
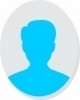
- Open Access
- Authors : Mani Shankar Anand, Eswara Babu A
- Paper ID : IJERTV12IS100108
- Volume & Issue : Volume 12, Issue 10 (October 2023)
- Published (First Online): 18-11-2023
- ISSN (Online) : 2278-0181
- Publisher Name : IJERT
- License:
This work is licensed under a Creative Commons Attribution 4.0 International License
Design and Development of servo system for Doppler Weather Radar
Mani Shankar Anand[1], Eswara Babu A[2]
D&E-RS/NS2, Bharat Electronics Limited, Bangalore, India
AbstractDoppler Weather Radar (DWR) servo system plays a vital role in the Antenna positioning mechanism to transmit or receive signals without deviations from the desired position in different modes of operation as per selected scan strategy.
For scan types of DWR systems, especially for antenna angular positioning, 25-bit high precision encoder is required in the design which meets the accuracy requirement of angular positioning and uniform rotation. The required controller algorithm is developed, synthesized, simulated and implemented on customized FPGA (XC4VFX20) board. The experimental results show that, antenna is able to achieve the desired velocity and position with respect to input command receives from Radar Controller.
This paper describes the Field Programmable Gate Arrays (FPGA) based servo controller hardware design and software algorithm to control the velocity and position of the antenna in both azimuth and elevation axes in different modes of operation for Doppler Weather Radar.
KeywordsDoppler Weather Radar, Absolute Encoder, FPGA, Servo System, Amplifier, Motor
-
INTRODUCTION
Doppler Weather Radar (DWR) system is meant for long- range weather surveillance and is capable of detecting and estimating the parameters of cyclone and other severe weather conditions like rainfall, air temperature etc. so that necessary preventive steps can be taken to alleviate the impact of such natural disaster in terms of loss of life and property. India Metrological Department (IMD) is the nodal agency for weather service in India. IMD operates a chain of conventional weather radars along the peninsular coastline for the cyclone detection and characterization of severe weathers. This chain of Cyclone Detection Radar (CDR) system is now replaced with Pulse Doppler Radar systems known as Doppler Weather Radar [1]. Pulse Doppler techniques are used to characterize severe weather condition for better accuracy. By studying the characteristics of the radar returns (or power received), and analyzing the variations in their amplitude phase or frequency shift or the change in the
polarization states, radar quantify the different characteristics of the precipitating medium within the
pulse volume [2]. It basically estimates the three base products, reflectivity, Mean Velocity and Spectral Width, which are essential to measure various primary and secondary data products like Radial Velocity, Echo Base, Echo Top, Rain fall intensity, precipitation accumulation etc. are generated to meet different hydro- meteorological applications like flood forecasting [3] [4] [5].
Doppler Weather Radar can be operated in various frequency bands such as W, K, X, C, S and L based on the requirements. In this paper, S-Band DWR servo system is considered for analysis and implementation. The Servo Control System is designed to interface with 2 servo drives of azimuth and elevation system. It takes care of motion control, modes of operation, Status, Interlock, Control Signal Generation and Interface to Radar Controller (RC) from which it takes user commands and sends over all status of the DWR for user to monitor and logging purpose. It is used to position the DWR antenna in both azimuth and elevation axes in different modes of operation. The antenna pedestal is elevation over azimuth type. Generally, a DWR system is depicted as shown in Figure 1 with Radome covered.
Figure 1: DWR Antenna with Pedestal
-
SYSTEM DESCRIPTION
The servo system of Doppler Weather Radar is required to position the antenna in both azimuth and elevation axes in different modes of operation as per the requirements. The antenna is elevation over azimuth type of pedestal. For continuous rotation of antenna pedestal, a slip ring unit is provided for continuous connectivity of elevation servomotor to amplifier, elevation angle data sensing through absolute shaft encoder and limit switches. The antenna is driven in azimuth and elevation axes through individual gearboxes. The servomotors used in both azimuth and elevation channels are brush-less servomotors, for maintenance free operation of the radar, which is required to operate round the clock. These motors have fail-safe brake with over temperature contact. The servomotors in azimuth and elevation channels will be connected to the respective servo amplifiers for both drivelines and the motors in-built resolver outputs. Also, the built-in brake lines and over temperature contact lines are used by interlock circuitry. The Servo System consists of Servo Rack and Drive Motors to drive the antenna in Azimuth and Elevation. The Servo System provides facility to locally control the antenna, as well as providing a local display to indicate the status such as current position of the antenna, desired position of the antenna, error, status of tell-backs/inter-locks, operating mode etc.
-
Servo System Description
Figure 2 shows Servo System Block Diagram design and developed for S-DWR.
Figure 2: Servo System Block Diagram
The 400V, 3-phase supply is fed to the Isolation Transformer through line filters and Molded Case Circuit Breaker (MCCB). Output of transformer is fed to the Servo Amplifiers through fuse and drive contactors. The 3 Phase indicator monitors the phase parameters, phase sequence, phase loss, over and under voltage and phase unbalance. In case of faults, it de-energizes the output relay. Only if all the phase parameters are correct, the drive ccontactors are energized.
The single-phase supply of 230V is fed to the Isolation Transformer through Miniature Circuit Breaker (MCB). The output of this transformer is fed to the 3 power supplies. Two power supplies generate 24v. One of which is fed to both the servo amplifiers (Azimuth and Elevation), other one to all interlock signals generation. The third power supply generates +5v, +3.3v, 15v to various LEDs and PCBs. The servo amplifiers outputs are fed to the motors (Azimuth and Elevation Motors) through choke boxes. The choke box is used to reduce velocity ripple and to protect the output stage of the amplifier. Based on the requirement (Operating Mode of the radar), the Controller PCB computes the velocities of the motors and feeds the same in analog format to the Servo Amplifiers. The servo amplifiers control the brush less synchronous servomotors through the choke box, with the closed loop control of torque, speed and position. The resolver output of motor is fed back to servo amplifier. The brakes in the motors can be controlled directly by the servo amplifier. During braking, with the aid of the motor, the energy is fed back to the servo amplifier. This energy is converted into heat in the regenerative resistor. The Azimuth and Elevation motor drives the antenna in Azimuth and Elevation axis through Gearboxes [6] [7].
The Servo System receives the commands from the Radar Controller (RC) units through a LAN and the LAN interface is provided in the Controller PCB. The status information of the servo system is provided to RC through LAN. The instantaneous position of the antenna (Azimuth and Elevation) is given by the respective encoders. The output of these encoders, which is in Endat2.2 format, is given to the Controller PCB, which in turn computes the velocities of the motors based on the errors. The various Interlock signals are also fed to the Controller PCB. The Controller PCB is connected to the Display/Keypad through a serial line. The Display is ued as a Local Display to display the status and operating mode. The Keypad is used to control the servo system in Local Mode. The Controller PCB also generates the 1 interrupt and Data Ready signals and these signals are given to the GSP and Transmitter units to provide the antenna current positions.
-
Servo System Specifications
Salient features of servo system are mentioned below:
-
Type of Pedestal: Elevation over Azimuth
-
Elevation Coverage : -2o to 90o
-
Azimuth Coverage : 0o to 360o
-
Velocity
Azimuth: up to 36o/sec (6 RPM) Elevation: up to 18o/sec (3 RPM)
-
Acceleration
Azimuth: 10o/sec2 Elevation: 10o/sec2
-
Pointing Accuracy: Better than 0.05°
-
Variation of velocity in Azimuth: Less than 0.01% of maximum velocity
-
Overshoot and Undershoot: Less than 0.50
-
Settling Time: Less than 1 sec.
-
Interlocks to protect antenna structure
-
Local/Remote Control features
-
Display to monitor real time system health status
-
-
-
CONTROL SYSTEM DESIGN
Controller PCB is the main controller of the servo system. It calculates velocity loop and position loop for both Azimuth and Elevation axis such that the servo control system can achieve optimum performance. The block diagram of servo controller card is as shown in Figure 4. Controller card receive the commands from RC with LAN interface (UDP protocol) and fed to FPGA through transceiver. It also read the azimuth and elevation encoder data through RS-485 interface to evaluate the current position of the antenna. The various interlock signals are implemented to protect the motors, antenna structure and personnel working at antenna. Controller card receive these interlock signals into FPGA through opto-coupler after voltage level conversion [8].
of operation. For volume scan mode, the signal is generated for every 1° of Azimuth rotation and for RHI mode, every 1° of elevation rotation. Data Ready signal is generated with respect to 1° interrupt signal which indicates validity / invalidity of data to Generation Simulation and Processing (GSP) unit and/or elevation angle transition time.
-
MODES OF OPERATION – S-DWR
DWR system modes of operation are discussed in the following paragraphs.
-
Volume Scan Mode
-
In volume scam mode, antenna operates in horizontal position for one or more elevations with full azimuth coverage.
-
Azimuth scan rate up to 36°/sec (6 RPM) in steps of 0.5°/sec with specified elevation angles (max 30 elevation)
-
Controller receives the volume header (VH) from RC which contains the information of selection of operation mode, azimuth scan rate (RPM) specified for each elevation, number of elevation (max 30 values) and start elevation angle.
-
After receiving VH, antenna reaches to desired start elevation angle and start azimuth rotation for full scan i.e. 360°
-
After completion of one full rotation (360°), antenna moves to next elevation angle and start rotation for full
ETHERNET SWITCH
LAN
LXT971
14 BIT
LC
Analog to Digital
conversion
From Servo Amplifiers
scan.
CLOCK
12 BIT
Az Az
LC
DAC AND MOTOR DRIVE CKT
TO Az
Servo Amplifier
-
Antenna follows the same pattern until it reaches to last
elevation angle.
DATA
25 Bit
FPGA
12 BIT DAC AND
TO Elv
CLOCK DATA
FROM Az & Elv ENCODERS
RS 485 level conversion 5V
LC
EL
25 Bit
ENCODED DATA
(Virtex-4: XC4VFX20)
EL
100MHz
Clock
100MHz
Clock
MOTOR
DRIVE CKT
Servo Amplifier
-
Figure 6 shows the waveforms generated in volume scan
mode and explain the antenna movement in azimuth and
5V
COMMAND OPTOCOUPLER
24V
LC LC LC
1 Degree Interrupt Radome Entry
elevation axis with different RPM and active period of
Data Ready and 1° Interrupt signal.
IGNALS
INTER LOCK SIGNALS
24V
OPTOCOUPLER
5V
S Data Ready
Serial Line
0
30
LCD DISPLAY
& KEYPAD
20
move to 2
0
move to 3
reach to 3 RPM
LC = Level Converter
10
3 RPM
move to 1
0
Figure 3: Controller Card Block Diagram
reach to 2 RPM
Based on the requirement (operating mode) and current position of the antenna, the FPGA computes the velocity of the Azimuth and Elevation motors. These velocity outputs (12 bits for Azimuth and 12 bits for Elevation) are passed through level converters; DACs and signal conditioning circuits to generate analog voltage of ±10V max. These analog voltages are fed to the Azimuth and Elevation Amplifiers. Amplifiers drive the motor as per incoming analog voltage of ± 10V.
LCD display and keyboard are connected to servo controller through RS-232 lines. The display provides the local display and also provides the facility to control servo system in local mode. The 1° interrupt signal is generated based on the mode
ELEVATION
2 RPM
2 RPM
3600
AZIMUTH
3600
3600
10 Interrupt
360 pulses
360 pulses
360 pulses
Data Ready
Fig 4: Volume Scan – Waveforms Pattern
-
-
-
-
Azimuth Sector Scan Mode
-
In Sector Scan mode, Antenna operate between specified azimuth angles at specified elevation step angles
-
Azimuth rate up to 36°/sec (6 RPM) in steps of 0.5°/sec
0
-
Antenna rotates from start azimuth angle to end azimuth angle (clockwise direction) at specified elevation angle
0
300 600 300 600 300 600
0
move to 3
0
-
After completion of first scan antenna moves to next desired elevation angle and it starts rotation from start azimuth angle to end azimuth angle (counter clockwise)
-
Fist scan end azimuth angle is same as second scan start azimuth angle
-
Antenna follow the same pattern until reaches to last
reach to 30
Elevation 30
move to 1
0
10
Azimuth
10 Interrupt
300
move to 2
0
20
3030
elevation angle
-
Figure 5 shows the waveforms generated in azimuth sector scan mode and explain the antenna movement in azimuth and elevation axis with different RPM and active
Data Ready
30 pulses 30 pulses 30 pulses
Fig 6: Elevation Sector Scan – Waveforms Pattern
period of Data Ready and 1° interrupt signal.
Azimuth return to 600
D. Position/Designation Mode
-
In Position Mode, Antenna goes to specified Azimuth and Elevation angles as per received command from RC
Azimuth
move to 30
0
300
2 RPM
50
600
600
60
300
-
In this mode, fixed 1° interrupt signal is generated as per required Dwell Time Period and Data Ready Signal is activated after reaching to specified AZ & EL position
reach to
-
Data Ready Signal will be ENABLE until controller
5
Elevation
30 steps 30 steps
0
receives EXIT command from RC
-
Figure 7 shows the waveforms generated in position scan mode and explain the antenna position in azimuth and
10 Interrupt
30 pulses 30 pulses
Data Ready
elevation axis and active priod of Data Ready and 1° interrupt signal.
Fig 5: Azimuth Sector Scan – Waveforms Pattern
-
-
-
-
Elevation Sector Scan/Range Height Indicator Mode
-
In RHI mode, Antenna operate between specified elevation angles at specified azimuth step angles
-
Elevation rate up to 18°/sec (3 RPM) in steps of 0.5°/sec
-
Antenna rotates from start elevation angle to end elevation angle at specified azimuth angle.
-
After completion of first scan antenna moves back to start elevation angle and the next desired azimuth angle
-
Fist scan start elevation angle is same as second scan start elevation angle
Elevation
Azimuth
10 Interrupt
Data Ready
30
0
300
reach to
reach to 6
0
0
600
100 ms
Fig 7: Position mode Scan – Waveforms Pattern
-
Antenna follow the same pattern until reaches to last azimuth angle
-
Figure 6 shows the waveforms generated in elevation sector scan mode and explain the antenna movement in azimuth and elevation axis with different RPM and active period of Data Ready and 1° interrupt signal.
-
-
GENERATION OF 1O INTERRUPT AND DATA
READY SIGNAL
A. 1° interrupt generation and implementation
The 1° interrupt signal is key parameter to know the current position of antenna and to control the antenna movement. It is generated based on the incoming encoder data from load and mode of operation. At every 1° crossovers, pulse is generated. Pulse width and time period of 1° interrupt signals are depending on the antenna speed (RPM). Pulse width and time period of antenna with respect to antenna speed (RPM) is explained in Figure 8.
1 Degree Interrupt (1 RPM)
1 Degree Interrupt (2 RPM)
1 Degree Interrupt (3 RPM)
1 Degree (1 RPM)
166.6 ms
166656.6 us
10 us
1 Degree (2 RPM)
83.3 ms
83323.3us
10 us
1 Degree (3 RPM)
51.5 ms
51545.5us
-
RESULTS
The following tests have been conducted with DWR system inside the BEL premises during trails.
-
Azimuth Motors Current for different Speed (RPM)
-
At 1 RPM Antenna Speed and 460 RPM Motor Speed
1 Degree Interrupt (4 RPM)
1 Degree Interrupt (5 RPM)
10 us
10 us
1 Degree (4 RPM)
41.6 ms
41656.6 us
1 Degree (5 RPM)
33.3 ms
33323.3us
-
At 2 RPM Antenna Speed and 920 RPM Motor Speed
1 Degree Interrupt (6 RPM)
10 us
1 Degree (6 RPM)
27.7 ms
27767.7us
10 us
Figure 8: 1° interrupts signal waveforms
-
-
Data Ready Signal
Data Ready Signal is key parameter for Radar system operation. It controls the actual Radar operation timing. As explained in above paragraphs Data Ready signal is generating based on mode of operation and 1° interrupt signal. In volume scan mode, the antenna rotation will not stop at each PPI scan. After one PPI Scan is completed, the elevation angle is incremented/decremented concurrently while antenna rotating in azimuth. Servo controller generates Data Ready signal which indicates validity /invalidity of radar data to other sub-system. As explained above, in volume scan mode operation, during transition period (when antenna shift to next elevation angle after completion of one full scan) data ready signal is inactive. Once it reaches to next elevation angle and achieves specified azimuth speed, Data Ready signal becomes active and it follows the same pattern for further scans. Following data ready waveforms indicating in Fig.9 describe the active/inactive time period with respect to antenna speed (RPM).
166.6 ms
Transition/
Change Over Time
166.6 ms
Data Ready (1 RPM)
83.3 ms
Data Ready (2 RPM)
Transition/
Change Over Time
83.3 ms
Data Ready (3 RPM)
51.5 ms
Transition/
Change Over Time
51.5 ms
Data Ready (4 RPM)
41.6 ms
Transition/
Change Over Time
41.6 ms
Data Ready (5 RPM)
33.3 ms
Transition/
Change Over Time
33.3 ms
27.7 ms
Transition/
Change Over Time
27.7 ms
Data Ready (6 RPM)
Figure 9: Data Ready signal waveforms
-
At 3 RPM Antenna Speed and 1380 RPM Motor Speed
-
At 4 RPM Antenna Speed and 1840 RPM Motor Speed
-
At 5 RPM Antenna Speed and 2300 RPM Motor Speed
-
At 6 RPM Antenna Speed and 2760 RPM Motor Speed
Summary of Motors Current v/s Speed
S. No
Antenna Speed (RPM)
Motor Speed (RPM)
Effective Current (Amp)
1
1
-461
0.982
2
2
-921
1.562
3
3
-1382
1.370
4
4
-1842
1.614
5
5
-2301
1.903
6
6
-2754
3.275
S.
No
Axis
Motor Speed (RPM)
Achieved Acceleration Rate
1
Azimuth
460
7.2°/sec2
2
920
8.1°/sec2
3
1382
8.5°/sec2
4
1842
9.1°/sec2
5
2301
9.5°/sec2
6
2754
9.9°/sec2
7
Elevation
250
7.5°/sec2
8
500
8.2°/sec2
9
1000
8.6°/sec2
10
1500
9.1°/sec2
11
2000
9.6°/sec2
12
2760
9.9°/sec2
Summary of Motors Acceleration Rate v/s Speed
Table 1. Motors Current v/s Speed
-
Measurement of Azimuth and Elevation Acceleration Rate (Step Response in Rate Loop)
-
Azimuth Acceleration
Speed response oscilloscope with Azimuth Amplifier speed command at 460 rpm
As shown in graph, Vcmd = 460 rpm, Time = 0.83s, Azimuth Motor Acceleration = (460/0.83)*6 = 3,325.3
°/sec2, Achieved Acceleration of motor = 3,325.3 °/sec2, Achieved Acceleration of Antenna = 3,325/460= 7.22°/sec2, As per configured settings, acceleration of antenna in AZ axis = 10°/sec2
-
Elevation Acceleration
Speed Response oscilloscope with Elevation Amplifier- speed command at 250 rpm
As shown in graph, Vcmd = 250 rpm, Time = 0.4s
Elevation Motor Acceleration = (250/0.4)*6 = 3,750°/sec2, Achieved Acceleration of motor = 3,750°/sec2, Achieved Acceleration of Antenna = 3,750/500= 7.5°/sec2, As per configured settings, acceleration of antenna in El axis = 10°/sec2
Table 2. Motors Acceleration Rate v/s Speed
-
-
Velocity Loop Test (Rise Time and Bandwidth)
Velocity loop test performed in both azimuth and elevation axis
-
Azimuth velocity loop test
Velocity loop test is performed at motor speed of 46 rpm
From the graph, following Rise Time and Bandwidth are achieved.
Rise Time = 574 m sec
Bandwidth = (0.35/0.57) = 0.6 Hz.
-
Elevation velocity loop test
-
Velocity loop test is performed at motor speed of 50 rpm
From the graph, following Rise Time and Bandwidth are achieved.
Rise Time = 110 m sec Bandwidth = (0.35/0.11) = 3 Hz.
-
-
CONCLUSION
In order to achieve the precision in the antenna positioning, the FPGA based servo controller is designed to control the antenna movement in azimuth and elevation axis in terms of 0.05° as tabulated in Table-2. For controller design, high-level modeling approach is used with VHDL platform. The advantage of FPGA based designs are reducing the design time, real time encoder data reading directly into FPGA, evaluation of the design functionality in a short time and quickly exploring of different design choices. Apart from Doppler Weather Radar, this design approach can be used for other antenna control systems where multiple axes control systems are required. Microcontroller or PLC based servo controllers having limitation of execution of parallel process and generation of narrow pulse width in the range of micro second. This limitation is easily overcome by FPGA based design approach. As real time simulation results shown for different antenna speed (RPM), all the desired results in terms of antenna acceleration, speed and position with respect to command are successfully achieved.
ACKNOWLEDGEMENTS
The authors would like to thank G.M. NS2, Cdr. [Retd.] K Kumar and A.G.M. Smt. Dharani. B for their continuous support and guidance in publishing this research work.
REFERENCES
[1] G. Viswanathan, R.C. Bhatia, V.P. Kamble and S. Rajesh Rao, Indian Doppler Weather Radar System an overview, IEEE International Symposium on Geoscience and Remote Sensing (IGARSS), pp. 1129- 1131, 1997. [2] Mario Garcia-Sanz, Trupti Ranka and Bhal Chandra Joshi, Advanced non-linear robust controller design for high-performance servo-system in large radar antennas, IEEE National Aerospace and Electronics Conference (NAECON), pp. 177-182, 2011. [3] Lei Ye, Jian Li, Zhendong Yao, Longfei Yi, Yong She and Shuo Wang, Design of X-band Doppler Weather Radar Servo System, IEEE International Conference on Meteorology Observations (ICMO), 2019. [4] Yan Li, Shengxian Zhuang and Luan Zhang, Development of an FPGA- Based Servo Controller for PMSM drives, IEEE International Conference on Automation and Logistics, pp. 1398-1403, 2007. [5] Clive Max field, Design Warrior Guide to FPGAs, Elsevier publications 2004. [6] Geeta Andrew, Nandini Gupta, Vijay Goyal and Hari Balakrishna, Realisation and validation of Servo control system for ship borne terminal (SBT), IEEE International Conference on Antenna Innovations and Modern Technologies for Ground, Aircraft and Satellite Application, Issue (24-26 Nov.2017). [7] Zeyad Assi, MH Marhaban, MN Hamidon, Design and Implementation of FPGA-based systems – a review, Australian Journal of Basic and Applied Sciences 3 (4), 3575-3596, 2009. [8] Nan Yang, Dewei Li, Jun Zhang, Yugeng XI, Model predictive controller design and implementation on FPGA with application tomotor servo system, Control Engineering Practice 20 (11), 1229-
1235, 2012.
[9] Arshia Tabassum and Rachna S N, Design and Realization of Antenna Control Servo System using Direct Drive Motors, International Research Journal of Engineering and Technology (IRJET), vol. 6(5), pp. 7571-7576, May 2019.Mani Shankar Anand, received M. Tech in System and Control from IIT-Roorkee in 2012. He completed his
B. Tech in Electronics and Communication from FIEM, West Bengal University of Technology, Kolkata in 2010. Presently serving as Dy. Manager in Bharat Electronics Limited, Bangalore. His area of
interest is Non-linear control, embedded system and digital signal processing.
Eswara Babu A, received B.E. from MVSR College of Engineering, Osmania University in 1998. Now serving as Dy. General Manager in Bharat Electronics Limited, Bangalore. His area of interest is Radar Signal and Data Processing.