
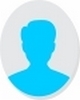
- Open Access
- Authors : Nguyen Van Hoa , Nguyen Anh Tuan , Nguyen Thanh Dat , Tran Vu Van Hoa
- Paper ID : IJERTV11IS110163
- Volume & Issue : Volume 11, Issue 11 (November 2022)
- Published (First Online): 06-12-2022
- ISSN (Online) : 2278-0181
- Publisher Name : IJERT
- License:
This work is licensed under a Creative Commons Attribution 4.0 International License
Improving Construction Cost Management Efficiency: A Case Study of Hoang an Joint Stock Company, Vietnam
Nguyen Van Hoa Vietnam Aviation Academy 104 Nguyen Van Troi, Phu Nhuan District, Ho Chi Minh City, Viet Nam. |
Nguyen Anh Tuan Ho Chi Minh City University of Transport 2 Vo Oanh Street, Binh Thanh District, Ho Chi Minh City, Viet Nam. |
Nguyen Thanh Dat Vietnam Aviation Academy 104 Nguyen Van Troi, Phu Nhuan District, Ho Chi Minh City, Viet Nam. |
Tran Vu Van Hoa Ho Chi Minh City University of Transport 2 Vo Oanh Street, Binh Thanh District, Ho Chi Minh City, Viet Nam. |
Abstract – Managing construction costs is a critical issue for construction companies. The article provides an overall assessment of Hoang An Joint Stock Companys performance in this area to identify the major cost- management related problems the company is currently facing and then propose relevant solutions to these. The study shows that the company is currently facing significant problems related to construction project management, machinery and equipment utilization, and human resource costs. Based on the nature of current problems, a number of relevant solutions are then proposed including project selection (project formulation and appraisal), contractor selection, project supervision and construction control (time, cost, quality, and risk) based on the nature of the identified problems and guided by relevant theories.
Keywords: Management, cost, efficiency, investment, construction works.
-
INTRODUCTION
Managing construction costs including those associated with human resources, equipment, and fuels is central to managers planning. During the whole project implementation process, the major aspects of cost management are general planning, disclosure, and investing. Cost management affects construction companies profits, making it essential for managers to control construction costs effectively [1].
Cost is defined as an amount that a business or individual incurs to achieve a certain goal. Construction costs of a project are the total costs incurred when building, repairing, renovating or expanding construction works. These costs are normally indicated by the criteria for the total investment of
the project during the whole construction process. These are affected by the estimated construction works and the value of payments and settlements of the investment capital when the construction project is finished and is in full operation [1,2].
Generally, the management of construction projects costs must comply with the following principles [3]:
Principle 1: To facilitate the achievement of construction projects objectives and effectiveness; meet the market economys requirements; and be simple, clear and easy to implement.
Principle 2: To be suitable to construction investment stages, design steps and types of capital sources; and comply with relevant state regulations.
Principle 3: To allow construction works prices to be determined by the law of value, the law of supply and demand, and the law of competition. Given that construction projects usually take years to complete, price fluctuations in markets for factors of production are inevitable. As a result, there should be a mechanism to account for price fluctuations during the whole process.
Principle 4: To understand the characteristics of construction works prices.
Principle 5: To determine construction works prices based on the nature of the works and design steps. This process must ensure the correctness, completeness, reasonableness, and conformity with actual market requirements.
Principle 6: To secure the states dual role as both a regulator and an investor (sponsor). It is essential that during
the whole process, these two roles need to be always clearly distinguished.
In the construction industry in general and the transportation industry in particular, cost management has been a significant concern and there has been a prominent need to find out an effective solution to enhance efficiency in this area [4]. For example, the study on the construction of irrigation works in Hung Yen province examines the major problems related to the cost management of irrigation construction projects using the state budget. There is another research on how to strengthen the cost management of construction projects by North River Ma Thanh Hoa Water Resource One Member Limited Liability Company which investigates cost-management related problems in all stages (policy, survey, design, design appraisal, project evaluation, and settlement) [5].
What is a cost overrun of a transportation project? What problems does it cause? How should overruns be measured? How common and prevalent are overruns worldwide? What are the potential ways of avoiding overruns? These are the questions that the authors address in their article, and the rationale is to provide a brief and comprehensive overview of all of these topics. They show different measures for overruns and recommend when and why they are useful. Furthermore, the authors rebuff earlier findings that cost overruns are more prevalent than underruns. Finally, the researches argue that, among several potential measures proposed in the literature to eradicate overruns, quality assurance of estimates is one of the most effective measures [6].
In recent years, Hoang An Joint Stock Company (hereafter Hoang An) has seen a significant decline in its business activities, which can be seen clearly in the declining number of its traffic projects from the companys annual reports. Especially in 2020, the countrys economy is affected by the Covid-19 pandemic which has a severe impact on the transportation industry. The company has been also influenced by problems including limited supplies of construction materials, increased material and fuel prices, decreased solvency, and financial imbalance, all affecting the implementation of its projects. As an officer working at the company, with the desire to contribute to its development, I have chosen to investigate the problems the company is having in the area of cost management as it is critical to the companys employment and financial performance.
-
RESEARCH METHOD
In this research, authors will apply the knowledge acquired through real work experiences and from related research documents to analyze the companys current problems and then recommend relevant solutions to these. This article collects data on the problems related to cost management at the company and utilizes the views from leaders and experts who are directly involved in project implementation at the company. The methods used to implement the research therefore include synthesizing and analyzing statistics, consulting with and interviewing leaders and experts, and exploring relevant literatures.
Fig. 1. The research process
-
REALITY
-
Introduction of Hoang An Joint Stock Company
-
The formation and development of Hoang An Joint Stock Company
Hoang An Joint Stock Company was established on March 1, 2003. Is a private enterprise operating mainly in the fields of construction of traffic works, public and civil works, construction of infrastructure, and repair construction rake peeling recycling. The company has invested in a number of the countrys major projects such as the Southern Coastal Corridor Project (Package CW7/2 built from Nga Bac to Ca Mau, Km170 + 900 – Km190 + 800), the project connecting the central area of the Mekong Delta package CW1A leading the north road to Cao Lanh bridge Km0 + 000-Km3 + 800), Repair Project Comprehensive Asphalt Foundation and Carpet Treatment for Road Surface Km1928 + 850 – Km1932 + 603, Km1935 – Km1940 National Highway 1 of Long An Province, Trung Luong – My Thuan Expressway Project (phase 1) in the form of a BOT contract, etc. [7]
In the future, the company aims to develop its brand name in areas of construction of transport works as well as repair works for recycling. The company also constantly enhances its technical capacities and measures and management systems to improve its competitiveness. It has improved management processes under the motto Never stop learning and creating.
-
Business results in recent years of the company
TABLE I. INCOME STATEMENTS OF HOANG AN [7]
TT
Content
Year 2017 (VND)
Year 2018 (VND)
Year 2019 (VND)
1
Total assets
950.572.192.427
853.461.249.610
742.471.247.623
2
Total Liabilities
752.415.407.523
636.751.022.435
553.943.516.790
3
Short -term liabilities assets
571.771.029.722
623.035.766.727
542.011.887.765
4
Short -term liabilities
553.504.904.472
432.800.525.151
376.516.152.347
5
Net revenue
165.240.952.611
248.746.842.653
216.398.083.324
6
Total profit before tax
120.336.867
75.550.686
66.774.367
7
Total profit after tax
96.269.494
60.440.549
53.419.494
From the performance reported in Table I, it is clear that there has been a decline in the companys business activities, especially in 2018 with pre-tax profit down 37.2% and short- term debt up by 33.7% year-on-year. Also, the companys revenue in 2019 decreases by more than 50% year-on-year. The declining financial performance has had a significant impact on the implementation its current and future projects.
-
-
Construction cost management at the company
-
Cost planning
It appears that the company is not well aware of the important role of cost planning as an effective means of managing construction costs. Management is one of the important bases for cost control in the following stages. Cost planning is only shown through the management of planned and accepted work volumes and there is no comprehensive management in terms of work volumes and unit prices. Moreover, cost planning has not been performed with adequate frequencies. Currently the company is just doing that monthly, quarterly, and yearly [8].
Arranging the companys lists of scattered projects, it seems that cost planning is not close to approved implementation schedules and annual implementation volumes. For example, there are projects that require significant amounts of capital but do not have a capital plan while there are projects that require negligible amounts of capital but secure huge amounts of funding. The annual planning work is also very important since it is the premise for the harmony to promote production. The layout of cost planning is not suitable for projects, resulting in the lack of capital, which in turn leads to delays to construction projects [8].
-
Personnel and process
The companys cost control has been mainly implemented through contracts, payment plans in phases, volumes of acceptance, and completion records. Cost control has a number of problems such as the lack of staff as well as detailed cost tracking for each project. Browsing through many departments and levels is time consuming, costly, and sometimes inconsistent.
The arrangement of employees in the company is not good and labor management is ineffective, leading to a surplus of indirect labor but a lack of direct labor, especially among the technical team.
The quantity and quality of personnel have not yet met the job requirements. The lack of professional and capable personnel in project design and formulation leads to a number of projects having to contract with construction drawing- designing units and hire consultants to verify estimates.
Personnel in the company changes frequently, thus causing difficulties for organization and management, due to the inability to take advantage of long-term personnels experiences, especially during important projects like QL1A which is a big project with a short duration. A team of experienced personnel normally estimates the total investment for a project. However, during the implementation phase, these officers change jobs and the new personnel cannot secure the required capital and the total investment must be therefore recalculated, incurring unnecessary costs.
-
Problems of controlling construction costs
Checking and accepting works are sometimes slow, affecting construction progress as the Executive Board and subcontractors have not prepared the acceptance documents well. Legal documents are usually loose and inaccurate, creating opportunities for parties to take advantage of the complete payment volume profile and hence seriously affecting the company. Since the supervision of departments has not been carried out regularly as required by regulations, the quality of acceptance test is still limited and there are issues related to skipping stages, testing through loudspeakers, and contracting contractor acceptance procedures, etc.
Being passive in the process of finding materials and fuels for construction projects and having limited strategic partners lead to high costs as the company has to purchase materials including sand, stone, steel, cement, etc. at high prices. For example, the unit price of sand for some projects such as Trung Luong – My Thuan Expressway Construction Project (phase 1) and Mid-Region Connection Project Center of the Mekong Delta (package CW1A the north Cao Lanh bridge Km0 + 000-Km3 + 800) is 10-12% higher than estimated.
Incurring additional costs is a common problem in construction. This is because additional works may be
generated, thus changing relevant terms in contracts. However, the problem that exists at the company is that additional costs have been very significant. Project Trung Luong – My Thuan Expressway (phase 1), implemented by the construction unit Tung Anh Construction Joint Stock
Company, Ha Transport Company provides an excellent example for this problem. The contents of construction of roadbeds and Kenh Xang bridges have the following quantity payments in Table II.
TABLE II. PAYMENT VOLUME FOR ROAD FOUNDATION, KENH XANG BRIDGE [7]
TT
Description
unit
BOQ Quantity
Quantity This period
Variation Order Quantity
%
1
2
3
4
5
6=5-4
9=6/4
I
Road
1
Driven Precast Piles (450 mm x 450 mm)
100m
63,000
143,010
80,010
127,0%
2
Site clearing
100m²
14,172
25,748
11,576
81,7%
1
Embankment construction from borrowing
100m³
81,790
204,475
122,685
150,0%
4
Granular Backfil
100m³
1,240
1,860
0,620
50,0%
II
Bridge
1
Concrete Class C35 Mpa
m³
84,325
116,350
32,025
38,0%
1
Concrete Class C30 Mpa
m³
0,120
0,240
0,120
100,0%
2
Concrete Class C10 Mpa
m³
15,068
49,793
34,725
230,5%
3
Reinforcing steel
tons
1,879
6,636
4,757
253,2%
The high work volumes generated make it difficult for both the company and contractors to handle, thus slowing construction progress because contractors do not have enough financial capacity to continue the construction and have to wait for the company to pay. However, getting the funding approved is a rather complicated and time-consuming procedure, leading to a backlog of initial investment costs.
-
Estimated costs
-
Basically, the estimation must comply with the guiding circulars of the competent state agency. However, there are some problems as follows:
The failure to continuously update new regulations on the management of construction costs, leading to a large number of works still being prepared under old circulars and decrees (leading to mainly errors in the cost structure of the total investment estimates)
The inaccuracy in the survey and design work for a number of projects, leading to an adjustment of the cost estimate
Shortcomings in the calculation of jobs and items in the estimates
The inappropriate selection of input prices.
Most of the engineers responsible for the estimation of works claim that prices of input factors greatly affect costs of building works. The determination of contingency costs is not appropriate and close to reality. Contingency costs are still determined by the old method, i.e., calculated as a percentage of costs of construction, equipment, site clearance compensation, project management, and private costs. Problems and other costs that are not based on implementation time and are therefore not close to actual costs. As a result, in the construction process, if there are risks due to generated volumes or price slippages, current levels of provision cannot be sufficient. A typical example is the NH1A Upgrading and Expansion Project of the southern part of Ben Thuy Bridge – Ha Tinh City (Table III), which shows the difference and the cause of the difference between the total estimate of the project before and after the appraisal.
TABLE III. THE RESULTS OF THE VERIFICATION OF TOTAL INVESTMENT IN THE PROJECT OF UPGRADING AND EXPANDING NH1A, SECTION SOUTH OF BEN THUY BRIDGE – HA TINH CITY [7]
STT
Contents
Total investment (VND)
Verification results (VND)
Difference (VND)
1
Construction costs
1.421.368.217.000
1.481.140.069.317
59.771.852.317
2
Site Clearing costs
414.937.230.760
414.937.230.760
–
3
Other costs
11.717.729.000
8.958.552.000
-2.759.177.000
4
Loan interest
179.394.000.000
–
-179.394.000.000
-
-
REASONS
-
Management capacity
As mentioned above, there is currently no separate management team at the company. The companys cost management activities are still mainly in the hands of departments due to the decentralization of responsibility within the company. However, the capacity of the members involved in cost management is usually weak and the work of cost management therefore has not been done effectively. The main reasons are:
The lack of building and training a team of core management staff
The lack of effective strategy and plan to attract, recruit, use and develop resources
-
Market activity
Market price fluctuations are shown through fluctuations of 3 main components including material cost, labor cost and construction machine cost. A prominent feature of construction projects is that they consume vast amounts of materials. As a result, even a slight increase in prices of inputs can lead to a significant rise in costs. High inflation together with fluctuations in input prices have resulted in significant financial difficulties for both investors and their contractors. These also make financial planning and cost management become much more challenging.
The lack of materials or scarcity will lead to an imbalance between supply and demand, which inevitably results in kinds of materials being forced by suppliers. Investors and contractors are forced to accept high prices for construction if they do not want to stop the construction. The inevitable consequence of this high price pressure is an increase in investment costs.
-
Inaccurate calculations
Material prices are changing constantly while cost estimates may not be timely updated. Cost estimates can be inaccurate due to incomplete information, lack of careful calculations or intention. In addition, they can be cut unjustifiably during the appraisal and approval process, and later require additional approval. The resulting cost estimates can be made late, even after a work item has been constructed so it has no effect on cost management.
Inaccurate estimates make it difficult to select construction contractors and control costs in the later period. A suitable method has not been developed to determine contingency costs. Contingency costs are often much lower than actual costs incurred during the construction process.
-
Unmanaged incurred work volumes
Construction is a complex field, related to many socio- economic fields and environmental factors. Removing the negative factors that cause the generated volumes are challenging. In fact, even if a project has been surveyed and
calculated carefully, it is inevitable that work volume will increase during the implementation process. It is possible to explain many reasons leading to the generation of additional work volumes as follows:
-
A sketch of the project with details about its size, design, and location may not match its real characteristics, natural conditions, socio-economic conditions, development strategies, and analysis of project effectiveness. This then leads to the need to adjust the project in the following periods.
-
Survey records and designs are incomplete and therefore must be modified during the construction process, resulting in a change in costs when settling.
-
There is usually inaccurate estimation due to extracting wrong volumes, applying inaccurate unit prices and norms, etc.
-
-
Really
The cost estimation dossier usually does not clear the type of materials. According to the current Construction Law, in order to combat the negatives, the supplier name is not specified in the design documents of the materials used for the works. As a result, cost estimates tend to incorporate unrealistic unit prices because prices are closely related to the types of product, the supplier, etc. During the construction process, it is certain that builders have to choose a category that is clearly approved by the company. This explains why the settlement value will certainly differ from the original estimated value. [6]
In addition to the volume incurred, changes of unit prices also have a great impact n the costs incurred. Changes in unit costs of works in company-owned projects are often due to the following reasons:
-
The increase in the prices of raw materials
-
Changes in policies and regimes related to salaries of employees
Between the above reasons, the first one is usually the main reason leading to the adjustment of unit prices, incurring costs and making investment costs significantly higher.
-
-
Weak financial capacity
The companys financial capacity sometimes fails to meet its capital needs, due to its responsibility to implement a number of projects at the same time. Implementing multiple projects at the same time requires it to spread the available capital across these. Moreover, as the form of capital mobilization at the company involves a lot of legal procedures, delays in payment, supplying equipment, etc. for contractors have been common, leading to delays and stagnant capital for construction units and companies.
-
Ineffective site management and supervision
The contractors site management includes all management tasks to ensure the site operates continuously and smoothly such as quality control, construction progress, worker management, and technical staff [1]. Tasks such as planning materials in and out, planning material supplies,
allotments at work, assignments, cost checking, salary payments, relationships management, etc. will need to be duly performed. However, the company is facing the following problems:
-
Infeasible construction organization plan;
-
Lack of qualified personnel to perform the job;
-
Unreasonable supply of human, machinery and materials;
-
Scheduled delays;
-
Delays in checking and accepting the completed work;
-
Delays in conducting a test and accepting the error;
-
Failure to comply with the acceptance procedure;
-
Delays in reporting performance and problems arising to the supervision consultant or the investor;
-
Lack of ongoing monitoring;
-
Loose site discipline supervision on labor safety, construction order, etc
-
Absence of favorable conditions for staff to work effectively failure to acknowledge workers material and spiritual life and promote their spirit.
-
-
Cost management tools
The companys management methods and tools are still traditional, simple and only performed by a few staff members. As a result, the effectiveness of cost management has not been enhanced and it is both time-consuming and costly.
Contractors cost management is more complicated than the investors as it involves more accounting. Therefore, if the contractor does not use advanced methods and tools to manage costs, uncontrolled implementation costs may incur.
-
-
PROPOSED SOLUTIONS
-
Completing the cost management process
Reforming the cost management process is now an important issue for companies. A sound and scientific cost management process has been shown to be the basic foundation for management activities and will be implemented by the expense manager. This process is divided into three phases as Fig. 2.
-
Estimation stage
-
Required
To gather the necessary documents to facilitate the cost estimate in accordance with each price indicator, being aware of the need to update adjusted estimates and manage risks
To ensure the match between the workload in cost estimation and design, with careful check of the workload before a cost estimate is made
To determine the amount of advance capital for the contractor during the early stages based on current regulations
To build a system of statistics on norms, unit prices, and methods to determine input data such as material prices, labor costs, etc.
Fig. 2. The construction cost management process at Hoang An company
-
Implementation content
To use different necessary estimation measures and tools to ensure the accuracy required to implement next steps
-
-
Cost planning stage
The cost plan is made after the budget for the project has been made.
-
Required:
To gather the necessary grounds for cost planning
To develop an appropriate cost plan to facilitate the cost control in the following stages
To disseminate the cost plan to managers or related subjects
-
Implementation content:
Depending on the purpose of the user and the job requirements, a cost plan can be developed for (1) each item or department or (2) according to the cost category.
To ensure the level of detail in the cost plan depends on the level of time detail.
To show the cost plan in form of a S-line, a column or a combination of these two.
-
-
Cost control stage
-
Cost control system for contractors
Implementation sequence (Fig. 3).
-
Cost control system
Required:
-
To collect full data on cost performance situation which will be usually statistically reported by the expense manager in the cost performance status report;
-
To collect approved change requests. Implementation content:
-
To compare the actual cost to the cost plan;
-
To perform value system analysis to determine the cost status of the project and identify its key drivers;
-
To suggest relevant solutions;
-
To perform budget forecast for the next period;
-
To submit the change request to the authorized person for approval.
Fig. 3. Cost control system for contractors.
-
-
Change control system
It is essential to strictly and fully control the changing requirements (arising volume, design change, unit price change, etc.) which are submitted to competent persons for consideration and decision to ensure the benefits of the parties involved in the project as well as achieve the projects goals.
-
-
Adjustment and approval work
This task will be decided by the Appraisal Council of the company including:
-
Chairman of the Board;
-
General Director;
-
Deputy General Manager in charge of construction;
-
Department of Technical Planning;
-
Department of Financial Accounting;
-
Department of Expense Management;
-
Department of Construction Project Management.
-
-
Final settlement of contract
A contract settlement dossier is made by the contractor, right after the project has been in full operation.
-
Handling of investment capital
The Department of Expense Management prepares and submits the plan to the authorized entity for decision.
-
-
Improving cost management staffs skills
The company needs to invest adequately in training and developing an effective team of cost managers.
-
For cost managers
The proposed solutions are:
To encourage cost managers to attend professional training courses on Valuation Engineers at facilities licensed by the Ministry of Construction;
To create favorable conditions for cost managers to have a valuation engineer certificate in accordance with the relevant regulations;
To facilitate participation in relevant training courses to improve cost management skills and construction investment policy mechanisms;
To develop a suitable strategy to promote the companys human resources on cost management to suit each stage.
-
For the Department of Financial Accounting
To ensure there are sufficient certified cost managers, as required by the companys management;
To be responsible for management consultancy when the company registers to do business in cost management consultancy;
To formulate appropriate and effective economic leverage policies to enhance the responsibilities and benefits of the companys management;
To build an efficient and active working environment.
-
-
Strengthening the labor force
Through the analysis of the management and employment problems at Hoang An Joint Stock Company, it is clear that the company should adopt relevant measures to attract highly skilled and experienced employees. Recruiting, training and
improving qualifications for managers and workers to meet production needs are essential. In addition, it is important to arrange the labor force and reduce the auxiliary labor for each phase. To do that, the company needs to organize and re- design the workforce within the organization at all levels as follows:
-
To actively research and apply technical advances, new equipment and effective management methods to increase the progress of digging, increase labor productivity, and reduce the weak labor force
-
For departments: To arrangement the management by reassigning the functions and tasks between departments more clearly and reasonably and ensure labor between departments should be reassigned in accordance with each projects requirements
-
For the executive boards and construction teams: To fully utilise the capacity of equipment, machinery and people, especially when urgent progress is required, thus causing a need for arranging overtime labor. The implementation of construction techniques should be regularly inspected and encouraged. They should also maintain the correct regime of regular and periodic maintenance and repair of means of transport, machinery and equipment mobilized and gathered at the project.
-
-
Strengthening material and equipment supplies
To estimate the use materials and then improve the construction efficiency effectively, the company needs to set up a material purchase unit to find suitable long-term, strategic partners and sources of raw materials assigned to production units. Material demand needs to be planned monthly based on the companys general plan. Specifically:
-
Monthly, based on production goals, business plans, technical and economic norms, and quantity of materials in stock, the unit shall estimate the demand for necessary supplies and equipment of production units
-
The unit should actively procure materials to promptly serve production, minimize unscheduled purchases, and reduce unreasonable inventories
-
The unit should train a team of capable technicians to effectively forecast the need to replenish materials, machinery, and equipment during the production process. The team shall also utilise IT in managing materials and equipment to provide necessary information to managers and users, ensuring timely supplies of materials.
-
-
Using technology in cost management
-
S-Curve software for project management
S-Curve software for Microsoft Project is used to construct S-curves for a single master project or selected activities [1]. The three curves presented include the plan line, the actual curve, and the value curve obtained for a given project. S- Curve can allow managers to visually see projects using S- Curve graphs. Progress and tempo are displayed with a baseline (See Fig. 4).
-
CendiBuilding 2: construction cost management software
-
CendiBuilding 2 is a software capable of managing and classifying construction costs, thus helping to synthesize necessary and accurate reports which allow managers to timely monitor projects financial standing. The software is suitable for individual contractors or small businesses in the fields of construction and interior decoration or these with the construction function.
Fig. 4. S-curve monitoring chart [1]
-
-
CONCLUSIONS AND RECOMMENDATIONS
-
Conclusions
Effective cost management allows construction companies objectives to be achieved. To ensure this, it is essential that the whole project, from the first stage of investment preparation, must be implemented appropriately, with full consideration for contractor selection, time management, progress, risk, quality, etc. as they are decisive factors which influence their ability to achieve their objectives. In other words, improving the efficiency of cost management must be an on-going process during the whole construction process. This essay has made the following major contributions:
-
Systematizing basic theoretical issues related project management and project cost management to clarify the nature, objectives, requirements and content of construction costs at the firm level. This forms the foundation for assessing the current problems and proposing solutions to these.
-
Providing a comprehensive analysis and assessment of the current problems at Hoang An Joint Stock Company during the 2017-2019 period.
-
Proposing a number of solutions to improve cost management in related areas – project selection (project formulation and appraisal), contractor selection, project supervision and construction control (time, cost, quality, and risk) based on the nature of the identified problems and guided by relevant theories.
-
-
Recommendations
To facilitate smooth and effective coordination between departments within the company;
To enhance the application of information technologies in cost management: 1) modernize IT equipment and apply new analysis and calculation techniques to access and process information promptly to guarantee timeliness, accuracy, and efficiency; 2) apply suitable software programs to analyze and evaluate projects to improve the quality of evaluation results;
3) apply IT to systematize management, exchange information between departments, and administration.
REFERENCES
[1] PMI, A Guide to the Project Management Body of Knowledge (PMBOK Guide) – Seventh Edition, 2021. [2] Bon-Gang Hwang, Ming Shan, Lei Zhu, Wai-Cheng Lim, Cost control in megaprojects: efficacy, tools and techniques, key knowledge areas and project comparisons. International journal of Construction Management, Volume 20, 2020 – Issue 5, pp. 437-449. https://doi.org/10.1080/15623599.2018.1484976 [3] Thai Ba Can, Financial management in the field of construction investment. Financial Publisher, 2003. [4] Jeremy Sharib et al., Cost-effectiveness of consensus guideline based management of pancreatic cysts: The sensitivity and specificity required for guidelines to be cost-effective. Surgery, Volume 168,Issue 4, 2020, pp. 601-609. https://doi.org/10.1016/j.surg.2020.04.052 [5] Pham Duc Huy (2017), Proposed solutions to the enhancement of the
cost management of irrigation investment projects of North River Ma
Irrigation Co., Ltd. – Thanh Hoa
[6] Donald Towey, Cost management of construction projects (1st Edition). Wiley-Blackwell, 2013. [7] Year-end report 2017, 2018, 2019 at Construction Investment Cost Mangement Hoang An Joint Stock Company. [8] Policy of Hoang Ans Joint Stock Company. [9] Vietnam Construction Law, 2014. [10] Vietnam Law Amending and Supplementing a Number of Articles of the Construction Law, No. 62/2020/QH14, The National Assembly, 2020.