
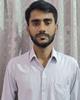
- Open Access
- Authors : Anil Agrahari , Ashutosh Verma , Abhishek Maurya , Ashish Kumar Pandey
- Paper ID : IJERTV11IS040099
- Volume & Issue : Volume 11, Issue 04 (April 2022)
- Published (First Online): 22-04-2022
- ISSN (Online) : 2278-0181
- Publisher Name : IJERT
- License:
This work is licensed under a Creative Commons Attribution 4.0 International License
Comparative Analysis of Various DC-DC Converters using MATLAB
Anil Agrahari1, Ashutosh Verma2, Abhishek Maurya3 , Ashish Kumar Pandey4
1 Assistant Professor, Department of Electrical Engineering, Shri Ramswaroop Memorial College of Engineering and Management, Lucknow, India
2,3,4UG Students, Department of Electrical Engineering, Shri Ramswaroop Memorial College of Engineering and Management, Lucknow, India
Abstract The design and simulation of various isolated and non isolated dc-dc converters is the focus of this research article. It includes theoretical derivations as well as parameter formulae, design and examples. Since the Electricity consumption is increasing day by day due to which a scarcity of conventional energy sources such as coal, petrol, gasoline, occurring day by day , so to fulfill requirement of energy sources an alternative methods are required urgently to meet the growing demand for electricity, therefore the researcher and industries are highly motivated towards the solar energy generation , wind power generation dc dc converter etc . A DC-DC converter is a stage in the power conversion process , This converter changes the voltage level from one level to another. Likewise the value of power level varies from small to high level . The standard approach frequently encounters problems such as poor power quality, delayed dynamic response, high device stress, harmonic rich, periodically dense, peaky, distorted input current, and harmonic rich, periodically dense, peaky, distorted output current in the conventional energy generation . This transgresses the international power quality limitations using the MATLAB tool different isolated and non isolated dc dcconvter are analyzed With changing the input parameters like inductance, capacitance, and switching frequency to see how the output voltage varies And added with simulation graph .
Index Terms: Buck converter, Boost converter, Cuk converter, Sepic converter, Zeta converter, Flyback converter, Half bridge DC-DC converter, Full bridge DC-DC converter, Push pull converter.
-
INTRODUCTION
As a tremendous growth in semiconductor devices, the switching devices are available with extremely fast switching rates and great power handling capabilities. It is possible to design converters with efficiency greater than 90% and also it can be designed at a low cost, small size, and light weight. As semiconductor devices are used to operate in OFF state or in ON state and each switching state will result in a low switching voltage or low switching current, and using a switching regulator, it is feasible to convert DC to DC with greater efficiency.
The Pulse width modulation (PWM) techniques and switching frequency modification are used to regulate the converter switching operation. Non-isolated DC-DC converters are converters that use pulse width modulation (PWM) for switching control. The various types of non- isolated type of converters include buck, boost, buck-boost, CUK, and SEPIC converters and various types of isolated converters include fly back, full bridge, half bridge etc. Since High frequency transformers are not included in the
structure of non-isolated converters as a result they are smaller, cheaper and easier to regulate. The non-isolated type of converters have a series inductor connection at the input, smaller output capacitance and output filter size, which provide switch protection against overvoltage and electromagnetic interference (EMI), lower stress on the components, better transient response, efficiency, and high power density.
Buck converters and boost converters are typically used to scale down the output voltage
Practical considerations limit the output voltage of a conventional boost converter to be approximately six times its applied voltage. In order to supply a high output voltage, the conventional boost converter must operate at extremely high duty cycle ratios, which impose a small off time or low switching frequency.
A feedback path can also be connected from outside side to input side of these converters to obtain a more accurate and less fluctuating output. Their feedback path includes a PID controller whose derivative, integral and proportional parameters need to be set according to circuit parameters.
In this paper, we have designed simulink models of converters with feedback loop as well.
Some loads are sensitive in nature. They require a stable supply with very less or no fluctuations at all. So, isolated types of converter are best for such kind of loads as they can isolate such loads from supply side with the use of transformers (generally referred to as isolating transformer). There are some type of converters which can both step up or step down the voltage level like Buck-Boost converter and CUK converter. In such type of converters, duty cycle decides their mode of operation. If value of duty cycle is greater than 50%, it steps up the voltage level, that is, it operates in boost mode. While, if duty cycle is less than 50%, it steps down the voltage level, operating in buck mode.
Various types of electronic switches can be used to design such types of converters like MOSFETs, BJTs, IGBTs, GTOs, FETs, etc. The use of any particular switch depends upon the load requirements and ratings. For example, MOSFETs are used in low power applications because their switching losses are less and their input resistance is also higher. IGBTs are generally used in high power applications.
Such DC-DC converters can be used in various electronic and electrical devices like in charging circuits.
-
TYPES OF DC-DC CONVERTERS
Fs=40 kHz
Duty Cycle=Vo/Vs=15/48=0.3125 , i.e. 31.25%
Inductance value:
=
Lmin (1)
2
= (10.3125)8
2×40×1000
= 68.75µ
……………(1)
We assume inductance to be 25% larger for inductor current to be continuous .So, we have
L=85.93µH
Capacitance Value:
C= 1
8()2
…………….(2)
We assume ripple () to be less than 5%
So, C=125.01µF (from above formula)
There is no feedback provided in Open loop Buck Converter , so variation of output voltage from required value is larger.
Fig.1: Types of DC-DC Converters
-
NON-ISOLATED DC-DC CONVERTERS
In this type of DC-DC converter input side is not isolated from output side. Hence, these type of converters are not used with sensitive type of loads which can not bear voltage or current fluctuations.
-
BUCK CONVERTER
-
It steps down the DC voltage level.
-
It can be designed in two ways:
-
Open loop
-
Closed loop OR with feedback loop
-
OPEN LOOP BUCK CONVERTER
PARAMETERS
Value
Resistor, R
8 ohm
Inductor, L
85.93 µH
Capacitor, C
125 µF
Vs (Supply voltage)
48V
Vo (Output Voltage)
15V
Duty Cycle
31.25%
Frequency
40 kHz
DESIGN:
Required Output voltage=15V Vs=48V
R=8 ohm
Fig.2: Simulink Model of Buck Converter
INPUT VOLTAGE WAVEFORM
Fig.3
OUTPUT VOLTAGE WAVEFORM
Fig.4
-
CLOSED LOOP BUCK CONVERTER ( WITH FEEDBACK PATH)
To obtain output voltage in permissible range, we eed to use a feedback path in the circuit. This type has greater reliance and much less variation of output voltage.
Parameters of PID Controller: Controller parameters: Proportional(P)=0
Integral(I)=7 Derivative(D)=0 Filter Coefficient=100
-
-
-
BOOST CONVERTER
-
It steps up the DC Voltage level.
-
It can be designed in two ways:
-
Open loop
-
Closed loop OR with feedback loop
-
OPEN LOOP BOOST CONVERTER
PARAMETERS
Value
Resistor, R
16.2 ohm
Inductor, L
60µH
Capacitor, C
16.44µF
Vs (Supply voltage)
12V
Vo (Output Voltage)
18V
Duty Cycle
33.33%
Frequency
25 kHz
DESIGN:
Duty cycle=1 = 1 12 = 0.333 = 33.33%
18
Fig.5: Simulink model of Buck converter with feedback loop
Inductance Value:
2 2
Lmin=(1) = 0 .33 (1 0.333 ) 8 = 47.99µ
INPUT VOLTAGE WAVEFORM
………….(3)
2
2×25×1000
We assume inductance to be 25% larger for inductor current to be continuous ,we have, Lmin=60µH
Capacitance Value:
C=
(
)
………….(4)
We assume ripple () to be less than 5%
Fig.6
OUTPUT VOLTAGE WAVEFORM
Fig.7
C=16.44µF
Fig.8: Simulink Model of BOOST converter
INPUT VOLTAGE WAVEFORM
Fig.9
OUTPUT VOLTAGE WAVEFORM
Fig.10
-
CLOSED LOOP BOOST CONVERTER (WITH FEEDBACK LOOP)
To obtain output voltage in permissible range, we need to use a feedback path in the circuit. This type has greater reliance and much less variation of output voltage.
Parameters of PID Controller:
Controller parameters:
-
-
-
-
BUCK- BOOST CONVERTER
-
It can both step up and step down the DC voltage level depending upon the duty cycle of the control switch
-
It changes the polarity of output voltage with respect to input voltage.
PARAMETERS
Value
Resistor, R
33.33 ohm
Inductor, L
165µH
Capacitor, C
66.60µF
Vs (Supply voltage)
40V
Vo (Output Voltage)
-50V
Duty Cycle
55.55%
Frequency
25 kHz
DESIGN:
Inductance Value:
2 2
Lmin=(1) = (1 0.55 ) × 33 .33 = 132µ ……(5)
2
2×25×1000
Proportional(P)=0
Integral(I)=7 Derivative(D)=0 Filter Coefficient=100
We assume inductance to be 25% larger for inductor current to be continuous,we have, Lmin=165µH
Capacitance Value:
C=
(
)
…………..(6)
We assume ripple () to be less than 5%
Fig.11: Simulink Model of BOOST converter with feedback loop
INPUT VOLTAGE WAVEFORM
Fig.12
OUTPUT VOLTAGE WAVEFORM
Fig.13
C=16.44µF
Fig.14: Simulink Model of BUCKBOOST converter
INPUT VOLTAGE WAVEFORM
Fig.15
OUTPUT VOLTAGE WAVEFORM
Fig.16
-
-
SEPIC CONVERTER
-
It stands for Single Ended Primary Inductor Converter.
-
It can step up or step down the voltage level depending upon the duty cycle of the control switch.
-
It is a combination of Boost Converter and BUCK- BOOST Converter. Hence, it works similar to BUCK-BOOST converter , but it has advantage of non-inverted voltage unlike BUCK-BOOST Converter(that is, output voltage has same polarity as that of input voltage).
Fig.17: Simulink Model of SEPIC converter
INPUT VOLTAGE WAVEFORM
Fig.18
OUTPUT VOLTAGE WAVEFORM
PARAMETERS
Value
R
2 ohm
L1
35.62 µH
L2
14.25 µH
C1
28.57µF
C2
28.57µF
Vs (Supply voltage)
15V
Vo (Output Voltage)
6V
Duty Cycle
28.57%
Frequency
250 kHz
DESIGN:
Duty cycle,D= 0
+0
= 0.2857(28.57%)
Fig.19
-
-
SEPIC CONVERTER WITH FEEDBACK LOOP
To determine average inductor currents and change in inductor
currents
IL2= = 6 = 3
2
IL1= = 1.2
Assuming 40% change in ripple current,
IL1= 0.4 x 1.2=0.48A
IL2=0.4 x 3=1.2A
Determination of inductor values:
To obtain output voltage in permissible range, we need to use a feedback path in the circuit. This type has greater reliance and much less variation of output voltage.
Parameters of PID Controller: Controller parameters: Proportional(P)=0
Integral(I)=7 Derivative(D)=0
IL=
L1=
1 ×
L2=
2 ×
= 35.62µ
= 14.25µ
………..(7)
Filter Coefficient=100
Determination of capacitor values:
C2=C1=
0
(
)
= 28.57µ ………….(8)
0
We have assumed 2% ripple .
Fig.20: Simulink Model of SEPIC CONVERTER with feedback loop
INPUT VOLTAGE WAVEFORM
Determination of inductor values:
IL=
…………(9)
L1=
1 ×
L2=
2 ×
= 820 µ
= 681 µ
Determination of capacitor values:
C1=
(1)
1
= 7.92µ …………(10)
Fig.21
C2= = 3.33µ ………….(11)
82(0)2
OUTPUT VOLTAGE WAVEFORM
Fig.22
-
CUK CONVERTER
CUK CONVERTER works similar to BUCK-BOOST converter. But it has advantage of zero ripple current. It can both step up and step down DC voltage depending on the duty cycle of the control switch. In this converter output voltage has opposite polarity with respect of input voltage.
0
We have assumed 1% ripple
Avg. voltage across C1 is 25-(-30)=55 volt
Max. change in Vc1=55 x 0.05=2.75 V (Ripple for C1 is taken as 5%)
Fig.23: Simulink Model of CUK converter
INPUT VOLTAGE WAVEFORM
Fig.24
OUTPUT VOLTAGE WAVEFORM
PARAMETERS
Value
R
15 ohm
L1
820 µH
L2
681 µH
C1
7.92 µF
C2
3.33 µF
Vs (Supply voltage)
25V
Vo (Output Voltage)
-30V
Duty Cycle
54.5%
Frequency
50 kHz
DESIGN:
Duty cycle,D= 0
+0
= 0.545 (54.5%)
To determine average inductor currents and change in inductor
currents
IL2= = 30 = 2
15
IL1= = 25 = 1.66
15
Assuming 20% change in ripple current,
IL1= 0.2 x 1.66=0.332 A
IL2=0.2 x 2=0.4 A
Fig.25
-
ZETA CONVERTER
-
It can increase or decrease voltage level depending on the duty cycle of the control switch.
-
It does not chang polarity of the output voltage.
OUTPUT VOLTAGE WAVEFORM
PARAMETERS
Value
R
10 ohm
L1
1.6 mH
L2
1.6 mH
C1
720 µF
C2
15 µF
Vs (Supply voltage)
12V
Vo (Output Voltage)
18V
Duty Cycle
60 %
Frequency
25 kHz
DESIGN:
Duty cycle=
+
= 18
12+18
= 0.6 (60%)
Fig.28
-
ISOLATED DC-DC CONVERTERS
In these type of converters , output side is isolated from input side with the help of a transformer.
Determination of inductor current and change in inductor current:
IL1=IL2= = 18 = 1.8
10
IL1=IL2=0.1×1.8=0.18 A (Assuming 1% ripple in current)
Determination of inductor values:
Types of Isolated DC-DC Converters:
-
Flyback Converter
-
Forward Converter
-
FLYBACK CONVERTER
IL=
L=
I×f
L1=L2= 12×0.6
0.18×25×1000
= 1.6
……….(12)
-
-
It can be used to convert either AC to DC or DC to DC.
-
It is similar to BUCK-BOOST Converter.
PARAMETERS
Value
R
40 ohm
C
17.45µF
VS (Supply voltage)
24V
VO (Output Voltage)
40V
Duty Cycle
35.71 %
Frequency
100 kHz
Fig.26: Simulink Model of ZETA CONVERTER
INPUT VOLTAGE WAVEFORM
DESIGN:
Determination of Capacitor values:
=
………..(13)
Fig.27
Substituting values,
C=17.85µF
Fig.29: Simulink Model of FLYBACK CONVERTER
INPUT VOLTAGE WAVEFORM
Fig.30
OUTPUT VOLTAGE WAVEFORM
Fig.31
-
FLYBACK CONVERTER WITH FEEDBACK PATH
To obtain output voltage in permissible range, we need to use a feedback path in the circuit. This type has greater reliance and much less variation of output voltage.
Parameters of PID Controller: Controller parameters: Proportional(P)=0
Integral(I)=7 Derivative(D)=0 Filter Coefficient=100
OUTPUT VOLTAGE WAVEFORM
Fig.34
-
HALF BRIDGE DC TO DC CONVERTER
-
-
It is a type of isolated DC-DC converter, which can higher or lower the output voltage value with respect to input voltage.
-
It provides isolation via a transformer.
-
It has two MOSFETs as control switches in its circuitary.
PARAMETERS
Value
R
8 ohm
L
268.19 µH
C
41.42 nF
Vs (Supply voltage)
50V
Vo (Output Voltage)
17.5V
Duty Cycle
70 %
Frequency
150 kHz
DESIGN:
Determination of inductance:
Average inductor current is given by,
IL= =17.5/8=2.187 A
Assuming 40% ripple, we get,
IL=0.4×2.187=0.87 A
L=(0.5) = 268.19µ
×
………..(14)
Determination of capacitance:
Fig.32: Simulink Model of FLYBACK CONVERTER with
12
feedback loop
= …………(15)
322
Assuming ripple to be 5%, = 0.05
INPUT VOLTAGE WAVEFORM
Fig.33
Solving we get, C=41.42 nF
Fig.35: Simulink Model of HALF BRIDGE DC TO DC CONVERTER
DESIGN:
Determination of inductance:
Average inductor current is given by,
IL= =35/8=4.375 A
Assuming 40% ripple, we get,
IL=0.4×4.375=1.75 A
L=(0.5) = 26.66 µ ………..(16)
×
Determination of capacitance:
= 1 2
…………(17)
INPUT VOLTAGE WAVEFORM
322
Assuming ripple to be 5%, = 0.05
Solving , we get,
C=416.77 nF
Fig.36
OUTPUT VOLTAGE WAVEFORM
Fig.37
-
FULL BRIDGE DC-DC CONVERTER
-
Full bridge DC-DC Converter provides isolation in addition to stepping up or down or input voltage.
-
Isolation of input and output side is done via a transformer.
PARAMETERS
Value
R
8 ohm
L
26.66 µH
C
416.77nF
Vs(Supply voltage)
50V
Vo(Output Voltage)
35V
Duty Cycle
70 %
Frequency
150 kHz
-
It has four MOSFETs as control switches in its circuitary.
Fig.38: Simulink Model of FULL BRIDGE DC TO DC CONVERTER
INPUT VOLTAGE WAVEFORM
Fig.39
OUTPUT VOLTAGE WAVEFORM
Fig.40
-
-
PUSH PULL CONVERTER
-
It is an isolated DC to DC converter.
-
It utilizes two control switches so that flow of current in the primary winding of the transformer is continuous. Hence efficiency at the output is high and it can operate for higher power rating.
-
OUTPUT VOLTAGE WAVEFORM
Fig.43
TABLE 1: OBTAINED OUTPUT VOLTAGE OF VARIOUS CONVERTERS
PARAMETERS |
Value |
R |
8 ohm |
L |
268.19 µH |
C |
41.42 nF |
Vs(Supply voltage) |
50V |
Vo(Output Voltage) |
17.5V |
Duty Cycle |
70 % |
Frequency |
150 kHz |
Type of Converter |
Supply Voltage |
Duty Cycle |
Output Voltage( in volts) |
BUCK CONVERTER |
25V |
50% |
12.03435 |
BUCK CONVERTER WITH FEEDBACK PATH |
25V |
50% |
15.0008 (Vref*=15V) |
BOOST CONVERTER |
25V |
50% |
47.7448 |
BOOST CONVERTER WITH FEEDBACK PATH |
25V |
50% |
35.62675 ( Vref=36V) |
BUCK BOOST CONVERTER |
25V |
50% |
(-)24.01485 |
CUK CONVERTER |
25V |
50% |
(-)23.86625 |
SEPIC CONVERTER |
25V |
50% |
21.9498 |
SEPIC CONVERTER WITH FEEDBACK PATH |
25V |
50% |
5.841( Vref=6V) |
ZETA CONVERTER |
25V |
50% |
23.71805 |
FLYBACK CONVERTER |
25V |
50% |
24.04045 |
FLYBACK CONVERTER WITH FEEDBACK PATH |
25V |
50% |
39.95725(Vref=40V) |
HALF BRIDGE DC-DC CONVERTER |
25V |
50% |
11.54735 |
FULL BRIDGE DC-DC CONVRTER |
25V |
50% |
23.4931 |
PUSH PULL CONVERTER |
25V |
50% |
23.9011 |
DESIGN:
Determination of inductance:
Average inductor current is given by,
IL= =17.5/8=2.187 A
Assuming 40% ripple, we get,
IL=0.4×2.187=0.87 A
L=(1) = 268.19µ …………(18)
×
Determination of capacitance:
= 1 2
………….(19)
322
Assuming ripple to be 5%, = 0.05
Solving we get,
C=41.42 nF
Fig.41: Simulink Model of PUSH PULL CONVERTER
INPUT VOLTAGE WAVEFORM
*Vref refers to reference voltage in case of converters with feedback loop
Fig.42
III CONCLUSION
Comparative analysis and comprehensive study of both non- isolated and isolated type of DC-DC converters is performed successfully. Simulink model of various DC-DC converters is designed successfully in MATLAB and their voltage waveform is also obtained in. A table showing obtained output voltage of various DC-DC converters (with respect to supply voltage of 25 volts
) is also drawn.
REFERENCES
[1] R.Felshiya Rajakumari, Assistant Professor , comparative analysis of DC DC converter 2nd International Conference on Power and Embedded Drive Control (ICPEDC) [2] PreethiSontakki, A.D.Srinivasan,Sepic Topology Based High Voltage Gain DC-DC converter, International Journal of Recent Technology and Engineering, ISSn:2277-3878, Vol.8, Issue:1, May 2019. [3] FarzadMohammadzadeshShahir, et al., Extended Topology ofboost DC-DC Converter, IEEE Transactions on Power Electronics, Vol.34, Issue:3, March 2019. [4] StephyMathew ,Nayana J , Review of DC-DC Converters for PFC in SMPS ,IOSR Journal of Electrical and Electronics Engineering (IOSR-JEEE) e-ISSN: 2278-1676,p-ISSN: 2320- 3331. [5] M.H. Rashid, Power electronics: circuits, devices and applications Prentice-hall, 1993. [6] N. Mohan, T.M. Undeland, and W.P. Robbins, Power electronics: converters, applications, and design, Wiley, 2007. [7] F. M. Shahir and E. Babaei, A New Structure for Non-Isolated Boost DC-DC Converter Based on Voltage-Lift Technique, in Proc. PEDSTC, 2017, pp. 25-30. [8] E. Babaei and M.E.S. Mahmoodieh, Calculation of output voltage ripple and design considerations of sepic converter, IEEE Trans. Ind. Electron., vol. 61, no. 3, pp. 1213-1222, Mar. 2014. [9] Abbas A. Fardoun, Senior Member, IEEE, and Esam H. Ismail, Senior Member, IEEE Ultra Step-Up DCDC Converter With Reduced Switch Stres , IEEE TRANSACTIONS ON INDUSTRY APPLICATIONS, VOL. 46, NO. 5,SEPTEMBER/OCTOBER 2010.
[10] L. Huber and M. M. Jovanovic, A design approach for server power supplies for networking, in Conf. Rec. IEEE Appl. Power Electron. Conf., 2000, pp. 11631169. [11] D. Maksimovic and S. Cuk, Switching converters with wide DC conversion range, IEEE Trans. Power Electron., vol. 6, no. 1, pp. 151157, Jan. 1991. [12] J. Wang, W. G. Dunford, and K. Mauch, A comparison of modified boost converters with continuous inductor current mode and ripple free input current with conventional converters, in Conf. Rec. IEEE Ind. Appl. Soc. Annu. Meeting, 1996, pp. 878 885. [13] T. J. Liang and K. C. Tseng, Novel high-efficiency step-up converter, Proc. Inst. Elect. Power Appl., vol. 151, no. 2, pp. 182190, Mar. 2004. [18] T. J. Liang and K. C. Tseng, Analysis of integrated boostflyback step-up converter, Proc. Inst. Elect. Power Appl., vol. 152, no. 2, pp. 217225, Mar. 2005. [14] On-Cheong Mak, Yue-Chung Wong, and Adrian Ioinovici, Senior Member, ZEEE , Step-up DC Power Supply Based on a Switched-Capacitor Circuit , Step-up DC Power Supply Based on a Switched-Capacitor Circuit. [15] Kwasinski Alexis, Identification of feasible topologies for multiple input DC to DC converters, IEEE Trans Power Electron 2009;24(3):85661. [16] Peng Fang Z, A new ZVS bidirectional DC to DC converter for fuel cell and battery application, IEEE Trans Power Electron 2004;19(1):5465. [17] Xu Haiping, Kong Li and Xuhui Wen, Fuel cell power system and high power DC to DC converter, IEEE Trans Power Electron 2004;19(5):12505. [18] A. Ajami, H. Ardi, and A. Farakhor, Design, analysis and implementation of a buckboost dc-dc converter, IET Power Electron., vol. 7, no. 12, pp. 2902-2913, Dec. 2014. [19] M.R. Banaei, H. Ardi, and A. Farakhor, Analysis and implementation of a new single-switch buckboost DC/DC converter, IET Power Electron., vol. 7, no. 7, pp. 1906-1914, July 2014. [20] M. Forouzesh, Y. P. Siwakoti, S. A. Gorji, F. Blaabjerg and B. Leman, Step-up dc-dc converters: a comprehensive review of voltage-boosting techniques, topologies, and applications, IEEE Trans. Power Electron., vol. 32, no. 12, pp. 9143-9178, Dec. 2017. [21] BenlafkihAbdessamad, Kritsalah-ddine, et al., Design and Modeling of DC-DC Boost Converter for mobiled Device Applications, International Journal of Science and Technology, Vol.2, No.5, May 2017. [22] ShafinazA.Lopa, S.Hossain, Design and Simulation of DC-DC converters, International Research Journal of Engineering and Technology, Vol.3, issue:1, Jan 2016. . [23] Ashfaq Shah, S.P.Phulambrikar, Simulation of Sepic Converter, International Journal of Engineering Sciences and Research Technology, ISSN:2277-9655, August 2015. [24] Travis Elichhorn, Boost Conveter Efficiency Through Accurate Conditions, Power Electronics Technology, September 2008. [25] D. S. L. Simonetti, J. Sebastian, F. S. dos Reis, and J. Uceda, Design criteria for SEPIC and Cuk converters as power factor Pre- regulators in discontinuous conduction mode,in Proc. IEEE Ind. Electron. Motion Control Conf., 1992, vol. 1, pp. 283288. [26] Y.P. Hsieh, J.F. Chen, T.J. Liang, and L.S. Yang, Novel high step-up dc-dc converter with coupled-inductor and switched- capacitor techniques for a sustainable energy system, IEEE Trans. Power Electron., vol. 26, no. 12, pp. 3481-3490, Dec. 2011.