
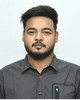
- Open Access
- [post-views]
- Authors : Swapnil Srivastava , Dr. Surendra Roy , Faraz Khan
- Paper ID : IJERTV11IS060053
- Volume & Issue : Volume 11, Issue 06 (June 2022)
- Published (First Online): 18-06-2022
- ISSN (Online) : 2278-0181
- Publisher Name : IJERT
- License:
This work is licensed under a Creative Commons Attribution 4.0 International License
Study of using Metakaolin and Vetiver Fiber As Partial Replacement of Cement in Concrete
Swapnil Srivastava1, Prof. (Dr.) Surendra Roy2, Faraz Khan3
1. M. Tech Scholar, Structural Engineering, Babu Banarasi Das University Lucknow,
2. Professor and HOD, Dept. of Civil Engineering Babu Banarasi Das University Lucknow,
3. Assistant Professor, Dept. of Civil Engineering, Babu Banarasi Das University Lucknow
Abstract:- Concrete is a very sturdy and multipurpose mouldable construction material. It is composed of cement, sand and aggregate (e.g., gravel or crushed rock) mixed with water. The cement and water together form a mixture which covers the sand and aggregate. The cement sector is that the third largest industrial source of pollution emitting over 500,000 tons per annum of CO2 , sulphur dioxide , oxide and carbon monoxide gas Researchers all over the world have started giving their best effort on the extension of partial supplementation of ordinary Port-land cement with minerals or raw materials by naturally occurring, manufactured, or manmade waste. Various types of pozzolanic materials fly ash, silica fume, metakaolin, blast furnace slag etc. are at hand which has cementeous properties. Mixing these materials with ordinary Portland cement can enhance the cementing and mechanical properties of cement. These days use of metakaolin is developing high popularity in partial replacement of cement due to its fineness in improving various strengths and parameters of mortars and concrete. Well in several research it has been seen that further addition of fibers (natural or man-made) increase concretes structural integrity. Fibers are small pieces providing reinforcement and certain other properties. They can be circular or flat. The fiber is frequently described by a suited parameter called aspect ratio. The aspect ratio of the fiber is the ratio of the length of the fiber to the diameter.so in the following research replacement of cement with vetiver fiber and metakaolin is carried out.
INTRODUCTION
Concrete is the extensively used material in construction and it is the primary component used for infrastructure. Due to the advanced development in construction, the use of replacement has become intense and need for strengthening agent has become an issue which should be addressed immediately in order to cope up with advancement in structural designs. The use of vetiver as strengthening agent in construction industry will be environmental friendly and economical more or less metakaolin also increases strength of concrete. Generally, dehydroxylated form of the clay mineral kaolinite is known as metakaolin. Rocks that have high amount of kaolinite in them are referred to as china stone or kaolin, traditionally utilized in the manufacture of porcelain. The metakaolin particle size is smaller than cement particles, but not as fine as silica. Fume. The quality and reactivity of metakaolin strongly depend on the aspect of the raw material used Metakaolin can be manufactured from many different types of primary and secondary sources containing kaolinite. Metakaolin is refined calcined kaolin clay under carefully controlled conditions to form an amorphous aluminosilicate which is reactive in concrete.
Some natural pozzolans material like fly ash and silica fumes, metakaolin react with the calcium hydroxide that is also known as lime is a by- product produced during cement hydration. Between 100-200°C, clay minerals lose most of the water present in them. Between 500-800°C kaolinite becomes calcined by losing water through de- hydroxylation. The de-hydroxylation of kaolin to metakaolin is an endo-thermic process because of the massive amount of energy required to get rid of the chemically bonded hydroxyl ions. Further increase in temperature range, kaolin becomes metakaolin, with a two-dimensional order in crystal structure. To achieve fines of 700-900 m2/kg this material is grounded. In order to form a pozzolan (supplementary cementing material) nearly complete dihydroxylation must be reached without overheating, i.e., thoroughly roasted but not burnt. This process of roasting produces an amorphous, highly pozzolanic state, where as overheating can cause sintering, to form the dead burnt, nonreactive refractory, called mullite.
LITERATURE REVIEW
J. hivva, April 2016 According to this investigation metakaolin and granite powder were use as partial replacement of cement with different percentage The bestcompressive strength of concrete increased with 15%MK and 20% GPreplacement in concrete. The compressive strength is increased around8.5% compared to conventional concrete in 15%MK and 20% GPreplacement. The split tensile strength of concrete increased by 11.6% thanconventional concrete. Further addition of Metakaolin and Granite powderdecrease thetensile strength of concrete.
A.k aur andV.P.S.Sran 2016 According to this research 3%,6%,9%, 12% of metakaolin was use as a partialreplacement of cement in concrete (M30), The replacement of cement with MKup to 9%, give better results from strength prospective. There is regular increasein compressive strength of concrete with increase in partial replacement of MKwith cement till 9%. Similarly, increase in split tensile strength of concrete wasobserved till 9% addition of MK at different interval of ages i.e. 7, 14 and 28Days respectively.
Dr. B. Krishna Rao,December-2016 The experiments were carried out at 10% replacement Of cement by metakaolinand 0, 10, 20, 30 and 40% replacements of fine aggregate by waste foundry sand. From the sieve analysis, it was found that waste foundry sand has finer material than fine aggregate. It was observed that as the percentage of
foundry sand increases, the workability decreases because of the presence of finer particles. the maximum replacement of foundry sand can be up to 30% in fine aggregate by keeping metakaolin at constant rate of 10%. Morsv M. S., 2008, He investigated the properties of Portland cement mortar by using nano kaon. The vartial substitutions of ordinarv portland cement with nano metakaoiln were carried out at 0%, 2%, 4%, 6%, 8% by weight of cement It was clearly depicted by the results that there were increase in compressive as well as tensile strenoths of concrete prevared with nano- metakaolin as compared with those of normal concrete.About 49% increase in tensile strength was observed.
Adel Al Menhosh (2016), He studied the effect of metakaolin additive and polvmer admixture on the concrete strength properties. Different proportions of the combination using two different polymers, metakaolin, and recycled fiber reinforcement have been used in this study. They found that, the addition of 5% optimized polymer and 15% cement replacement using metakaolin generates an optimized concrete mixture or strengt
Zhiguang Shi (2015) He conducted the experiment on effect of metakaolin and sea water on performance and microstructure of concrete. Thev have used 0-6 wt% MK used in the study. The compressive strength at 28 days increased by 33% when addition of 5 wt% MK and by 22% when mixed with seawater. The combination of both increased compressive strength by 52%. The pore structure was retined under both conditions.
O. Pavithra,D. Gayathri,NareshKumar December -2017 In this 10% of metakaolin is fixed and ditterent percentage of quartz sand is used 25,50,75 as partial replacement of cement A combination of 10% metakaolin and 50% quartz sand in concrete is found to be optimum (41.97 N/mm2 ) for compressive strength at 28 days. A combination of 10% metakaolin and 50% quartz sand in concrete is found to be optimum for split tensile strenth at 28 days improved the tensile strength by 14.6% in contrast with the conventional mix . The mix having 10% metakaolin and 50% quartz sand which had highest compressive strength had shown lowest permeability which is a good indication for better concrete.
K.Madhu T.Divya Bhavana and Syed Eashan Adil December 2016
In this metakaolin and rice husk with ditterent percentage were use as replacement of cement it 1s observed that rice husk ash based concretes have achieved an increase in strength for 10% replacement of cement and 5% replacement of cement by metakaolin and combine 10% RHA and 5% metakaolin at the age of 28 das when compared to conventional concrete in compressive test. it is observed that rice husk ash based concretes have achieved an increase in strength for 10% replacement of cement and 5% replacement of cement by metakaolin and combine 10% RHA and 5% metakaolin at the age of 28 days when compared to conventional concrete in solit tensile test. combine effect of RHA and metakaolin are given result
Objective of my research
To study the performance of concrete containing different percentages of metakaolin and vetiver fibre to identify the optimum replacement percentage.
To study the comparative effect of metakaolin and vetiver fibre on compressive strength and tensile strength of concrete.
Experimental work
The experimental Studies consist of testing of 24 specimen for each test (50 samples were total made) 3 sample with specimen of cement replaced mk with 4% 8% 12%, 3 specimen of vetiver fibre reinforced concrete along with mk different percentage , The load failure of each cubes is discussed. The aimed of the experimental programmed to achieve many objectives through comparison between the strength with normal concrete. Testing of specimen discovered the compression strength and the split tensile strength on effect of different percentages of metakaolin and the vetiver fiber.
Compressive strength of concrete with partial replacement of cement with metakaolin.
Concrete construction applications are particularly resistant to the most the compressive stresses. If the plain concrete is under pressure, cube diagonal falls on the vertical plane. Due to the lateral tension strain cracks occurs. Specimen size of (150*150*150) mm3 cube are testing on compression strength of concrete after 7days and 28 days of curing. The sample was prepared by control Mix and with different percentages of metakaolin
Table 1 – Result of compressive strength test of replacement of cement with metakaolin.
Mix |
7th days Flexural Strength |
28th day Flexural strength |
Conventional concrete |
2.33 N/mm2 |
3.50 N/mm2 |
MK1 |
2.35 N/mm2 |
3.73 N/mm2 |
MK2 |
2.54 N/mm2 |
4.06 N/mm2 |
MK3 |
2.65 N/mm2 |
4.21 N/mm2 |
The compressive strength examined for different percentages of metakaolin is replacement of cement
with weight for 4%, 8%, 12% metakaolin. As compared to the normal concrete mix strength is increased by 12.29% at 5% replacement of metakaolin after 7 days and for 28 days there was increase in strength by 9%. For 8% replacement strength is a increased by 30.44% for 7 days and for 28 days is increased by 17.40% as compared to the normal mix after 28 days testing.and for 12% replacement metakaolin compressive strength was increased by 37.88% for 7 days and for 28 days it is increased by 25%. So the optimum level of partial replacement of cement with metakaolin is 4-12% which gives the increase in strength after 28 days .
Flexural strength of concrete with partial replacement of cement with metakaolin.
The concrete beam of 150*150*700 was used for testing the flexural strength after 7 days and 28 days. The concrete specimen has been made for different percentages having metakaolin content of 4%, 8%, 12%, replacement. 1 sample has been casted for each percentage the results of flexural strength are reported in the table below, which shows the gain flexural strength for different percentages of metakaolin.
Table 2- Result of Flexural strength test of replacement of cement with metakaolin
mix |
7th days Compressive Strength |
28th day compressive strength |
Conventional concrete |
17.08 N/mm2 |
24.3 N/mm2 |
MK1 |
20.18 N/mm2 |
27.6 N/mm2 |
MK2 |
23.28 N/mm2 |
29.53 N/mm2 |
MK3 |
24.55 N/mm2 |
31.42 N/mm2 |
The compressive strength examined for different percentages of metakaolin is replacement of cement with weight for 4%, 8%, 12% metakaolin. As compared to the normal concrete mix strength is increased by 12.29% at 5% replacement of metakaolin after 7 days and for 28 days there was increase in strength by 9%. For 8% replacement strength is a increased by 30.44% for 7 days and for 28 days is increased by 17.40% as compared to the normal mix after 28 days testing.and for 12% replacement metakaolin compressive strength was increased by 37.88% for 7 days and for 28 days it is increased by 25%. So the optimum level of partial replacement of cement with metakaolin is 4-12% which gives the increase in strength after 28 days .
CONCLUSION
It is seen that when metakaolin used alone without vetiver fiber strength is increased. Metakaolin and vetiver fiber together give best result at low percentage 4% mk and 0.3% vf.
As the metakaolin in concrete increases workability decreases to some extend. As there is a reduction in fineness modulus of cementatious material, quantity of cement paste available for providing lubricating effect is less per unit surface area of aggregate thus addition of vetiver fiber balance the effect and slightly increases the workability of concrete with even increasing the w/c ratio.
FUTURE SCOPE
Since it is widely available in India it can be obtained easily and many other test which are pending are need to be done specially split tensile test.
REFERENCE
[1] J. Thivya 1, M. Arivukkarasi2, Comparative analysis on Partial Replacement of Cement by Metakaolin and Fine Aggregate by Granite Powder International Journal of Advanced Engineering Research and Technology (IJAERT)Volume 4 Issue 4, April 2016, ISSN No.: 2348 8190
[2] A.Kaur and V.P.S.Sran,Use of Metakaolin as Pozzolanic Material and Partial Replacement with Cement in Concrete (M30), Asian Review of Mechanical Engineering ISSN: 2249– 6289 Vol. 5 No. 1, 2016, pp. 9-13 © The Research Publication, www.trp.org.in
[3] Dr. B. Krishna Rao, M. Anil Kumar, A Study on Partial Replacement of Cement with Metakaolin and Fine Aggregate with Waste Foundry Sand, International Journal of Engineering Research & Technology (IJERT) ISSN: 2278-0181 IJERTV5IS120328 Vol. 5 Issue 12, December-2016 [4] K.Madhu,T.DivyaBhavana, Sayed Eshan Adil, Study on partial replacement of cement with rha and metakaoline ISSN: 2320-5407 Int. J. Adv. Res. 4(12), 300-305 [5] O. Pavithra, D. Gayathri, T. Naresh Kumar,Experimental Analysis on Concrete with Partial Replacement of Cement with Metakaolin and Fine Aggregate with Quartz Sand, International Journal of Advance Engineering and Research Development ,Volume 4, Issue 12, December -2017 e-ISSN (O): 2348-4470p-ISSN (P): 2348-6406 [6] Santhoshkumar S, Kuralamuthan.S, Experimental Investigation on Vetiver as Fibre in Conventional Concrete, International Journal of Engineering Research & Technology (IJERT)http://www.ijert.org ISSN: 2278-0181IJERTV6IS040362 (This work is licensed under a Creative Commons Attribution 4.0 International License.)Published by : www.ijert.org Vol. 6 Issue 04, pril-2017
[7] M. S. Morsy, S. H. Alsayed, M. Aqel, Effect of Nano-Caly on Mechanical properties and Microstructure of Ordinary Portland Cement Mortar, International Journal of Civil & Environmental Engineering, 2008, Vol: 10, No-01, pp: 23-27. Chandrakant u. mehetre , pradnya p. urade , shriram h. mahure& k. ravi4, comparative study of properties of self compacting concrete with metakaolin and cement kiln dust as mineral admixtures, impact: International Journal of Research in Engineering & Technology (IMPACT: IJRET), Vol. 2, Issue 4, Apr 2014, 37-52