
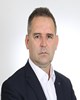
- Open Access
- Authors : Omar Kopcic , Ibrahim Plancic , Edin Begovic
- Paper ID : IJERTV12IS010021
- Volume & Issue : Volume 12, Issue 01 (January 2023)
- Published (First Online): 16-01-2023
- ISSN (Online) : 2278-0181
- Publisher Name : IJERT
- License:
This work is licensed under a Creative Commons Attribution 4.0 International License
Numerical Simulation of Erichsen Cupping Test of Workpieces Made of Structural Steel and Aluminium Alloy
Ibrahim Plancic Associate Professor University of Zenica
Edin Begovic Associate Professor University of Zenica
Omar Kopcic
Student University of Zenica
Abstract The paper presents the basis of one of the most used stretchforming methods knownas the Erichsen cupping test. Erichsen cupping test is used to show the formability of metal sheets and it is a useful measure showing the ductility of materials planned for further usage. Furthermore, finite element analysis – FEA was done using the software Ansys Workbench 19.2 and the main goal of this paper is to compare deformation and Von-Misses strain for structural steel and aluminium alloy with thicknesses of 2 and 3 mm. The hypothesis of this paper is to accomplish results that will confirm that aluminium alloys are more ductile than structural steels and that with the increase of sheet thickness drawing depth is also increasing.
Keywords Ansys, ductility, Erichsen cupping test, FEA, stretchforming
1. INTRODUCTION
Formability is a measure of the ability of a sheet made to be stamped or formed successfully into useful components without developing any failures. Formability is the extent to which a sheet metal can withstand plastic deformation without defects. The common failure encountered during sheet metal forming is fracturing, wrinkling, puckering; shape distraction loose metal etc. Formability is not easily quantified as it depends on several interacting factors. Material factors such as material flow properties, ductility, and tool factors such as die geometry, die materials, lubrication conditions and press speed contribute to the success or failure of the formed sheet metal components to varying degrees in an inter-dependent manner. Formability should be viewed more as a system parameter, as it is a function of the sheet metal that is being formed, the process conditions, the forming press, and the component shape.
In the formability test, the sheet undergoes tearing at a particular location as a result of necking. [5,6]
Sheet metal forming is the process of converting a flat sheet of metal into a part of the desired shape without fracture or excessive localized thinning. Sheet metal forming process like bending, curling, expanding, hammering and hydroforming is carried out in industries based on the product requirements. One of the many types of forming is stretch forming. Stretching is a process where the surface area of a blank is increasing as a result of tension and thinning of the metal. [3,5]
-
STRETCH FORMING
Two dimensional – tensile stress state is also called stretching. Its characteristics are positive stress components in two directions. Such a stress state is often present in the area of sheet forming. To determine material properties, there are a lot of tests such as the Erichsen cupping test based on the two-dimensional tensile stress state. A vast variety of deformations and stresses occur on different parts of the spherical shape. During these tests, at the top of the hemispherical punch two-dimensional state is obtained. Stretching is considered as forming where the material is simultaneously stretched in multiple directions, and during that forming body, the circumference is pressed with a holder.
The main scheme of strech-forming is given in the Fig 1.
Fig 1. Force equilibrium during stretch-forming [2]
-
FUNDAMENTALS OF ERICHSEN CUPPING TEST
-
Erichsen suggested the first method for testing deep drawing ability in 1912, and that method was accepted as one of the most important methods for rating sheet formability. Erichsen cupping test use sheet metals or strips with thickness 0,2 3 mm. The modified Erichsen cupping test is one of the currently used formability tests, which evaluates the ability of sheet metal to be formed into useful components successfully. As ductility is an indicator of the ability of a material to deform plastically under tensile load, Erichsen cupping test is
also a ductility test. The formability test index is identified as one of the most important formability test results that could be used on a routine basis by the industry for grading, selecting and sorting incoming sheet metals for manufacturing various
components. In former Erichsen tests,
the results obtained were uncertain, as there was no control of the clamping force. The test consists of forming an indentation by pressing a punch with a spherical end against a square-shaped specimen (dimensions of sheet or strip are usually 90×90 mm) clamped between a blank holder and a die until a crack appears within. The depth of penetration thereby obtained is measured as an Erichsen index (IE), representing the formability of the specimen. The Erichsen number increase with an increase in the thickness of the sheet metal. According to the standard, the die and punch should have a hardness of over 750 HV. Contemporary experiments use lubrication to reduce the factor of friction which is inevitable during tests, and it is demanded to polish the punch before mounting it on the machine. [3,6]
Fig 2. Scheme of Erichsen cupping test [1]
According to the standard [1], Table 1 Symbols and designations, proper dimensions from Fig 2. are given and can be implemented to create a 3D model.
-
-
SETUP OF NUMERICAL SIMULATION Numerical simulation has been conducted in the software Ansys, and for Explicit Dynamics analysis, non-linear steel and aluminium alloy were picked. The properties of these default materials approximately fit with S275 NL and AA 6061-T6 properties and their mechanical and chemical properties are given below.
TABLE I. STRUCTURAL STEEL S275 NL AND ALUMINIUM ALLOY 6061- T6 – MECHANICAL AND CHEMICAL PROPERTIES
Element content (%)
C
max.
Si max.
Mn max.
P max.
S
max.
N max.
Al max.
S275 NL
0,14
0,4
0,5-
1,5
0,025
0,02
0,015
0,02
Element content (%)
Si
Fe
Cu
Mn
Cr
Zn
Ti
Al 6061 T6
0,59
0,45
0,28
0,028
0,27
0,04
0,05
Tensile strength Rm [MPa]
Yield Strength [MPa]
Al 6061 T6
310
276
S275 NL
350-510
275
A 3D model of the Erichsen cupping test machine was created in SolidWorks and saved as a neutral format file – STEP for importing to Ansys.
Fig 3. 3D Model of Erichsen Cupping Machine
Punch and specimen will only participate in FEA analysis to reduce the time of simulation and create a better view of FEA results. Essential steps for numerical simulation were:
-
Assign material to punch (tool steel) and specimen (Aluminium Alloy or Structural Steel),
-
Delete contact between punch and specimen,
-
Define velocity (the value of velocity is set to 100 m/s for 3 mm thickness and 66,67 m/s for 2 mm thicknes and is defined by the component, in this case, it is Y axis),
-
Define endtime (end time is defined as 0,001 s),
-
Allocate fixed support on side faces,
-
Create a mesh with the default elements size and run a simulation (to compare two specimens' thicknesses, it is necessary to create the same conditions such as the number of mesh elements).
Fig 4. Conditions before simulation start in Ansys
In the next chapter, proper deformations and Von-Misses strains for structural steel and aluminium alloy with thicknesses of 2 and 3 mm will be compared. To ensure the same force during analyses for different sheet metal thicknesses, it is required to decrease the value of velocity during FEA analyses for 2 mm thickness.
-
-
RESULTS AND DISCUSSION Presentation of the appropriate distribution of deformations and strains and their values are given below.
Fig 5. Total deformations of all four specimens
Fig 6. represents deformations of all four specimens during FEA analyses. It shows that the highest level of deformations provides AA (3 mm), AA (2 mm), SS (3 mm), and SS (2 mm) respectively.
Fig 6. Distribution of equivalent strains of all four specimens
The distribution of Von Misses strains and stresses is easy to explain. Von Misses strains appear when punch starts to act on a specimen, and values of stresses and strains are increasing in the region of contact between two corresponding parts. With further propagation of punch to the specimen, values of stresses and strains continue to increase until the end of the simulation. The red region in Fig 7. represents the maximum of Von-Misses strains where the appearance of a crack can be expected and the red region with the yellow region represents the contact between punch and die. The green region is slightly away from the punch but is going through a little deformation. It is noticeable that the distributions of strains are different for each of the four specimens.
Fig 7. Diagram of the change of total deformations during simulation
According to [9], the Erichsen index for AA 6061-T6 (2 mm thickness) is 11,8 under the dry conditions of stretching. Maximum values of deformation during FEA analysis of the same alloy do not deviate from the experimental values. It is logical to expect occurring of a crack when deformation exceeds the value of 11. AA 6061
-
T6 is considered a structural Aluminium Alloy and can be compared to Structural Steel. Aluminium Alloys have better ductility due to their Face Centered Cubic Structure (FCC) where the atoms can be easily scheduled within the structure and Atomic Packing Factor is higher for FCC
structure than for BCC structure which characterized Iron which is, Carbon, the main component of Steel.
It is common knowledge that carbon decrease ductility. For example, according to [9], IE for steel DC04 with and thickness of 0,4 mm is 8,5 mm. Due to the higher level of carbon, it can be expected that S275 NL would have a lower value of drawing depth under the same conditions.
-
-
CONCLUSION
Based on the conducted FEA analyses, the following conclusions are:
-
Aluminium alloy AA 6061-T6 is more ductile than structural steel S275 NL, due to a higher degree of deformation which is obtained in FEA analyses,
-
With the increase of sheet metal thickness, the Erichsen index is increasing both for aluminium alloy and structural steel,
-
FEA analyses can be a useful tool to determine the possible location of cracks during the stretch forming method such as the Erichsen cupping test. Places on the specimen with the highest level of stresses and strains are places where crack formation can be expected.
-
-
REFERENCES
Erichsen cupping test
[2] LIU Chun-guo, LIU Wei-dong, DENG Yu-shan: Effect of multi-point punch active loading path on the stretch-forming of sheet, Roll Forging Research Institute, Jlinin University,Changchun 130022, China
[3] V. Dhinakaran, Rakesh Patil, Gokulakrishnan Sriram, N. Siva Shanmugam: Studies on Crack Propagation in Plasma Arc Welded Ti-6Al-4V Joint during Erichsen Cupping Test, International Journal of Recent Technology and Engineering (IJRTE), May 2019. [4] M. Rama Narasimha Reddy, M. Saran Theja, M. Gangadhar Tilak: Modified Erichsen Cupping Test for Copper, Brass, Aluminium and Stainless Steel, The SIJ Transactions on Industrial, Financial & Business Management (IFBM), May June 2013. [5] Rajesh Ramadass, Saravanan Sambasivam, Vishnu Vignesh Nagaraj: Formability Studies on Titanium Grade 2 Sheet using Erichsen Cupping Test, International Journal of Mechanical Engineering, February 2022. [6] SalunkheUjwala Sunil, K. Baba Pai: Investigation of formability of CRCA Steel sheet by Erichsen Cupping Test analysis, IOSR Journal of Mechanical and Civil Engineering (IOSR-JMCE), Mart April 2014. [7] Anoop Kumar: Influence of Sheet Metal thickness on Formability of Aluminium Alloy 6061, Department of Mechanical Engineering, St. Martins Engineering College Dhullapally, Hyderabad [8] Bhav Gautam, Vaibhav Chandra, Praveen Kumar, Narayan Agrawal and Sunny Kumar: Investigation on formability of Aluminium 6061 alloy Sheet under various forming conditions through Erichsen Cupping Test Machine, International Journal of Current Engineering and Technology, 2016. [9] Valentin Oleksik, Adinel Gavrus: Experimental and Finite Element Analysis of Erichsen Test. Application to Identification of Sheet Metallic Material Behaviour, The Annals Of Dunrea De Jos University Of Galai Fascicle V, Technologies In Machine Building, 2009.