
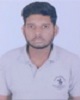
- Open Access
- Authors : Vasu. V. S , Dr. Shanmuganathan, S. P
- Paper ID : IJERTV11IS080001
- Volume & Issue : Volume 11, Issue 08 (August 2022)
- Published (First Online): 06-08-2022
- ISSN (Online) : 2278-0181
- Publisher Name : IJERT
- License:
This work is licensed under a Creative Commons Attribution 4.0 International License
Finite Element Modelling and Numerical Simulation of Transient Temperature in Friction Stir Welding of AA 6061 and AA 7075 Alloys
Vasu. V. S, Dr. Shanmuganathan. S.P Department of Mechanical Engineering, Dayananda Sagar College of Engineering, Bengaluru-560078
Abstract:- One method of solid-state joining is friction stir welding (FSW). Because of its distinctive qualities, such as the high-speed nature of the joints, the friction stir welding technique has drawn a lot of attention. Heat is one of the crucial components in FSW that is produced as a result of friction between the tool and the work piece.
A basic aspect of friction stir welding is the creation and dispersion of heat. Temperature measurement in the stir zone is challenging because of the stringy materials. We can determine the temperature in the stir zone with the aid of numerical simulation. In the current work, a three- dimensional coupled thermo-mechanical finite element model in the Abaqus Dynamic Explicit software is used to simulate numerical results on temperature distribution over the weld zone in friction stir welding of AA 6061 and AA 7075 aluminium alloys.
-
INTRODUCTION
Aluminium alloys used in aircraft typically have low weldability when using the conventional fusion welding method. The advancement of friction stir welding has given producers of aluminium joints an improved alternative that is quicker and more dependable. Due to their low melting temperatures, these alloys are, however, difficult to combine using fusion welding procedures. Additionally, during fusion welding, flaws including porosity deformation, oxidation, shrinkage, and etc are seen. FSW has developed as an alternative to fusion welding processes in order to solve these challenges.
The heat produced at the point where the tool and workpiece first contact is one of the crucial components in the FSW process. This heat is what propels the FSW process forward. The heat flux must maintain the workpiece's maximum temperature at a level that allows the material to be soft enough for the pin to stir without melting. According to Tang et al. and Colegrove et al., the maximum temperature produced by the FSW process ranges from 80% to 90% of the melting temperature of the welding material, thereby minimising or avoiding welding defects and significant distortion that are frequently associated with fusion welding.
During FSW, frictional heatwhich is produced when the tool slides over the workpiecewas seen as a significant
heat source. Chao et al.[12] created a 3-D thermal and thermal-mechanical FEM model for FSW while only taking into account frictional heat as the heat source. However, a parameter termed slip rate (), which ranges from 0 to 1, was established by H.B. Schmidt et al.[17] to create contact conditions between the tool and work piece. If the slip rate is zero, the contact state is sliding and heat is only produced by friction; on the other hand, if it is one, the contact situation is sticking and heat is only produced by shear deformation. The deformation and frictional heat produced during the stirring process in FSW are directly proportional to heat generation.
Li & Liu, [18] employed an external heat source for the heat generation from tool movement instead of heat generation by friction or plastic deformation. Frictional contact heat and plastic deformational heat were regarded as heat sources in the modelling friction stir welding. They claimed that the temperature-dependent heat transfer coefficient and contact pressure greatly impact the thermal analysis. A two-dimensional solid mechanical FE model using ABAQUS Explicit and a two-dimensional CFD model using Fluent were both introduced by Reynolds et al. with the primary goal of revealing the material flow around the probe.
We provide the results of our investigation into the heat distribution during the FSW process for both the workpiece and the tool in the current publication. The FSW was used to attach plates made of the aluminium alloys AA6061 and AA7075. This study examines the temperature distribution in FSW to ascertain whether tool motion toward the plate edge causes heat to vary or tool motion away from the plate edge.
Using the finite element programme Abaqus Dynamic Explicit, a 3D model was created to analyse temperature distribution during friction stir welding. For the workpiece and the tool in this model, an 8-node thermally connected brick solid element C3D8RT was used due to its large deflection, stress stiffness, and plasticity properties.
Fig 1. (Schematic view of the model.)
2. Experimentation
Friction stir welding was carried out by joining two AA6061-AA7075 plates together and having dimensions L x B x H =150 x 100 x 6.35 each as shown in Fig.1. The proposed model consists of deformable plates which are AA6061- 7075 and an AISI HSS M2 rigid tool.
For meshing purposes, the eight-node coupled temperature displacement
brick element (C3D8RT) was used to discretize the aluminium plate. The element can compute displacement and temperature in x-, y-, and z-directions and produce uniform strain, in addition to using the hourglass control feature ABAQUS/EXPLICIT. A total of 42,625 elements were used to mesh the workpiece.
In terms of material behaviour, the elastoplastic Johnson- Cook model was used to compute the flow stress as outlined by Jorgensen and Swan. This was done in accordance with a temperature and strain rate-dependent material law.
Table1. Johnson-Cook material constraints
In the present simulation, both tool rotation speed (900 rev/min) and traverse speed (0.5 mm/s) were applied to the tool reference point, while the workpiece plate was constrained at the bottom and sides. The traverse welding speed in ABAQUS was determined by a series of values at specific times in time to prevent instability effects brought on by the welding tool's lateral motion at the start of the moving phase.
Three simulations with different tool dimensions were simulated using this method. Three tool dimensions are
1Tool Parameters (Square Tool)
-
Length= 5mm, Depth= 5.8mm.
-
Shoulder Dia of the tool= 21mm, Height of the Shoulder= 15mm.
-
Shank Dia= 20mm, Height of the shank= 50mm.
2 Tool Parameters (M6 Threaded Cylindrical Tool)
-
Length= 5mm, Depth= 5.8mm.
-
Shoulder Dia of the tool= 21mm, Height of the Shoulder= 15mm.
-
Shank Dia= 20mm, Height of the shank= 50mm.
3 Tool Parameters (Cylindrical Tool)
-
Length= 5mm, Depth= 5.8mm.
-
Shoulder Dia of the tool= 21mm, Height of the Shoulder= 15mm.
-
Shank Dia= 20mm, Height of the shank= 50mm.
Fig 2
The Coulomb's friction law, which has a nonlinear friction value that fluctuates with regard to the temperature at that zone, was applied to the aluminium workpiece and welding tool to satisfy the friction. The simulation used a maximum equivalent shear stress condition to simulate the sliding problem. According to the condition, the sliding scenario will be satisfied regardless of the magnitude of the contact pressure stress if the equivalent shear stress value reaches its maximum value.
-
RESULTS AND DISCUSSION
The current finite element model offers the opportunity to assess FSW process outcomes, such as temperature, stresses, plastic strain, plunge force, and heat generation, over the course of the three dissimilar friction stir welding steps of AA 7075-T651 and throughout the entire region of the welded structure. As stated above, the lunging, living, and traversing steps of the FSW method used the ABAQUS/EXPLICIT software to model heat transport.
Fig 3.1
Fig 3.2
Fig 3.3
Fig 3.4
Fig 3.5
The figures (3.1, 3.2, 3.3, 3.4, 3.5) shown above are taken at different time instances during the friction stir welding simulation in Abaqus Dynamic Explicit.
The ABAQUS/EXPLICIT software package was used in the current work to build the thermo mechanical model for friction stir welding. In the current work, it is assumed that the aluminium alloy's thermal and physical characteristics vary on temperature. In this scenario, the friction coefficient is likewise thought to be temperature-dependent and it lowers as the temperature rises. The temperature distribution in the welded aluminium plates is determined using transient thermal finite element analysis, with a maximum temperature of 478.42C, 496.084C and 438.08C absorbed at 8 different time instants over a time period of
12 sec, for different tool dimensions (M6 Threaded Cylindrical Tool, Square Tool and Cylindrical Tool).
Fig 3.6 Temperature flow on the weldzone during FSW process (Cylindrical Tool)
Table 3.1 Temperature absorbed at different time instance. (Cylindrical Tool)
Fig 3.7 Temperature flow on the weld zone during FSW process (Square Tool)
Table 3.2 Temperature absorbed at different time instance. (Square Tool)
Fig 3.8 Temperature flow on the weld zone during FSW process (Threaded Cylindrical)
Table 3.3 Temperature flow on the weld zone during FSW process (Threaded Cylindrical Tool)
Fig 3.9 Temperature observed at the 7th second of the FSW process.
Fig 3.10 Temperature observed at the 5th second of the FSW process.
Fig 3.11 Overall differences between the temperature distributions of the material using different tool geometry.
-
CONCLUSION
The experiment was carried out for friction stir welding of dissimilar combinations of AA6061-AA7075 plate samples with dimensions of 300mm length, 200mm width, and 6.35mm thickness using temperature data obtained in the previous session and numerical simulation using different tool geometry models moving heat source using Abaqus 20 software. The experimental data are compared to the benchmark papers of Yuh j. Chao, X. Qi, W. Tang,[11] numerically simulated results, and the following conclusions are drawn:
-
The temperature curve indicates that friction stir welding occurs in the plastic state, and the maximum temperature reached in the simulation is in good agreement with experimental data, indicating that the simulation study of heat transfer behaviour of the friction stir welding process has been validated.
-
Parametric comparison has been done with the square tool, cylindrical tool, and M6 Threaded Cylindrical Tool.
-
Due to the close thermal characteristics of both metals, the heat distribution is identical in both AA5052 and AA6061 Aluminum alloys, as evidenced by the temperature contours.
-
The highest temperature observed by the Yuh J. Chao, X
.Qi, W. Tang, [11] were nearly similar with the highest temperature recored was 450 and from our currret study thed the highest temperatures were 438 (cylindrical tool), 496 (Square Tool) and 478 (Threaded Cylindrical Tool) with an error percentage of 2.66% ~ 5.25%.
REFERENCES
[1] S. Madhavaraoa, Ravi Varma Penmetsaa, Investigation on Mechanical Properties of Friction Stir Welded Aa7075 & Aa6061, S. Madhavarao et al. / Materials Today: Proceedings 18 (2019) 22882297 ICMPC-2019 [2] Guo JF, Chen HC, Sun CN, Bi G, Sun Z, Wei J. Friction stir welding of dissimilar materials between AA6061 and AA7075 Al alloys effects of process parameters. Materials & Design (1980- 2015). 2014 Apr 1; 56:185-92. [3] Padmanaban, G. and V. Balasubramanian, 2009, Selection of FSW tool pin profile, shoulder diameter and material for joining aluminum 7075 an experimental approach, Mater. Des, 2009, 30(7):2647-2656 [4] Venugoapl, T.,K.Srinivas Rao and K.Prasad Rao,2004, studies on friction stir welded 7075AA trans. indian inst.met., vol.57,no.6, December 2004 [5] R. S. Mishra and M. Komarasamy, Friction Stir Welding of High Strength 7XXX Aluminum Alloys, Elsevier, Denton, TX, USA, 2016 [6] S. K. Hussein, Analysis of the temperature distribution in friction stir welding of AA 2024-T3 and AA 6061-T6 using finite element method, UPB Scientific Bulletin, vol. 78, no. 4, pp. 119132, 2016. [7] P. H. Shah and V. Badheka, An experimental investigation of temperature distribution and joint properties of Al 7075 T651 friction stir welded aluminium alloys, Procedia Technology, vol. 23, pp. 543550, 2016. [8] M. Riahi and H. Nazari, Analysis of transient temperature and residual thermal stresses in friction stir welding of alu minum alloy 6061-T6 via numerical simulation, 2e International Journal of Advanced Manufacturing Technology, vol. 55, no. 14, pp. 143152, 2011 [9] ABAQUS, Inc., ABAQUS/Explicit, ABAQUS, Inc., Provi dence,RI, USA, 2006
[10] V. Soundararajan, S. Zekovic, and R. Kovacevic, *Thermomechanical model with adaptive boundary conditions for friction stir welding of Al 6061, International Journal of Machine Tools and Manufacture, vol. 45, no. 14, pp. 1577 1587,2005
[11] Chao, Y. J., Qi, X. Heat Transfer and Thermo-Mechanical Analysis of Friction Stir Joining of AA6061-T6 Plates, Proceedings of the First International Symposium on Friction Stir Welding, June 1416, 1999, Rockwell Science Centre, Thousand Oaks, California, 1999 [12] Nandan, R., Roy, G.G., Debroy, T. Numerical simulation of 3D heat transfer and plastic flow during friction stir welding, Metallurgical and materials transactions A. 37a, 1247 1259, 2006. DOI: 10.1179/174329306X107692 [13] Jonckheere C, De Meester B, Denquin A, Simar A (2012) Dissimilar friction stir welding of 2014 to 6061 aluminum alloys. In: 7th International Conference on Processing and Manufacturing of Advanced Materials, THERMEC2011, August 1, 2011 August 5, 2011, Quebec City, QC, Canada, vol. 409, pp. 269274. [14] Schmidt, H., Hattel, J. and Wert, J., An analytical model for the heat generation in friction stir welding. Modelling and Simulation in Materials Science and Engineering, vol. 12(1), pp. 143-157, 2003 [15] Li, H., & Liu, D., Simplified thermo-mechanical modeling of friction stir welding with a sequential fe method, International Journal of Modeling and Optimization, 4(5), pp. 410-418, 2014 [16] Schmidt, H. B., & Hattel, J. H., Thermal modelling of friction stir welding. Scripta Materialia, vol. 58(5): pp. 332-337, 2008.