
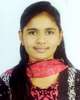
- Open Access
- Authors : Pooja U R , Kendra N , Dr. A. Murugarajan
- Paper ID : IJERTV12IS080097
- Volume & Issue : Volume 12, Issue 08 (August 2023)
- Published (First Online): 13-09-2023
- ISSN (Online) : 2278-0181
- Publisher Name : IJERT
- License:
This work is licensed under a Creative Commons Attribution 4.0 International License
Obstacle Detection AGV
Pooja U R
B.E, Robotics and Automation Sri Ramakrishna Engineering College
Coimbatore, India
Kendra N
-
, Robotics and Automation Sri Ramakrishna Engineering College
Coimbatore, India
Dr A Murugarajan
HOD & Professor (Department of Robotics & Automation)
Sri Ramakrishna Engineering College
Coimbatore, India
Abstract – AGVs are used to facilitate the movement of materials from one location to another. The majority of material handling tasks are now carried out by AGVs across most industries. There is a chance of colliding with obstacles in such congested areas. We suggested a technology called Obstacle detection AGV to avoid such impediments. Line following is the basis for how this operates. Line following and obstacle detection are handled by the infrared (IR)sensor, while coordination and intelligence processing are handled by an Arduino AT mega 328p. Here the robot chassis is mounted with an IR sensor, an Arduino, and motor driver. The infrared sensor installed in front of the chassis helps the AGV detect the line (a black line on a white surface). The microcontroller receives the sensor data and uses it to transmit a signal to the motor driver, who then uses the information from the IR sensor to drive the motor of the robot chassis. The IR sensor delivers a signal to the microcontroller, which then sends a signal to the piezoelectric buzzer, which causes the buzzer to ring, if any obstacles are found in the path. An AGV resumes moving in the direction of its destination once the obstruction has been eliminated.
KeywordsAGV, Line following, Obstacle Detection
-
INTRODUCTION
A mobile robot known as an automated guided vehicle (AGV) follows wires or lines that have been imprinted on the floor or navigates by radio waves, cameras, magnets, or lasers. They are most frequently employed in industrial settings to move big objects inside sizable industrial structures like factories or warehouses. Since their introduction in 1953, these devices have played a part in the transportation of materials. These AGVs can now carry out the majority of material handling tasks currently carried out by people and can work for longer periods of time than people. They are frequently employed in many sectors to increase the effectiveness of material handling procedures, hence their significance to the process cannot be overstated. While there are many components of an AGV that might be explored, successful and secure navigation from one place to another still needs to be prioritized. One essential component is that the AGV must be able to recognize obstacles in its path in order to avoid colliding with them. In any other case, these crashes risk damaging both the vehicles and the goods or materials being delivered. This project demonstrates how an IR sensor is used to detect obstacles.
-
COMPONENTS REQUIRED
A. Components and its Description
Arduino ATMEGA-328P: The Arduino ATmega328P is a pivotal component in the world of microcontrollers. Operating at up to 16 MHz, it embodies an 8-bit AVR RISC architecture. With 32KB of Flash memory, it accommodates program codes, while 2KB of SRAM handles temporary data storage. Additionally, 1KB of EEPROM provides non-volatile memory for crucial information. Boasting 23 versatile I/O pins, it allows for digital and analog operations. This microcontroller's versatility and capability make it the cornerstone of countless innovative projects in the realm of electronics and automation.
Motor driver (L293D): The L293D motor driver is a compact and versatile integrated circuit designed to control the movement of DC motors. It acts as a bridge between microcontrollers and motors, allowing for precise direction and speed control. With its dual H-bridge configuration, the L293D can drive two motors independently, making it ideal for robotics and automation projects. Its built-in protection diodes help prevent damage from back EMF (electromotive force) generated by the motors. Additionally, the L293D is capable of handling relatively high current, making it suitable for a wide range of motor sizes
Infrared sensor (Right & Left IR sensors): Both the heat and motion of an item can be measured by an IR sensor. Typically, all objects in the infrared range emit some kind of thermal radiation. Although these radiations are undetectable to the human eye, infrared sensors are able to detect them. We used this type of infrared sensors to detect the line and follow the appropriate path.
Infrared sensor (Obstacle Detection): The receiver detects the infrared light from the LED that reflects off an object as it gets close to the sensor. This is how the sensor is serving the purpose of detecting the obstacle.
Piezo Electric Buzzer: A piezoelectric buzzer is a compact electronic component that generates sound through the piezoelectric effect. It consists of a piezoelectric crystal or ceramic disc sandwiched between two metal plates. When an electrical voltage is applied across the plates, the piezoelectric material deforms, producing mechanical vibrations that create sound waves. Piezo buzzers are known for their simplicity, reliability, and efficiency. They find wide application in alarms, electronic devices, timers, and other systems where a clear and audible alert is needed. Due to their low power
consumption and durability, piezo buzzers are favored in many electronic circuits for their ability to provide effective audio feedback.
Power supply-Lead acid battery: A lead-acid battery is a rechargeable energy storage device that employs a chemical reaction involving lead plates submerged in an electrolyte solution, usually sulfuric acid, to store and release electrical energy. These batteries have been widely used for over a century due to their reliability and relatively low cost. Lead- acid batteries come in various forms, including automotive batteries for starting engines and deep-cycle batteries for continuous, slow discharges. They are prevalent in vehicles, uninterruptible power supply (UPS) systems, solar energy storage, and other applications where a reliable and robust energy storage solution is required. While they have been
-
Software model
-
-
PROPOSED SYSTEM
largely superseded by newer technologies like lithium-ion, lead-acid batteries continue to be indispensable in numerous industrial and automotive settings.
DC Motor associated with wheels: A DC motor is an electrical device that generates force through the use of direct current (DC). The most popular kinds depend on magnetic forces generated by currents in the coils. Almost all DC motor types contain some internal device, whether electromechanical or electronic, to change the direction of the motor's current regularly. Here it is used in the left and right side of the AGV for facilitating the motion.
Relay: An automatic switch called a 5volt relay is frequently used in automatic control circuits to regulate high currents with low current signals. The relay signal's input voltage spans the 0 to 5V range. Here it is used to cut off the supply in the proposed system when the obstacle is detected and activates alarm.
Jumper wires: They are just cables with connector pins on each end, which make it possible to connect them without soldering. Since electricity requires a medium to go through in order to move from one place to another on a circuit, connecting wires enables this movement. They are usually made of copper, a good conductor of electricity.
Toggle Switch: A toggle switch is mde to give current a path via which it can either turn on or off (break or create a circuit). Toggle switches are actuated by hand, typically by flicking a small lever left or right or up or down.
Caster Wheel: There is a supporting wheel named castor wheels which aids in the direction-change of two-wheel driven AGV. It is a a wheel that is not propelled and is intended to be attached to the base of a larger object and used to move it. Device moving equipment has caster wheels attached to the base that enable mobility of certain objects. They make it possible to move heavy objects with less force.
Fig. 1. Circuit connections of proposed model
The simulation of our project is based on obstacle detection AGV (line follower) robot. As we know, the line follower robot is used to find the black line on a white path or vice- versa. Here we used 2 IR sensors to follow a black line on a white path and an IR sensor to detect the obstacles. The other components used are Arduino, Right and left DC motor, Motor Driver(L293D) and the battery is not very essential for simulation as it is sufficient with the Arduinos power supply of 5V. Hence, the obstacle detection AGV simulation.
-
Block Diagram Explanation
Fig. 2. Block Diagram of the proposed model
Note: The pictures used above are only to easily visualize the flow of the proposed system. This may not resemble the actual product.
*The image of our hardware module setup is clearly mentioned below*
The step-by-step process for constructing an obstacle detecting AGV was shown in the block diagram.
[1] First off, it entails the robotic vehicle, also known as the robot chassis, which has two wheels attached to it for mobility and one wheel acting as a support system for the entire setup. [2] We all know that a line follower robot is used to locate a black line on a white path or vice versa. [3] Additionally, we employed an IR sensor to identify the obstacles and give an alarm via buzzer. [4] Arduino, a right and left DC motor, and a motor driver (L293D) are the other components used. [5] We have integrated the line follower with the obstacle detection sensor. [6] Finally, we have combined the hardware and software using Arduino IDE platform. [7] Hence, the block diagram illustrating the proposed system's flow. -
Arduino Software Code
a.
// Black Line Follower
int IR1=8; //Right IR sensor
int IR2=9; //left IR Sensor
int IR3=7; //IR sensor (3) for obstacle detection
// Motor A
int enA = 5; //Right motor
int MotorAip1=2; int MotorAip2=3;
// Motor B
int enB = 6; //Left motor
int MotorBip1=4; int MotorBip2=7; void setup ()
{
pinMode(enA, OUTPUT); pinMode(enB, OUTPUT); pinMode(IR1,INPUT); pinMode(IR2,INPUT); pinMode(MotorAip1,OUTPUT); pinMode(MotorAip2,OUTPUT); pinMode(MotorBip1,OUTPUT); pinMode(MotorBip2,OUTPUT); pinMode(7,INPUT); pinMode(13,OUTPUT); Serial.begin(9600);
}
void loop ()
{
if(digitalRead(IR1)==HIGH && digitalRead(IR2)==HIGH)
//IR will not glow on black line
{
//The below code would stop both Motors digitalWrite(MotorAip1,LOW); digitalWrite(MotorAip2,LOW); digitalWrite(MotorBip1,LOW); digitalWrite(MotorBip2,LOW); analogWrite (enA, 0);
analogWrite (enB, 0);
}
elseif(digitalRead(IR1)==LOW&& digitalRead(IR2)==LOW)
//IR not on black line
{
//The below code would move both the Motors digitalWrite(MotorAip1,HIGH); digitalWrite(MotorAip2,LOW); digitalWrite(MotorBip1,HIGH); digitalWrite(MotorBip2,LOW);
analogWrite (enA,100); analogWrite (enB,100);
}
Elseif(digitalRead(IR1)==LOW&& digitalRead(IR2)==HIGH)
{
//The below code would help to tilt robot towards left by stopping the left wheel and moving the right one digitalWrite(MotorAip1,HIGH); digitalWrite(MotorAip2,LOW); digitalWrite(MotorBip1,LOW); digitalWrite(MotorBip2,HIGH);
analogWrite (enA,100); analogWrite (enB, 50);
delay (100);
}
elseif(digitalRead(IR1)==HIGH&& digitalRead(IR2)==LOW)
{
//The below code would help to tilt robot towards right by stopping the right wheel and moving the left one digitalWrite(MotorAip1,LOW);
// If I want to turn right then the speed of the right wheel should be less than that of the left wheel, here, let a be the right wheel
digitalWrite(MotorAip2,HIGH); digitalWrite(MotorBip1,HIGH); digitalWrite(MotorBip2,LOW); analogWrite (enA, 50);
analogWrite (enB, 100);
delay (100);
}
else
{
//Stop both Motors digitalWrite(MotorAip1,LOW); digitalWrite(MotorAip2,LOW); digitalWrite(MotorBip1,LOW); digitalWrite(MotorBip2,LOW); analogWrite (enA, 0);
analogWrite (enB, 0);
}
{
Serial.print("IR SENSOR (OBSTACLE)");
Serial.println(digitalRead(7)); if(digitalRead(7)==0)
{
digitalWrite(13,HIGH); //The buzzer which is connected to the 13th pin produces an alarm
}
else
{
digitalWrite(13,LOW);
}
}
}
-
-
HARDWRE MODULE SETUP
obstacle is removed. Since we use Arduino, we can alter the programming if needed without much time consumption.
-
Disadvantages
It can only travel along black over white line (vice versa). Since IR sensors is used Obstacle detection AGV cannot be used under sunlight as the sunlight might interfere with IR radiation.
-
Future Scope
-
In future, Obstacle detection AGV can be made to integrate with an arm as a result it can be used to transport light weighted objects like plastic, paper etc.,
-
We can also program our AGV in such a way where it decides its own path which through further development of the model can be used in destructed areas to select a safer path for the rescue team
VI. CONCLUSION
In this project we have developed a real time model that can automatically move along the path by detecting the obstacle on its path. Obstacle detection AGV senses obstacle in the path, detects it and resumes running once the obstacle is removed. In future, Obstacle detection AGV can be made to integrate with an arm as a result it can be used to transport light weighted objects like plastic, paper etc We can also program our AGV in such a way where it decides its own path which through further development of the model can be used in destructed areas to select a safer path for the rescue team.
REFERENCES
A. Advantages
-
-
DISCUSSION
-
It is light weighted. Obstacle detection AGV senses obstacle in the path, detects it and resumes running once the