
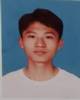
- Open Access
- Authors : Kangling Li , Yunfei Wu , Peizh Li , Zhipeng Cai
- Paper ID : IJERTV11IS110058
- Volume & Issue : Volume 11, Issue 11 (November 2022)
- Published (First Online): 28-11-2022
- ISSN (Online) : 2278-0181
- Publisher Name : IJERT
- License:
This work is licensed under a Creative Commons Attribution 4.0 International License
Bionic Cross-Country Demining Manipulator
Kangling Li, Yunfei Wu , Peizhe Li, Zhipeng Cai
(College of Information Engineering
Henan University of Science and TechnologyLuoyang Henan 471023China
Abstract:- In this paper,an off-road bionic demining manipulator based on 32-bit microcontroller is designed. Single-chip camera using the images collected, combined with laser radar, through the grid scanning method to achieve automatic navigation.Sensors to monitor the outdoor environment, combined with the steering gear, the robot arm for demining work, and through the BC28 NBIOT module, the information through the MQTT protocol, uploaded to Alibaba Cloud, with Beidou positioning module, so that monitors through the web side real-time monitoring and control of the robot arm.
Key words:- Image recognition, Robotic arm motion, Automatic navigation, Cloud platform, NBIOT, Environmental detection, Beidou positioning
0 INTRODUCTION
In many war-torn countries around the world, unexploded ordnance and landmines are strewn about.For example, in the area of more than 10,000 square kilometres along the Kuwait-Iraq border after the Gulf War, there were 250,000 landmines, 850,000 artillery shells manufactured by 16 countries, and 25 million bombs and cluster bombs droppe d by the multinational force, at least 20 per cent of which did not explode.In addition, in many countries and regions, there are even remnants of unexploded bombs and mines in World War I and World War II. Therefore, the demand for mine sweeping robots is very large.
At present, the development of domestic demining machines is relatively slow. At present, there are few working sites that domestic demining machines can adapt to. For complex areas such as mountain rain forests, there are few demining machines to achieve demining. Most of them are manual demining by deminers. In this complex site, the working conditions are complex, and the life safety of deminers is greatly threatened. Therefore, we designed a NBIOT technology as a carrier off-road bionic demining manipulator.The manipulator can realize complex work in mountain rainforest by relying on the off-road base. Through the intelligent system integrating high-precision Beidou satellite positioning technology, communication technology, Internet of things, cloud computing technology and other cutting-edge technologies, the remote operation can realize automatic demining.The mechanical arm not only guarantees the life safety of deminers, but also realizes automatic demining, improves the efficiency of deminers and reduces labor costs.
Fund Project :
2022 Henan University of Science and Technology Student Research and Training Program funded Class C ( 2022112) Author Profile :
Li Kangling ( 2002.01.06 ), male, Loudi, Hunan, undergraduate, the main research direction for embedded development and hardware design.
1 SYSTEM WORK FLOW
The overall system diagram is shown in Figure 1. The system is divided into three main sub-processes, namely off-road vehicle automatic navigation system, manipulator motion system, cloud control system.
Process 1 : The camera ( 1 ) collects the image of the environment for the first time, and the lidar performs a grid-shaped full-field scanning of the surrounding environment. Finally, the information is integrated and the optimal path is planned. The optimal path solution and the position information of the Beidou module are fed back to Alibaba Cloud by NBIOT, so that the cloud can monitor the operation status of the automatic navigation system in real time, and human intervention can be performed under special circumstances.
Process 2 : Camera ( 2 ) performs image acquisition and image analysis on the object to be operated. The position of the target object is sent to the cloud by NBIOT, and the control signal is sent to the manipulator motion system by the cloud. The PWM control signal is sent by the STM32 main control to complete the motion control of the manipulator and finally realize the demining work.
Process 3 : cloud control system for data collection, analysis, instructions sent, is the final control platform, cloud control platform to achieve remote control.
Fig. 1 System block diagram
2 HARDWARE DESIGN
The system hardware mainly includes two parts, as shown in Fig. 2, which are off-road vehicle system and manipulator system hardware design.The off-road vehicle system adopts STM32F4 single-chip microcomputer as the main controller. The motor drive adopts H-bridge circuit. At the same time, auxiliary sensors such as encoder and gyroscope are added to make the off-road vehicle driving process more stable.The manipulator system controls the motion of the steering gear
by the PWM wave output circuit. The end of the arm is equipped with a pressure sensor to feedback the grasping force. The attitude data is collected by the gyroscope. The two systems are sent to NBIOT through the serial port to communicate with the cloud platform.
-
Camera OPENMV visual module
Fig. 2 System hardware schematic
Image acquisition plays an important role in the stability of automatic navigation system of off-road bionic manipulator.[ 1 ] The OPENMV camera module is based on STM32F743 CPU, with MT9V034 camera photosensitive element. On the small hardware module, the core machine vision algorithm is efficiently implemented by Python programming, and the machine vision function of the OPENMV module is realized.The OPENMV camera module is wired to the microcontroller, and the captured image is returned to the microcontroller in a set of 8 -bit binary data.MT9V034 has a CMOS global shutter : the entire image is reset before exposure, and the pixel can accumulate charge during exposure time ; after the exposure, the charge accumulated by each pixel is simultaneously transmitted to the storage area of the shielded light, and then the signal is read out from this area.. Because all pixels are reset at the same time, the exposure integral is the same interval, and is transmitted to the light shielding storage area at the same time, there is no deformation for the moving object, which is of great significance for the moving off-road bionic manipulator.
-
NBIOT module BC28
The NBIOT module BC28 includes MQTT communication protocol and NBIOT communication module. The NBIOT module BC28 is connected to Ali cloud. The module can obtain the data of the demining t arget object through the OPENMV vision module and the Beidou positioning module, upload it to the Ali cloud, send the control signal to the STM32 through the cloud, and finally control the manipulator by the STM32 to complete the demining work.
-
Laser radar
Figure 3 NBiot module BC28 module circuit
LiDAR is a system that integrates laser, global positioning system ( GPS ) and inertial navigation system ( INS ) technologies to obtain point cloud data and generate accurate digital 3D models. The combination of these three techniques enables the acquisition of surrounding 3D scenes with consistent absolute measurement points. It can obtain the terrain of the ground digital elevation model ( DEM ), realize the digital simulation of the ground terrain through the limited terrain elevation data, and represent the ground elevation with a set of ordered numerical arrays. With LiDAR technology, the cross-country bionic mechanical arm can better adapt to the demining work in complex areas such as mountainous rain forests.
3 SOFTWARE DESIGN
Software design mainly includes : laser radar grid scanning method, mechanical arm reverse motio, motor motion control, cloud control.
-
Laser radar grid scanning method
The grid scanning [ 2 ] is a scanning method that scans in a reciprocating sequence along the horizontal or vertical direction, and its scanning trajectory is shown in Figure 4. The grating scan first scans continuously and uniformly in one direction. After completing one line of scanning, the transformation direction reaches the next line, and then scans in the opposite direction of the adjacent lines. This process is called a line cycle scanning.
The row period can be divided into four stages when representing the grating scanning trajectory. By adjusting the size of these four cycles T1, T2, T3, T4, the length of the scanning line can be changed. Equations ( 1 ) to ( 4 ) correspond to four scanning cycles :
Cycle T1 Cycle T2 Cycle T3 Cycle T4
In the formula : xn tyn t
Represents the coordinates of the center position of the scanning spotn denotes the
nth row period ; parameters a, b represent the rate of change of the scanning distance over time in b oth horizontal and vertical directions, the greater the value, the faster the scanning speed AxAy Represents the scope of the scan.
Fig.4 Grid scan
The grating scanning has the following characteristics : the scanning spot is evenly distributed, the implementation method is simple, it can better meet the needs of horizontal detection and vertical detection, and can be used for target search.
-
Reverse motion of mechanical arm
Inverse solution problem [ 3 ] is under the condition that the position parameter of target matrix is known,position posture of whole arm-problem of each member parameter.
[ 4 ] The desired pose of the robot is now known, and each joint value is solved.nx ox ax
n
o
a
0 y y y
px
p
y 0 1 2 3 4
Known : 5T
nz oz az
T T T T T
z
p 1 1 2 2 3 3 4 4 5 5
1
0
1
0
0
1Solve1 and multiply the left side of Equation ( 1 ) by 1T 1
to remove one of the variables:
0 -1
1T 1
0T 2T 2 3T 3 4T 4 T 5 2
0 1 5 1
2 3 4
5
Let the ( 3,3 ) ( 3,4 ) elements at both ends of the equation be equal, then :
a d
-
P
axd5 Px
1
A tan y 5 y
2Solve 2 . multiply the left side of Equation ( 2 ) by 2T 2 :
1 1
2T 2
1T 1
5T 3T 3 4T 4 5T 5
1 1 0
1 0 2 3 4
d (a C
-
a S ) P C
-
-
P S
Also solved :
A tan 5 x 1 y 1 x 1 y 1
(3)
2
Pz azd5
3Solve3
. multiply the left side of Equation ( 3) by
3
3
2T
1 :
3T 123
0T 4T 4 5T 5 4
0 1 5 3 4
Let the elements of ( 1, 4 ) and ( 2, 4 ) be equal, then:
P C
-
P S
A tan y 1 x 1
(5)
3 P S
-
P C C
-
P C S
z 2
x 1 2
y 2 1
4Solve 4 . The ( 1,3 ) and ( 3,3 ) elements in the pair ( 4 ) correspond to each other to be equal :
P (C C C
-
-
S S
) P (C S
C C S ) P C S
-A tan x
1 2 3
1 3 y 1 3
2 3 1
z 3 2
4 P C
-
d P C S
-
P S S
5Solve5 .
z 2 3
y 1 2
x 1 2
o C
-
o C S
-
o S S
A
z 2 x 1 2 y 1 2
5 – tan n C
-
n C S
-
o S S
z 2
x 1 2
y 1 2
-
-
motor motion control
After image processing, motor control is the key to automatic navigation. The classic PID algorithm is used to calculate the path deviation value :
err M Xm
(3)
In the formula, err is the calculated path deviation value, M is the total path of the automatic navigation algorithm, and Xm is the camera center coordinate.
After the deviation value is calculated by the PID controller, it is superimposed on the PWM output of the left and right motors, one plus one minus, so as to realize the differential speed of the rear wheel. The traditional P ID algorithm is :
PIDout Kp err Ki err Kd (err errlast )
(4)
The traditional PID speed response is slow, in the case of some large deviations, can not be timely response, in order to solve this problem, on the basis of motor control joined the Luban algorithm [ 5 ], such as figure 6 :
Figure 6 PID with Luban algorithm
When the motor is detected to have a large deviation value, the robust algorithm will be triggered to enable the motor to respond more quickly. The traditional incremental PID is still used in the normal deviation. This design solves the problem that the large deviation response is not timely.
-
Data Upload Cloud
NBIOT : [ 6 ] Narrow Band Internet of Things ( NBIoT ) is an important branch of the Internet of Things. It is characterized by only consuming about 180 KHz bandwidth and can be directly deployed in GSM networks, UMTS networks or LTE networks to reduce deployment costs and achieve smooth upgrades. As an emerging technology in the field of the Internet of Things, NB-IoT supports cellular data connections for low-power devices in wide-area networks. It is also called low power consumption and is used in wide-area network applications. NB-IoT supports efficient connection of devices with long standby time and high network connection requirements.
[ 7 ] MQTT protocol : The main advantage is that according to the publish \ subscription mode information, the messages published by different clients ( MQ-Client, another part of the communication ) are sent to different subscription clients, and then the end-to-end processing is realized. In the process of message forwarding, it is completely based on the information channel of publish \ subscription. In addition to this channel, do not distinguish between IP address and port, unlike the traditional WinSocket communication.4 CONCLUSION
In this paper, an off-road bionic demining manipulator based on cloud platform control and monitoring is designed based on 32-bit microcontroller. The scheme is proposed in data transmission, automatic navigation algorithm, motor motion control, manipulator grasping and so on. Relying on automation equipment, with the help of mechanical arm in demining work, the life safety of soldiers is guaranteed, and the efficiency of demining work is improved.
REFERENCE
[1] An intelligent pathfinding car based on OpenMV vision module and MPU6050 angle sensor [ J ].Shen Zhongkun, Xu Jinjie.Electronic production, 2022,30 ( 3 ) : 28-30,19. [2] aser radar scanning mode [ J ]. Yuan, Ma, Liu, et al. Strong laser and particle beam, 2020, 32 ( 4 ) : 61-66. [3] Hysteretic dynamics modeling and robust control of piezoelectric micro-rods [ J ].Wang Haifeng, Feng Xingwei, Li Qing, et al. Electro-optics and control, 2022,29 ( 7 ) : 114-118,125. [4] Research on inverse kinematics of working arm of concrete spraying trolley [ J ].Han Yong, Guan Huisheng.Tunnel construction, 2013,33 ( 4 ) : 281-286. [5] Motion Analysis and Trajectory Planning of 5-DOF Manipulator [ J ]. Xie Jia, Dou Lianghao, Li Yongguo, et al. Manufacturing Automation, 2022, 44 ( 7 ) : 11-15. [6] A design of intelligent parking front-end system based on narrowband Internet of Things ( NBIOT ) [ J ].Zhang Yuming, Jiang Zhe.Digital users, 2018,24 ( 26 ) : 25-26. [7] Research and development of IoT system for workshop equipment based on MQTT protocol [ J ]. He, Yang, Liu, Wang, Modular Machine Tool and Automated achining Technology, 2019 ( 04 ) : 154-156.Main Author photo