
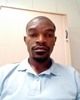
- Open Access
- [post-views]
- Authors : Josua K Junias, Fillemon N Nangolo, Petrina T Johannes
- Paper ID : IJERTV12IS070125
- Volume & Issue : Volume 12, Issue 07 (July 2023)
- Published (First Online): 12-10-2023
- ISSN (Online) : 2278-0181
- Publisher Name : IJERT
- License:
This work is licensed under a Creative Commons Attribution 4.0 International License
Effects of Ageing Suspension Components of Heavy Vehicle on Vertical Displacement Dynamic Response
Josua K Junias*
Department of Mechanical and Metallurgical Engineering University of Namibia (UNAM)
Ongwediva, Namibia
Fillemon N Nangolo
School of Mechanical, Industrial and Electrical Engineering Namibia University of Science and Technology (NUST) Windhoek, Namibia
Petrina T Johannes
Department of Civil and Mining Engineering University of Namibia Ongwediva, Namibia
AbstractThe usage of ageing suspension leaf springs and deflated tires can impact the dynamic response of heavy vehicles, often due to inadequate maintenance or delayed tire repairs. This can negatively affect ride comfort and cause damage to the pavement. To better understand this issue, a study was conducted to investigate the effects of using ageing suspension components and deflated tires on the vertical vibration of translating heavy vehicles under asymmetrical loading configurations and wheels eccentric kinematic excitations. The study used SIMWISE 4D to create virtual 3D 24 DOF translating heavy vehicle models with varying loading configurations and kinematic excitations. The models were analyzed to compare their vertical displacement dynamic responses at a specified vehicle speed, pothole depth, and diminished leaf springs and tire suspension properties. The results showed that the displacements and orientations of the sprung mass center of mass were shifted by asymmetric loading and the use of ageing suspensions, both in static and dynamic conditions. This indicates the importance of the distribution of elastic and dissipative properties on the vehicle suspension and their influence on vehicle motion responses in the presence of asymmetrical kinematic excitations and loading configurations.
Keywords eccentricities; general asymmetries; vertical dynamic response; heavy vehicles; ageing suspension
-
INTRODUCTION
Recent literature has focused on improving the comfort of vehicle rides by studying fundamental vibration models, which are widely used today. However, most of these studies have only considered symmetrical cases of vehicle vibration caused by factors such as uneven road profiles or impact loads on the vehicle. Asymmetrical cases, such as those caused by combined loading configurations and kinematic excitations, are rarely investigated. Additionally, the effects of aging suspensions or driving on deflated tires on vehicle vibrations are often not studied. Therefore, it could be argued that an uneven distribution of elastic and dissipative properties due to localized aging suspension and deflated tires, along with eccentric vehicle loading and wheel kinematic excitation, could
affect vertical vehicle vibration. Researchers, including [1], have identified wheel time flow as a key factor in general asymmetry, which can be categorized into cases such as sprung mass distribution asymmetries, road surface unevenness, and distribution of elastic and dissipative properties. These cases often occur together, especially on less regulated aging routes traveled by older vehicles. This study aims to investigate the combined outcomes of these factors, which can have negative effects on both vehicles and pavement structures, to gain a better understanding of vibration issues in transportation systems.
Many researchers have recognized the issue of overloading on heavy vehicles, but some have overlooked the nature of the overloading or how the loads are distributed on the vehicles. When a system is symmetrically overloaded, it may have less impact on pavement deterioration. However, when the loading is eccentric or excessive, it can significantly affect the dynamic response of the pavement and amplify damage, particularly around large cracks or deep potholes. Along the longitudinal axis, a vehicle is only symmetrically loaded if the load is evenly distributed across all axles, as shown in Figure 1.
Figure 1: Transverse Axes Asymmetric Loading (Incorrect position) Versus Symmetric Loading (Correct position) [2]
Figure 2: Longitudinal Axes Eccentric Loading (incorrect) Versus Symmetric Loading (Correct) [2]
In addition, a heavy vehicle can also have an asymmetric load distribution along the transverse axis, where the loads are concentrated on one wheel set and not evenly distributed across the center of the axle configuration, as shown in Figure 2. Both cases of asymmetrical loading shown in the illustrations can change the center of mass of the heavy vehicle and impact its vertical and rotational dynamic responses. This research will examine these effects as well as the impact of eccentric kinematic excitations on the wheel, vehicle translation, and the effects of aging suspensions and/or driving on deflated tires.
-
REVISED LITERATURE
There exist literatures that examined the effect that a change on a set composed by vehicles inertial, elastic and dissipative parameters has on the ride comfort of a driver as conducted by [3]. They have analyzed the ride comfort of the driver in terms of exposition to vibrations induced by the road unevenness to the vehicle body. Their findings and approach are important in determining the vehicle vertical vibration responses due to changes in relative parameters. Most importantly, the determination of the vertical dynamic responses of a certain point on a mechanical model due to these changes in vibration parameters could determine the influential aging suspensions and or driving on deflated tires effects on the overall vehicle body vibration. In particular, among other researchers, [4] had also proposed a method on rails to determine arbitral points vertical displacements. Their research proposed model allows solving various vibration tasks for model of vehicle with higher degree of freedom. It allows analyzing the effect of the input values, e.g. body geometry and its support, properties of springs and dumping, mass distribution, track imperfection; it is simplifying analysis of the resulting motion, including frequency analysis.
The tyre-pavement interactions also relatively contribute to the overall dynamic vehicle body responses. This is as outlined by several researchers including [5], [6] [7], [8] and [9], who had evaluated the interactions of the tire and the pavement during free rolling of the vehicle and several other drive conditions to understand the nature of forces imposed on to the pavements from the suspended sprung mass. On the same aspects, [6] had virtually tested the pothole impacts onto the vehicle tyre among other factors, an investigation in which they had revealed the effect of potholes to the lumped and unlumped mass of the systems under analysis. Even though they had not investigated the effect of aging suspensions and only indicated the post negative effects of tire-pothole interactions (that leads to damaged rims hence deflates the tires), their conclusions
basically imply that, despite the neglected loading configurations investigation, potholes on pavements does influence the vertical displacement, velocity and acceleration dynamic responses of the vehicle body. This is the case as [6] presented a wheel pothole impact test in which the vehicle is travelling at varying speed as the tyre engages with the pothole was presented. In these cases, the tyre was observed to lose contact with the ground and as a counter effect, at acceleration much greater than that due to gravity (g = 9.81 m/s2), the unsprung mass was forced downward by the suspension spring. This effect adds on to the gravitational acceleration acting on the center gravity of the sprung-unsprug mass systems. Most importantly, as the tire drops in the pothole, the vehicle is no longer in level, and the weight begins to shift more severely over the tire [6].
For pavement induced kinematic excitations, eccentric load and elastic and dissipative properties distribution effects on vehicle body vibration analysis, a vehicle can be models as a 1- dimensional, 2-dimensional or 3-dimensional model, whereby the simplest pavement-vehicle models have been considered to be those that are of 1-dimensional, 1 DOF so-called quarter car models or as complex as multiple DOF systems models wherein multiple wheels are considered, with static loads due to the car-body and suspension-body representing the static nature of forces from wheels, where the wheel-pavement contact is maintained by the linear or non-linear spring systems. 2DOF mass-damper spring models have been modelled in most studies including that of [10] to permit dynamic coupling between several lumped masses on a study. Overall, quarter-car virtual and mathematical models have been accepted as the fundamental mean of validating vibration studies hence applied in several research works models, a concept whereby, on 2 DOF systems, pavement deterioration post effects (potholes and random unevenness) onto mechanical systems mathematical formulations for vibration studies has been applied on them to analyses the most assumed symmetrical kinematic excitations on the vehicle wheels. There exist a few studies, such as that of [11], [12] and [13] on general vehicle vibration that uses mathematical functions as kinematic excitations onto the above-mentioned model wheels. Their approach is fundamental on understanding potholes modelling hence their model can be used in the evaluation of vehicle behavior (wheel loads on pavements) especially in conditions wherein, at constant speed, it has run into a distress factor (pothole) on a pavement surface.
Half and full vehicle single or multi directional models have also been developed in recent studies. Reference [3] used a full vehicle three-dimensional model, that consists of a sprung mass (vehicle body) connected to an independent suspension carried by the axles and wheels unsprung masses which are in contact with the road, with seven 7 DOF to analyses the driver positions vertical vibration when the vehicle is excited by the road. Even though they had only studied the effects of inertial, dissipative and rigidity properties of the heavy vehicle sprung and unsprung masses on the ride comfort, it could also be useful in determining the inertial influence of asymmetric loading in the presence of wheels kinematic excitations for a specified reduction in suspension properties of both the wheels and leaf springs.
This is worth noting as, even though there exist different vehicle models of several complexities and DOF that are meant to simulate the vehicles dynamics, they all falls under the two main categories as per approach used to model the system namely; (a)multi-body models that consider the detailed individual rigid bodies that connect with one another kinetically or dynamically to form a detailed assembly equivalent to the entire vehicle system while the (b)lumped- mass vehicle models only consider different parts of the vehicle to be lumped masses, as of an example, the vehicle bodies and wheel sets [14]. The asymmetrical track-vehicle dynamic system was presented in [15] study to consist of an adaptive wheel-rail contact onto two rails and a 10 DOF vehicle model. For the models wheels and rail defects, they had obtained all the time histories for most of the components simultaneously. This indicates that multi-directional and multi-degree of freedom models could study the interactive effects of an individual dynamic responses to the other components. It is therefore based on their findings that an argument can be made that most of the mathematic and or virtual models established tend to not consider the interactive influence of unsprung masses onto the sprung masses or other adjacent wheels due to the approach adopted of modelling the unsprung mass as composed of individual mass-damper spring sub-models.
Suspensions properties, especially the leaf or air springs mechanical properties, influences the dynamics response of the suspended mass for a specified sprung mass loading configuration. This case has been also investigated by most researchers including [16] who have conducted several studies on analyzing the suspension kinematics by means of mathematical, virtual and physical models in order to fully understand and define this problem using quarter car models. Their approach is influential in that it provides the basic principles of suspension kinematics even though they tend to have assumed symmetrical loading and excitation conditions only. Based on these judgments, [17] had established simplified equivalent mechanical springs model for the elliptic leaf spring that can be incorporated in virtual 3D models to mechanically represent the suspension system of the simplified modelled vehicles. What this reveal is the realistic motion response of the leaf spring in addition to its load carrying capabilities while ensuring the stability of these models. These leaf spring models are employed in this study.
Narrowing the scope, even though additional system damping effects are due to interactions of leaf springs elements, the leaf springs ability to absorb potential energy diminishes with time due to several factors such as deflections of leaf springs which leads to spring blades sliding against each other, cracks and fracture in the leaves and the presence of moisture in between leaf blades which causes fatigue in the leaf spring blades. These factors have an impact on the vibration response of most vehicles as they weaken the leaf springs causing the vehicle axle to wrap, a situation wherein the axle twists back and forth. Further, improper maintenance practices such as only replacing an old damper or leaf spring set or blade (leave) also contribute to the harmful vibration responses which in turns have a direct effect onto pavements deteriorations. When the vehicle is loaded in any configurations, a fatigued leaf spring blade may seem to have
diminishing leaf curvature as compared to its initial curvature when it is new, this could imply a slight increase in its stiffness properties because when it is loaded, it seems to straighten less, transmitting most of the shock loads to the suspended system. It is weakened and a slight to significant reduction in the stiffness properties may be observed. Additionally, the shape restoration was less which could mean that the damping properties has also slightly decreased. The diminishing effects could be modelled by modifying the damping and stiffness properties of the affected leaf spring in the models, accordingly.
-
STUDY MODEL DEFINITION
The study established a 3-axle mass-damper spring 3D 24 DOF vehicle model (including a tandem drive rear axle) to evaluate the combined effect of driving on deflated tires and aging leaf springs under known eccentric loading and kinematic excitations at various speeds and pavement distress factors (pothole depth). The study analyzed only the vertical vibration and relative rotational dynamic responses of the contributing elements in great detail. Several models were developed to account for possible cases of general asymmetric loading, including: (a) both loads having their longitudinal axes collinear and overall mass concentrated at about the loading bed center, (b) both loadings along the longest edge of the loading bed, (c) both loadings at the back of the vehicle, (d) one loading at the back left (or right) corner while the other located towards the front right (or left) corner of the loading bed, and (e) all the loadings located towards the back left (or right) corner of the loading platform. The study also considered different kinematic excitations, such as (I) all wheels encountering the potholes at the same time, (II) all the left (or right) wheels encountering the pothoes at the same time, (III) all the back wheels encountering potholes at the same time,
(IV) the front right (or left), back front left (or right), back back right (or left) wheels encountering potholes at the same time, and (V) only the front left (or right) and back front left (or right) wheels encountering potholes at the same time. Two of these eccentric configurations comprised the primary normal model, which was defined by no aging leaf spring and deflated tire, in comparison to the defective primary model consisting of at least one, either the front axle leaf springs or rear axle leaf springs aging and one of the wheels deflated. Specifically, these defects were defined by a 5% reduction of the leaf and tire dissipative and elastic properties as defined by [18].
The researchers created 450 sub-models by categorizing variations in vehicle speed and pothole depths for both normal and defective primary models. To narrow down the models for analysis, they used a non-probability sampling approach to select load configurations A, B, and E, and kinematic excitations I, III, and V that had the most impact on the system's vertical dynamic response. The selected models were then divided into three categories based on vehicle speed and pavement distress factor, resulting in a sub-population of 75 models. From this, 27 models were thoroughly analyzed in the study. The mathematical description of potholes used in this study is outlined in Table 1. The trajectory of the wheel as it hits a pothole of a specific depth is defined using a sine function, with the angular velocity determined by the ratio of
the vehicle's speed to the pothole depth and the vehicle's translational speed.
Table 1: Categorized Kinematic Excitation Forcing Functions [19]
Excitation
Excitation Function
25, 60
If(and(time>11.3 s, time<12.1 s), (25*Sin(2.4*time)), 0)
25, 80
If(and(time>11.0 s, time<11.6 s), (25*Sin(3.2*time)), 0)
50, 60
If(and(time>12.7 s, time<14.0 s), (50*Sin(1.2*time)), 0)
In this case, represent angular velocity (the rate at which the wheel seemingly respond to gain contact with the pavement during the pothole-wheel encounter before it impacts the opposite end wall of the pothole) defined by the ratio of the heavy vehicle speed to the pothole depth, with r the depth of the pothole (mm) and v, the truck speed (km/h). This is conducted to imitate the effect of wheels as they encounter the potholes at different speeds, these responses incorporate the rate at which the suspension tends to force the wheel downward to form contact with the ground [6]. They represent the time constrained sine wave whose trough of amplitude 25mm and 50mm are used to impose kinematic excitation on the unsprung mass hence the sprung mass whose data were analyzed.
The SIMWISE 4D was used to create a model of the 3-axle tandem drive heavy vehicle. This model had a lumped sprung mass that included the cabin, chassis, loading platform, and payloads. The unsprung masses were linked to the sprung mass by means of leaf springs, as described in [17]. The wheels were represented as linear springs that connected the tandem beam to the sections of pavement. Figures 3 and 4 illustrate this configuration.
Figure 3: 18 DOF Heavy Vehicle Pavement model (longitudinal axes) [19]
With reference to the front and rear axle, the center of mass (COM) is located by distance Lf and Lr, to enable an even heavy vehicle self-weight distribution.
Figure 4: 18 DOF Heavy Vehicle Pavement model (Transverse axes) [19]
The suspension system for the vehicle model shown in Figures 3 and 4 was defined using simulation parameters from a report by [18], as outlined in Table 2. The parameters included values for Ma and Mb, which represent the masses of the two loadings on the platform.
Table 2: Simulation Model Parameters [18]
Parameters Description
Parameter Values
Mass of the Truck (ms)
7200.0 kg
Truck Pitch moment of inertia (I)
100000.0 kgm2
Front tire and axle assembly mass (muf)
353.0 kg
Rear tire and axle assembly mass (mur)
653.0 kg
Front axle suspension stiffness (Ksf)
295.3 kN/m
Rear axle suspension stiffness (Ksr)
797.3 kN/m
Front axle suspension damping coefficient (Csf)
2.9 kNs/m
Rear axle suspension damping coefficient (Csr)
5.9 kNs/m
Front tire suspension stiffness (KTf)
1100.0 kN/m
Rear tire suspension stiffness (KTr)
2200.0 kN/m
Front tire suspension damping coefficient (CTf)
0.4 kNs/m
Rear tire suspension damping coefficient (CTr)
0.8 kNs/m
Distance from front axle to Center of Gravity (lf)
3.757 m
Distance from rear axle to Center of Gravity (lr)
2.441
-
RESULTS AND DISCUSSIONS
The purpose of this study was to investigate the effects of general asymmetries on pavement-vehicle interactions by studying the dynamic responses of virtual models that bridge the gap between existing classes of models. These models were designed to predict the vertical dynamic response of complex mechanical systems with aging suspensions and deflated tires in the presence of asymmetry loading and kinematic excitation. First, the study presents an investigation into the shifting and orientation of the COM static position, followed by an analysis of the control model vertical dynamic responses, which are compared to other models.
The study analyzed how much the COM shifted away from the origin due to the nature of the load configuration used in the models. Both models' COM shifted downwards with 24.1mm from the pre-defined origin (0, 0, 0) mm, due to the vehicle self-weight and the added effects of the two payloads. A 1% change in the vertical COM static displacement was noted, which could be attributed to the asymmetrical dissipative and elastic properties distribution on the defective study model. The study provides a foundation for further investigation into the effects of general asymmetries on pavement-vehicle interactions.
Table 3: Chassis Static Equilibrium Position (COM) [19]
Loading Configuration
X (mm)
Y (mm)
Z (mm)
A
Normal
-0.198
-24.1
0.00148
Defective
-0.26
-24.09
0.286
B
Normal
-0.208
-24.2
5.19
Defective
-0.273
-24.6
5.61
E
Normal
-0.775
-23.4
2.59
Defective
-0.854
-23.7
2.99
Table 3 shows that the longitudinal eccentric loading configuration, which involves loading on one back corner of the loading platform, causes a slightly lower COM downward shift of 2.49% compared to the COM shift for models loaded with payloads along the longest edge of the loading bed and 2.90% lower than that of the control model, with a shift of 23.4mm. The E loading configuration showed a high COM shift along the longitudinal axes (x-axis) compared to the other two loading configuraions. On defective models, significant lateral and longitudinal static displacements were observed in all the load configurations. This suggests that eccentric loading configurations not only shift the COM significantly along the lateral and longitudinal directions but also relatively shift it downward less than symmetrical loading configurations. The same relative effect was observed in the defective models. Table 4 indicates the rotational displacement of the models from the initial orientation conditions (0, 0, 0) degrees, measured from the vertical, longitudinal, and transverse principal axis lines passing through the COM.
Table 4: Chassis Static Equilibrium Orientation [19]
Loading Configuration
Rx (Deg)
Ry (Deg)
Rz (Deg)
A
Normal
-0.0015
0.000185
0.0216
Defective
0.0549
-2.8E-6
0.029
B
Normal
0.969
0.00268
0.0226
Defective
1.05
0.00273
0.0313
E
Normal
0.484
0.00173
0.0862
Defective
0.559
0.0019
0.0939
The control loading factor (A loading configuration) demonstrated a sustained normal model static orientation, indicating that symmetrical loading configurations do not significantly impact the orientations about the vertical, longitudinal, and lateral axes. Although the A and B configured
loading models had near-similar static orientation about the lateral axis, significant differences were observed between the B and E loaded models about the vertical and longitudinal axes as compared to the control loading configuration. This difference could be attributed to the load distribution on the loading platform. When the payloads were distributed towards the back corners of the HV loading platforms, the COM was slightly lowered vertically and shifted backwards along the longitudinal axis, resulting in a significant orientation of the chassis about the transverse principal axes with moderate orientations observable about the transverse axes.
The two systems show similar behavior with regards to insignificant orientations about the vertical axis. However, the models loaded using the B loading configuration (loading them along the long edge of the loading platform parallel to the longitudinal axes) exhibit higher orientations about the longitudinal axes due to the eccentric load distribution towards the long edge of the loading platform. This results in a 5.19mm shift of the COM along the transverse axes compared to the control model, and 50% more than the E load configured HV chassis. A reduction of 5% on the right leaf spring and tire elastic and dissipative properties caused a significant static orientation of the sprung mass about the longitudinal axes for the A and B load configurations, but not for the E loading configuration. All defective models loading configurations exhibited insignificant orientation about the Y-axis, while the B and E loading configurations showed significant orientation about the transverse axes compared to the normal models' static orientations.
To analyze the effects of aging leaf springs on the left rear axle and a deflated back front right tire, the vertical dynamic responses of the models were overlaid and compared to the normal model's vertical dynamic responses using the control model as the reference model. The control model exhibited moderate amplitudes of the heavy vehicle chassis COM vertical displacement in response to harmonic motions between
-
seconds and 12.1 seconds. The displacement decayed for a period of 5 seconds to its static equilibrium position after interacting with potholes of depth 25mm. The control model had characteristics of an underdamped system with a high damping ratio of about 0.0033, which is 5% different from the validating quarter car model sprung mass vertical dynamic response in [11] and the corresponding study by [12].
In addition, as illustrated in Figure 5, a significant downward shift of the COM occurred during the interaction between the wheels and the pothole. This is because when both wheels hit the 25mm pothole, the sprung mass accelerates downwards, which is offset by the upward response of the unsprung mass as the wheels make contact with the opposite side of the pothole wall. Consequently, a high-amplitude dynamic response is noticeable during the period when the wheels interact with the pothole. When compared to the defective model with the same loading configuration and kinematic excitation category (Defective control model), a similar type of vertical dynamic response was observed but at a slightly lower position than that of the normal control model.
This could be mainly due to the distribution of the sprung mass to which the sprung mass is suspended.
Figure 5: Normal Control Model Versus Defective Control Model(Defective AIw25-60) Sprung Mass Vertical Dynamic Response
In spite of having the same loading configurations and damping effects, it was found that the AIw25-80 defective model showed a minor increase in its vertical dynamic response at higher vehicle speeds, but a significant response during the wheel-pothole interaction period, as depicted in Figure 6. The primary reason for this dynamic response is the unsprung mass vertical dynamic response, mainly due to the right walking beam rotational dynamics response about the spindle.
Figure 6: Normal Control Model Versus Defective AIw25-80 Sprung Mass Vertical Dynamic Response
Interestingly, when the pothole depth increased from 25mm to 50mm at the same vehicle speed of 60km/h, the vertical dynamic responses of both the defective AIw50-60 and normal control model (AIw25-60) were similar throughout the study period, as shown in Figure 7.
Figure 7: Normal Control Model Versus Defective AIw50-60 Sprung Mass Vertical Dynamic Response
The comparable vertical dynamic response of the defective AIw50-60 and normal AIw25-60 models shown in Figure 7 can be attributed to the symmetrical loading and damping effects of the suspension system. Despite the eccentric distribution of elastic and dissipative properties about the x- axis, the suspension system evenly distributes the load.
In order to evaluate how the vertical vibration of the sprung mass is affected by aging leaf springs and a deflated tire under loading configuration E at a speed of 60km/h and a pothole depth of 25mm, the vertical dynamic response of the normal model was superimposed in Figure 8, while the vertical dynamic responses of the defective models were superimposed in Figure 9. The control model (Normal AIw25060) was used as the reference model in both cases.
Figure 8: Normal Control Model Versus Normal E(I,III,V)w25-60 Models Sprung Mass Vertical Dynamic Response
Figure 9: Normal Control Model Versus Defective E(I,III,V)w25-60 Models Sprung Mass Vertical Dynamic Response
For all the kinematic excitations on both the normal and defective models, the vertical harmonic response with diminished amplitudes as compared to the control model are noted with the V kinematic excitation indicating very low amplitudes. The relatively low response amplitudes could be mainly due to the distribution of the load, as in this case, the load is concentrated at the side having reduced elastic and dissipative properties. Further, the V as well as the III kinematic excitations tends to have a dominant rotational dynamic response other than the vertical COM displacements mainly due to their nature of kinematically exciting the study models wheels; (a) the V kinematic excitations tends to rotate the walking beam about the pindle central transverse axis hence slightly lowering the real spindle as it rotates about its central longitudinal axes while the front spindle dynamically rotates about the longitudinal axes in response to the kinematic excitation on the front left wheel only, while (b) the III kinematic excitation tends to lower the rear axle evenly hence orients the sprung mass about the transverse axes as it slightly lowers in response to the kinematic excitation.
Figure 10: Normal Control Model Versus AIw25-80 Versus Normal B(I,III,V)w25-80 Models Sprung Mass Vertical Dynamic Response
Figure 11: Normal Control Model Versus Defective AIw25-80 Versus Defective B(I,III,V)w25-80 Models Sprung Mass Vertical Dynamic Response
In general, the vertical dynamic response of the models when encountering potholes is lower than the effects of the I kinematic excitation. For the B load configured models, their responses are mostly similar in phase after encountering potholes for all kinematic excitations, except for the I kinematic excitation on the asymmetrically loaded defective models. In this case, there is a dominant vertical dynamic response, influenced by the rotational dynamic response of the walking beam about the spindle central axis and the interaction rotational dynamic response of the spindle about the longitudinal axes. This is reflected in the chassis COM static displacements and orientations tables.
For the normal models, the III and V kinematic excitation have similar effects on the vertical dynamic response of the sprung masses. The location of the center of mass, which is relatively towards the back of the model, induces both static and dynamic rotational responses of the sprung mass. Therefore, for the same pothole depth, the III kinematic excitation mainly influences the rotational dynamic responses rather than the vertical dynamic responses. On the other hand, the V kinematic excitation's effects on the vertical dynamic responses are influenced by the location of the payloads' distribution, as in the case of the B loading configuration. The defective suspension properties are also noticeable in Figure 9 and 11, specifically for the V kinematic excitation.
These results are consistent with the time progression of the wheel's behavior and its impact on the overall asymmetrical effects, as discussed by [1]. Additionally, the uneven distribution of elastic and dissipative properties in the vehicle affects its vertical dynamic response, especially in the case of eccentric loading configurations with a defined eccentric wheel time flow history. Furthermore, through time-domain analysis of the systems' sprung mass vertical dynamic responses, it is apparent that aging suspensions and differences in tire inflation result in uneven load distribution between tires on both axles, ultimately influencing the study models' vertical and rotational dynamic responses.
[4] J. Soukup, J. Skoilas and B. Skoilasová, "Vertical vibration of the vehicle model with higher degree of freedom," Modelling of Mechanical and Mechatronic Systems MMaMS 2014(ScienceDirect) , pp. 435-443, 2014.
[5] A. Vaitkus, J. Graulyt and K. Rita, "Influence of Static and Impact Load on Pavement Performance," in The 9th International Conference Evironmental Engineering, 2014.
[6] B. K. Mohammed, C. Guilherme and R. Rena, "Simulation of Vehicle Pothole Test and Techniques Used," SAE Technical Paper, 2015.
[7] G. Minrui and Z. Xinglin, "Tire-Pavement Contact Stress Characteristics and Critical Slip Ration at Multiple Working Conditions.," HINDAWI, 2019.
[8] H. Haiqi, L. Rui, Y. Qihui, P. Jianzhong and F. Guo, "Analysis of the Tire-Pavement Contact Stress Characteristics during Vehicle Maneuvering," KSCE Journal of Civil Engineering, pp. 2451-2463, 2021.
[9] L. Jiao, "Vehicle model for tyre-ground contact nature of forces evaluation.," Department of Aeronautical and Vehicle Engineering TKH Royal Institute of Technology, Stockholm, 2013.
[10] G. Bonin, G. Cantisani, G. Loprencipe and A. Ranzo, "Modelling of dynamic phenomena in road and airport pavements," Dipartimento di Idraulica, Transporti e Strade (DITS)-Universita degli Studi di Roma, Roma, 2004.
[11] R. Mahmoud and B. Atanu, "Passive Suspension Modelling and Analysis of a Full -Car Model," International Journal of Advanced Science and Engineering Technology, pp. 250-261, 2013.
[12] A. B. Kunya and A. A. Ata, "Half Car Suspension System Integrated with PID Controller," in Proceedings 29th European Conference on Modelling and Simulation ©ECM, 2015.
[13] F. N. Nangolo, "Analytical Extraction of Modal Parameters of Damped Mechanical Systems," in International Multi-Topic Conference on Engineering and Science (IMCES), 2019.
[14] F. M. Soong, R. Ramli and A. Saifizul, "Between Simplicity and Accuracy: Effect of Adding modelling details on quater vehicle model accuracy.," Kuala Lumpur, : Advanced Computational and Applied mechanics(ACAM) research Group, Department of Mechanical Engineering, University of Malaya , Malaysia, 2017.
[15] K. Hou, J. Kalousek and R. Dong, "A dynamic model for an asymmetrical vehicle/track system," Journal of Sound and Vibration, pp. 591-604, 2003.
[16] D. Crolla and Y. Fan, "Vehicle Dynamics and Control (Based on a lecture notes of University of Leeds)," People's Communication Press, Leeds, 2004.
[17] B. Mike and H. Damian, "Modelling and Assembly of the Full Vehicle: Modelling Leaf Springs," in The Multibody Systems Approach to Vehicle Dynamics (Second Edition), 2015.
[18] V. Muluka, "Optimal Suspension Damping and Axle Vibration Absorber for Reduction of Dynamic Tire Loads," Bell & Howell Information and Learning, Canada, 1998.
[19] J. K. Junias, F. N. Nangolo and P. T. Johannes, "Investigating the Effects of General Asymmetries on Heavy Vehicles Vertical Displacement Dynamic Responses," Manuscript in preparation, 2022.
-
-
CONCLUSION AND RECOMMENDATIONS
In summary, a validated model was created to investigate the effects of asymmetric loading on the vertical vibration of sprung masses under eccentric kinematic excitations and elastic and dissipative properties distributions. It was noted that;
-
Eccentric loading configurations not only shift the center of mass significantly but also shift it downward relatively less as compared to symmetrical loading configurations.
-
Aging leaf springs can induce static orientation about longitudinal and transverse axes in certain load configurations.
-
The V kinematic excitations induce less vertical dynamic response with low response amplitudes and the same decaying time in all models observed.
-
The four basic asymmetry cases have a significant influence on the vertical dynamic response of the sprung mass.
-
Finally, aging suspensions and tire inflation differences cause unequal load sharing between tires on both axles, which affects the vertical and rotational dynamic responses of the study models.
It is suggested that an examination be carried out to determine the impact of altering the payload weight on the suspension system properties described in the models, to assess the models' responses to increased inertial effects. Additionaly, a more comprehensive multi-directional 24 DOF mathematical model should be created to verify the results of these models. To gain further insight into the responses of defective models compared to control models, additional analysis should be performed by relocating the defective suspension properties to any other possible location on the models to draw further conclusions from these models.
ACKNOWLEDGMENT
The assistance provided by the staff members in the Mechanical and Metallurgical Department of the University of Namibia is greatly appreciated. The support provided by this research works supervisors is extremely appreciated. This work forms part of a Master study undertaken at the University of Namibia.
REFERENCES
[1] J. Soukup and J. Volek, Vibration of Mechanical System, Ústà nad Labem (ISBN 978-80-7414-020-4), 2008. [2] "Heavy rigid vehicle stability and dynamics," WAKA Kotahi NZ Transport Agency, [Online]. Available: https://www.nzta.govt.nz/resources/heavy-learner/heavy-rigid- vehicles/4.html. [Accessed 15 September 2022]. [3] L. Muñoz and A. Polanco, "Effect of the change of inertial, elastic and dissipative parameters on the ride comfort of a road vehicle. ResearchGate," ResearchGate, 2013.