
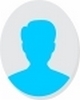
- Open Access
- Authors : Frosina Velichkovska, Marija Stojchevska, Sara Srebrenkoska, Svetlana Risteska, Vineta Srebrenkoska
- Paper ID : IJERTV12IS060034
- Volume & Issue : Volume 12, Issue 06 (June 2023)
- Published (First Online): 19-06-2023
- ISSN (Online) : 2278-0181
- Publisher Name : IJERT
- License:
This work is licensed under a Creative Commons Attribution 4.0 International License
Properties of Composite Parts Manufactured using UD Carbon Fiber/Epoxy Prepreg
Frosina Velichkovska 1, Marija Stojchevska1, PhD Sara Srebrenkoska2, PhD Svetlana Risteska3, PhD Vineta Srebrenkoska1,
1Faculty of Technology, Goce Delcev University, Krste Misirkov 102A, 2000 Stip, Republic of North Macedonia
2Faculty of Mechanical Engineering, Goce Delcev University, Krste Misirkov 102A, 2000 Stip, Republic of North Macedonia
3Institute of Advanced Composites and Robotics-Krusevski pat bb Prilep, R. North Macedonia
Abstract – Polymer composites based on carbon fibers are used in a large number of applications generaly as bearing structural parts in aerospace, automotive and other industries. In many composite parts, unidirectional (UD) tapes are used to create structures in aircraft, vehicles in addition to sporting and consumer markets. UD tapes are lightweight and exceptionally durable and they are the basic building blocks for a production of composite structural laminates. The aim of this work is to determine the influence of angles and technologies for curing on the structural and mechanical properties of UD carbon fiber/epoxy laminate, manufactured with Automated Tape Layup (ATL) and Automated Fiber Placement (AFP) technologies. The tensile strength and modulus at different laminates with different technologies were calculated since ASTM D3039. The failure analysis of the samples was investigated by scanning electron microscopy (SEM). The results have shown that the mechanical properties depend on technologies for curing. The results of the present study indicate that angles have a significant effect on composite failure mode. It is also found that the strength of UD composites both increased at samples curing with press technology.
Keywordscomposite, AFP/ATL, tensile strength, curing
-
INTRODUCTION
The use of composite materials in aerospace, automotive and ship industry allows manufacturing lighter and more efficient mechanical structures. Indeed, proper use of the orthotropic properties of these materials enables further tailoring of the structure to the loadings than when using isotropic materials. However, this comes at the cost of a more complicated design and sizing process firstly because of the orthotropic behavior of composite materials but also because of the manufacturing process which induces specific constraints in the use of these materials [1,2]. Besides the manufacturing of composites part by hand layup of large pieces of reinforcement material, another group of methods is gaining interest since its first introduction in the 1970s. These methods rely on the robotized layup of bands of unidirectional reinforcement material allowing more accurate and more repeatable manufacturing process [2-15]. In this group, two main methods can be identified Automated Tape Layup (ATL) and Automated Fiber Placement (AFP). ATL makes use of a robotic arm to layup tapes (up to 150mm wide) of unidirectional prepeg and benefits from high productivity for large and simple flat parts. Therefore, the manufacturing of more complicated parts can be handled by AFP but with a lower productivity than ATL. For ATL and AFP processes, one of the manufacturing issues is the
determination of successive courses trajectories. Indeed, for these processes, it is crucial that there are no overlaps and no gaps between adjacent courses in order to ensure maximal strength and minimum weight for the final part. [3] New approach for computing fiber orientations resulting from ATL/AFP draping is used as the basis for composite shell optimization. The main advantages of this approach over previous research is that it allows determining fiber orientations and deposition courses that correspond to a layup free from overlaps and gaps between successive courses.
In this paper, study of the influence of fiber orientation on the structural and mechanical properties of laminate manufactured with help of AFP and ATL technologies is presented. With help of mathematical method was achieved similar thickness on all of manufactured composite parts, while mechanical properties studied include values of tensile strength, strain and modulus of elasticity. With help of factorial design of experiment (DOE) the influence between technological parameters used in sample production was presented.
-
EKSPERIMENT
-
Specimen Preparation
A unidirectional laminate was prepared using 8/14 layers of UD150 IM7 12K/M21 carbon fiber/epoxy prepreg with a 34 wt.% nominal resin content (Hexcel, France). Prepreg properties are presented in table I. Automatic fiber placement was carried out on laboratory ATL/AFP machine manufactured from Mikrosam D.O.O. Manufactured composite laminates had different angles on UD placement.
Unidirectional laminates were cured with two process technologies – pressure (PR) and vacuum bagging (VB) (show at fig 1 to fig. 4). After curing, from the produced composite laminates were cut samples for testing according to ASTM D 3039 [16]. The manufactured test samples ready for testing are shown in figure 5.
Fig.1 Hydraulic press with temperature and pressure / Curing curve for pressing: time temperature
Fig. 2. Finished composite parts from pressure.
Fig.3 Vacuum Bagging of composite parts / Curing curve for vacuum bagging: time temperature
Properties of manufactured prepreg
Volatile content (%)
<1
Mass resin content (%)
30-36
PAW (g/m2)
300
Fig. 4. Finished composite parts from vacuum bagging. TABLE I. PROPERTIES OF PREPREG
-
Mechanical Testing
Tensile properties of manufactured samples were determined with test in accordance with the procedure described in ASTM D 3039 standard. For that purpose computer controlled universal testing machine (UTM) Hydraulic press, SCHENCK- Hidrauls PSB with maximal load of 250 kN, constant crosshead speed of 5 mm/min was used. Load and displacement were recorded by an automatic data acquisition system for each sample. Minimum four reproducible tests were conducted for each sample at room temperature. Samples ready for testing are presented on Fig. 5, whereas test is given on Fig. 6
Fig.5 Prepared composite samples ready for testing.
Fig.6. Tensile test on universal testing machine.
-
Design Of Experiment (DOE)
To optimize the production process of laminated composite samples and quantitatively to determine the influence of production parameter: technology of placement (X1), polymerization technology (X2) laying angle (X3), design of experiment (DOE) has been applied. DOE has been well known for its efficiency and allow gaining a maximum of information from a minimum amount of experiments.
For that aim factorial design of experiment with 23 permutations was used in the production of composite samples. Table II represents technological parameters which are used in two different levels of variation and totally 8 different experiments takeing in account all combinations of parameters, whereas Table III represents manufacturing parameters of each laminated sample.
The analysis of the curing (PR/VB) and placement technologies (AFP/ATL) of the various designs were performed by tensile tests which were carried out on 32 samples (8×4 replications).
-
Fractographic Analysis
Fractured surfaces obtained from performed tests were examined at different magnification with help of scanning electron microscope (SEM) from Tesan type Vega3 in order to observe fracture behavior of laminated specimens.
TABLE II. LEVEL OF USED PARAMETERS
Symbol
Parameters
Parameter level
1
-1
A (X1)
technology of placement
ATL
AFP
B (X2)
polymerization technology
PR
VB
C (X3)
laying angle
90
0
Sample No
X1
X2
X3
A
B
C
1
AFP
VB
0
-1
-1
-1
2
ATL
VB
0
1
-1
-1
3
AFP
PR
0
-1
1
-1
4
ATL
PR
0
1
1
-1
5
AFP
VB
90
-1
-1
1
6
ATL
VB
90
1
-1
1
7
AFP
PR
90
-1
1
1
8
ATL
PR
90
1
1
1
TABLE III. DESIGN OF EXPERIMENT (23) FOR LAMINATED SAMPLES
-
-
RESULTS AND DISSCUSSION
-
Tensile Strength
Manufactured composite samples were clamped and tensile tests were performed. The tests were closely monitored and the load at which completed fracture of the specimen occurred has been accepted as breakage load. Load-displacement curves were plotted for every sample and values for stress, strain and module of elasticity were calculated as average. The flexural stress () in the outer surface of the test specimens occurred at the midpoint. These stresses were determined from the relation [16]:
TABLE V. RESULTS OF TENSILE STRENGTH SPECIMENS –
COMPARED
=
laying angle
polymerization technology
VB
PR
VB
PR
technology of placement
AFP
ATL
00
angle
1
average (MPa)
No 1
average (MPa)
No 3
average (MPa)
No 2
average (MPa)
No 4
1831
1926
1546
1334
900
angle
2
average (MPa)
No 5
average (MPa)
No 7
average (MPa)
No 6
average (MPa)
No8
21.78
36 .43
7.33
9
(1)
Where, is the Tesnsile strength (MPa), F is the load (N), A is the area (mm2), b is the width of the specimen (mm), and
h is the thickness of the specimen (mm).Tensile modulus of elasticity (E) and strain () of the composite specimens were determinate using equations according standard [16].
TABLE IV. RESULTS FROM TENSILE TESTING FOR EACH DESIGN
Sample No
1
1
1501.35
5
1
26.691
2
2216.67
2
12
3
1606.43
3
12.653
4
2000.00
4
14.004
2
1
1404.79
6
1
7.25
2
1404.79
2
7.38
3
1777.64
3
7.46
4
1597.44
4
7.24
3
1
1756.89
7
1
39.60
2
1715.69
2
32.42
3
1838.24
3
38.14
4
2392.58
4
35.57
4
1
1318.00
8
1
9.90
2
1350.00
2
8.10
3
1318.00
3
9.90
4
1350.00
4
8.10
Received results from performed tests on laminated composite samples are given in table V, where maximal flexural strength of 1925.85 MPa for sample No3 and minimal flexural strength of 7.33 MPa for sample No6 can be observed.
Comparison between results of specimens manufactured at same technological parameters, but different fiber orientation can give a notice that all samples tested at UD direction (00) had performed better mechanical properties in comparison to the samples tested at CD direction (900). This means that fiber direction directly affects Tensile strength of laminated composite samples up to 99%. Received average results from tensile tests are shown in table VI
-
Design Of Experiment (DOE)
The results for tensile strength, dispersion and minimal value of parameters final coefficients for factorial design 23 in this research are shown in table VI. According to table VI, minimal calculated value of parameters final coefficients is 71,98. Parameters function and their interaction with 5% mistake are represented with (2). In the experimental design the term X1X3 is the interaction between the factors which might also have the influence on the response, in our case tensile strength (Y value).
Y= 838.3-114X1-821X3+105X1X3 (2)
From design 23 were calculated Cochran criteria (Gcal) with value 0.43 and Fisher criteria (Fcal) with value 0.9, which fulfill the rule Gcal < Gtab and Fcal < Ftab [17, 18]. According to this, the hypothesis for model 23 is acceptable with 5% mistake.
By analyzing the regression equation (2), it should be noted that the main positive contribution to the Y is given by the parameter C (X3) and the parameter A (X1). The influence of the polymerization process or parameter B (X2) affects insignificantly on the tensile strength. For the contribution of the interaction of the two factors to the Y, only parameter AC (X1X3) has a small effect on the tensile strength. This can also be seen from the following graphs (fig. 7 and fig, 8).
1546.2
No
yexp
ycal
Sy2
bi
1
1831.1
1878.5
102570
71.98
2
1440.1
32061.2
3
1925.8
1878.5
99409.3
4
1334
1440.1
341.33
5
21.782
29.11
87.88
6
7.33
8.17
0.01
7
36.43
29.11
9.95
8
9
8.17
1.08
TABLE VI. RESULTS FROM DESIGN OF EXPERIMENT (DOE)
Fig.7. The factors that affect the mechanical characteristics
Fig.8. The factors that do not affect the mechanical characteristics
-
Scanning Electron Microscopy (SEM) Analysis
Scanning electron microscopy (SEM) analysis were performed in order impregnation quality of carbon fibers into the epoxy resin during VB/PR process to be determined. In figure 9 are presented SEM analysis from composite samples. However, voids with smaller dimensions can be observed on some places at samples manufactured with No.4 and 8, which can lead to reduction of mechanical properties of laminated samples.
Fig. 9. SEM analysis of samples.
-
-
CONCLUSION
Experimental measurements of the tensile strengths of laminated samples for determined ranges of parameters have been carried out implementing 23 full factorial experimental design. Regression equation was established for tensile strength
as a function of the technology of placement, polymerization technology and laying angle. The experimental procedure described in the present work is sufficient to show the influence of the parameters on the tensile properties of laminated samples
. The test results indicated that the change of the technology of placement and laying angle cause a variation in the final mechanical results, whereas the influence of the other parameter: technology of placement is much lower, and the interaction of the factors has a negligible effect on the response.
REFERENCES
[1] Stephen W. Tsai (1985): Composites Design, 4 th edition pp 815 [2] Daniel Gay , Suong V. Hoa, Stephan W. Tsai, (2003). Composite materials: Design and application [3] Robert M.Jones (1975): Mechanics of composite materials [4] G. Rathnakar and H. K. Shivanan, Experimental evaluation of strength and stiffness of fiber reinforced composites under flexural load, International Journal of Engineering and Innovative Technology (IJEIT), Vol. 2, Issue 7, January 2013. [5] M. Davallo, H. Pasdar and M. Mohseni, Effects of laminate thickness and ply-stacking sequence on the mechanical properties and failure mechanism of unidirectional glass-polyester composites, International Journal of ChemTech Research, Vol. 2, No.4, pp. 2118-2124, October- December 2010. [6] A. Bruce Hulcher, David M. McGowan and Brian W. Grimsley, (2001): Processing and Testing of Thermoplastic Composite Cylindrical Shells Fabricated by Automated Fiber Placement; NASA conferences. [7] Y. Basavaraj and H. Raghavendra, Experimental and numerical study of the influence of volume fraction on tensile and flexural strength of e-glass epoxy cross ply laminates, International Journal of Mechanical and Industrial Technology Vol. 2, Issue 1, pp. 39-44, April 2014 – September2014.
[8] C. Dong and I. J. Davies, Flexural strength of bidirectional hybrid epoxy composites reinforced by E glass and T700S carbon bres, Composites Part B: Engineering, Vol. 72, pp. 65-71, April 2015. [9] S. R. J. Bumpus, Experimental setup and testing of fiber reinforce composite structures, Master Thesis, Department of Mechanical Engineering, University of Victoria, 2005. [10] C. Dong and I. J. Davies, Flexural properties of hybrid composites reinforced by S-2 glass abd T700S carbon fibres, Composites Part B: Engineering, Vol. 43, Issue 2, pp. 573-581, 2012. [11] I. D. G. A. Subagia, L. D. Tijing, H. R. Pant and H. K. Shon, Effect of stacking sequence on the flexural properties of hibrid composites reinforced with carbon and basalt fibers, Composites Part B: Engineering, Vol. 58, pp. 251-258, 2014. [12] C. Dong and I. J. Davies, Flexural properties of glass and carbon fiber reinforced epoxy hybrid composites, J. Materials: Design and Applications, Vol. 227, Issue 4, pp. 308-317, 2013. [13] A. Azzam and W. Li, An experimental investigation on the three-point bending behavior of composite laminate, 2014 Global Conference on Polymer and Composite Materials (PCM 2014), 2014. [14] H. Zhu, B. Wu, D. Li, D. Zhang and Y. Chen, Influence of voids on the tensile performance of carbon/epoxy fabric laminates, J. Mater. Sci. Technol., Vol. 27, Issue 1, pp. 69-73, January 2011. [15] S. Risteska, B. Samakoski and M. Stefanovska, Properties of composite trapezoidal parts manufactured with help of filament winding technology using taguchi method, International Journal of Engineering Research & Technology (IJERT), Vol. 3 Issue 7, July 2014. [16] Standard ASTM 3039 Standard Test Method for Tensile Properties of Polymer Matrix Composite Materials, Annual Book of ASTM Standards Vol 03.01,2000. www.astm.org [17] . . and . . , , , 1980. [18] A. Dean and D. Voss, Design and analysis of experiments, Springer- Verlag New York, 1999. [19] Salman Khan, (2011): Automated Fiber Placement Process Overview. Concordia University: Thermal Control System Design for AFP Process, chapter 2 [20] Lukaszewicz, D. H. -J. A., Ward, C., & Potter, K. D. (2012): The engineering aspects of automated prepreg layup: History, present and future. Composites Part B: Engineering, 43(3), 997-1009. 10.1016/j.compositesb.2011.12.003