
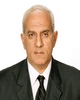
- Open Access
- Authors : Sharaf El-Dien* T.A.Y , Mohamed Abd El-Latif , Metwally Mohamed
- Paper ID : IJERTV11IS040121
- Volume & Issue : Volume 11, Issue 04 (April 2022)
- Published (First Online): 11-05-2022
- ISSN (Online) : 2278-0181
- Publisher Name : IJERT
- License:
This work is licensed under a Creative Commons Attribution 4.0 International License
Study of Vehicle Crashworthiness Applying Composite Materials (Frontal and Offset Impact)
Sharaf El-Dien* T.A.Y Dr., Egyptian Armed Forces Cairo, Egypt
Mohamed Abd El-Latif
Machine Design & Production Department MTC
Cairo, Egypt
Metwally Mohamed Automotive Department MTC
Cairo, Egypt
Abstract The automotive industry is faced with an unprecedented challenge, to produce lighter vehicles with less fuel consumption and pollution without sacrificing internal roominess and passenger safety. Therefore , new materials other than steel are being considered . This study presents the usage of composite materials instead of steel in certain parts (main rail, bumper, hood, fenders, wheel housing and doors) of the vehicle to improve its performance by studying of vehicle crashworthiness (frontal and offset impact). A finite element model of a 1994 Chevrolet C-1500 pick-up truck was modified and used for this purpose with the aid of the multi-purpose finite element code LS-DYNA . The results showed that, the usage of composite materials in vehicle frame (or all parts together) gives higher percentage of weight reduction and higher percentage of absorbed energy , than in the case of steel .
Keywords Car Body Structural Analysis, Finite Element Analysis, composite materials, crashworthiness .
-
INTRODUCTION
Automotive industry is one of the leading industries in the world . One of the goals of automotive industry is a lighter and safer vehicle, with more miles per gallon and fewer pollutants . Many factors are considered and the vehicle structure is the main dominating one .
A key factor in the structural engineering design, is the impact protection for vehicle occupants. A lighter vehicle means lighter weight materials which should fulfill the requirements of safety. So, new materials other than steel are being considered in the fabrication of vehicle's structural parts such as composite materials. The composite materials give the solution for these problems in design and can be tailored to satisfy the required needs.
Several approaches were investigated in order to achieve the goal of producing a lighter and safer vehicle. One approach was to downsize the vehicle ; after 1973 [1]; another approach was to substitute conventional structural materials with innovative materials [2] , which give the same or better performance (but with less weight). Almost every part of the vehicle structure was investigated by replacement with another one made from non-conventional material . For example vehicle frame was replaced with another frame made totally from reinforced aluminum by Ford Corporation [3]. Moreover , the steel body was replaced by a reinforced
aluminum one in a model of Audi's cars [3] . The objective of this work is to study the vehicle structural mechanics and the possibility to replace the conventional materials with composite ones in automotive structural parts (main rail, bumper, hood, fenders, wheel housing and doors) separately and as a combination, to improve the performance of the vehicle (decrease the vehicle weight, increase the power to weight ratio and improve the absorbed energy).
The LS-DYNA Chevrolet C-1500 model [4] , [5] was modified to fulfill the above objectives . The modified model was validated by comparing the results with that of the tests and models of the National Crash Analysis Center (NCAC
-
METHOD OF APPROACH
LS-DYNA [6] is a general purpose finite element code for analyzing the large deformation and dynamic response of structures. It uses a displacement-based, Lagrangian, central- difference finite element formulation to solve the dynamic response of nonlinear structural problems. The formulation makes use of Cauchy's first law of motion and the principle of virtual work to determine the potential energy equation for the general three-dimensional problem [6] , [7]:
where ij is the virtual strain tensor attributed to the virtual displacement xi for a three-dimensional body located in a fixed (Lagrangian) space. The body is subjected to traction forces ti(t) (forces per unit area) over a portion of its outer surface St, prescribed displacements di(t) over a surface Sd and external body forces bi(t) (forces per unit volume) over its entire volume V, ij denotes Cauchy's stress tensor is the material current density, and is the current acceleration of the particle .
The potential energy equation is first discretized in space through the finite element mesh and shape functions. It is then discretized in time through the explicit central difference method to derive the dynamic equations of motion .
A finite element model was developed by the NCAC, (using LS-DYNA code) , for a 1994 chevrolet C-1500 pick-up truck as a regular- cab, fleet side long-box with a total length of 5.4 meters and a wheelbase of 3.34 meters.
The engine is a 4.3 liter Vortec V6 with electronic fuel injection coupled to an automatic transmission with a rear wheel drive configuration [4] , [5] . This model was in static condition ( zero impact velocity ) with no wall or floor . To use this model in the present study , it was necessary to be modified by :
-
Using impact velocity 35 mph (56.3 km/hr) .
-
Changing the material behavior of the main rail
from piecewise linear plasticity to composite damage
.
-
Adding wall and floor .
The modified model results were compared with those of the crash test and crash simulation conducted by the NCAC and was found adequate [8-9] .
-
-
MODEL RESULTS AND ANALYSIS
It is important to analyze the energy absorption by the different components in the vehicle. This can be obtained in the simulation by computing the material internal energies in the model. The internal energy of the materials is the sum of the plastic strain energy and the elastic strain energy.
Frontal Impact :
Table (1) shows the percentage of the total energy absorbed through the different components [4] , [5] . From this table , it is obvious that , the main rail, bumper, hood, fenders, wheel housing and doors are the effective parts in crashworthiness and have the maximum values of absorbing the internal energy. A comparison is made for (displacement, velocity and internal energy) curves for the chosen parts before and after changing their materials to composite materials and aluminum alloy .
Frontal impact is studied for each of the chosen parts and for all the chosen parts together at node 16154 under the driver on the frame and at node 81 on the middle of the pumper because they represent the driver location and the total deformation during the crash test as shown in Fig (1) .
Tables (2), (3) and (4) show the properties of steel [3-5] , kevlar/epoxy [2] , boron /Al [2] and aluminum alloy materials [3-5] . Tables (5) and (6) show the chemical composition of aluminum alloy and volume fraction of kevlar/epoxy and boron/Al materials.
TABLE (1). Material internal energy for a 56 km/hr frontal impact into a rigid wall ( before changing materials ) [4-5].
Density
7.85 (103Kg/m3)
Youngs Modulus
210 (GPa)
Poissons Ratio
0.3
Yield Stress
215 (MPa)
Fig. (1). Position of the node 16154 on the model. TABLE (2) The properties of steel material [3-5].
TABLE (3) The properties of aluminum alloy material (2024-T4) [3-5].
ong's Modulus (GPa)
Poisson's Ratio
Ultimate Stress (MPa)
Yield Stress (MPa)
Density (103Kg/m3)
74.5
0.33
470
320
2.77
TABLE (4) The properties of composite materials (boron/aluminum and kevlar/epoxy) [2].
Boron /Al
Kevlar /Epoxy
Density
2.65E-09
(ton/mm3 )
1.38 E-09 (ton/mm3 )
Axial Youngs modulus
227 (MPa)
76.8 (MPa)
Transverse Youngs modulus
139 (MPa)
55 (MPa)
Poissons ratio 12
0.24
0.34
Poissons ratio 23
0.36
0.37
Shear modules G12
57.6 (MPa)
2.07 (MPa)
Shear modules G23
49.1 (MPa)
1.4 (MPa)
TABLE (5) The chemical composition of aluminum alloy material [3-5].
(Al) %
Others Total %
(Ti) %
(Zn) %
(Cr) %
Remainder 93.05-90.75
0.15
0.15
0.25
0.1
(Mg) %
(Mn) %
(Cu) %
(Fe) %
(Si) %
1.2-1.8
0.3-0.9
3.8-4.9
0.5
0.5
TABLE (6) The volume fraction of kevlar /epoxy and boron / aluminum materials [2].
Material Parts
Internal Energy (KJoules)
Percentage
Whole Vehicle
214
100%
Rails and its matching structures
93.20
43.55%
Bumper and its matching structures
26.10
12.20%
Engine and its matching structures
23.00
10.75%
Radiator and its matching structures
21.80
10.19%
Toepan and front floor
15.20
7.10%
Hood
10.70
5.00%
Fender
9.80
4.58%
Wheelhouse
1.65
0.77%
Remaining components
12.50
5.84%
(Epoxy) %
(Kevlar) %
(Al) %
(Bo) %
31.6
68.4
0.85
0.15
The resulting curves are plotted in the longitudinal direction (x direction) only , because the car does not rotate significantly around the z-axis even after the max. deformation point is reached . Thus , the variations in the y and z directions are neglected. Figure (2) shows two images of the vehicle before and after the frontal impact test [8].
Fig. (2) Vehicle before and after the frontal impact test [1].
Figure (3) shows that the Boron/Al applied on main rail provides displacement (1.3 times steel) . The max time at which velocity reaches zero is shown in Fig. (4). The max. internal energy (6 times steel) is shown in Figure (5).
Changing the bumper material, Fig. (6) shows that the displacement resulting value of the Boron/Al is located between the steel and the aluminum alloy (1.07 times steel). The max time at which velocity reaches zero is shown in Fig. (7) . The internal energy has the max. value (90 times
steel) as shown in Fig. (8).
In the case of changing of (hood, fenders, wheel housing and doors) material by Boron/Al, Fig. (9) shows that Boron/Al provides the max. displacement (1.07 times steel). The max time at which velocity reaches zero is shown in Fig.
(10) . The max. internal energy (90 times steel) is shown in Fig. (11).
In case of changing of the all parts materials together, Fig. (12) shows that Boron/Al provides the max. displacement (1.24 times steel).
The max time at which velocity reaches zero is shown in Fig. (13). The max. internal energy (6.2 times steel) is shown in Fig. (14).
1E+03
9E+02
8E+02
7E+02
1.8E+04
1.6E+04
1.4E+04
Velocity (mm/s)
1.2E+04
1.0E+04
8.0E+03
6.0E+03
4.0E+03
2.0E+03
0.0E+00
-2.0E +01
-4.0E+01
1E+08
9E+07
Internal Energy (joules)
8E+07
7E+07
6E+07
5E+07
4E+07
3E+07
2E+07
1E+07
0E+07
9E+02
8E+02
Displacement (mm)
7E+02
6E+02
5E+02
4E+02
3E+02
2E+02
AL
Boron/AL Steel Kevlar/Apoxy
117 213 340 465 581 697 813 929 1045 11611277 1393 1509 1625 17411857 1973 2069 2205 2321
Time (ms)
Fig. (4) Velocity of node 16154 due to frame material changing.
AL
Boron/AL Steel Kevlar/Apoxy
11 21 31 41 51 61 71 81 91 101 111 121 131 141 151 161 171 181 191 201 211 221 231 241
Time (ms)
Fig. (5) Internal energy of frame due to material changing.
AL
Boron/AL Steel Kevlar/Apoxy
Displacement (mm)
6E+02
5E+02
4E+02
3E+02
AL
Boron/AL Steel
1E+02
0E+02
117 213 340 465 581 697 813 929 1045 11611277 1393 1509 1625 17411857 1973 2069 2205 2321
Time (ms)
2E+02
1E+02
0E+02
Kevlar/Apoxy
213 465 697 929 1161 1393 1625 1857 2069 2321
Fig. (6) Displacement of node 16154 due to bumper material changing.
1.8E+04
1.6E+04
1.4E+04
Time (ms)
Fig. (3) Displacement of node 16154 due to frame material changing
1.2E+04
Velocity (mm/s)
1.0E+04
8.0E+03
6.0E+03
AL
Boron/AL Steel Kevlar/Apoxy
4.0E+03
2.0E+03
0.0E+00
-2.0E +01
-4.0E+01
117 213 340 465 581 697 813 929 1045 11611277 1393 1509 1625 17411857 1973 2069 2205 2321
Time (ms)
Fig. (7) Velocity of node 16154 due to bumper material changing.
1E+08
1E+03
9E+07
9E+02
Internal Energy (joules)
8E+07
8E+02
7E+07
6E+07
5E+07
4E+07
3E+07
2E+07
AL
Boron/AL Steel Kevlar/Apoxy
Displacement (mm)
7E+02
6E+02
5E+02
4E+02
3E+02
2E+02
AL
Boron/AL Steel Kevlar/Apoxy
1E+07
1E+02
0E+07
11 21 31 41 51 61 71 81 91 101 111 121 131 141 151 161 171 181 191 201 211 221 231 241
Time (ms)
0E+02
117 213 340 465 581 697 813 929 1045 11611277 1393 1509 1625 17411857 1973 2069 2205 2321
Time (ms)
Fig. (8) Internal energy of bumper due to material changing
Fig. (12) Displacement of node 16154 due to all parts material changing.
9E+02
Displacement (mm)
8E+02
7E+02
6E+02
5E+02
4E+02
3E+02
2E+02
1E+02
0E+02
AL
Boron/AL Steel Kevlar/Apoxy
117 213 340 465 581 697 813 929 1045 11611277 1393 1509 1625 17411857 1973 2069 2205 2321
Time (ms)
1.8E+04
1.6E+04
1.4E+04
Velocity (mm/s)
1.2E+04
1.0E+04
8.0E+03
6.0E+03
4.0E+03
2.0E+03
0.0E+00
-2.0E +01
-4.0E+01
AL
Boron/AL Steel Kevlar/Apoxy
117 213 340 465 581 697 813 929 1045 1161 1277 1393 1509 1625 1741 1857 1973 2069 2205 2321
Time (ms)
Fig. (9) Displacement of node 16154 due to hood, fenders, wheel housing and door material changing.
1.8E+04
1.6E+04
1.4E+04
Fig. (13) Velocity of node 16154 due to all parts material changing.
1E+08
9E+07
Velocity (mm/s)
1.2E+04
1.0E+04
8.0E+03
6.0E+03
4.0E+03
2.0E+03
0.0E+00
-2.0E +01
-4.0E+01
AL
Boron/AL Steel Kevlar/Apoxy
117 213 340 465 581 697 813 929 1045 11611277 1393 1509 1625 17411857 1973 2069 2205 2321
Time (ms)
8E+07
Internal Energy (joules)
7E+07
6E+07
5E+07
4E+07
3E+07
2E+07
1E+07
0E+07
AL
Boron/AL Steel Kevlar/Apoxy
11 21 31 41 51 61 71 81 91 101 111 121 131 141 151 161 171 181 191 201 211 221 231 241
Time (ms)
Fig. (10) Velocity of node 16154 due to hood, fenders, wheel housing and doors material changing.
1E+08
9E+07
Internal Energy (joules)
8E+07
7E+07
Fig. (14) Internal energy of all parts due to material changing.
The previous results are summerised in Table (7) .
Frame
Bumper
Hood, Fenders,etc
All
Dis.
Vel.
I.E.
Dis.
Vel.
I.E.
Dis.
Vel.
I.E.
Dis.
Vel.
I.E.
Boron/Al
3
1
1
2
3
1
3
2
1
3
2
1
Kevlar/Epoxy
4
2
4
4
1
3
4
1
4
4
1
4
Al Alloy
2
3
2
3
2
2
2
4
2
2
3
2
Steel
1
4
3
1
4
4
1
3
3
1
4
3
TABLE (7): Frontal impact summary ( driver node 16154 ).
6E+07
5E+07
4E+07
3E+07
2E+07
1E+07
0E+07
AL
Boron/AL Steel Kevlar/Apoxy
11 21 31 41 51 61 71 81 91 101 111 121 131 141 151 161 171 181 191 201 211 221 231 241
Time (ms)
where 1:Best 4: Weak.
The same work was done in frontal impact but at the bumper node 81 , and the results are summerised in Table (8).
Fig. (11) Internal energy of hood, fenders, wheel housing and doors due to material changing
TABLE (8): Frontal impact summary ( bumper node 81 ).
Frame
Bumper
Hood, Fenders,etc
All
Dis.
Vel.
I.E.
Dis.
Vel.
I.E.
Dis.
Vel.
I.E.
Dis.
Vel.
I.E.
Boron/Al
3
1
2
2
2
1
3
2
1
3
2
1
Kevlar/Epoxy
4
2
1
4
1
4
4
1
4
4
1
4
Al Alloy
2
3
3
3
3
2
2
4
2
2
3
2
Steel
1
4
4
1
4
3
1
3
3
1
4
3
Tables (7) and (8) show that Boron/Al is the best material to absorb energy which is the most important factor in crashworthiness (then comes velocity and displacement results ). However, Kevlar / Epoxy gives the weakest results especially in internal energy than the others (Al Alloy, Boron/Al and Steel), therefore, the Kevlar/Epoxy will be excluded .
Offset Impact :
Fig. (15) Vehicle before and after the offset impact test.
Similarly, the above work was repeated but for the offset impact at the same mentioned nodes [8] . The results are summarised in Tables (9) and (10).
TABLE (9): Offset impact summary ( driver node 16154 ).
Frame
Bumper
Hood, Fenders,etc
All
Dis.
Vel.
I.E.
Dis.
Vel.
I.E.
Dis.
Vel.
I.E.
Dis.
Vel.
I.E.
Boron/Al
3
1
1
3
1
1
2
3
1
3
1
1
Al Alloy
2
2
2
1
3
2
3
1
2
2
2
2
Steel
1
3
3
2
2
3
1
2
3
1
3
3
TABLE (10): Offset impact summary ( bumper node 81 ).
-
CONCLUSIONS
From both frontal and offset impacts results , it is clear that replacing steel by Boron/Al is the best choice to improve the vehicle performance (weight reduction) and to fulfill the requirements of safety (higher energy absorption).
The choice of the part to be replaced is also important . Therefore , the results of parts replacement by (Boron/Al) for displacement, velocity and internal energy for both frontal and offset impacts are recalled .
The frontal impact study showed that the main rail material change provides the maximum displacement, maximum time of velocity to reach zero and maximum internal energy .
The offset impact study showed that all parts material change provides the maximum displacement and maximum time of velocity to reach zero , but for internal energy the main rail material change is the best .
REFERENCES
[1] Banthia, V.K. , Miller, J.M. , Valisetty, R.R. and Winter, E.F.M. ''Light Weighting of Cars with Aluminum for Better Crashworthiness'', J.SAE, v: 5 p: 5432-5447, 1994. [2] Eltaher, H.M., ''Vehicle Structural Mechanics Considering Innovative Materials'', MSc. Thesis, MTC, Cairo, Egypt, 2000. [3] Donald R., "The Science and Engineering of Materials", Broks/Cole Engineering Division, California, 1984. [4] Zaouk A.K., Bedewi N.E., Kan C.D., Schinke H., "Evaluation of a Multi-Purpose Pick-up Truck Model Using Full Scale Crash Data with Application to Highway Barrier Impacts", Presented at the 29th International Symposium on Automotive Technology and Automation, Florence, Italy, June, 1996. [5] Zaouk A.K, Nabih, N.E., Bedewi, Kan C.D. and Marzougui D., ''Development and Evauation of a C-1500 Pick-Up Truck model For Roadside Hardware Impact Simulation'', FHWA Simulation Conference, Langley, VA, FHWA and GWU, July, 1996. [6] Hallquist, J.O., "LS-DYNA3D Theoretical Manual", Livermore Software Technology Corporation, LSTC Report 1018, 1998. [7] Murphy, "Advanced Mechanics of Materials", McGraw Hill, 2nd ed, USA, 1946. [8] Sharaf El Dien, T.A., ''Applications of Composite Materials in Automotive Engineering (Study of Vehicle Crashworthiness)'', MSc. Thesis, MTC, Cairo, Egypt, 2005. [9] John Fenton, ''Hand Book of Vehicle Design Analysis'', Bretun G, SAE.
Frame |
Bumper |
Hood, Fenders,etc |
All |
|||||||||
Dis. |
Vel. |
I.E. |
Dis. |
Vel. |
I.E. |
Dis. |
Vel. |
I.E. |
Dis. |
Vel. |
I.E. |
|
Boron/Al |
3 |
1 |
1 |
3 |
1 |
1 |
2 |
3 |
1 |
3 |
1 |
1 |
Al Alloy |
2 |
2 |
2 |
1 |
3 |
2 |
3 |
1 |
2 |
2 |
2 |
2 |
Steel |
1 |
3 |
3 |
2 |
2 |
3 |
1 |
2 |
3 |
1 |
3 |
3 |
Tables (9) and (10) showed the same behavior as in frontal impact .