
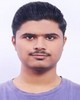
- Open Access
- Authors : Pratik Shinde , Mita Dhaygude , Niraj Rathod, Revant Pund , Neha Dhere, Pratyush Doshi
- Paper ID : IJERTV12IS040252
- Volume & Issue : Volume 12, Issue 04 (April 2023)
- Published (First Online): 04-05-2023
- ISSN (Online) : 2278-0181
- Publisher Name : IJERT
- License:
This work is licensed under a Creative Commons Attribution 4.0 International License
Thermal analysis of IC Engine Cylinder using Ansys
Pratyush Doshi
Dept. of Mechanical Engineering VIT Pune Pune, India
Niraj Rathod
Dept. of Mechanical Engineering VIT Pune Pune, India
Pratik Shinde
Dept. of Mechanical Engineering VIT Pune Pune, India
Revant Pund
Dept. of Mechanical Engineering VIT Pune Pune, India
Mita Dhaygude
Dept. of Mechanical Engineering VIT Pune Pune, India
Neha Dhere
Dept. of Mechanical Engineering VIT Pune Pune, India
Abstract Fins play a crucial role in the cylinder block of an IC engine as they facilitate the efficient dissipation of heat generated during the combustion process through convection. The efficient dissipation of heat is crucial for maintaining the consistent efficiency of an internal combustion engine.. This Paper does thermal analysis of Fins on a cylinder block of an IC engine with varying fin shape, size and fin density. The analysis is further continued by analyzing different materials like Structural Steel, Aluminum, Alumina 92% and Alumina 96%. And the results are discussed.
Keywords IC Engine Fins, Ansys, Thermal Analysis, Heat flux.
-
INTRODUCTION
Internal combustion engines play a crucial role in the global economy, powering heavy vehicles such as trucks and buses that transport goods across the world. They are also used in passenger cars and civil construction vehicles. However, internal combustion engines generate a high amount of heat during operation, which must be dissipated through various cooling systems. These systems typically rely on fins and can be classified as air-cooled, oil-cooled, or water-cooled. Ultimately, the effectiveness of engine cooling depends on the quality and design of the fins. The effectiveness of engine cooling is heavily dependent on the presence of fins, which can be classified as:
-
Air cooled engines
-
Oil cooled engines
-
Water cooled engines
Air cooled engines, These types of engines are used in both spark ignition and compression ignition engines. It typically features fins attached to the combustion cylinder, allowing direct interaction between air and cylinder for the purpose of cooling.
COOLING FINS :-
-
Fins are extruded surfaces created to increase the heat transfer rate for a given surface temperature or to decrease the surface temperature for a defined heat transfer rate.
-
They can be used to increase heat transfer by convection between two surfaces and the surrounding fluid. Fins are often utilized in various engineering applications to
dissipate large amounts of thermal energy from small areas, thereby aiding in achieving the desired cooling effect.
-
Fins increase the effective surface area of a model, thereby increasing energy transfer by convection. There are two types of straight fins: rectangular fins and triangular fins. Triangular fins are a popular choice because they require much less volume than rectangular fins for the same heat transfer.Therefore, fins are of practical importance because they maximize heat flow per unit mass and are easy to manufacture.
STRUCTURE OF FIN:
The effectiveness of heat dissipation in fins is heavily influenced by their structure. Many researchers have proposed different shapes of fins and evaluated their heat transfer effectiveness under different heat flux conditions. Parametric evaluations have also been performed by varying fin thickness, fin spacing, and length of the fin. Some of the different types of fin structures include rectangular fins, offset strip fins, triangular fins, perforated fins, wavy fins, and louvered fins.
-
-
METHODOLOGY
To find the dimensions of the cylinder that will be analyzed, the maximum power is considered to be 43 BHP at 9000 RPM and the bore x stroke distance is 89 x 60 mm.
After stress calculations the thickness of the cylinder is calculated to be 17.88 mm. And the length of the cylinder is found to be 69 mm. The clearance for the stroke is 9mm. The number of studs calculated are 5.
-
Tools Used
The Cad modeling of the cylinder is made using Solidworks software. CAD files of cylinder blocks with and without fins are designed based on the dimensions mentioned above. Two types of fins are designed, circular fins and rectangular fins. In each type of fins 4 different fins are designed with different fin size, spacing and density.
The four different designs are
-
2.5 mm fins with 5 mm spacing, total number of fins is 14
-
2.5 mm fins with 7.5 mm spacing, total number of fins is 10
-
2.5 mm fins with 10 mm spacing, total number of fins is 7
-
5 mm fins with 10 mm spacing, total number of fins is 7
And the Analysis is done using the Ansys software. The details are given below in setup.
-
-
Setup
Steady-State Thermal in ansys software is used to do the thermal analysis of the cylinder block. The .igs files are imported in Ansys and a nodal temperature of 2000 C is given inside the cylinder as the most powerful stroke of the piston produces the temperature of 1900 C to 2200 C.
Then for convection all surfaces are selected except the inside of the cylinder and the holes for the studs. Then 4 different materials are used that are :-
-
Structural Steel (Isotropic Thermal Conductivity is 60.5 Wm^-1C^-1)
-
Aluminum (Isotropic Thermal Conductivity is 237.5 Wm^-1C^-1)
-
Alumina 92% (Isotropic Thermal Conductivity is 25 Wm^-1C^-1)
-
Alumina 96% (Isotropic Thermal Conductivity is 26 Wm^-1C^-1)
-
The Isotropic Thermal Conductivities given above are embedded in the Ansys software itself.
For convection the ambient temperature is taken to be 22 C(ramped). Then in the solutions the Temperature and Heat Flux are added and the solutions for each Cylinder block with and without Fins is checked.
-
-
RESULTS & DISCUSSION The results for all the Models are as follows :-
-
Cylinder block Without any fins
Materials
Analysis Outcomes
Nodal Temperature
Minimum Temperature
Heat Flux
Minium
Maximu m
Structural Steel
2000
1935.2
256.27
1.44 e^5
Aluminum
2000
1983
271
1.48 e^5
Alumina 92%
2000
1856.2
254.34
1.37 e^5
Alumina 96%
2000
1851
253.62
1.37 e^5
Table 1 : Analysis Data Without Fins
Fig1.Temperature analysis no fins
Fig 2.Heat Flux Analysis no Fins
It can be observed that the minimum temperature for the cylinder block without any fins the minimum temperature achieved is 1851 C for the material Alumina 96% . The Heat Flux is maximum with 253.62 WM-2 near the area of the studs that is closer to the cylinder for Alumina 96%. And is minimum with 1.48 e^5 WM-2 near the area of the studs that is away from the cylinder for Aluminum.
-
With Circular fins
Fig 3.Temperature analysis with Circular fins
Fig4.Heat Flux Analysis with Circular Fins
Materials
Analysis Outcomes
Nodal Temperature
Minimum Temperature
Heat Flux
Minium
Maximu m
Structural Steel
2000
1645.5
5944.2
6.35 e^5
Aluminum
2000
1894
6515.9
7.38 e^5
Alumina 92%
2000
1333.1
5328
5.21 e^5
Alumina 96%
2000
1315.7
5293.4
5.14 e^5
-
2.5 mm fins with 5 mm spacing, total number of fins is 14
Material s
Analysis Outcomes
Nodal Temperatur e
Minimum Temperature
Heat Flux
Miniu m
Maxim um
Structur al Steel
2000
1574.8
8753.3
8.72
e^5
Aluminu m
2000
1867
10773
1.05
e^6
Alumina 92%
2000
1233.2
6650.3
6.90
e^5
Alumina 96%
2000
1215.3
6521.6
6.80
e^5
Table 2 : .Analysis Data With 2.5 circular fins with 5 mm spacing, total number of fins is 14
It can be observed that the minimum temperature for the cylinder block with 2.5 circular fins with 5 mm spacing, the minimum temperature achieved is 1215.3 C for the material Alumina 96% . The Heat Flux is maximum with 6521.6 WM- 2 near the area of the studs that is closer to the cylinder for Alumina 96%. And is minimum with 1.05 e^6 WM^-2 near the outer perimeter the fins for Aluminum
-
2.5 mm fins with 7.5 mm spacing, total number of fins is 10
Table 4 : .Analysis Data With 2.5 circular fins with 10 mm spacing, total number of fins is 7
It can be observed that the minimum temperature for the cylinder block with 2.5 circular fins with 10 mm spacing, total number of fins is 7, the minimum temperature achieved is
1315.7 C for the material Alumina 96% . The Heat Flux is maximum with 5293.4 WM-2 near the area of the studs that is closer to the cylinder for Alumina 96%. And is minimum with 7.38 e^5 WM^-2 near the outer perimeter for Aluminum
d. 5 mm fins with 10 mm spacing, total number of fins is 7
Materials
Analysis Outcomes
Nodal Temperature
Minimum Temperature
Heat Flux
Minium
Maximu m
Structural Steel
2000
1616.4
3063.2
7.22 e^5
Aluminum
2000
1883.3
3655.8
8.49 e^5
Alumina 92%
2000
1292.1
2439.2
5.85 e^5
Alumina 96%
2000
1274
2403.6
5.77 e^5
Table 3 : .Analysis Data With 2.5 circular fins with 7.5 mm spacing, total number of fins is 10
It can be observed that the minimum temperature for the cylinder block with 2.5 circular fins with 7.5 mm spacing, the minimum temperature achieved is 1274 C for the material Alumina 96% . The Heat Flux is minimum with 2403.6 WM- 2 near the area of the studs that is closer to the cylinder for Alumina 96%. And is maximum with 8.49 e^5 WM^-2 near the outer perimeter for Aluminum
c. 2.5 mm fins with 10 mm spacing, total number of fins is 7
Material s
Analysis Outcomes
Nodal Temperatur e
Minimum Temperature
Heat Flux
Miniu m
Maxim um
Structur al Steel
2000
1729
6358
4.72
e^5
Aluminu m
2000
1921.8
6957.4
5.32
e^5
Alumina 92%
2000
1471
5564.3
4.00
e^5
Alumina 96%
2000
1456.7
5517
3.96
e^5
Table 5 : .Analysis Data With 5 mm fins with 10 mm spacing, total number of fins is 7
It can be observed that the minimum temperature for the cylinder block with 5 circular fins witp0 mm spacing, total number of fins is 7, the minimum temperature achieved is
1456.7 for the material Alumina 96% . The Heat Flux is maximum with 5517 WM-2 near the area of the studs that is closer to the cylinder for Alumina 96%. And is minimum with
5.32 e^5 WM^-2 near the outer perimeter for Aluminum
-
-
With Rectangular fins
Fig 5.Temperature analysis with Rectangular fins
Fig 6 .Heat Flux Analysis with Rectangular Fins
Materials
Analysis Outcomes
Nodal Temperature
Minimum Temperature
Heat Flux
Minium
Maximu m
Structural Steel
2000
1250.1
8504.1
1.20 e^6
Aluminum
2000
1734.5
10382
1.59 e^6
Alumina 92%
2000
829
6667.5
8.64 e^5
Alumina 96%
2000
809.81
6570.7
8.48 e^5
a. 2.5 mm fins with 5 mm spacing, total number of fins is 14
Materials
Analysis Outcomes
Nodal Temperature
Minimum Temperature
Heat Flux
Minium
Maximu m
Structural Steel
2000
1250.1
8504.1
1.20 e^6
Aluminum
2000
1734.5
10382
1.59 e^6
Alumina 92%
2000
829
6667.5
8.64 e^5
Alumina 96%
2000
809.81
6570.7
8.48 e^5
Table 7 : .Analysis Data With 2.5 rectangular fins with 7.5 mm spacing, total number of fins is 10
It can be observed that the minimum temperature for the cylinder block with 2.5 rectangular fins with 7.5 mm spacing, total number of fins is 10, the minimum temperature achieved is 809.81 C for the material Alumina 96% . The Heat Flux is maximum with 6570.7 WM-2 near the area of the studs that is closer to the cylinder for Alumina 96%. And is minimum with 1.59 e^6 WM^-2 near the vertices of the fins for Aluminum
Materials
Analysis Outcomes
Nodal Temperature
Minimum Temperature
Heat Flux
Minium
Maximu m
Structural Steel
2000
1303.1
6890.8
8.81 e^5
Aluminum
2000
1761
9104.6
1.12 e^6
Alumina 92%
2000
882.23
4898.2
6.62 e^5
Alumina 96%
2000
862.27
4805.7
6.52 e^5
c. 2.5 mm fins with 10 mm spacing, total number of fins is 7
Table 6 : .Analysis Data With 2.5 rectangular fins with 5 mm spacing, total number of fins is 14
It can be observed that the minimum temperature for the cylinder block with 2.5 rectangular fins with 5 mm spacing, total number of fins is 14, the minimum temperature achieved is 809.81 C for the material Alumina 96% . The Heat Flux is maximum with 6570.7 WM-2 near the area of the studs that is closer to the cylinder for Alumina 96%. And is minimum with 1.59 e^6 WM^-2 near the vertices of the fins for Aluminum
b. 2.5 mm fins with 7.5 mm spacing, total number of fins is 10
Table 8 : .Analysis Data With 2.5 rectangular fins with 10 mm spacing, total number of fins is 7
It can be observed that the minimum temperature for the cylinder block with 2.5 rectangular fins with 10 mm spacing, total number of fins is 7, the minimum temperature achieved is 862.27 C for the material Alumina 96% . The Heat Flux is maximum with 4805.7 WM-2 near the area of the studs that is closer to the cylinder for Alumina 96%. And is minimum with 1.12 e^6 WM^-2 near the vertices of the fins for Aluminum
d. 5 mm fins with 10 mm spacing, total number of fins is 7
Materials
Analysis Outcomes
Nodal Temperature
Minimum Temperature
Heat Flux
Minium
Maximu m
Structural Steel
2000
1339.3
4240.9
8.31 e^5
Aluminum
2000
1778.4
6071.4
1.05 e^6
Alumina 92%
2000
919
3217.8
6.19 e^5
Alumina 96%
2000
899.24
3192.9
6.08 e^5
Table 9 : .Analysis Data With 2.5 rectangular fins with 10 mm spacing, total number of fins is 7
And is minimum with 1.05 e^6 WM^-2 near the vertices of the fins for Aluminum
-
-
CONCLUSION
It can be observed that the maximum heat dissipation is happening in the material Alumina 96% with Isotropic Thermal Conductivity of 26 Wm^-1C^-1 no matter what the shape or size or density of the fins is. And the minimum heat dissipation is happening in Aluminum with Isotropic Thermal Conductivity of 237.5 Wm^-1C^-1.
The Maximum Heat flux is always near the area of the studs on the side that is closer to the cylinder block, and is minimum on the farthest point from the cylinder block. The maximum Heat Flux is always achieved in the Aluminum material and the minimum is always in Alumina 96% material.
The Maximum heat dissipation is always happening in the
2.5 fins with 5 mm spacing. And The minimum heat dissipation is happening in the cylinder block without any fins, and the maximum heat dissipation is happening in 2.5 mm rectangular fins with 5 mm spacing no matter what the material is. This is because the 2.5 mm rectangular fins with 5 mm spacing have more area as well as more volume for convection and conduction respectively.
The maximum heat dissipation is seen in 2.5 mm Rectangular fins with 5 mm spacing with Alumina 96% material with minimum temperature of 809.81 C.
-
FUTURE SCOPE
The current project focused on conducting thermal analysis of the cylinder in an internal combustion engine. However, the same analysis could also be performed on the cylinder head. Additionally, there is potential for using different types of materials in the analysis and exploring various shapes and sizes of fins for optimal heat dissipation.
-
REFERENCES
April-2021
[3] Ravindra R. Navthar, Design and analysis of cylinder and cylinder head of 4-stroke SI engine for weight reduction, International Journal of Engineering Science and Technology (IJEST), ISSN : 0975-5462 ,Vol. 4 No.03 March 2012
[4] Syed Mujahid Husain1, Siraj Sheikh, DESIGN AND ANALYSIS OF ROCKER ARM, ISSN 2278 0149 www.ijmerr.com Vol. 2,No. 3, July 2013 © 2013 IJMERR
[5] Kunal S. Nagrik, Nawaz M. Merchant, Mukesh S. Rajpurohit, Swanand S. Pachpore, Design, analysis and comparison for a different cylinder head of C.I. Engine, International Journal of Advance Research, Ideas and Innovations in Technology, ISSN: 2454-132X, (Volume3, Issue2)