
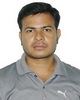
- Open Access
- [post-views]
- Authors : Menonjyoti Kalita, Dr. Pradip Baishya
- Paper ID : IJERTV12IS080093
- Volume & Issue : Volume 12, Issue 08 (August 2023)
- Published (First Online): 05-09-2023
- ISSN (Online) : 2278-0181
- Publisher Name : IJERT
- License:
This work is licensed under a Creative Commons Attribution 4.0 International License
Design and Development of Semi-Automatic Recycled Insulator Panel Maker from Waste Plastic and Cloth
Menonjyoti Kalita
Assam Science and Technology University, Assam, India.
Dr. Pradip Baishya Department of Mechanical Engineering, Assam Engineering College, Assam, India
Abstract – Solid waste management refers to the process of collecting, treating, disposing of, and recycling solid waste materials generated by human activities. solid waste management faces several challenges that vary depending on factors such as urbanization, industrialization, economic development, and cultural practices.in this paper a design of semi-automatic insulator panel maker is made which produces high value-added composite materials by combining clothes fiber and plastic waste. Waste clothes fiber was used as the reinforcement material, while plastic caps and clothes fibers were used as the matrix material for the production of composite panels. The results indicate that the developed textile-based composite panels are applicable as commercial support materials and offer improved thermal and acoustic insulation properties.
Keywords – Solid waste, matrix material, reinforcement, panels
1.0 INTRODUCTION
Every year, an estimated 11.2 billion tonnes of solid waste is collected worldwide. The world was estimated to generate 2.24 billons tonnes of solid waste, amounting to a footprint of 0.79kg per person per day. Solid waste management issue is the biggest challenge to the authorities of both small and large cities in developing countries. This is mainly due to the increasing generation of such solid waste and the burden posed on the municipal budge.
Plastic wastes are rapidly produced and exposed at a high rate due to the worlds industrial development and population growth. Both biodegradable and no degradable wastes are highly generated from man-made activities (operational sectors and climatic conditions, industrial growth, socio-economic development) and the natural processes of living creatures. Textile industry waste is an important issue and waste management is a critical factor for many countries. Textile waste comprises 6% of the total waste produced. Cotton is the most widely-used textile fibers worldwide; therefore, enormous amounts of cotton waste are produced during all stages of textile production. In a field study conducted, the amount of waste generated in the consumption of 167,850 kg cotton was given as 19,086 kg, which indicates that at least 11% of the raw material was separated as waste.
Waste management reduces the effect of waste on the environment, health, and so on. Waste plastic and waste clothes fiber provide a sustainable source of raw materials to the manufacturing industry. Using this two raw materials and then converting them into commercial composite panels will help us to manufacture products that can be used as insulators for various purposes. These insulators can be used in house walls for providing good heat insulation during winter. As this insulator is made from waste materials, the production prices will be lower so we can keep the product price very affordable.
The feasibility of using plastic and clothing waste as insulation materials depends on a number of factors, including the availability of waste materials, the cost of processing and manufacturing the materials, and the effectiveness of the insulation panels.
-
Availability of waste materials: The use of plastic and clothing waste as insulation materials relies on a steady supply of these materials. There must be a constant availability of plastic bottles and textile waste for the insulation panel to be produced in large scale.
-
Processing and manufacturing costs: The cost of processing and manufacturing insulation panels from plastic and clothing waste can vary depending on the technology used and the location of the manufacturing facility.
-
Effectiveness of the insulation panels: The thermal and acoustic properties of insulation panels made from plastic and clothing waste must be comparable to traditional insulation materials; this will ensure its acceptance in the construction industry.
-
Safety and toxicity: The use of insulation materials made from waste plastic and clothing must be safe and non-toxic, as some types of plastic can release toxic chemicals when they degrade, which is a serious concern.
-
Environmental impact: It is important to consider the environmental impact of the insulation materials, including the carbon footprint of manufacturing, the life cycle analysis of the product, and the potential for waste generation from the insulation panel.
-
Regulations and standards: Building codes and industry standards must be met. The insulation panel has to comply with all the regulations and standards set by the authorities, to ensure its acceptability in the market.
Overall, the feasibility of using plastic and clothing waste as insulation materials will depend on a variety of factors, including the availability and cost of waste materials, the effectiveness of the insulation panels, and safety and environmental considerations.
2.1 LITERATURE REVIEW
A literature review is an overview of the previously published works on a topic. The term can refer to a full scholarly paper or a section of a scholarly work such as a book, or an article. A literature review is supposed to provide the researcher/author and the audiences with a general image of the existing knowledge on the topic under question. A good literature review can ensure that a proper research question has been asked and a proper theoretical framework and/or research methodology have been chosen. To be precise, a literature review serves to situate the current study within the body of the relevant literature and to provide context for the reader. In such case, the review usually precedes the methodology and results sections of the work.
Waste management is a very important topic of concern in the modern world. Over the past few years, waste management has become a global concern. Commonly, waste is generated in households, factories, construction sites etc. As the population is increasing, consumption trends are changing. Along with the improvement in lifestyle, it has posed alarming threats to the environment. If waste is not managed properly it can cause serious problems to human health and the environment. So, it is necessary for people and businesses to know the importance of waste management.
We can develop different techniques for using waste materials to recycle and reuse them in our day to day work. Using waste plastic and waste cloth fiber we can produce different eco-friendly product which can also be market size.
-
Review on Waste Management in Asia
Daniel Hoornweg, Laura Thomas (1999) in this paper reviews the broad trends related to solid waste management in Asia. It focuses on waste management only as it pertains to urban environments. The study analyzes the trends and provides preliminary suggestions for reducing the trends' impacts. Consumes from local government budgets is examined. The paper briefly discusses possible policies and budget requirements for dealing with the burgeoning waste stream. In compiling the solid waste generation data, the authors identified shortcoming with terminology used and sampling methods and built-in problems with consistency.
-
Review on Global Solid Waste Management
Hoornweg, Daniel; Bhada-Tata, Perinaz (2012) has discussed about As the world hurtles toward its urban future, the aount of municipal solid waste (MSW), one of the most important by-products of an urban lifestyle, is growing even faster than the rate of urbanization. Ten years ago there were 2.9 billion urban residents who generated about 0.64 kg of MSW per person per day (0.68 billion tonnes per year). This report estimates that today these amounts have increased to about 3 billion residents generating 1.2 kg per person per day (1.3 billion tonnes per year). By 2025 this will likely increase to 4.3 billion urban residents generating about 1.42 kg/capita/day of municipal solid waste (2.2 billion tonnes per year).
-
Review on Plastic Waste and Management Strategies for Environmental Sustainability
HandeSezgin, MarveKucukali Ozturk, Omar Berk Berkalp, Ipek Yalcin Enis (2021) in this paper discussed about the provide awareness of plastic waste uses and routine management as a part of our life style. Plastics are produce through bio chemical process of polymerization and poly condensation plastic waste has many adverse impacts on the environment if not process and managed in a proper way. Here aims to discuss the lifestyle of plastic products according to their different categories, including polypropylene (PP), high density polyethylene (HTPE), polyethylene terephthalate (PETE) and others.
-
Concept of Making Insulation Panel
Niyitianga Evode, Sarmad Ahmed Qamar, Mohammad Billal, Damia Barcelo, Hafiz M.N. Jqbal (2021) has discussed about how to produce high value added composite material by reinforcement of textile is done by matrix material such as polypropylene and polyethylene bottle caps, food and cleaning containers. The composite panels produced having air permeability and thermal and acoustic insulation behavior.
-
Thermal Properties of Plastic material
Maxim Z., A Yu. Iziumova, O. A. Plekhov & A. Vshivkov (2019) has conducted an experimental investigation of an effect of plastic deformation on the thermal diffusivity, the thermal conductivity and the specific heat capacity of AISI 304 stainless steel. To identify the thermal diffusivity and thermal conductivity during mechanical tests the transient technique based on infrared thermography has been used. The important part of the proposed technique is the data processing algorithm that allows us to perform an identification of the characteristics by fitting an analytical solution to the temperature measurements. The solution has been obtained from the heat transfer model approximating real experimental conditions. A verification of the proposed model is conducted by the numerical simulation. As a result of the study, it has been established that the thermal characteristics of the material variety linearly under an increase of the plastic deformation.
-
Thermal properties of cloths fiber
-
P K Choudhuri , P K Majumdar (2013) has made a study among many important properties of fabrics, whose thermal properties has been given due importance by many researchers in three types of structures like woven, non-woven and knitted. This paper made clear understandings between thermal behavior and its influencing factors have also resulted in the development of some prediction models claiming sufficiently efficient.
-
Epoxy Material as a Binding Material
KP Unnikrishnan, Eby Thomas Thachil (2006) Epoxy resins constitute an important class of thermo sets which are used extensively in the field of composites, adhesives surface coatings, etc. They are of aliphatic, cycloaliphatic or aromatic backbones. Epoxy resins based on biphenyl are commercially available and they have good thermal and mechanical properties. They show comparatively low cure shrinkage. Cured epoxies are brittle with poor resistance to crack initiation and growth. Their mechanical properties, in particular toughness, can be modified by incorporating a rubbery phase into the resin matrix. The epoxy matrix can also be modified by various other methods such as incorporation of thermoplastics and particulate fillers. The toughening process leads to improvement in fracture toughness and impact resistance.
-
Thermal properties and Binding strength of Epoxy
F L Jin , S J Park (2012) has made a research on Epoxy resin/filler hybrid which composites were prepared by the melt blending of diglycidylether of bisphenol-A (DGEBA), as the epoxy resin, with nano-Al2O3 or nano-SiC particles, as the nano scaled fillers. Resulting in the thermal properties, such as the curing behavior, thermal stability, dynamic mechanical properties, and thermal mechanical properties of the DGEBA/nano-Al2O3 and DGEBA/nano-SiC composites were examined using a range of techniques. As a result, the DSC curve peak temperature of both composites decreased with increasing filler content. The integral procedure decomposition temperature increased from 630 °C to 853 °C for DGEBA/nano-Al2O3 composite and 858 °C for DGEBA/nano-SiC composite. The char yield at 800 °C increased from 14.3% to 26.226.6% for both composites. Both composites had a 10 °C higher glass transition temperature than the neat epoxy resin. The coefficient of thermal expansion of both composites at the glassy and rubbery regions decreased with increasing filler content.
-
Bio Composite material with Epoxy behavior
G Bansal , A Roy , A Ghanata & S Panwar (2018) has conducted research on Fabrication of the bio composite material is done in the laboratory. Rockwell hardness and Izod Charpy Experimental Characterization of the cast specimens of Epoxy Resin based composites which are reinforced with Chicken Feather Fibre (CFF).Composite materials are fabricated with different weight percentages of Feather and characterization of all the samples with varying weight percentages of fibre is done. Results obtained were attractive for the composite applications and have potential application in light weight composites. In this study, we investigated about the optimum CFF-epoxy resin composition. Figure 1 shows the variation in Rockwell hardness value with change in CFF wt% in epoxy based composite. Ten readings per sample were taken for the evaluation of exact Rockwell hardness of the prepared composite samples. From the results obtained (Table 1) it can be seen that with increase in wt% of CFF the hardness of the composite is increasing and it is maximum (i.e. 140.57 HRL) at 5 wt% of CFF in epoxy resin. The hardness value of neat epoxy (control) is 130.45 HRL
-
Impact and hardness properties of Epoxy resin matrix
-
-
Suresh , R. Pugazhenthi , R. Girimurugan & M K Pon (2020) has made a research on the impact and hardness properties of the epoxy resin matrix, banana fiber-reinforced, and Camellia Sinensis particles, filled bio-composites were established. Four composite specimens for Izod impact test and Rockwell hardness test were prepared as per the ASTM standards by keeping weight percentage of the matrix material as constant (65%) and varying the weight percentage of banana fiber (35, 33, 31, 29%)/Camellia Sinensis particles (0, 2, 4, 6%) respectively. Izod impact test and Rockwell hardness tests are performed on the four composites specimens as per ASTM standards. Experimental results reveal that by adding Camellia Sinensis particles with
epoxy resin matrix/banana fiber composites enhance the hardness and diminishes the impact of energy and impact strength of the composites considerably
3 OBJECTIVES
-
To use waste plastic and clothing materials in order to divert these materials from landfills and reduce the environmental impact of waste and to create a low-cost insulation panel that is easy to install and can be used in a wide range of applications.
-
To create a low-cost insulation panel that is easy to install and can be used in a wide range of applications
-
To explore and validate the possibility of converting waste into a valuable resource, that is, up cycling the material.
-
lloy Steel
-
Stainless Steel
-
-
4.0 MATERIAL SELECTION:
Stainless steel is a strong and durable material that can withstand the wear and tear of the shredding process. Its strength and hardness make it less likely to deform, crack or break under the force of the shredder machine. Also, Stainless steel is highly resistant to corrosion, even in harsh environments where the machine is exposed to moisture, chemical or other contaminants. This can help to extend the lifespan of the machine and reduce maintenance costs.
Alloy steel is a strong and durable material that is suitable for applications that demand high strength and toughness. The addition of alloying elements can increase the hardness of the steel; this can increase the wear resistance and the longevity of the blade.
On the other hand, Aluminum is a light-weight metal, it is less durable than steel and can be damaged more easily, it also have lower wear resistance properties than steel, which makes it less suitable for use in a shredder machine. And Cast iron is a strong and durable material; however, it's not as resistant to wear and tear as steel, which makes it less suitable for use in a shredder machine.
-
Initials of Tools of Data Collected:
There are two ways to collect data for any project
-
Primary data collection: Primary data collection is the process of gathering data through surveys, interviews or experiments.
For this project we were not using any type of primary data collection methods due to short time period for executing this project.
-
Secondary data collection: Secondary data refers to data that is collected by someone other than the primary user. Example: Information collected by government departments, journal papers, online website etc.
In this project the process of collecting data fully depends on the method of secondary data Collection .From the journal paper we get
-
The idea of proper execution of the project such as different process execution and the different method implementation to get required desired output.
-
How to direct in a definite direction for better result includes for definite progress applying definite way in proper direction.
-
Idea of carrying operation one after another includes sequences of operations to processing the model in a way that results greater efficiency.
-
How to select an area for materials selection.
From online website we get brief description of individual operation of the project.
-
-
-
Resin Selection:
Epoxy resin
Epoxy resins known for its high strength and durability. It can be used to bond fibers together and provide a strong, stiff and waterproof material. Epoxy resin is known for its high strength and durability, which makes it a suitable choice for insulation panels made from plastic and clothing waste. The strong bond that it creates between the fibers can help to hold the insulation panel together and maintain its shape, even under stress and pressure.
Compared to other types of resin, such as polyester and polyurethane, epoxy resin has some advantages when used in insulation panels.
-
High strength and durability: Epoxy resin is known for its high strength and durability, which makes it an ideal choice for insulation panels that will be used in high stress or high traffic areas.
-
Waterproof: Epoxy resin is waterproof, which makes it useful for insulation panels that will be used in areas where moisture is a concern.
-
Chemical resistance: Epoxy resin is also resistant to a wide range of chemicals, making it suitable for insulation panels that will be used in industrial or commercial settings.
-
Temperature resistance: epoxy resin can withstand high temperatures which make it suitable for insulation panels that will be used in high temperature environments.
-
Fire resistance: Some epoxy resins are designed to be fire-resistant which make it a suitable choice for insulation panels used in building codes that require fire resistance.
Additionally, some epoxy resins are known to release toxic fumes when curing, so it's important to ensure that the resin being used is safe and non-toxic, and that proper ventilation is provided during the curing process.
Overall, epoxy resin can be a suitable choice for insulation panels made from plastic and clothing waste.
-
-
Working Principle
In Semi-Automatic Recycled Insulator Panel Maker the collected materials (Fiber and plastic) are placed into a shredding and grinding chamber where the materials will be shredded separately. Then the separated particles will be forwarded into a binding chamber for mixing up the shredded particles. This mixture is then sent into a pressurize container where resin will be added to make a compact compound which will be resulted into a useful product. By repeating this cycle, addition of different layers forms Acoustic Insulator.
-
Working Procedure of Making Insulator Panel with the help of Insulator Panel Maker Machine
Cloth fibers obtained from waste cloth fabrics were used as the main composition material. To obtain these cotton fibers, first, the waste cloth fabrics were put on shredder machine. This step was repeated twice to obtain homogeneous fibers. After completing this step we will keep them on hold, and let them to cool down and will inspect if there are any uneven materials present then that will be removed with hand.
On the second step, we will collect the plastic bottles. After collecting them we will cut them into small pieces using scissors to make the grinding process easier. The cut materials were then placed into the grinder and the grinder speed was increased from 1200 rpm to 1500 rpm. The granulated pieces were then collected. The size of the granules is varied between 1 to 5 mm. Before combining this granulated pieces and the reinforcement material, we will inspect whether the granulated pieces matches the requirement size. If there remains any plastic that is too thick then we will separate them from the granulated pieces and put them into another bucket for future recycle use. On the other hand start the blower, blower gives hot air and apply on the shredded plastic which are already shredded by the plastic shredder. After applying heat on the shredded plastic, it converted into liquid crystal form.
On the next process, when the plastic and cloths fiber converted into desire size suction chamber sucked the both plastic and cloths from the respective shredder and put them in to the mixing chamber. In the mixing chamber both the shredded plastic and cloths mixed together and leave that mixture for while for the process of cooling. After this process, the ratio of Plastic and cloth fibers will be 3:7, Where 70% is cloth fibers and 30% is granulated plastic material. After they got mixed in the desired proportion, put them into the moulding chamber manually. Inside the moulding chamber there is a die which have exact proportion of the insulating panel. The mixture of the plastic and cloth fiber put in to the die and poured resin manually in the mixture which is already present in the die. Commercial Epoxy Resin (C21H25CIO5) is used for this process. After drying 8 to 24 hours we get a desirable insulation panel. Depending upon the size of the die, the size of the insulation panels varies.
Our desired thickness of the composite panel is around 1.2cm thick. It was ensured that all samples were produced at equal thickness. After cooling of the panel thickness will be measured using Vernier calliper to inspect whether it matches the standard.
-
Final Fabricated Model
Fig1: Final fabricated model
-
Project Components
-
Shredder Machine-The shredders are useful machines for volume reduction of bulky waste and different materials such as scrap iro ,copper, plastic as well as municipal solid waste and industrial waste. In this project, two types of shredded machines are used. This are-
-
Plastic Shredder Machine-
A plastic shredder machine is a machine that is designed to shred plastic materials into small particles. These machines are used in a variety of industries, including recycling, waste management, and manufacturing.
For the production of insulation panels, a plastic shredder machine can be used to shred plastic waste materials, such as plastic bottles into small particles. These particles can then be mixed with other materials, such as fibres from clothes, to create a composite insulation material. The shredded plastic provides insulation properties, while the fibres provide strength and durability.
Fig2: Plastic shredder machine
-
Cloth Shredder Machine
Cloth Shredder is doing process of Shredding all waste cloth or fabric, and it is using as RDF or for Textile Recycling. Textile recycling is the process by which old clothing and other textiles are recovered for reuse or material recovery. It is the basis for the textile recycling industry.
For the production of insulation panels, a clothes shredder machine can be used to shred textile waste materials such as old clothes, fabric scraps, or textile fibers, into small fibers. These fibers can then be mixed with other materials, such as shredded plastic, to create a composite insulation material. The shredded textile fibers provide the necessary strength and durability, while the shredded plastic provides insulation the necessary strength and durability, while the shredded plastic provides insulation properties.
-
Blower
-
-
Fig 3: Clothes shredder machine
Blowers are equipment or devices which increase the velocity of air or gas when passed through equipped impellers.
In semiautomatic insulator panel maker machine blower connected with the plastic shredder machine and blow hot air in to the shredded plastic. Due to this hot air shredded plastic converted into liquid crystal form.
-
Suction Chamber
A suction chamber is designed to provide a tough of low pressure between the sealed area and the intake.
In semi-automatic insulator panel maker machine sucked the shredded plastic and shredded cloths which are previously shredded by plastic shredder and cloth shredder machine, which are taken into mixing chamber.
-
Mixing Chamber
Mixing chamber is a chamber where two or more different or similar types of matter mixed together.
In the semi-automatic insulator panel maker machine, plastics and cloths from respective plastic and cloths shredder machine are sucked to the mixing chamber and manually mixing is done.
4.3.4 Moulding Chamber
Moulding chamber is a chamber in which insulation panel give its desired shape. In the molding chamber there is another chamber, is called die chamber which is inserted on the moulding chamber. The size of the insulator panel is depended upon the size of the die chamber. After manual mixing, mixture is sent to the moulding chamber and spread uniformly in the chamber. Then externally resin is applied to the mould.
-
Parameter
-
RPM Selection and Determination
In general, higher RPMs will produce smaller and more consistent shredded material, while lower RPMs will produce larger and more irregular shreds. The most suitable RPM would depend on the type of plastic and clothing that you are shredding, the final product and the design of the shredder.
The insulation panel is intended for soundproofing, it's important that the fibers are small and consistent to produce a good sound insulation. Whereas, if the insulation panel is intended for thermal insulation, the fibers can be larger and more irregular, as long as they fill the voids and provide a good thermal insulation. To find the most suitable RPM, it's a good idea to test different speeds to find the one that provides the best balance between shred size and consistency, energy efficiency, and machine lifespan.
Determination of RPM
-
For cloth shredder 1200-1500 rpm
-
For plastic shredder 1200-1500 rpm
-
-
-
Determination of Insulator Plate Thickness Determination of Thickness-
-
Insulator 1.2 cm
-
-
Size Determination
Determination of Size-
-
For shredded plastic 1-1.5 mm
-
-
Energy Requirement Determination Determination of Energy Required
-
12V,2 Ampere step-down transformer
-
12V DC motor
-
-
Design of the actual model components
-
Plastic Shredder
Internal Diameter (d)= 110.5mm External Diameter (D) =117.2mm Depth=65.1mm
Height (h)=67mm
Volume of the Plastic Shredder
=× (D2-d2)×h
=3.14× (117.22-110.52)×67
=320953.62mm3
-
Cloth Shredder
Internal Diameter (d) =110.5mm External Diameter (D) =117.2mm Depth =65.1mm
Height(h) = 67mm
Volume of the Cloth shredder
= ×(D2-d2)×h
=3.14×(117.22-110.52)×67=320953.62mm3
-
Mixing Chamber
Internal Diameter = 110.5mm External Diameter = 117.2mm Depth = 65.1mm
Height = 64.8mm
-
Moulding Chamber
-
Wall thickness = 4.3mm Length (l) = 127mm Breadth (b) = 110mm Height (h) = 51.2mm
Volume of the moulding Chamber =l×b×h
=127×110×51.2
=715264mm3
5.5mould
Wall thickness = 4.3mm Wall height (h) = 125.85mm Length (l) = 90mm Breadth(b) = 90mm
Volume of the mould=l×b×h
=90×90×125.85
=1019385mm3
6.1 FINAL PRODUCT
Fig4: Insulation Panel before Drying Fig5: Insulation Panel after drying
-
Measurements Length = 87.8mm Breadth = 87.8mm Height = 12mm
-
Calculations
6.3.1Volume of the insulation panel=Length×Breadth×Height
=87.8×87.8×12
=92506.08mm3
6.3.2Surface area of the insulation panel
=2(lb+ bh +hl)
=2{(87.8×87.8) + (87.8×12) + (12×87.8)}
=2(7708.84+1053.6+1053.6)
=19632.08mm2
7 CONCLUSION
India generates 62 million tonnes of waste each year. About 43 million tonnes (70%) are collected, of which about 12 million tonnes are treated, and 31 million tonnes are dumped in landfill sites. Solid waste management is an important focus for many countries as this waste poses numerous risks to the environment.
Globally, vast quantities of textile and plastic waste are generated, for which recycling is not economical. In this study, the main goal was to develop composite panels from 100% recycled components to be used as alternative insulation materials. Making insulator panels from recycled materials would help us to reduce manufacturing cost.
This project will provide a great message for others to design and manufacture devices for using wastes to make more commercial products. We have taken the raw materials from solid waste which helps in getting raw materials in available way and reduce raw materials purchasing and carrying cost.
REFERENCE
[1] Hande Sezgin ,Merve Kucukali-Ozturk, Omer Berk Berkalp, Ipek Yalcin-Enis,Design of composite insulation panels containing 100% recycled cotton fibers and polyethylene/polypropylene packaging wastes (1 July 2021) 304:510-526. [2] Jià Zach, Richard Slávik, VÃtzslav Novák, Investigation of the Process of Heat Transfer in the Structure of Thermal Insulation Materials Based on Natural Fibers Procedia Engineering,( 2016)151:pp: 352-359 . [3] Shafiqul Islam, Gajanan Bhat, Environmentally-friendly thermal and acoustic insulation materials from recycled textiles, Management, (1st December 2019), 109536: pp: 223-256. [4] N. Evode, S.A.Qamar, M. Billal, Damia Barcelo, Hafiz M.N. Jqbal.Plastic waste and management strategies for environmental sustainability (26th September.2021). [5] HandeSezgin, MarveKucukali Ozturk, Omar Berk Berkalp, Ipek Yalcin Enis. ,Design of composite insulation panels containing 100% recycle cotton fibres and polyethylene / polypropylene packaging wastes (12April 2021). [6] H. Daniel; Bhada-Tata, Perinal. Global Review of Solid Waste Management 2012. [7] K.P.U, Eby T Thachil, Waste management in Asia, International Journal in Waste management, (2012). [8] KP Unnikrishnan, Eby Thomas Thachil Toughening of epoxy resins (2006, September). [9] Labayen I. Yuan Q,bn, A Review on Textile Recycling Practices and Challenges(2022) [10] https://ihsmarkit.com/products/fibers-chemicaleconomics-handbook.html (accessed on 6 December 2019). [11] https://www.statista.com/statistics/263154/worldwide-production-volume-of-textile-fibers-since-1975/ (accessed on 6 December 2019) [12] https://businessinsurrey.com/wpcontent/uploads/2018/05/UnravellingtheProblemofApparelWasteintheGreaterVancouverAreaMarcp 2018.pdf (accessed on 10 March 2019). [13] https://www.globalfashionagenda.com/publications/#pulseofthefashionindustryreport (accessed on 22 November 2018). [14] Luamkanchanaphan T., Chotikaprakhan S.and Jarusombati S, A study of Physical, Mechanical and thermal Properties for thermal insulation from Narrow-leaved Cattail Fibers (2013)