
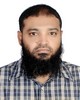
- Open Access
- Authors : Mohd Mushtaq Ahmed , Dr. K. Manjula Vani
- Paper ID : IJERTV11IS110148
- Volume & Issue : Volume 11, Issue 11 (November 2022)
- Published (First Online): 01-12-2022
- ISSN (Online) : 2278-0181
- Publisher Name : IJERT
- License:
This work is licensed under a Creative Commons Attribution 4.0 International License
Synergistic Effect of Micro Silica and Nano Silica on Packing Properties of Cement Matrix
1Mohd. Mushtaq Ahmed 2Dr. K.Manjula Vani
1Research scholar, Department of Civil Engineering, JNTUH College of Engineering, Hyderabad, Telangana, India. 2Professor,
Department of Civil Engineering, JNTUH College of Engineering, Hyderabad, Telangana, India.
AbstractModern day infrastructural needs, architecture, space constraints and the cutting-edge construction practices require the concretes that are highly flowable, possess high strengths, durable and sustainable. Highly flowable concretes like self compacting concrete and ultra-high performance concrete are the promising types for the present and future trends especially from the perspective of 3D printing of structural elements. The enhanced flowability of these concretes, at low water-binder ratio, is the result of the dense packing of the constituent fine and ultra-fine particles, coupled by the action of super plasticizers. Nano materials consisting of particles in the size range of 0.1 to 100nm, exhibit novel properties that are different from their bulk counterparts, that also include surface reactivity and filler effect. In this study an attempt is made to study the synergistic effect of micro silica (which is also an essential ingredient of high and ultra-high performance concretes) and nano silica on packing properties of the cement matrix, as it is the microstructural packing that controls the rheology and flow characteristics of the concrete to a large extent. Puntke test is used to evaluate the packing density of the control, binary and ternary cement matrices. It is observed that the synergistic effect of micro silica and nano silica resulted in enhanced packing density of the ternary cement matrix when compared to their individual effect.
KeywordsFlowability, microstructural packing, nano silica, packing density, silica fume, synergistic effect
-
INTRODUCTION
Traditional concretes made with ordinary Portland cement (OPC) and other cementitious materials or industrial by- products of particle size distribution (PSD) in the similar range as that of OPC are unable to match the requirements, in terms of strength, durability and construction practices, of the special and ultra-high performance concretes, that are required for the construction of specialty structures like super tall buildings, blast resistant structures, bridge piers and deck connections, marine structures, sleek architectural facades, high-strength precast elements, repair concretes and 3D printable concretes [1-3]. To match the special properties the concretes should possess to make them suitable for such applications, concretes having high flowability, ductilty in addition to high compressive and tensile strengths are to be developed. These characteristics can be achieved by improving the packing density of the concrete mixtures, reducing the void content and having a discontinuous pore structure [4]. To design concrete mixtures with higher packing density, the materials used for making the concrete should be so selected, that they contain a wide particle size distribution
(PSD) range in order to fill in the voids leftover by larger particles, by smaller particles and so on. Such enhanced microstructural packing can be attained by making a dense cement matrix that has micro and nano particles which are carefully selected and very well proportioned based on particle packing technology [5-6].
Ultra-high performance concrete (UHPC) is one such emerging and innovative concrete that has high flowability, greater compressive and tensile strengths, improved ductility and toughness and highly durable, which is again a consequence of high packing density of the cement matrix [4]. The extensive use of micro silica (M), (owing to its reactivity, shape and sub-micron particle size), in designing densely packed cementitious matrices, ultra-high performance concrete (UHPC) and reactive powder concrete (RPC) has been widely reported in literature [7-8]. To achieve denser particle packing and pozzolanic reactivity, micro silica dosages of about 20% to 30% of the total binder material in UHPC, have been recommended [8-12].
More recently, inclusion of nano particles in the cement based materials have been increasingly attracting the attention of researchers, specifically to improve the rheology, packing density, strength and durability properties of the concrete [13-14]. Nano silica (N) is one such material that has been reported to exert effective influence on packing density and the strength of cementitious materials. A considerable increase in the compressive strength of the cementitious paste with less than 2.0% nano silica at 3 days has been reported [13,15]. Studies also showed that 1% N increased the strength by 13% at 7 days and 8.6% at 28 days when compared to control specimen [14, 16]. Nano silica could also serve as a base for the precipitation of C-S-H gel to promote the hydration of cement [17]. In most cases, the interfacial transition zone (ITZ) is densified in the presence of N, due to its filling effects and also due to the additional C- S-H formed from nano silica [18]. Nano silica exerts both physical effect (by providing nucleation sites and as a reactive filler) and chemical effect (being pozzolanic) on hydration reaction [19, 20, 21, 22]. Above literature survey points to a conclusion that both micro silica (M) and nano silica (N) can be used in designing and developing densified cement matrices having enhanced properties.
Despite the positive effects of M and N on fresh and hardened properties of concrete, when used individually along with other cementitious materials and fillers, there is very limited study regarding the simultaneous use of both M
and N and their combined effect on cement matrices. The combination of different pozzolanic materials in the cementitious matrix alters the rheology, packing density, reaction processes, phase compositions and microstructure development in addition to mechanical properties. In this paper, an experimental investigation is done to study the synergistic effect of micro silica and nano silica on the packing density of the cement matrix when both these materials are used simultaneously. The effect of these materials on packing density of cement matrix when used individually, at varying levels is also studied. Packing density is considered as the main parameter, as a cement matrix with optimized microstructural packing and high packing density results in the production of concrete that has superior rheological and mechanical properties [23-34]. Puntke water demand test [35] is used to evaluate the packing density of the control, binary and ternary blended cement matrices.
-
EXPERIMENTAL PROGRAM
The intention of the experimental program was to determine the synergistic effect of M and N on the packing density, Ø of the various cement matrices at different levels of cement replacement so as to determine which combination of constituent materials result in a cement matrix with maximum packing density. The reference cement matrix was made of ordinary Portland cement (OPC). Two types of binary cement matrices were formulated i) using OPC and M, with M percentages varying from 5 to 20% with an increment of 5% and ii) using OPC and N, with N percentages varying from 1 to 4% with an increment of 1%. Ternary cement matrices were formulated using OPC, M and N, with M percentages varying from 5 to 20% with an increment of 5% and N percentages varying from 1 to 4% with an increment of 1%. For adequate dispersion of fine particles, Poly carboxylic ether (PCE) basedsuper plasticizer, 2% by mass of binder is used for all mixtures. To determine the packing density and/or water demand of the fine particle mixtures in wet condition, Puntke test (water demand Germany) is adopted in this study. The test method is based on the principle that, a fine and less cohesive particle packing without a load, then and then only, can be compacted to a powder specific value, when the water content is sufficient to fill all the voids in the packing. When the particle packing is humid but not yet saturated, the capillary forces block the water from surrounding the particles. These capillary forces vanish at the saturation point and the particles
can easily be packed to the characteristic highest packing density. Its not the compaction energy that is important, but the compactability. The test is relatively simple to perform, and as the results are reliable [36], it has been extensively used for the evaluation of packing density of fine powders esp. in the concrete industry.
-
Materials
The materials used for the preparation of blended cement matrices are: Ordinary Portland cement (OPC) (53 grade; consistency = 30%; Soundness = 1.5 mm; IST = 120 min; FST = 230 min) conforming to IS: 12269-1987 (R2004), microsilica (M) 920 supplied by Elkem Industries, Mumbai conforming to ASTM-C(1240-2000) in dry densified form and nano silica (N) supplied by Astrra chemicals, Chennai. Poly carboxylic ether (PCE) based super plasticizer (SP) supplied by Hella infra, Mumbai and potable water conforming to IS 456-2000 are used. The chemical composition and physical properties of the materials used in the study is presented in Table 1. Fig. 1 shows the representational SEM and TEM images of OPC, micro silica and nano silica.
10µm
(a)
(b)
20 nm
(c)
Fig. 1. Representational particle sizes of micro and nano materials a) SEM image of cement b) SEM image of micro silica c) TEM image of nano silica
Table 1 Chemical composition and physical properties of materials used
Material
SiO2
%
Al2O3
%
Fe2O3
%
CaO
%
MgO
%
SO3
%
LOI
%
Avg. Particle size – µm
Specific gravity
Fineness M2/gm
OPC (C)
21.41
4.88
3.82
63.69
1.56
2.36
1.4
15
3.15
0.33
Micro silica (M)
92.9
1.2
0.74
0.02
1
0.1
1.8
0.15
2.2
15 (min)
Nano silica (N)
99.88
0.005
0.001
–
–
–
0.66
0.017
2.3
202
-
Test method
Puntke test was performed to find the ideal combination of materials that yield the highest possible packing density. The advantage of this test procedure is that the materials are tested in wet condition which closely represent the field conditions. Total volume of the cement matrix considered is 20cm3 for all mixes. Materials were proportioned by volume for different cement matrix combinations. PCE super plasticizer, 2% by mass of binder is used for all mixes. The mix proportions for control (reference mix), binary and ternary blends of cement matrices are represented in Table 2.
Table 2 Mix proportions for control, binary and ternary cement matrix
saturation was recorded and packing density was calculated by using the Eq. 1.
Packing density, Ø = 1 [Vw / (Vs + Vw)] (1)
Where, Vw is volume of water and Vs is volume of solids. Packing density of all mixes was calculated.
-
-
RESULTS AND DISCUSSION
Packing density of the cement matrices for different combinations of OPC, micro silica and nano silica was calculated using Eq.2. Packing density of binary cement
matrices containing i) OPC and micro silica (at varying
Mix ID OPC
(Vol%)
Micro silica (M)
Nano silica (N)
OPC
(grams)
Micro silica (M)
Nano silica (N)
Water demand
(Vol%)
(Vol%)
(grams)
(grams)
(cm3)
C100
100
63.00
15.83
C95M5
95
5
59.85
2.22
16.25
C90M10
90
10
56.70
4.44
15.92
C85M15
85
15
53.55
6.66
15.33
C80M20
80
20
50.40
8.88
16.25
C99N1
99
0
1
62.37
0.46
16.58
C98N2
98
0
2
61.74
0.92
16.33
C97N3
97
0
3
61.11
1.38
17.00
C96N4
96
0
4
60.48
1.84
17.58
C94M5N1
94
5
1
59.22
2.22
0.46
16.42
C93M5N2
93
5
2
58.59
2.22
0.92
16.83
C92M5N3
92
5
3
57.96
2.22
1.38
17.00
C91M5N4
91
5
4
57.33
2.22
1.84
17.42
C89M10N1
89
10
1
56.07
4.44
0.46
16.33
C88M10N2
88
10
2
55.44
4.44
0.92
15.75
C87M10N3
87
10
3
54.81
4.44
1.38
16.42
C86M10N4
86
10
4
54.18
4.44
1.84
17.08
C84M15N1
84
15
1
52.92
6.66
0.46
16.25
C83M15N2
83
15
2
52.29
6.66
0.92
16.08
C82M15N3
82
15
3
51.66
6.66
1.38
16.33
C81M15N4
81
15
4
51.03
6.66
1.84
16.83
C79M20N1
79
20
1
49.77
8.88
0.46
16.58
C78M20N2
78
20
2
49.14
8.88
0.92
16.92
C77M20N3
77
20
3
48.51
8.88
1.38
17.25
C76M20N4
76
20
4
47.88
8.88
1.84
17.42
levels) and ii) OPC and nano silica (at varying levels) are shown in Fig. 2 and Fig. 3 respectively. Fig. 4 shows the packing density of ternary cement matrices containing OPC, 10% micro silica and 1 to 4% of nano silica. Packing density for all the cement matrices are shown in Fig. 2.
Fig. 2. Cement to Micro silica Vs Packing density
Fig. 3. Cement to Nano silica Vs Packing density
Calculated amounts of selected materials were dry-mixed adequately in a container having a flat bottom, to get a homogenous mixture before adding water. Low amount of potable water (pre-mixed with super plasticizer) was gradually added to the dry mix with continuous mixing and simultaneous pressing of the mixture against the wall of the container. The container was then tapped twenty times on a flow table. The procedure was repeated by gradually adding the water in increments, till a glossy and shiny surface is achieved on the top of the mix which indicates that the saturation point has reached. For each mix the test was repeated three times to obtain the least amount of water required for saturation. Mean value of the water required for
Fig. 4. Cement to Nano silica Vs Packing density
Fig. 5. Packing densities of various mix proportions for control, binary and ternary cement matrix
From figures 2 to 4, it is observed that the packing density Ø, for the control cement matrix containing OPC alone is calculated as 0.558. From Fig. 2, it is noted that, from the group of all the binary cement matrices containing OPC and M (with percentages of 5, 10, 15 and 20%), the matrix with 15% M has the maximum packing density of 0.566, and all other matrices with 5, 10 and 20% M have Ø even less than the control matrix. This means that lower percentages of M (5 and 10%) are inadequate to fill-in the voids of the cement matrix. At 20% of M the Ø is again lowered which may be due to the loosening effect that has occurred due to the presence excess fine particles. 15% M is the optimum content in the binary matrix in order to have the higher Ø. From Fig. 3, it is noted that, from the group of all the binary cement matrices containing OPC and N (with percentages of 1, 2, 3 and 4%), the matrix with 2% N has the maximum Ø of 0.55, and all other matrices with 1, 3 and 4% N have Ø much less than that of the control matrix packing density of 0.558. Also beyond 2% N, the Ø decreased as N% increased. This low Ø can be attributed to the nano size of the particles that possess high inter-particle forces which result in increased voids. Effect of very high specific surface area of the nano silica may also result in more water demand. Also the effect of manual mixing cannot be ruled out.
From Fig. 4 and Fig. 5, it is seen that, of all the ternary cement matrices containing OPC, M (with percentages of 5, 10, 15 and 20%), and N (with percentages of 1, 2, 3 and 4%), the cement matrix with a combination of OPC, 10% M and 2% N has a Ø of 0.56, which is marginally higher than the control matrix. Also it can be noted that the ternary matrices containing OPC, M and N, have a better packing density than that of the binary matrices containing OPC and
-
The higher Ø of the ternary matrices clearly direct to the improved and optimum microstructural packing of the matrix. This is due to the presence of wide particle size distribution range that has resulted in a reduced void content which in- turn is a consequence of inclusion of M in the matrix with OPC and N. Thus, it can be said, that the synergistic effect of using both M and N in the cement matrix with OPC resulted in the matrices with improved packing density.
-
-
CONCLUSIONS
In this paper, an attempt is made to study the individual and synergistic effects of using micro silica and nano silica on packing properties of the cement matrix. Cement matrix is the base for all types of concretes, which along with the aggregates, controls the rheology/flowability and also the strength of the resultant concretes. High packing density of the cement matrix, because of denser microstructural packing, results in low water to binder ratio, which is an essential parameter to improve the rheology and strength charac-teristics of the concretes. A simple and easy to perform, Puntke test was adopted to determine the packing density of cement matrix. From the presented results of the study, conclusions drawn are as follows:
-
Binary cement matrices containing OPC and only micro silica have a higher packing density when compared to the packing density of the binary cement matrices containing OPC and only nano silica. The packing density decreased with the increasing percentage of nano silica. In-adequate dispersion and high specific surface area of nano particles could be the reason for the low packing density. Avoiding use of only nano silica in the cement matrix seem to be appropriate .
-
Use of both micro silica and nano silica in the ternary cement matrix along with OPC resulted in the improved packing density due to the presence of wider particle size distribution. Due to filling effect of differently sized particles, reduction in void content has occurred, which has resulted in reduced water demand. Hence, a combination of micro and nano materials in the cement matrix, by acting synergistically, improve the packing density of the cement matrix. Also the proportion of the nano material should be optimum, which, in this study, is obtained as 2% by volume of the cement matrix
-
By conducting tests on a large number of sample mixes, it has been observed that, Puntke test provides reliable and consistent results and can be used to evaluate packing density of the fine powders in wet condition.
REFERENCES
[1] Graybeal, B.A. (2012). Ultra-high-performance concrete composite connections for precast concrete bridge decks, US department of transportation, FHWA. [2] Buswell, R.A., Soar, R.C., Gibb, A.G.F., Thorpe, A (2007) Freeform construction: megascale rapid manufacturing for construction, Autom. Con. Struct. 16 (2), 224231. [3] Buchli, j., Giftthaler, m., Kumar, n., Lussi, m., Sandy, t., D¨orfler, K., Hack, N. (2018) Digital in situ fabrication – challenges and opportunities for robotic in-situ fabrication in architecture, construction, and beyond, Cement and Concrete Research. 112, 6675, [4] American Concrete Institite (ACI). (2018). Ultra- highperformance concrete: An emerging tech. report,ACI 239R- 18. [5] Reda, M. M., Shrive, N.G., and Gillott, J. E. (1999). Micro- structural investigation of innovative UHPC. Cement and Concrete Research. 29(3), 323329. [6] Ghafari, E., Arezoumandi, M., Costa, H., & Julio, E. (2015a). Influence of nano silica addition on durability of UHPC. Construction and Building Materials. 94, 181188. [7] Richard, P., & Cheyrezy, M. (1995). Composition of reactive powder concretes. Cement and Concrete Research. 25(7), 1501 1511. [8] Ma, J., Schneider, H. (2002). Properties of Ultra-highperformance concrete. Leipzig Annual Civil Engineering Report (LACER). 7, 25-32. [9] Matte, V., & Moranville, M. (1999). Durability of reactive powder composites: Influence of silica fume on leaching properties of very low water/binder pastes. Cement and Concrete Research, 21(1), 19. [10] Chan, Y., & Chu, S. (2004). Effect of silica fume on steel fibre bond characteristics in reactive powder concrete. Cement and Concrete Research, 34(7), 11671172. [11] Wille, K., Naaman, A. E., and Parra-Montesinos, G.. (2011c). Ultra-high performance concrete with compressive strength exceeding 150 MPa (22 ksi): A simpler way. ACI Mater. Journal. 108(1), 4654. [12] Xing, F., Huang, D., Cao, L., & Deng, L. (2006). Study on preparation technique for low-cost green reactive powder concrete. Key Engineering Materials, 302303, 405410. [13] Liu, J., Li, Q., Xu, S. (2015). Influence of nanoparticles on fluidity and mechanical properties of cement mortar, Constr. Build. Mater. 101(Part 1), 892901. [14] Oltulu, M., Sahin, R. (2011). Single and combined effects of nano-SiO2, nano-Al2O3 and nano-Fe2O3 powders on compressive strength and capillary permeability of cement mortar containing silica fume,Mater. Sci. Eng.,A528(22)7012 7019. [15] Stefanidou, M., Papayianni, I. (2012). Influence of nano-SiO2 on the Portland cement pastes, Compos. B. Eng. 43 (6) 27062710. [16] Shaikh, F.U.A., Supit, S.W.M., Sarker, P.K. (2014). A study on the effect of nano silica on compressive strength of high volume fly ash mortars and concretes, Mater. Des. 60, 433442. [17] Zhang, B., Tan, H., Shen, W., Xu,G., Ma, B., Ji, X. (2018).Nano- silica and silica fume modified cement mortar used as Surface Protection Material to enhance the impermeability, Cem. Concr. Compos. 92, 717.
[18] Liu, Z., Xu,D., Zhang, Y. (2017). Experimental investigation and quantitative calculation of the degree of hydration and products in fly ash-cement mixtures, Adv. Mater. Sci. Eng. 2, 112. [19] Zhang,M.H., Islam,J. (2012). Use of nano-silica to reduce setting time and increase early strength of concretes with high volumes of fly ash or slag, Constr. Build. Mater. 29, 573580. [20] Gao, Y., Zou, C. (2015). Experimental study on segregation resistance of nanoSiO2 fly ash lightweight aggregate concrete, Constr. Build. Mater. 93, 6469. [21] Hou,P.K., Kawashima, S., Wang, K.J., Corr, D.J., Qian, J.S., Shah, S.P., (2013). Effects of colloidal nanosilica on rheological and mechanical properties of fly ashcement mortar, Cem. Concr. Compos. 35 (1), 1222. [22] Li, W., Huang, Z., Zu, T., Shi, C., Duan, W., and Shah, S. (2015). Influence of nano limestone on the hydration, mechanical strength, and autogenous shrinkage of ultra- high performance concrete. Journal of Materials in Civil Engineering, 28(1), 1 9. [23] Arora, A., Aguayo, M., Hansen, H., Castro, C., Federspiel, E., Mobasher, B., Neithalath, N., (2018). Microstructural packing and rheology based binder selection and characterization for ultra- high performance concrete (UHPC), Cement and [24] De Larrard, F., and Sedran, T. (1994). Optimization of ultra-high- performance concrete by the use of a packing model. Cement and Concrete Research. 24(6), 9971009. [25] De Larrard, F. (1999). Concrete mixture proportioning:A Scientific approach, E&FN, Spon, London, UK. [26] Khayat, K.H. and Meng, W.(2017). Improving flexural performance of ultra-high-performance rheology control of suspending mortar, Compos. Part B 117 (2017) 2634. [27] Wille, K., Naaman, A. E., and El-Tawil, S. (2011a). Optimizing ultra-high performance fiber-reinforced concrete. Concr. Int., 33(9), 35 41. [28] Shi, C., Wu, Z., Xiao, J., Wang, D., Huang, Z., and Fang, Z., (2015). Review on Ultra-high performance concrete: Part I. Raw materials and Mixture design. Constr. Build. Mater., (101), 741-751. [29] Fennis, S.A.A.M.,and Walraven, J.(2011). Design of ecological concrete by particle packing optimization. Tese (doutorado), Technische Universiteit Delft, Delft, Netherlands,256. [30] Fuller, W., and Thompson, S. E. (1907). The laws of proportioning concrete. Trans. ASCE 59(2), 67143. [31] Brouwers, J. J. H., and Radix, H. J. (2005). Self-compacting concrete: The role of the particle size distribution. 1st Int. Symp. on Design, Performance and Use of SCC, Changsha, Hunan, China, RILEM Publications Sarl, Bagneux,France, 109118
[32] Kumar, S. V., and Santhanam, M. (2003). Particle packing theories and their application in concrete mixture proportioning: A review. Indian Concr. J., 77(9), 13241331. [33] Mehta, K., & Monteiro, J. (2006). Concrete: Microstructure, properties, and materials (4th ed., p. 659). New York, NY: McGraw-Hill. [34] Funk, J. E., and Dinger, D. R. (1994). Introduction to predictive process control. Predictive process control of crowded particulate suspensions, Springer, New York, 116. [35] Puntke, W., Wasseranspruch von feinen Kornhauf-werken. Beton 52 (2002). H. 5, S. 242-248 [36] Wong, H.H.C., Kwan, A.K.H. (2008). Packing density of cementitious materials: Part-1 Measurement using a wet packing method, Materials and Structures. 41(4) 689-701