
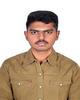
- Open Access
- Authors : M. Arvind , Aakash Raj P
- Paper ID : IJERTV11IS110073
- Volume & Issue : Volume 11, Issue 11 (November 2022)
- Published (First Online): 23-11-2022
- ISSN (Online) : 2278-0181
- Publisher Name : IJERT
- License:
This work is licensed under a Creative Commons Attribution 4.0 International License
IIOT Aided Machine Vision Surveillance System for Industries
IIOT Aided Machine Vision Surveillance System for Industries
M. Arvind¹, P. Aakash Raj²,
Bachelor of Engineering¹ & Bachelor of Engineering ² Department of Electronics and Instrumentation Engineering
R.M.K Engineering College, Anna University
Abstract:- An effective solution for conventional tracking, auditing, sensing system in industries to increase the efficiency, boost the production output and reduce the manual efforts. Automated Inspection allows the detection of possible failures before their occurrence. Our Proposal on IIOT Aided Machine Vision Surveillance System will aid in the optimization and automatic monitoring of production process. We have considered Automated Inspection employing Machine Vision Technology for prototyping, which allows standardization of inspection process. Visual inspection makes it possible to guide robots (robotic arm) to produce more adaptable manufacturing processes. The system will be able to decrease overall time and increase production compared with conventional system. Human operation in industrial environments should be reduced as much as possible, sometimes human presence cannot be avoided, but it can limited to safe distance. The utilization of robotic Guidance speeds up the process. This is a very powerful feature of machine vision because parts may be represented to the camera in unknown orientations during production. The PLC manages the overall control of the process. A PLC can make a quick response with a control process. Human-Machine Interface (HMI) is a user interface that connects a person to a machine / controller on the local station .IIOT (INDUSTRIAL INTERNET OF THINGS) platform plays a vital role in upcoming and existing industries in various aspects. Data logger is designed to collect production data that are stored in the cloud and retrieved when needed. The surveillance data is then stored in the Cloud Data Base using IIOT via Gateway. IIOT Aided Machine Vision Surveillance System satisfy the 360 degree aspect of the industry which includes starting from defect less raw material to standard finished product with high efficiency and meet the requirements of the manufacturing industry.
Keywords: Machine Vision, IIOT, Flawless Production
-
INTRODUCTION:
In the industrial quality control, instead of manual inspection, conventional vision based automatic inspection has been applied. The approach aims to sort
Objects or products according to vision features , which are predefined, into variant categories indicating different quality levels. Quality grading and automatically sorting of object is a typical example with respect to its size, dimensions etc. However, the increasing interests are not only aimed at simply sorting the defective objects from flawless objects, but also processing the defective objects directly after defect detection. The vision based path planning which can be applied for guiding the manipulator to process defective objects, is becoming an important issue in vision based automatic inspection system. To monitor product quality several parameters should be checked, using different measuring tools in many cases. Manual inspection process could
be much slower than the production process leading to less frequent inspection. Any deviation in quality parameters between inspection runs will result in scrap production. The fact that machine vision systems are non-contact, fast and can easily be computerized make them a potential tool for online quality monitoring during actual production in such processes. Automated Visual Inspection (AVI) can estimate dimensions of work parts using visual information and is most often automated by employing machine vision techniques. Machine vision is a tool used to control products in automated production lines in different fields such as food industry, Hardware industry, and automobile industry. Such a tool has the advantage of non-contact measurements without running off the production process. Vision systems have been applied for many applications including inspection of surface defects, for Bottle inspection, for pharmaceutical tablets, defect detection Etc. Using multiple image sensors at different levels of the production line and different angles of shots allows monitoring the different stages of the production process and collection of the information needed to assess product quality and flow of production. Here the overall activity is monitored and controlled by the specialized computer known as PLC. An HMI (Human Machine Interface) is used to view the process by the user and it acts as a local control.
-
OBJECTIVES :
The main objectives of our proposed idea with machine vision system is to perform the automatic process in the industries that include all production industries .To check the presence and absence of parts in the goods that move in a conveyor line, the position of parts can be determined in automobile industries. Dimensional analysis of products to determine their quality in many manufacturing industries. Batch analysis can be done by verifying the lot. No or Bar code readability can be done which is an enhanced application that are used in modern manufacturing industries .The datas are acquired and stored in the cloud via gateway this is the main objective of proposed system.
-
SORTING :
Sorting is known as the heart of much distribution system. Sorting is the process of inducting and separating products to precise targeted lanes with the need for arranging products for better means of distribution in order to increases the rate of production. Sorting systems are required when the high graded products needs to flow to the destination for packaging and shipping process. Sorting are solution for segregating products from conveyor lines to shipment lanes, palletizing operation and other sorting applications. Sorters are versatile and can sort a wide range of product size and weights to multiple distinct lanes. The products which are made to send via the conveyor belt undergo a mechanism known as sorting. In the sorting process the products are been distinguished according to the size, dimension, types etc with intact of Machine Vision System. The process is been monitored fully regarding to its product that is whether the
desired product is either a raw material or finished goods. Under many circumstances of industrial revolution, a sorting process has to be done in order to separate different or desired & undesired items among those out flow on a moving conveyor belt. This process consists of a large number of items been dispersed on the conveyor string, localizing any single item, recognizing within the stipulated time. Most of the industry follow the hand picking process (Manually) which is a time consuming process and even include unavoidable human errors. The above flaws can be replaced with the help of Machine Vision System which averts the inaccuracy, mismanagement, miscalculation, glitch etc.
-
PLC
A PLC is known as Programmable Logic Controller is a esoteric computer used for supervision and monitoring in the manufacturing process and machinery fields. In our proposed system for identification and segregation process we use PLC as a main controller ,initially the inputs from the switch are set for the control action and the output signal is given to the conveyor line motor, as the conveyor line moves into action and the machine vision gets the input and the identification and other process takes place and the inputs from machine vision is given to the controller for the necessary ation to take place ,the controller action takes place by acquiring the signal from Each process and then the controller output is given to the arm specified for tracking the products and locate them into different conveyor lines. The controller action takes place in the PLC when the required conditions are true. This is the main advantage of using PLC controller in our proposed system.
-
MACHINE VISION :
Machine vision technology is the method used to provide the automatic inspection. The process used in robotic guidance, process control mainly in industries. The machine vision process first acquire its requirements from the process and provides the control .After acquiring the requirements the planning takes place and control action begin upon the process. In our proposed system machine vision is the main part of the system; it is placed in the conveyor line to sort the raw materials or to sort the finished goods. This system performs the process that is done by various type of sensors in the conveyor line. In conventional method various types of sensors are used for the detection, sorting, analysis etc, here machine system itself performs all the process in the conveyor line. Machine vision is an emerging technology in industries. All industry need flawless manufacturing and goods which will be their quality management ,which serves reputation of the industry, so every industry are ready to invest for their reputation and to save time for production and detection of errors. This paves way for the industries to use machine vision system. The machine vision system is interfaced with PLC and the overall function is controlled.
-
PROCESS DESCRIPTION
The Machine Vision System performs the following condition
track, trace, audit the materials.
-
Track: The path of inspection line is tracked by Machine Vision System for ensuring flawless pathway on the instruction line.
-
Trace: The materials are traced and the guidance is given to the robotic arm for segregation.
c) Audit: The materials are inspected through a system and the datas are uploaded in local data base and cloud storage.
Our process will take place in a conveyor line where either the raw material are the finished goods are to be sorted. The Machine Vision System is placed over the conveyor line and it deals with materials in the conveyor line. The system performs the functions dimension analysis, color analysis and deformation analysis. Depending on the needed parameters the system performs the desired functions. After analysis of the process the conveyor line are separated into two or 3 lanes. The controller acts as the control for overall process which includes Machine Vision, Conveyor lanes etc. The robotic arms are placed which are used to separate the materials from the main conveyor lane to the subordinate lanes which are placed. Parameter goods are known to be the finished goods are separated from the main conveyor line by the robotic arm. Similarly the unfinished goods are also separated. The same process is also applicable for raw material sorting. A Variable Frequency Drive is a type of motor controller that drives an electric motor by varying the frequency and voltage supplied to the electric motor. The Human Machine Interface (HMI) is the interface between the process and the operators
in essence an operators dashboard. This is the primary tool by which operators and line supervisors coordinate and control the industrial and manufacturing processes in the plant. HMIs serve to translate complex process variables into usable and actionable information.
The above diagram represents the overall outline of the process. The information which is a known as the data is been given to the data loggers. Data loggers are electronic devices which automatically monitor and record environmental parameters over time, allowing conditions to be measured, documented, analyzed and validated. The data logger contains a sensor to receive the information and a memory to store it. Then the information stored in the data logger is transferred to a computer for analysis. After the datas are been analyzed the collected datas are been given to the cloud storage base via a intermediate known as gateway. A cloud storage gateway is a hardware- or software-based appliance located on the customer premises that serves as a bridge between local applications and remote cloud base storage.
A cloud storage gateway provides basic protocol translation and simple connectivity to allow the incompatible technologies to
communicate transparently. The need for A bridge between cloud storage systems and enterprise applications arose because of an incompatibility between the protocols used for public cloud technologies and legacy storage systems. The user is allowed to access the cloud storage for further contemplate the data acquired.
The system starts with an input signal from the controller and the conveyor motor makes its action and moves the product in the lane and the machine vision diagnosis takes place like dimension detction,color detection etc and are send via desired lanes as decided the processed products comes out and they are moved with help of robotic arm structures to the desired lanes and sorted.
-
-
BLOCK DIAGRAM:
The overall controller is the Programmable Logic Controller, here the inputs for the controller are the machine vision system, and the outputs are given to the VFD and the electric motors for the movement of conveyor lane. Another output is given to the robotic arm .If the input conditions are true the output will be performed by the controller.
-
CONCLUSION AND ENHANCEMENT This proposed project reduces human efforts and their errors in large manner, in industries a minimal error can cause drastic change in the process or end product which leads to many losses like time, economy etc. To overcome all the errors and to ensure a flawless production, Our system will ensure a flawless production in an economical manner .The datas which are collected from the process are stored in database using data logger concept and they are stored in the cloud storage. As industries are moving towards modern technology and Industry 4.o the data are stored via gateway using IIoT. Our system can be altered based on the application of the industry needs. It can be opted for various industry like food and beverage industries, electronic industry, automobile industry etc .Since our project is based on the conveyor lane, we can enhance the conveyor lane by using an emerging technology celluveyor lanes ,these conveyor lanes are customized blocks of lanes which are basically a mechanical connections. These celluveyor connections are made depending on the need and controlled by an intelligent controller; these are the future enhancement of our proposed project.
REFERENCES
[1] Automatic inspection system using machine vision{IEEE} [2] Authors U.S. Khan Dept. of Mechatronics , Nat. Univ. of Sci. & Technol., Rawalpindi, Pakistan ,J.Iqbal Dept. of Mechatronics , Nat. Univ. of Sci. & Technol., Rawalpindi, Pakistan ,M.A. Khan Dept. of Mechatronics , Nat. Univ. of Sci. & Technol.,Rawalpindi, Pakistan
[3] Machine vision applications and development aspects {IEEE} [4] Authors Antonio O. Fernandes Universidade Federal de Minas Gerais, Brasil Luiz F. E. MoreiraInvent Vision Sistemas de Imagem e Visão, BrasilJosé M. Mata Universidade Federal de Minas Gerais, Brasil [5] PLC-based control systems for industrial production of fuel alcohol {IEEE} Authors Sheng Qiang Dept. of Control Sci. & Eng., Harbin Inst. of Technol., China [6] A Conveyor-Belt Based Pick-and-Sort Industrial Robotics Application {IEEE}Authors Yizhe Zhang Univ. of Virginia,Charlottesville, VA, USA
[7] Lianjun Li Univ. of Texas at Dallas, Dallas, TX, USA ,Michael Ripperger Southwest Res. Inst., San Antonio, TX, USA,Jorge Nicho Southwest Res. Inst., San Antonio, TX, USA ,Malathi Veerarghavan Univ. of Virginia, Charlottesville, VA, USA