
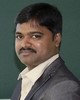
- Open Access
- Authors : Gurushanth B Vaggar , Mohammed Sameer , Muzammil Chitragar , Mubeen Riyaz Sharif, Abdul Kareem
- Paper ID : IJERTV11IS060221
- Volume & Issue : Volume 11, Issue 06 (June 2022)
- Published (First Online): 23-06-2022
- ISSN (Online) : 2278-0181
- Publisher Name : IJERT
- License:
This work is licensed under a Creative Commons Attribution 4.0 International License
Plastic Extrusion Machine: A Review
Gurushanth B Vaggar1*
1*Associate Professor Department of Mechanical Engineering
Alvas Institute of Engineering and Technology Moodbidri, Karnataka State, India.
Mohammed Sameer2, Muzammil Chitragar3, Mubeen Riyaz Sharif4, Abdul Kareem5
2, 3, 4, 5Undergraduate Students
Alvas Institute of Engineering and Technology Moodbidri, Karnataka State, India.
Abstract In this paper we discussed the topic of study and development of plastic extrusion machines, the structure of an extrusion machine is rather similar to that of a commercial one however it emphasizes production fundamentals as well as cost- effectiveness. The purpose of this work is to create low-cost plastic extrusion devices that end-users can employ at home to prevent plastic pollution. Many producers and researchers have found plastic extrusion to be a tough procedure to use in order to make items with a variety of criteria at a reasonable cost. This review work will result in the development of a plastic extrusion machine at a low cost that can be used at home by end-users to combat plastic pollution. In addition to this, the machine is made from different modular units that can be easily assembled or disassembled including gearbox, motor units that can be utilized. The goal of this article is to give a thorough overview of the extrusion process, with a focus on the numerous defects and their impact on product quality. The machine is meant to be simple to maintain and employs locally available raw materials that are straightforward to fix. In this machine, shredding and melting of, material feed into the hopper is accomplished by conveying and heating, and it is operated by only one or two people.
Keywords Extrusion, plastic, melting, extrusion, reduce, reuse, temperature, gearbox.
-
INTRODUCTION
Plastics processing requires a basic knowledge of the raw materials, additives, process controls, and ultimately product properties required to complete the final product. Plastic material has a useful combination of properties that can be modified for use in a variety of applications. The processing method of thermoplastic resin can be divided into batch process and continuous process [1]. Batch processes include injection molding and rotational molding. Plastic extrusion is a continuous process. However, blow molding can be used in both batch and continuous processes. Currently, online continuous thermoforming machines are available with the extrusion process. Manufacturing is the process of giving a raw material the required shape so that it can meet the geometric requirements of the raw material. The part associated with the task [3]. Various manufacturing processes are carried out based on desired shape and type of raw material. The manufacturing process is molding, machining, joining, Moulding and shearing, and additive processing. In India, the expulsion method is the most often used, accounting for 60 percent of all-out use by downstream plastic handling companies. The other well-known interaction is infusion shaping, which accounts for about a quarter of all interactions. Blow forming is used for 5% of the plastic, Roto moulding is used for 1%, and the rest of the plastic is
processed via various cycles. [2] From the above information, we can see that ~60 % expulsion process utilized in the business yet it has been seen that there are bunches of issues in the expulsion process which led to blemished items. In expulsion items, deserts due to handling incorporate, helpless comprehension of the handling strategy, utilization of old machines, be shy of prepared staff, the machine separates. Because of this, it becomes fundamental that businesses have a better expulsion process [1]. The expulsion machine is an exceptionally strong machine of the Precious Plastic armory as it can make interesting items and can run constantly. Assuming that we have sufficient plastic and an all-around smoothed-out process, we could be reusing every minute of every day. With the expulsion machine, we can make fiber, crush or get inventive working with molds. This machine is likewise extraordinary for instructive purposes as the cycle is exceptionally direct and straight forward [6]. This method pleasantly mixes in an unexpected way shaded plastics together and yields a homogeneous and smooth tone, for instance, if we blend highly contrasting plastic, we will get a quite smooth dark result. We can involve this element for our potential benefit in our plans [5].
In this review, an expulsion pultrusion machine was created to deliver a carbon fiber-filled thermoplastic composite fiber [9]. The machine was planned and manufactured to oblige a combined capacity of expulsion and pultrusion. The fiber was exposed to coupling specialist treatment at raised temperature to expand their surface harshness before taking care of them into extruder kick the bucket. The impregnation bites the dust had a softened pool, also the fiber went through spreader pins connected to this dissolve pool. The fiber was focused on having consistency in shape and aspects, high volume division, and high impregnation quality. Besides, the fibers can be sliced into pellets and used to manufacture complex items through trim interaction. Notwithstanding, this study is meant to demonstrate the plan idea and guarantee the machine's exhibition in delivering fibers as the base material for composite pellets. In this stage, a plausibility study was conveyed tentatively. Further examination is expected to research the impact of various interaction boundaries on the nature of the composite fiber.
-
PLASTIC EXTRUSION PROCESS
Plastic ejection is a high-volume manufacturing process that softens and frames rough plastic into a homogeneous contour. The first step in this cycle is to transfer plastic material (pellets, granules, chips, or powders) from a container into the extruder's barrel [3]. The mechanical energy provided by turning screws, as well as radiators arranged along the barrel, continuously dissolves the
substance [1]. The liquid polymer is then forced through a pass-on, which moulds the polymer into a solid shape as it cools. There are two essential sorts of plastic expulsion. Screw expulsion and smash expulsion [8]. A slam extruder is an extruder where, rather than an expulsion screw, a slam or unclogged is utilized and an unclogged goes through a barrel and pushes out the material under tension. The slam extruder was the earliest extruder to be utilized in the plastics industry. This normal interaction is applied for creating profiles, sleeves, pole, block, tubing, lining sheet bars, and so on the smash expulsion process is exceptionally viable for explicit materials like PTFE which are not expelled effectively utilizing screw extruder on account of its low erosion. In this interaction plastic material in powder structure is gravity taken care of into a chamber. In the extruding chamber, the sap powder is warmed at sintering temperature. Ultra-high atomic weight polyethylene becomes coagulated as it dissolves so it very well may be expelled with this kind of cycle. A pressure-driven smash pushes the sap materials like PTFE, UHMW, and so forth from the chamber to kick the bucket. The pass on in reality gives the state of the ideal plastic like a bar, tube, or on the other hand a profile shape with the essential inside or external distance across. At the point when the material emerges from the kick the bucket, it moves the length of the transport. The profiles can be made perpetually and cut by the nonstop expelling of every length. A helical feed screw that rotats inside a barrel is used for screw ejection. Plastics ejection is a high-volume manufacturing technique that involves liquefying basic plastic and shaping it into a consistent contour [2]. Line/tubing, weather-stripping, fencing, deck railings, window outlines, plastic movies and sheeting, thermoplastic coatings, and wire protection are all made by expulsion. This interaction begins with the extruder's barrel receiving plastic material (pellets, granules, bits, or powders) from a container. The mechanical energy created by twisting screws and radiators arranged along the barrel gradually liquefies the substance. The liquid polymer is then forced through a pass- on, which moulds the polymer into a solid shape as it cools. [1]. Plastics are one of the most regularly utilized materials in this present reality [5]. The gigantic amounts of plastic items presently being advertised will at last track down their approach to the squander dumpsites. This is making a very significant issue at dump locales for a long time. Additionally, the presence of plastic squanders in the climate is viewed as a perilous undertaking for they are at risk to burst into flames effectively, consume for extensive stretches and subsequently contaminate the climate. They additionally misuse arable soil for ranch work. Thusly, an activity ought to be taken to advance the reusing of plastic materials [5]. Plastic reusing will undoubtedly understand a great deal of saving underway expenses, monitor restricted assets, and reduce natural contamination. Volumes of waste hardware requiring handling are expanding quickly in both the industrialized and industrializing universes. Non-industrial nations, similar to Nigeria, need to import virgin plastic for an extreme price. Reusing exercises are typically low in these nations [6]. The casual area is prepared all of the time to embrace any financially feasible endeavor. Apparatus accessible to them for plastic reusing is for the most of the extremely significant expense and mass. This to an extraordinary degree forces genuine limitations to the reusing of plastics in emerging nations [10]. Hence, to defeat these
inadequacies, it was important to create a machine that had some expertise in its application altogether to accomplish the set goals of diminished expense furthermore, size ideally utilizes locally accessible materials [2].
Deciding on ideal interaction boundary settings impacts usefulness, quality, and cost of creation in plastic-related ventures. To determine the best interaction boundary setting for plastic expulsion, creation engineers have already used either an experimentation strategy or Taguchi's boundary plan technique. In any case, these strategies are unsatisfactory in the current situation due to the expanding intricacy of the item plan and the prerequisite of multi-reaction quality attributes [9]. Upgrading process boundary issues are regularly acted in the assembling industry, especially in setting the last ideal cycle boundaries. The last ideal process boundary setting is perceived as one of the main advances in plastic expulsion for working on the nature of expelled items [4]. In the face of global competition in the plastic-items sector, relying on experiments to determine the interaction boundaries for plastic expulsion is no longer sufficient. Many scientists have experimented with various approaches for ensuring process boundaries for plastic expulsion in order to reduce the chance of advertising and obtain the predictable character of expelled pieces [3].
-
WORKING PROCESS OF PLASTIC EXTRUSION MACHINE
The point was to assemble a machine that could serve as a piece of a reusing line that could be utilized for the show in the research facility. The reusing line comprises a plastic shredder, an extruder, a pulverize-making machine, and an infusion forming machine [8]. The plan of the extruder is the same as extruders utilized in the business.
Figure.1. 3D Model of plastic extrusion machine.
The functioning guideline of the planned extruder is as follows:
the extruder is taken care of through the hopper with the destroyed plastic or the crush, after which the screw, for our situation a boring tool, export the plastic material into the barrel the turning movement, because of the warmth in the framework the thermoplastic material melts and is constrained out on a pass-on, creating a fiber with diameter
cross-area [6]. The pass on additionally contains a valve that can be utilized to build the tension in the barrel, along these lines expanding the homogenization of the dissolve, the turning movement of the screw, the drill, is guaranteed by an ac engine, that is associated with the wood drill with a unique connector through the minimizer [3]. The ousting gathering generally includes screw, barrel, heat control unit, and the fail horrendously during the removal interaction [1]. The working of the removal machine is a direct result of the gravitational power the plastic is dealt with into the extruder in the design drops into the rotational screw of the extruder. Then, the screw starts to turn with the goal that the scouring is made to deliver heat and the plastic materials start to mellow. In solicitation to condense extra materials additional warming barrels are joined in the extruder. The electric hotness control goes probably as safeguarding influence which doesn't allow hotness to go out where the fluid plastic is imbued to fail horrendously. It additionally goes about as nuclear power to the cycle [3]. Then, at that point, the liquefied plastics is gone through the little opening to eliminate the pollution and afterward go through the pass on to the result. The expulsion process is primarily for enormous scope enterprises. In this producing process, it is vital to keep the right working control sources of info and temperature estimations for required polymer and tar. On the off chance that we adhered to the directions, simply we can get eventual outcomes. During this expulsion interaction, there may be numerous mistakes in the item, for instance on the off chance that the temperature isn't kept up with appropriately the result which will get isn't generally as great as it ought to be [10].
Container
This is the section that is available at the start of the process, where the plastic is taken care of into the framework, which works by gravity to deliver grains to the container [7]. Container is primarily cone-shaped to allow for easy movement of the basic ingredients. Most containers are gotten together with the assistance of a nut and screw so it tends to be eliminated for various shapes and sizes of material [4].
Screw
The screw is responsible for moving the material from the compartment into the system. The grains are pushed into the barrel by the spinning screw. The screw is the most important component to operate on the foolish arrangement, presuming that the screw may cause risks and incorrect outcomes [6]. The screw is the most important component to work on the foolish layout, assuming that the screw may cause risks and poor outcomes.
Barrel
PTC or terminated radiators in the barrel warm the granules through five paths of heat. The granules go from a solid to a liquid condition [7]. This area is known as the warming and mixing zone. Because the barrel temperatures are sufficiently high to relax the plastic, the contact power between the screw and the granules makes it easier to condense. The fluid material passes through the barrel and into the kick the pail's apertures, where the state of the thing is determined.
Spout
The main component of the extruder is a breaker plate, which is used to slow down materials that are directly related to the spout. Normally, the stuff siphons are by and large put
in the middle of the spout in request to keep a uniform strain which brings about creating uniform elements of the cross area. So, it serves as a seal between both the spout and the extruder, and it has a hole through which the polymers are forcefully sent after the turning development process. It likewise decreases the pollution while going through the spout. We can change the spout as indicated by the necessary size of the fiber. Accordingly, in this cycle, the spout is a crucial component [7].
Control unit
This control unit is the gadget that connects each contraption to its function. The creation can be handled by the basic or electronic control unit. With the help of this control unit, the speed and light in the barrel may be maintained [7]. In essence, it is an electronic game strategy that is linked together to make eviction easier. In the show leading body of the control unit, the creation regard and the power taken by the motor are also commonly found [4].
Electrical Heaters
In this machine, electrical radiators are employed to replace alternative fluid warmers or steam warming systems. These are employed because they are capable and cost effective maintaining the link between the warming structure and the environment is not prohibitively expensive. Electric radiators typically cover a larger area than other types of heating installations. It has turned into an expert very much arranged despising system in ousting measure. The current passes via a guide with specified checks, and these resistance capacities act as an obstruction in the stream, causing the light. Warmers are necessary for the condensing of materials to be dealt with in the next stage. In the extruder, if the machine is small and has few zones, it has few warmers, however if the machine is large and has many zones, it has many electric radiators [7].
PID Controller
The PID is the device that tells the SSR when to turn on and when to turn off. With the help of an indoor controller, ID examines the temperature of the any structure It restricts the structure of the information board. Most routine cycles in the industry are controlled by extremely important temperature controls. They usually come in a variety of DIN sizes, with varying yields and programmable yield restrictions. Furthermore, these controllers can execute PID control for improbable general control circumstances. They are mostly found in the front board, with a feature that allows for rudimentary overseer transparency [4]. These controllers offer a pre-tune capability for determining the PID temperature for a cycle, as well as a steady tuneability for fine-tuning the PID temperature over time. This considers a quick plan, time savings, and waste reduction [5].
Thermocouple
The thermocouple's fundamental capacity is used to calculate temperature. It functions similarly to sensors made of a variety of materials and two wires. When current is carried via the wires, a few voltages are produced, which determine the temperature of the framework. These are essentially utilized since they are modest and gauges high temperatures.
Motor
The DC engine is the major power source of this machine. With the assistance of directions issued to the engines, this engine may pivot both clockwise and counter clockwise. They have the ability to summon an army up to three times in a crisis. The energy in this engine is instantaneously transferred to the resistors, allowing them to work in various domains as needed. The engine can work constantly with next to no brake and can come to a condition of rest without the assistance of a switch. It reduces the size of mechanical brakes [7].
-
CONCLUSIONS
The following conclusions are inferred from this study.
-
Present study conveys, a limited-scale plastic expulsion machine can be manufactured. The machine could be utilized at social orders, in reverse regions where plastic contamination is for a bigger scope, and by reusing individuals could bring in cash by selling reused plastic as crude materials to the business. On the off chance that such short-scope machines are adjusted by a wide scope of individuals, there will be a huge measure of waste or plastic decrease.
-
Plastic won't wind up in landfills or water assets imperiling the environment. While the fate of plastic reusing is very encouraging, it has quite far to step ahead. A fundamentally high extent of plastic squanders goes to landfills, for quite some time, including deficient inclusion of metropolitan reusing programs, conflicting regulations, and disarray among the overall population whether or not a material is recyclable, item configuration issues, as well as different issues.
ACKNOWLEDGMENT
The Authors are very much grateful to Prof. Sharathchandra Prabhu, Associate Professor, AIET, Moodbidri, Karnataka, India for their valuable suggestions, guidance and support. I Thank GOD almighty for his grace throughout the work.
[7] Kumar, Sagar, R. Sooraj, and MV Vinod Kumar. Design and Fabrication of Extrusion Machine For Recycling Plastics. IOP Conference Series: Materials Science and Engineering. Vol. 1065. No.1. IOP Publishing, 2021.
[8] Mwanza, Bupe Getrude, Charles Mbohwa, and Arnesh Telukdarie. Strategies for the recovery and recycling of Plastic Solid Waste (PSW): A focus on plastic manufacturing companies. Procedia Manufacturing 21 (2018): 686-693. [9] Thiounn, Timmy, and Rhett C. Smith. Advances and approaches for chemical recycling of plastic waste. Journal of Polymer Science 58.10 (2020): 1347-1364. [10] Jha, Kundan Kumar, and T. T. M. Kannan. Recycling of plastic waste into fuel by pyrolysis-a review. Materials Today: Proceedings 37 (2021): 3718-3720.REFERENCES
[1] Patil, P. M., & Sadaphale, P. D. B. (2018). A study of the plastic extrusion process and its defects. International Journal of Latest Technology in Engineering, Management & Applied Sciences (Basel, Switzerland), 7(9), 13-20. [2] Ugoamadi, C. C., and O. K. Ihesiulor. Optimization of the development of a plastic extrusion machine. Nigerian Journal of Technology 30.3 (2011): 67-81. [3] Raju, Geo, Mohan Lal Sharma, and Makkhan Lal Meena. Recent methods for optimization of the plastic extrusion process: a literature review. International Journal of Advanced Mechanical Engineering 4, no. 6 (2014): 583-588. [4] Gyarfas, Attila, and Attila GerGely. The Design of a small-scale PlasTic exTruDer machine. Muszaki Tudományos Közlemények 11.1: 73-76. [5] Reddy, Sudhakara, and Thunga Raju. Design and development of mini plastic shredder machine. IOP Conference Series: Materials Science and Engineering. Vol. 455. No. 1. IOP Publishing, 2018. [6] Budiyantoro, Cahyo, Heru SB Rochardjo, and Gesang Nugroho. Design, Manufacture, and Performance Testing of Extrusion Pultrusion Machine for Fiber-Reinforced Thermoplastic Pellet Production. Machines 9.2 (2021): 42.