
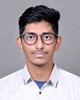
- Open Access
- Authors : Prasanna Venkatesh M , Ramana S K , Santhosh S , Sukumar T R
- Paper ID : IJERTV11IS060040
- Volume & Issue : Volume 11, Issue 06 (June 2022)
- Published (First Online): 10-06-2022
- ISSN (Online) : 2278-0181
- Publisher Name : IJERT
- License:
This work is licensed under a Creative Commons Attribution 4.0 International License
Sensor Based Vibration Detection in Lathe
Mr. Sukumar T R
Associate professor, Department of Mechanical Engineering, Kumaraguru College of Technology, Tamil Nadu, India.
Prasanna Venkatesh M
Student, Department of Mechanical Engineering, Kumaraguru College of Technology,
Tamil Nadu, India.
Ramana S K
Student, Department of Mechanical Engineering, Kumaraguru College of Technology,
Tamil Nadu, India.
Santhosh S
Student, Department of Mechanical Engineering, Kumaraguru College of Technology,
Tamil Nadu, India.
Abstract This project is based on Vibration Detection in conventional lathe using Arduino. Vibration monitoring is the measurement of passing movements in a structure. This project involves developing an Graph Plotter alert when unusual vibrations are detected. It includes a lab-based experiment of detecting vibrations when the different magnitude of the force is applied. This force causes the change in values of the sensor from its initial values. Values of acceleration can be seen on the Display and analysis can be done when required. With the help of this, we can be aware of the vibrations. Properly done, vibration monitoring can be extremely helpful in preventing damage to structures understanding the nature of the damage and ascertaining its cause. Currently, we are using Arduino microcontroller, accelerometer sensor, and LCD Module as our main components. The code of the Arduino Uno microcontroller is written in C++
Keywords Vibration sensor, Lathe vibration, Arduino vibration, Microcontroller
-
INTRODUCTION
Vibration is a mechanical phenomenon whereby oscillations obtain about an equilibrium point. Vibration detection emphasizes the need for incorporating multifunctional, multidisciplinary and sectored approach involving engineering, social and financial processes. This can be useful in many sectors to easily detect the effect of vibrations. Vibration monitoring is the measurement of passing movements in a structure. We are using LCD instruments to detect and record the movement. This project is about "A Vibration Detection Instrument based on Sensors" where electromechanical devices are used to measure acceleration forces. Such forces may be static like the continuous force of gravity or, dynamic to sense movement and vibrations. Acceleration is the measurement of the change in velocity or speed divided by time.
This change is due to vibrations caused by the force that is applied. When the vibrations are detected, its values can be easily noted. The webpage includes the initial set of values and difference between the values when the operation is performed from initial values. When the value exceeds a limit, an alert signal would be generated and Display would be sent to mobile phones.
The objective of this project is to create a vibration detector using Arduino Uno and accelerometer sensor that is used to detect the vibrations. Whenever it would detect unusual vibrations, then alert signals would be generated using buzzer and LED glow and also a message would be sent on a particular mobile number. When an emergency occurs, the first priority is always the safety of life whether ours or others. There are many actions that can be taken to stabilize an incident and minimize potential damage. Actions taken immediately in the first minutes following an emergency situation will significantly affect what happens afterward. So, sending an alert to all the concerned authorities in an emergency situation can help in safeguarding lives. This prototype device will help us to note the vibrations created and if the reading exceeds the particular limit, then it will generate an alert signal.
-
PROBLEM STATEMENT
The decreasing performance and life of machine tools due to undesired vibration is one of the major problems in manufacturing industries. The factors due to vibration reduces the lifetime of the tool pieces and workpiece. The spark occurs at a high-speed rate and deep depth of cut which may damage the tool or affect the surface finish of the workpiece.
-
Causes of Vibration
-
Inhomogeneities in the workpiece material. Variation of chip cross section.
-
Disturbances in the workpiece or tool drives.
-
Dynamic loads generated by acceleration/deceleration of massive moving components.
-
Vibration transmitted from the environment.
-
Self-excited vibration generated by the cutting process or by friction (machine-tool chatter).
-
-
Effects of Vibration
-
Improper surface finish of the workpiece
-
Disfigure/Breakage of cutting tool
-
Risk to employees.
-
-
-
LITERATURE SURVEY
Md. Hasibuzzaman, & Abu Shufian et al (2020) proposed a experiment, It performs the following functions: detecting
vibration, assessing total vibration, and comparing the accuracy of the device to the standard device. The system will employ four ADXL-345 Triple-Axis Accelerometers to detect the object's vibration and relay the data to Arduino.
Viral K. Patel, Maitri N. Patel (2017) the paper describes, the Vibration monitoring has shown to be a powerful tool for detecting localised machine faults, according to analytical methodologies. When these modules are placed close to a bearing housing, they can successfully gather both stationary and nonstationary vibration signature data. Bearing defect detection algorithms may be applied for online bearing condition monitoring since most vibration sensors are positioned near bearing housings.
Adrian Villarroel & Grover Zurita, et al (2019) reported that, Creating an effective antialiasing filter to decrease industrial noise is a difficult task. Evaluations of frequency response and phase noise were carried out in order to verify the created system. Vibration measurements were also taken in the industry under a variety of operating situations and machine setups. A standard reference system and a low-cost vibration measurement system were used to collect data at the same time. Fast Fourier Transform and Welch's technique were used to process the data.
Urvashi Jindal & Vaibhav Gupta et al (2018) When odd vibrations are detected, this project entails creating an SMS warning. It contains a lab-based experiment that involves detecting vibrations when various force magnitudes are applied. The alarm signal would be issued based on the greatest magnitude at which destruction is high. Using GSM technology, this notice would be transmitted to many mobile phones. We can be conscious of the vibrations with the aid of this.
Adam Hjort & Mans Holmberg et al (2015), As a slave I/O, we used an Arduino microcontroller with two accelerometers for vibration measurements and a serial adapter to link the hardware to an EPICS IOC for analysis. In order to find a transfer function, the data from the two accelerometers were crosscorrelated. Theoretically, our findings matched our findings.
-
METHODOLOGY
The most readily controlled parameters in cutting operations are cutting speed, depth of cut, feed rate. Consideration of the vibration generated during machining operations. In the current study, an attempt is made to relate the surface roughness with the vibration level of the machine tool.
Scope of project
Literature survey
Problem statement and objective
Selection of parameters and materials
Design of Experiment
Performance of Experiment using FFT Analyzer
Comparison of results
Results and Discussion/p>
Table 1
-
FFT Analyser
The quick Fourier change (FFT) is an effective calculation used to register a discrete Fourier change (DFT). This Fourier change yields vibration abundancy as an element of recurrence so the analyzer can get what is causing the vibration.
-
Instrument and Materials
-
M+P Analyzer
m+p Analyzer is a completely coordinated answer for dynamic sign estimation, examination and progressed announcing of all commotion and vibration, acoustics and general unique sign applications. Exhaustive time and recurrence investigation is accessible with both on the web and disconnected information handling.
-
m+p VibPilot
m+p VibPilot is m+p world wides smaller 4/8channel equipment stage custom-made to meet the high necessities of the present vibration control and dynamic sign examination. It is a finished multi-reason arrangement utilizing our demonstrated m+p VibControl, m+p Analyzer and m+p Coda programming for vibration control and dynamic sign examination applications.
-
Accelerometer
An accelerometer is a gadget that actions the vibration, or speed increase of movement of a construction. The power brought about by vibration or an adjustment of movement (speed increase) makes the mass "crush" the piezoelectric material which creates an electrical charge that is relative to the power applied upon it.
Fig 1 Experimental setup
Fig 2 Working setup
-
-
WORKING
FFT Analyzer is fundamentally a testing instrument that measures vary parameters in a system at Radio frequency range. A piece of normal testing equipment would measure the quantity based on its amplitude with respect to time. It measures the vibration range of amplitude when tool piece hits the workpiece with different time lapse, rpm and depth of cut. The analyzed amplitude range gather input from VibPilot
and it gives the output amplitude waves and display it on the m+p software.
Fig 3 At different rpm
-
Frequency Calculation
Frequency Hz
Table 2
-
Analysis and Testing
For experimental analysis we change 3 depths of cut for 3 different speeds in lathe machine. Selected Speeds are of high- level speed of lathe machine which got by changing belt position.
Table 3
-
-
HARDWARE AND SOFTWARE
REQUIREMENTS:
HARDWARE REQUIREMENTS:
-
ESP32
-
Battery
-
LCD
-
Vibration Sensing Device
-
Hardware Description: ESP32:
32-bit MCU & 2.4 GHZ Wi-fi & Bluetooth 5 (LE)
-
Xtensa® 32-bit LX7 dual-core processor that operates at up to 240 MHz 512 KB of SRAM and 384 KB of ROM on the chip, and SPI, Dual SPI, Quad SPI, Octal SPI, QPI, and OPI interfaces that allow connection to flash and external RAM
-
Additional support for vector instructions in the MCU, which provides acceleration for neural network computing and signal processing workloads
-
Peripherals include 45 programmable GPIOs, SPI, I2S, I2C, PWM, RMT, ADC and UART, SD/MMC host and TWAITM
-
Reliable security features ensured by RSA-based secure boot, AES-XTSbased flash encryption, the innovative digital signature and the HMAC peripheral, World Controller
ESP32-DevKitC V4 with ESP32-WROOM-32 module soldered
-
-
Battery
This board is made for 12-volt battery sealed acid. When we use this board, the battery avoids malfunctioning and is fully automatic. This board has 4 connectors with 2 connector DC inputs and a negative and positive print and two connectors at the same output and also a negative-positive print. A twelve-volt battery has six single cells in series producing a fully charged output voltage of 12.6 volts. … A typical 12-volt battery used in a RV or marine craft has a rating 125 AH, which means it can supply 10 amps of current for 12.5 hours or 20-amps of current for a period of 6.25 hours. 12-volt batteries are commonly used as car batteries. One of the most common uses of a 12-volt battery is for transportation applications, such as in cars and boats. In these cases, the battery may be able to be recharged as current is only needed to start the vehicle.
-
LCD
A liquid-crystal display (LCD) is a flat panel display, electronic visual display, or video display that uses the light modulating properties of liquid crystals. Liquid crystals do not emit light directly. LCDs are available to display arbitrary images (as in a general-purpose computer display) or fixed images which can be displayed or hidden, such as preset words, digits, and 7-segment displays as in a digital clock. They use the same basic technology, except that arbitrary image are made up of a large number of small pixels, while other displays have larger elements.
Fig 4: LCD
LCDs are used in a wide range of applications including computer monitors, televisions, instrument panels, aircraft
cockpit displays, and signage. They are common in consumer devices such as DVD players, gaming devices, clocks, watches, calculators, and telephones, and have replaced cathode raytube (CRT) displays in most applications. They are available in a widerrange of screen sizes than CRT and plasma displays, and since they do not use phosphors, they do not suffer image burn-in. LCDs are, however, susceptible to image persistence. The LCD screen is more energy efficient and can be disposed of more safely than a CRT. Liquid crystals do not emit light directly. LCDs are available to display arbitrary images (as in a general-purpose computer display) or fixed images which can be displayed or hidden, such as preset words, digits, and 7-segment displays as in a digital clock. They use the same basic technology, except that arbitrary image are made up of a large number of small pixels, while other displays have larger elements. They are common in consumer devices such as DVD players, gaming devices, clocks, watches, calculators, and telephones, and have replaced cathode raytube (CRT) displays in most applications. They are available in a wider range of screen sizes than CRT and plasma displays, and since they do not use phosphors, they do not suffer image burn-in. LCDs are, however, susceptible to image persistence.
VII.VIBRATION SENSING DEVICE
A vibration sensor is a device that measures the amount and frequency of vibration in a given system, machine, or piece of equipment. Those measurements can be used to detect imbalances or other issues in the asset and predict future breakdowns. Vibration sensors are piezoelectric accelerometers that sense vibration. They are used for measuring fluctuating accelerations or speeds or for normal vibration measurement.
There are three main types of accelerometers: piezoelectric, piezoresistive, and capacitive MEMS. The working principle of these are all slightly different and therefore the best applications for each accelerometer type is different.
-
SOFTWARE REQUIREMENTS:
-
Arduino IDE
-
Proteus 8
-
Embedded C
SOFTWARE DESCRIPTION:
-
ARDUINO
Arduino is a computer hardware and software company, project, and user community that designs and manufactures microcontroller kits for building digital devices and interactive objects that can sense and control objects in the physical world. The project's products are distributed as open- source hardware and software, which are licensed under the GNU Lesser General Public License (LGPL) or the GNU General Public License (GPL), permitting the manufacture of Arduino boards and software distribution by anyone. Arduino
boards are available commercially in preassembled form, or as do-it yourself kits.
Arduino board designs use a variety of microprocessors and controllers. The boards are equipped with ses of digital and analog input/output (I/O) pins that may be interfaced to various expansion boards (shields) and other circuits. The boards feature serial communications interfaces, including Universal Serial Bus (USB) on some models, which are also used for loading programs from personal computers. The microcontrollers are typically programmed using a dialect of features from the programming languages C and C++. In addition to using traditional compiler toolchains, the Arduino project provides an integrated development environment (IDE) based on the Processing language project.
The Arduino project started in 2005 as a program for students at the Interaction Design Institute Ivrea in Ivrea, Italy,[2] aiming to provide a low-cost and easy way for novices and professionals to create devices that interact with their environment using sensors and actuators. Common examples of such devices intended for beginner hobbyists include simple robots, thermostats, and motion detectors.
The name Arduino comes from a bar in Ivrea, Italy, where some of the founders of the project used to meet. The bar was named after Arduin of Ivrea, who was the margrave of the March of Ivrea and King of Italy from 1002 to 1014.
-
PROTEUS 8
Proteus 7.0 is a Virtual System Modelling (VSM) that combines circuit simulation, animated components and microprocessor models to co-simulate the complete microcontroller-based designs. This is the perfect tool for engineers to test their microcontroller designs before constructing a physical prototype in real time. This program allows users to interact with the design using on-screen indicators and/or LED and LCD displays and, if attached to the PC, switches and buttons. One of the main components of Proteus 7.0 is the Circuit Simulation-product that uses a SNOCMUCE3f5 analogue simulator kernel combined with an event-driven digital simulator that allow users to utilize any SNOCMUCE model by any manufacturer. Proteus VSM comes with extensive debugging features, including breakpoints, single stepping and variable display for a neat design prior to hardware prototyping.
In summary, Proteus 7.0 is the program to use when you want to simulate the interaction between software running on a microcontroller and any analog or digital electronic device connected to it. The application framework lets you view modules of Proteus as tabs in a single window or, via drag and drop, as separate windows for a side-by-side view the common parts database enables sharing of information between schematic and PCB so that changes to data are instantly reflected across the software.
The live netlist means changes to connectivity in the schematic can be instantly reflected in the PCB, the Bill of Materials and the Design Explorer. The integrated
VSMStudio IDE binds your firmware project to your schematic design and Active Popups bring the schematic into your VSMStudio debug session.
-
EMBEDDED C
Embedded C is a set of language extensions for the C Programming language by the C Standards committee to address commonality issues that exist between C extensions for different embedded systems. Historically, embedded C programming requires nonstandard extensions to the C language in order to support exotic features such as fixed- point arithmetic, multiple distinct memory blank, and basic I/O operations. In 2008, the C Standards Committee extended the C language to address these issues by providing a common standard for all
implementations to adhere to. It includes a number of features not available in normal C, such as, fixed-point arithmetic, named address spaces, and basic I/O hardware addressing.
Embedded C uses most of the syntax and semantics of standard C, e.g., main () function, variable definition, datatype declaration, conditional statements (if, switch, case), loops (while, for), functions, arrays and strings, structures and union, bit operations, macros, etc.
-
-
-
CONCLUSION:
One of the main causes of structural damage to the building is vibration. By detecting early vibration through digital technology, many losses and accidents can be reduced.
This project focuses on demonstrating the reasons of vibration control and determining the impulse movement that provides accurate information about the equipment condition and how it impacts the structure. As a result, vibration monitoring is an important aspect of maintaining the machinery in this established period. The main goal of this project was to detect the unusual vibrations and generate the alert when the limit exceeds. This can be useful for emergency response planning. It is going to implement by using both hardware and software and thus its implementation is easy and economical.
-
Emergencies can come without warning at any time. Being prepared is the best way to handle these unexpected incidents and disasters. Emergencies are the source of risk and therefore have the probability of causing an undesired event.
-
After a disaster occurs, immediate action is taken to protect staff, visitors & collections and sending concern authority using alert.
-
Since it is done on a small scale as it is lab-based analysis, it could further be implemented on real data.
-
-
FUTURE WORK:
-
This project involves the study using experimental setup within Lab. This instrumentation has scope to utilize analysis on real-world using real-world situation. While carrying out an experiment it was felt the magnitude of the applied force is required to analyze the vibration created in the test bed. The amount of force applied to create vibrations can be measured for more accurate results. The project can also include the sending of alarms on internet messaging services like (E-Mail or Twitter) so that the alarm could spread fast. Duration of vibration can be put as a concern. What immediate actions should be taken upon notification of an emergency?
REFERENCES
[1] Jardine, A.K.S.; Lin, D.; Banjevic, D. A review on machinery diagnostics and prognostics implementing condition-based maintenance. Mech. Syst. Signal Process. 2006, 20, 14831510. [2] Cibulka, J.; Ebbesen, M.K.; Hovland, G.; Robbersmyr, K.G.; Hansen, M.R. A Review on Approaches for Condition Based Maintenance in Applications with Induction Machines located Offshore. Model. Identif. Control A Nor. Res. Bull. 2012, 33, 69 86. [3] Tirpude, V.D.; Modak, J.P.; Mehta, G.D. Vibration Based Condition Monitoring of Rolling Mill. Int. J. Sci. Eng. Res. 2011, 2, 10. [4] Prajapati, A.; Bechtel, J.; Ganesan, S. Condition based maintenance: A survey. J. Qual. Maint. Eng. 2012, 18, 384400. [5] Carden, E.P.; Fanning, P. Vibration Based Condition Monitoring: A Review. Struct. Health Monit. 2004, 3, 355377. [6] Bilski, P.; Winiecki, W. A low-cost real-time virtual spectrum analyzer. IEEE Trans. Instrum. Meas. 2007, 56, 21692174. [7] Swiszcz, G.; Cruden, A.; Booth, C.; Leithead, W. A data acquisition platform for the development of a wind turbine condition monitoring system. In Proceedings of the 2008 International Conference on Condition Monitoring and Diagnosis, Beijing, China, 21 24 April 2007; pp. 13581361. [8] Zhang, J.Z.; Chen, J.C. Tool condition monitoring in an end- milling operation based on the vibration signal collected through a microcontroller-based data acquisition system. Int. J. Adv. Manuf. Technol. 2008, 39, 118 128. [9] Katalin, A. Microcontroller based system for vibration analysis. In Proceedings of the 2008 IEEE International Conference on Automation, Quality and Testing, Robotics, Cluj-Napoca, Romania, 2225 May 2008; pp. 171174. [10] Florin, G.; Luminita, P.; Constantin, C. Acquisition System for Monitoring Vibrations. In Novel Algorithms and Techniques In Telecommunications, Automation and Industrial Electronics; Springer: Dordrecht, The Netherlands, 2008; pp. 8992..