
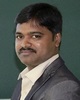
- Open Access
- Authors : Gurushanth B Vaggar , Yashwanth K , Sameer , Umar Farooq, Pavan Kumar
- Paper ID : IJERTV12IS010017
- Volume & Issue : Volume 12, Issue 01 (January 2023)
- Published (First Online): 16-01-2023
- ISSN (Online) : 2278-0181
- Publisher Name : IJERT
- License:
This work is licensed under a Creative Commons Attribution 4.0 International License
Benefits of Rice Husk Ash used in Cement Concrete: A Review
Gurushanth B Vaggar1* 1*Associate Professor, Department of Mechanical Engineering Alvas Institute of Engineering and Technology Moodbidri, Karnataka State, India. |
Yashwanth K2, Sameer3, Umar Farooq4, Pavan Kumar5, 2,3,4,5Undergraduate Students Alvas Institute of Engineering and Technology Moodbidri, Karnataka State, India. |
AbstractThe use of rice husk ash as a partial substitute for cement is one of several initiatives being taken to lessen the negative impact of the global construction industry. As of yet, there isn't a way to forecast the strength properties (SP) of mixed rice husk ash. Concrete (RHAC). In this study, of RHAC was predicted using sophisticated machine learning methods (artificial neural networks, artificial neuro-fuzzy inference systems). Considering the published using leftover industrial and agricultural materials to make alkali-activated concrete (AAC). has a chance to significantly advance sustainability objectives. The construction business demands a building material that satisfies the necessary strength and other propertystandards as outlined in Experimental research was done on theeffectiveness of a sustainable green concrete made of fly ash (FA), rice husk ash (RHA), and stone dust (SD) in place of some of the cement and sand. FA and RHA are naturally quitepozzolanic, contain a lot of silica, and have a lot of surface area. These by-products exhibit filler effects that increase the density of concrete. The results demonstrated that the FA and RHA ingredients efficiently build strength at a young age of concreteand have good hydration behavior. Concrete may be made stronger in compression and bending by using SD as a stress- transfer medium within the concrete. As a result, sustainable concrete's capacity to absorb water was less than that of regularconcrete. However, a slight loss of strength.
Keywords Rice Husk Ash. Concrete (RHAC), Strength Properties (SP), Alkali-Activated Concrete (AAC). Stone Dust(SD), Fly Ash (FA.)
-
INTRODUCTION
The goal of this study is to put it to good use. Rice Hush Ash (RHA), a regional supplement, has been discovered to be extremely pozzolanic in a positive the high expense of structural repairs concrete. [1] How to get rid of rice husk ash (RHA), an agricultural waste product, is a concern. Issue for garbage managers. Today, concrete has surpassed all other construction materials in terms of global consumption. The binder (cement) is the most expensive component of concrete; thus, replacing it in part with a more natural, inexpensive local substance like RHA would not only address the issue of waste management but also lower the issue of the high cost of concrete and Housing. The binder (cement) is the most expensive component of concrete; thus, replacing it in part with a more natural, inexpensive local substance like RHA would not only address the issue of waste management but also lower the issue of the high cost of concrete and Housing. The significance is rising. The rise in emissions of greenhouse gases (EHG) in the air is blamed for climate change. The equivalent of 54 rigatonis of in 2017, the total yearly GHG emissions were measured as carbon dioxide equivalents (CO2-
eq). [1,2] Due to the increasing growth of the construction sector, it is anticipated that both the consumption of concrete and the demand for cement will rise in the future. Due to economic and environmental factors, sustainable construction is progressively becoming more difficult. Due to the primary user of natural Resources being the construction industry, which generates a significant amount of garbage [1].
Concrete is a widely used building material that is expensive to produce since it needs a lot of different elements. Approximately 5% to 8% of the world's carbon dioxide emissions are produced. The concrete used by the building industry is used globally. Is enormous. The crucial component of concrete is cement, which is commonly used. The production of regular Portland cement (OPC) results in significant emissions that pollute the environment and produce large amounts of CO2 gas [1]. By-products, including fly ash (FA). RHA) are generated in huge quantities in India, and their waste handling contributes to environmental problems. Utilizing such a by-product as a partial substitute for OPC in concrete is one way to address this issue. Most of these byproducts were pozolanic in character. You may get RHA by eating paddy rice. The yearly the melting of the Antarctic is a consequence of increased greenhouse gas (GHG) emissions. [3,4,5] Ice caps in the Arctic. Due to this, there are now serious environmental issues on Earth. The production of large amounts of GHG is required for the installation and development of structures, as well as for the manufacturing and transportation of building materials. Buildings in the member nations of the European Union use about 50% of the entire energy used over their life cycle, which entails construction, operation, and destruction, and contribute to roughly 50% of the CO2 emissions in the environment. The demand for concrete in the construction industry is still rising.
A significant part of concrete that significantly increases GHG emissions is regular Portland cement (RPC). [7,8] OPC manufacturing causes around 5% to 8%. The high- performance cement (HPC) type called calcium aluminate- cement concrete is produced using calcium aluminate cement (CAC) as the primary binder material in the cement matrix (CACC). Additionally, the chemical makeup of CAC and regular Portland cement (OPC) differs in that CAC has a higher alumina concentration. And it has less silica than OPC does. Superior characteristics of CAC, such as its quick strength growth and strong fire resistance, make it ideal for use in environments where chemical resistance and refractoriness are required. Consequently, using CAC is a practical technique to increase fire resistance. Several elements, including the
concrete. The performance of concrete when subjected to heat depends on the constituent properties, exposure temperature and time, and cooling technique. Literature demonstrates the At room temperature, the much more stable C3AH6 and AH3 phases develop, and leads to an increase in porosity and a decrease in strength. In order to accommodate the population, there is a growing need to lower the price of ordinary Portland cement. The usage of several locally accessible materials that may be utilized as a partial substitute for Portland Cement (OPC) for civil engineering construction works is being studied.
The majority of the requirements for lasting concrete may now be met by supplemental cementitious ingredients, and blended cements are currently employed in many parts of the world. The binary mixes of ordinary Portland cement with various pozzolans in the creation of cement composites have been the subject of several research studies. RHA, or rice husk ash contrasted with OPC concrete. Later, ground RHA with smaller particles than OPC improves, according to Malhotra and Mehta (2004), concrete characteristics, such as the fact that adding RHA increases compressive strength and lowers water absorption values, are produced by larger replacement percentages. In-depth research on Brazilian recycled aggregates and Rice Straw Ash (RSA) by Corriero, Filo, and Fairborn (2009) showed that grinding boosts RHA's pozzolani city and that the high strength of RHA and RSA concrete allows for the manufacture of blocks with a good ultimate load in a rural contxt. Their research has shown that combining RHA or RSA with lime results in a weak cementitious material that might be utilized to stabilize laterite and increase the material's bearing strength. For many years, one of the main materials utilized to create buildings and other civil engineering projects has been concrete. Cement, fine aggregates, coarse aggregates, and water are combined to create a composite material. When appropriate, mixes can be added to concrete to change certain qualities in the fresh and/or hardened phases. When the substance is appropriately batched and fully mixed, the hydration process begins, and the material hardens into concrete that can withstand. [9,10,11]
Fresh concrete can be shaped into a variety of shapes and sizes due to its elasticity. Despite several severe inconsistencies, concrete is a flexible material and is still the most often used building material worldwide. The durability of concrete has received a lot of attention recently. Notably in unfavorable environmental circumstances. Even during the past three decades, it has been clear that durability and workability are essential components for enhancing concrete, in addition to hardness. Pre-stressed concrete bridges will not only be robust but will also experience less shrinkage and creep, which is necessary for nuclear structures exposed to high temperatures where the cement must be strong enough to survive thermal fissures. Due to this, establishing acceptable performance and developing HPC with a life span of greater than 100 years but no less than 50 years was given priority. A by-product of the rice milling process is rice husk, which is also referred to as rice hull. Due to Malaysia's population growth, which surpasses 2.3% yearly, the production of rice has surged. In a paddy milling operation, around 22% of the total weight is received as husk, and the remaining 78% is rice.
The disposal of vast amounts of husk has becomes a severe issue. Owing to the present necessity of environmental protection. Uncontrolled combustion or open-field burning contributes to serious environmental risks that worsen the quality of the air in the affected. [12,13,17]
The unburnt rice husk comprises roughly 50% cellulose, 25% 30% lignin, and 15%20% silica, according to Ahmed and Waliuddin. Consequently, the inclusion of silicon in this pozzolan allows for its usage in various pozzolanic materials have the potential to replace some of the cement in the manufacturing of self-compacting concrete (SCC). In order to keep up with the current study on the use of met kaolin and rice husk ash (RHA), On The following review begins with explaining the idea of SSC and SCM because of their manufacture, followed by a brief summary of the properties of rice husk ash with sintered clays as cementitious SSC. This review also identifies the gaps that need to be filled by more research. A thorough literature review that focuses on the mechanical, fresh, and durability characteristics of SCC using RHA, calcination temperature clays, or a combination of both materials follows. Automatically Compacting Cement (SCC) was developed for the first time in Japan in the early 1980s.
A reasonably impermeable concrete was created as a result of the uniform composition and good workability of the material. The SCC is now utilized in situations where High Efficiency Concrete (HEC) and High Toughening (HSC) specifications Midrise buildings are defined as concrete constructions with a height between 12 and 15 meters. For these midrise structures, M25 and M30 cement grades have been commonly employed in order to incorporate SCC features into the regular strength conventional concrete with possibility of adding ash from agricultural waste, such as Bottom Ash (BA) or Rice Husk, is the main goal of the current study (RHA). Every year, enormous amounts of husk ash, the byproduct of rice processing, are created globally. Every year, the world produces approximately 550 billion metric tons of rice, during the milling process, husk is produced as a byproduct. The paddy grain is encircled by this. Approximately 78% of the weight of the paddy that is milled is received as rice, broken rice, and bran. Husk makes up the remaining 22 percent of the mass of the paddy. The rice mills burn this husk as fuel to produce water for the parboiling procedure. About 75% of the husk's volatile organic compounds are organic, with the remaining 25% during the burning process, 25% of the weight of these husks is transformed into ash, or rice husk ash (RHA). And because it's challenging.
Concrete is employed as the primary component in every man- made construction, including bridges, buildings, and dams. In terms of usage, concrete is only used by humans after water (Hinsonton, including bridges, buildings, and dams. In terms of usage, concrete is only used by humans after water (Hanson 1995). The most important component of concrete is cement, which holds all of the aggregates together in the matrix. However, cement uses a lot of energy and resources. A metric ton of OPC needs 4GJ of energy to produce, and it also releases around a metric ton of CO2 into the environment [1]. Almost 7% of all CO2 emissions each year come from the cement industry [2]. As a result, much research is now being
conducted on geopolymer concrete as a full substitute for cement in concrete by various OP materials. After producing biomass energy from the husk, rice milling enterprises produce a byproduct called corncob ash (RHA) (rice hull). The RHA is often burned in the boiler using direct combustion or gasification to create heat energy at a regulated temperature. The mill processes the paddy using this thermal energy. Following this procedure, a non-biodegradable waste product called rice husk ash is created, which is high in silicon dioxide. RHA residue amounts to around 55 kg for every 1000 kg of rice. About 125 million tons of RHA are produced annually globally, with India being the second-largest producer after China. This production has posed a serious environmental risk in recent years. Because of its low weight, aerated concrete is employed in many building applications today. Building and maintaining buildings made of lightweight concrete is simple. Utilized frequently in civil engineering projects is lightweight structural concrete as a fairly simple replacement for conventional concrete.
Lightweight concrete lowers the structures' overall self- weight, which reduces the size of the foundations and lowers expenses while enhancing durability. Aerated concrete lacks coarse aggregate, making it a more uniform material than conventional concrete, although it still has a wide range of properties. By encasing air in the matrix, aerated concrete is produced using either admixtures or physical foaming agents. This reduces the product's weight and is responsible for the majority of its advantageous impacts, including material savings, robust thermal insulation, and advantages that result in financial savings. Aerated concrete is defined as concrete that has a considerable number of air gaps within the matrix but was created without the use of coarse particles. Cement may be partially replaced with mineral additives such as fly ash, slag from blast furnaces, and rice husk ash to help reduce CO2 emissions [22,25] and the requirement for new resources. Additionally, this might reduce the price of finished goods and give industrial waste a purpose, promoting sustainable growth, given that concrete is like a steel frame and, as such, should offer safety and last for the expected amount of time, the physical advantages of adding these materials to concrete make its usage necessary in many situations [3], independent of any economic or environmental concerns. Natural resources are used less when buildings are made to last since there is less need for maintenance and replacement.
-
EXPERIMENTAL MATERIALS
-
Methodology:
By carefully burning rice husks without harming the environment, rice husk ash is produced. When burnedproperly, it contains a lot of SiO2.and may be added to concrete as an additive. Ash from rice husks has strong pozzolanic properties,which help concrete have high strength and great impermeability. The rice husk has the following physical properties: density of 495 kg/m3, specific gravity of 2.53, meanparticle size of 0.15 to 0.25 m, minimum specific surface area of 220 m2/kg, sphericalness of the particles, and moisturecontent (% by weight) of 2.15. Materials including
river sand, coarser aggregates, groundwater, RHA, and SP were employed,along with OPC 43-quality cement. In the mix design of concrete, 3.13 specific gravity cement, 2.6 zone II river sand, and 2.64 zone 20-mm coarse aggregate were employed. In the RHA. [2,4]
-
Cement:
The cement used in the trials is ordinary Portland cement of IS: 12269-2013 grade, with a dry density of 3.15 The structural properties of the cement as verified by suitable testing Grade 53Normal Portland Cement (NPC) was used. It is made up of lime stone (calcium oxide) and clay, shale (Al2O3.2SiO2), or another type of alumina silicate. OPC's chemical composition is CaO=60-67%, SiO2=17-25%, Al2O3=3.0-8.0%, Fe2O3=0.5-6.0%, Mg=0.1-4.00%,
alkalizes (K2O, Na2O) = 0.4-1.3%, and SO3=1.3-3.0%. The initial setup time for OPCis 30 minutes, and the maximum total floating time is 500 minutes (maximum). In dry circumstances, RHA-blend cements were created by replacing OPC with different percentages of RHA (35% by weight of the cement).
-
Rice Husk Ash:
The rice husk ash utilized in this experiment was sourced fromthe KRBL rice mill in Ghaziabad, Uttar Pradesh. Table 2 lists the specifications and physicochemical parameters of this RHA. Rice husk ash is generated when you burn rice husks in a regulated manner that does not pollute the environment. It has a high SiO2 concentration when properly burned and may be used as a concrete additive. Rice husk ash has significant pozzolanic properties and helps to maintain the strength and impermeability of concrete. Density = 495 kg/m3 is the physical property of rice husk. Rice husks were burned for 48 hours in an open area using an uncontrolled burning method. The Temperature ranged from 400 to 6000 degrees Celsius. The collected ash was sieved using a BS standard sieve size of 75 mm, and its color was determined. [6][8].
-
Aggregates:
The project's scope is limited to river sand collection. The sandhad been gathered to guarantee that there wasn't permit for harmful elements in the sanding this study, granite with a height limit of 20mm was employed. A thorough check was performed to verify that it was free of harmful elements. The granite came from the Zenith quarry in Akamai, Cross River state. Fine aggregate was acquired that met the requisite qualities of fine aggregate for experimental work, and the sand corresponds to IS 383: 1970 zone III criteria. Density = 2.62 Fine aggregate factor = 2.5 A Metal of crushed angular granite machine as coarse aggregate, 20mm statutory size from a local source is employed. It is devoid. [7][9].
-
Water:
Water is essential in the production of concrete. Production (mix) in the sense that it begins the interaction of a cement and the aggregates. It aids in the hydration of the body. Mix. The water utilized in this project was piped water that is devoid of contaminants. The inclusion of very tiny admixture particles in
the concrete matrix causes a tightly populated and less densely packed structure.[12][23] Because of the porous structure, the water absorption capacity is limited. As seen in Fig. 4, the absorption of water after adding cement and sand, the concrete's capacity dropped. The supplemental contents took their place. Because of their properties, RHA, and SD serve as filler materials. High fineness qualities, resulting in thick concrete. Matrix, lowering the water absorption capacity. The concrete mixture specimen. [14]16]
-
Sulfuric Acid:
Sulfuric acid, having the chemical formula H2SO4, is a very corrosive, strong mineral acid. It is sometimes painted dark brown during manufacture to warn people about its dangers. This acid was previously known as "oil of vitriol." Sulfur is a triatomic chemical with variable characteristics depending on concentration. Sulfuric acid is a vital commodity chemical, and a country's ability to produce it is a strong measure of its industrial.
Figure.1. (a) Ordinary Concrete, (b) RHA Based concrete against acid attack [8]
-
-
EXPERIMENTAL TESTINGS.
Prepared specimens were dried for 28 days at a temperature of 20 degrees Celsius and a relative humidity of 75%. For evaluating. Three 100-mm concrete cubes were created from each mix to test the compressive capability according to the guidelines of BS-EN123090 [6]. Furthermore, 300-mm diameter cylinder specimens were created in accordance with ASTM C496 [3]. Figure 4 depicts the stress and tension tests that were performed on the three concrete cubes and three concrete cylinders created from each mix after they had been weighed. Even though the compression test's loading rate range, according to BS-EN123090, is between 0.6 and 0.2 MPa/s, in this study, 0.25 MPa/s was used.
-
Compressive strength:
The cube sample was placed into the machine, which had a capacity of 2000 kN. Plate 1 shows how the pressure was increased at a rate of roughly 145 kg/sq. cm/min until the specimen's resistance to the rising load could be sustained. The outcomes are provided. Strength is the most important attribute to consider when designing concrete buildings. Previous research has shown that including RHA as an SCM in ordinary concrete increases its compressive strength. The higher compressive strength caused by the inclusion of RHA is mostly due to the improved pozzolanic and pore refinement supplied by the RHA particles [19]. The introduction of RHA particles to concrete reduces Ca (OH) Concrete cube compressive strength tests show that as the percentage of RHA increased, the compressive strength decreased. However, as the number of curing days increased, the compressive strengths increased with each percent RHA substitution. Table 3 shows that the
compressive strength of the control cube rose by about 66% from 17.51 N/mm2 at 7 days to 29.15 N/mm2 at 28 days. As demonstrated in Table 4, the 28- day strength was greater than the required value of 25 N/mm2 for grade 26 concrete (BS 8110, 1997). The compressive strength increased by 64%, from
-
N/mm2 at seven days to 27.68 N/mm2 at 28 days after the rice husk ash substitution of 5%. The 28-day endurance The compressive capabilities decreased by 6, 11, 21, and 24% at age 28 days, when there was, correspondingly, 2.5, 5, 7.5, or 10% RHA. If RHA is present, it first absorbs a sizable amount of water from the concrete mix, which reduces the quantity of water needed for the hydration of the cement [50]. The W/C ratio, curing method, and mix proportions are some of the variables that are associated with a compressive capacity decline [51]. At 90 days old overall compressive capacity values in the RHA-concrete samples were significantly greater than those in the control samples. This specimen had a maximal three- month compression capacity, which was almost 23% higher than a 28-day compressive capacity.
Figure 2. Compression Testing.
The SCC mix M1 (10% RHA and 0% CCW) provided the greatest ultimate strength of 35.4 MPa greater than reference. As a comparison, consider sample M0. The compressive strength of the SCC mix had been significantly increased by adding up to 10% RHA. SCC mixtures containing 10 and 20% RHA provide stronger results that are 31-41% higher than those of the reference SCC combination. In contrast, using CCW instead of cement reduces the compressive strength of SCC mixtures. The SSC mixture improved after the inclusion of RHA and CCW. In comparison to the data obtained for the SCC mixture comprising 10% RHA and 5%, the ultimate strength of the sample material was 33.9 MPa lower.
RHA addition increased the compressive strength of SCC by up to 10% weight percent of binder [10]. Instead of using SCM, the writers used RHA for VMA. The drop in the ratio of water to binder caused by the injection of RHA is what causes the rise in strength. In the refining of grain size, pores, and denser particle packing [10]. Due to its high reactivity, which results in the creation of additional CSH and enhances the strength development of SCC when employed as an SCM, RHA improves the structure of a pasted matrix or transition zone [16]. Similar to this, when RHA substituted up to 15% of cement, a compact development of the hydration product that reduced the porosity of the cement was seen and shown the connection between compressive strength and curing age. Units with varied replacement levels have compressive strengths that are greater than the 2.8 N/mm2 minimum standard. According to MS 76. Every block type in the same graph trend demonstrates an increase in strength. This could be
explained by the synergistic effects of low cement concentration and an early, sluggish pozzolanic reaction. Table 3 displays the average statistics regarding resistance to curing age. Every sort of block type has a comparable graph trend showing how its strength has grown over time. It is clear that RHA15 reaches its strongest points after 60 days. RHA15, which contains 15% RHA replacement, acquired the results at 28 days.
displays the least strength. The escalating trend. When introducing any pozzol as SCM, it is critical to investigate shrink and creep behavior. This is because sluggish hydration kinetics cause large free plastic shrinkage and high-water evapotranspiration, especially in dry environments.
Table 1. Compressive strength of M-40 [4].
Rice Husk Ash (%)
7 days (Mpa)
28 days (Mpa)
0
28
41.60
5
26.8
38.90
7.5
28.4
42.68
10
27.8
41
12.5
26.9
39.60
15
25.7
38.90
Figure 3. compressive strength of M-40 mix at different % levelsof RHA [4].
Figure 4. Split Tensile Testing.
In contrast to SCCs devoid of SCMs. There is currently no literature on the shrinkage and creep behavior of SCC in ternary both stated that the introduction of RHA had no appreciable impact on the shrinking behavior of SCC. However, because of its micro fine particles, RHA enhanced the dry shrinkage of concrete when it was finely milled. Nevertheless, when employed in place of the clinker phase.
Rice Husk Ash (%)
7 days (Mpa)
28 days (Mpa)
0
2.5
3.2
5
2
3
7.5
2.8
3.4
10
2
3
12.5
1.8
2.9
15
1.6
2.8
Table 2. Split Tensile Strength of M-40 [4].
-
-
Split Tensile strength:
The pack skip (a wooden strip) or loading pieces were carefully placed at the top and bottom of a plane for unloading the specimen, with the cylindrical specimen being centered horizontally. The load was applied gradually at a marginal rate between 1.2 and 2.0 without any shocks. Till the specimen fails, N/mm2 /min reaches 2.4 N/mm2 /min. At failure, the maximum load was recorded. Plate 2 depicts the appearance of cement and any underused aspects of the sort of failure that was also noticed. Flexural modulus and tensile splitting are the next most fundamental and important characteristics of concrete, following compressive strength [84]. It has been discovered that adding RHA particles to concrete boosts its tensile and flexural strength.
Compare the RHA and CCW-splitting SCCs' tensile strengths. There was a similar pattern of conduct. a specimen of M1 concrete with 10% RHA, and the behavior improves at 0% CCW due to its maximum splitting tensile strength of 3.11 MPa. The pozzolanic reaction and parking ability are often enhanced by the inclusion of RHA as an additive [28]. As the ratio of CCW rose, the strength dropped. The cement's diluting impact and the insufficient generation of C-S-H gel, which led to a pozzolanic reaction with calcium carbide waste, may be to blame for the drop in strength. It can be concluded that CCW alone has a detrimental effect on SCC strength since the concrete mix with 0% RHA and 10% CCW
Figure 5. Split tensile strength of M-40 mix at different % levelsof RHA [4].
-
-
CONCLUSION
The review results allow us to draw the following conclusions:
-
The length and temperature of the furnace are significant factors that affect the RHA pozzolans' reactivity. When husks are burned at a high temperature, silica in the
amorphous state that it first takes on may change to a crystalline form. Additionally, silicon in rice husk ash won't stay porous and amorphous when burned for a long time at a temperature above 650 °C or for a shorter amount of time than the manufacturing time.
-
The pozzolanic activity findings show that the generated rice husk ash concrete has a higher pozzolanic activity index than the control. To put it another way, the generated rice husk ashes, which contain up to 90% amorphous silica, completely meet other requirements. In this work, various models for the estimation of a CS for RHAC were established.
-
The models created in this study are based on a variety of data, including several factors that have been shown by experimental investigations and are present in it. Literature. The models used as inputs used the variables that had the greatest impact on CS. The findings of this study closely match those of the experimental research.
-
Concrete's compressive strengths after being cured in ordinary water for 28 days, cement weighted between 9 and 10% has attained the desired mean strength. A comparison of ash from rice husk concrete with different replacement ratios of RHA showed that, due to significant pozzolanic activity, concrete with a replacement rate of 6% RHA performs and displays superior strength to concrete with other replacements.
-
The workability, passing ability, and resistance to segregation of self-compacted concrete are all dramatically decreased when calcium carbide waste and rice husk ash are added to the mix. The decline could be caused by the rice husk ash's capacity to absorb water. However, a lot of concrete mixtures have complied with the 650750 mm EFNARC 2002 restriction. A positive result was obtained by using rice husk ash as the only ingredient, which significantly enhanced the mechanical behavior, including Concrete was made with grounded RHA in and engineering qualities established.
-
According to research, the typical consistency and setting periods of cement are the increment varies depending on the RHA %. RHA promotes water quality. Concrete absorbs more water, increasing its to be concrete, RHA has been included.
-
The compression strengths were found to be equal to or greater in all of the mixes.at 28 and 91 days, respectively, compared to the reference combinations, demonstrating the high degree of sensitivity of this pozzolan. Only slag and bottom ash mixtures with a w/b ratio of 0.35 at 2 weeks demonstrated performance that was equivalent to or better than the REF combination. Higher compressive strength values (2891 days) were obtained for all the studied combinations when longer curing duratons were used. The only combinations that didn't show substantial strength gains were those that included slag. Increases in RHA mixes are accommodated.
REFERENCES
[1] Mehta, P.K., "High-performance, high-volume fly ash concrete for sustainable development", Proceedings of the International Workshop on Sustainable Development and Concrete Technology, Beijing, China, May 2021, 2004. [2] Mehta, P.K., "Mineral admixtures for concrete an overview of recent developments". Advances in cement and concrete, Proceedings of an Engineering Foundation Conference, University of Newhampshire, ASCE, pp. 243- 256, 1994. [3] A. Ramezanianpour, F. Gafarpour, M.H. Majedi, The use of rice husk ash in the building industry, Building and Housing Research Center (BHRC), winter 1995 [4] Anil Kumar Suman, Anil Kumar Saxena, T. R. Arora (2015), Assessment of Concrete Strength using Partial Replacement of Cement for Rise Husk Ash, International Journal of Soft Computing and Engineering (IJSCE), ISSN: 2231-2307, Volume-4, Issue-6, January 2015. [5] Ch.Sivanarayana, K Pratyusha, P V Rambabu, G V Ramarao (2014), A Study on Sulphuric Acid Attack on Concrete with Rice Husk Ash as a Partial Replacement of Cement, International Journal of Engineering Research and Development, e-ISSN: 2278-067X, pISSN: 2278-800X, Volume 10, Issue 4, pp.43-49, April 2014. [6] Deepa G Nair, K. Siva Raman and Job Thomas, (2013), Properties of Rice Husk Ash (RHA) – High strength Concrete, American Journal of Engineering Research (AJER) e-ISSN: 2320-0847, pISSN: 2320-0936, Volume-3, pp-14-19. [7] D. Siva Prasad and Dr. A. Rama Krishna (2011), Production and Mechanical Properties of A356.2 /RHA Composites, International Journal of Advanced Science and Technology Vol. 33, August, 2011. [8] Joseph Davidovits (1994), Global Warming Impact on the Cement and Aggregate Industries, Published in World Resource Review, Vol. 6, No. 2, pp. 263-278, 1994. [9] K. Gurunaathan and G. S. Thirugnanam (2014), Effect of mineral admixtures on durability properties of concrete, International Journal of Advance Structures and Geotechnical Engineering, ISSN 2319-5347, Vol. 03, No.01, January 2014. [10] Obilade, I.O (2014), Use of Rice Husk Ash as Partial Replacement for Cement in Concrete International Journal of Engineering and Applied Sciences, ISSN 2305-8269, Vol. 5, No. 4, Sept. 2014. [11] S. D. Nagrale, Dr. HemantHajare, Pankaj R. Modak, (2012), Utilization Of Rice Husk Ash, International Journal of Engineering Research and Applications (IJERA) ISSN: 2248-9622, Vol. 2, Issue 4, July-August2012.
[12] P.K.Mehta, Properties of Blended Cements Made from Rice Husk Ash, ACI Journal/September 1977 pp. 440-442. [13] P.K.Mehta and D.Pritz, Use of Rice Husk Ash to Reduce Temp in HSC, Journal/February 1978 pp. 60-63. [14] British Standard Institution (2002). Methods of test for water for making concrete, BS EN 1008, British Standard Institution, London. [15] Adewuyi, A.P. and Ola, B.F. (2005). Application of waterworks sludge as partial replacement for cement in concrete production, Science Focus Journal, 10(1): 123-130. [16] Bakar, B.H.A., Putrajaya, R.C. and Abdulaziz H. (2010). Malaysian Saw dust ash Improving the Durability and Corrosion resistance of concrete: Prereview. Concrete Research Letters, 1(1): 6-13, March 2010. [17] British Standard Institution (1983). Methods for Determination of Compacting Factor, BS 1881, Part 103, British Standard Institution, London. [18] Jefferis, S.A.; Mangabhai, R.J. Effect of temperature rise on properties of high alumina cement grout. In Calcium Aluminate Cements; Chapman and Hall: London, UK, 1990; p. 363. [19] Scrivener, K.L.; Cabiron, J.-L.; Letourneux, R. High- performance concretes from calcium aluminate cements. Cem. Concr. Res. 1999, 29, 12151223. [CrossRef]. [20] Bensted, J. Calcium aluminate cements. Struct. Perform. Cem. 2002, 2, 114138. [21] Parr, C.; Wöhrmeyer, C.; Veyrat, D. High purity calcium aluminate binders for demanding high temperature applications. In Proceedings of the centenary conference Calcium Aluminate Cements, Avignon, France, 30 June2 July 2008; pp. 417428. [22] Williams, C.M.; Garrott, F. Recycling/Reclaiming a savingsspree: Chicago reuses to the max on famous shopping mile. Ill. Interchang. Ill. Dep. Transp. Springf. 2012. Available online: https://www.roadsbridges.com/recyclingreclaiming- savings-spree (accessed on 5 January 2022). [23] M. Sivakumar, N. Mahendran, Strength and permeability properties of concrete using fly ash, Rice husk ash and eggshell powder, J. Theor. Appl. Inform. Technol. 66 (2014) 489499. [24] S. Wild, J.M. Khatib, A. Jones, Relative strength, Pozzolanic activity and cement hydration in super plasticized Metakaolin concrete, Cem. Concr. Res. 26 (1996) 15371544. [25] M. Thiedeitz, W. Schmidt, M. Härder, T. Kränke, Performance of Rice husk ash as supplementary cementitious material after production in the field and in the lab, Materials 13 (2020) 4319. [26] L. Courard, A.D.M. Schouterden, F. Ferauche, X. Willium, R. Degeimber, Durability of mortars modified with metakaolin, Cem. Concr. Res. 33 (9) (2003) 14731479.