
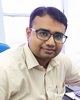
- Open Access
- Authors : Bindul A Gohil
- Paper ID : IJERTV11IS040113
- Volume & Issue : Volume 11, Issue 04 (April 2022)
- Published (First Online): 23-04-2022
- ISSN (Online) : 2278-0181
- Publisher Name : IJERT
- License:
This work is licensed under a Creative Commons Attribution 4.0 International License
A Case Study on Repairing and NDT inspection of 3000 MT Ammonia Storage Tank Installed at GSFC Sikka Unit
Bindul A. Gohil Deputy Manager (Mechanical)
Mechanical Maintenance Department
Gujarat State Fertilizers & Chemicals Ltd, Sikka Unit PO: Motikhavdi District: Jamnagar
Abstract This article describes the methodology followed for the NDT inspection and repairing of both ammonia storage tanks, repairs and modifications carried out on the tank. Ammonia Storage Tank No.76-2001 was commissioned in year 1986-87 & Tank No.76-2017 was commissioned in year 2001 at M/S. Gujarat State Fertilizers & Chemicals Limited, Sikka Unit and is in service since then. This case study outlines the important methods and techniques of repairing of Ammonia tank and Non-Destructive techniques for the same. After continues services of more than 17 years it was decided to de- commission the tank to carry out NDT inspection of Ammonia storage tank No.1 (Tag No.76-2001). All the activities start from de-commissioning to re-commissioning was carried out in house. Only support of external agencies was taken for repair and inspection Services.
Keywords Maintenance management, Non-destructive testing, Enhance tank service life.
-
INTRODUCTION
Being a part of our expansion plan, and, with an aim of catering to the needs of Gujarat's farmers, GSFC established its coastal Di-Ammonium-Phosphate (DAP) plant at Sikka, Motikhavdi (27 KM from Jamnagar, and 10 KM from the Sikka Port. This venture has a capacity of producing 9, 84,000 MTPA DAP. The plant produces DAP from merchant grade Phosphoric Acid and Ammonia. The Phosphoric Acid is sourced from Morocco, Tunisia and South Africa, whereas Ammonia comes from Bahrain, Qatar, and Saudi Arabia. Both Phosphoric Acid and Ammonia then arrive at Sikka jetty, from where it is transported via a pipeline to the GSFC plants. Sulphuric Acid and Bentonite are added for grade adjustment. The plant was originally designed for DAP, but it also has the flexibility of producing other products that are attuned to the market requirements. The plant successfully produced Ammonium Phosphate Sulphate (APS) for the first time in 2001. The unit has been duly facilitated to produce NPK Fertilizers.
Inspection & Maintenance play a vital role in the field of Mechanical engineering. Ammonia tank is a very critical in nature and hazardous also. Storage of liquid ammonia is a very big thing in Fertilizers industries. In this case study all Major repairing of ammonia tank bottom and shell portion and Non-Destructive techniques of ammonia tank are mentioned. All the activities perform with zero accident and
no harm. It would be beneficial to the maintenance or project engineer who engaging the same field. Also, in the subject case study activity flow chart mentioned for the detail Repairing work like replacement of bottom and shell portion.
-
OBJECTIVES
-
Prevention of damages due to corrosion effect and keep tank in good working condition
-
To repair the tank, extend the good service life.
-
To avoid major and minor accidents and incidents of tank.
-
-
DESCRIPTION OF AMMONIA STORAGE TANK
The complex has two ammonia storage tanks each having 3000 MT capacity for storage of liquid ammonia at near atmospheric pressure and at 33 °C. The tanks were commissioned in 1986- 87 and 2001 respectively. Both Tanks have their independent refrigeration and re-liquefaction systems. The storage tank is double walled, double integrity type, also known as Cup-in- Tank comprising as inner cup (in which ammonia liquid is stored) & the outer tank. The outer tank is designed for full containment of liquid & vapor in the event of failure of inner tank. The annular space and dome provide the required vapor space. Both inner cup & outer cup and the outer tank are fabricated out of low temperature carbon steel (LTCS).
Fig. 1. Ammonia Storage Tank
The tank is designed as per API 620, Appendix R. The outside of the outer tank is insulated with 150 MM thick polyurethane foam insulation that shall be foamed in Situ. Insulation is protected from surrounding by corrugated aluminum sheet cladding. The tank bottom is insulated with 150 MM foam glass & siphorex block. The top of cup below the roof is insulated with resin bonded mineral wool stacked to a thickness of 250 mm on a deck suspended from the dome roof. The roof is bare painted.
The tank is provided necessary instruments like float type level indicator, dP type level indicator, temperature recorder, level indicator for annular space, pressure recorder
& pressure indicator. Tank is provided for 02 Nos. of pressure relief vales with set pressure of 1000mmwcg & 1050mmwcg to safeguard the tanks against overpressures & 02 Nos of vacuum relief valves for protecting the tank from vacuum.
The tank rest on elevated foundation slab supported on concrete columns to permit free air passage below the tank so as to avoid
the freezing of foundations. The tank is provided with a ladder for going inside the cup.
-
Design Parameter of Ammonia Storage tank
-
Capacity: 3000 MT
-
Type: Double integrity cup-in-cup tank
-
Diameter: 21.6m
-
Height: 16m
-
Material: LTCS
-
Design Pressure: -50 to 1050mmWC g
-
Design Temperature: -40 °C
-
Process fluid: Liquid Ammonia at -33 °C
-
Density: 0.6814 Kg/m3
-
Design Pressure: Atmospheric
-
Tank CUP ID: 20000 mm,
-
Tank CUP height: 15000 mm
-
-
Visual Inspection
After completion of de commissioning activities, outer tank shell manhole cutting started with hot work permit. After cutting of outer tank shell manhole, it is required to check oxygen content inside the tank. After getting comfort condition inside (Annular space) the tank cutting of CUP manhole started. After opening of CUP manhole, it is necessary to check oxygen level again. If there is no any comfort working condition inside the tank, De humidifier with ID (Induce Draft) fan connected with the tank manhole and top roof manhole respectively. The oxygen level needs to be checked every day basis. After getting the comfort condition inside the tank, visual inspection started. While inspecting the tank from inside, it was observed that many cup bottom plates were bulged in convex shape from its original position (almost 50% of bottom) and also there was fracture from cup shell to cup bottom plate. The fracture/ through cracks mentioned in Photos at figure No. 5/6.
Fig 2. Opening of tank Manhole
Fig 3. Visual Inspection
Fig 4. Bulging and through crack at bottom
Fig 5. Through Crack at bottom
Fig 6. Fracture at Bottom to shell joint
-
Activities for repairing of tank
-
Measurement of Bulge area of Tank Bottom/sketch plate and annular plate
-
Bottom plate layout marking
-
Estimation of total quantity required
-
Selection of MOC- (Material of Construction) & Create PR for the same
-
Tender Enquiry for Repairing Activity & work order awarded
-
Removal of insulation & cutting of bottom & Shell plates
-
Preparation of Welding Procedure Specifications (WPS)
-
Preparation of Procedure Qualification Record (PQR)
-
Approval of Inspection Test Plan (ITP)
-
Welding of bottom and Shell plate
-
100 % DP Testing of bottom and Shel plate welding
-
100 % Radiography Testing of shell plate welding
-
Diesel Chalk testing of new shell to bottom plate joint
-
Vacuum box & WFMPI of repaired portion of Tank bottom
-
Final Site Clearance of tank for further NDT inspection
-
-
Measurement of bulge area
Fig 7. Measurement of bulge area
The green zone indicates bulge area inside bottom of tank.
-
Scope of work for repairing of tank
After detailed examine the tank bottom, it was decided by Inspection and Maintenance department following actions to be taken for repairing of subject ammonia tank.
-
This work incorporated major activities like Permit procedure, removal of outer tank insulation, cutting of outer tank shell and CUP shell for easy movement of bottom plate and manpower, fabrication and replacement of bottom damaged plates and shell plate
& reversal activities.
-
We have observed that approx. 270 M2 area including bottom & shell plates are in damaged condition and same had been replaced.
-
The welding of bottom area is 180 Running meter & Shell area is 30 Running meter.
-
Removal of outer tank shell insulation of approx. 2 Meter X 8 Meter size (One plate of first shell course).
-
Cutting of outer tank shell plate approx. 2 Meter X 8 Meter size (One plate of first shell course) for entry of man/material.
-
Cutting of CUP tank shell plate approx. 2 Meter X 8 Meter size (One plate of first shell course) for entry of man/material.
-
Providing of stiffener/ supports to cup shell plates to
maintain circularity & height/level.
-
Replacement of damaged bottom plates of CUP tank as per existing bottom plate layout with new plates (Overlap Joints).
-
After completion of bottom plate & shell plate replacement 100 % DP test was carried out for following: (1) After back chipping and (2) After final welding (from inside).
-
100 % radiography as per API-620 Appendix-R was carried out for all but joints of tank shell & CUP shell plate joints.
-
After completion of above repairing work, NDT inspection of bottom & shell portion of tank was carried out by inspection team and no any abnormalities found in bottom as well as shell.
-
-
Check points of weld procedure
-
Prior to start of welding all fit up shall be checked to verify & confirm in accordance with approved WPS. WPS will have to be qualified preparing fresh PQR. Impact testing will also be required for PQR.
-
All filler metal used for tack welds shall be of the same composition as the filler metal for the joint.
-
Tack welds that are incorporated in to the finished weld shall be visually inspected for defects. All defects shall be removed before covering tack welds with additional weld metal.
-
Welding conditions such as current, voltage, polarity, pre- heating, inter pass temperature, type of consumables, welding process and base metal shall be verified prior to start of welding.
-
WPS number and Welder ID number shall be marked adjacent to the joint to be welded and only qualified welder shall carry out welding as per approved WPS.
-
Welding qualification validity shall be checked prior to allocation of the welders on the job.
-
All electrodes and filler wire to be used shall conform to AWS 7018-1 SUPRATHERM SPECIAL and shall be approved make of D & H/GSFC Approved only.
-
Welder shall be qualified as per ASME Sec. IX or API 620. The welder has to be qualified by inspection agency, deputed by GSFC.
-
-
Check points of Inspection work
-
Stage wise inspection of all stages starting from Material inspection to completion of job.
-
The subject job is to be carried out under the direct supervision and instruction of GSFCs inspection engineer/engineer in charge. Decision of engineer in charge shall be considered as final and binding.
-
All the records and readings/measurement taken during the course of execution shall be prepared and submitted in triplicate to GSFC.
-
On completion of welding, all welds shall be 100% visually inspected for following.
-
Irregular bead, excess reinforcement, roots penetration (If access permits)
-
Surface defects such as cracks, undercutting, and lack of fusion.
-
Leg length and throat thickness of fillet weld.
-
Removal of slag, spatters, arc strikes etc.
Fig 8. Removal of Shell insulation
Fig 9. Removal of bottom plate
Fig 10. Cutting of bottom plate
Fig 11. Bottom sand layer 50 mm
Fig 12. New plates unloading at site
Fig 13. New plate welding started
Fig 14. Plate piece for welding test
Fig 15. DP test of welding joints
Fig 16. Final welding inside tank
Fig 17. Diesel chalk test of bottom to shell joint
Fig 18. Wet Fluorescent magnetic particle test
Fig 19. Vacuum Box testing
Fig 20. Final welding of inner tank shell
Fig 21. Final welding of outer tank shell
-
-
-
NDT Inspection of complete tank
After completion of repairing and 100 % inspection of repaired/replaced portion, further complete NDT inspection was started as per scope. Following inspections carried out.
-
Wet Fluorescent Magnetic Particle Testing (WFMPT)
-
Dye Penetrant Test (DP TEST)
-
Thickness measurement:
-
Hardness Test
-
Micro structure Examination
-
Vacuum Box Test
-
Foundation Inspection
-
Examination of Insulation of Deck
-
Dished end weld inspection (Radiography and DP test)
-
-
Wet Fluorescent Magnetic Particle Testing (WFMPT)
-
100 % WFMPT of all weld joints including HAZ of Shell (LS & CS), shell to bottom plates, bottom plates, Supports, nozzles etc. from inside of inner tank and inside out outer tank
-
100% of WFMPT of roof weld joints from inside up to approachable level from suspended deck.
-
100% of WFMPT of all nozzles weld joints connected to tanks from inside and wherever possible from outside.
-
100% of WFMPT of all anchors anchor Gusset plate, Bent plate C-clamp for anchor and Seal plate welds.
-
100% of WFMPT support part of fillet joints of monkey ladders, level indicator and pipe support connection from inside and outside wherever possible.
-
On locations where any abnormality is observed during visual inspection.
Fig 22. WFMPT
Wet Fluorescent Magnetic Test (WFMT) this technique requires the use of UV light in a darkened environment. This is the most sensitive MPI technique and used extensively in the Power Generation and Petrochemical Industry during maintenance inspections. Electromagnet or Portable AC/DC Coil units are used for this inspection technique.
-
-
Dye Penetrant Test (DP TEST):
-
Random DP Check of internals welded to the shell e.g. Tank stiffeners, internal supporting structures of deck, etc. where WFMPT is not feasible.
-
Fillet weld and butt weld of all anchors and fillet weld of nozzles by DP Test where WFMPT is not feasible.
-
Any other locations where WFMPT is not feasible
Fig 23. DPT
-
-
Thickness measurement:
-
Min. 9 points on each plate of Inner tank bottom plate & annular space.
-
Min. 9 points on each plate of Inner tank shell.
-
Min. 9 points on each plate of outer tank shell.
-
Min. 5 points on each plate of roof.
-
Min. 4 points (Top, bottom and sides) of all connected nozzles to the tanks.
-
Min. 4 points at every 1.5-meter length of internal piping.
-
-
Hardness Test:
-
Micro structure Examination
-
In-situ metallographic shall be carried out at selected @ 12 location of bottom plate, first shell course of cup shell, outer shell and nozzles covering weld, HAZ and parent metal.
-
Equipment used
-
For Surface preparation: Different fine size of Emery paper, Diamond paste
-
For Etching: methanol, 6% nital, 3% nital solution
-
For replication: plastic tape made of Cellulose acetate material is soaked in Acetone
-
Surface condition: surface preparation with mechanical / electrolytic polishing methods
-
-
Vacuum Box Test:
-
100% Vacuum box leak test under the vacuum of approx. 200 mm of Hg. of the weld joints of bottom plate including annular space for detecting the leakage through defects.
-
Equipment Used
-
Vacuum Boxes for Both Lap & Butt Welds
-
Vacuum Pump
-
Vacuum Gauge
-
Sealing Clay (Putti)
-
Soap Solution
-
Surface Condition: Cleaned, Dust Free & Smooth
-
Test Pressure: Under Vacuum of 200mm of Hg
Vacuum box testing is a non-destructive examination (NDE/NDT) used for locating welding leaks. A vacuum box and a compressor create a high or low-pressure vacuum and a detergent solution is applied to the test area. The detergent bubbles help to identify the leaks within the created pressure envelope. The main objective of the Vacuum box testing technique is to locate leaks in welds due to through-thickness discontinuities. This is accomplished by applying a solution to a weld and creating a differential pressure across the weld causing the formation of bubbles as leakage gas passes through the solution. This testing is to be performed prior to any main vessel or tank testing following the completion of all welding. This article will briefly explain the leak testing procedure using the vacuum box method that can be used for all metals.
-
-
-
Foundation Inspection
-
Visual inspection of civil foundation to identify weak spots if any.
-
Inspection by rebound hammer test at selected @ 300 locations.
-
Ultrasonic pulse velocity test with digital ultrasonic concrete tester at @ 150 locations
-
Carbonation test at about 7 to 10 spots.
-
Half-cell potentiometer at @ 10 spots
Fig 24. Foundation Test
-
-
Dished end weld inspection (Radiography and DP test):
On completion of inspection job, inspection of welding of dished ends by DP. Also arrange for radiography and review radiographs of these welds.
Fig 25. Dished End- Main Manhole welding & Inspection
Fig 26. Scaffolding prepared inside the tank
Fig 27. Inspection of Suspended deck
-
Procedure of Hydro testing of Tank after completion of Inspection & repairing
-
Vent the tank to atmosphere when filling with of water.
-
Fill the cup with water up to 25% level in one step per day i.e., cup to be filled up to 15.8 M level in 4 steps in 4 days
-
After full filling up to 15.8M level start visual inspection in annular space.
-
Make the arrangements for hydro-pneumatic testing.
-
Apply to the enclosed space an air pressure equal to 1313 mm of water column.
-
Hold this pressure for one hour.
-
Reduce the air pressure up to the design pressure of 1050 mm of water column.
-
Check all joints of roof and tank by soap solution. Check the opening pressure of pressure
& vacuum relief valves by pumping air and releasing the pressure followed by partial withdrawal of water from the cup shell, up to 50 mm WC.
-
Release the air pressure & bring the tank to atmospheric pressure by opening vent valves connected with tank roof.
-
Drain out the water from cup.
-
-
Conclusion
Ammonia Storage Tanks (ASTs) are most critical equipment considering the highly hazardous nature of the stored liquid ammonia thus considering safety first. ASTS are also one of the most challenging and difficult equipment to inspect. By the combined efforts of maintenance & Inspection department of GSFC, the numerous unforeseen problems that arose as the repair work progressed were tackled, the tank repaired successfully. Now NDT inspection & hydro testing of tank is under progress.
-
AKNOWLEDGEMENT
The authors would like to thank all those who helped direct or indirect to complete work. A specially thank to Inspection department of GSFC.
-
Abbreviations:
-
AST: Ammonia Storage Tank
-
DPT: Dye Penetrant Testing
-
SST: Sikka Shore Terminal
-
GSFC: Gujarat State Fertilizers & Chemicals Limited
-
SU: Sikka Unit
-
HAZ: Heat Affected Zone
-
MPT: Magnetic Particle Testing
-
NDT: Non-Destructive Testing
-
PUF: Poly Urethane Foam
-
RT: Radiographic Testing
-
SCC: Stress Corrosion Cracking
-
WFMPT: Wet Fluorescent Magnetic Particle Testing
-
-
Reference
-
Code of Practice for Liquid Ammonia Storage vessels UHDE, 1986-87
-
Tank Inspection Repair, Alteration, and Reconstruction API Standard 653, Second edition, Dec 1995
-
Nondestructive Examination – ASME section V
-
Design and Construction of Large, Welded, Low-Pressure Storage Tanks API 620,Ninth Edition, Feb 1996
-
Decommissioning, Repair and Inspection of 10,000 MT Ammonia Storage TankbyGSFC Sikka Unit in year 2015-16.
-