
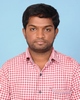
- Open Access
- Authors : G Praveen Kumar , Cn Nandakumar
- Paper ID : IJERTV12IS010005
- Volume & Issue : Volume 12, Issue 01 (January 2023)
- Published (First Online): 16-01-2023
- ISSN (Online) : 2278-0181
- Publisher Name : IJERT
- License:
This work is licensed under a Creative Commons Attribution 4.0 International License
Determining The Effect of Welding Parameters of Friction Stir Welding on Al 64430 (Aluminium) and Cu 46400 (Copper)*
G Praveen Kumar
Cyient Hyderabad, Telangana, India
CN Nandakumar Cyient
Hyderabad, Telangana, India
Abstract The experiments described mainly about the procedures for the joining of Al (64430) and Cu (46400) with the help of solid state stir welding procedure. The setup of joining the two dissimilar metals is mainly due to the increase in demand at industrial level application. A hybrid structure and reducing the cost to weight ratio of the component. These experiments also give a scope on weld ability of Al and Cu with varying melting points and its effect on welding parameter such as rotational speed, welding speed to achieve the prefect joint. A comparative study is performed on tool pins, which is designed and manufactured for welding the Al, and Cu. Edx (Energy- dispersive X-ray spectroscopy) is performed to analysis the defect and to understand the micro structural behavior of the joints.
Keywords Aluminium (Al); (Cu)Cupper; mechanical properties; frictio stir welding; melting points; circular ; taper; tensile;hardness;RPM(revolution per minute ) ; microstructure ;
I. INTRODUCTION
This paper deal with the joining the two dissimilar metals with the help of fabrication process that is welding where high heat to melt the parts binding and allowing them to cool causing the fusion. The difficulty of making high strength, fatigue and fracture resistant welds in there are many type of welding process from which Thomas Wayne discovered the FSW (Friction stir welding) in the year 1991. which was well known in that in those days. Welding all aluminum alloys, including those that cannot normally be joined by conventional fusion welding techniques such as aluminum- lithium alloys. Dissimilar aluminum alloys can also be joined.
-
Welding of dis-similar metals.
In traditional or fusion welding the material must be melting and re solidified, but in case of FSW, the joint is in solid state it never melts. Instead, the joint is created below stipulations of extreme plastic deformation the massive distinction between FSW and fusion welding (other than the lack of melting) is the capability to manipulate top temperatures with the aid of desire of extraordinary welding parameters. This can be achieved accurately through simulation of the process using Simulation software like ANSYS10.0 software. This will reduce the time for simulation. FSW offers the capability to manipulate the homes of the steel and tailor them for one-of-a- kind applications, and viable to optimize tensile strength, fracture toughness, or fatigue resistance based totally on the particular application. [5]
Fig:1 : (FSW) friction stir welding is used for joining the two dissimilar
metals [15]
-
Friction stir welding
Due to its advantages over conventional joining procedures, friction stir welding has drawn interest from all over the world since it was first developed. FSW is essentially a local thermo- mechanical metal working procedure that modifies local properties without affecting those of the rest of the structure. Additional adiabatic heating is added throughout this process from metal deformation. The pin and shoulder of the tool can be altered in a variety of ways to affect material flow and the development of microstructures, as will be discussed later. [8] The material to be treated is entered with a rotating tool with a pin and shoulder, which is then moved along the line of interest (Figure-1). To perform FSW, the tool and the processing area are shifted in relation to one another so that the tool traverses the area in overlapping passes until the entire area is processed. Friction Stir welding has opened up a new process for inducing directed, localized, and controlled materials properties in any arbitrary location and pattern to achieve revolutionary capability in high value-added components. Friction stir welding provides the ability to thermo-mechanically process selective locations on the structures surface and to some considerable depth (>25mm) to enhance specific properties. Research is being increasingly focused on this aspect of the technology for usage with alloys for automobiles. For instance, the suspension and driveline of cars are made of cast aluminum alloys like A319, for example.
A fine, equi-axed grain morphology with a banded, bimodal grain size of 1 to 5 microns is produced by FSW. When subjected to super plastic circumstances of high temperature and dynamic strain, the microstructure of friction stir-welded aluminum alloy is typically stable. High-angle grain boundaries can improve super plasticity and related grain boundary sliding. However, a homogenous distribution of equi-axed grains with a minimal grain size is necessary for optimal super plasticity. For any particular set of treatment settings, FSW microstructures do not have a uniform grain size distribution. The size of the grains vary from top to bottom and from the side that is moving forward to the side that is retreating Numerous researchers have shown the capability of friction stir welding to modify the local microstructure through thermomechanical functioning. [10] The heat produced at the point where the tool and work piece meet is one of the crucial components in the FSW process. This heat is what propels the FSW process forward. The heat flow must be maintained at maximum levels while the temperature in the work piece remains low enough to prevent melting and high enough to make the material pliable enough for the pin to stir. According to Tangential measurements, the maximum temperature produced by the FSW process ranges from 70% to 90% of the melting point of the work piece material (1988) and Cole Grove et al. (2000), so that welding flaws and the significant distortion that is frequently connected to fusion welding are reduced to a minimum or eliminated. [5] The friction and deformation process predominantly produces the heat flux in friction stir processing. Both the tool and the work item are subjected to this heat transfer. A successful process is determined by the quantity of heat transferred into the work piece, which is in turn determined by the quality, form, and microstructure of the processed zone, as well as the residual stress and distortion of the work piece. The life of the tool and its capacity to generate a high-quality processed zone are determined by the amount of heat applied to the tool. For instance, inadequate heat produced by friction could due to the material not being sufficiently soft, causing the tool's pin to shatter. Understanding the friction stir welding process's heat transport component is crucial for both science and optimizing the uniqueness of the process. For instance, this template's head margin is proportionately larger than usual. This measurement and others are intentional; they follow guidelines that assume your paper will be a component of the full procedure and not stand alone. Please don't change any of the labels that are currently in place. [3]
1.3. Types of Friction stir welding tool materials.
Materials with the potential (in terms of high temperature strength) to be utilized as FSW tool probes for welding aluminum alloys include intermetallic alloys, silicides, Laves phase alloys (two phase Nb-Ti-Cr alloys), iridium alloys, and ceramics. The majority of these materials, however, have very poor fracture toughness and break quickly via brittle fracture when employed as friction stir tools, according to earlier research at TWI. Thes materials are both difficult to source and difficult to manufacture using the FSW probe geometrics that are currently thought to be required to produce high-
quality welds. Friction stir welding tool materials for (Al alloys)
-
Hot work tool steels AISI H13 HWTS has been used extensively)
-
High speed steels.
-
Superalloys (Ni- and-Co-based)
-
Cemented carbides (WC-Co-have limited use)
-
Tool design
-
EXPERMENTAL PROCEDURE
In order to understand the bonding of welding metals firstly we should know the selection of metals according to the introduction
Fig:2 : (FSW) Tool design with its abbreviations [16]
Background
Over the past 30 years, a huge variety of Friction Stir Welding (FSW) tool probe and shoulder designs have been created all over the world, many of which have been successfully employed and some of which have even been patented. However, standards and specifications like BS EN ISO 25239- 1:2020 friction stir welding aluminum and AWS D17.3/D17.3M:2016 specification for friction stir welding of aluminum alloys for aerospace applications have never included a standard FSW tool probe shoulder design. There are already a few businesses offering "off the shelf" FSW tools, despite the fact that there is no standard probe shoulder design for FSW instruments. However, the bulk of FSW users regard the designs of their FSW tools as confidential, and as a result, there are very few articles in the public domain.
-
Basic principles
-
In order to discuss how a FSW tool is designed, we first must understand its various roles. In order to create a solid-state weld between two pieces of metal, the FSW tool probe and shoulder combination is rotated and inserted into the interface between two plates or sheets while being applied axial force,
as shown in Figure 3. This keeps the FSW tool in the proper position throughout the weld cycle. It is crucial that the plates or sheets are held in place in a clamping fixture by a steel backing bar on the underside. This bar serves as a response to the axial force. In order to prevent the plates or sheets from splitting when the FSW tool travels along the weld contact, side clamping is also necessary. When the aluminum alloy has been sufficiently softer, the tool is moved over the weld interface. Rotation of the tool causes frictional heating and softens the weld interface region. The thread form on the probe body disrupts the softened weld zone material as it rotates and moves across it. [13] It also crushes and disperses any oxide layer at the joint surfaces. Complex forging and extrusion take place, and softened material is transported 180 degrees from the leading edge to the trailing edge of the probe. Because of time, temperature, and pressure, a solid- state weld is produced. A compressive force is applied to the surface of the plates/sheets while the rotating shoulder (illustrated in Figure 3) travels along the weld contact, heating and confining the softened material underneath. The plates/sheets can be joined using lap welding or butt-welding approaches.
Figure 3. take from a FWS book
2.1.4 Early Developments
The starting point for the design of the FSW tool setter was a simple parallel-sided (cylindrical) threaded probe body that became the first commercially successful probe in 1995. Since then, TWI has gradually developed his family of FSW tool setters as shown in Fig. 3. The thread profile is cut to the left of the probe body. [8]
Figure 4. [12]
2.1.3 Tool-Design-Evolution
As FSW development progressed, commercial users of the process required higher welding speeds in much higher strength aluminum alloys, hence the MX-Triflute probe. A version of the MX-Triflute probe is shown in Figure 3. It is not obvious, but the body tapers slightly. The tapered probe body shown in Figure 2b and the three evenly spaced spiral grooves move much less material during the welding cycle than the original cylindrical body probe, thus maintaining high quality. While achieving much higher welding speeds. The three tip flutes and the MX thread form broke the material in the weld more actively, generating frictional heat faster and improving the efficiency of the FSW process. [2] The MX-Triflate FSW Tool Probe is typically used for thin welds <15mm>15mm. FSW tool shoulders are generally simpler in design than probes. The tool shoulder is not necessarily parallel to the workpiece surface. For simple straight welds, the tool is often tilted, causing the trailing edge of the shoulder to penetrate the workpiece and apply additional forging pressure. Dose etc. (1995) developed a concave shoulder design that works reliably at an operating angle (tool tilt) of 23 degrees (Fig. 3a). The desire to improve the welding speed of 5xxx series aluminum alloys led to the development of the spiral shoulder (Figure 3a-b). This shoulder face has a spiral machined into the shoulder face that pulls material from the outside edge of the shoulder into the root. Probes (Dawes et al Thomas, 1999). The idea was developed to facilitate vertical flow of material, but initial trials showed that such design changes also enabled the use of vertical (zero-pitch) tools. rice field. This shoulder design is commonly used today for applications requiring weld paths in two and three dimensions. The shoulder profile of the tool greatly influences the generation of frictional heat during FSW. A tool shoulder profile that restricts material flow such as B. Snail provides maximum heat delivery due to increased surface area. Therefore, a reduced volute shoulder diameter can be used. This has proven particularly beneficial as joint designs and weld paths become more and more
complex. Tooling design is often driven by joint geometry constraints.
Figure 5.
Fig 6. Existing tool
-
Experimental procedure for FWS
-
Types of Friction stir welding tool designs (Developed tool designs)
-
Straight circular threaded.
-
Taper circular threaded.
Fig 7. Straight circular threaded.
Fig 8. Taper Circular threaded.
Table 1. Tool Specifications.
Specifications.
Straight circular thread.
Taper circular threaded.
Shoulder diameter
High speed steel
High speed steel
Pin diameter
18 mm
18 mm
Pin length
6 mm
6 mm
Thread orientation
5.7 mm
5.7 mm
Thread angle
Anti-clock wise direction
Anti-clock wise direction
Thread pitch
60 degrees
60 degrees
Thread pitch
1 mm
1 mm
-
-
Material High Speed steel.
-
A typical HSS Composition features chromium (4%), tungsten (approx.6percentage), molybdenum (up to 10%), vanadium (around 2%), cobalt (up to 9%) and carbon (1%). The different grade types depend on the varying levels of elements added. Chromium improves hardenability and prevents scaling. Basic grades of HSS and their applications are summarized in Table 2.
General description |
ISO/Germany/USA steel description |
Material no. (steel code) |
Range of application |
HSS |
S 6-5-2 (DMo5/M2) |
1.3343 |
Standard tool material for most common applications |
HSS-Co |
S 6-5-2-5 (EMo5Co5/M35) |
1.3243 |
High heat resistance, especially suited for roughing or when coolant insufficient |
HSS-E |
S 6-5-3 (EMo5V3/3) |
1.3344 |
High friction resistance and cutting- edge stability, especially important for reaming operations |
HSS-E M 42 |
S 2-10-1-8 (M42) |
1.3247 |
Increased heat resistance and hardness, suitable for difficult-to-machine materials |
P/M HSS-E |
S 6-5-3-9 |
1.3207 |
High hardness, heat resistance and cutting- edge stability |
Table 2. Grades of high-speed steels (general ISO designation: S W-Mo-V-co)
The preparation of the specimens for the experimentation of FWS (friction stir welding) or the bed and tool preparation we have to do some changes such as to control the tool rotation speed and the max speed of the machine specification where the model is FWS-DC-10T-2000-CNC.
Figure 9 Machine setup
-
Conventional machining tools
The procedure of fsw is similar in phrases of precept of opera- tion of the system to different technological manufacturing techniques such as machining, deburring, grinding and drilling. All of these Techniques consist in shifting a rotating tool via a piece, generating dragging of material, which constitutes the paintings piece. Thus, it is possible to assume that a conventional machine tool, which includes a Milling system, can be used to perform fsw. However, the hundreds generated all through the fsw Technique benefit more relevance whilst this equipment is used. The loads concerned in fsw are higher than the Loads generated in the milling manner. For this reason, traditional device gear should be reinforced if you want to boom their load and stiffness talents. As a result, there are capability possibilities to modify current equipment to carry out fsw. The gadget changes may be made on numerous levels: structural, flexibility, decision-making and sensing. The structural changes are completed with a view to make the equipment extra robust (some components of equipment may be changed consisting of Methods, guides, rails, automobiles, spindles, and many others.
The ability can be extended by the advent of extra motors that offer extra stages of freedom to the equipment. Thanks to the high loads concerned within the fsw method, most of the people of the answers have carried out force control to save you gadget harm and make certain human safety and to gain true weld great. The decision-making of the device can nonetheless be stepped forward offering movement in more guidelines on the same time. Besides that, the machine may be geared up with a couple of sensors to acquire extraordinary facts if you want to be used to control the device thru an embedded manage answer.
Figure 10 Machine setup
Gadget that is utilized in (FWS) presented with one-of-a- kind traits which concerns to its bodily configuration that's specially relied on the application of welding joint. The system and gear, which displays the maximum appropriate houses need to be selected according to unique technical skills which include accuracy, sensing selections making and
versatility these talents are understood in detail in the following phase.
-
Experimentation done according to the table
PROCESS PARAMETERS |
OUTPUT RESPONSE |
||||||||
TOOL USED |
J OINTS |
TOOL ROTATIONA L |
WELDING |
TENSILE TEST |
ROCKWELLHARDNESS |
||||
SP EED |
SP EED |
(N/mm²) |
|||||||
(Rpm) |
(mm/min) |
||||||||
IMP |
1 |
IMP 2 |
IMP 3 |
AVG |
|||||
TAPERED |
JOINT |
1 |
800 |
10 |
49.595 |
62 |
64 |
60 |
62 |
JOINT |
2 |
850 |
10 |
||||||
CIRCULA |
|||||||||
R |
JOINT |
3 |
900 |
12 |
|||||
THREADE |
JOINT |
4 |
950 |
12 |
|||||
D |
|||||||||
JOINT |
5 |
1000 |
12 |
||||||
STRAIGH |
JOINT |
1 |
800 |
12 |
32.468 |
66 |
64 |
66 |
65.33 |
T |
JOINT |
2 |
850 |
12 |
|||||
CIRCULA |
|||||||||
JOINT |
3 |
900 |
12 |
||||||
R |
|||||||||
JOINT |
4 |
950 |
12 |
||||||
THREADE |
|||||||||
D |
JOINT |
5 |
1000 |
12 |
Fig 11. At evry 800,850,900,950 RPM the two materials are FWS is done as we can see in the Picture where the parts are welded at varing speed with strightcircular thread joint
Fig 12 . At evry 800,850,900,950 RPM the two materials are FWS is done as we can see in the Picture where the parts are welded at varing speed
with taper circular thread joint
5.1 Conclusion
Fig 13. Defect are formed at high RPM due to this the cracking and surface tunneling is formed
Fig: 14 Defect are formed at high RPM due to this void and cracks are formed and we have compared it with micro structural images
6: RESULTS
Voids and cracks are observed in the SEM analysis for the joints made of Taper threaded circular tool .Voids and cracks are formed due to the improper stirring of Al and Cu .From the EDS analysis it is observed that for the joint made of Taper threaded circular tool aluminum is occupied than copper due to this the tensile strength is more than the other joint .For the other joint made of Straight Cylindrical Threaded tool no defects are formed. From the EDS analysis it is observed that for the joint made of Straight Cylindrical threaded circular tool both aluminum and copper are Stirred in the equal portion so that it has very less tensile strength. Defects like cracks, surface tunneling, voids are formed they occur due to less heat input and welding parameters
REFERENCE
[1] Sheikh-Ahmad, J.Y.; Ali, Dima S.; Deveci, Suleyman; Almaskari, Fahad; Jarrar, Firas (February 2019). "Friction stir welding of high density polyethyleneCarbon black composite". Journal of Materials Processing Technology [2] Numerical simulation of three-dimensional heat transfer and plastic flow during friction stir welding. Metallurgical and Materials Transactions [3] Reliable Plant. Retrieved 7 August 2013. [4] Arora A.; DebRoy T.; Bhadeshia H. K. D. H. (2011). "Back-of-the- envelope calculations in friction stir welding Velocities, peak temperature, torque, and hardness". Acta Materialia. 59 (5): 20202028.
[5] Prado, R. A.; Murr, L. E.; Shindo, D. J.; Soto, H. F. (2001). "Tool wear in the friction stir welding of aluminium alloy 6061+20% Al2O3: A preliminary study". Scripta Materialia. [6] Hou, Z.; Sheikh-Ahmad, J.; Jarrar, F.; Ozturk, F. (2018-05-01). "Residual Stresses in Dissimilar Friction Stir Welding of AA2024 and AZ31: Experimental and Numerical Study&uot;. Journal of Manufacturing Science and Engineering [7] T. Trap, E. Helder, P.R. Subramanian [8] V. Jata, M.W. Mahoney, R.S. Mishra, S.L. Semiatin, T. Lienert (Eds.), Friction Stir Welding and Processing II, TMS, Warrendale, PA,
USA (2003), p. 173
[9] M.C. Juhas, G.B. Viswanathan, H.L. Fraser Proceedings of the Second Symposium on Friction Stir Welding, Gothenburg, Sweden (June 2000) W.B. Lee, S.B. Jung The joint properties of copper by friction stir welding Mater. Lett., 58 (2004), pp. 1041-1046 [10] J.B. Lumsden, G. Pollock, M.W. Mahoney Mater. Sci. Forum, 426 432 (2003), p. 2867 [11] C.S. Paglia, B.C. Pitts, M.C. Carroll, A.P. Reynolds, R.G. BuchheS.A. David, T. DebRoy, J.C. Lippold, H.B. Smartt, J.M. Vitek (Eds.), Pro ceedings of the Sixth International Conference on Trends in Welding Research, Pine Mountain, GA, ASM International (2003), p. 279
[12] C.S. Paglia, M.C. Carroll, B.C. Pitts, A.P. Reynolds, R.G. Buchheit Mater. Sci. Forum, 396402 (2002), p. 1677 [13] E.I. Meletis, P. Gupta, F. NaveK.V. Jata, M.W. Mahoney, R.S. Mishra, S.L. Semiatin, T. Lienert (Ed s.), Friction Stir Welding and Processing II, TMS, Warrendale, PA,
USA (2003), p. 10
[14] M. Graf, E. Hornborgen Acta Metall., 25 (1977), p. 883 [15] Welding and processing of metallic materials by using friction stir technique: A review Mostafa M.El-SayedaA.Y.ShashbcM.Abd-RaboubdMahmoud G.ElSherbiny
[16] Analysis of Tools used in Friction Stir Welding process Akshansh Mishra, Adarsh Tiwari [17] Influence of Pin Offset and Weave Pattern on the Performance of Al-Cu Joints Reinforced with Graphene Particles
[18] Design and Experimental study of Friction stir welding of AA6061- T6 Alloy for optimization of welding parameters by using Lathe Machine [19] Design and Experimental study of Friction stir welding of AA6061- T6 Alloy for optimization of welding parameters by using Lathe Machine [20] 20: Influence of process parameters and its effects on friction stir welding of dissimilar aluminium alloy and its composites -a review