
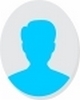
- Open Access
- Authors : Rebka Andarge , Hu Shan
- Paper ID : IJERTV12IS040033
- Volume & Issue : Volume 12, Issue 04 (April 2023)
- Published (First Online): 24-04-2023
- ISSN (Online) : 2278-0181
- Publisher Name : IJERT
- License:
This work is licensed under a Creative Commons Attribution 4.0 International License
Design of Level Cascade Control Based on S7-1200
Rebka Andarge, Ph. D.
Ass. Prof. Hu Shan
Tianjin University of Technology and Education
Abstract:- In industrial control, level control is a crucial parameter of process control, and cascade control is one of the advanced control systems that promotes the performance of process control in the occurrence of a disturbance, which enhances access to high- quality products.
The system is designed to be flexible and adaptable to various control tank sizes and valve characteristics. The performance of the proposed system was evaluated in an actual experiment, and the results show that it is capable of accurately maintaining the desired water level and flow rate, even under varying demand conditions. The proposed system has the potential to improve production quality in various applications, including domestic, agricultural, and industrial settings.
This paper discusses the design of a water level control system based on a cascade control system based on a Siemens S7 1200 PLC. The intended system consists of level sensors, a flow sensor, a control valve, and a cascade control system that employs two loop PID controllers in tandem.
Keywords PID controller, cascade control, S7-1200, software TIA Portal V15.1
1.INTRODUCTION
In industrial control, level control is a crucial parameter of process control. It involves maintaining a precise level of liquid, solid, or gas in a tank or another container by ensuring that the process operates safely and efficiently and preventing overflow or underfilling. Level control plays a critical role in various industrial applications, including the chemical and food industries [1, 2].
This paper is going to utilize cascade control, which can provide improved performance and is particularly effective at rejecting disturbances because it allows the secondary loop to act as a filter for the disturbance before it reaches the primary loop. The secondary loop can respond more quickly to disturbances than the primary loop, and the primary loop can respond more quickly to changes in the setpoint than in single loop control, leading to better setpoint tracking. By controlling a secondary variable that affects the process variable, one can effectively control the process [3, 4].
A single loop control system is not very effective in responding to disturbances; disturbances can affect the process variable, and the controller may take some time to respond and bring the process variable back to the setpoint. A single loop controller can only control one process variable at a time.
In a cascade control system, two control loops are used in tandem. The primary loop controls the main process variable, while the secondary loop controls a secondary variable that directly affects the primary variable. The output of the secondary loop is used as the setpoint for the primary loop. By using the secondary variable as a setpoint for the primary loop, the cascade control system can effectively filter out disturbances and improve the system's response. This study addresses the improvements that cascade control brings over traditional single-loop flow and level control [5].
2. OVERALL DESIGN OF SYSTEM
Cascade control with a PLC can improve the control quality of an industrial process by providing quicker disturbance rejection and improved dynamic response compared to single-loop control systems, faster response times, and more precise tuning.
In a cascade control system, the output of an inner is used as the setpoint for an outer loop. One-step tuning refers to a method of tuning the master loop based on the response of the slave loop to a step change in its setpoint. In this cascade control system provide one-step tuning method first stabilizing the slave loop by tuning its proportional-integral-derivative (PID) controller using standard tuning methods. Once the slave loop is stable, a step change is introduced to its setpoint, and the response of the process variable is observed. The time constant of the slave loop's response is then used to estimate the ideal proportional gain for the master loop's controller. Specifically, the master loop's proportional gain is set to be the product of the slave loop's proportional gain and the ratio of the time constants of the two loops. The integral and derivative gains of the master loop's controller are then tuned using standard methods, taking into account the interaction between the two loops [6].
Overall, using a cascade control system with a PLC can improve the dynamic response of the system, as the PLC can respond quickly to changes in the process variable and set the setpoint for the primary controller. This can be particularly important in industrial processes to reduce the impact of disturbances and improve the overall control quality of the system [7 ,8].
Furthermore, the PLC provides centralized control of the cascade control system, which simplifies the design, installation, and maintenance of the system. The PLC can be programmed to implement complex control algorithms, process logic, and safety interlocks, which improves the efficiency, reliability, and safety of the industrial process [9 ,10].
Figure 2-1: System Block Diagram
The controller output signal y is computed as follow:
= + + = ; = .. Equation (2-1)
3.Design Methodology
A controlled item is seen as an experimental device for process control. The primary variable is the tank's level control loop, while the secondary variable is the flow control loop. Through automated adjustment, the water level in the tank is set to the desired level. An electrically powered valve is used to control water inflow, and the level transmitter is utilized to measure level. The controller is S7-1200 CPU1214C.
The control strategy used is cascading due to the fact that there are several measurement signals and a control variable. The interconnection of the primary loop with the secondary loop was done in such a way that the output of the primary controller in feedback is also the set point of the secondary controller in feedback. The output of the latter will be the one that finally acts on the control valve. For this, a new sub-program was created using the previously scaled values and adding an organizational block OB to the cycle that corresponds to the variable level whose input of Setpoint is %MD100. directly, the scaled value of the level transmitter was taken in the %IW14 direction, which represents the input of the controller for the variable level. In order to interconnect the variable level of the primary loop with the variable flow of the secondary loop, the same organizational block of the cyclical interruption type was used to add a second segment represented by the PID_Compact_2 instruction that works with the variable flow and has as an input from Setpoint the output value of the variable level controller. Then, the scaled value of the flow transmitter, direction %MD318, represents the input of the second controller; in this way, the opening percentage of the valve is direction %MD128.
Figure 3-1: Cascade control programing
4.RESULTS
The results obtained using single loop and cascade control with and without disturbance are described briefly, and the associated graphical answers are displayed. During the disturbance, this was brought on by opening one of the vents in the discharge outlet pipe located in the lower part of the main tank.
-
Comparison of two control strategies
-
Analyzing and comparing without disturbance
First, the level of the tank is controlled without disruption using single-loop and cascade controls, respectively. A response curve is displayed in Fig. 4-1 after the PID parameters have been adjusted and optimized.
Setpoint Input Output
-
Cascade control response without disturbance (b) Single loop control response without disturbance.
Figure 4-1: Comparison of cascade and single loop controller without disturbance
The PID parameters of the cascade control system are obtained using the one-step tuning approach in the figure 4-1(a) (primary controller KP=4, Ki=220, Kd=30; secondary controller Kp=8, Ki=0, Kd=0 and set point 20-25).
Results for cascade control without disturbance in Figure 4-1 shows the level for a set point of 25. For that, it started with a level initially located at 20, and after entering that Set Point in the primary controller, it is observed that the variable water level (represented in green color) approaches the desired value or the Set Point (represented in black color) generating a more stable answer with a reduction in error and small fluctuations. In this way, an output represented in red, which in turn will be delivered to the secondary controller as a new Set Point value.
The PID parameters of the single loop control system are (Kp=10 ,Ki=200 ,Kd=50 and set point 20-25).
In contrast to Figs4-1 a and b, better performance of the controller is achieved on the cascade control, while the fluctuation in the level is within 5%. Cascade control improves the dynamic performance by adding vice-loops to the structure of the control system because adding vice-loops reduces the time constant of the equivalent process.
-
-
Analyzing and comparing with disturbance
Second, consider the disturbance that happened. A set of optimal PID parameters is designed that is similar to the above method. A set of response curves is shown in Fig. 4-2.
Setpoint Input Output
-
Cascade control response with disturbance (b) Single loop control response with disturbance
-
-
Figure 4-2: Comparison of cascade and single loop controller with disturbance
The PID parameters of the cascade control system with disturbance are obtained using the one-step tuning approach in the figure 4-1(a) (primary controller KP=4, Ki=220, Kd=30; secondary controller Kp=8, Ki=0, Kd=0 and set point 15-25) and the PID parameters of the single loop control system in figure4-1(b) (Kp=100, Ki=200, Kd=50 and set point 20-25).
Comparing with Figs4-2. a and b, the response of a single-loop control system is unsatisfied, which has large oscillations and is uneasy to reach the steady state. While under cascade control, the system can also achieve a steady state in a short time, although it may have an overshoot, which is allowed in industrial production.
The situation where the disturbance happened is much closer to the controlled parameter, so the influence is more obvious. To cascade control, the overshoot is smaller and the transient response is faster because the vice-loop plays the rule of filter methods for the disturbance, which greatly improves the ability to overcome the secondary disturbance.
Through the above experiments, it is not hard to see that the control method based on cascade control is better than the single- loop control method, whether there is an absence of disturbance in the loop or not. The reason why cascade control can improve control quality is that adding some vice-loops to the structure can overcome multiple disturbances effectively.
5.CONCLUSION
This study contrasts the single-loop and cascade control systems when both are used to regulate tank level, which is influenced by disturbances and without disturbance. In a cascade control system, the primary controller measures the process variable and sends the signal to the secondary controller, which measures the manipulated variable and adjusts it to compensate for any disturbances. This allows the cascade control system to respond quickly to disturbances before they affect the process variable, resulting in better control quality. The inner loops in a cascade control system are designed to be faster and more responsive than the outer loops, which quickly and accurately compensate for disturbances. By using multiple controllers in a cascaded structure, the cascade control system is better able to handle disturbances and maintain control quality. However, the single-loop control system struggle to maintain a stable control output when there are disturbances the control output of the single-loop control system may fluctuate, leading to an unsatisfactory response curve this is because the single-loop control system only has one controller that directly controls the process variable, and any disturbances that affect the process variable can cause it to deviate from the desired setpoint.
So, cascade control systems have better performance than single-loop control systems, no matter whether disturbances get into the control system or not.
REFERENCE
[1] Laxman Singh Kushwah and Rajiv Gupta "Level Control Systems in Chemical Process Industries: A Review" https://www.ijareeie.com/upload/2015/november-15/IJAREEIE%2066.pdf [2] Fernando Moraes and Luiz Eduardo Borges da Silva Journal "Level Control in Industrial Processes Current Trends and Future Directions" https://www.sciencedirect.com/science/article/pii/S0019057816301221[3] H. Chakraborty and M. Chidambaram: "Cascade Control in Process Industries" https://www.ijeat.org/wp- content/uploads/papers/v9i3/C6854029320.pdf
[4] Comparison of Single-Loop and Cascade Control for a Nonlinear System" by M. E. Tuna and M. J. Korenberg:https://aiche.onlinelibrary.wiley.com/doi/abs/10.1002/aic.690410813. [5] Emerson Automation Solutions. "Cascade Control: What Is It and How Does It Work?" https://www.emerson.com/en-us/automation- solutions/cascade-control [6] Akash, D., & Harche, R. (2018). Cascade Control of Liquid Level Using PLC. (http://www.ijert.org/view-pdf/19238/cascade-control-of-liquid-level- using-plc) [7] "One-step tuning method for cascade control systems" by M. J. Ogorzalek and J. M. Zurada (Control Engineering Practice, 2005). This paper presents a one-step tuning method for cascade control systems based on the proportional-integral-derivative (PID) control algorithm. [8] Ebrahim, F. S., & Salama, M. M. A. (2019). Experimental implementation of PLC-based control system for liquid level in a tank. Alexandria Engineering Journal, 58(2), 501-508. (https://www.sciencedirect.com/science/article/pii/S1110016818304114) [9] "Design and implementation of cascade control of liquid level and flow using programmable logic controller" by T. G. Solanke and O. A. Omotosho. https://ijece.iaescore.com/index.php/IJECE/article/view/21136. [10] Alper, A. E., & Bostanci, H. (2016). A PLC-Based Cascade Control System for Liquid Level. In Proceedings of the 5th International Conference on Control, Decision and Information Technologies (pp. 355-360). IEEE. (https://ieeexplore.ieee.org/document/7466315) [11] A. R. Yusuf and M. D. Dauda "Design and Implementation of Cascade Control System using Programmable Logic Controller". https://www.researchgate.net/publication/308156657_Design_and_Implementation_of_Cascade_Contr ol_System_using_Programmable_Logic_Controller