
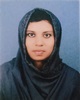
- Open Access
- Authors : Hiba Farhana K A , Dr. S Syed Ibrahim , Rashida P K
- Paper ID : IJERTV11IS070070
- Volume & Issue : Volume 11, Issue 07 (July 2022)
- Published (First Online): 16-07-2022
- ISSN (Online) : 2278-0181
- Publisher Name : IJERT
- License:
This work is licensed under a Creative Commons Attribution 4.0 International License
Structural Performance of Orthogonal and Flat Type Stainless-Steel Plated Shear Wall
Hiba Farhana K A1, Dr. S Syed Ibrahim2, Rashida P K3
1M Tech, Structural Engineering, Ilahia College of Engineering and Technology, Muvattupuzha, Kerala , India 2Associate Professor, Ilahia College of Engineering and Technology, Muvattupuzha, Kerala , India 3Assistant Professor, Ilahia College of Engineering and Technology, Muvattupuzha, Kerala , India
Abstract:- As a part of lateral force resisting system, steel plate shear walls have been widely used in number of buildings. In this study, stainless steel plates are used. Since it has better durability and corrosion resistance when compared to traditional steel. Stainless steel plated shear wall (SSPSW), as an innovative type of wall, consists of stainless-steel plates that are connected by different connector types such as stud, truss and combined stud and truss by welding. By different combination methods, the SSPSW can be used as beam, columns, floors, walls and other components in the building structure. In this study, T-shaped, L-shaped and flat type rectangular SSPSW are used for loading resistance. These SSPSWs are subjected to various loading condition like axial loading, eccentric and lateral loading along major and minor axis and evaluated the suitability of structure. The finite element analysis using ANSYS was used to analyze the influence of different design parameters SSCPW on load- bearing and seismic capacities.
Keywords: Stainless steel plated shear wall, axial loading, eccentric and lateral loading, load-bearing capacity, seismic capacity
-
INTRODUCTION
Stainless steel plated shear wall (SSPSW) is a new type of lateral load resisting system and are similar to sandwich structure. Stainless steel plated shear wall (SSPSW) consists of stainless-steel plates that are connected by different connector types such as stud, truss and combined stud and truss by welding. Stainless steels materials have better durability and corrosion resistance when compared to traditional steel. By different combination methods, the SSPSW can be used as beam, columns, floors, walls and other components in the building structure. In this study, T- shaped, L-shaped and flat type rectangular SSPSW are used for loading resistance. T-shaped SSPSW is connected by two rectangular walls and installed at the interior of building. L-shaped SSPSW is also connected by two rectangular walls and installed at the corner of the building. Flat type rectangular SSPSW can be installed at exterior or interior of the building. In this study, these SSPSWs are subjected to various loading condition like axial loading, eccentric and lateral loading along major and minor axis and evaluated the suitability of structure.
For new type of sandwich structural element, there are many researches existing on the bearing capacity under different loading situation. Xing-Ping Shu, Su Yan, Yi Li and Bei- Rong Lu investigated the failure mechanism of T-shaped SSCPW under axial compression experimentally and numerically [1]. Xing-Ping Shu, Huai-Bing Wang, Yi Li, Zhi-Shen Yuan and Ke Li studied the failure mechanism of
L-shaped SSCPW under axial compression by experiments and FE analysis [2].
-
ADVANTAGES OF STAINLESS-STEEL PLATED SHEAR WALL
-
An SPW system, when designed and detailed properly, has relatively large energy dissipation capability with stable hysteretic behaviour, thus being very attractive for high-risk earthquake zones.
-
Because the web tension field acts much like a diagonal brace, an SPW system has relatively high initial stiffness, and is thus very effective in limiting wind drift.
-
Compared to reinforced concrete shear walls, SPWs are much lighter, which ultimately reduces the demand on columns and foundations, and reduces the seismic load, which is proportional to the mass of the structure.
-
Compared to reinforced concrete construction, the erection process of an all-steel building is significantly faster, thus reducing the construction duration, which is an important factor affecting the overall cost of a project.
-
By using shop-welded, field-bolted SPWs, field inspection is improved and a high level of quality control can be achieved.
-
For architects, the increased versatility and space savings because of the smaller cross-section of SPWs, compared to reinforced concrete shear walls, is a distinct benefit, especially in high-rise buildings, where reinforced concrete shear walls in lower floors become very thick and occupy a large proportion of the floor plan.
-
All-steel construction with SPWs is a practical and efficient solution for cold regions where concrete construction may not be feasible, as very low temperatures complicate construction and freeze- thaw cycles can result in durability problems.
-
In seismic retrofit applications, SPWs are typically much easier and faster to install than reinforced concrete shear walls, which is a critical issue when building occupancy needs to be maintained throughout the construction time.
-
In the event of inelastic response, steel panels are more readily replaced, and repairs are otherwise simpler than for equivalent reinforced-concrete systems.
-
-
OBJECTIVES
-
To study under different connector types i.e., stud, truss type and combined stud and truss type.
-
To study different shapes of wall such as T- shaped, L-shaped, flat type rectangular wall.
-
To study different shapes of walls under eccentric loading to find out the bending performance.
-
To study different shapes of walls under axial loading to find out the load bearing capacity performance.
-
To study different shapes of walls under lateral loading to find out the lateral load resisting capacity.
-
-
-
METHODOLOGY
The stainless-steel plated shear wall is modelled with different shapes and using different connectors. The models are then studied under different loading conditions such as axial loading, eccentric and lateral loading along major and minor axis. The modelling and analysis are carried out using ANSYS software. Load bearing capacity, bending capacity and seismic capacity of SSPSW is evaluated.
2.2 ANSYS SOFTWARE- MODELLING AND ANALYSIS
ANSYS is an American Computer-aided engineering software which stands for Analysis of Systems. ANSYS publishes engineering analysis software across a range of disciplines including finite element analysis, structural analysis, computational fluid dynamics, explicit and implicit methods and heat transfer.
In this project, stainless steel plated shear wall with different connectors is modelled using Finite Element Software ANSYS. These models are studied under different loadings such as axial, eccentric and lateral loading.
Static structural analysis will be carried out for the analysis of project work. A static structural analysis determines the displacements, stresses, strains, and forces in structures or components caused by loads that do not induce significant
inertia and damping effects. Steady loading and response conditions are assumed; that is, the loads and the structure's response are assumed to vary slowly with respect to time. A static structural analysis can be either linear or non-linear. As per the ANSYS manual for software verification, following are the acceptance criteria:
Exact: There is no difference between the ANSYS results and the independent results.
Acceptable: For maximum load carrying capacity values, the difference between the ANSYS software and the independent results does not exceed fifteen percent (15%). Unacceptable: For maximum load carrying values, the difference between the ANSYS software and the independent results exceeds fifteen percent (15%).
3 MODELLING OF STAINLESS-STEEL PLATED SHEAR WALL
Stainless-steel plated shear walls are modelled using ANSYS software with different shapes and different connectors. In this project, three different shapes of stainless-steel plated shear wall are used for modelling. They are T-shaped, L-shaped and flat type rectangular wall. The different connectors used are stud, truss and combined stud and truss respectively.
The size of the wall is considered as scale down approach. So, the height and width of the wall is scale down into 3:1 ratio. The dimension details of stainless-steel plated shear wall are given in Table 1.1 respectively.
Parameters of specimen |
Dimension |
Height of wall |
1800mm |
Width of wall |
600mm |
Thickness of wall |
147mm |
Diameter of stud |
16mm |
Diameter of truss |
16 mm |
Table 3.1 Dimensional Details
-
MATERIAL PROPERTIES OF STEEL
Table 3.2 Material Properties
Properties
Value
Youngs Modulus
1.93 x 105 MPa
Poissons Ratio
0.3
Density
7850 kg/m3
Yield Strength
238 MPa
-
(b) (c)
Figure 3.1 Modelling of T-shaped stainless-steel plated shear wall using (a) stud as connector
-
truss as connector (c) combined stud & truss as connector
(a) (b) (c)
Figure 3.2 Modelling of L-shaped stainless-steel plated shear wall using stud as connector(b) truss as connector (c) combined stud & truss as connector
(a) (b) (c)
Figure 3.3 Modelling of flat type rectangular stainless-steel plated shear wall using (a) stud as connector (b) truss as connector (c) combined stud & truss as connector
-
-
MESHING The meshing is done as quadrilateral mesh which is an 8- noded mesh. Programme controlled coarse mesh is adopted for meshing.
-
(b) (c)
-
Figure 3.4 Meshing of T-shaped stainless-steel plated shear wall using (a) stud as connector (b) truss as connector (c) combined stud & truss as connector
-
(b) (c)
Figure 3.5 Meshing of L-shaped stainless-steel plated shear wall using (a) stud as connector (b) truss as connector (c) combined stud & truss as connector
-
(b) (c)
-
Figure 3.6 Meshing of flat type rectangular stainless-steel plated shear wall using (a) stud as connector (b) truss as connector (c) combined stud & truss as connector
-
ANALYSIS OF T-SHAPED, L-SHAPED AND FLAT TYPE RECTANGULAR STAINLESS STEEL PLATED SHEAR WALL UNDER AXIAL LOADING USING DIFFERENT CONNECTORS
In this, the analysis of T- shaped, L-shaped and flat type rectangular stainless steel plated shear wall using different connectors under axial loading. Nine models are created using ANSYS software. For each shape, three models are
created with three different types of connectors. The different connectors used are stud, truss and combined stud and truss type.
-
LOADING
The loading is given as displacement-controlled method till failure occurs. The boundary conditions of the finite element model are free at the upper end and fixed at the lower end. Loading is shown in fig. 4.1, fig. 4.2, fig. 4.3
-
(b) (c)
Figure 4.1 Loading of T-shaped stainless-steel plated shear wall using (a) stud as connector (b) truss as connector (c) combined stud & truss as connector
-
(b) (c)
Figure 4.2 Loading of L-shaped stainless-steel plated shear wall using (a) stud as connector (b) truss as connector (c) combined stud & truss as connector
-
(b) (c)
Figure 4.3 Loading of flat type rectangular stainless-steel plated shear wall using (a) stud as connector (b) truss as connector (c) combined stud & truss as connector
-
-
-
-
ANALYSIS
Analysis is carried out to study the performance of different shaped stainless steel plated shear wall under axial loading
using different connectors. Nonlinear static structural analysis is carried out in ANSYS software. Deformation and load carrying capacity is studied. The deformation diagrams are shown in following figures.
-
(b) (c)
Figure 4.4 Deformation diagram of T-shaped stainless-steel plated shear wall using (a) stud as connector (b) truss as connector (c) combined stud & truss as connector
(a) (b) (c)
Figure 4.5 Deformation diagram of L-shaped stainless-steel plated shear wall using (a) stud as connector (b) truss as connector (c) combined stud & truss as connector
(a) (b) (c)
Figure 4.6 Deformation diagram of flat type rectangular stainless-steel plated shear wall using (a) stud as connector (b) truss as connector (c) combined stud & truss as connector
The result obtained from the Nonlinear static structural analysis of different shaped stainless steel under axial compression using different connectors is compared each other. For that load deformation curve is taken for each model. The load and deflection obtained are compared. The
Table 5.2 shows the load and deflection of the Stainless-steel plated shear wall under axial loading by changing shapes and connectors and Fig.5.13 shows the comparison of load deflection curve.
Table 4.1 Comparison of Results
Models
Deformation (mm)
Load (kN)
T-ST-AX
11.412
1532.4
L-ST-AX
11.883
1520.4
F-ST-AX
12.498
2809.6
T-TR-AX
4.5191
3179.9
L-TR-AX
11.581
1665.7
F-TR-AX
4.3231
3075.5
Comb-T-TR-ST-AX
6.6173
2637.8
Comb-TR-ST-AX
10.383
1427
Comb-F-TR-ST-AX
1.4015
1138
Figure 4.7 Load- Deformation Curve
From figure 5.13 and table 5.2, it is observed that the range of load values varied from a minimum of 1138kN to a maximum of 3179.9kN on study of stainless-steel plated shear wall under axial loading by using different connectors. Flat type rectangular stainless-steel plated shear wall using combined stud and truss as connector shows less load carrying capacity i.e., 1138kN, when compared to other models. It indicates that it cannot perform effectively as a high strength stainless-steel plated shear wall. T-shaped stainless-steel plated shear wall using truss as connector shows more load carrying capacity when compared to other models. It signifies that it can perform effectively as a high strength stainless-steel plated shear wall in steel buildings.
-
-
-
ANALYSIS OF T- SHAPED, L-SHAPED AND FLAT TYPE RECTANGULAR STAINLESS STEEL PLATED SHEAR WALL UNDER ECCENTRIC LOADING ALONG X-AXIS USING DIFFERENT CONNECTORS
In this, the analysis of T- shaped, L-shaped and flat type rectangular stainless steel plated shear wall using different connectors under eccentric loading along x-axis. 100% eccentricity is provided. Nine models are created using ANSYS software. For each shae, three models are created with three different types of connectors. The different connectors used are stud, truss and combined stud and truss type.
-
LOADING
The loading is given as displacement-controlled method till failure occurs. The boundary conditions of the finite element model are free at the upper end and fixed at the lower end. Loading is shown in fig. 5.1, fig. 5.2, fig. 5.3
-
(b) (c)
Figure 5.1 Loading of T-shaped stainless-steel plated shear wall using (a) stud as connector (b) truss as connector (c) combined stud & truss as connector
(a) (b) (c)
Figure 5.2 Loading of L-shaped stainless-steel plated shear wall using (a) stud as connector (b) truss as connector (c) combined stud & truss as connector
(a) (b) (c)
Figure 5.3 Loading of flat type rectangular stainless-steel plated shear wall using (a) stud as connector (b) truss as connector (c) combined stud & truss as connector
-
-
ANALYSIS
Analysis is carried out to study the performance of different shaped stainless steel plated shear wall under eccentric loading along x-axis using different connectors. Nonlinear
static structural analysis is carried out in ANSYS software. Deformation and load carrying capacity is studied. The deformation diagrams are shown in following figures.
-
(b) (c)
Figure 5.4 Deformation diagram of T-shaped stainless-steel plated shear wall using (a) stud as connector (b) truss as connector (c) combined stud & truss as connector
(a) (b) (c)
Figure 5.5 Deformation diagram of L-shaped stainless-steel plated shear wall using (a) stud as connector (b) truss as connector (c) combined stud & truss as connector
(a) (b) (c)
Figure 5.6 Deformation diagram of flat type rectangular stainless-steel plated shear wall using (a) stud as connector (b) truss as connector (c) combined stud & truss as connector
The result obtained from the Nonlinear static structural analysis of different shaped stainless steel under eccentric loading along x-axis using different connectors is compared
each other. For that load deformation curve is taken for each model. The load and deflection obtained are compared. The Table 6.2 shows the load and deflection of the Stainless-steel
plated shear wall under axial loading by changing shapes and connectors and Fig.6.7 shows the comparison of load deflection curve
Table 5.1 Comparison of Results
Models
Deformation (mm)
Load (kN)
T-ST-E-X-300
12.243
1207.4
L-ST-E-X-300
14.303
1020.4
F-ST-E-X-73.5
43.152
1287
T-TR-E-X-300
12.188
1126.1
L-TR-E-X-300
13.573
1068
F-TR-E-X-73.5
47.013
1465.9
Comb-T-TR-ST-E-X-300
11.113
981.57
Comb-TR-ST-E-X-300
12.964
936.86
Comb-F-TR-ST-E-X-73.5
44.255
1355.9
Figure 5.7 Load-Deformation Curve
From figure 6.7 and table 6.2, it is observed that the range of load values varied from a minimum of 936.86kN to a maximum of 1465.9kN on study of stainless-steel plated shear wall under axial loading by using different connectors. L-shaped stainless-steel plated shear wall using combined stud and truss as connector shows less load carrying capacity i.e., 936.86kN, when compared to other models. It indicates that it cannot perform effectively as a high strength stainless- steel plated shear wall. Flat type rectangular stainless-steel plated shear wall using truss as connector shows more load carrying capacity when compared to other models. It signifies that it can perform effectively as a high strength stainless-steel plated shear wall in steel building.
-
-
-
ANALYSIS OF T- SHAPED, L-SHAPED AND FLAT TYPE RECTANGULAR STAINLESS STEEL PLATED SHEAR WALL UNDER ECCENTRIC LOADING ALONG Z-AXIS USING DIFFERENT CONNECTORS
This chapter deals with the analysis of T- shaped, L-shaped and flat type rectangular stainless steel plated shear wall
using different connectors under eccentric loading along z- axis. 100% eccentricity is provided. Nine models are created using ANSYS software. For each shape, three models are created with three different types of connectors. The different connectors used are stud, truss and combined stud and truss type.
-
LOADING
The loading is given as displacement-controlled method till failure occurs. The boundary conditions of the finite element model are free at the upper end and fixed at the lower end. Loading is shown in fig. 6.1, fig. 6.2, fig. 6.3
-
ANALYSIS
Analysis is carried out to study the performance of different shaped stainless steel plated shear wall under eccentric loading along z-axis using different connectors. Nonlinear static structural analysis is carried out in ANSYS software. Deformation and load carrying capacity is studied. The deformation diagrams are shown in following figures.
-
(b) (c)
Figure 6.1 Loading of T-shaped stainless-steel plated shear wall using (a) stud as connector (b) truss as connector (c) combined stud & truss as connector
(a) (b) (c)
Figure 6.2 Loading of L-shaped stainless-steel plated shear wall using (a) stud as connector (b) truss as connector (c) combined stud & truss as connector
(a) (b) (c)
Figure 6.3 Loading of flat type rectangular stainless-steel plated shear wall using (a) stud as connector (b) truss as connector (c) combined stud & truss as connector
(a) (b) (c)
Figure 6.4 Deformation diagram of T-shaped stainless-steel plated shear wall using (a) stud as connector (b) truss as connector (c) combined stud & truss as connector
-
(b) (c)
Figure 6.5 Deformation diagram of L-shaped stainless-steel plated shear wall using (a) stud as connector (b) truss as connector (c) combined stud & truss as connector
-
(b) (c)
-
Figure 6.6 Deformation diagram of flat type rectangular stainless-steel plated shear wall using (a) stud as connector (b) truss as connector (c) combined stud & truss as connector
The result obtained from the Nonlinear static structural analysis of different shaped stainless steel under eccentric loading along z-axis using different connectors is compared each other. For that load deformation curve is taken for each model. The load and deflection obtained are compared. The
Table 7.2 shows the load and deflection of the Stainless-steel plated shear wall under axial loading by changing shapes and connectors and Fig.7.7 shows the comparison of load deflection curve.
Table 6.1 Comparison of Results
Models
Deformation (mm)
Load (kN)
T-ST-E-Z-300
27.195
1483.8
L-ST-E-Z-300
16.974
927.98
F-ST-E-Z-300
11.618
1022.3
T-TR-E-Z-300
21.943
1089
L-TR-E-Z-300
17.79
699.91
F-TR-E-Z-300
9.8001
1098
Comb-T-TR-ST-E-Z-300
21.68
1049
Comb-TR-ST-E-Z-300
15.474
794.55
Comb-F-TR-ST-E-Z-300
12.952
1062
Figure 6.7 Load-Deformation Curve
From figure 7.7 and table 7.2, it is observed that the range of load values varied from a minimum of 699.91kN to a maximum of 1483.8kN on study of stainless-steel plated shear wall under axial loading by using different connectors. L-shaped stainless-steel plated shear wall using truss as connector shows less load carrying capacity i.e., 699.91kN, when compared to other models. It indicates that it cannot perform effectively as a high strength stainless-steel plated shear wall. T-shaped stainless-steel plated shear wall using stud as connector shows more load carrying capacity when compared to other models. It signifies that it can perform effectively as a high strength stainless-steel plated shear wall in steel building.
-
-
-
-
ANALYSIS OF T- SHAPED, L-SHAPED AND FLAT TYPE RECTANGULAR STAINLESS STEEL PLATED SHEAR WALL UNDER LATERAL LOADING ALONG X-AXIS USING DIFFERENT CONNECTORS
In this, the analysis of T- shaped, L-shaped and flat type rectangular stainless steel plated shear wall using different connectors under lateral loading along x-axis. 6% drift is provided. Nine models are created using ANSYS software. For each shape, three models are created with three different types of connectors. The different connectors used are stud, truss and combined stud and truss type.
-
LOADING
The loading is given as displacement-controlled method till failure occurs. The boundary conditions of the finite element model are free at the upper end and fixed at the lower end. Loading is shown in fig. 7.1, fig. 7.2, fig. 7.3
-
(b) (c)
Figure 7.1 Loading of T-shaped stainless-steel plated shear wall using (a) stud as connector (b) truss as connector (c) combined stud & truss as connector
(a) (b) (c)
Figure 7.2 Loading of L-shaped stainless-steel plated shear wall using (a) stud as connector (b) truss as connector (c) combined stud & truss as connector
(a) (b) (c)
Figure 7.3 Loading of flat type rectangular stainless-steel plated shear wall using (a) stud as connector (b) truss as connector (c) combined stud & truss as connector
-
-
ANALYSIS
Analysis is carried out to study the performance of different shaped stainless steel plated shear wall under lateral loading along x-axis using different connectors. Nonlinear static
structural analysis is carried out in ANSYS software. Deformation and load carrying capacity is studied. The deformation diagrams are shown in following figures.
-
(b) (c)
Figure 7.4 Deformation diagram of T-shaped stainless-steel plated shear wall using (a) stud as connector (b) truss as connector (c) combined stud & truss as connector
(a) (b) (c)
Figure 7.5 Deformation diagram of L-shaped stainless-steel plated shear wall using (a) stud as connector (b) truss as connector (c) combined stud & truss as connector
(a) (b) (c)
Figure 7.6 Deformation diagram of flat type rectangular stainless-steel plated shear wall using (a) stud as connector (b) truss as connector (c) combined stud & truss as connector
The result obtained from the Nonlinear static structural analysis of different shaped stainless steel under lateral loading along x-axis using different connectors is compared each other. For that load deformation curve is taken for each model. The load and deflection obtained are compared. The
Table 8.2 shows the load and deflection of the Stainless-steel plated shear wall under axial loading by changing shapes and connectors and Fig.8.7 shows the comparison of load deflection curve
Table 7.1 Comparison of results
Models
Deformation (mm)
Load (kN)
T-ST–LLX
11.247
324.35
L-ST-LL-X
11.497
226.49
F-ST-LL-X
58.675
151.34
T-TR-LL-X
10.598
297.29
L-TR-LL-X
14.614
294.82
F-TR-LL-X
54.238
166.54
Comb-T-TR-ST-LL-X
10.724
276.23
Comb-TR-ST-LL-X
15.865
277.92
Comb-F-TR-ST-LL-X
61.762
162.64
Figure 7.7 Load-Deformation Curve
From figure 8.7 and table 8.2, it is observed that the range of load values varied from a minimum of 151.34kN to a maximum of 324.35kN on study of stainless-steel plated shear wall under axial loading by using different connectors. Flat type rectangular stainless-steel plated shear wall using stud as connector shows less load carrying capacity i.e., 151.34kN, when compared to other models. It indicates that it cannot perform effectively as a high strength stainless- steel plated shear wall. T-shaped stainless-steel plated shear wall using stud as connector shows more load carrying capacity when compared to other models. It signifies that it can perform effectively as a high strength stainless-steel plated shear wall in steel building.
-
-
-
ANALYSIS OF T- SHAPED, L-SHAPED AND FLAT TYPE RECTANGULAR STAINLESS STEEL PLATED SHEAR WALL UNDER LATERAL LOADING ALONG Z-AXIS USING DIFFERENT CONNECTORS
In this, the analysis of T- shaped, L-shaped and flat type rectangular stainless steel plated shear wall using different connectors under lateral loading along z-axis. 6% drift is provided. Nine models are created using ANSYS software. For each shape, three models are created with three different types of connectors. The different connectors used are stud, truss and combined stud and truss type.
-
LOADING
The loading is given as displacement-controlled method till failure occurs. The boundary conditions of the finite element model are free at the upper end and fixed at the lower end. Loading is shown in fig. 8.1, fig. 8.2, fig. 8.3
-
ANALYSIS
Analysis is carried out to study the performance of different shaped stainless steel plated shear wall under lateral loading along z-axis using different connectors. Nonlinear static
structural analysis is carried out in ANSYS software. Deformation and load carrying capacity is studied. The deformation diagrams are shown in following figures.
-
(b) (c)
Figure 8.1 Loading of T-shaped stainless-steel plated shear wall using (a) stud as connector (b) truss as connector (c) combined stud & truss as connector
(a) (b) (c)
Figure 8.2 Loading of L-shaped stainless-steel plated shear wall using (a) stud as connector (b) truss as connector (c) combined stud & truss as connector
(a) (b) (c)
Figure 8.3 Loading of flat type rectangular stainless-steel plated shear wall using (a) stud as connector (b) truss as connector (c) combined stud & truss as connector
(a) (b) (c)
Figure 8.4 Deformation diagram of T-shaped stainless-steel plated shear wall using (a) stud as connector (b) truss as connector (c) combined stud & truss as connector
(a) (b) (c)
Figure 8.5 Deformation diagram of L-shaped stainless-steel plated shear wall using (a) stud as connector (b) truss as connector (c) combined stud & truss as connector
(a) (b) (c)
Figure 8.6 Deformation diagram of flat type rectangular stainless-steel plated shear wall using (a) stud as connector (b) truss as connector (c) combined stud & truss as connector
The result obtained from the Nonlinear static structural analysis of different shaped stainless steel under lateral loading along z-axis using different connectors is compared each other. For that load deformation curve is taken for each model. The load and deflection obtained are compared. The
Table 9.2 shows the load and deflection of the Stainless-steel plated shear wall under axial loading by changing shapes and connectors and Fig.9.7 shows the comparison of load deflection curve.
Table 8.1 Comparison of Results
Models
Deformation (mm)
Load (kN)
T-ST-LL-Z
38.046
307.27
L-ST-LL-Z
56.503
361.27
F-ST-LL-Z
8.993
553.6
T-TR-LL-Z
26.886
278.27
L-TR-LL-Z
42.045
354.15
F-TR-LL-Z
10.017
594.98
Comb-T-TR-ST-LL-Z
18.095
221.47
Comb-TR-ST-LL-Z
38.538
340.43
Comb-F-TR-ST-LL-Z
10.91
543.85
Figure 8.7 Load-Deformation Curve
From figure 9.7 and table 9.2, it is observed that the range of load values varied from a minimum of 221.47kN to a maximum of 594.98kN on study of stainless-steel plated
shear wall under axial loading by using different connectors. T-shaped stainless-steel plated shear wall using combined stud and truss as connector shows less load carrying capacity
-
., 221.47kN, when compared to other models. It indicates that it cannot perform effectively as a high strength stainless- steel plated shear wall. Flat type rectangular stainless-steel plated shear wall using truss as connector shows more load carrying capacity when compared to other models. It signifies that it can perform effectively as a high strength stainless-steel plated shear wall in steel buildings.
-
-
-
-
CONCLUSION
Stainless-steel plated shear walls with different shapes are modelled by using different connectors such as stud, truss and combined stud and truss and analyzed under different loading conditions such as axial, eccentric and lateral loading along major and minor axis. The comparison of stainless-steel plated shear walls is studied. The following conclusions are obtained:
-
From the study it is observed that the use of stainless steel plates increases the stiffness of the structure
-
From the study of axial loading case, it is observed that the range of load values varied from a minimum of 1138kN to a maximum of 3179 kN on studies of use of different connectors.
-
T- shaped stainless steel plated shear wall connected by truss performed effectively while providing axial load.
-
From the study of eccentric loading along x- axis, it is observed that the range of load values varied from a minimum of 936kN to a maximum of 1465kN on studies of use of different connectors.
-
Flat type rectangular wall connected by truss showed effective performance while providing eccentric loading along x-axis.
-
From the study of eccentric loading along z- axis, it is observed that the range of load values varied from a minimum of 699kN to a maximum of 1483kN on studies of use of different connectors.
-
T- shaped stainless steel plated shear wall connected by stud showed good performance while providing eccentric loading along z-axis.
-
From the study of lateral loading along x- axis, it is observed that the range of load values varied from a minimum of 151kN to a maximum of 324kN on studies of use of different connectors.
-
T- shaped stainless steel plated shear wall connected by stud performed effectively while providing lateral loading along x-axis.
-
From the study of lateral loading along z- axis, it is observed that the range of load values varied from a minimum of 221kN to a maximum of 594.98kN on studies of use of different connectors.
-
Flat type rectangular wall connected by truss showed effective performance while providing lateral loading along z-axis.
-
It can be concluded that T-shaped stainless steel plated shear wall connected by truss shows the better performance when compared to all models studied under different loading condition and different connectors.
REFERENCES
[1] Xing-Ping Shu et.al. (2021) Strength design of T-shaped stainless steel core plate wall under axial compression, Journal of Constructional Steel Research, P-106891 [2] Xing-Ping Shu et.al. (2021) Study on the bearing resistance of axially compressed L-shaped stainless steel core plate wall based on the stability loss, Journal of Engineering Structures, P-113264 [3] Ke Wang et.al. (2021) Seismic Analysis and Design of Composite Shear Wall with Stiffened Steel Plate and Infilled Concrete, Materials, volume 15, 182 [4] Jing-Shen Zhu et.al. (2020) Seismic performance of concrete- infilled double steel corrugated-plate walls: Experimental research, Journal of Engineering Structures, P- 110601 [5] Hongbo Li et.al. (2020) Axial Compression Performance and Ultrasonic Testing of Multicavity Concrete-Filled Steel Tube Shear Wall under Axial Load, Hindawi Advances in Civil Engineering, Volume 2020, Article ID 8877282, https://doi.org/10.1155/2020/8877282 [6] Meng-Zheng Wang et.al. (2019) Sectional strength design of concrete infilled double steel corrugated plate walls with T- shaped, Journal of Constructional Steel Research, PP-2344 [7] Jing-Shen Zhu et.al. (2019) Strength design of concrete-infilled double steel corrugated-plate walls under uniform compressions,Journal of Thin-Walled Structures, P-153174
[8] Lihua Chen et.al. (2019) Seismic behavior of double-skin composite wall with L-shaped and C-shaped connectors, Journal of Constructional Steel Research, PP- 255270 [9] Jing-Zhong Tong et.al. (2018) Shear resistance of stiffened steel corrugated shear walls, Journal of Thin-Walled Structures, PP-76- 89 [10] Anjana R K Unnithan et.al. (2017) Design and analysis of high rise Building with steel plate shear wall, International Journal of Civil Engineering and Technology (IJCIET), Volume 8, Issue 4,April 2017, pp. 1012-1025
[11] Xin Qian et.al. (2016) Development of a high-performance steel plate shear wall system, International Journal of Earthquake and Impact Engineering (IJEIE), PP-57-80 [12] Pundkar R. S et.al. (2013) Influence of Steel Plate Shear Wall on Multistorey Steel Building, International Journal of Engineering Research and Applications (IJERA), Vol. 3, Issue 4, PP-.1940- 1945