
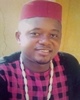
- Open Access
- Authors : Obute K.C, Anih L.U, Ezechukwu A.O, Olufolahan Oduyemi, Aniagboso A.O
- Paper ID : IJERTV12IS080001
- Volume & Issue : Volume 12, Issue 08 (August 2023)
- Published (First Online): 26-08-2023
- ISSN (Online) : 2278-0181
- Publisher Name : IJERT
- License:
This work is licensed under a Creative Commons Attribution 4.0 International License
Improvement of Performance Indices of Three-Phase Transfer Field Reluctance Motor Through Induced Rotor Current
Obute K.C, Anih L.U, Ezechukwu A.O, Olufolahan Oduyemi, Aniagboso A.O 1- Department of Electrical Engineering, Nnamdi Azikiwe University, Awka.
2- Department of Electrical Engineering, University of Nigeria Nsukka.
3-Department of Engineering and Technology, SouthEast Missouri State University, Cape Giradeau, Missouri MO63701, USA. Corresponding Author Obute Kingsley Chibueze
Abstract
This paper aims at discussion by analysis on improvement of performance indices of three-phase transfer field reluctance motor
through induced rotor current. Obviously, the inherent set-back of all transfer-field motors is essentially its low-output characteristics. These include the output torque, low output power factor etc. These characteristics features of the motor are very much inferior to those of the induction motor counterpart with comparable ratings and sizes. This is a result of the low ratio of its direct axis (xd) to quadrature axis (xq) reactances. This is further worsened by its excessive leakage reactance, mainly contributed by the quadrature axis reactance, due to its rotor-pole structure. To improve the output performance of the motor, the excessive leakage reactance must be minimized by optimizing the salient rotor design. This new configuration is conceived to reduce the overall leakage reactance of the existing motor with the corresponding increase in the maximum and starting torque at a better power factor.
Key words: Direct axis reactance, Quadrature axis reactance, Leakage reactance, Maximum torque, Starting torque, Power factor, Rotor-pole structure.
1.0 – INTRODUCTION
In its broad definition, a reluctance machine is an electric machine in which torque is developed by the tendency of a movable part (rotor) to move into a position where the inductance of an energized phase winding is a maximum. Structurally, the transfer field machine is basically a reluctance machine. It differs from the simple reluctance machine in two important aspects viz;
-
it has two set of windings instead of one, as obtainable in simple reluctance machine
-
each winding has a synchronous reactance which is independent of rotor position, while the winding reactance of simple reluctance machine varies cyclically (L.A.Agu 1984). Acceptably, the output characteristics of all transfer-field reluctance motors are low and very inferior to those of induction motors of related capacities. This is the attribute of their excessive leakage reactances from the quadrature axis reactance, owing to the salient nature of their rotor pole structure.
This research is aimed at reducing the overall leakage reactance of the existing motors (without rotor windings) with the corresponding increase in the maximum and starting torques. This is achieved by the introduction of rotor windings at the rotor pole structure.
In this study, the rotor windings are wound at the periphery of the rotor pole structures connecting the two machine sets (A and B). Just as in the auxiliary windings, the rotor windings are transposed between the machine sets, and then connected in parallel with the auxiliary windings. The reason for such parallel connection is based on the idea that when impedances (in the form of coils) are connected in parallel to the utility supply, their resultant impedance will be less than the least impedance and when impedance is reduced in a circuit, higher current flows in the circuit.
The use of short-circuited rotor windings, would lead to considerable improvements in its performance. The rotor windings do not only give rise to an increase in the induced e.m.f but also augment output power by effectively lowering the synchronous reactance of the output windings, thus leading to a higher output and greater synchronous stability. Hence, there is the necessity to raise the output of the cage-less three phase transfer field machine by way of using circuits on the structure (shaft), so as to augment the effect of saliency (E.S Obe and A. Binder 2011). Additionally, the windings in the rotor of a three-phase transfer field reluctance motor could go a long way to improving its performance characteristics and a better ability to preserve the voltage wave shape following a sudden addition or removal of load than does a three-phase transfer field reluctance motor without rotor windings. Also, the three-phase transfer field reluctance motor without rotor windings is only capable of yielding less than half the rated power while the T.F machine with a rotor windings is able to produce more than two-thirds of the rated power. This is due to the inability of the three-phase transfer field reluctance motor without rotor windings to excite at capacitance value high enough to circulate the rated current in the machine windings. Unlike the T.F motors with windings at the rotor, the counterpart without rotor windings produces a lower voltage and lower load current and, hence can only yield lower power.
In its normal running condition, the operation of the transfer field motor is asynchronous, that is, the rotor speed is different from that of the field. It follows therefore that the winding impedances will be influenced by closed electric circuit in the rotor (L.A Agu 1984). A short circuited full rotor cage or poly-phase winding will reduce the effective reactance of the primary winding in the same way that it would in a conventional induction motor operating at a slip. The rotor winding being almost wholly inductive; the rotor current produce a field which is nearly totally demagnetizing with respect to the applied primary field; additional primary current is drawn from the supply to balance the rotor current. In terms of the supply therefore, the primary reactance is effectively reduced. If the rotor is connected to a capacitive load such that the rotor current is leading, the rotor field will act in the direction of the applied field, and the total current drawn from the supply will be reduced. So in supply terms, this will amount to an increase in primary reactance.
The rotor winding can be split into two separate d-axis and q-axis windings. The d-axis winding has its axis along the direct axis of the salient pole rotor, and the q-axis winding has its axis along the quadrature axis of the salient pole rotor. The d-axis and q-axis have been shown in fig1.
The direct (d)-axis and quadrature (q)-axis flux path involve two small air gaps and two large air gaps respectively. The first is path of minimum reluctance, where as the second is the path of maximum reluctance (Smarajit Ghosh (2007).
Fig 1 Direct (d) axis and quadrature (q) axis of two-pole salient pole rotor (Smarajit Ghosh (2007).
A single phase d-axis rotor winding will have no influence on the reactance of the primary winding, the latters axis concides with the q-axis of the rotor, but will have the must effect when the winding axis coincides with the rotor d-axis. Similarly, a q-axis rotor winding will have the most effect on the quadrature axis reactance of the primary winding and non on the direct axis reactance. If the current induced by the primary winding in the d-axis rotor magnetic field will assist the primary field; and so, for given applied voltage the primary current will be less than it would be if the rotor coils were absent. The primary winding d-axis rotor winding, lagging power factor (pf) currents in the d-axis rotor winding will reduce the primary d-axis reactance. The primary q-axis reactance is lowered by induced reactive currents in th q-axis rotor windings. It can be deduced therefore that a combination of d-axis rotor winding with leading power factor (pf) currents and q-axis rotor windings, with lagging power factor (pf) current will raise the effective Xd to Xq ratio of the transfer field (TF) machine.
2.0 METHODOLOGY
The new configuration of 3-phase transfer field reluctance motor (motor with rotor windings) is intended to minimize the excessive leakage reactance associated with the existing three phase transfer field motor (motor without rotor winding). To achieve the afore-mention goal, the following methods were adopted, viz;
-
Analytical (calculation) Method: This method follows the following procedure;
-
Development of mathematical model of the motor, necessary to explain its behaviour under steady-state and dynamic state condition
-
Derivation of mathematical equations from the model, necessary for the formation of the machines equivalents circuit diagrams
-
Derivation of the machines output characteristics equations from the equivalent circuit diagrams
-
Establishment of the machines circuit parameters.
-
Simulation of the derived equations as in (iii) and (iv)
-
Generation of the machine plots (graphs) from (v) for analysis of the machines output characteristics
-
-
Modification Method: Here, the existing three-phase transfer field motor without rotor windings is modified by optimizing the rotor design. This is achieved by the introduction of rotor windings at the rotor sections of the machine sets (M/C A and M/C B). The idea is that when resistance (in the form of coils) are added to the rotor circuit the rotor power factor is improve, which inturn results in improved starting torque. This of course increases the rotor impedance and therefore decreases the value of rotor current, but the effect of improved power factor predominates and the starting torque is increased (V.K Mehta et al 2000). To bring down the effect of such reduction in rotor-induced current, the main windings of the machine sections are connected in series and then connected to the utility supply. The auxiliary and cage (rotor) windings of both machine sections are connected in parallel but transposed between the two sections of the machine halves and short circuited. The fact that when impedances are connected in parallel, the resultant impedance will be lower than the least impedances and when impedances are reduced, higher current will flow into the circuit and output power increases, thereby resulting in higher electromagnetic torque, forms the basis of research methodology of this study.
The analytical method adopted to achieve the results in this work follows the chronological order as below;
-
Analysis of three-phase transfer field reluctance motor (T.F.M) without rotor windings.
-
Analysis of three-phase transfer field reluctance motor with the introduction of rotor windings
-
Analysis of compared results.
-
-
Analysis of the three-phase transfer field reluctance motor (T.F.M) without rotor windings
The three-phase transfer field reluctance machine is a new breed of electrical machine which operates under synchronous and asynchronous mode. It has the dual characteristics of both machines depending on the mode of operation.
-
Motor description/Physical Configuration
The transfer field reluctance motor (TFM) as shown in Plate 1, comprises a two stack machine in which the rotor is made up of two identical
equal halves whose pole axes are 2 radians out of phase in space. They are housed in their respective induction motor type stators. There are no windings in the rotor. The stator has two physically isolated but magnetically coupled identical windings known as the main and auxiliary
windings. The axes of the main windings are the same in both halves of the machine, whereas the axes of the auxiliary windings are transposed in passing from one half of the machine to the other. Both sets of windings are distributed in the stator slots and occupy the same slots for perfect coupling and have the same number of poles. The two sets of windings of the transfer field machine are essentially similar and may be connected in parallel which of course double its output.
The stator and rotor of the machine are wound for the same pole number and both are star connected as in fig 2.
1
Fig 2 – Connection diagram for a three phase transfer field reluctance motor without rotor windings
-
Machine Model
-
The per-phase coupled coil representation of the Transfer Field reluctance motor is shown in fig 3.2 below
Im XmA xmB
Ia xaA
V
xmaA
xaB xmaB Main winding
Auxiliary winding
(Transposed and Short-circuited)
X Y
Rotor shafts
Machine 1
Machine 2
Fig 3. Per phase coupled coil representation of a T.F. Motor without rotor windings
Each machine half is similar in features to the conventional synchronous machine. The major unorthodox characteristics of the machine are;
-
the stator and rotor are arranged in two identical halves; and hence the machine may be treated as two separate reluctance machines whose stator windings are connected in series.
-
there are no windings in the rotor
-
the pole axes of the two pole half are mutually in space quadrature
-
there is second set of poly-phase stator windings (auxiliary windings) whose conductor side are shifted electrical by 1800 (anti-series), by passing through one section of the machine to another. The main and the auxiliary windings are identical in all respects and occupy the same electrical position in the stator slot, thus ensuring a perfect coupling between the windings.
-
dynamic model of 3-phase transfer field machine
For the stator windings of the three-phase TF machine of fig2, the mathematical model of the voltage equation is given by; VA = rA iA + PA (1)
VB = rB iB + PB (2)
VC = rC iC + PC (3)
Where VA = VR (Red)
VB = VY (yellow)
VC = VB (Blue) are the three phase balance voltage which rotate at the supply frequency () at the main winding.
For the rotor, the flux linkages rotate at the speed of the rotor (r).
Therefore, for the auxiliary winding of the machine, we have;
Va = ra ia + a (4)
Vb = rb ib + b (5)
Vc = rc ic + c (6)
Equations (1-6) can be written in a compact form as;
VABC = rABC iABC + ABC (7)
Vabc = rabc iabc + abc (8)
where;
= d/dt (derivative term, as usual)
(VABC)T = [VA, VB, VC] (9)
(Vabc)T = [Va, Vb, Vc] (10)
rABC = diag ([rA rB rC]) (11)
rabc = diag ([ra rb rc]) (12)
In the above two equations (9) and (10), ABC subscript denotes variables and parameters associated with the main winding and the subscript abc denotes variables and parameters associated with the auxiliary winding. Both rABC and rabc are diagonal matrices each with equal non zero element. For a magnetically linear system, the flux linkages may be expressed as (Anih L.U. 2009);
= [ ] [
wb turn (13)
[ ]]
Where,
ABC = (A, B, C,)t
abc = (a, b, c,)t
iABC = (iA, iB, iC,)t (14)
iabc = (ia, ib, ic,)t
The super-script t of equation (14) denotes the transpose of the array.
The inductance matrices term LGG , LGH, and LHH are obtained from inductance sub-matrices L11, L12, L21 and L22 for machines A and B, defined as;
L = 11 12] [
21 22
L11 = [ ]
L12 = + [ ] (15)
L21 = +[ ]
L22 = [ ]
Where;
L = The augmented matrix, for the inductance matrix for machine A and B
L11 and L22 are self inductances of main and auxiliary windings respectively.
L12 and L21 are the mutual inductances between the main and auxiliary windings. LGG is obtained by adding L11 for machine A and L11 for machine B.
This will yield;
1 1
(2LLs+Lmd+ Lmq) – 2 (Lmd+Lmq) – 2 (Lmd+Lmq)
LGG
md
– 1 (L
2
1
+Lmq
) (2LLs
1
+Lmd
+ Lmq
md
)a – 1 (L
2
+Lmq)
(16)
[- 2 (Lmd+Lmq) – 2 (Lmd+Lmq) (2LLs+Lmd+ Lmq)]LGH is obtained by adding L12 for machine A to L12 for machine B to give
cos 2 r cos(2 r-) cos(2 r+)
LGH = (Lmq Lmd) [
Where = 2
3
cos(2 r-) cos(2 r+) cos 2 r
cos(2 r+) cos 2 r cos(2 r-)
] (17)
By applying the same method, LHG and LHH are obtained. So far the main and auxiliary windings in both machine halves are identical, LGG is
observed to be equal to LHH. So also LGH and LHG. Owing to this observation of equality, auxiliary winding parameters do not change values when they are referred to the main winding.
Equations (16) and (17) resemble the inductance expressions for a wound rotor induction machine, even though the individual machine making up the composite machine possesses salient pole rotors with no conductors.
-
Machine Model in arbitrary q-d-o reference frame
In order to remove the rotor position dependence on the inductance seen in equation (17), the voltage equations (7) and (8) need to be transferred to q-d-o reference frame.
The technique is to transform all the state variables to an arbitrary reference frame. Equation (13) is then rewritten in q-d-o frame as;
( )
( )1
( )1
( )
= [
] (18)
[( )]( )1
( )1 ] [
(
)
Cos ( ) ( + )
Here, KG = 2 [Sin ( ) ( + )] (19)
3 1 1 1
2 2 2
Cos ( ) ( + )
KH = 2 [Sin ( ) ( + )]
3 1 1 1
2 2 2
Where, r = rotor position
= speed of rotation of the arbitrary reference frame.
As = 2r = , as in equation (17), the time varying inductance frame, the voltage equation will be totally eliminated. Hence, the voltage equations (7) and (8) will after the transformation yield;
VQ = D + Q + rIQ (20)
VD = Q + D + rID (21)
VO = O + rIO (22)
Doing like-wise for the rotor quantities (auxiliary windings) yield;
Vq = (-2r) d + q + rIq (23)
Vd = (-2r) q + d + rId (24)
Vo = (-2r) o + rIo (25)
Also, the flux linkages of equation (17) are expressed as; Q = (2L1 + Lmq +Lmd)IQ (Lmd – Lmq)Iq
= 2 L1 IQ + Lmq IQ + Lmd IQ – Lmd Iq+ Lmq Iq
= 2 L1 IQ + Lmq IQ + Lmd IQ+ Lmd IQ- Lmd IQ- Lmd Iq+ Lmq Iq
= 2 L1 IQ + 2Lmd IQ + Lmq IQ- Lmd IQ- Lmd Iq+ Lmq Iq
= 2(L1 + Lmd) IQ + [IQ (Lmq+Lmd) + Iq (Lmq – Lmd)]
= 2 (L1 + Lmd) IQ+ (IQ+Lq) (Lmq – Lmd)
Q = 2(L1 + Lmd) IQ+ (IQ+Iq) (Lmq – Lmd) (26)
Similarly
D = (2L1+ Lmq + Lmd) ID + (Lmd – Lmq) Id
D = 2(L1+ Lmq) ID + (ID – Id) (Lmd – Lmq) (27)
O = 2L1 IO (28)
Also
q = (2L1+ Lmq+ Lmd) Iq – (Lmd – Lmq) IQ
= 2(L1+ Lmd) Iq + (Lmq – Lmd) (IQ+Iq) (29)
d = (2L1+ Lmq+ Lmd) Id + (Lmd – Lmq) ID
= 2(L1+ Lmq) Id + (Lmd – Lmq) (ID+Id) (30)
O = 2L1IO (31)
As before, equations (26 28) represent the flux linkages of the main winding circuit while equations (29 31) represent the flux linkages of the auxiliary winding, and r in equations (20 25) is the sum of the resistances of the main or auxiliary windings in both machine halves.
Hence, equation (26) can be put into equation (20), and equations (30) into equation (23) to yield; VQ = D + [2(L1+ Lmd) IQ + (Lmq – Lmd) (IQ+Iq)] + rIQ
= D + j [2(L1+ Lmd)] IQ + j (Lmq – Lmd) (IQ+Iq) + rIQ (32)
Vq = (-2r) d + [2(L1 + Lmd) Iq] + (Lmq – Lmd) (IQ+Iq)] + rIq
Vq = (-2r) d + j [2(L1+ Lmq)] Iq +j (Lmq – Lmd) (IQ+Iq) + rIq (33) Equation (32) and (33) result the T equivalent circuit shown below in figure 4.
IQ r
D J2 (L1+Lmd) j2 (L1+Lmd)
(-2r)d Iq
+ + –
VQ
(IQ + Iq)
J (lmq Lmd)
+ – r +
Vq
– –
Fig 4-Arbitrary reference frame equivalent circuit for a 3-phase symmetrical transfer field reluctance motor in the q-variable.
Applying the same method to equation (27) and (21) and then equations (29) and (24) we have;
VD = – Q + [2(L1+ Lmq) + (Lmd – Lmq) (ID+Id)] + rID
= – Q + j2 (L1+ Lmq) ID + j (Lmd- Lmq) (ID+Id) + rID (34) Vd = – ( – 2r) q + [2(L1+ Lmq) Iq + (Lmd – Lmq) (ID+Id)] + rId
= – ( – 2r) q + j2 (L1+ Lmq) Iq + j (Lmd – Lmq) (ID+Id)] + rId (35) Equations (34) and (35) result the Tequivalent circuit shown below in figure 5.
D J2 (L1+Lmq)
J2 (L1+Lmq) (-2r) q
+ ID r
VD
-+ + – r
(ID+ Id)
J (Lmd Lmq)
Id +
Vd
– –
Fig 5 -Arbitrary reference frame equivalent circuit for a 3-phase symmetrical transfer field motor in the d-variables
More still, from equation (22) and (26) Vo = o + rIo
= (2L1 Io) + rIo (36)
Vor = o+ rIo
= (2L1 Io) + rIo (37)
Equations (36) and (37) result the T equivalent circuit shown in fig 6.
+ IO r
j2L1
j2L1 r IO
Vo Vor
–
Fig 6-Arbitrary reference frame equivalent circuit for a 3 phase symmetrical transfer field reluctance motor in the 0 variable
2.1.2.1.1 q-d-o Torque Equation
The expression for electromagnetic torque is obtained from energy considerations and derived to be (Anih L.U 2009);
Te = [
( )] [ [
] [
( )] (38)
2
]
Equation (38) can be shown to yield;
Te = 3 Pn (Lmd Lmq) (IQ Id Iq ID) (39)
4
Equation (39) shows that currents in both the main and auxiliary windings contribute positively to torque production, therefore, there is no
copper penalty limitation of space for auxiliary winding conductor is utilized. The electromechanical (rotor) dynamic equation for the machine is expressed as;
J = Te – TL (40)
Where;
Pn = Number of poles
TL = motor shaft load torque in N-m Te = Electromagnetic torque in N-m
J = Moment of inertia of motor in kg m2 m = Mechanical rotor speed in rads-1
2.1.2.2 Steady state model of 3-phase transfer field reluctance motor in arbitrary q-d-o reference frame
The steady state equivalent circuit of a three-phase transfer field machine may be derived from the d-q-o equivalent circuit. This can be achieved with the understanding that all the derivative terms of equation (20) through equation (26) are set to zero, and the following relations exist between the q-axis and d-axis variables.
FD = jFQ (Main winding circuit)
Fd = – jFQ (Auxiliary winding circuit) VQ = VA, IQ = IA, Vq = Va, Iq = Ia
As the machine is half speed type with synchronous speed 1 = ; the per slip is given by;
2
=
= .5
.5
= 2
(41)
= -2r (42)
But for the normal induction motor counterpart;
s =
r = -s (43)
Putting equation (43) into equation (42), yields;
= 2s 1 (44)
It can be recalled from equations (20 26) that;
VQ = D + Q + rIQ
= D + (0)Q + rIQ
= D + rIQ
VQ = D+ rIQ
= j [2 (L1+ Lmq) ID + (Lmd – Lmq) (ID+Id)] + rIQ
= j[2 (x1+ xmq) ID + (xmq – xmd) (ID+Id)] + rIQ
VA = [j2(x1+ xmq)+r] IA + j (xmd – xmq) IA+Ia) (45)
Similarly
Vq = (-2r) d + d + rIq
= (-2r) d + (0)q + rIq
= (-2r) d + rIq
= d+ rIq
= [2(L1+ Lmq)) Id + (Lmd – Lmq) (ID+Id)] + rIq
= j [2(x1+ xmq)) Id + (xmd – xmq) (ID+Id) + rIq Dividing both sides by , we have;
= j [2(x1+ xmq)) Id + (xmd – xmq) (ID+Id) +
= [j2(x1+ xmq)Ia] + j(xmd – xmq) (IA+Ia) +
= [2j(x1+ xmq) + ]Ia + j(xmd – xmq) (IA+Ia)]
Referring to equation (44);
21
= [j2(x1+ xmq) + ] Ia + j [(xmd – xmq) (IA+Ia)] (46)
21
Equations (45) and (46) result a per phase T equivalent circuit as shown in figure 7
+ IA
r J2 (X1+Xmq) J2 (X1+Xmq)
2 1
Ia +
(IA+ Ia)
VA J2 (Xmd-Xmq)
2 1
– –
Fig 7-Per phase steady state T equivalent circuit of a 3-phase transfer field reluctance motor, using the q-variable.
The rotor (auxiliary) is usually short circuited and hence from figure 7, = 0
21
Also,
21
= r + 2 (1 )
21
(47)
Hence, figure 7 can be redrawn for better as in figure 8 to suit equation (47) as below.
+ IA
r J2 (X1+Xmq) a
J2 (X1+Xmq)
r Ia +
Im = (IA + Ia)
VA J (Xmd – Xmq)
2(1 )
2 1
– –
Figur8-Per phase steady state Tb – equivalent circuit of a 3-phase transfer field reluctance motor.
N.B – Figure 8 can also be obtained using the d-variable of equation (21) and (24).
-
Power across air gap, Torque and Power output in 3-phase Transfer field reluctance motor
With reference to the equivalent circuit of figure (8), the power crossing the terminals (ab) in the circuit is the electrical power input per phase minus the stator losses (stator copper and iron losses) and hence, is the power that is transferred from the stator (main windings) to the rotor (auxiliary windings) through the air-gap magnetic field. This is known as the power across the air gap. Its 3-phase value is symbolized as PG. From figure 8,
PG = 3(Ia)2
21
The Auxiliary winding copper loss Pc(aux) = 3()2
From equations (48) and (49);
PG = ( )
21
(48)
(49)
Pc (aux) = (2S-1)PG (50)
If equation (49) is subtracted from equation (48), we have; PG Pc (aux) = Pm (Mechanical output (gross) power)
Pm = [ 3(Ia)2
] – [ 3(Ia)2r]
21
= 6(Ia)2 (1 )
21
Pm = 2PG (1-s) (51)
From the equations established so far, it is evident that high slip (s) operation of the transfer field machine would be highly inefficient, hence, transfer field motor just as the induction motor counterpart are therefore designed to operate at low slip at full load.
-
Analysis of Torque/Slip characteristic of a 3-phase transfer field reluctance motor without rotor windings
The torque- slip characteristic of a 3-phase transfer field reluctance motor without rotor windings can be studied for clarity if the per phase steady-state equivalent circuit of figure (8) is modified as shown fig 9 below; taking x1 + xmq = xq
+ IA r
VA
J2xq
Ia
J2xq r
a
Im
j(Xmd+Xmq)
2(1 )
2 1
b
–
Fig 9
+ IA r
J2xq
a J2xq Ia
Im
VA j (Xmd+Xmq)
2 1
– b
Fig 10
Fig 9/10 Modified per phase steady-state T- equivalent circuit of a 3-phase transfer field reluctance motor without rotor windings.
From figure 9, the VTH (voltage across a-b) is given by;
()
VTH =[
] VA volts
()+ (+2)
()
=[
+ (+2)
] VA volts (52)
If r<< j (xmd-xmq+ 2xq), then equation (52) becomes;
()
VTH =[
(+2)
TH
V =[ ()
] VA volts (53)
] V volts
(+2)
()(+ 2)
Also ZTH =
=
()+ (+2)
()(+2)
+( +2)
(54)
If r<< j (rmd-xmq) + 2xq), then equation (54) become;
()(+2)
ZTH =
(+2)
()(+2)
=
(+2)
= ()+ 2 ()
(+2 )
= +
() (+2)
(55)
(2() (+2)
But ZTH = RTH (Real Component) + XTH (Imaginary component)
TH
Hence, R = ()
+2
X =
[(2()]TH
+2
(56)
(57)
The circuits of figures (9/10), then reduce to that of figure 11, in which it is convenient to take VTH as the reference voltage
RTH + j XTH
J2Xq
Ia
a
VTH
2 1
b
From figure 11,
Ia =
Fig 11-Thevenin equivalent of 3 phase transfer field reluctance motor without rotor windings circuit model
Amperes (58)
( +
21
)+ (+2)
2
(Ia)2 = ( )
Amperes (59)
(+
2
) + (+2)2
21
The expression for the steady state electromagnetic torque is given by;
2
Te = = ( 6( ) ) ( 1 )
21
2 2
= ( 6( ) ) ( 1 ) = 6( )
N-m (60)
(1)
21
(21)
Hence, putting equation (59) into equation (60) yields;
2
Te =( 6 ) ( )
( ) N-m (61)
(+
2
) + (+2)2
21
21
-
alysis of Efficiency/Slip characteristics of 3-phase transfer field reluctance motor without rotor windings
The Efficiency/Slip relationship for a 3-phase transfer field reluctance motor without rotor windings can be investigated using the per phase steady-state equivalent circuit of a fig 10
From fig 10,
The input impedance (Z) looking through the input terminals is;
( )(2+
Z = r + j2xq + [
)
21 ] (62)
21
+ (2+( ))
Also, the current in the main winding (IA) is given by;
IA =
The current in the auxiliary winding is given by;
( )
(63)
Ia = [
21
+ (2+( ))
]IA (64)
The copper losses in the main and auxiliary windings = 3r(IA + Ia)2 (65) Input power = Output power + the copper losses, excluding windage and friction losses.
From equation 51,
The machine input power = 6r ( 1 ) (Ia)2 + 3r(IA + Ia)2
21
= 3r [2( 1 ) ( )2 + (
+ )2 ] (66)
21
1 2
Hence, the machine Efficiency = = 2(21) ()
(67)
2( 1 ) ( )2+( + )2
21
-
Analysis of Power factor/Slip characteristics of 3-phase transfer field reluctance motor without rotor windings
From the Thevenin equivalent of a 3-phase transfer field machine circuit model of fig 11, the machines power factor (cos) is given by;
Power factor (cos ) = ( )
()2+ ()2
(68)
+
= 21
(69)
2 2
( + 21) + (+ 2)
-
Analysis of Auxiliary current (Ia)/slip(s) Characteristics of 3-phase transfer field motor without rotor winding.
-
The Auxiliary current (Ia) against Slip (s)can be analyzed, using equation 58 above.
2.2 Analysis of three-phase transfer field reluctance motor with rotor windings.
The structural arrangement of the motor is shown in fig 12. Unlike the three phase transfer field reluctance motor without rotor windings counterpart, the three-phase transfer field reluctance motor with rotor windings comprised two identical poy-phase reluctance machine with moving conductors (rotor windings), whose salient poles rotor are mechanically coupled together, such that their d-axis are in space quadrature. As depicted in fig 12, the stator windings, are integrally wound. Each machine element has three sets of windings. Two sets out of the three sets of windings of the machine are identical and are housed in the stator. These are called the main (primary) and the auxiliary windings. The main windings of the machine carry the excitation current, while the auxiliary windings, carry the circulating current. The (2s-1) 0 low frequency current is confined in the auxiliary winding without interfering with the supply. The main windings of the machine sets are connected in series while the auxiliary windings, though also in the stator are transposed between the two machine stacks. They are wound for the same pole number and both are star connected. The third set of windings known as the rotor (cage) windings are wound at the periphery of the rotor shaft connecting the two machine sets. Just as in the auxiliary windings, the rotor (cage) windings are also transposed between the two machine stacks and then connected in parallel with the auxiliary windings (see fig 13).
M/C A
MACHINE SHAFT
M/C B
Rotor winding
R
Main Winding
Y
B
Auxiliary winding
Fig 12: Connection diagram for three phase transfer field reluctance motor with rotor winding
2.2.1 Steady state analysis of the configured 3-phase transfer-field reluctance motor with rotor windings. The steady state analysis of the configured motor can be done, using the schematic diagram of figure 13 below;
i I
WWW WWW
i
R
R R
Ld
V Ld Ld
V
M/C
V
WWW WWW
R
R R
Lq
q
Lq L
M/C B
Fig 13 -Per phase schematic diagram of 3-phase transfer field reluctance motor with rotor windings.
i2
i1 i3
R1 R2 R3
~ (i2 + i3) xd
xd
V1
~
(i1 + i3) xd xd
~ (i1 + i2) xd xd
M/cA
V3 V2
R1 R2 R3
Fig 14 Modified per phas(ie2s+chie3m) xaqtic diagram of the three-(pip a+sei3t)raxnqsfer field reluctan(ci1e +moi2t)orxqwith rotor windingsMund/ercroBtor stand-
still condition, tha~t is slip(s)=1, Nr=0
xq
~ ~
xq xq
Main Winding
Auxiliary winding
Rotor winding
i2
i1 i3
R1 R2 R3
~ (i2 + i3) xd
xd
V1
(i1 + i3) (2s-1) xd
~
xd
~
(i1 + i2) (2s-1)xd xd
M/c A
V3 V2
R
R2 R3
1
~
(i2 + i3) xq
~
(i1 + i3) (2s-1) xq
~
(i1 + i2) (2s-1)xq
M/c B
xq xq xq
Fig 15- Modified per phase schematic diagram of the three-phase transfer field reluctance motor with rotor windings under run condition, that is slip = (2s-1).
Where, V1 = Main winding voltage
V2 = Auxiliary winding voltage V3 = Cage (rotor) winding voltage
Ld1 = L d2 = L d3 = Ld = Direct axis inductances
Lq1 = L q2 = L q3 = Lq = Quadrature axis inductances
R1 = R2 = R3 = R = Resistance of the machine windings i1 = Current at the main windings
i2 = Current at the Auxiliary windings i3 = Current at the rotor windings
Also , L12, L13. L21 L23 L31 and L32 are the mutual couplings between coil 1, 2, and 3 at the direct axis.
Similarly, 12, 13, 21, 23, 31 and 32 are the mutual couplings between coil 1, 2, and 3 at the quadrature axis. Hence L12 = L13 = L21 = L23 = L31 = L32 = k = Ld
Similarly, 12= 13= 21= 23 = 31 = 32 = k = Lq
Owing to the fact that the pole strductuaxreis of the machine is salient in nature as in fig,16 Ld Lq. that is;
ld
lq
q – axis
Fig 16 The Salient pole structure of the three-phase transfer field reluctance motor with d-axis and q-axis positions
From figure 3.18,
2
But Ld = N2Pd =
2
Lq = N2Pq =
(70)
Sd =
Sq=
From fig 16, Iq > ld, at constant A and N,
Sq > Sd
Ld > Lq Where
ld = Direct axis air-gap length
lq = Quadrature axis air gap length
Pd, Sd = Direct axis permeance and reluctance respectively
Pq, Sq = Quadrature axis permeance and reluctance respectively Ld = Direct axis inductance
Lq = Quadrature axis inductance
Taking the voltage equation of the machine sections of fig 3.17b, we obtain;
V1 = (R1 + R1) i1 + Ld 1 + Lq 1 + L12 2 – 2 + L13 3 –
3
12
13
d
V1 = (R1 + R1) i1 + Ld 1 + Lq 1 + L 2
– Lq
2
+ Ld
3
-Lq
3
V1 = 2R1 i1 + jLd i1 + jLq i1 + jLd i2 jLq i2 + jLd i3 jLq i3
V1 = 2R1 i1 + jxd i1 + jxq i1 + jxd i2 – jxq i2 + jxd i3 – jxq i3
V1 = 2R1 i1 + j(xd + xq (xd – xq) i1 + j(xd – xq)i1+ (xd – xq)i2+ j(xd – xq)i3
V1 = 2R1 i1 + j (2xq)i1 +(xd – xq) (i1 + i2 + i3) (71)
d
V2 = (R2 + R2)i2 + L 2
+ Lq 2
+ L21 1
1
– 2
+ L23 3
–
3 23
d
V2 = (R2 + R2) i2 + Ld 2 + Lq 2 + L 1
– Lq
1
+ Ld
3
-Lq
5
V2 = 2R2 i2 + (2s -1) [ jLd i2 +ji2 + jLd i1 jLq i1 + jLd i3 jLq i3]
V2 = 2R2 i2 + (2s -1) [ jxd i2 + jxq i2 + jxd i1 – jxq i1 + jxd i3 – jxq i3]
V2 = 2R2 i2 + (2s -1) [ j(xd + xq (xd – xq)) i2 + j(xd – xq)i2+ j(xd – xq)i1+ j(xd – xq)i3] V2 = 2R2 i2 + (2s -1) [ j (2xq) i2 +j (xd – xq) (i2 + i1 + i3)
2
21
= 22 2 + j (2xq)i2 + j(xd- xq) (i1 + i2 + i3) (72)
21
Also, V3 = (R3 + R3)i3 + Ld 3 + Lq 3 + L31 1 – 1 + L32 2 –
2
L
31
32
d
V3 = (R3 + R3)i3 + L 3
+ Lq 3
+ Ld 1
1
q
+ Ld 2
q
– L 2
V3 = 2R3 i3 + (2s -1) [ jLd i3 + jLq i3 jLq i1 + jLd i1 jLq i2 + jLd i2] V3 = 2R3 i3 + (2s -1) [ jxd i3 + jxq i3 + jxd i1 – jxq i1 + jxd i2 – jxq i2]
= 2R3 i3 + (2s -1) [j(xd + xq ( xd – xq))i3+j( xd – xq) i3 + j( xd – xq)i1 + j( xd – xq)i2
= 2R3 i3 + (2s -1) [j(2xq)i3 + j( xd – xq) (i3 + i1 + i2 )
3
21
= 23 3 + j(2xq) i3+ j(xd- xq) (i1 + i2 + i3) (73)
21
Equations 71 73 result an equivalent circuit of fig 17 below;
j 2xq
23
2 1
2R1
j 2xq
2
i1 i3 i
j 2xq
22
2 1
I1+ i2 + I3
j(xd -xq)
2 2 1
3 2 1
Fig. 17 Per phase steady state equivalent circuit of a 3-phase transfer field reluctance motor with rotor windings.
Since the rotor and auxiliary windings are short circuited, 3
21
=0, 2
21
= 0. Hence, fig. 17 yields;
j 2xq
23
2 1
2R1
j 2xq
2
i1 i3 i
j 2xq
22
2 1
i3+ i2 + I3
j(xd -xq)
V1
Fig 18 Per phase steady state equivalent circuit of a 3-phase transfer field motor with rotor and auxiliary windings short circuited.
From fig 18, So far R1 = R2 = R3 = R,
( 2 )+ (2
Z2 z3 = [ 21
) ( 2 )+ (2 )
21 ]
( 2 )+ 2
21
+ ( 2 )+ (2 )
21
[( 2 )+ (2= 21
2
)]
2[( 2 )+ (2
21
2 +2
)]
= 21
2
= 2 2(21)
+
2
2
Z2 z3 =
21
+ (74)
Hence, fig 18 can be redrawn as below;
j2xq
j x q
i
2R i23
1
WWW
i1 + i23
j (xd – xq)
V1
R 2s -1
Fig. 19 The modified steady state equivalent circuit of a 3-phase transfer field reluctance motor with rotor and auxiliary windings short circuited.
From Fig. 19,
Also, 2 = R + 2 (1 )
(75)
21
21
Hence, Fig 19 becomes;
2R
j 2xq
23
i1 a i j xq R i1 + i23
V1 VTH
j (xd – xq)
2R (1-s)
2s -1
b
Fig 20 Modified steady state equivalent circuit of a 3-phase transfer field reluctance motor with rotor and auxiliary windings short circuited and rotor external resistance (R). From fig 20,
VTH = [
()
()+ (2+2 )
] 1
= [ ()
] 1 (76)
2+ (+2)
If 2R <<j (xd xq + 2 xq), we have;
()
VTH = [
(+2)
] 1
VTH = [
+
] 1 volts (77)
Also
ZTH =
()(2+2 )
()(2+2 )
(78)
= ()(2+2 )
2+ (+2)
If 2R <<< j (xd xq + 2 xq), then;
()(2+2 )
ZTH =
(+2)
(79)
= ()(2+2 )
(+)
But (xd xq) (2R + j2 xq) = 2R (xd xq) + j(2xq (xd xq))
= 2R (xd xq) + j(2xq xd 2xq xq)) (80)
ZTH =
2 () (+)
2
(2 2() )
+
(+)
But ZTH = RTH + XTH
Hence RTH =
2 ( ) (+ )
-
Real value of ZTH (81)
XTH =
(2xq xd2(xq)2) =
(+ )
2 ( ) (+ )
-
Imaginary value of ZTH (82)
Hence fig 3.19d reduces to;
i1
ZTH
a j xq R
+
VTH –
2R (1-s)
2s -1
b
Fig 21 Thevenin equivalent circuit of three phase transfer field reluctance motor with rotor winding
From fig 21
i1 = =
2(1)
(+ +
)+ ( + )
21
=
( + )+ ( + )
21
(83)
1
2 =
()2
2
[(+ 21)+ (+)]2
= ( )
(84)
2 2
(+ 21) + (+)
-
Power Across Air gap, Torque and Power Output in three-phase transfer field reluctance motor with rotor winding
With regards to the equivalent circuit of fig 21, the power crossing the terminal ab in the circuit is the power that is transferred from the stator windings to the auxiliary and rotor windings, through the machine air-gap magnetic field. This is called the power across the air gap or simply air-gap power, whose three phase value is shown below;
PG = 3 (i23)2
21
Watts (85)
Auxiliary/rotor windings copper loss Pc (aux/rotor) = 3(i23)2R (86) Putting equation 86 into equation 85, we have;
(/)
PG =
21
Pc (aux/rotor) = (2s-1) PG Watts (87)
But Mechanical Output (gross) Power (Pm) of the machine is given by; Pm = PG Pc (aux/rotor)
Pm = [3(23)2
] – [3(23)2 ]
21
= 6 (i23)2 R (1 ) Watts
21
Pm = 2PG(1-s) Watts (88)
From equation 87 and 88, it can be inferred that high slip operation of the machine will favour auxiliary/rotor winding copper losses Pc(aux/rotor) at the detriment of the mechanical output (gross) Power (Pm), and would make the machine highly inefficient. Hence, the machine is particularly designed to operate at low slip, even at full load.
-
Analysis of Torque/slip Characteristic of 3-phase transfer field reluctance motor with rotor windings
From fig 21, The expression for the steady-state electromagnetic torque of the machine is given as below;
Te = =
(89)
(1)
= [6 (i23)2 R (1 ) x 1 ]
2
= 6( 23 )
(21)
2
21
(1)
= 6( 23 ) N-m (90)
(21)
Putting equation 84 into equation 89, we have;
2
) [
Te = 6 (
()
] N-m (91)
21
(+
21
2
) + (+)2
Equation 91 is the expression for torque developed as a function of voltage (VTH) and slip (s).
-
Analysis of Efficiency/Slip characteristics of the 3-phase transfer field reluctance motor with rotor windings.
The efficiency/slip relationship for the 3-phase transfer field reluctance motor with rotor windings can be studied for better, using the per phase steady-state equivalent circuit of the machine as in fig 19.
The input impedance looking through the input terminals is;
() (+ )
Z = 2R + j2xq + [ 21 ]
+ ( + ( ))
21
() (+ )
= 2R + j2xq + [ 21 ] (92)
+
21
The current I1 in the main winding;
iI = 1
Similarly, the current in the auxiliary and rotor windings (i23) is given by;
()
(93)
i23 = [
21
+(+ ()
] 1 (94)
The copper losses in the main, auxiliary and rotor winding = 3[2(1)2 + (23)2 ]
=3[2(1)2 + (23)2 ] (95)
But, Input Power = Output Power + Copper losses in the main, auxiliary and rotor winding, excluding windage and friction losses;
Input Power = 6R ( 1 ) (
23
21
)2 + 3R (2(i1)2 + (i23)2)
= 3R [2 ( 1 ) (
23
21
)2 + 2(1)2+(23
)2] (96)
2( 1 ) ( )2
23
The machine efficiency () = 21
(97)
2( 1 ) (
23
21
)2+ 2(1)2+(23)2
-
Analysis of Power factors/Slip characteristic of the 3-phase transfer field reluctance motor with rotor windings
From the Thevenin equivalent of the configured machine of fig 20 the machines power factor (cos) is given by;
Power factor (cos) = ( )
()2+ ()2
+
= 21
)2+ (
2
+ )
(98)
(+21
-
Analysis ofRotor current (i23) Slip(s) characteristic of 3-phase transfer field reluctance motor with rotor windings
Using equation 83, the analysis of the effect rotor current on slip is done
-
The machine parameters
Table 1- The Machine Parameters used for the plots
S/No
Parameter
Value
1
Lmd
133.3Mh
2
Lmq
25.6Mh
3
LLs = Lia = Ler
0.6Mh
4
rm = ra = rr = 2R
3.0
5
J
1.98×10-3kgm3
6
V
220V
7
F
50HZ
8
P
2
-
The machine output characteristic plots.
2.2.1.7.1- Toque/Slip characteristics of 3-phase transfer field reluctance motor with/without windings.
In the composite machine, the interaction between the main, auxiliary and the rotor windings currents produce the flux necessary for the torque production. With the machine parameters of table 1, we use equations 53-91 to produce plots to the torque developed at various ranges of slips for the two motors respectively.
2
Electromagnetic Torque (N-m)
1.5
1
0.5
0
-0.5
-1
Plot of Electromagnetic Torque against Slip A Plot of
0 0. |
2 0. |
4 0. |
6 0. |
8 |
1 1. |
Torque/Slip Characteristics of 3- Phase Transfer Field Motor Without Rotor Winding
A Plot of
Torque/Slip
2 Characteristics of 3- Phase Transfer
Field Motor With Rotor Winding
-1.5
-2
Slip (s)
Fig 22 A plot of torque developed against ranges of slip(s) for 3-phase transfer field reluctance motor with and without rotor windings
2.2.1.7.2 Power factor/slip characteristics of the 3-phase transfer field reluctance motor with and without rotor windings
The plots of the power factor (cos )/slip relationships for 3-phase transfer field reluctance motor with and without rotor windings are obtained using equations 69 and 98 respectively. Their plots are depicted in figure 23
Plot of Power Factor against Slip
1
0.9
0.8
Power Factor
0.7
0.6
0.5
0.4
0.3
0.2
0.1
0
0 0.2 0.4 0.6 0.8 1 1.2
Slip (s)
A Plot of Power Factor/Slip of 3-Phase Transfer Field Motor Without Rotor Winding
A Plot of Power Factor/Slip of 3-Phase Transfer Field Motor With Rotor Winding
Fig. 23 Power factor/slip characteristics of 3-phase transfer field reluctance motor with and without rotor windings
2.2.1.7.3. Induced current/slip characteristics for 3-phase transfer field reluctance motor with and without rotor windings
The plots of the induced current (Ia and I23)/slip relationship for the existing and the improved motors are obtained using equations 58 and 83 respectively. Their respective plots are shown in figure 24.
A Plot of Auxiliary/Rotor Currrents against Slip
Auxiliary /Rotor Current Ia/I23 (A)
8
7
6
5
4
3
2
1
0
0 0.2 0.4 0.6 0.8 1 1.2
Slip (s)
A Plot of Auxiliary Current against Slip for 3-Phase Transfer Field Motor Without Rotor Winding
A Plot of Rotor Current against Slip for 3-Phase Transfer Field Motor With Rotor Winding
Figure 24 A plot of auxiliary current against slip for 3-phase transfer field reluctance motor with and without rotor windings.
2.3 Result
Table 2: Summary on the improvement on the output characteristics of 3-phase transfer field reluctance motor with and without rotor windings
Output characteristics |
3-phase transfer field reluctance motor without rotor windings |
3-phase transfer field reluctance motor with rotor windings |
Percentage improvement |
Electromagnetic torque against slip |
Has starting torque of 0.171N-m |
Has starting torque of 0.296N-m |
73.09% |
Power factor against slip |
The power factor at start is 0.107 |
The power factor at start is 0.180 |
68% |
Auxiliary/rotor currents against slip |
Induced auxiliary current at start is 5.409A |
Induced rotor current at start is 7.475A |
38% |
The results obtained showed that the three-phase transfer field reluctance motor without rotor windings has starting torque of 0.171N-m, while the three-phase transfer field reluctance motor with motor windings has starting torque of 0.296N-m, thereby having a percentage improvement of 73.09. Similarly, the power factor at start, for the three-phase transfer field reluctance motor with and without rotor windings were 0.180 and
0.107 respectively, with a percentage improvement of 68%. Also, the rotor/Auxiliary currents at start for the three-phase transfer field reluctance motor with and without windings were 7.475A and 5.409A respectively, with a percentage improvement of 38%.
2.4 – Conclusion
From the results obtained, it is important to state that the accelerated rotor current is a consequence of the rotor windings added to the rotor poles of the existing motor. Also, the increased induced rotor current is responsible for the improved output power, electromagnetic torque and power factor of the existing motor.
Plate1: The experimental machine Courtesy of Electrical machine lab, Electrical Engineering department, University of Nigeria Nsukka
REFERENCES
Agu, L. A. & Anih, L. U. (2002). Couple Poly phase reluctance machine without rotating windings. A technical Transactions of Nigeria society of Engineers. Pp. 37, 46 53.
Agu, L. A. (1978). The transfer field machine, Electric Machine and Electro Mechanics. pp 403-418.
Agu, L. A. (1984). Output enhancement in the transfer-field machine using rotor circuit induced currents. Nigeria Journal of Technology Vol.
8, No. 1. Pp. 7 11.
Alger P. (1970). The nature of induction motor2nd edition, Gordon & Breach New York
Ani, L.U. et al (2012). The steady-state performance characteristics of single phase transfer field machine operating in the asynchronous mode.
Nigeria Journal of Technology vol.31, No 3, November 2012 pp 219-226
Anih, L. U. (2009). Magnetic of an idealized Asynchronous reluctance machine with no moving conductors. The Pacific Journal of Science and Technology Vol. 10 Pp 3-4
Anih, L. U. & Obe E. S (2001). Performance analysis of a composite Dual winding machine. Pp 23 of 18
Anih, L. U. et al (2004). Modelling and Performance of a hybrid synchronous reluctance machine with adjustable ratio. A publication of the
IET Electric Power Applications.
Anih,. L. U. & Agu, L. A. (2008). Mechanism of Torque production in a coupled polyphase reluctance machine. Nigerian Journal of Technology
Vol. 27 No. 1. Pp 29 38.
Bhatta, C. S. K. (2009). Electrical machines (second edition). Published by Tasta McGraw-hill Publishing Ltd 7 West Pastel Nagar, New Delhi 110008 pp495
Brodway, A. R. W. & Tan, S.C.F. (1973). Brushless stator – controlled synchronous induction machine. Pp 120, 860-866 Chee-mun O. (1997). Dynamic Simulation of Electric Machinery using Matlab/simulink. Prentice Hall PTR, New Jersey.
Eleanya, M.N. (2015). Comparative Analysis of a transfer field machine and induction machine. Thesis submitted to the Department of Electrical Engineering University of Nigeria Nsukka pp 72
Fitzgerald, A. E; Charles, K. Jr. & Stephen, D. U. (2003). Electric Machinery, Tata McGraw-Hill
Gapta, J. B. (2006). Theory and performance of Electrical machine. S.K Katania and Sons 4424/6 Guru Namak Market, Naisarak Delhi-110006, pp. 578-579.
Gupta, J. B. (2000). A course in Power Systems. Published by Sanjeev Kumar Kataria and Sons. 6 Guru Nanak Market, Nai Sarak, Delhi 11006. Tenth edition. Pp. 66 69.
Ijeomah, C. N. et al (1996). Torque Enhancement of a reluctance effect machine by step-frequency secondary voltage injection method. Krishnan, R. (2000). Electric Motor drives: Modeling, analysis and control, Prentice Hall, New Jersey.
Lipo T. A. amp; Chang, K. C. (1985). A new approach to flux and Torque Sensing in induction machines IEEE IAS annual meeting.
Menta, V.K. & Rotit M. (2000). Principles of Electrical Machines published by S. Chand and Company Ltd. Rann Nagar, New Delhi 110055 pp 386
Okozi, S. O. et al (2017) Starting, steady-state modeling and simulation studies of single-phase transfer field reluctance motor, operating in the asynchronous mode. International journal of scientific research publications vol. 7 issue 1 Jan 2017 pp 182-188
Eleanya, M. N. et al (2016). Analytical determination of steady state performance indices of single-phase induction motor, using symmetrical components of unbalanced voltages of 3-phase system. International journal of recent advances in multi disciplinary research vol.03, issue 11 November pp 1913 1918.
Smarajit, G. (2005). Electrical Machine Published by Dorling Kindersley (India) PVT. Ltd. Pp. 375.
Stephen J.C. (2007). Electric Machinery Fundamental". 1221 Avenue Americas New York McGraw Hill Inc, New York 10020. Forth edition