
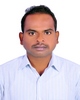
- Open Access
- Authors : Md. Yakoob Pasha, M. Tirumala Devi, T. Sumathi Uma Maheswari
- Paper ID : IJERTV12IS070131
- Volume & Issue : Volume 12, Issue 07 (July 2023)
- Published (First Online): 17-08-2023
- ISSN (Online) : 2278-0181
- Publisher Name : IJERT
- License:
This work is licensed under a Creative Commons Attribution 4.0 International License
Reliability Analysis of the Shaft Subjected to Torsion When Shear Stress Follows the Exponential Distribution
Md. Yakoob Pasha
Department of Mathematics,
Kakatiya University, Warangal-506009, Telangana, India.
M. Tirumala Devi
Department of Mathematics,
Kakatiya University, Warangal-506009, Telangana, India.
T. Sumathi Uma Maheswari
Department of Mathematics,
Kakatiya University, Warangal-506009, Telangana, India.
Abstract – The term torsion describes how a straight part will twist when subjected to a turning moment or torque that has the tendency to cause a rotation about the longitudinal axis. In order to transmit energy by rotation, a turning force is always used in workshops and factories. This rotating force is applied to the pulley's rim, a point that is keyed to the shaft, or any other suitable location that is spaced from the shaft's axis. The reliability analysis of the shafts subjected to torsion and torque conveyed by a hollow or solid circular shaft when shear stress has an exponential distribution is presented in this work.
Keywords Reliability, shear stress, exponential distribution, circular solid shaft, hollow circular shaft.
-
INTRODUCTION
The shaft is the major part of the power transmission system that requires careful design for the machine to operate effectively. The spinning part that transfers electricity from one location to another is the shaft. The most important part of practically every mechanical machine and system is the shaft. Anil Misra et al. [1], discussed with the view of developing methods for reliability based design, the finite difference technique was combined with the Monte-Carlo simulation method to create a probabilistic loaddisplacement analysis. The Monte Carlo simulation method was used, in lieu of other closed-form probabilistic techniques, due to the complexity of the loaddisplacement analysis. Dr. Edward E. Osakue et al. [2] studied a design verification study of three shafts loaded in bending and torsion was conducted based on probabilistic approach using Gerber failure rule. The probabilistic model parameters like mean and variance values to estimate expected design results while then reliability of the design is evaluated using the
coefficients of variation or covariance of the design parameters. The equations for the covariance of strength and stress parameters were developed using sensitivity analysis based on first order Taylor series expansion of design relationships. Dr R. K. Bansal [3] and R. S. Khurmi [7] discussed shear stress produced in a circular shaft subjected to torsion, Torque transmitted by a circular solid shaft and a hollow circular shaft. E. Balagurusamy [4] discussed stress dependent hazard models, the failure rate of almost all components is stress dependent. K. C. Kapur and L. R. Lamberson [5] discussed design of a shaft subjected to torsion, when a shaft is subjected to a torque a shearing stress is produced in the shaft. The shear stress varies from zero in the axis to a maximum at the outside surface of the shaft. P. Hari Prasad et al. [6] studied eccentricity of symmetrical column in a widely varying range of values. The increase in eccentricity was not reflective of the increase in reliability. T. S. Uma Maheswari et al. [8] Reliability analysis of unsymmetrical columns subjected to eccentric load for stress follow exponential distribution has been obtained.
-
STATISTICAL MODEL
The probability of failure as function of time can be defined by
where is a random variable denoting the time to failure.
Reliability function is
The failure rate of the almost all components is stress dependent. For such cases, a power function model is defined [9] as given below
(1)
Therefore
where is the failure rate at rated stress conditions, is hazard function, and are stress ratios for two different kind of stresses and a, b are positive constants.
The exponential distribution is the probability distribution of the time between events in a process in which events occur continuously and independently at a constant average rate. Its probability density function is given by
where and is the scale parameter.
The corresponding cumulative distribution function is given by
and the reliability function
The formula for the hazard function of the exponential distribution is
-
TORSION OF SHAFTS
The shaft is said to be in torsion when equal and opposing torques are applied to the shaft's two ends. The torque is calculated by multiplying the force (tangential to the shaft ends) by the shaft's radius. The shaft experiences a twisting moment as a result of the torques applied at the two ends. The material of the shaft is subjected to shear loads and strains as a result.
-
Shear stress produced in a circular shaft subjected to torsion
The maximum shear stress induced in a shaft subjected to twisting moment [3] is given by
where is radius of the shaft is modulus of rigidity is angle of twisting moment and is length of the shaft.
The reliability function for shear stress is,
where , the failure rate function
-
Torque transmitted by a circular solid shaft
The maximum torque transmitted by a circular solid shaft is obtained from the maximum shear stress induced at the outer surface of the solid shaft. The torque transmitted by a solid shaft [3] is given by
where is maximum shear stress and is diameter of circular solid shaft.
(2)
The reliability function for the circular solid shaft is
-
Torque transmitted by a hollow circular shaft Torque transmitted by a hollow circular shaft is obtained in the same way as for a solid shaft.
The torque) transmitted by hollow circular shaft [9] is given by
where is maximum shear stress, is external diameter of hollow circular shaft and is internal diameter of hollow circular shaft.
(3)
The reliability function for hollow circular shaft is
-
-
Numerical results and discussion for reliability
Table 1
R=16mm, C=73.1 GPa, L=64mm,
t
R(t)
0.1
0.85261313
0.2
0.726949149
0.3
0.619806389
0.4
0.528455065
0.5
0.450567727
0.6
0.384159960
0.7
0.327539826
0.8
0.279264756
0.9
0.238104798
1.0
0.203011277
radian.
1
0.9
Reliability
0.8
0.7
0.6
0.5
0.4
0.3
0.6
0.182538653
0.7
0.232742437
0.8
0.279264756
0.9
0.321788036
1.0
0.360423338
R(t)
0.2
0.1 0.2 0.3 0.4 0.5 0.6 0.7 0.8 0.9 1
Time
R(t)
0.4
0.35
0.3
Figure 1: Time vs Reliability
Table 2
t=0.6, R=16 mm, C=73.1 GPa, L=64 mm.
0.25
0.2
0.15
0.1
0.05
0
0.1 0.2 0.3 0.4 0.5 0.6 0.7 0.8 0.9 1
Scale Parameter
Figure 3: Scale Parameter vs Reliability
Table 4
t=0.9, R=6 mm, radian, L=32 mm.
R(t)
0.06
0.193060822
0.08
0.111581501
0.10
0.064489684
0.12
0.037272481
0.14
0.021542016
0.16
0.012450431
0.18
0.007195856
0.20
0.004158919
0.22
0.002403691
0.24
0.001389238
C
R(t)
4.2
0.940034749
16.2
0.787793178
28.2
0.660207607
40.2
0.553284918
52.2
0.463678694
64.2
0.388584478
76.2
0.325652005
88.2
0.272911643
100.2
0.228712748
112.2
0.191672003
0.2
0.18
0.16
R(t)
Reliability
0.14
0.12
0.1
0.08
0.06
0.04
0.02
0
Twisting Moment
0.06 0.08 0.1 0.12 0.14 0.16 0.18 0.2 0.22 0.24
Figure 2: Twisting Moment vs Reliability
1
0.9
0.8
R(t)
Reliability
0.7
0.6
0.5
0.4
0.3
0.2
Table 3
t=0.8, R=16mm, L=64mm, C=73.1 GPa,
0.1
0 20 40 60 80 100 120
Modulus of Rigidity
radian.
R(t)
0.1
3.69938E-05
0.2
0.006082254
0.3
0.033320360
0.4
0.077988804
0.5
0.129904982
Figure 4: Modulus of Rigidity vs Reliability
Table 5
t=0.6, R=4 mm, C=73.1 GPa, radian
L
R(t)
55
0.757060857
50
0.736281471
45
0.711657397
40
0.682032137
35
0.645747410
30
0.600352678
25
0.542110404
20
0.465167836
15
0.360423338
10
0.216381116
-6
x 10
9
8
Reliability
7
6
5
4
R(t)
3
2
1
0
0 1 2 3 4 5 6 7 8 9 10
Total Torque
7
x 10
0.9
Figure 6: Total Torque vs Reliability
0.8 R(t)
0.7
Reliability
0.6
0.5
0.4
0.3
R(t)
240
0.438400764
230
0.382182624
220
0.32088532
210
0.255237078
200
0.187065524
190
0.120078851
180
0.060849983
170
0.018926206
160
0.001607273
150
2.89656E-07
0.2
Length of the Shaft
Table 7
t=0.8, T=982000,
10 15 20 25 30 35 40 45 50 55
Figure 5: Length of the Shaft vs Reliability
Table 6
t=0.4, D=198 mm.
T
R(t)
98900000
4.34673E-57
88900000
2.17287E-51
78900000
1.08619E-45
68900000
5.42971E-40
58900000
2.71424E-34
48900000
1.35681E-28
38900000
6.78251E-23
28900000
3.39048E-17
18900000
1.69486E-11
8900000
8.47236E-06
0.45
0.4
Reliability
0.35
0.3
0.25
R(t)
0.2
0.15
0.1
0.05
0
150 160 170 180 190 200 210 220 230 240
External Diameter
Figure 7: External Diameter vs Reliability
Table 8
t=0.4, T=982000, mm.
R(t)
246
0.182589922
242
0.351685826
238
0.465538792
234
0.543827213
230
0.600182156
226
0.642409481
222
0.675091594
218
0.701050479
214
0.722105835
210
0.739479147
Reliability
distribution, School of Mathematical Sciences, University of Science and Technology of China and Springer-Verlag GmbH Germany, part of Springer Nature 2019.
[7] T. S. UmaMaheswari et al. (2019): Reliability Analysis of Resultant Stress for Unsymmetrical Columns for Stress Follow Exponential Distribution, International Journal of Engineering and Advanced Technology (IJEAT) ISSN: 22498958, Volume-8, Issue-6S3, September 2019.
[8] Pasha, M. Y., Devi, M. T., & Maheswari, T. S. U. (2022). Reliability Comparison of the Shafts when Shear Stress follow the Different Distributions. Mathematical Statistician and Engineering Applications, 71(4), 589-599.0.8
0.7
R(t)
0.6
0.5
0.4
0.3
0.2
0.1
210 215 220 225 230 235 240 245 250
Internal Diameter
Figure 8: Internal Diameter vs Reliability
-
CONCLUSION
The torsion reliability of a circular shaft under exponentially distributed shear stress has been calculated. It has been determined if a hollow or solid circular shaft will reliably transmit torque. It has been found that the shaft's reliability reduces with increasing time, twisting moment, and stiffness modulus, as well as with decreasing external diameter and shaft length. Shaft reliability rises with decreasing interior diameter and total torque.
-
REFERENCES