
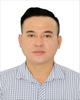
- Open Access
- Authors : Nguyen Manh Tuong, Nguyen Van Hoa, Nguyen Anh Tuan, Nguyen Thanh Dat
- Paper ID : IJERTV12IS080088
- Volume & Issue : Volume 12, Issue 08 (August 2023)
- Published (First Online): 13-09-2023
- ISSN (Online) : 2278-0181
- Publisher Name : IJERT
- License:
This work is licensed under a Creative Commons Attribution 4.0 International License
Research for Dynamic Responsibilities of Pile In Civil Aviation Construction and the Bearing Capacity of Piles Under Dynamic Load In Civil Aviation Activities
Nguyen Manh Tuong
PhD in Civil, Lecturer at the Civil Engineering department
Ho Chi Minh City College of Construction (HCC), Vietnam
Nguyen Anh Tuan
Vietnam Aviation Academy
104 Nguyen Van Troi, Phu Nhuan District, Ho Chi Minh City, Viet Nam.
Nguyen Van Hoa
Vietnam Aviation Academy
104 Nguyen Van Troi, Phu Nhuan District, Ho Chi Minh City, Viet Nam.
Nguyen Thanh Dat
Associate Professor in Civil, Lecturer at the Civil Engineering department
Vietnam Aviation Academy (VAA), Vietnam
Abstract – In practice, especially on soft ground, it is necessary to understand the characteristics of the soil under the effect of dynamic loads. In the southern area, there are many civil aviation projects under construction or renovation such as: Long Thanh airport, Bien Hoa airport, Thanh Son airport… The foundation of the construction works in the airport. Piles foundations are not often used, which have a large load capacity, especially the impact of dynamic loads when the aircraft takes off and lands. These loads have different frequencies, amplitudes and strengths transmitted from the foundation of the building to the pile, or from the surrounding soil, affecting the pile itself and the extreme deformation area around the pile. In addition, the dynamic loads acting on the foundation are also caused by explosions, impulse loads, machines, motors, equipment… These types of loads are the cause of large deformations in the soil as well as effects. affect the concurrent work of the project. The comprehensive study of the effects of dynamic loads as well as the approach trends in the world is an urgent issue at present.
Keywords – frequencies, civil aviation constructions, extreme deformation, dynamics load, bearing capacity.
-
INTRODUCTION
The Southern area is located in a dynamic economic development area, focusing on many industrial civil construction site. In this area, many places below the soft soil are fine sand layers of medium-tight state. Building that use pile foundations, the pile tip is often resistant in this soil layer. According to calculations this layer of sand bearing is quite good under the effect of static loads. However, when subjected to dynamic load, the load capacity of this soil layer is significantly reduced, causing disadvantage to the pile system. In industrial parks, export processing zones havefactories that place machine foundations subject to dynamic loads of different frequencies, amplitudes and intensities. The above loads from the building transmitted to the pile, or from the surrounding ground affect the pile causing the
pile itself, the extreme deformation area around the pile different effects. Therefore, the study of calculating the dynamic load bearing capacity of the pile to support the building as well as finding the reduction of load bearing capacity after the building is subjected to dynamic load is necessary. Currently, the calculation of the effect of the dynamic load on the load capacity of piles has many methods. Usually to add to the effect of the dynamic load on pile load bearing, one adds the coefficient to the result of static load bearing of piles. The static compression experiment has the effect of dynamic load, initially clarifying the effect of dynamic parameters on pile load bearing. The results of the experiment identified the correlations between pile deformation and frequency of dynamic load as well as force-resistance relationships. These are the figures that serve as the basis for the design calculation, assessing the effect of the dynamic load on pile load capacity in soft soil.
-
RESEARCH METHOD
-
Overview of the effect of dynamic loads on pile load capacity.
Intensity, deformation under the influence of instantaneous load.
Figure 1. Stress – Strain of soil with impulse load at tL = 0.02s
Figure 2. Stress – Deformation of soil with impulse load.
According to Han (2018) studied the model of driven pile field experiments to find load bearing and residual load in piles. According to Naggar (2019), the study established a model of stress wave energy transmission in background. Simulation results for piles are compared to control software for frequency effects with different physical influences.
According to Wu (2020), Tolun (2020), Rajpoot (2020), Lin (2020) simulates a number of different models for piles to study the dynamic reaction of the back ground pile. Ahmed (2015), Azizkandi (2018),Chaudhuri(2020), Zhang(2020), Lou(2020), Yan(2016), Liu(2020), Zhu (2020) studied dynamic load effects and found fairly reasonable results for the direction of digital simulation research. Garala (2020) studied aluminum pile with centrifugal test. Rui He (2019) studied the dynamic single pile model with frequencies. Huang (2020), Mishra (2019), Li(2020), Subramanya(2019), Varghese(2020), Zhanfang (2020), Yi (2017), Zhou (2019), researching the design of dynamic load-bearing models.
-
Maintaining the Integrity of the Specifications
The template is used to format your paper and style the text. All margins, column widths, line spaces, and text fonts are prescribed; please do not alter them. You may note peculiarities. For example, the head margin in this template measures proportionately more than is customary. This measurement and others are deliberate, using specifications that anticipate your paper as one part of the entire proceedings, and not as an independent document. Please do not revise any of the current designations.
-
-
APPLICATION OF FEM
A. Study the application of FEM in the analysis of pile load bearing calculation.
Combining the semi-experimental formula of the foundation construction company, field experiments, numerical simulation is the research direction of scientific and practical value in calculating pile load bearing using Plaxis software with background models.
Figure 3. Result in MCC model
Figure 4. MCC model P-S chart (FEM) with LoadTest
The results of correlation of parameters in the MCC model: M-Kappa: M = 0.4073-0.219; Lambda-Kappa: =
729.622 – 13.653 + 0.0652
-
APPLICATION OF THE PHYSICS
The research model looks at the effects of the load on Stress
Deformation throughout the length of the pile body and the pile tip, simulating custom changes to many factors affecting static and dynamic loads on pile.
According to studies and evidence, the frequency f has a decisive effect on the displacement of the pile: f = g(L; D; ; ; c; d)
Transform Pi equation g = 0
The research parameters range from 7 independent quantities after the transformation of Pi to 4 dependent quantities. The dependence and relevance between quantities shows the degree and importance of quantities with the parameters of the dynamics due to the external dynamic load acting on affecting the deformation and displacement of the pile.
Figure 5. Pile lowering process Check the verticality and press
Figure 6. Signal system for devices and connections
Figure 7. Installation diagram of model laboratory equipment system
Piles are pressed according to the pile pressing and resting process, then static compression tests are conducted. Measurement results on probe mounting positions according to static compression cycles are shown below.
At the time of the maximum compression force P = 186.2(kgf) the nose deformation is equivalen to 158(µ). Meanwhile, the position of SG2 near the pile tip measured 968(µ) much larger than the pile tip. Thus, the Law of Force – Deformation shows the distribution of longitudinal force, wall friction, pile tip specifically.
Experiments on small-scale physical models can ensure compatibility conditions as well as lower costs. Meanwhile, it is possible to increase the options for input parameters compared to large-scale off-site experiments. Studying the effect of soil mechanical indicators, L/D ratios on deformation, displacement and pile load capacity is sufficient to ensure the appropriate experiment. The experiment affects the geometric parameters of the L/D pile, the mechanical indicators of soil c, the , the parameters of the dynamics due to the external dynamic load affecting the deformation, the displacement of the pile ensures the reduction of the experimental parameters but still has the acceptable results at the permissible level. The design studies of the model structure system ensure the ratio problem and issues related to pile-soil interaction. Researching the design and installation of laboratory equipment system to measure the impact on the dynamic load on the behavior of piles, the load capacity is enough to ensure that the experiment meets the standards and objectives set out. After proceeding with the static compression pile, rest the pile on time, conduct dynamic experiments on the pile to study the behavior of the pile.
-
EXPERIMENT
-
The experiment determined the effect of the dynamic load on pile load capacity.
Dynamic parameters are loaded on speed control software
Figure 8. Force-Strain relationship on pile body positions
Figure 9. Connect the device system on the dynamic load test model.
-
The results of dynamic teste and the behavior of piles.
Figure 10. Settlement – Frequency relationship
Figure 11. FFT frequency analysis of pile (f = 20Hz)
The results of frequency analysis show that at the frequency of 18Hz, the peak acceleration reaches 0.0055m/s 2 . The spectrum plot at 25Hz shows that the peak acceleration increases very quickly and reaches 0.158m/s 2 . Analysis by time domain, at frequency 26Hz, the strain intensity has a rapid increase in amplitude and changes quite perturbed. This is very different from the smooth pile where the dynamic response of the pile to the frequency changes in magnitude is not much.
-
Analysis of experimental results of research model applied to reality
Calculations applying research results to piles in practice
FS1
F = -0.125P2 + 57.062P – 9.3687
Q_p
F = 2.937P2 1221.18P + 200.56
Force – Lateral resistance ratio / Tip resistance
Pile head
FS0/Q_p = -0.125P2 + 63.56P – 11.608
Pile tip
FS1/Q_p = 0.25P2 91.875P + 15.264
TABLE I. CORRELATION EQUATION AT ACTUAL DESTRUCTIVE FREQUENCY
-
Application research FEM of small model experiments.
Numerical model is applied to simulate dynamic test to determine the effect of dynamic load on pile load capacity. Plaxis 3D Dynamics software simulates a miniature model experiment to perform comparative evaluations, which helps to limit the disadvantages of other methods. Numerical simulation helps to quickly implement, increase input parameters to customize options according to research requirements.
Perform simulation of experimental soil parameters, input parameters, using the selected MCC model to run the dynamic model. The numerical model built to simulate the ground has the same geometrical and mechanical properties as the dynamic experimental model.
Figure 12. Frequency – Settlement chart of L/D piles
The numerical simulation results for the correlation between Settlement – Frequency response of the piles are quite similar to the experimental results. All three types of piles have no dynamic response at frequencies from 0 to 15Hz. From the time of the frequency of 18Hz – 20Hz, the pile has a slow settlement rate and in the frequency range of 20-25Hz, all 3 piles begin to have a high settlement rate. Due to the small lateral load capacity, L40 pile responds earlier and tends to decrease sharply, settlement increases faster. In the first stage from 15-20Hz, the L50 pile responds quite like the L60 pile. However, at a later stage, the dynamic response pile L50 tends to be similar to the pile L40. This result is quite similar to the experiment, however, the difference is that at the failure frequency, the L60 pile has a smaller settlement than the other 2 piles. This can be explained by the experiment during the construction of pile pressing and static compression test, causing the pile-soil friction of the upper body to be strongly reduced. The pile body is separated during construction and is subjected to dynamic loads, which reduces lateral friction. Meanwhile, the numerical simulation does not consider the effect of the construction process on the lateral resistance of piles with large L/D in loose soil environment.
TABLE II. CORRELATION EQUATION FREQUENCY – MODEL PILE SETTLEMENT
Pile type
L/D
Correlation equation
L40
20
S = -0.1339f 2 + 2.2278f – 4.0259
L50
25
S = -0.1167f 2 + 1.9992f – 3.6974
L60
30
S = -0.079f 2 + 1.3456f – 2.5407
Figure 13. Histogram of the frequency- Resistance Qp on the pile
The tip resistance Qp of the piles responds to quite similar frequencies from 0 -10Hz. According to the analysis of the effect of dynamic loading on the grain arrangement leading to an increase in compaction. From the frequency of 10Hz onwards, the nose resistance increases rapidly, and the nose load capacity increases the most. When the ground reaches the peak state, the expansion angle reaches the maximum, the ground enters the sliding state. Qp rapidly declines at time f = 22Hz. However, the L60 pile has a slower Qp because the frictional resistance is mainly concentrated in the Qs part. The results are relatively consistent with the miniature model experiment. The pile L60 continues to increase Qp after the frequency of 22Hz, so the total resistance Q of the pile increases compared to the two piles L40, L50.
Figure 14. Frequency – Resistance Qs on L/D piles
-
Compare the results of modeling experiments and numerical simulations.
To study and find out the rules of frequency effects on the dynamic response of piles, we set up correlation charts between the two experiments and numerical simulation. The experimental pile is set to automatic measurement at each time interval and the correlation with the settlement measurement value by the displacement transducer is output. Meanwhile, the pile simulates the number of cumulative measurement results continuously and records the results in a continuous frequency range. Therefore, the numerical simulation data is continuous, smooth and quite uniform. This is the advantage of numerical simulation when automatically outputting results compared to model experiments that require data processing tools.
The Qp resistance of the piles responds to quite the same frequency from 0-10Hz. According to analyses of the effect of the dynamic load on the particle arrangement leads to an increase in tightness. From the frequency of 10Hz onwards the tip resistance increases rapidly the greatest increase in tip load capacity. When the background reaches the peak state, the angle of expansion reach its maximum, the ground transitions to a sliding state. Qp rapidly declines at the time of f
= 22Hz. However, the L60 pile has a slower mobilization Qp because the friction resistance is mainly concentrated in the Qs section.The results are relatively consistent with the miniature model experiment. L60 piles continue to increase Qp after a frequency of 22Hz, so the total Q resistance of the pile increases compared to 2 piles L40, L50.
Figure 15. Frequency comparison – Pile deformation L40
Figure 16. Frequency comparison – Pile deformation L50
Figure 17. Frequency comparison – Pile deformation L60
From FEM results and experiments, the advantages of the FEM in geotechnical problems in general and the problem of
simulating the load-bearing pile foundation in particular. With numerical simulation experiments, the advantages of time conducted, speed of program processing, results are more reasonable. The model test before simulating the number has the advantage of identifying the convergence of the program. Simulation of the following number will reduce the stages of running the program with the defined frequency bands thereby significantly reducing the time of effort and reliable results. As such, the frequency range has a dynamic response of piles from 15-30Hz. Tip resistance varies quite chaotically when the frequency of sabotage is reached and tends to decrease sharply. The analysis of the dynamic response mechanism of the background – pile in the experiment and FEM can be satisfactorily explained on the basis of the stress roadmap. The dynamic response of the pile body and the tip of the pile when subjected to stress waves transmitted down along the pile body and the mechanism of transmission from the pile to the extreme plastic deformation land around the pile can be explained by the PDA quite clearly.
-
-
CONCLUSIONS
From small-scale modeling experiments to model theory studies and proportional law according to the above-mentioned analyses show:
-
The model pile shows the relationship of pile deformation corresponding to different frequencies; Deformation value – deformation; Deformation relationship – unit tip resistance – unit side friction; Deformation – The ratio of unit friction force and tip resistance according to the depth of piles shows that with the specific frequency, the L / D ratio will most pronounce the load resistance.
-
The L40 pile, which starts the frequency of 26Hz, is worth the number of tip resistance Q_p is sharply impaired. At a frequency of 28Hz responds to the pile head with a frequency that causes the tip resistance to increase suddenly. The compression force coincides with the stress wave causing a strong increase in resistance according to the mechanism of damage to the pile head. The L50 pile has a fairly stable Q_p and loses load capacity at deformation S = 5mm.
-
Starting frequency 15Hz to 20Hz, deformation of straingages of pile body and pile head has small fluctuations, deformation at near the pile station with large value variation. From a frequency of 22Hz to 28Hz, distortions have a high absolute value that describes behavior when subjected to fluctuating frequencies. Shifting through the balance position of the pile increases rapidly leading to sabotage of side friction.
-
Throughout the pile length, the analysis found forces- unit friction- tip resistance as well as force relationships – the ratio of FS1/tip resistance to the correlation equations established in chapter 5 of the thesis.
-
The pile has an L/D of 20 or more, with the D400mm prototype pile, a ratio of 1/25, a frequency of a ratio (1/25)-1/2 (ratio = 5). With a frequency range from 22Hz to 28Hz, an average of 25Hz, the pile with L/D > 20 internal forces reached dangerous value, the deformation increased rapidly, the load capacity of the pile ground load decreased sharply. As such, it can be speculated in fact that frequencies above 5Hz can cause L/D piles = 20 to degrade strong load bearings, the pileheads and reinforced concrete pile joints near the pile head may be
damaged due to the dynamic response of the pile to the destructive frequency.
-
With the numerical simulation pile, at the actual frequency of 5Hz pile begins to reduce load capacity, the pile has L/D = 20 strong load resistance depletion and has a stronger deformation result than the L/D pile = 25 and L/D =
30. At the time the pile reaches the destructive frequency, the side load capacity decreases steadily. However, the tip load capacity Q_p suddenly declined sharply. This is similar to the miniature model pile proving that the frequency plays a decisive role in the passive pile load capacity.
-
The combination of numerical simulation and experiments shows the advantages of the FEM in Geotechnical problems in general and the problem of simulating dynamic pile foundations subject to load in particular. With numerical simulation experiments, the advantages of time conducted, speed of program processing, results are more reasonable. However, in order to be able to assess whether the numerical model reflects the actual dynamic response, the model experiment is necessary to observe the qualitative trend assessment and quantify the results. The model test before simulating the number has the advantage of identifying the convergence of the program. Simulation of the following number will reduce the stages of running the program with the defined frequency bands thereby significantly reducing the time of effort and reliable results.
-
As such, the frequency range has a dynamic response of the pile from 5 to 10Hz. The tip resistance varies quite chaotically when the frequency of infestation is reached and tends to decrease sharply. From the experiment showed that the fact that large L/D piles are prone to bending when subjected to dynamic loads, reducing tip resistance while the pile simulating the effect of vertical bending is quite small.
-
The analysis of the dynamic response mechanism of the background – pile system in the experiment and the numerical simulation can be satisfactorily explained on the basis of the stress path of the soil around the pile. The term around the pile can be explained in accordance with the PDA quite clearly.
-
The input parameters of the D400mm pile actual number simulation have been analyzed backwards and are quite reasonable value to put into use the numerical simulation. the parameters are calculated according to model theory with
the law of ratios that produce fairly reasonable results. The results of the survey of the frequency of piles showed that the response of the pile with reasonable frequency in accordance with reality and the model experiment with a value of 5-10Hz.
-
The effect of the 2 layers of leveling soil and the clay layer above the sand layer placed the pile head is quite reasonable when meeting the pile head of the building is really reduced. The frequency spectrum when comparing the two simulations and experiments showed that the effect of this value should meet the dynamics of the pile head when reaching the destructive frequency is quite clear through the pile resistance chart.
REFERENCES
[1] Chaidul Haque Chaudhuri et al. (2020), Three-dimensional numerical analysis on seismic behavior of soil-piled raft-structure system, Structures , Elsevier, p. 905-922. [2] Linya Chen et al. (2020), "Physical modeling of combined waves and current propagating around a partially embedded monopile in a porous seabed " , Ocean Engineering . 205, p. 107307. [3] H Elahi et al. (2018), "Pseudostatic seismic response analysis of a pile group in a soil slope " , Geotechnical Geological Engineering 36(2), p. 855-874. [4] Mohammed Y Fattah and Bushra S Zabar (2020), "Effect of saturation on response of a single pile embedded in saturated sandy soil to vertical vibration " , European Journal of Environmental Civil Engineering . 24(3), p. 381-400. [5] Zhi-Ren Feng et al. (2019), "Three-dimensional finite element modeling for seismic response analysis of pile-supported bridges " , Structure Infrastructure Engineering . 15(12), p. 1583-1596. [6] Thejesh Kumar Garala, Gopal SP Madabhushi and Raffaele Di Laora (2020), "Experimental investigation of kinematic pile bending in layered soils using dynamic centrifuge modelling " , Géotechnique , p. 1-16. [7] Rui He and Tao Zhu (2019), "Model Tests on the Frequency Responses of Offshore Monopiles " , Journal of Marine Science and Engineering . 7(12), p. 430. [8] Yu Huang et al. (2020), "Centrifuge modeling of seismic response and failure mode of a slope reinforced by a pile-anchor structure " , Soil Dynamics Earthquake Engineering & Structural Dynamics . 131, p. 106037. [9] Guillermo Alfonso Lopez Jimenez (2019), Static and Dynamic behavior of pile supported structures in soft soil , University Grenoble. [10] Elham Dehghan Haddad and Asskar Janalizadeh Choobbasti (2019), "Response of micropiles in different seismic conditions " , Innovative Infrastructure Solutions . 4(1), p. 53.