
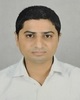
- Open Access
- Authors : Indrajitsinh J. Jadeja , Dr. Nirav P. Maniar
- Paper ID : IJERTV11IS070129
- Volume & Issue : Volume 11, Issue 07 (July 2022)
- Published (First Online): 26-07-2022
- ISSN (Online) : 2278-0181
- Publisher Name : IJERT
- License:
This work is licensed under a Creative Commons Attribution 4.0 International License
A Computer Aided Manufacturing Approach to Developed A Micro-Mechanism
Mr. Indrajitsinh J. Jadeja
Ph.d Scholar,
Gujarat Technological University, Chandkheda, Gandhinagar, Gujarat,
Dr. Nirav P. Maniar
Associate Professor,
-
Engineering College Rajkot , Gujarat, India
Abstract Computer-aided design tools for micro-mechanisms that help designers validate correct function, detect design flaws, and assess the effects of part clearances. The domain characteristics of curved geometry, joint play, and higher pairs render traditional software inappropriate. For the purpose of computer aided micro mechanism software uses configuration spaces to model the kinematic function of micro-mechanisms. It uses the configuration spaces to perform real-time simulation, to compute functional kinematic tolerances, and to support parametric design. Designers can visualize system function under a range of operating conditions, can find and correct design flaws, and can optimize dynamical function. Through the medium of this seminar I will demonstrated on a surface micro machined with help of a two case study which are to be developed through the software of computer aided micro-mechanism
KeywordsVLSI, LIGA, CAD, CAM
-
INTRODUCTION
The micro mechanism is a challenging field of engineering, in which mechanical, electrical, and material Technologies are integrated together. There are several computer-aided design systems to support the designer to explore this new field,
The computer-aided design tools for micro-mechanisms. Recent advances in fabrication technology make possible the synthesis of complex micro mechanisms, such as gears, ratchets, and transmissions. Designers need to analyses candidate micro-mechanisms to validate correct function, to detect design flaws, and to assess the effects of part clearances. Traditional computer aided design software is inappropriate for these tasks. VLSI design software is not meant for moving parts. Finite element analysis is difficult and slow due to the large number of parts, the curved geometry, and the many part contact changes. It is computational overkill for designs that can be modelled as rigid-body systems. Mechanical system simulators offer an efficient alternative to finite element codes, but are limited to systems with permanent part contacts, such as pin joints, prismatic joints, and involutes gears.
These conditions are unrealistic for micro-mechanisms because the fabrication process cannot produce ideal joints and because changing contacts play a major role in micro design. We have developed an interactive computer-aided design program, called HIPAIR that supports micro-mechanism design. HIPAIR automates kinematic analysis via a novel configuration space computation code, performs fast dynamical simulation, computes worst-case and statistical kinematic tolerances, and supports functional parametric design. Designers can visualize system function under a range of operating conditions, can find and correct design flaws, and can optimize dynamical function. HIPAIR handles planar
systems of curved, rigid parts with custom pairs, open and closed kinematic chains, and contact changes.
The central idea of these systems is the use of computer simulation. Their common goal is to perform calculation of geometrical and material properties from the information of fabrication processes, or to simulate electrical and mechanical behaviors. Since the behavior of a micromechanism can be complex and different from a mechanism of an ordinal size, their approach is obviously of great importance for the micromechanism design.
In this developing field, however, there are a lot of potential possibilities to create novel concepts. To investigate a new concept, it is crucial to search for alternative design principles and evaluate in various aspects. To make an approach to the support of this design process, we study the role of design knowledge. The approach may be called a knowledge cantered approach, in contrast to the simulation centred approach. The knowledge centred approach includes providing knowledge bases for reasoning about the design object. In a broader sense, it also aims at supporting a team of designers to share knowledge in various formats, including documents, models, and computer programs that contain knowledge in the algorithms.
-
MICRO-MECHANISM FABRICATION Fabrication technologies for micro-electro-mechanical systems can be broadly categorized into three groups: bulk micro-machining, LIGA, and surface micro-machining. Bulk micro-machining technologies make use of the differential etch rates between crystal planes of a bulk material, such as single crystal silicon. These techniques can create high aspect- ratio geometry that is useful as seismic mass, diaphragms, or vibrating elements in inertial or pressure sensors. LIGA is a micro-machining process that can form high aspect-ratio metallic parts with small features. LIGA processes involve making molds using lithographic patterning and etching. The molds are used in electro-plating processes to form the individual parts. Surface micro-machining uses the same tool set as the semiconductor industry, which enables high volume batch fabrication, integration with microelectronics, and definition of mechanical parts with small feature size. Surface micro-machining fabrication involves the repeated deposition, patterning and etching of materials such as poly crystalline silicon (polysilicon), silicon dioxide, and silicon nitride. Most fabrication methods use polysilicon as the mechanical structural material, silicon dioxide as the sacrificial material removed at the end of the process to release the mechanical layers, and silicon nitride as an electrical insulating layer.
Surface micro-machining is the only process that can batch fabricate a system. Bulk and LIGA processes produce components that need further assembly, which is very difficult at these scales.
The Sandia Summit process is a surface micromachining process that can fabricate micro- mechanical devices with four mechanical layers, uses silicon nitride as ground plane isolation, and used silicon dioxide as the sacrificial material. Figure 1 is a schematic cross-section of a pinion gear that has a hub and a pin-joint connection to a linkage.
Figure 1. Pinion Gear Cross Section
The shape of the mechanical elements is defined via lithography. The retile for this part is shown at the top of the figure. The colour of the closed contours indicates their mechanical levels. The minimum feature size is dictated by the line width/space limitations of the lithography process, which is 1 micron for the Summit process. The formation of a hub and pin-joint is a key element of the process to facilitate the fabrication of movable mechanical linkages. A 0.5 micron layer of sacrificial oxide is used to define the spacing in the hub and pin-joint..
Surface micro-machining enables the fabrication of complex mechanical elements, which has been demonstrated for a number of applications. However, it raises design issues that are different from traditional mechanical design. Since surface micromachining is a batch fabrication method, the mechanical elements must be fabricated in place, which subjects their clearances and tolerances to the limitations of the fabrication process. The clearance and tolerance effects are of three categories: line width/space rules of the lithography, sacrificial oxide space in the hub and pin-joint, and size tolerance (one sided) of the mechanical elements due to release processing.
-
ABOUT HIPAIR
We are eveloping a unified approach to computer-aided mechanical assembly design in which all design tasks are performed within a single computational paradigm supported by integrated design software. Mechanical assembly design is the task of devising an assembly of parts that performs a function reliably and economically. It is a ubiquitous activity that spans mechanical, electrical, and biomedical engineering. Designers need to devise, analyze, and compare competing design prototypes to produce optimal designs. Computer-aided design reduces design time and improves quality by allowing
designers to substitute electronic prototypes for physical prototypes in diverse tasks.
We have developed a prototype design environment called HIPAIR for general planar assemblies. The environment supports the key design tasks of simulation, parametric design, and functional tolerance for a broad range of mechanical assemblies, such as camera shutter mechanisms, part feeders, robotic arms, and knee prostheses. HIPAIR organizes the design tasks around the fundamental task of contact analysis, which we automate by configuration space computation. Configuration space is a complete, concise, and explicit representation of rigid body interactions and contains the requisite information for design tasks involving contacts. HIPAIR allows designers to perform computations that lie outside the scope of previous software and that defy manual analysis. It allows them to visualize assembly function under a range of operating conditions, to find and correct design flaws, and to evaluate the functional effects of part tolerances. It has been tested on hundreds of pairs and on a dozen assemblies. HIPAIR performs at interactive speed on assemblies of ten parts with tens of thousands of contacts.
We are expanding this approach to selected spatial assemblies and to other design tasks, such as tolerance assembly planning, validation, and parametric design. We plan to integrate HIPAIR with existing CAD systems and to validate it with practicing engineers on real design examples. This research should lead to a better understanding of mechanical design and pave the way for the next generation of rapid prototyping tools that will help industry reduce design time and increase product quality.
-
GEAR DISCRIMINATION DEVICE
A surface micro- machined counter meshing gear discrimination device in Figure 2. The mechanism is a lock based on gears and ratchets. We will focus on the function of the indexing assembly. The pinion and gear rotate on fixed axes, the pawl is attached to the frame by an L-shaped spring, and the anchor is fixed to the frame. The designer intends for the pinion to rotate clockwise and to advance the gear by one tooth per rotation. Counter-clockwise rotation is prevented by the pawls blocking against the anchor. Clockwise rotation is limited to one tooth per cycle by the damping effect of the strut, which bends as the pawl follows the gear profile
Figure 2. Photograph of surface micro-machined counter-meshing gear discriminator
Figure 3. Detail of indexing assembly CAD model
-
CONFIGURATION SPACE
-
We represent the kinematic function of the micromechanism with configuration spaces [2, 1]. We work with the configuration spaces of pairs of planar parts. Configuration space is a parameter space whose points specify the spatial configuration (position and orientation) of the parts. The part geometry is encoded by partitioning the configurations into three disjoint classes: blocked space where the parts overlap, free space where they do not touch, and contact space where they touch without overlap. Blocked space represents the illegal configurations, free space represents the independent part motions, and contact space represents motion constraints induced by part contacts. The spaces have useful topological properties. Free and blocked space are open sets whose common boundary is contact space. Contact space is a closed set comprised of algebraic patches that represent contacts between part features.
We illustrate these concepts on the gear/pinion pair of the indexing assembly (Figure 4). We assume for the moment that the joints have no play, hence that each part has one, rotational degree of freedom. The configuration space coordinates are the part orientations. Free space is white, blocked space is grey, and contact space is black. Contact space consists of many short contact curves that represent contacts between the pinion and the gear teeth (more precisely, between the geometric features that form the parts). The left part of the configuration space consists of narrow, slanted channels in which the part motions are coupled. As the pinion rotates clockwise, the configuration moves horizontally left until it reaches the nearest channel boundary then follows the boundary up, meaning that the gear rotates counter-clockwise. The right part of the configuration space represents the rotation of the pinion from when it exits the channel on the left (breaks contact with the gear) until it reaches the right side of the channel above.
FIGURE 4. GEAR/PINION CONFIGURATION SPACE
This analysis ignores a crucial aspect of micro fabrication: the
-
micron play in every joint. This means that the pinion and the gear each has three degrees of freedom: one micron of horizontal translation relative to its hub, one micron of vertical translation, and unrestricted rotation. We need three- dimensional configuration spaces to model this situation. The configuration space coordinates are the position (u; v) and orientation of the gear relative to the pinion. Figure 5 shows 1/64 of the gear/pinion configuration space. The shaded surface is contact space, the exterior is free space, and the interior is blocked space. Each of the 3664 contact patches are shaded a different colour. Although this figure is extremely complicated, we can derive a complete kinematic analysis from it.
Figure 5. Gear / pinion configuration space with play Design tools
We can validate the indexing assembly function with HIPAIR through kinematic analysis of the interacting pairs, simulation, and visualization. We illustrate this process on the gear/pinion pair. The first step is to check the configuration space for correct kinematic function. The desired function is that the pinion advance the gear by one tooth per cycle. The contact space shape is consistent with this function. As the pinion rotates, the configuration enters a channel (engagement), follows it (coupled motion), and exits (disengagement) after one gear tooth. Kinematic simulation provides an alternative way of studying kinematic function.
We use HIPAIR to compute the gear motion induced by constant, clockwise rotation of the pinion. The simulator
computes part motions due to contacts, but ignores dynamical effects, such as friction and inertia. We can animate the simulation to validate the kinematic function or can examine the motion path in configuration space. The next step is to assess the effects of joint play on the function.
We start by examining cross-sections of the configuration space, which quantify the play in key part orientations (Figure 6).
(a)
(b)
Figure 6. Cross section of three dimensions Gear Pinion configuration space
-
Disengaged (b) Engaged
-
The circles mark the range of motion due to joint play. The part play is too small to cause unintended contacts. In the disengaged orientation, the circle lies in free space, which rules out other contacts that could cause chatter, vibration, and wear. In the engaged configuration, the circle centre lies on the nominal contact curve and the circle does not intersect any other contact curves, which rules out backlash and jamming. The next steps are to evaluate the mechanism dynamics via simulation and to study the functional effects of part tolerances. Although we omit these steps for lack of space, they are supported by HIPAIR.
-
TORSIONALRATCHETING ACTUATOR
Figure 7 shows the original torsional ratcheting actuator. The mechanism consists of a driver, a ratchet, a ring gear, and an anti-reverse. The gear and the anti-reverse are mounted on the substrate with pin joints, while the ratchet is attached to the driver with a pin joint. (These are really flexures; pin joints are an accurate, simple approximation.) The driver is attached to the substrate by springs that allow planar rotation, but prevent translation. The driver is rotated 2.5 counter clockwise by an electrostatic comb drive. The ratchet engages the inner teeth of the gear and rotates it counter clockwise. When the voltage drops, the springs restore the driver to its start orientation, which disengages the ratchet. The anti-reverse prevents the gear from rotating clockwise. Its outer, involutes teeth drive an external load.
Figure 7. Torsional ratcheting actuator
The main purpose of the redesign is to ensure that the gear advances by one tooth per cycle. The
Original design exhibits overrun where the ratchet/gear impact causes the gear to jump two or more teeth. An anti-overrun and a riser were added to the design to prevent this. A second goal is to ensure correct function despite gear hub play, which is estimated at 0.5 microns. A third goal is to optimize performance factors, including voltage, power, wear, and area. This paper addresses the first two goals, which mostly involve the kinematic function of the mechanism.
Figure 8.Simulation of Modified Design
Figure 8 illustrates the modified design. The riser is fixed to the substrate and the anti-overrun is attached to the driver with a pin joint. It is rotated 2.375°counterclockwise by the
electrostatic comb drive (ac). The ratchet rotates with the driver, engages the inner teeth of the gear (b), and rotates it counter clockwise (c). The anti-overrun rotates with the driver, rides over the riser (b), engages the gear (c), and prevents further gear motion. When the voltage drops, torsional springs restore the drive wheel to its start orientation, which disengages the ratchet and the anti-overrun (de). As before, the anti-reverse prevents the gear from rotating clockwise.
-
CONFIGURATION SPACE
Kinematic analysis is performed by constructing configuration spaces for the interacting pairs of parts. These spaces encode the part interactions in a uniform geometric format that supports function validation, simulation, tolerance, and synthesis. The configuration space of a pair is a manifold with one coordinate per part degree of freedom. A general planar pair has a three-dimensional configuration space whose coordinates are the position and orientation of one part relative to the other. A pair of rotating parts can be modelled with a simpler, two-dimensional space whose coordinates are the part orientation angles. Although our program handles both cases, we will discuss only the simpler case.
Figure 9.Gear/anti-reverse configuration Space.
Figure 9 shows the gear/anti-reverse configuration space. The coordinates are the gear orientation and the ant reverse orientation in degrees. The dot marks the displayed configuration where the parts are engaged. The part contacts are encoded by partitioning configuration space into three disjoint classes: blocked space (grey) where the parts overlap, free space (white) where they do not touch, and contact space (black) where they touch without overlap. Blocked space represents the illegal configurations, free space represents the independent part motions, and contact space represents motion constraints induced by part contacts. Contact space consists of many short contact curves that represent contacts between pairs of part features (points, line segments, and arcs).
The displayed configuration lies at the meeting point of two contact curves. The configuration space shows that the pair functions correctly. The slanted contact curve to the right of the displayed configuration represents the contact between the long side of a gear tooth and the top of the anti-reverse. If the gear rotates counter clockwise (increases), this contact causes the ant reverse to rotate counter clockwise (increases), as the configuration of the pair follows the contact curve. The near vertical contact curves to the left of the displayed configuration represents the contact between the short side of a gear tooth and the side of the anti-reverse. This contact prevents the gear from rotating clockwise, since every direction in which decreases like in blocked space.
The gear/ratchet pair has a three-dimensional configuration space because the ratchet rotates around a rotating point, hence has three degrees of freedom. The interactions are invariant
when both parts are rotated by the same angle, so we can analyse the pair in a two-dimensional space whose coordinates are the angle between the parts and the ratchet orientation. Equivalently, we freeze the driver at zero degrees, which also freezes the ratchet centre of rotation.
Figure 10.Gear ratchet Configuration Space
Figure 10 shows the configuration space. The coordinates are the gear orientation and the ratchet orientation the dot marks the displayed configuration where the ratchet is driving the gear. The near vertical contact curve to the left represents the contact between the short side of a gear tooth and the ratchet tip, which prevents the gear from rotating clockwise relative to the driver. The configuration space reveals a design flaw: the curve slope is positive (and very large), which implies that the gear can rotate clockwise, escape the ratchet, and jump to the next tooth. Friction will prevent this until the driver torque reaches a critical value. Load variation and hub play can exacerbate the problem.
-
SIMULATION
Configuration space analysis reveals the kinematic constraints due to contacts among the parts of the actuator. We combine this analysis with rigid body simulation to predict the system function. Kinematic analysis is a prerequisite for simulation because contacts create forces that effect part motion.
We have developed a simulator that computes the configuration spaces of the interacting pairs before the simulation and queries them at each time step for part collisions and contact changes.
When these occur, the simulator backs up to the change time and updates the contact equations. Running on a personal computer, the simulator handles systems with tens of moving parts at interactive speeds.
It generated the simulation shown in Figure 8, which validates the initial nominal design. It also validated the revised design described below.
-
TOLERANCE ANALYSIS
Our analysis ignores shape variation and hub play. The dominant factor is gear hub play, which is estimated at 0.5 microns. Flexures have minimal play and shape variations are negligible in the Summit V process. We model the gear hub play by parameter zing the centre of rotation and allowing Each choice of parameter values generates a different part with its own gear/ratchet, gear/anti-reverse, and gear/ant overrun configuration spaces. We compute zones around the nominal contact spaces, called contact zones that bound their worst- case variation.
Figure 11.Gear/Ratchet Contact zone
Figure 11 shows the gear/ratchet contact zone, which is displayed as light bands around the contact curves. The contact curves are guaranteed to lie in the zone whenever the parameters lie in the specified interval. The gear/ratchet contact zone shows that hub play can cause incorrect function. The near vertical curve, which is meant to prevent jumping, can slope to the left without leaving the contact zone. The gear will then be able to rotate clockwise and jump. The gear/anti- reverse and gear/ant overrun contact zones show correct function despite hub play. Each choice of parameter values generates a different part with its own gear/ratchet, gear/anti- reverse, and gear/antioverrun configuration spaces. We compute zones around the nominal contactspaces, called contact zones that bound their worst-case variation. Figure 11 shows the gear/ratchet contact zone, which is displayed as light bands around the contact curves. The contact curves are guaranteed to lie in the zone whenever the parameters lie in the specified interval.
The gear/ratchet contact zone shows that hub play can cause incorrect function. The near vertical curve, which is meant to prevent jumping, can slope to the left without leaving the contact zone. The gear will then be able to rotate clockwise and jump. The gear/anti-reverse and gear/antioverrun contact zones show correct function despite hub play.
Figure 12.Modified Gear Configuration Space
We modified the gear/ratchet pair to prevent jumping, using our interactive kinematic synthesis program. We specified the kinematic changes by mapping nominal contact configurations to desired configurations. In Figure 10, the nominal configurations are the base points of the two arrows and the desired configurations are the arrow heads. The program modifies the design parameters to achieve the changes, while preventing unintended changes. Figure 12 shows the modified pair. The gear tooth slope and the matching ratchet slope are larger. In configuration space, the near horizontal contact has
rotated enough that its slope is negative, and stays negative despite hub play. The gear/ratchet modifications alter the kinematics of the other pairs. We validated the entire mechanism via configuration space computation, simulation, and tolerance analysis.
-
CONCLUSION
Here, represented a configuration space method of Kinematic analysis, tolerance and synthesis with the use of two case studies. Demonstrate a efficiency and implementation on the design of micro mechanism fabrication using this above mention procedure. Where VLSI technology is not useful for simulation and analysis for micromechanism fabrication component, on that point the technology of Computer aided Micromechanism by the use of configuration space model techniques and it will give the ideal validate design and its mechanism. It is also to minimize the effort for prototyping and design time.
REFRENCES
[1] Sacks, E. and Joskowicz, L. Dynamical simulation of planar systems with changing contacts using configuration spaces. Journal of Mechanical Design (2001). to appear. [2] Senturia, S.D.: CAD for Microelectromecanical Systems, Solid-State Sensors and Actuators, pp.5-8, (1998). [3] Polosky, M. A., Garcia, E. J., and Allen, J. J. Surface micro machined counter-meshing gears discrimination device. in: Proc. SPIE Smart Electronics and MEMS, San Diego, CA, (1998). [4] L.joskowicz and E.sacks Computer Aided Mechanical Design using configuration space, tech report,(1998)