
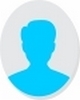
- Open Access
- Authors : Swarna Mayuri K , Shwetha M , Abhilasha A. N
- Paper ID : IJERTV11IS080154
- Volume & Issue : Volume 11, Issue 08 (August 2022)
- Published (First Online): 09-09-2022
- ISSN (Online) : 2278-0181
- Publisher Name : IJERT
- License:
This work is licensed under a Creative Commons Attribution 4.0 International License
Design and Development of a Fixed Wing Unmanned Aerial Vehicle
Swarna Mayuri K1 , Shwetha M2 , Abhilasha A.N3
Research Students, Aerospace Department Indian Institute of Science (Bangalore, India)
Abstract The project focuses the development of a UAV wing encompassing the entire process from design to manufacture and finally, its implementation on the aircraft. The unique design features of this UAV are its ability to take-off and land on a short runway, a stable glide, a maximum speed of about 36 m/s and a long endurance of around 4 hours. Taking these requirements into account the maximum target weight of UAV was fixed at 9kg including a payload of 2 kg and fuel for 4 hours endurance. The standard design procedure applicable for sizing and design of a wing was followed for the present UAV design. Detailed design calculations were carried out using a MATLAB and Spread sheet program to finalize the aerofoil, wing geometry and power requirement. Hence this project encompasses a large intent which is to assemble an actual UAV with mission capabilities.
Pre-checks were conducted to verify the integrity of the components. Finally, a successful flight demonstration was carried out to test the model for steady flight to verify the design.
Keywords Low speed aircraft, fixed wing, airfoil selection, matching plot, gust resistant UAV.
-
INTRODUCTION
Unmanned aerial vehicles (UAVs) ranging from the size of an insect to that of a commercial airliner, are defined as powered, aerial vehicles that do not carry a human operator, use aerodynamic forces to provide vehicle lift, can fly autonomously or be piloted remotely, can be expendable or recoverable, and can carry a lethal or nonlethal payload.
This project involves the development of a rectangular wing, encompassing the entire process from design to manufacture, and finally its implementation on an aircraft and performing flight tests for their validation. The project can be divided into three main components namely,
-
Design and analysis
-
Fabrication
-
Flight test
Considering that UAV has been designed for operations up to 3 km altitude and with gusts up to 20 m/sec, UAV can be deployed at different terrain conditions (like hilly areas, seashore, and desert areas) for surveillance, traffic monitoring etc.
-
-
DESIGN REQUIREMENTS AND SPECIFICATIONS
Mission requirements of the UAV govern the design of the wing. The table below shows the general specification of the aircraft based on the detailed study of statistical trends of the other existing UAVs of similar configuration.
TABLE 1. SPECIFICATIONS OF THE UAV
Maximum gross takeoff weight
< 10kg
Payload
2kg
Minimum range
3.5km
Maximum Cruise speed
25 m/sec
Stall speed
14m/sec
Maximum speed
30m/sec
Minimum endurance
3 hours
Maximum altitude
Up to 3000m (sea level)
Cruise altitude
1000 Feet
Maximum take off distance
< 60m
Reynolds number range
3,00,000 to 4,00,000
-
DESIGN
-
Estimation of gross takeoff weight of the aircraft
-
Empty weight estimation
The empty weight was obtained from the statistical values of the existing UAVS that belonged to the same class (10 kg class UAV)
TABLE II. ESTIMATION OF EMPTY WEIGHT
Empty weight + related accessories
750gms
Fuselage + tail weight
1000gms
Wing weight
1200gms
Landing gear weight
500gms
4 servos
100gms
Others
500gms
Hence total estimated empty weight
4050gms (4 kgs approximately)
-
Fuel weight estimation
The fuselage contains a fuel tank of 2 litres capacity; hence it can carry fuel up to 2 liters. With a 20 cc DLE engine that is being used, half a liter of fuel was found to give up to 1hour of endurance. Hence 2litres of fuel could produce a minimum endurance of 3hours 30 minutes.
-
Payload weight estimation
According to the design the aircraft should be able to carry a payload of up to 2kgs.The types of payloads that can be considered are -Optical Camera, Infra-Red camera, for night vision Thermal and Chemical Sensors Data transmitter/receiver unit for real time transmission of data and video Flight Data Recorder, for data acquisition.
4) Design GTOW of the aircraft
Therefore, maximum payload weight= 2kg
Hence, the design gross takeoff weight was found to be, Design GTOW = 4kg + 2kg + 2kg = 8kg
-
-
Airfoil selection
-
The design lift coefficient should be high.
-
The airfoil should be cambered to produce more lift even at zero angle of attack
-
The airfoil should have a high maximum lift coefficient.
Calculation.
Fig 1: Wingspan versus Take-off weight
-
The airfoil should have minimum drag coefficient.
-
The airfoil should be designed for low Reynolds number in the range of 3 lakhs to 3.5 lakhs.
-
Thickness should be more as it increases the bending stiffness of the wing and provide a stable glide or cruise.
-
The stall angle should be high.
-
The airfoil profile should be simple and easy to fabricate.
Various airfoils were selected based on their performance graphs obtained from wind tunnel data and the values for the short-listed airfoil are shown below.
TABLE III. EXPERIMENTAL VALUES OF SHORTLISTED AIRFOILS
We know, AR = b/c.
Chord c = (b/AR) = 2.25 / 8 = 0.28 m Area (S) = b x c = 0.28 x 2.25 = 0.63 m2
Therefore, the Initial Wing Geometry is
TABLE IV.
INITIAL WING GEOMETRY
AR
8
B
2.25 m
C
0.28 m
S
0.63 m2
2) Final sizing of the wing
The matching plot (W/P) Vs (W/S) {power loading Vs wing loading} for each of the performance points are drawn and the most optimum values of (W/P) and (W/S) are taken for defining the wing dimensions and power requirement.
The table below gives the values of various performance parameters for obtaining the matching plot of (W/P) versus (W/S)
Airfoil
Stall angle In degrees
CLmax
(L/D)
max
CL at =5
CD at =5
AG 35
12
1.091
41.903
0.759
0.011
E 387
12
1.143
58.18
0.9
0.009
AG 24
11.80
0.995
40.839
0.798
0.011
NACA0012S
7.50
0.962
55.303
0.55
0.0074
td> CLARK Y
11.50
1.295
51.615
0.87
0.053
TABLE V. PERFORMANCE PARAMETERS
Vmax
30 m /sec
Vcruise
25 m /sec
Vstall
14 m /sec
VTO (1.1 Vstall)
15.5 m /sec
RoC
STO
60 m
-
5 m / sec
-
10 m / sec
Eppler 387 matched the requirement to its best hence it was chosen for the fabrication of the wing
-
-
Wing geometry selection
-
Initial wing sizing
-
For low-speed aircrafts an aspect ratio of 6-10 was desirable hence an aspect ratio of 8 was chosen from the experience from previous designs.
The value of the wingspan was chosen to be 2.25m for initial calculations, from the graph of wing span versus aircraft weight obtained from statistical data which is shown below in fig. 1
The final matching plot obtained using Matlab program based on performance equations for the wing design is shown below in fig. 2
Fig 2: Matching plot for wing design
From the final plot, it can be seen that the most optimum wing loading is from12 to 13 kg/m2 for RoC of 5 m/s and 10 m/s. considering that a margin is required for any error or approximation in theory, a value of wing loading of 12 kg/m2 is taken.
-
Control surfaces used on the wing
Aileron:
Ailerons are the control surfaces at the trailing edge of the wing which are moved differentially to control the roll motion of the aircraft. Unlike conventional design, where only a small portion of the wing (outer portion) trailing edge is movable and constitutes about 20% of the wing chord (or area).
Flap:
Flap is a high lift device which is used at the trailing edge of the wing to produce additional lift by increasing the camber of the wing airfoil sections on being deflecting.
-
-
WING FABRICATION
-
The structural layout of the wing consists of the
-
Inner core
-
Ribs and spars
-
Lamination or outer skin
-
-
The materials used for the fabrication are-
There is no influence of RoC on wing loading. Hence
for a RoC of 10 m/sec the power loading remains same for any value of wing loading.
Therefore, for a wing loading of 12 kg/m2 the value of power loading is 7 Kg/KW.
Aircraft weight (W) = 9 kg W/S = 12kg / m2
Wing Area S = 9/12= 0.75m2
AR= b/c = 8; b = 8*c; S = b*c = 8 c2 c = (0.75/8) = 0.32m, b= 2.5 m
Hence the final wing geometry for fabrication was taken as follows
TABLE VI. GEOMETRY OF THE WING USING EPPLER387 AIRFOIL
Chord (m)
0.28m
Span (m)
2.6m
Area (m2)
0.728
Plan form
Rectangular
Aspect Ratio
9
Cross Section
Eppler 387
Wing Incidence
0
D. Calculation of the power required
For the calculation of the power requirement the matching plot graph shown in figure 2 is used. The maximum power requirement is decided by the RoC requirement of 10 m/sec.
W/P = 6.8 kg/Kw 7 kg / kW (for W= 9 kg) P = 9/7 = 1.3 Kw.
Thus, the power available from the engine should be at least equal to or greater than 1.3 kW (Engine shaft power).
The wing core was made up of thermo foam material for light weight, (30 kg/m3 or 0.003 gm/cc) High density thermo foam provide high stiffness in all directions.
The ribs were made up of balsa wood.
Aluminium 12 x 12 mm hollow pipes were used as spars. Aluminiums Youngs modulus is 70 GPa
The other materials used are adhesives such a cynoacralite and araldite.
C. Tools used-
Hot wire foam cutter, long rulers, voltage regulator, work bench, power supply.
D. Procedure for wing fabrication
The thermo foam is cut into smaller blocks according to the thickness of the airfoil and its chord length for the ease of handling. A pair of the airfoil templates is then fixed to either side of the thermo foam block using a double side tape. The hot wire foam cutter setup was made ready for cutting the wing segments. Making sure that the foam cutter is tightened to have the right tension and adequately heated by proper voltage regulation. This enables a fine and smooth cutting of the segments. The thermo foam wing segments were slowly and smoothly cut by moving the foam cutter wire carefully over the profile of the airfoil template. The ribs were cut out of balsa wood to be placed in between the wing segments while assembling the wing segments together. Next the ribs and wing segments that are cut were assembled on the aluminium spars with the help of adhesives such as araldite and cynoacralite. The trailing edge of the wing for about 3cm was cut off along the length of the wing and replaced with a long piece of balsa wood. This was done to eliminate the weak trailing edge section and replace it with a stronger material to avoid damaging of the trailing edge during handling and
flight. The control surfaces.i.e., the ailerons and flaps were then cut with 8mm balsa wood and hinged to the trailing edge of the wing. The wing was stickered with a coloured plastic tape for smooth finish and an aesthetic look.
Fig 3: The final finished wing using eppler 387 airfoil
-
EMPENNAGE
The horizontal and vertical tail is made of balsa wood of 3 mm thickness. The flat plate also acts like an aerofoil with slightly higher drag. The control surfaces namely elevator & rudder are made as separate pieces and attached to the horizontal and vertical tail with the help of a twisted tape glued with cyano acrylate.
V. FUSELAGE AND TAILBOOM DESIGN
The fuselage is the primary structural component of the UAV and houses the engine, fuel, propulsion system and the electronic system. The dimensions of the structure are decided by the dimensions and orientation of the largest item that has to be housed within the fuselage. The external attachment to the fuselage is wing, landing gear, propeller, and empennage.
Engine:
Fig 6. Empennage
-
OTHER COMPONENTS
In addition to this the geometry of the fuselage needs to have
good aerodynamic efficiency and hence aircraft performance. The fuselage layout was based on the CAD 3-D modelling of fuselage Considering the internal equipment and integration of external structural components. The layout of fuselage is shown in following fig.4
The power requirement of the UAV should be at least 1.3 Kw. Based on the specification of the available engines, a two- stroke petrol engine with power of 2.5 HP (1.865 kW) satisfying the minimum power requirement was selected.
Propeller:
Fig 7: 20 cc DLE engine
Fig 4: Fuselage layout
Considering the overall size of UAV, the tail boom length was decided as 1 m. The tail boom rod is made of PVC tube with appropriate slots for fixing the tail surfaces. The 3-D modelling of the tail boom shown in the fig.5
Fig 5: Tail boom attached to the Empennage
Usually, the type of propeller is recommended by the engine manufacturer for each engine. The propeller selected for the current engine is a 16 x 6 composite propeller (as shown in fig. 8)
Fig 8: 2 blade composite propeller
Fuel Tank:
For an endurance flight of 4 hours, about 2 litres of fuel quantity is required. The specification and the fuel tank are given in below.
Fuel Tank : DU-BRO (USA) Cat No. 795 Capacity : 1800 cc (1.8 Liters)
Dimension : 8.235 x 3.625 x 4.5 (L x H x W) Tank Weight : 82 grams
<2>Landing gear wheels:
The landing gear is a tri-cycle wheel with a nose wheel attached at the front and the main wheels at wing location (also CG) of the fuselage. The wheels are made of tubeless rubber wheel of diameter 3.5.
Actuators:
The actuation (or movement) of control surfaces and engine controls are done using servos
Following six actuators are required for control of the engine throttle, nose wheel landing gear steering, ailerons, elevators, rudder, and flaps.
The servos are operated electrically with input voltage between 4.8 to 6 volts. The input to servo is from remote control, with a receiver in the fuselage. The power supply to the servo is from the battery placed inside the fuselage. The linear motion for the control is achieved by connecting the control rod to one of the pick-up holes of the output shaft assembly of servo.
-
THE FINAL ASSEMBLY OF THE UAV
The final assembled UAV with the wing and other components installed in it are shown in the fig. 9 below.
Fig 9. Final assembled UAV
-
FLIGHT TESTING
On successful completion of all the pre-flight checks and rectification of ground snags and incorporating the suggestions made by the professional pilot at IISc, a limited flight demonstration was carried out for take-off, sustenance of steady flight in air and to land safely within the visibility range. The flight test was performed with the aircraft demonstrating a steady flight, thus validating the design concept and fabrication of UAV.
-
CONCLUSIONS
Firstly, the gross take-off weight of the UAV was estimated from statistical trends of existing UAVs in the lab. The design the wing was carried out using published aerodynamic formula, MATLAB analysis and catia modelling tool. Due to the low-speed characteristics of UAV, Eppler 387 airfoil which is best suited for low Reynolds number was chosen. The calculated wing geometry agreed very well with the statistical trend data of existing UAVs thus confirming the analysis. The wing fabrication was then carried out using hot wire foam cutting method and further assembling and finishing. A small study and documentation on the design of other parts of the UAV was conducted. The wing was implemented on the UAV and a successful flight demonstration was then carried out to test the model for steady flight for about 15 minutes.
-
SCOPE FOR FUTURE WORK
-
The present objective of the project work was to design, fabricate and flight test the UAV. The flight demonstration has confirmed the initial stability during take-off, flight, and safe landing in calm wind conditions. However, a detailed flight test must be carried out covering the specification or altitude and speed envelope to validate the design. Completion of these tests and carrying out any modifications (if required) would enable the UAV to be adapted for many practical applications
ACKNOWLEDGMENT
We are highly indebted to our Guide and mentor, Dr. S.N. Omkar, Principal Research Scientist at the Aerospace Engineering Department of IISc, for enabling us in taking up this project and making it a success. We have immensely benefitted under his constant supervision and have been a fascinating experience for us.
Above all we thank God and our parents for their unconditional love and support which paved the way for the success of this project.
REFERENCES
[1] Anderson, John D., Introduction to Flight (5th ed.), McGraw- Hill (2004). [2] Anderson, John D., Fundamentals of Aerodynamics (4th ed.),McGraw-Hill (2005).
[3] Raymer, D., Aerodynamics, Aircraft Design: A Conceptual Approach, 4 ed., AIAA, Virginia, 2006, pp. 303-354. [4] J. Roskam and Dr.Chuan-Tau Edward Lan Airplane Aerodynamics and Performance (1997). [5] Anderson J. D., Aircraft Performance and Design, McGraw- Hill, 1999. [6] Abbott and Vandhoff, Theory of wing sections, Dover publications, inc. New York.