
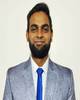
- Open Access
- Authors : Faizur Rahman A , Priyank Hanuman Mhatre
- Paper ID : IJERTV11IS060109
- Volume & Issue : Volume 11, Issue 06 (June 2022)
- Published (First Online): 17-06-2022
- ISSN (Online) : 2278-0181
- Publisher Name : IJERT
- License:
This work is licensed under a Creative Commons Attribution 4.0 International License
Mini Tractor Operated Vibrating Potato Harvester For Hill Terrain Farming
Faizur Rahman A
Associate Professor Department of Mechanical Engineering CSI College of Engineering, Ketti Valley
The Nilgiris, Tamilnadu, India
Priyank Hanuman Mhatre Senior Scientist and Head ICAR-CPRS, Muthorai Ooty, The Nilgiris Tamilnadu, India
Abstract Potatoes have an important role in human food consumption. Potato harvesting in hill terrain regions is very challenging for humans due to bad weather conditions, frequent animal disturbances, and scattered landscapes. In this paper, a potato harvester machine was designed and developed, especially for hill terrain regions. It can be easily coupled with available farm power. It can harvest 0.12 hectares per hour. This machine consists of four main components: a harvesting blade, transmission system, eccentric mechanism, and vibrating unit. Manual harvesting and machine harvesting were compared. The major factors considered in this paper were exposed potatoes, unexposed potatoes, damaged potatoes, time to complete the harvest, labour required in collecting plant debris, potatoes, and digging the soil. When compared to machine harvesting, nearly 11.24% of potatoes were damaged during manual harvesting. Furthermore, machine harvesting saved 42.33 percent of the cost.
Keywords Vibrating potato harvester, Hill terrain farming, Harvesting machinery, potato, Eccentric mechanism
-
INTRODUCTION
Potato (Solanum tuberosum.L) is regarded as one of the most important vegetable crops that meet India's nutritional needs. India is the second largest potato producing country next to China. Potatoes are cultivated on 21.8 million hectares of land, producing 52.5 million metric tons per year. There is a projection of 711.5 million metric tons by 2050. The weather and the climate are the greatest challenges for the harvesting of potatoes. More than 90% of the potatoes in India are harvested during the October and March months that fall under short days in the northern hemisphere. Due to short daytime and lack of sunlight, the productivity of the potatoes leads to a lower potential yield.
In the Nilgiris, the potatoes are harvested from February to March. Small and marginal farmers compromise on the yield and opt for an early harvest of potatoes, which results in a 30 40% loss in productivity. Also, while harvesting the potatoes with either hand tools or machines, the tubers may get damaged. It was observed that the greatest percentage of damaged tubers occurred due to the greatest impact of the working bodies of the harvester [1]. Potato harvesting technologies need more improvements in areas like digging, picking, and grading. The potato harvesting machine is based on four basic operating principles: reciprocating, conveying, rotating, and spinning [2]. This paper presents the method of conveying and separating the potato-soil mass. Major parameters like exposed tubers, unexposed tubers, damaged tubers, machine field capacity, fuel consumption, and cost of harvesting operations were discussed [3]. Also, there is a need
for more improvements in potato-soil separation. A neat potato-soil separating mechanism was developed and classified the whole mechanism into shearing area, bending area, throwing area, cleaning area, and conveying area. Only 0.89% of the damage rate of potatoes was observed in this mechanism [4]. Several researchers focused on developing potato harvesting machines [5]. A one-row potato digger with a rotary blade was designed and developed [6]. Various methods were discussed in developing onion harvesting machines [7]. The design and development of the harvesting blade, transmission system, eccentric mechanism, and vibrating unit were the major roles played in this paper. The harvesting blade angle was kept at 210 [8].
-
MATERIALS AND METHODS
The main objective of this research is considered as an outcome of fabricating an efficient potato digger, especially for hill terrain regions. Here, a newly developed potato digging blade attached to a vibrating unit was discussed. This potato harvesting covers 0.12 hectares per hour and it is made up of four main components: the harvesting blade, transmission system, eccentric mechanism, and vibrating unit. The harvesting blade lifts the potatosoil mass to the vibrating unit, where it separates the potatosoil mass under vibration. This vibration is caused by an eccentric mechanism connected to the machine. So, the potato-soil mass gets separated in the vibrating unit and the potatoes fall to the rear of the machine. All the parts in this harvester machine were easily replaceable and economical for the farmers. The overall dimensions of this machine are length 55 inches x width 24 inches x height 30 inches and it weighs 98 kg. This machine is connected with a tractor capacity from 18 hp to 30 hp through three-point hitch systems and a PTO unit. The major parts of the machine were marked, and it is shown in figures 1 and 2.
Fig. 1 Vibrating Potato Harvester under fabrication
Fig. 2 Parts of the Vibrating Potato harvesting machine
540 rpm. No speed reductions in the gear system due to both the gears being the same size are shown in figure 5. Also, the speed of the PTO shaft can be increased through the tractor throttle process depending on the soil and harvesting conditions.
A. Potato Harvesting Blade
In Figure 3, it was shown that the furrows and ridges were the size of potatoes planted in the field. So, the potato digging blades were developed accordingly.
C. Eccentric Mechanism
Fig. 5 Bevel gears
Fig. 3 Schematic diagram of the potato plant ridges and furrows distance in the field
Hardened mild steel plates and flats are used for fabricating the digging blades. Four hardened mild steel flats of 50 mm in width and 350 mm in length are welded with a 20 mm gap in between with an inclination of 210 (Digging blade angle). The digging blade was fabricated with reference to the manual potato hoe design and it is shown in figure 4. Also, the gaps between the flats are provided to reduce the weight and drop the soil while digging.
Finally, digging blades with dimensions of 400 mm wide, 8 mm thick, and 210 (blade angle) were fabricated. I- channels made up of mild steel with dimensions of 300 mm in width and 500 mm in length, and is attached to the digging blade through fasteners. I-channel was used to connect these harvesting blades to three-point hitch systems in tractors. This harvest can be easily attached to the vibrating unit through fasteners.
Fig. 4 Potato harvesting blade
B. Transmission System
This system contains two hardened mild steel shafts of size 1 inch in diameter, 22 teeth, and an EN8 Bevel gear of 2 numbers. The power from the tractor PTO was transmitted to the right-angled bevel gear system through a universal joint. Also, a hardened mild steel shaft of size 40 mm in diameter with 6 splines was attached in between the gear system and the universal joint. The tractor PTO operates at
An eccentric mechanism was attached to the output power of the bevel gear system. It consists of a bearing cup, a bearing, and an eccentric joint. The figure clearly illustrates the eccentric mechanism of the harvesting machine. The bearing cup holds the eccentric joint and bearing together and is also connected with the rotating shaft. The power is transferred from the tractor PTO to the eccentric mechanism via the universal joint, transmission system, and rotating shaft. tray gets vibrated through an eccentric mechanism.
D. Vibrating Unit
Mild steel flat of size 50 mm widh, 10 mm thickness and 12 inch length attached on the body of eccentric mechanism. The other end attached with vibrating tray. Similarly four mild steel flats of same size from the main body of the harvesting machine are connected with vibrating tray through mild steel bushes of 30 mm diameter. This vibrating tray made up of 10mm diameter and 25 inch length polished mild steel rods, to avoid damages to potatoes while vibrating and it is shown in figure 6. At the end of the vibrating unit, a tray made up of mild steel 3 mm sheet with dimensions 16 inch width and 20 inch length are attached.
Fig. 6 Vibrating unit
-
RESULTS AND DISCUSSIONS
Details of the testing parameters and specifications are clearly indicated in Table 1. Figure 7 depicts the completion of all trail runs and field testing at ICAR-CPRS, Muthorai, Ooty, The Nilgiris district, Tamilnadu, India.
Fig. 7 Potato harvesting machine under field testing at ICAR-
CPRS, Ooty
-
rial run observations
Approximately 15 trial runs were conducted in a field with hard soil at an approximate length of 500 feet. Testing parameters and specifications are tabulated in Table I. It was noted that few failures occurred in the machine and it is shown in figure 8. Heavy soil load got stuck in the digging blade conveying area due to higher blade taper angle. Initially it was kept at 250, but bevel gear tooth failure occurred due to heavy load conditions. Initially, the bevel gears used are 20-tooth mild steel gears. Also, the bearing cup cap dislocated due to weaker fastening joints, and the bearings inside it are exposed to dirty areas. Given the aforementioned issues, the blade angle was kept at 200 degrees, EN8 22-tooth bevel gears were used, and the bearing cup cap was tightened with extra fasteners.
-
(b) (c)
-
Fig. 8 Various remarks noted after testing of Version 3 vibrating Potato Harvester in the field (a) Heavy soil load got stuck in the digging
blade due to lesser blade conveying area (b) bevel gears failed due to heavy load conditions (c) Eccentric cup dislocated due to weaker screwed joints
Table I. Testing parameters and specifications
potatoes can be stored and used for seeding purposes. Also, four laborers are required to collect the potatoes on the entire land and the time consumed is around four hours.
For the manual method, eight laborers are required per day to complete the entire field. Six days to complete the harvest. During harvesting, laborers use hand hoes to dig the soil, and some of the potatoes will be damaged due to tool material.
From Table III, it was noted that 42.33% of the cost was saved while using the potato harvester machine. Also, 11.24% of potatoes were damaged during manual harvesting compared with the potato harvester machine.
Observations
PLOT-1
PLOT-2
Potato Harvester Machine
Manual Method
Results
Cost in Rs.
Results
Cost in Rs.
Area Covered in hectare
1
1
–
Total potatoes harvested
16.56
tonne
16500 kg
–
16.23
tonne
16230
kg
–
Exposed potatoes
86.37%
14251.05
kg
–
100%
16230
kg
–
Unexposed potatoes
7.15%
1179.75
kg
–
Nil
–
Damaged potatoes
6.48%
1069.20
kg
–
7.30%
1184.79
kg
–
Time to complete
8 hours 30 min
–
8 hours/ day for 6 days
–
Fuel Consumption litres/hour
3
2366
Nil
–
Labours required to clean the plant debris
2 nos
1 hour
1400
Nil
–
Labours required for harvesting using hand hoe
2 nos
3 hour
4200
8 nos
48
hours
33600
Labours required for collecting potatoes from the field
4 nos
4 hour
11200
Nil
–
Miscellaneous
500
500
Total cost in Rs.
19666
34100
Table II. Comparative results of machine harvesting and manual harvesting the potatoes
Test Place
ICAR-CPRS, Muthorai, Ooty
Tractor
Mitsubishi Shakti MT 180D series mini tractor
Hitching
Three point linkage
Soil
Sandy Loam
Moisture content (%)
7.6
Materials
Mild Steel & Hardened Steel
Trial runs
15
Factors
Dimensions of digger and thickness of digging blade
Observations
Exposed potatoes, Unexposed potatoes, Damaged potatoes, Time to harvest, Fuel consumption, Labours required to clean the plant debris – manual hoe and collecting potatoes
Angle
210
Field Area
500 feet
Potato variety
Kufri Jyoti & Kufri Swarna
B.Field Test
Field tests of the developed harvester machine were compared with manual harvesting using labour with hand hoes. Two different field plots of the same size (1 hectare) were taken and compared. Two weeks before, a weed spray will be used to kill potato plants to completely remove the potatoes from the soil in dry conditions. At the time of harvesting, potato plants will be completely dried and can be easily picked up by hand. So, two laborers are required to clean the plant debris for a 1 hectare field in one hour. Finally, the harvesting of potatoes was completed by a manually operated and developed harvester machine and the results are shown in Table II. However, few potatoes are left under the soil and two laborers are required to dig the soil in two hours to complete 1 hectare of land. It was also noted that few potatoes were cut and damaged during harvesting due to the material used and the speed of the conveyor. These cut
Table III. Consolidated results
Description
Manual Method
Potato Harvester Machine
Cost difference in Rs.
Cost save in Rs.
34100
19666
14434
Percentage of cost saving
42.33%
-
-
CONCLUSIONS
A potato harvester machine designed and developed especially for hill terrain farming. Harvesting blade, transmission system, eccentric mechanism and vibrating unit are the major components used to fabricate the potato harvester machine. In this machine, a specially designed eccentric mechanism is used to vibrate the potato-soil mass tray while digging. In the trial tests, it was noted tha few failures like soil load stucked in the digging blade conveying area, gear system failure and weaker fastening joints. Also some potatoes were unexposed during harvesting and minor
adjustments are made in the machine. Harvesting the potatoes was compared with manual and potato harvester machine with same plot size of 1 hectare. It was noted that cost of manual harvesting and Potato harvester machine is Rs.34100/- and Rs.19666/- respectively. Nearly 42.33% of cost was saved while using potato harvester machine and 11.24% of potatoes were damaged in manual harvesting compared to potato harvesting machine.
ACKNOWLEDGMENT
With great pleasure, we would like to extend our sincere gratitude and thanks to Science and Engineering Research Board (SERB) for sponsoring this funded project under Teachers Associateship for Research Excellence (TARE) to develop a potato harvester machine for hill terrain farming.
I again thank Indian Council of Agricultural Research (ICAR) Central Potato Research Institute (CPRI), Shimla, Himachal Pradesh and Central Potato Research Station (CPRS), Ooty, The Nilgiris in supporting to develop the potato harvester machine and conduct the field experiments.
REFERENCES
[1] Alexei Siberev, Alexandr Aksenov, Alexei Dorokhov and Andrei Ponomarev (2019), Comparative study of the force action of harvester work tools on potato tubers. Research in Agricultural Engineering, vol. 65, pp. 8590. doi : https://doi.org/10.17221/96/2018-RAE. [2] Dessye Belay (2021), Design, Construction and Performance Evaluation of Potato Harvesters: A Review. International Research Journal of Engineering and Technology (IRJET), vol. 8, pp. 2747 2771. [3] Gamal El-Din Mohamed Nasr , Mohamed Nagiub Rostom , Mohamed Morsy Mohamed Hussein , Ahmed El-Fateh Farrag and Maher Fathy Attia Morsy (2019), Development of suitable potato crop harvester for small holdings. Agricultural Engineering International: CIGR Journal, vol. 21, pp. 34-39.
[4] Bei Wu, Tianci Huang, Xuanxuan Qiu, Tianlin Zuo, Xiushan Wang and Fangping Xie (2021), Design and Experimental Study of Potato- Soil Separation Device for Sticky Soils Condition. Applied Sciences, vol. 11, pp. 1-21. doi : https://doi.org/10.3390/app112210959. [5] Rangarajan R V, Arun Kumar G, Chandru R, Dhinakaran P and Gokul Nath M, Design and Fabrication of Automatic Potato Harvester, International Journal of Engineering Research & Technology (IJERT), vol.9., no.10, pp. 84-86, 2021 [6] V.M.Mhetre, A.A.Surve, P.R.Shirke, V.S.Patil, S.A.Mali , K.M.Swami and V.S.Gondkar, Design and Development Potato Harvesting Machine, International Journal of Innovative Studies in Sciences and Engineering Technology, vol. 7, no.7, pp.20-26, 2021 [7] Prof. Dr. A. J. Gujar, Pavan P. Sankpal, Salman S. Desai, Sumedh Ghorapade and Shubham S. Nakate, Literature Review on Digging and Conveying System for Self-Propelled Onion Harvester, International Journal of Engineering Research & Technology (IJERT), vol.8, no.11, pp.907-909, 2019 [8] K. C. Budhale, A. G. Patil, V. S. Shirole, S. S. Patil, R. S. Desai and S.B. Salavi (2019), Design and Development of Digging & Conveyor System for Self – Propelled Onion Harvester. International Research Journal of Engineering and Technology (IRJET), vol. 6, pp. 3304- 3307.