
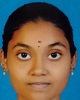
- Open Access
- Authors : Chennuru Bhavana , Deevi Vijay Babu , Jaya Nikitha Nallapati, Korampalli Raghu Hanuma, Mallelli Prasanna Venkata Balaji, P. Narendra Babu, N A G K Manikanta Kopuri
- Paper ID : IJERTV13IS030020
- Volume & Issue : Volume 13, Issue 03 (March 2024)
- Published (First Online): 12-03-2024
- ISSN (Online) : 2278-0181
- Publisher Name : IJERT
- License:
This work is licensed under a Creative Commons Attribution 4.0 International License
Experimental Study on Concrete by Partial Replacement of Fine Aggregate With Bituminous Road Waste
Chennuru Bhavana , Deevi Vijay Babu , Jaya Nikitha Nallapati, Korampalli Raghu Hanuma, Mallelli Prasanna Venkata Balaji, P. Narendra Babu,
N A G K Manikanta Kopuri
UG Students Final Year, Associate Professor & HOD, Associate Professor Department of Civil Engineering, NRI Institute of Technology, Agiripalli, India
Abstract: In this study, we investigated the improvement in strength of concrete by partially replacing fine aggregate with bituminous road waste. Our goal is to enhance the mechanical properties of concrete while promoting sustainability in construction. Through experimental analysis, evaluated the compressive and split tensile strengths of concrete by testing cubes and cylinders with varying replacement percentages. This study aims to investigate the feasibility of utilizing bituminous road waste as a partial replacement for fine aggregate in concrete. The research investigates the potential for enhancing the strength of concrete through the partial replacement of fine aggregate with bitumen road waste, specifically focusing on M30 grade of concrete. This study explores replacement percentages of 10%, 20%, and 30%, and evaluates the impact of curing durations at 7, 14, and 28 days on the concrete's mechanical properties.
Key words: Cement, Aggregates and Bituminous Road Waste (BRW).
-
INTRODUCTION
Concrete is a widely used construction material, but traditional concrete production methods have a significant environmental impact due to the extraction of natural resources and the emission of greenhouse gases. That's where the concept of using bituminous road waste as a partial replacement for fine aggregate comes in. Bituminous road waste refers to the materials generated during road construction and maintenance, such as asphalt, bitumen, and other road-related debris. Instead of disposing of this waste, it can be recycled and incorporated into concrete production. The process involves sieving the bituminous road waste to obtain the desired particle size. This recycled material can then be used as a partial replacement for fine aggregate in concrete mixtures. By doing so, we can reduce the demand for natural sand, which is often obtained through environmentally damaging methods like riverbed mining. The addition of bituminous road waste in concrete offers several benefits. Firstly, it helps in utilizing a waste material that would otherwise end up in landfills, contributing to
environmental pollution. Secondly, it improves the mechanical properties of concrete, such as compressive strength and durability. The bituminous materials act as a filler, enhancing the overall performance of the concrete mixture. However, it's important to note that the percentage of replacement should be carefully determined through experimentation and testing. Different proportions of bituminous road waste can have varying effects on the concrete's properties, so it's crucial to find the right balance.
-
LITERATURE REVIEW
The following literature elaborates the research studies made on the concrete with different alternatives as partial replacement to fine aggregate.
Otunyo et al (2013) The results of this exploratory study, it can be safely concluded that crushed periwinkle shell can be used as a partial replacement of river sand in the production of light weight concrete in areas where the periwinkle shells are in abundance.
Jaylina and Reshma (2014) Partial replacement of fine aggregates with 5% of rubber can potentially be used in low strength concrete applications.
Yogesh et al (2014) The possibility of substituting natural fine aggregate with industrial by-product aggregate such as waste foundry sand and bottom ash offers technical, economic and environmental advantages which are of great importance in the present context of sustainability in the construction sector.
Malkit et al (2014) River sand replaced with 0%, 20%, 30%,
40%, 50%, 75% and 100% coal bottom ash. The test results of this research work indicate that at fixed water cement ratio, workability and loss of water from bleeding decreased with the use of coal bottom ash as a replacement of river sand in concrete.
Sabarish et al (2015) In this investigation, percentage laterite content (0%, 10%, 20%, 30%, 40% and 50%). Data results revealed that the laterite fines used could satisfactorily
replace the sand up to 30%. By fixing the laterite content as 30% of fine aggregate.
Dash (2016) It can be observed that the concrete where sand is replaced by copper slag, imperial smelting furnace slag, class F fly ash exhibits improved strength and durability properties, but its slump increases as the rate of replacement increases in the case of copper slag and the slump decreases in the case of class F fly ash. There is a less research work reported on ferrochrome slag and palm oil clinker used as sand substitution.
Tiwari et al (2016) The paper reviews the feasibility of a wide variety of industrial by-products such as bottom ash, waste foundry sand, copper slag, plastic waste, recycled rubber waste, crushed glass aggregate etc., as a potential replacement for fine aggregate in the concrete manufacturing process in terms of strength and durability characteristics. A framework for further research has been proposed to attain reliable, robust, eco-friendly and economic concrete as the end product.
Rashad (2016) This paper presents an overview of the previous studies carried out on the use of the previous wastes as a partial or full of natural fine aggregate replacement in traditional mortar/concrete mixtures based on Portland cement (PC). Other cementitious material such as ground basaltic pumice and metakaolin (MK), which can replace part or full of natural fine aggregate was also included. Fresh properties, hardened properties and durability of mortar/concrete containing these waste/cementitious materials as natural fine aggregate replacement have been reviewed.
Ravindra and Anil Kumar (2016) Marine Sand as Partial Replacement of Fine Aggregate with 50% of replacement can be done without any addition of admixtures for achieving the strength.
Priyansha et al (2016) The addition of jarosite as a partial sand replacement in concrete (along with fly ash as mineral admixture) up to 25% could be a new alternative feasible solution to its disposal issue. Also, the concrete with 15% jarosite as a sand replacement could be best suited for road and building construction purpose.
Alexander et al (2016) The partial replacement of sand in concrete has been done using red soil in a mix proportion of 1:1.5:2.75 which gives the significant improvement in strength and imperviousness. The characteristics of red soil has a great impact on strength, imperviousness and anti pest control. After conducting all these tests, red soil is found suitable for concrete as an admixture of it which can be used in construction of buildings.
Otunyo and Okechukwu (2017) Waste glass as partial replacement for fine aggregates at 15%, 25%, 35%, 45%, and 50%. The results of the study generally demonstrated that partial replacement of fine aggregate with WG is economical. Since the quantity of the expensive sand (fine aggregate) can be reduced up to 15% replacement level and considering the fact that WG is usually disposed of and can be obtained at little or no cost in comparison with sand, cost of concrete production can be relatively reduced using this waste.
Naveen et al (2017) The river fine aggregate will be replaced wth waste foundry sand (0%, 5%, 10%, and 15%) in the concrete. From the results obtained it is suggested that WFS
and Reclamation of WFS with a substitution rate up to 25% can be used effectively as a fine aggregate in good concrete production without affecting the concrete standards.
Mohanalakshmi et al (2017) Then cubes were casted for the 5 parts of partial replacement as 20%, 40%, 60 %, 80%, and 100 %. All the specimens are used for 7 & 28 days and tested for compressive, flexural and split tensile strength. We have observed the maximum strength is obtained for 80% replacement of sea shell.
Rohit (2018) The addition of powdered rubber to the concrete mix results in a negative effect on the modulus of elasticity. The decrease of elasticity reflects the capability of rubberized concrete to behave in an elastic manner when loaded in tension, thus improving the failure manners of typical concrete.
Sabih et al (2019) The tests were performed with 10 percent,
30 percent, 40 percent, 50 percent substitution of fine aggregates with ceramic powder by weight and 28 days of strength testing to evaluate the mechanical characteristics. The research above shows that ceramic powder can be used as a substitute for finer aggregates by 20%.
Sanjay et al (2020) Sandstone cutting waste and further river sand was replaced with sandstone cutting waste using replacement level of 10%, 20%, 30%, 40%, 50% & 100% along with optimum levels in between. It was observed that sandstone cutting waste can be utilized in the production of structural concrete as partial replacement of river sand up to 10% replacement level using w/c ratio of 0.35 & up to 30% replacement level using w/c ratio of 0.4 & 0.45.
Kishor et al (2020) All the concrete mixes were created by substituting 0, 10%, 20%, and 30% of fine aggregate with crushed seashells. The result indicates higher compressive, split-tensile and flexural strength at 10% partial replacement of fine aggregate.
Kaish et al (2021) The result also shows that optimum replacement content of fine aggregate with industrial waste were 10% for oven-dried alum sludge, whereas 15% for quarry and limestone dust content that improved all strength properties investigated in this study. All industrial waste employed in this study as fine aggregate have proven to be a good filler material by filling the concrete internal void and improving the strength properties for a normal strength concrete.
Manoj and Sanjaya (2021) Traditional sand was substituted with six percentages (0% for reference mix, 10%, 20%, 30%, 40% and 50%) of ferrochrome slag by weight in all concrete mixtures. This experimental study concludes that that ferrochrome slag can be used in the production of concrete as a partial substitution of traditional sand with no unfavourable ecological, micro-structural and mechanical effects.
-
MATERIALS USED
3.1 CEMENT: Cement is a binder, a material that sets and hardens and can bind other materials together. Cement is a product including lime as the primary curing ingredient, but it is far from the first material used for cementation. Cement starts to set when mixed with water which causes a series of hydration chemical reactions.
Table-1 Tests Results of Cement
S.NO
PROPERTIES
RESULT
1
Normal Consistency
30 %
2
Initial Setting Time
&
Final Setting Time
34 min & 330 min
3
Fineness
3.34 %
4
Specific Gravity
3.05
-
SAND: Those fractions from 4.75 mm to 150 microns are termed as fine aggregate. The river sand and crushed sand is being used in combination as fine aggregate conforming to the requirements of IS: 383-2016.
-
BITUMINOUS ROAD WASTE (BRW): Bituminous road waste typically consists of materials such as reclaimed asphalt pavement (RAP), aggregates, bitumen, and potentially other additives. RAP is a major component, comprising recycled asphalt from old roads. The aggregates can include crushed stone, sand, and gravel, while bitumen serves as the binder that holds the materials together in the asphalt mix. The specific composition may vary based on the recycling process and the original road materials.
Figure 1: Bituminous Road Waste
Table-2 Test Results of Sand And BRW
S.NO
PROPERTIES
SAND
BRW
1
Specific Gravity
2.67
2.42
2
Fineness Modulus
2.55
2.65
3
Bulking
34 %
43 %
3.3 COARSE
AGGREGATE: As per IS 383-2016, Coarse aggregates can be defined as irregular broken stone or naturally-occurring rounded gravel used for making concrete. Coarse aggregates are retained on the sieve of mesh size 4.75mm. It acts as volume increasing component and it is responsible for strength, hardness and durability of concrete.
Table-3 Test Results of Coarse Aggregate
S.NO
PROPERTIES
RESULTS
1
Specific Gravity
2.71
2
Fineness Modulus
7.2
3
Aggregate Impact Value
20.27 %
4
Aggregate Crushing Value
21.06 %
-
-
RESULTS & DISCUSSIONS
-
COMPRESSIVE STRENGTH VALUES: This test is considered as one of the most important properties of concrete and it is often used as an index of the overall quality of concrete. For this, the cubes were tested for its compressive strength at the age of 7th, 14th & 28th days of curing. From the test results, it was observed that the strength of concrete which contains bituminous road waste is slightly higher than the conventional concrete up to 20 % replacement of bituminous road waste for river sand. Below listed tables and graphs shows the relationship between the no. of days of curing and its mean compressive strength.
Figure 2: Cube Under Compression Testing Machine
S. NO
% REPLACEMENT OF BRW
COMPRESSIVE STRENGTH
(N/mm2)
7 DAYS
14 DAYS
28 DAYS
1
0
43.55
54.66
60.22
2
10
45.77
57.21
63.33
3
20
49.12
59.77
66.28
4
30
48.12
56.43
63.18
Table-4 Compressive Strength of Cubes At 7, 14 & 28 Days of Curing
70
63.33
57.21
66.28
0
0%
10%
20%
30%
% REPLACEMENT OF BRW
7 DAYS 14 DAYS 28 DAYS
60
60.22
54.66
63.18
59.77
56.43
50
49.12
48.12
43.55
45.77
40
30
20
10
COMPRESSIVE STRENGTH (N/mm2)
Figure 3: Compressive Strength VS % Replacement of BRW
-
SPLIT TENSILE STRENGTH: The cylindrical specimens were tested for its split tensile strength at the age of 7, 14 & 28th days of curing. The test result shown in table revealed that split tensile strength of concrete which contains bituminous road waste.
Figure 4: Cylinder Under Compression Testing Machine
S. NO
% REPLACEMENT OF BRW
SPLIT TENSILE STRENGTH (N/mm2)
7 DAYS
14 DAYS
28 DAYS
1
0
3.91
4.01
4.12
2
10
4.18
4.25
4.42
3
20
4.23
4.39
4.53
4
30
4.01
4.19
4.25
Table-5 Split Tensile Strength of Cylinders At 7, 14 & 28 Days of Curing
SPLIT TENSILE STRENGTH (N/mm2)
4.6
4.5
4.4
4.3
4.2
4.1
4
3.9
3.91
4.01
4.12
4.18
4.25
4.42
4.23
4.39
4.53
4.01
4.19
4.25
3.8
3.7
3.6
0% 10% 20% 30%
% REPLACEMENT OF BRW
7 DAYS 14 DAYS 28 DAYS
Figure 5: Split Tensile Strength VS % Replacement of BRW
-
-
CONCLUSIONS
Based on the experimental testing, following conclusions were drawn
-
The compression strength values gets increased up
to 20% replacement of fine aggregate by bituminous road waste i.e. optimum value occurs at 20% replacement.
-
The split tensile strength values gets increased up to 20% replacement of fine aggregate by bituminous road waste i.e. optimum value occurs at 20% replacement.
-
From the test results, it is observed that 5.16 %,
10.06 % and 4.91 % improvement in compressive strength of concrete at 10 %, 20 % and 30 % replacement of bituminous road waste to fine aggregate, when compared with conventional concrete.
-
From the test results, it is observed that 7.32 %, 9.95
% and 3.15 % improvement in split tensile strength of concrete at 10 %, 20 % and 30 % replacement of bituminous road waste to fine aggregate, when compared with conventional concrete.
REFERENCES
[1] Otunyo, A. W., Friday, I. U., & Israel, T. A. (2013). Exploratory study of crushed periwinkle shell as partial replacement for fine aggregates in concrete. Journal of Emerging Trends in Engineering and Applied Sciences, 4(6), 823-827. [2] Rana, J., & Rughooputh, R. (2014). Partial replacement of fine aggregates by rubber in concrete. Journal of Emerging Trends in Engineering and Applied sciences, 5(5), 312-317. [3] Aggarwal, Y., & Siddique, R. (2014). Microstructure and properties of concrete using bottom ash and waste foundry sand as partial replacement of fine aggregates. Construction and Building Materials, 54, 210-223. [4] Singh, M., & Siddique, R. (2014). Strength properties and micro- structural properties of concrete containing coal bottom ash as partial replacement of fine aggregate. Construction and Building Materials, 50, 246-256. [5] Sabarish, G., Ratnam, M. K. M. V., Prasad, A. C. S. V., & Raju, U.R. (2015). A study on strength and durability characteristics of concrete with partial replacement of fine aggregate by laterite sand. International journal for innovative research in science and technology, 2, 134-141.
[6] Dash, M. K., Patro, S. K., & Rath, A. K. (2016). Sustainable use of industrial-waste as partial replacement of fine aggregate for preparation of concreteA review. International Journal of Sustainable Built Environment, 5(2), 484-516. [7] Tiwari, A., Singh, S., & Nagar, R. (2016). Feasibility assessment for partial replacement of fine aggregate to attain cleaner production perspective in concrete: A review. Journal of Cleaner Production, 135, 490-507. [8] Rashad, A. (2016). Cementitious materials and agricultural wastes as natural fine aggregate replacement in conventional mortar and concrete. Journal of Building Engineering, 5, 119-141. [9] Ravindra, V., & Buraka, A. K. (2016). Mechanical Properties of Concrete with Marine Sand as Partial Replacement of Fine Aggregate. Dr. V. Ravindra Int. Journal of Engineering Research and Applications, 6(2), 8-11. [10] Mehra, P., Gupta, R. C., & Thomas, B. S. (2016). Properties of concrete containing jarosite as a partial substitute for fine aggregate. Journal of cleaner production, 120, 241-248. [11] Alexander, S. J., Godwin, A., & Alexander, S. (2016). Study on partial replacement of fine aggregate with red soil in concrete. International Journal for Research in Applied Science and Engineering Technology, 4(5), 138-145. [12] Otunyo, A. W., & Okechukwu, B. N. (2017). Performance of concrete with partial replacement of fine aggregates with crushed waste glass. Nigerian journal of technology, 36(2), 403-410. [13] Arasu, N., & Robinson, J. (2017). Experimental analysis of waste foundry sand in partial replacement of fine aggregate in concrete. International Journal of ChemTech Research, 10(8), 605- 622. [14] Mohanalakshmi, V., Indhu, S., Hema, P., & Prabha, V. (2017). Developing concrete using sea shell as a fine aggregate. IJIRST, 3, 282-286. [15] Rohit, P., PVSSPG, V., & Sk, A. (2018). Partial replacement of fine aggregate with crumb rubber in concrete. Int. J. Civ. Eng. Technol., 9, 895-903. [16] Ahmad, S., Anwar, A., Mohammed, B. S., Wahab, M. B. A., & Ahmad, S. A. (2019). Strength behavior of concrete by partial replacement of fine aggregate with ceramic powder. Int. J. Recent Technol. Eng, 8(2), 5712-5718. [17] Mundra, S., Agrawal, V., & Nagar, R. (2020). Sandstone cutting waste as partial replacement of fine aggregates in concrete: A mechanical strength perspective. Journal of Building Engineering, 32, 101534. [18] Panda, K. C., Behera, S., & Jena, S. (2020). Effect of rice husk ash on mechanical properties of concrete containing crushed seashell as fine aggregate. Materials Today: Proceedings, 32, 838-843. [19] Kaish, A. B. M. A., Odimegwu, T. C., Zakaria, I., & Abood, M.M. (2021). Effects of different industrial waste materials as partial replacement of fine aggregate on strength and microstructure properties of concrete. Journal of Building Engineering, 35, 102092.
[20] Dash, M. K., & Patro, S. K. (2021). Performance assessment of ferrochrome slag as partial replacement of fine aggregate in concrete. European Journal of Environmental and Civil Engineering, 25(4), 635-654.