22 24 26 28 30
Time (Minute)
thermos-electric power generator must to a constant temperature and heat transfer system is low performed.
ACKNOWLEDGMENT
This work has been performed at the mechanical engineering department, Rajamangala University of Technology Krungthep, Bangkok. The authors would truly like to recognize the university of engineering for providing technical and location assistance without it this work is difficult to complete successfully.
REFERENCES
[1] J. Vázquez, A.S. Sanz-Bobi, R. Palacios, A. Arenas, State of the Art ofThermoelectric Generators Based on Heat Recovered from the Exhaust Gases of Automobiles" [2] G. Rohit, D. Manaswini, K. Vinod, and S.R. Nagaraja, Performance study of thermo-electric generatorInternational Conference onFigure 6 Difference temperature of thermo-electric of 40 km/hour and 60km/hour within 159 kg loading at 42°C environment
-
Voltae Generating of Thermo-Electric at a Differnct Speed with Loaded
As the knowledge of the thermoelectric power generator, they must difference temperature on working. The 40 km/hour speed shows higher than 12 voltages at 10 minutes; it's enough to charge the battery 12 VDC. But at 60 km/hour used only 4 minutes, it can be charging the battery.
Voltage of thermo-electric generator (V)
Voltage generating by thermo-electric at difference speeds with 150kg loading and 42°C environment
30.0
25.0
20.0
15.0
10.0
40Km/hour
5.0
60Km/hour
0.0
0 2 4 6 8 10 12 14 16 18 20 22 24 26 28 30
Time (Minute)
Figure 7 Voltage generating by thermo-electric difference speeds with 15 kg/loading and 42°C environment
-
-
CONCLUSION
The studying of thermoelectric power generator performance with the exhaust heat of a two-wheels motorcycle used 20 pieces of the thermoelectric plate. The 60 km/hour speed generated voltage average 21.86 volts, 0.55 Amp, it can be charged to 12 VDC battery by-charger controller for the preventive reverse to the thermos-electric plate. The difference temperature for idle speed of both environments has the lowest, and not enough to charge the battery. The error of
Functional Materials, Characterization, Solid State Physics, Power, Thermal and Combustion Energy AIP Conf. Proc. 1859, 020094-1 020094-6; doi: 10.1063/1.4990247 Pblished by AIP Publishing. 978-0- 7354-1533-1/$30.00
[3] M. D. Rowe, Thermoelectric waste heat recovery as a renewable energy sourceInternational Journal of Innovations in Energy Systems and Power, Vol. 1, no. 1 (November2006). [4] A.J. Muhammad, Y. Zulkarnain, M.F.M. Omar, A.W.J. Wan, and N.R. Mohamed, Feasibility study of Thermal Electric Generator Configurations as Renewable Energy Sources International Conference on Materials Physics and Mechanics 2017, IOP Conf. Series: Journal of Physics: Conf. Series 914 (2017) 012024 [5] S. Mratyunjay, N. Sanjay, and M. Ashutosh, Thermoelectric Generator: A ReviewIOSR Journal of Mechanical and Civil Engineering (IOSR- JMCE) e-ISSN: 2278-1684,p-ISSN: 2320-334X, Volume 12, Issue 3 Ver.III (May. – Jun. 2015), PP 40-45 www.iosrjournals.org
[6] T. Ssennoga, Y.Y. JieZhu BoLi, A comprehensive review of thermoelectric technology: Materials, applications, modeling and performance improvement Renewable and Sustainable Energy Reviews 65 (2016 )698726 [7] H. Javan, Optimal design of thermoelectric generator 0- 7803-63 124 /00, 2000, IEEE.
[8] Melcor Thermoelectric Handbook (www. melcor.com) [9] I.B. Cadoff, and E. Miller, (Eds.) "Thermoelectric materials and devices" Reinhold, New York,1959. [10] P. Shyam, Applications of Thermoelectric Energy: A ReviewInternational Journal for Research in Applied Science & Engineering Technology (IJRASET), ISSN: 2321-9653; IC Value: 45.98; SJ Impact Factor: 6.887 Volume 6 Issue V, May 2018- Available at www.ijraset.com [11] R. James, Salvador, Y.C. Jung, Y. Zuxin, E. Joshua,. Moczygemba, J.T. Thompson, W.S. Jeffrey, D.K. Jan, M. Ryan, T. Travis, S. Jeffrey, W. Hsin, and A.W. Andrew, Conversion efficiency of skutterudite-based thermoelectric modulesPhys.Chem.Chem.Phys.,2014, 16, 12510 [12] W. LUAN, TU Shantung, "Recent developments of thermoelectric power generation"Chinese Science Bulletin, Vol. 49 No. 12, 1212_1219, 2004. [13] Z.H. Dughaish, Lead telluride as a thermoelectric material for thermoelectric power generationElsevier Science, Volume 322, Issues 1-2, September 2002, Pages 205-223.Surachai Hemhirun, the authors received the B. Eng. Degree in Mechanical Engineering from Rajamangala University of Technology Krungthep (RMUTK), Thailand in 2008, M. Eng. Degree in Mechanical Engineering from King Mongkuts University of Technology Thonburi (KMUTT), Thailand in 2011. AND PhD. Degree in Mechanical Engineering from Srinakharinwirot (SWU), Thailand in 2020. Currently, he is a lecturer at Rajamangala University of Technology Krungthep (RMUTK) and his research interest includes energy management for dryer, moisture measurement in grain, and automatic control systems.
Kittikom Nontprasat, the authors received B. Eng. Degree (InE.) in Mechanical Engineering from Saints John University, Thailand in 1998, M. Eng. Degree in Mechanical Engineering from Srinakharinwirot University (SWU), Thailand in 2009. B. Eng. Degree (MechE.) in Mechanical Engineering form Rajamangala University of Technology Pranakhorn (RMUTP), Thailand in 2019. and PhD. Degree in Mechanical Engineering from Srinakharinwirot University, Thailand in 2020. Currently, he is a special lecturer at Chiangrai Campus and his research interest includes automatic control, and applied engineering.