
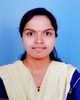
- Open Access
- Authors : V. J. Khot , Manisha Shankar Mane
- Paper ID : IJERTV11IS060271
- Volume & Issue : Volume 11, Issue 06 (June 2022)
- Published (First Online): 30-06-2022
- ISSN (Online) : 2278-0181
- Publisher Name : IJERT
- License:
This work is licensed under a Creative Commons Attribution 4.0 International License
Design and Development of Automatic Fabric feeding and cutting Machine for Medical Field
Prof. V. J. Khot1, Professor,
Department of Mechanical Engineering,
Dr. J. J. Magdum College of Engineering, Jaysingpur, Maharashtra, India.
Manisha Shankar Mane2, M.tech Student,
Department of Mechanical Engineering,
Dr. J. J. Magdum College of Engineering, Jaysingpur, Maharashtra, India.
Abstract:- Importance Of Industrial Machinery. During the last few decades various automation and rationalization technique has been introduced in the field of manufacturing in order to enhance the overall industrial productivity. For this we have to develop / modify existing system, also new attachment and jigs and fixtures are required. In this modern world, machines play a crucial role in different industries and they have replaced the need for labor work. With the tremendous development in technology dependence on manual work is decreased significantly. Some of the leading manufacturers of material handling equipment, industrial machinery from India is recognized for their high-quality products. In this machinery cutting machinery also plays the important roles. The modernization and new technologies are required in this field. The best example is hacksaw cutting machinery used in the industry.
In this project we have tried to develop automatic cloth feeding and cutting Mechanism for medical field.
1.1 Problem Statement and Background: –
CHAPTER 1
Problem Statement
In India, 10-30% of hospital admissions are due to road traffic injuries and a majority of these people tend to develop varying levels of disabilities. An accident victim may just have a fracture, but not handling the person properly while transferring them to a hospital can worsen the condition. A simple splint could prevent matters from getting worse.
. Presently the company uses manual method for cutting the raw material as per required length. To increase the production and to avoid manual interference the sponsorship company wants the automatic cutting and feeding machine.
Fig:- Required shapes and proposed dies for cutting the raw material
Company would like to manufacture the raw material of different sizes of Fabric length, hook length and loop length.
Reference of Table-
All dimensions in CM |
|||
Sizes |
Fabric Length |
Hook Length |
Loop Length |
Size 1 |
32 |
5 |
30 |
Size 2 |
55 |
5 |
42 |
Size 3 |
62.6 |
5 |
53 |
Size 4 |
60 |
5 |
53 |
Size 5 |
78 |
5 |
64 |
Size 6 |
85.5 |
5 |
64 |
Size 7 |
171 |
5 |
64 |
1.2 OBJECTIVE
-
Improve and optimize the present procedure.
-
To improve accuracy.
-
Minimize the time required by using Mechatronics Technology.
The objectives of the project are to design a system for an automatic wire cutting machine which is:
-
Automation
-
Efficient
-
User-friendly
-
Transportable
-
Cost-effective
-
Reduce strenuous and repetitive task
-
Functional requirement of proposed system
-
Respond as per users input
-
Display users input
CHAPTER 2
Introduction
FractoAid is an orthopedic splint which provides early and instant immobilization to the fractured limb.
-
Stabilizes and restricts the motion of injured limb
-
Reduces muscle pain and muscle spasm
-
Accommodates the muscle swelling
-
Prevents the chances of closed fracture becoming open
-
-
FractoAid is an integrated package of composite material enclosed in a unique liner with in-built straps of hook-loop fastener for better securement of fractured limb. The hybrid composition gives high strength to weight ratio and provides stiffness with quick setting time of 3 minutes. The functional strength is achieved within 5 minutes of time. The unique liner allows easy access of water into the splint. The layer in contact with skin is biocompatible, breathable and provides cushioning to the patient. The device provides therapeutic positioning thus conforms to the specific area of patients extremity. The 3 step application process makes the device user-friendly
Fig:- Handicapped person uses the fabric material
Relevance /Motivation
In this modern world, machines play a crucial role in different industries and they have replaced the need for labor work. With the tremendous development in technology dependence the manual work is decreased significantly. Some of the leading manufacturers of material handling equipment, industrial machinery from India is recognized for their high quality products. In this machinery feeding and cutting machinery also plays the important roles and the modernization and new technologies are required in this field. In the medical field according to demand and requirement on time delivery is very important. In this field the demand is consistent, so medical equipment and accessories developers try to use modern and mechatronics machinery for better accuracy and on time delivery by reducing labor and manufacturing cost.
In this project we have tried to develop automatic cloth feeding and cutting mechanism for medical field.
CHAPTER 3
Literature survey
Yong-Seok Kim, Chan Se Jeong has given information for the automatic cutting mechanism of the perforation pipes in an automobile muffler. This cutting mechanism makes continuous work possible, because it performs the batch work via the sequential operation of loading, feeding, cutting, and discharging. The proposed cutting mechanism consists of the frame unit, escape unit, turning unit, feeding unit, vision system, clamping unit, spindle/cutting unit and cooling unit. And, these mechanisms have been modularized through mechanical, dynamical and structural optimized design using the SMO (SimDesigner Motion) analysis module. Also, the virtual prototype was carried out using the 3-D CAD program. The cutting process cycle is performed in the order of loading, vision processing, feeding, clamping, cutting and discharging. And the cycle time for cutting one piece was designed to be completed in four seconds.
M.Khaja Gulam Hussain author has explained about, many efforts being made for taking away the burden on the humans. For this purpose, there are many efforts going on for the Automization of machines. This paper has taken up the fabrication of Automatic Feeding and Cutting Mechanism. This machine automatically feeds its stock and performs the cutting operation. It involves simple lever mechanisms. Here the power input for the machine is provided by means of a motor. It involves simple mechanisms which transfers the motion from one form to the other. This mechanism is very useful in making holes on metal sheets in industries, by changing the tool. By using this mechanism for stitching of big bags in agriculture
Shital K.Sharma1 , Ashish V.Waghmare, has explained about to reduce human effort for repetitive work of cutter pieces of pipes as well as providing a convenientfixture to support and hold the pipes/rods during cutting. The subject is undertaken as a part of B.E mechanical project. It can be termed as smart machine. There are many industrial applications where round bar or square bars are required to be operated on different machines to make machine components such as Shafts, Bolts, Screws, etc. This needs more and more number of pieces to be cut for mass production of those components. The bar feeding mechanism is a metal cutting machine tool designed to feed the metal. The machine is exclusively intended for the mass production and they represent faster and more efficient way to feed the metal. The clamping arrangement can be varied according to need of operations suitable. The overall system is compact in size, light weight, modular and flexible to be used in small works jobs who need batch production. The setup overall configuration can be adopted by a semi-skilled worker easily and can vary the operations by making certain small changes. The system even has the potential to add up a PLC system to control its overall working with ease and with less effort provided. This system has the potential to adopt higher level of automation if desired in future.
Mohan M, Sathish M author given information on The objective of this work is to automate the conventional power hacksaw machine in order to achieve high productivity of work-pieces than the power hacksaw machine. The automated machine the number of pieces to be cut and the length of each piece that is required to be cut. The inputs are given by with the help of a battery. The operator need not measure the length of the work-piece that is to be cut and to load and unload the work-piece from the chuck each time after a piece has been cut. The machine automatically feeds the given length of work-piece in to a chuck and starts to cut till the given number of work-pieces has been cut. which is driven by a DC motor and an IR sensor ensures that the feeding stops when the specified length has been reached. Bring about the reciprocating motion required for cutting the work-pieces. There is a electromagnetic self-weight attached with the reciprocating mechanism to provide the necessary downward force required for penetration of hacksaw blade in to the work-piece.The machine we designed and fabrication is used for cutting any shape of object like circular. According to the type of material to be cut, the cutting tool can be changed .This project givens details of pipe. This machine can be widely applied in almost all type of industries. The pipe cutting process is a main part of the all industries. Normally the cutting machine is manually hand operated one for medium and small scale industries. Automation in the modern world is inevitable .Any automatic machine aimed at the economical use of man machine , and material worth the most. The pipe cutting machine works with the help of motor .In our project small and large size pipe cutting used adjustment in various type of pipe.
CHAPTER 4
-
Theory
Methods of Fabric Cutting in Garment Industry
During cutting, separate garment components are cut out from the fabric spreading in accordance with their shape and number determined by the marker. Fabric cutting is completed by different types of fabric cutting machines. In most of the cutting methods, a sharp blade is pressed against the fibers of the fabric to separate them. The cutting knife has to present a very thin edge to the fibers, to shear the fibers without exerting a force that will deform the fabric. The act of cutting de-sharpens the blade, which should be sharpened frequently. The cloth cutting types of methods are discussed on https://clothingindustry.blogspot.com .
-
Literature Summary:-
In the present literature survey information about mainly bar and pipe automatic feeding- cutting machineries/ mechanisms are discussed. In garment sector automatic machineries are available but cost and constraints are there. Specific of fabric cutting as per requirement the machineries are not available. In the present literature the maximum information is available for raw material cutting and feeding.
-
Literature Gap:-
The semiautomatic machines in fabric cloth industries are not available easily, also some constraints are there. For required size and shape special purpose machineries are require to develop. In this project work we have tried to develop semiautomatic machine, which have huge scope and demand in fabric / garment industry.
Surgical face masks are worn by health care professionals during surgery or while attending to patients in order to avoid contact with bacteria shed in the form of liquid droplets and aerosols from the mouth and nose or infectious blood and body fluids. Surgical face masks are used as a protective barrier to prevent cross-contamination among patients and surgeons. They are made mostly from non-woven fabric and are available in the two-layer and three- layer form. Surgical face masks are used in operation theatres and every area of health care that requires patient inspection. Rise in awareness regarding airborne infections has led to an increase in usage of surgical face masks is not only large health care facilities but also smaller ones across the world. The usage of surgical face masks has increased among the general public owing to the rise in outbreaks of airborne diseases in recent times. The inevitable use of surgical face masks and lower threat of their substitutes are expected to propel the global surgical face masks market during the forecast period.
Market Potential:
Increase in aging population, prevalence of hospital acquired infections (HAIs), and rise in demand of improved healthcare facilities in the developing economies drive the market. The global disposable medical masks market is segmented based on type, end user, and region. On the basis of type, the market is bifurcated into facemasks and respirators. Based on application, it is categorized into hospitals & clinics, industrial, individual and others. The global surgical face mask market can be segmented based on distribution channel, end- user, and region. Healthcare professionals or the general public are the end users of surgical face masks. Surgical face masks are widely available through all distribution channels, and owing to the rise in number of outbreaks, the usage of surgical masks is expected to increase considerably in the near future. In terms of distribution channel, the global surgical face mask market can be segregated into independent pharmacies, online sales, hospital pharmacies, retail stores, and others.
Technical aspects:
Process of Manufacturing: One set mask machine is connected to three mask ear belt welding machines. After the mask body is made, the conveyor belt is sent to the ear belt welding machine for ear belt welding. It can complete an ear mask and only one operator can operate the whole production line. The production line realizes the full automatic production of plane mask, mainly including coil feeding, folding, pressing, nose rib feeding, mask shaping, mask cutting, ear feeding and welding, finished product cutting and other processes. The mask is comfortable to wear, no pressure, good filtering effect, can be used in health care, electronics and other industries.
Quality Specification:
BIS IS 16289: 2014
Medical Textiles Surgical Face Masks Specification
CHAPTER 5
Proposed work in project
Design and development of automatic fabric feeding and cutting mechanism for Medical field.
Specification of Proposed mechanisms:-
-
Function : Feeding and cutting the fabric smoothly as per required length and shape.
-
Specification :
-
Type : fabric material cutting and feeding.
-
Power:- AC /DC.
-
Man power requirement:- one operator
-
Overall dimensions (Tentative): 1230 x 1250 x 835 mm
-
Fabric cutting: By using Cutting blade / Dies.
-
Capacity: As per size and length of the fabric material.
-
Selected size: – As per manufacturers chart.
-
General Information:
The machine consists of a standard timing roller and microcontroller electronics circuit, feeding conveyor, control panel.
-
-
Analysis of different critical parts of mechanism.
-
Design and Development of guide roller shaft.
-
Design and Development of fabric grip mechanism.
-
Design of spring.
-
Design of Dies.
-
Design of Cutting mechanism (Blades/Dies vertical reciprocating mechanism)
-
-
Selection of materials, components, bearings, Motor, Coupling and drives for automatic mechanism.
-
Analysis of critical components
-
-
Analysis of guide roller.
-
Analysis of mechanical linkages used for cutting of fabric.
-
Analysis of drive shaft.
5.1 This project will undergo through following seven phases. Phase I: Literature Survey
A detailed literature survey will be carried out in the related area. Majorly the selected project is come under industrial field influence, So In this phase we will do small scale industrial visits, Feedbacks and problems faced by vendors.
Phase II: Concept Generation
In this phase, we are going to do schematic arrangement of design and drawing of major component which we can use for the completion of our project. In this phase we will generate the schematic drawing on the basis of problem statement and feedback and suggestion received from end customer and vendors.
Phase III: Design calculations
In this phase we are going to do the design calculations by referring the standards, catalogue and reference books. In this work we will finalize the design and components dimensions. We are also selecting the material according to parts and components function and loading conditions. In this phase we will decide the size and shape of components and its position in the assembly. Also we will decide the limit and tolerance between components and also machining methods required to select to manufacture the components.
Phase IV: Preparation of Drawings
In this phase we are going to prepare the design. The suitable component and assembly drawings will be prepared which will help the visualize to actual project set up. In this phase we will prepare the drawings as per the industrial format.
Phase V: Structural Analysis of the Critical Components
In this phase we will do analysis of one components which is under critical loading condition. And by doing analysis we can decide the final dimensions and material of the component.
Phase VI: Fabrication
-
Manufacturing of various components and subassemblies will be carried out by using suitable manufacturing processes.
-
The components will be assembled per the drawing.
-
Working trials of the project will be conducted to confirm and testing parameters (Time and speed) we will decide for to get best quality of product.
Phase VII: Experimental Investigations (Actual Field Trial)
The fabricated mechanism will be tested for the suitability to the intended application. This experimental testing will include the testing of machine at actual site.
-
Design of shaft.
-
The spring load on cloth considered 5kg
-
The speed of roller selected = 30rpm
CHAPTER 6
Design of experiment set up
For this project we have considered PMDC motor. They are available easily and having low cost The clamping and guiding arrangement
So we have taken rollers for guiding against machine.
To take grip and for guiding we have considered 5kg load on roller.
The self weight and for design purpose we have considered 20 kg load on roller
So total load on roller = 20 kg = 200N Torque on shaft = 200 x roller diameter
Roller diameter = 50mm.
Design load considered = 20 kg on each roller = 200N For suitable roller considered = 50mm dia
Total torque on crank = 200 x 25= 5000N-m T = Max Torque generated to rotating Crank
= 145 N/ mm2 considering factor of safety = 4
Design of shaft against torsion:-
As per Design data book shaft material is selected Carbon steel C40
= 145 N/mm2 As per ASME code
0.3 X Yield strength N/mm2
0.18 X ultimate strength N/mm2} whichever is smaller
0.3 x 330 = 99 N/mm2 .(a)
0.18 x 580 = 104 N/mm2 ..(b) From equation (a) & (b)
Allowable stress value will be 99 N/mm2 If key ways will provide to shaft then
= 99 x 0.75 = 74.25 N/mm2
Max torsional moment equation is given by
Where T = 5000N-mm
By using above equation drive shaft dia d = 7mm .A
Design against bending:-
Fig Drive shaft loading condition.
The static load considered on shaft 100 kg. By considering errors in alignment and fabrication work of project The center distance we have considered = 200mm
P = 1000 N
FY 0
RA + RB= 1000
As per load condition and farm condition the total load on wheel is considered
RB =500 N RA = 500 N
Calculation of bending moment at loading point P, BM at M = 500 x 100 = 50000N-mm
= 145 N/ mm2 considering factor of safety = 4
By using above equation drive shaft dia d = 15.49mm ..B
From equation A and B we have selected the diameter of shaft = 20mm considering extra jerk and for safe design.
According to maximum shear stress theory
= 34.40 < 74 N/mm2 and
= 66.07 < 145 N/mm2
By using above equation we have checked the allowable shear stress and allowable bending stress and it is seen that the both values are within limit hence design is safe.
-
-
Selection of bearing :-
P = RB = 500 N
Life in hrs = 10000 hrs
L = 36 millions of rev
a = 3 for ball bearing.
From SKF bearing catalogue we have selected the bearing static capacity for shaft dia 20mm = Co = 2.32 KN From above equation = C = 285 N
So calculated dynamic capacity C < bearing catalogue dyanamic capacity C = 4.32KN Hence from catalogue bearing selected = 61204
-
Design of springs
Materials for springs: The material for spring should have high fatigue strength, high ductility, high resilience and it should be creep resistant.
-
0.9% – 1.0% carbon is common material for springs.
Steel with 0.85% – 0.95% carbon and 0.3% – 0.4%
-
Manganese is used for longer sized springs.
-
Alloy steels such as chrome – vanadium and silicon manganese steels are used for better grade springs.
-
Chrome steel, phosphorus bronze and Monel metal (nickel alloy) can also be used in special cases, to increase corrosion resistance and temperature resistance.
Parameters and Geometric Dimensions of a Cylindrical Spring
(wire dia.), d (outside dia.), D2 (inside dia.), D1 (mean dia.), D
(pitch), p
(pitch angle), Ø
-
(free length), Lf
STRESS IN SPRINGS:
Consider a helical spring made of circular wire diameter, 'd' mm. Pitch of spring is very small. The action of load "W" tends to twist the wire there by causing torsional shear stresses in the wire. Such springs are designed for torsion.
Neglecting effect of bending and direct shear. Let, W = axial load
R = mean radius of coil d = diameter of coil wire
Stress can be calculated by using torsion equation, .
T/J = fs/R
Fs = TR/J = T/Zp Where , Zp = section modulus = /16xd
T = torque transmitted by the spring = WxR
Shear stress induced, fs = 16 WR/nd3
Design of spring wire
The load on spring considered 25kg = 250N
Wahls factor K = We know that
4C 1 0.615
x
4C -4 C
8w
= 1.31
= K x ————
D2
D2 = 1.06x8x0.25x103x5
D2 = 7.49
X450
D = 2.43mm
D = 2.5 mm
Mean diameter d = cxd = 5x 2.5 = 12.5 mm Let us assume number of turns n=5
For square and ground ends
n1 = n+2= 5+2=7
Deflection of spring
The load on spring considered 25kg = 250N
3 3 3
8Wd n 8 0.25 10 12.5 5 6.25mm
Gd 4
Free length of the spring
8 104 (2.5)4
f
l (n1 d ) (0.15 ) (5 2.5) 6.25 (0.15 6.25) 19.68mm
For our project length required 300mm
Pitch of the coil
f ree length 19.68
p 4.92mm
7. DC Motor
n1 1
5 1
Fig. 17 DC Motor
-
High efficiency, high quality low cost DC motor with gearbox for robotics applications. Very easy to use and available in standard size. Nut and threads on shaft to easily connect and internal threaded shaft for easily connecting it to wheel.
-
Features
-
3.5 RPM to 1000 RPM at 12V DC motors with Gearbox, RPM can vary when operating from 3 to 15V
-
5kgcm torque
-
3000RPM base motor
-
6mm shaft diameter with internal hole
-
125gm weight
-
Same size motor available in various rpm
-
No-load current = 60 mA(Max), Load current = 300 mA(Max
-
Working
A DC motor relies on the fact that like magnet poles repel and unlike magnetic poles attract each other. A coil of wire with a current running through it generates an electromagnetic field aligned with the center of the coil. By switching the current on or off in a coil its magnetic field can be switched on or off or by switching the direction of the current in the coil the direction of the generated magnetic field can be switched 180°. A simple DC motor typically has a stationary set of magnets in the stator and an armature with a series of two or more windings of wire wrapped in insulated stack slots around iron pole pieces (called stack teeth) with the ends of the wires terminating on a commutator. The armature includes the mounting bearings that keep it in the center of the motor and the power shaft of the motor and the commutator connections. The winding in the armature continues to loop all the way around the armature and uses either single or parallel conductors (wires), and can circle several times around the stack teeth. The total amount of current sent to the coil, the coil's size and what it's wrapped around dictate the strength of the electromagnetic field created. The sequence of turning a particular coil on or off dictates what direction the effective electromagnetic fields are pointed. By turning on and off coils in sequence a rotating magnetic field can be created. These rotating magnetic fields interact with the magnetic fields of the magnets (permanent orelectromagnets) in the stationary part of the motor (stator) to create a force on the armature which causes it to rotate. In some DC motor designs the stator fields use electromagnets to create their magnetic fields which allow greater control over the motor. At high power levels, DC motors are almost always cooled using forced air.
CHAPTER 7
Constructional details
Fig:-7.1 detailed drawing of proposed mechanism
Fig:-7.2 schematic arrangement of project set up
CHAPTER 8
Component details
-
Structural Frame:-
In the design of this project frame is the main supporting member which provides support for other components like motor, adjustable arm, spring mechanism, rollers, bearings etc. In order to get sufficient strength the material which we have selected for the frame is MS (Mild Steel).
-
Drive Shaft Wheel
Specifications of drive shaft wheel:
-
Material: Mild Steel
-
Outer diameter: 140 mm
-
Inner diameter: 16 mm
-
Thickness: 25 mm
Fig:8.1- structural frame
-
6 holes of 20 mm diameter are provided in order to reduce weight of the wheel.
-
-
Rollers/Pulleys
Rollers are used to support and rotate the belt during coating. In this project rollers made up of Mild Steel are used having following dimensions. 1. Outer diameter: 50 mm 2. Inner diameter: 20 mm is provided to avoid slipping of bar from the rollers during feeding.
8.4.1 Pillow block Bearing Material: Housing, grey cast iron.
Bearing: Ball-bearing Pillow block bearing UCP204
Seal: Rubber NBR.
Surface finish: Housing, painted.
Fig:-8.4.1 UCP 204 bearing Ref:- UCP bearing catalogue
Pedestal block bearings consist of a sealed single-row ball bearing with a spherical outer ring which is mounted in housing. Because of the spherical outer surface of the bearing, shaft misalignment can be compensated for. The bearings are manufactured with a plus tolerance. This results in transition or press fits when using shafts with h-tolerances. The shaft is secured by grub screws on the inner ring. In normal applications, pillow block bearings are maintenance-free due to the lifetime lubrication. Temperature range: -15 °C to +100 °C. It is a split type of bearing. This type of bearing is used for higher speeds, heavy loads and large sizes. This bearing facilitates the placements and removal of the shaft from the bearing.
Pillow blocks are usually referred to the housings which have a bearing fitted into them and thus the user need not purchase the bearings separately. Pillow blocks are usually mounted in cleaner environments and generally are meant for lesser loads of general industry. Bearing housings are usually made of grey cast iron. However various grades of metals can be used to manufacture the same. ISO 113 specifies internationally accepted dimensions for Plummer blocks.
-
Electronic components:
Fig:- 8.5 Circuit diagram for bar feeding and cutting mechanism
The concept of this project is to lower the cost and time requirements for a small scale user. The brief idea is to develop a system which will perform the wire cutting operation. In this a mechanical assembly interfaced with micro controller based circuit is used to perform these tasks. Mechanical assembly will consist of dc motors which passes the wire with his rotations.
The system will consist of the following control & monitoring parameters and Hardware:
-
Micro-controller unit
-
DC motor
-
Power Supply
-
LCD Display
-
Keypad
-
Relay Drive Circuit
-
DC Motors
-
Magnetic sensor
-
-
POWER SUPPLY:
The microcontroller need +5V DC, These specifications dictate the use of a low-cost, ubiquitous linear regulator National Semiconductor LM7805. The LM7805 requires an input voltage of at least 7.5V in order to guarantee regulation, so the unregulated power supply should supply at least this voltage under worst-case current consumption, assumed to be about 200mA.
Because a full-wave rectifier will be used for efficiency (diodes D1-D2), we can assume that about 1.4V will be lost across the bridge (0.7V per conducting diode). We therefore need a transformer was selected as T1, which is of rating 9 -0-9 secondary at 500 mA
-
Transformer:-
Transformer is electrical device that transfer energy between two or more circuits through electromagnetic
induction.
A) 9v 500mA Transformer (230V to 9V) [9-0-9]:
Fig.8.5.2 Transformer(9-0-9)
Good Quality Transformer, power supplies for all kinds of project & circuit boards. Step down 230 V AC to 9V with a maximum of 500mAmp current. Generally known as 9-0-9
-
Specification:
-
voltage: 2 x 9V
-
current: 1 x 500mA
-
rated power: 9VA
-
B) 12V500mA Transformer (230V to 12V) [12-0-12]:
-
This meansoutput voltage available 12V from center of both sides end to end 24V. The safe maximum current along of this transformer is 500mA.
-
Specification:
-
voltage: 2 x 12V
-
current: 1 x 500mA
-
rated power: 12VA Application of transformer
-
-
-
To increase voltage before transmitting electrical energy.
-
If can isolates two circuits electrically.
icrocontroller at89s52:
-
If can acts as impedance transmitting device.
-
-
M
Overview
The Arduino Uno is a microcontroller board based on the ATmega328 (datasheet). It has 14 digital input/output pins (of which 6 can be used as PWM outputs), 6 analog inputs, a 16 MHz ceramic resonator, a USB connection, a power jack, an ICSP header, and a reset button. It contains everything needed to support the microcontroller; simply connect it to a computer with a USB cable or power it with a AC-to-DC adapter or battery to get started.
Summary
Microcontroller – ATmega328 Operating Voltage – 5V
Input Voltage (recommended): 7-12V Input Voltage (limits): 6-20V
Digital I/O Pins: 14 Analog Input Pins: 6
DC Current per I/O Pin: 40 mA DC Current for 3.3V Pin: 50 mA
Flash Memory: 32 KB (ATmega328) SRAM: 2 KB (ATmega328) EEPROM: 1 KB (ATmega328)
Clock Speed: 16 MHz
Power
The Arduino Uno can be powered via the USB connection or with an external power supply. The power source is
selected automatically. External (non-USB) power can come either from an AC-to-DC adapter (wall-wart) or battery. The adapter can be connected by plugging a 2.1mm center-positive plug into the board's power jack. Leads from a battery can be inserted in the Gnd and Vin pin headers of the POWER connector. The board can operate on an external supply of 6 to 20 volts. If supplied with less than 7V, however, the 5V pin may supply less than five volts and the board may be unstable. If using more than 12V, the voltage regulator may overheat and damage the board. The recommended range is 7 to 12 volts.
The power pins are as follows:
VIN: The input voltage to the Arduino board when it's using an external power source (as opposed to 5 volts from the USB connection or other regulated power source). Can supply voltage through this pin, or, if supplying voltage via the power jack, access it through this pin.
5V: This pin outputs a regulated 5V from the regulator on the board. The board can be supplied with power either from the DC power jack (7 – 12V), the USB connector (5V), or the VIN pin of the board (7-12V). Supplying voltage via the 5V or 3.3V pins bypasses the regulator, and can damage board.
3V3: A 3.3 volt supply generated by the on-board regulator. Maximum current draw is 50 mA. GND: Ground pins.
Memory
The ATmega328 has 32 KB (with 0.5 KB used for the bootloader). It also has 2 KB of SRAM and 1 KB of EEPROM (which can be read and written with the EEPROM library).
Input and Output
Each of the 14 digital pins on the Uno can be used as an input or output, using pinMode(), digitalWrite(), and digitalRead() functions. They operate at 5 volts. Each pin can provide or receive a maximum of 40 mA and has an internal pull- up resistor (disconnected by default) of 20-50 kOhms. In addition, some pins have specialized functions:
Serial: 0 (RX) and 1 (TX). Used to receive (RX) and transmit (TX) TTL serial data. These pins are connected to the corresponding pins of the ATmega8U2 USB-to-TTL Serial chip.
External Interrupts: 2 and 3. These pins can be configured to trigger an interrupt on a low value, a rising or falling edge, or a change in value. See the attachInterrupt() function for details.
PWM: 3, 5, 6, 9, 10, and 11. Provide 8-bit PWM output with the analogWrite() function.
SPI: 10 (SS), 11 (MOSI), 12 (MISO), 13 (SCK). These pins support SPI communication using the SPI library.
LED: 13. There is a built-in LED connected to digital pin 13. When the pin is HIGH value, the LED is on, when the pin is LOW, it's off.
The Uno has 6 analog inputs, labeled A0 through A5, each of which provide 10 bits of resolution (i.e. 1024 different values). By default they measure from ground to 5 volts, though is it possible to change the upper end of their range using the AREF pin and the analogReference() function. Additionally, some pins have specialized functionality:
TWI: A4 or SDA pin and A5 or SCL pin. Support TWI communication using the Wire library. There are a couple of other pins on the board:
AREF: Reference voltage for the analog inputs. Used with analogReference().
Reset: Bring this line LOW to reset the microcontroller. Typically used to add a reset button to shields which block the one on the board.
Communication
The Arduino Uno has a number of facilities for communicating with a computer, another Arduino, or other microcontrollers. The ATmega328 provides UART TTL (5V) serial communication, which is available on digital pins 0 (RX) and 1 (TX). An ATmega16U2 on the board channels this serial communication over USB and appears as a virtual com port to software on the computer. The '16U2 firmware uses the standard USB COM drivers, and no external driver is needed. However, on Windows, a .inf file is required. The Arduino software includes a serial monitor which allows simple textual data to be sent to and from the Arduino board. The RX and TX LEDs on the board will flash when data is being transmitted via the USB-to- serial chip and USB connection to the computer (but not for serial communication on pins 0 and 1).
A SoftwareSerial library allows for serial communication on any of the Uno's digital pins. The ATmega328 also supports I2C (TWI) and SPI communication. The Arduino software includes a Wire library to simplify use of the I2C bus.
Programming
The Arduino Uno can be programmed with the Arduino software. Select "Arduino Uno from the Tools > Board menu (according to the microcontroller on your board).The ATmega328 on the Arduino Uno comes preburned with a bootloader that allows to upload new code to it without the use of an external hardware programmer. It communicates using the original STK500 protocol. Can also bypass the bootloader and program the microcontroller through the ICSP (In-Circuit Serial Programming) header.
Automatic (Software) Reset
Rather than requiring a physical press of the reset button before an upload, the Arduino Uno is designed in a way that allows it to be reset by software running on a connected computer. One of the hardware flow control lines (DTR) of the ATmega8U2/16U2 is connected to the reset line of the ATmega328 via a 100 nanofarad capacitor. When this line is asserted (taken low), the reset line drops long enough to reset the chip. The Arduino software uses this capability to allow you to upload code by simply pressing the upload button in the Arduino environment. This means that the bootloader can have a shorter timeout, as the lowering of DTR can be well-coordinated with the start of the upload. This setup has other implications. When the Uno is connected to either a computer running Mac OS X or Linux, it resets each time a connection is made to it from software (via USB). For the following half-second or so, the bootloader is running on the Uno. While it is programmed to ignore malformed data (i.e. anything besides an upload of new code), it will intercept the first few bytes of data sent to the board after a connection is opened. If a sketch running on the board receives one-time configuration or other data when it first starts, make sure that the software with which it communicates waits a second after opening the connection and before sending this data. The Uno contains a trace that can be cut to disable the auto-reset. The pads on either side of the trace can be soldered together to re-enable it. It's labeled "RESET-EN".
USB Ovecurrent Protection
The Arduino Uno has a resettable polyfuse that protects your computer's USB ports from shorts and overcurrent. Although most computers provide their own internal protection, the fuse provides an extra layer of protection. If more than 500 mA is applied to the USB port, the fuse will automatically break the connection until the short or overload is removed.
Physical Characteristics
The maximum length and width of the Uno PCB are 2.7 and 2.1 inches respectively, with the USB connector and power jack extending beyond the former dimension. Four screw holes allow the board to be attached to a surface or case.
AT 89S52 PINOUT:
Fig.11 Microcontroller
Microcontroller at 89s52 features:
-
Compatible with MCS 51 products
-
8k bytes of in system Re-programmable Flash Memory
-
Fully static operation : 0 Hz to 24 MHz
-
256 x 8 bit internal RAM
-
32 programmable I/O Lines
-
Three 16 bit Timer or Counters
-
8 Interrupt sources
-
Programmable serial channel
-
Low power Idle & power down modes
-
Microcontroller at 89s52 description:
The Microcontroller IC 89S52 has 256×8 bit internal RAM which is most important feature for this application. Here eight to ten readings can be recorded in RAM after each half an hour to achieve data logging.
The Timer/Counter application of 89S52 is used to count the pulses from proximity sensor. The interrupt pin INTR0 is used to switch into different setting modes the serial channel is used to get interface with pc for data logger application.
The AT89C52 provides the following standard features: 8Kbytes of Flash, 256 bytes of RAM, 32 I/O lines, three 16- bittimer/counters, six-vector two-level interrupt architecture, a full duplex serial port, on-chip oscillator, and clock circuitry. In addition, the AT89C52 is designed with static logic for operation down to zero frequency and supports two software selectable power saving modes.
The Idle Mode stops the CPU while allowing the RAM, timer/counters, serial port, and interrupt system to continue functioning. The Power down Mode saves the RAM contents but freezes the oscillator, disabling all other chip functions until the next hardware reset.
-
Capacitors:
-
1uf Electrolytic capacitor:
Fig. 13 Capacitor 1uf
This is a 1uF (micro farad) electrolytic capacitor. Used for much application, very commonly used with MAX232 IC for charge pumps and bypass capacitor.
-
1000uf Electrolytic capacitor:
Fig. 14 Capacitor 1000uf
Description: Electrolytic decoupling capacitors 1000uF/25V. These capacitors are great transient/surge suppressors and work well in high-voltage and audio applications.
-
-
7805 Voltage regulator:-
A voltage regulator is designed to automatically maintain a constant voltage level.
Fig. 15- 7805 Voltage regulator
Pin No
Function
Name
1
Input voltage (5V-18V)
Input
2
Ground (0V)
Ground
3
Regulated output; 5V (4.8V-5.2V)
Output
Table no. 3.3.1- 7805 Pin Description
The LM 78LXX series of three terminal positive regulators is available with several fixed output voltages making them useful in a wide range of applications. When used as a zener diode/resistor combination replacement, the LM 78LXX usually results in an effective output impedance improvement of two orders of magnitude and lower quiescent current. These regulators can provide local on card regulation, eliminating the distribution problems associated with single point regulation. The voltages available allow the LM 78LXX to be used in logic systems, instrumentation, Hi-Fi and other solid state electronic equipment.
Features
-
Output voltage tolerances of +-5% over the temperature range.
-
Output current of 100mA.
-
Internal thermal overload protection.
-
Output transistor safe area protection.
-
Internal short circuit current limit.
-
No external components.
PIN Diagram
Working
A ULN2003A is a high-voltage, high-current Darlington transistor array.[1][2]
It consists of seven NPN Darlington pairs that feature high-voltage outputs with common-cathode flyback diodes for switching inductive loads.
It is very similar to the ULN2801A, ULN2802A, ULN2803A,[3] ULN2804A, and ULN2805A, only differing in logic input levels (TTL, CMOS, PMOS) and number of inputs (8).
The drivers can be paralleled for higher current capability, even stacking one chip on top of another, both electrically and physically has been done.
Features
-
500 mA rated collector current (single output)
-
50 V output
-
Includes output flyback diodes
-
Inputs compatible with various types of logic
-
-
Relay:-
Fig. 8.5.7 Relay
A relay is an electrically operated switch. Many relays use an electromagnet to mechanically operate a switch, but other operating principles are also used, such as solid. Relays are used where it is necessary to control a circuit by a low-power signal (with complete electrical isolation between control and controlled circuits), or where several circuits must be controlled by one signal. The first relays were used in long distance telegraph circuits as amplifiers: they repeated the signal coming in from one circuit and re-transmitted it on another circuit. Relays were used extensively in telephone exchanges and early computers to perform logical operations.
-
Keypad
Fig. 8.5.9 Keypad
This 16-button keypad provides a useful human interface component for microcontroller projects. Convenient adhesive backing provides a simple way to mount the keypad in a variety of applications. The Keypad 4×4 features a total of 16 buttons in Matrix form. This is a membrane keypad with no moving parts. It has a nice overlay depicting a telephone type keypad with additional four functional buttons. A female 8-pin berg connector is provided for interfacing it with your microcontroller circuits.
-
Features
-
Ultra-thin design
-
Adhesive backing
-
Excellent price/performance ratio
-
Easy interface to any microcontroller
-
Application Ideas
-
Security systems
-
Menu selection
-
Data entry for embedded systems
-
Key Specifications
-
Maximum Rating: 24 VDC, 30 mA
-
Interface: 8-pin access to 4×4 matrix
-
Operating temperature: 32 to 122 °F (0 to 50°C)
-
Dimensions: Keypad, 2.7 x 3.0 in (6.9 x 7.6 cm)
-
Keypad:
Fig.19 Matrix Keypad
Typically one port pin is required to read a digital input into the controller. When there are a lot of digital input that has to be read, it is not feasible to allocate one pin for each of them. This is when a matrix keypad arrangement is used to reduce the pin count.Therefore, the number of pins that are required to interface a given number of inputs decreases with increase in the order of the matrix.
Initially all switches are assumed to be released. So there is no connection between the rows and columns. When any one of the switches are pressed, the corresponding rows and columns are connected (short circuited). This will drive that column pin (initially high) low. Using this logic, the button press can be detected. The colours red and black are for logic high and low respectively. Here are the steps involved in determining the key that was pressed.
-
16X2 LCDDisplay:
Fig.8.6 LCD Display
LCD indicates different mode settings & set point adjustment. Also 16 char are divided to indicate speed output. The LCD Display used here is 16 characters by 2 line display. The 16 characters in both lines are equally divided to indicate commands and speed. In sub routines Enter Speed and Current Speed message, set Speed value is indicated on screen.
In our project LCD is interfaced with the port-0 (D0-D7) i.e. from pin number 32 to pin number 39. In other words the data-bus D0-D7 is connected to port-0 of IC 89s52. Pin RS is directly connected to Pin11 of controller and one more another important pin EN (LCD enable) is directly connected to pin 14 of the controller. On the other hand pin R/W of LCD is connected to ground. The LCD interfacing is done here for indicating various display messages for the user.
The interfacing is given in detail which is as follows:-
In this equipment the LCD which is used is 16X2 type. i.e. 16 characters per rows and two rows. The function of LCD is to display the status of events performed by the respective circuit or to display those resulting parameters which have to be displayed on the screen as per user requirement.
Pin details:
Fig.8.6.1 LCD Pin Details
LCD-Liquid Crystal Display –
The LCD display has two lines of character,16 character per line. Each character is composed of matrix of pixels size5x8.The matrix is controlled by Hitachi HD44780 controller, which performs all the operation is done in accordance with the instruction it receives as described below:
-
DB0-DB7, the 8 data bus lines, which perform read/write of data
-
Vss,Vdd Voltage supply pins
-
R/W- Pin writing/reading to/from-LCD
-
RS-Pin selects registers between Instruction Register and Data Register
-
E -Enabling pin; when this pin is set to logical low,the LCD does not care what is happening with R/W,RS,and the data bus lines; when this pin is set to logical high, the LCD is processing the incoming data
-
Vo-pin for LCD contrast
-
Fig:- Circuit diagram for actual set up.
Fig:- Flow chart for actual set up for hacksaw machine.
CHAPTER 9
References
[1] 11.1 Mr. R. S. Khurmi & J. K. Gupta Machine Design Pub.: Eurasia Publishing House [2] Pvt. Limited. [3] 11.2 Automatic stock bar feed mechanism for automatic screw machines, Petent No. US 2300457 A by MARIOTTE, Filed Sept. 24, 1940 2 Sheets-Sheet 2 Patented Nov. 3, 1942
[4] 11.3 United Statespatent Office Automatic Stock Bar Feed mechanism for. Automatic screw machines..KshirsagarPrashant R. , RathodNayan J , RahatePrashant P , HalayePrashant P , SurveSachin S, ,International Journal for innovative research in Science and Engineering, Volume No. 01, Issue 02, March 2016. 2. [5] 11.4 Theoretical Analysis of Multi-Way Power Hacksaw Machine by Prof. MuthuKrishnan.A, Sre. NandhaGuhan. K.S, 5th International & 26th All India Manufacturing Technology, Design and Research Conference (AIMTDR 2014) December 12tp4th, 2014, IIT Guwahati, Assam, India. [6] 11.5 Design And development of automated vegetable cutting machine by Tony Thomas.A