
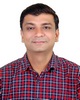
- Open Access
- Authors : Yogesh K. Kirange , Dr. Vijay S. Patil , Kiran L. Patil , Shoeb R. Patel, Harshal S. Sapkale, Jayesh B. Patil
- Paper ID : IJERTV12IS040083
- Volume & Issue : Volume 12, Issue 04 (April 2023)
- Published (First Online): 24-04-2023
- ISSN (Online) : 2278-0181
- Publisher Name : IJERT
- License:
This work is licensed under a Creative Commons Attribution 4.0 International License
An Overview of Matlab/Simulink Dynamic Model of an Electric Vehicle’s Performance
Yogesh K. Kirange
Electrical Engineering Department RCPIT, Shirpur, Dhule, India
Shoeb R. Patel
Electrical Engineering Department RCPIT, Shirpur, Dhule, India
Dr. Vijay S. Patil Electrical Engineering Department
RCPIT, Shirpur, Dhule, India
Harshal S. Sapkale
Electrical Engineering Department RCPIT, Shirpur, Dhule, India
Kiran L. Patil
Electrical Engineering Department RCPIT, Shirpur, Dhule, India
Jayesh B. Patil
Electrical Engineering Department RCPIT, Shirpur, Dhule, India
Abstract The goal of this study is to develop not only an electrical car with a wide range of gear train components, but also an energy model of such a vehicle in MATLAB/SIMULINK. Using this technique of simulation and design, we regularly seek out the energy usage of the vehicle due to various forces occurring on the vehicle after completing a number of standard driving cycles. Several different types of electrically powered and hybrid vehicles are analyzed in this work's market research section. As electric vehicles gain traction as environmentally friendly transportation options, scientists are devoting more time to studying and simulating them. This work proposes a MATLAB-Simulink simulation model of an all-electric car to analyze power usage. A single action that accomplishes both driving and regeneration. The drive train components include a motor, battery, motor controller, and electric battery controller, as determined by their calculations. The simulation results are shown and debated. Energy efficiency and flow were evaluated based on driving and regeneration conditions, measured by torque and speed. This research establishes a baseline for future exploration and development.
Keywords-Electric vehicle, Motor Circuit, Controller Subsystem, State of charge (SoC), State of Discharge (SoD)
-
INTRODUCTION
In the coming years, electric vehicles will be mass- produced for the first time, and there will likely be more studies and experiments conducted on the topic. The widespread use of electric vehicles is only one example of how technological advancements have made and will continue to make our daily lives better and more convenient (EVs). Electric vehicles are efficient because they can generate, store, and transmit power in addition to using it. This sets them apart from other types of cars that run on fossil fuels. They save money over time and are better for the planet than traditional gas or diesel vehicles. They use a reversible energy storage mechanism. Electric vehicles, on the other hand, are emission- free, simple to operate, and less noisy than their predecessors. Rapid adoption of electric vehicles in urban areas was driven primarily by women. As more individuals in the 1910s had access to electricity and charging infrastructure, electric cars became increasingly popular. Many original thinkers joined in on the trend. Porsche created the first hybrid electric car, which combined electric propulsion with a gasoline-powered generator. Thomas Edison, who was convinced that electric cars were the future, worked on improving their battery
technology. The need for charging infrastructure is growing in tandem with the increasing number of electrical vehicles on the road. Recent years have seen widespread shifts in the planning procedures used by most industries as a result of new technological developments. The aerospace, automotive, and other industries already adopt a model-based approach for sophisticated embedded systems.
The ancient world made progress through a methodical process that included requirements, Design, Implementation, Check, justification or validation. With Predictive Model- Based Design, engineers may quickly test and verify specifications vs. requirements by using models early on in the feasible specifications phase. The engineer employs Simulink/Real Time and Embedding Coder's automated code generation tool to effectively convey the subsystems' and components' functionality. Assist with Hardware-in-the-Loop (HIL) testing as the cost of developing a new product reduces, simulation is playing a larger role in the design process. Model-In-The-Loop (MIL), Software-In-The-Loop (SIL), and Hardware-In-The-Loop (HIL) development modelling are all tools available to the engineer for simulating the design process in real time. Using simulation software allows engineers to complete and test products sooner, for less money, and to reduce the time spent on the design process.
-
METHODOLOGICAL SURVEY
Sai Krishna Vempalli et al., [1] presented throughout his work on EV design, modeling, and simulation, the author has paid special attention to the problem of field orientation control in 2018. In this research work, Yu Inoue et al., [2] built a prototype electric vehicle (BEV) to measure electric motor power consumption. In addition to the motor inverter, battery, and motor, a BEV also has a driver controller and vehicle dynamics in 2021. By 2018, Kroeze and Krein scheduled for fully dynamic EV simulators that include overcharging the battery necessitate knowledge about the battery's projected state of charge, as well as the IV characteristics and dynamic behavior of various battery types [3]. Using a permanent magnet synchronous machine, it is controlled by Lab View software that performed dynamic testing on a car by Sorina-Maria Ciornei et al., [4]. Kumar, R.,
& Saxena, R examined the open- and short-circuit performance of SRM drives for electric vehicles, analyzing
the latter's responsiveness through measurements of speed, torque, and battery charge in 2019.
In 2020, Wei, D et al., [6] proposed an energy efficiency of the motor during the whole driving cycle is analyzed, as is the distribution of energy throughout the driving cycle examined the potential advantages of reducing energy loss. Most battery models are developed using simulations of electric vehicles, therefore progress in this area is crucial. An enhanced equivalent circuit model was developed by Abulifa,
A. A et al., [7] in 2017 to precisely analyze the performance of LiFePO4 batteries by analyzing the dynamic parameters and comparing numerous battery models. This study investigated by A, L., and R, B. K. [8] in 2019, permanent magnet synchronous motors by examining their high efficiency and variable speed (torque-to-current ratio). A PMSM with a radial flux inner rotor was proposed in this study. In 2020, Author Gaurav and Gaur [9] investigated the proposed work and presented their research work on to build a 3.45 kW on- board prototype that conforms to industry requirements for connecting electric vehicles to electrical vehicle charging stations, power supply using MATLAB. To model the charging process for Li-ion batteries, used to generate torque for propulsion, see here. Chargers with many stages are preferable because of their ability to regulate voltage and current levels. When utilised for both static and dynamic charging, Inductive Power Transfer (IPT), is the only feasible technique of charging electric vehicles (EVs) using electromagnetic energy while they are in motion, and it presents prospects that are unequalled by any other technology. In 2019, Niculae, D. et al. [10] set out to assess the efficacy of energy charging techniques that make use of magnetically coupled coils in autos.
The author of this study looked into how to improve the performance of a parallel HEV by maximizing the efficiency of its battery pack, and they modeled, simulated, and analyzed the system. Moreover,technological factors are explored to lessen mechanical and electrical power losses and increase brake system energy absorption by Mohammadi, F et al., [11]. The report recommends an alternative method for quickly discharging the voltage stored in an electric vehicle's capacitor in the event of a breakdown. The PMSM's windings are used for this purpose in the driving system. For large machine rotor inertia and low system safe current, however, the classical winding-based discharge method may not be effective. It is proposed work by Chao Gong et al. [12] in 2019 to discharge the capacitor voltage using a current control algorithm to prevent any potential voltage surge. For the PMSM drive system evaluated, this technique shortens the discharge time to less than 3 seconds. E-bikes, often known as electric bikes, are bicycles that use an integrated electric motor to supplement human pedalling. When compared to a traditional bicycle, an e-bike reduces the amount of effort needed to climb hills. It's easy to use; just connect it to a power outlet and go. The use of electric bikes as a means of relieving mental and physical stress has been on the rise over the past decade and this work is conducted by author Hamid and Umar [13] in 2022. This research analyzes how the energy consumption and driving range of battery electric vehicles vary under simulated and real-world scenarios (BEVs). In this research work , researchers looked at data from 197 identical BEVs over the
course of a year and over a variety of driving scenarios and seasons. The findings reveal that BEVs' electricity usage, travel habits, and charging routines differ greatly depending on the vehicle's intended use and the time of year. Researchers Hao, X et al., [14] observed that the New European Driving Cycle (NEDC) test's projected numbers for BEV electricity consumption and range were significantly off from the actual readings in 2020. In order to extend the range of EVs, the authors of this research propose installing a cruise control system (CCS). Electric vehicles' existing driving habits may cause them to cruise faster than the average traffic speed, which can result in kinetic energy loss owing to traffic ripples. The proposed CCS limits the car's top speed so it doesn't get too far ahead of the lead vehicle and keeps a safe space between them.
The design and simulation analysis of the suggested CCS was carried out in a MATLAB simulation environment in 2020, and the results showed a reduction in energy consumption of around 36.6% in urban driving cycles and 15.4% in highway drive cycles, as reported by Madhusudhanan and Na [15]. An efficient electric vehicle driven by a vector-controlled induction machine is the target of this project's design efforts. The efficiency of vehicle modelling has been increased by the use of a physical modeling approach. To further extend the range of the car, regenerative braking control has been implemented by Vempalli et al., [16]. This system recoups momentum lost during deceleration and channels it towards battery charging. Models and simulations of the EV have been run in Matlab/Simulink with the help of the Sim Power System/Sim Driveline toolbox in 2018. By 2020, flexible energy dispatch is possible with electric vehicles, but it is difficult to predict how much electricity will be needed to charge them and how much space would be needed for their batteries. Accurate predictions of electric vehicle behavior and charging requirements can be made by evaluating journey data and employing a novel neural network model, the R-ANN, based on space-time activity. This allows us to determine the storage capacity of groups of electric vehicles and the charging power of individual vehicles by Wenwen Fan et al., [17]. In 2020, fuel cell hybrid electric vehicles (FCHEVs) are efficient and ecologically friendly cars that have drawn the attention of governments and communities worried about environmental and energy challenges. This work focuses on the creation of a control algorithm for FCHEVs. Modeling power systems and controlling and simulating FCHEVs throughout time are at the heart of this study. The research suggests a new approach to estimating the slip ratio by tire modeling, and the control algorithm uses feed forward control and Proportional-Integral feedback control to achieve the desired levels of anti-slip and target driving torque. To comply with ECE braking standards by Hang Li et al., [18], the braking force is dispersed to optimize regenerative braking performance. The production of greenhouse gases is exacerbated by the widespread usage of conventional internal combustion engine vehicles (ICEV), making the electrification of vehicles a crucial area of study. By 2020, The use of electric vehicles (EVs) has many benefits, including decreased pollution, increased efficiency, and decreased upkeep expenses. In this research, we analyze the performance of EVs and ICEVs across a range of metrics,
including torque, speed, and range. Analysis is carried out in MATLAB/Simulink, and the results are presented alongside a number of performance metrics by Poornesh, Kavuri et al., [19]. In 2020, one of the major benefits of hybrid and electric vehicles is their regenerative braking mechanism. To optimize available energy for recovery while adhering to stability requirements, this research suggested by Yongliang Li et al., [20] a solution based on Artificial Neural Networks to address the optimal braking force distribution problem. Up to 37% of UDDS (urban driving pattern) energy demand can be recovered using the proposed method. Aggressive driving is shown to decrease the amount of energy that can be recovered by up to 7%. Raising the energy recovery rate is a good way to save money on gas and cut down on pollution.
In 2020, Khalil Sinjari and Joydeep Mitra [21] designed a hierarchical coordination framework to control active and reactive power dispatch for a fleet of EVs connected to a distribution network. Proposed models and algorithms coordinate EV charging with reactive power support to improve power flow on the grid. By analyzing real-world charging scenarios, we show that coordinated charging can decrease charging costs and increase the number of electric vehicles (EVs) that can be accommodated in overburdened distribution networks. This is especially true if charging takes place in non-unity power factor mode. In the long run, our method can help the grid and EV charging run more smoothly, which is good for everyone. In 2019, the goal of this study is to create a method for simulating the energy requirements and battery level of a long-range electric car (EREV) and this work is carried out by Kusuma et al., [22].
The simulation approach accurately predicts energy consumption by modeling the EREV propulsion system and using driving cycle data. The results were consistent with expectations, validating the method. Future EREV designs may benefit from this simulation approach, but it requires more precise data and modeling to accurately predict battery states of charge [22].
Electric vehicles aim to be economical and energy- efficient while also being kind to the environment. Electric vehicles can only achieve this with properly engineered electric motors. In this research, Rachev, Svilen et al., [23] analyzed the effect of varying parameters on electric power losses in the drive of a small electric car while in dynamic modes. Simulations were run using a mathematical model of the electromechanical system, and results were presented in tabular and graphical formats. With this model, one may determine how to best design electric motors and control systems to fulfill specific user needs in 2019.
Onboard chargers for electric vehicles are the subject of this research, which details the design and simulation of such a device. This charger can be used with a 48V, 35Ah lead-acid battery and a single-phase AC power supply. An AC-DC converter and a Buck type DC-DC converter are incorporated into the onboard charger to control the charging voltage and current. Using MATLAB/Simulink, we are able to model the charging process for an EV's battery and see how efficient the charger is. In order to combat the depletion of fossil fuels and the resulting increase in pollution, this technology is crucial for the advancement of electric cars by Kamat and Jadhav [24]. Sarathkumar et al., [25] their research underlined the
importance of electric vehicles in comparison to conventional modes of transportation that rely on fossil fuels, which have negative effects on the environment. They input driving cycles from SAEJ227 and EUDC into MATLAB/SIMULINK to model and simulate the operation of an electric vehicle. In order to assess the energy flow and capabilities of the electric drive for different driving cycles, the simulation results produce motor and battery characteristics. This research aids in the creation of electric vehicles that are both economical and gentle on the planet in 2020.
This research looks on the practicality of electric three- wheeled motorcycle taxis in Dar es Salaam from both a technical and user perspective. Based on the drivers' perspectives, the study evaluates two different types of electric power trains. The energy consumption of the car is estimated using a simulation model, and a Dar es Salaam-specific driving pattern is derived from GPS data. Depending on the results, a different power train option may be recommended by Wachter, Christian et al., [26] based on the vehicle's battery weight, energy requirement, and range. This article explained the value of using simulation models to learn about the inner workings of a vehicle and highlights the significance of electric car technology in 2020. It recommends simulating the charging process for an EV with a traction inverter model.
The author of this essay presented a new method of adaptive learning based on fraction calculus in 2021. This method is utilized by K. M. Sidorov et al. [27] to enhance learning performance in a signal processing context, and it has been shown to be both stable and convergent. Simsek, Mustafa et al., [28] in 2019, a novel method of assessing the magnetic field produced by a wireless power transfer system for electric vehicles was discussed by the author. In 2018, using finite element analysis and electric simulation software, they may take into account the system's electric behavior and magnetic reaction simultaneously by Guerroudj, Salim et al., [29].
In this study, we propose a method for improving the efficiency of HEVs through better engine and vehicle coordination. In 2020, the optimal solution to a constrained optimization issue is found by applying the paper's speed planning technique and energy management strategy. To prove the viability of the strategy by Fuguo Xu and Tielong Shen [30], the solution is tested in a traffic-in-the-loop powertrain simulation environment.
-
PROPOSED METHODOLOGY
Block diagram of the given model is shown below which consist of various blocks each block is explained ahead:
-
Block Diagram of System
Fig. 3.1: Block diagram of electric vehicle system
The basic structure of an EVS is depicted in figure 3.1. (Electrical Vehicle System). This section of the electric car consists of several different parts and a complex network of cables. In this case, the internal combustion engine (IC) has been replaced by an electric motor. The energy source, which is the battery pack, is transferred to the motor. Figure 3.2 depicts a critical component of the electrical vehicle system.
Essential parts of electric cars are the motor, chassis, controller, and battery pack. A wide variety of motor designs are employed in electric cars. Common types of electrical motors include brushless DC (BLDC) motors, brushed DC (DC) motors, and alternating current (AC) induction motors. The vehicle's body houses the tires, differentials, and housing. In the past, we would simply turn on the engine or the battery to get things going. These days, however, we often require operating power from batteries. Several modules make form a battery pack, each of which is constructed from individual cells.
The motor can't spin without some juice from the battery. Let's pretend that we routinely use a direct connection between the motor and the battery. There is no way to alter the motor's speed, thus it must always run at its specified maximum. The controller allows us to adjust the velocity of the motor. The controller can work with input from the driver.
-
Vehicle Body Subsystem
Fig. 3.2: MATLAB/SIMULINK Model of Vehicle Body Subsystem
The first thing we've made is a working version of the vehicle's body subsystem. The tires, differential, gearbox, and vehicle body are only some of the blocks from the simscape library that have been integrated to the vehicle body subsystem. The parameters of the block can be adjusted to suit our purposes. Put together the primary subsystem by linking the wheels, differential, transmission, and body components.
-
Motor Circuit And Controller Subsystem
Fig. 3.3: MATLAB/SIMULINK Model of Motor Circuit & Controller Subsystem
The battery will supply the motor with regulated power, which it will use to convert electrical energy into mechanical energy. The motor circuit and controller subsystem MATLAB/SIMULINK model is displayed in Figure 3.3. The generated power is transferred to the mechanical rotating frame and gearbox. The motor circuit and controller block were both taken straight from the Sims cape library and used into the final product. We used a basic DC motor, and an H- bridge controller was used to direct its rotation. The H-bridge controller bridge allows us to perform acceleration, deceleration, and braking. To manage the PWM wave, we have included a voltage block that is both regulated and PWM. We can adjust the block's settings to meet our requirements. Figure 3.4 depicts the interconnections between the various blocks that make up a given subsystem.
-
Battery Pack Subsystem
Fig. 3.4: MATLAB/SIMULINK Model of Battery Pack Subsystem
The battery pack will supply the power for the motor. The range before needing to recharge and the lifespan of the battery can be determined using state-of-charge (SOC) calculations. We utilized a lithium-ion battery so that we could see the SOC % in real time. Battery charging and discharging data can be analyzed with SOC. The blocks in the following diagram can be connected to form a subsystem as shown in figure 3.4.
-
Driver Input Subsystem
Fig. 3.5: MATLAB/SIMULINK Model of Driver Input Subsystem
According to Figure 3.5, the powertrain block library's longitudinal driver block is responsible for producing normalized acceleration, while reference and feedback speeds inform braking commands. The signal builder block can be used to create a custom signal, or the built-in driving cycle can be used as a reference rate. The actual vehicle speed is used for the feedback speed calculation. As a result of the divergence in frames of reference, a signal and the actual speed deviation will be produced. The car will try to match the speed of the error by either speeding up or slowing down. Using the longitudinal block and the Signal Builder block, the Drive Input module of this system was built. You can see the interconnections between the blocks in the diagram.
-
Drive Cycles
Fig. 3.6: MATLAB/SIMULINK Model of Drive Cycles
A timed drive cycle is generated by the block seen in Figure 3.6. It comprises mostly of time versus speed data with erratic acceleration and deceleration patterns, simulating real-world driving circumstances as nearly as possible. The factory preset driving cycle is FTP75. The Full Throttle option is also available. Spreadsheet data, a glider block, and a signal builder block can also be used to acquire information about drive cycles. The FTP75 simulation time is set to 2474 seconds by default.
-
Overall Model
Fig. 3.7: Overall MATLAB/SIMULINK Model of Electric Vehicle
Including a construction element for power interfaces in Simulation. In order to investigate the outputs and actions of the electrical Vehicle model, you should add a scope and a display block. We were able to produce a standard reference signal by utilising the signal builder block in our system. We will provide explanation for the operation of the feedback loop by using a graph that contains the reference signal and the actual speed.. We can also estimate an electric car's typical top speed. Using the SOC graph, we can see how the battery charges and discharges in response to the command to accelerate or decelerate. Using the software model shown in the accompanying image, which depicts the vehicle's overall electrical model, we analyzed the SOC % and average speed.
-
-
MATLAB/SIMULATION RESULTS
To begin, we used the signal builder to set a baseline velocity. We opted for a rapid pace of 100 kmph. The model has been simulated for a full minute. The first 400 seconds will include accelerated movement. For the next 200 seconds, the tempo stays the same before gradually slowing down for the last 400. We used the signal builder block to create the reference signal seen in figures. Various results are obtained Signal builder input waveform, Signal builder drive cycle output waveform, Signal builder drive cycle output waveform of the SOC of battery, FTP75 drive cycle output waveform, FTP75 drive cycle output waveform of the SOC of battery of FTP75 drive cycle.
Fig. 4.1: Signal builder input waveform
Fig. 4.2: Signal builder drive cycle output waveform
Fig. 4.3: Signal builder drive cycle output waveform of the SOC of battery
Fig. 4.4: FTP75 drive cycle output waveform
Fig. 4.5: FTP75 drive cycle output waveform of the SOC of battery of FTP75 drive cycle
-
CONCLUSION
The energy flow, functionality, and efficiency of the electric vehicle drive train can be studied with great benefit by modeling and simulation in MATLAB-Simulink. For this analysis, we ran the simulation in both driving and regeneration modes and compared the results. The motor's mode of operation is decided either by the required road speed and torque or by the polarity of the current and voltage supplied to the motor. Energy flows from the battery to the load when the engine is running, and back to the battery during regeneration. The controller's efficacy in eradicating error from the system is a key factor in the EV's overall performance. In this study, a P-I controller was utilized to correct the voltage inaccuracy, and a simple controller was employed to maintain a constant input-output power from the battery.
This research presents a reduced version of the electric vehicle design. Due to the high cost and difficulty of prototyping and testing, automotive designers must rely on simulation and modeling to help them choose the most efficient method of energy control, identify the correct size of the component, and cut down on energy use. One day, we'll be able to build electric cars that run on renewable energy sources like solar electricity. Regular gasoline has a higher calorific value than batteries. There is still a higher conversion efficiency for batteries than for gasoline. There is great promise in hybrid technology, and it could prove to be quite useful. In terms of transportation, it would be extremely beneficial to the environment if we could switch to electric vehicles instead of those that run on fossil fuels.
REFERENCES
[1] Sai Krishna Vempalli, J. Ramprabhakar, S. Shankar, Prabhakar. Electric Vehicle Designing, Modelling and Simulation. 4th International Conference for Convergence in Technology (12CT) SDMIT Ujire, Mangalore, India. Oct 27-28, 2018. [2] Yu Inoue, Takashi Kosaka, Hiroaki Matsumori, Nobuyuki Matsui. Modeling and Simulation of Battery-powered Electric Vehicle on MATLAB/Simulink. 2021 24th International, 2021. [3] Ryan C. Kroeze, Philip T. Krein. Electrical Battery Model for Use in Dynamic Electric Vehicle Simulations. 39th Annual IEEE Conference on Power Electronic Specialists Conference (PESC) 2018. [4] Sorina-Maria Ciornei, Raul-Octavian Nemes, Mircea Ruba, Calin Husar, RealTime Simulation of a Complete Electric Vehicle Based onNI VeriStand Integration Platform. 10th International Conference & Exposition on Electrical and Power Engineering (EPE) 2018
[5] Kumar, R., & Saxena, R. (2019). Simulation and Analysis of Switched Reluctance Motor Drives for Electric Vehicle Applications using MATLAB. 2019 4th International Conference on Electrical, Electronics, Communication, Computer Technologies and Optimization Techniques (ICEECCOT) 2019. [6] Wei, D., He, H., & Li, J. (2020). A Computationally Efficiency Optimal Design for a Permanent Magnet Synchronous Motor in Hybrid Electric Vehicles 2020 IEEE 9th International Power Electronics and Motion Control Conference (IPEMC2020-ECCE Asia) 2020. [7] Abulifa, A. A., Ahmad, R. K. R., Soh, A. C., Radzi, M. A. M., & Hassan,M. K. (2017). Modelling and simulation of battery electric vehicle by using MATLAB-Simulink. 2017 IEEE 15th Student Conference on Research and Development (SCOReD) 2017. [8] A, L., and R, B. K. (2019). Permanent Magnet Synchronous Motor for Electric Vehicle Applications. 2019 5th International Conference on Advanced Computing & Communication Systems (ICACCS) 2019. [9] Gaurav, A., & Gaur, A. (2020). Modelling of Hybrid Electric Vehicle Charger and Study the Simulation Results. 2020 International Conference on Emerging Frontiers in Electrical and Electronic Technologies (ICEFEET) 2020. [10] Niculae, D., Iordache, M., Stanculescu, M., Bobaru, M. L., & Deleanu,S. (2019). A Review of Electric Vehicles Charging Technologies Stationary and Dynamic. 2019 11th International Symposium on Advanced Topics in Electrical Engineering (ATEE) 2019.
[11] Mohammadi, F., Nazri, G.-A., & Saif, M. (2019). Modeling, Simulation, and Analysis of Hybrid Electric Vehicle Using MATLAB/Simulink. 2019 International Conference on Power Generation Systems and Renewable Energy Technologies (PGSRET) 2019. [12] Chao Gong; Yihua Hu; Guipeng Chen; Huiqing Wen;Zheng Wang; Kai Ni; A DC-bus capacitor discharge stratagy for pmsm drive system with large inertia and small system safe current in EVs IEEE, Year : 2019 [13] Hamid, Umar Zakir Abdul (2022). "Autonomous, Connected, Electric and Shared Vehicles: Disrupting the Automotive and Mobility Sectors". Retrieved 11 November 2022. [14] Hao, X.; Wang, H.; Lin, Z.; Ouyang, M. Seasonal Effects on Electric Vehicle Energy Consumption and Driving Range: A Case Study on Personal, Taxi, and Ridesharing Vehicles. J. Clean. Prod. 2020 [15] Madhusudhanan, A.K.; Na, X. Effect of a Traffic Speed Based Cruise Control on an Electric Vehicles Performance and an Energy Consumption Model of an Electric Vehicle. IEEE/CAA J. Autom. Sin. 2020 [16] Vempalli, S. K., Ramprabhakar, J., Shankar, S., & Prabhakar, G. (2018). Electric Vehicle Designing, Modelling and Simulation. 2018 4th International Conference for Convergence in Technology (I2CT). doi:10.1109/i2ct42659.2018.9058161 [17] Wenwen Fan;Siyuan Zhang;Yuqin Xu;Yongzhang Huang; (2020). Analysis of Electric Vehicle Load Storage Resource Potential Based on R-ANN Activity Behavior Model. 2020 IEEE 4th Conference on Energy Internet and Energy System Integration (EI2), (),.doi:10.1109/ei250167.2020.934662
[18] Hang Li;Jianqiu Li;Jiayi Hu;Jingkang Li;Zunyan Hu;Liangfei Xu;Minggao Ouyang; (2020). Modeling and simulation of coordinated driving and braking control for fuel cell hybrid electric vehicle. 2020 4th CAA International Conference on Vehicular Control and Intelligence (CVCI), (), . doi:10.1109/cvci51460.2020.9338542 [19] Poornesh, Kavuri; Nivya, Kuzhivila Pannickottu; Sireesha, K. (2020). [IEEE 2020 International Conference on Smart Electronics ad Communication (ICOSEC) – Trichy, India (2020.9.10-2020.9.12)] 2020 International Conference on Smart Electronics and Communication (ICOSEC) – A Comparative study on Electric Vehicle and Internal Combustion Engine Vehicles. , (), 11791183. doi:10.1109/icosec49089.2020.9215386 [20] Yongliang Li;Changlu Zhao;Ying Huang;Xu Wang;Fen Guo;Long Yang; (2020). Study on Regenerative Braking Control Strategy for Extended Range Electric Vehicles. 2020 IEEE Vehicle Power and Propulsion Conference (VPPC), (), . doi:10.1109/vppc49601.2020.9330885 [21] Khalil Sinjari;Joydeep Mitra; (2020). Electric Vehicle Charging with Reactive Power Compensation to Distribution Systems. 2020 IEEE Industry Applications Society Annual Meeting, (), . doi:10.1109/ias44978.2020.9334838 [22] Kusuma, Christopher Fernaldy; Budiman, Bentang Arief; Nurprasetio, Ignatius Pulung (2019). [IEEE 2019 6th International Conference on Electric Vehicular Technology (ICEVT) – Bali, Indonesia (2019.11.18- 2019.11.21)] 2019 6th International Conference on Electric Vehicular Technology (ICEVT) – Simulation Method for Extended-Range Electric Vehicle Battery State of Charge and Energy Consumption Simulation based on Driving Cycle. , (), 336344. [23] Rachev, Svilen; Stefanov, Dimo; Dimitrov, Lyubomir; Koeva, Dimitrina (2019). IEEE 2019 Electric Vehicles International Conference (EV) – Bucharest, Romania (2019.10.3-2019.10.4)] 2019 Electric Vehicles International Conference (EV) – Evaluation of Electric Power Losses of an Induction Motor Driving a Compact Electric Vehicle at Change of Parameters and Loads. , (), 15. [24] Kamat, Suraj; Jadhav, Seema (2019). [IEEE 2019 International Conference on Advances in Computing, Communication and Control (ICAC3) – Mumbai, India (2019.12.20-2019.12.21)] 2019 International Conference on Advances in Computing, Communication and Control (ICAC3) – Design and Simulation of Low Power Charging Station for Electric Vehicle. [25] Sarathkumar, Tirunagaru V; Poornanand, Maramreddy; Goswami, Arup Kumar (2020). IEEE Students Conference on Engineering & Systems (SCES) – Prayagraj, India (2020.7.10-2020.7.12)] 2020 IEEE Students Conference on Engineering & Systems (SCES) – Modelling and Simulation of Electric Vehicle Drive through SAEJ227 & EUDC Cycles. [26] Wachter, Christian; Schuttoff, Martin; Rinderknecht, Frank; Goletz, Mirko; Ehebrecht, Daniel; Lenz, Barbara; Kuhnel, Meike; Hanke, Benedikt (2020). IEEE 2020 Fifteenth International Conference on Ecological Vehicles and Renewable Energies (EVER) – Monte-Carlo, Monaco (2020.9.10-2020.9.12)] 2020 Fifteenth International Conference on Ecological Vehicles and Renewable Energies (EVER) – Electric three-wheelers as an alternative to combustion-engined autorickshaws in Dar es Salaam – Generation of a standard drive cycle, Power Train modelling and simulation of the energy demand of light electric vehicles. [27] K. M. Sidorov;A. G. Grishchenko;B. N. Sidorov;V.I. Stroganov; (2021). Electric Propulsion System Simulation as Basis for the Electric Vehicle Digital Twin Development. 2021 Systems of Signals Generating and Processing in the Field of on Board Communications. [28] Simsek, Mustafa; Bilgin, Berk; Adam, Halil Ibrahim (2019). IEEE 2019 11th International Conference on Electrical and Electronics Engineering (ELECO) – Bursa, Turkey (2019.11.28-2019.11.30)] 2019 11th International Conference on Electrical and Electronics Engineering (ELECO) – A New Approach in Co-Simulation for Battery Electric Vehicle Modelling. [29] Guerroudj, Salim; Boulzazen, Habib; Riah, Zouheir (2018). [IEEE 2018 IEEE International Conference on Electrical Systems for Aircraft, Railway, Ship Propulsion and Road Vehicles & International Transportation Electrification Conference (ESARS-ITEC) – Nottingham, United Kingdom (2018.11.7-2018.11.9)] 2018 IEEE International Conference on Electrical Systems for Aircraft, Railway, Ship Propulsion and Road Vehicles & International Transportation Electrification Conference (ESARS-ITEC) – New approach for the evaluation of magnetic fields in dynamic wireless charging for electric vehicles. [30] Fuguo Xu;Tielong Shen; (2020). Look-ahead Horizon based Energy Optimization for Connected Hybrid Electric Vehicles. 2020 IEEE 3rd Connected and Automated Vehicles Symposium (CAVS).