
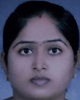
- Open Access
- Authors : Pawar M.N, Raulkar K.B, Lamdhade G.T.
- Paper ID : IJERTV13IS030065
- Volume & Issue : Volume 13, Issue 03 (March 2024)
- Published (First Online): 21-03-2024
- ISSN (Online) : 2278-0181
- Publisher Name : IJERT
- License:
This work is licensed under a Creative Commons Attribution 4.0 International License
Synthesis and Characterization of Magnesium Oxide ( MgO) Doped Cupric Oxide (CuO) Multilayer Thick Film
Pawar M.N, Raulkar K.B, Lamdhade G.T.
Department of Physics, G.S.Tompe Arts,Commerce and Science College,Chandur Bazar,
Dist.Amravati, M.S. India
Department of Physics, Vidya Bharati Mahavidyalaya, CK Naidu Road, Amravati, M.S. 444602 India
ABSTRACT
In this paper study Copper oxide,Magnesium Oxide nanoparticles were synthesized by sol gel method.Recently Copper and Magnesium Oxide nanoparticles attracted the investigators due to their significant characteristics and employment in semiconductors,magnetic storage media,solar energy transformation,gas sensors and photothermal devices. In this paper is focused on preparation of cupric oxide doped magnesium oxide multilayer thick film by screen printing method on alumina substrates. XRD and SEM are used to study structural and morphological properties of MgO-CuO. The XRD pattern of (MgO-CuO) system samples show nanocrystalline form and found the desired peaks of composites. FESEM study reveals that the grain size of nanometer order and shows nano- porous structure, which leads to exhibit large surface area, stability and highest response to gas. In present study C3 sensor (70MgO:30CuO) is found to optimized multilayer thick film.
Keywords: MgO, CuO, CO2 gas sensor, Sol-gel method, XRD,SEM
INTRODUCTION
In recent year, a great attention has been paid to the development and application of environmental gas sensors.Chemical gas sensor has been of much scientific and commercial interest already for several decades. New application ares provoke a steady development of new sensors types to meet the additional requirements. At the same time, new sensor types open up new application areas.CO2 gas is very difficult to detect by conventional gas sensor due to high stability at ambient temperature.
Maier et al. had first time demonstrated the CO2 gas detection, since then many researches [1-5] have reported CO2 gas detection by using metal oxides. Now a days, there is a great interest in implementing sensing devices in order to improve environmental and safety control of gases. The most used gas sensors devices can be divided in three big group depending on the technology applied in their development: solid state,spectroscopic and optic.In this work was centered in studying the semiconductors
properties, in those material using MgO and CuO as sensing material. The main purpose of this paper is to study new material for gas sensing elements starting from the knowledge in thick film production using screen printing technique.
Due to interesting properties and promising applications Cupric oxide (CuO)and MgO nanostructures gain interest in many applications. Nanoparticles CuO and its composite oxides have potential applications as gas sensor. As compared to bulk materials, nanoparticles of Copper oxide (CuO) show high catalytic activity and selectivity due to their large surface to volume ratio. The sensitivity and response time of CuO and MgO based sensors strongly depend on the particle size of the material [6]. With introducing changes into the procedure of its chemical synthesis, physical and micro structural properties of metal oxide can be modified. Different nanostructures of CuO and MgO like nanowire, nanorod, nanoneedle, nano-flower and nanoparticles are synthesized by using various approaches such as; Sol-Gel Combustion Route [7], Microwave Assisted Co- Precipitation Method [8],Chemical Precipitation Method [9], Simple Precipitation Method [10], Sono-chemical Method [11-12] and etc.
Several methodologies were employed to get ready copper oxide NPs. Sol Gel technique has many beneficial. Solitary sol-gel installation could produce material with ultra-temperature .However, The report on the preparation and characterization of nanocrystalline CuO are relatively few to some other transition metal oxide such as Zinc oxide, titanium dioxide, Tin dioxide and Iron dioxide .
In the present work, Mgo and CuO sensors have been prepared by screen printing technique on glass substrate. The sensors were used for different concentration (ppm) of CO2 gas investigated at different temperature. The characteristics of MgO and CuO was done through XRD,SEM to known about the material structure and thermal stability which may be related to its detection properties.
2. EXPERIMENTAL WORK
In the present work the list of chemical and material along with the sources and grades used for the preparation of sensors are given in the table 1.
Table 1. Chemical and materials with sources and grade
Chemicals |
Acronym |
Grade |
Source |
Magnesium oxide |
MgO |
AR |
SD Fine India |
Ammonium persulphate |
APS |
AR |
SD Fine India |
Copper Oxide |
CuO |
AR |
SD Fine India |
Sodium hydroxide |
NAOH |
AR |
SD Fine India |
Alumina |
Al2O3 |
GR |
LOBA Chemi,India |
Methanol |
CH3OH |
AR |
SD Fine India |
Acetone |
CH3COCH3 |
AR |
SD Fine India |
Ethyl Cellulose |
[C6H7O2(OC2H5)3]n |
AR |
SD Fine India |
Butyl Carbitol |
C8H8O3 |
AR |
Merck,India |
In the present work, we have used sol-gel method (which is under liquid phase synthesis) for the synthesis of pristine nano-particles of MgO, CuO and Al2O3 [13-15]. All the chemicals used in this study were of GR grade purchase from Sd-fine, India (purity 99.99%). The chemicals are used without any further purification.
-
Synthesis of MgO
The Sol-gel technique is advantageous in the synthesis of nanosized material because it has the advantages of simple procedure, low temperature processing and low cost. Initially the magnesium Nitrate Hexahydrade of wt. 5.21gm (0.2M) and dissolved in 100 ml of distilled water. The 0.8 gm (0.2M) of NaOH in 200 ml distilled water. Then 100 ml of NaOH solution is added in solution of [Mg (NO2(H2O)] drop wise by using glass rod. After that, solution kept under magnetic stirring for 2 h after stirring the solution was kept on table for 2 h so that, the precipitation is formed at the bottom of beaker. This precipitation was filtered and washed several times by using distilled water and ethanol so as to get the final products. The final product is kept in vacuum
oven (Quality Make,India) at 80oC for 4h for drying product and removing the moisture. This dried powder is then crush and make it very fine powder by using mortal pestle. Finally the fine powder of MgO is calcinated at 400oC for 3h for the removal of impurities present in the powder. So that we will get synthesized MgO possessed high crystalline with the particle size in nanosized range.
-
Synthesis of CuO
CuO nano particles are synthesized by Co- precipitation method using copper (II) acetate [Cu(CH3COO)2H2O)] and Ammonia (NH3). In short, 0.2 M copper (II) acetate solutions (100 ml) and Ammonia was added drop wise to maintained pH in a round-bottom flask and under magnetic stirrer. The colour of the solution revolves from blue to black instantaneously and a black suspension formed smultaneously. The reaction was carried out under stirring and boiling for 3 hr. The mixture was cooled to room temperature CuO precipitate was obtained. The precipitate was filtered and washed with distilled water for several times. The resulting product was dried at 60C for 2 hr to obtain the dry powder of CuO Nano Composite.
-
Synthesis of Al2O3
All chemicals used were analytical grade. Aluminium chloride, AlCl3 (MOLYCHEM), 25% NH3 solution (QUALIGEN Fine Chemicals) and polyvinyl alcohol (PVA) were used as raw materials for the synthesis of aluminium oxide nanoparticles. 1M alcoholic AlCl3 solution was prepared, followed by addition of 25% ammonia solution. The resulting solution turned to a white sol. This was followed by the addition of PVA (0.5M). The solution was stirred continuously using a magnetic stirrer until it became a transparent sticky gel. The gel was allowed to mature for 24 hours at room temperature. The resultant gel was heat treated at 100°C for 24 hours which led to the formation of light weight porous materials due to the enormous gas evolution. The dried gel was, then calcined at 1000°C for 4 hours and finally, the calcined powders were crushed using mortar and pestle to get the fine homogeneous dense powder ofAlumina (Al2O3).
-
Fabrication of Sensors
The samples prepared were MgO:CuO with Al2O3 base of multilayer sensors. The different combinations are shown in tables 2.
Table 2. Samples Codes of Series: MgO:CuO
Sr. No.
Sample Codes
Composition of MgO:CuO (mole %)
1
C1
90MgO-10CuO
2
C3
70MgO-30CuO
3
C5
50MgO-50CuO
4
C7
30MgO-70CuO
5
C9
10MgO-90CuO
6
PM
100MgO-0CuO
7
PC
100CuO-0MgO
Out of various methods of sensors preparation, the screen-printing (thick film technology) is most widely used. Screen- printing is the transfer of pastes though a fabric screen onto a substrate.
-
Multilayer preparation
Fig. 1 (a), and 1(b) show fabrication of interdigited electrodes, actual photographs of interdigited electrodes respectively.
-
(b)
-
Fig. 1 (a) Fabrication of interdigited Electrodes (b) Actual photograph of interdigited electrodes
Fig.2 Design of multilayer Sensor
On clean glass substrate, Al2O3 was deposited by using screen-printing technique and it was used as base of the sensor. On Al2O3, the sample layers were prepared. Finally on the top, Interdigited
electrodes were fabricated using conducting silver paste as shown in the Fig. 1(b). Design of multilayer sensor is shown in Fig. 2.
RESULTS AND DISCUSSION
-
XRD of MgO and CuO Nanomaterial and their dopings
The average crystallite size was calculated by Debye-Scherers equation with the help of XRD patterns as shown in figure 3. The strong and sharp peak of MgO observed at 37.85° position with (0 0 2) indicates that the sample is having high crystalline quality, and it is in the structure of monoclinic with lattice parameters a = 3.1300 nm, b = 3.1300 nm, and c = 4.7500 nm, which is good agreement with JCPDS card number 1010484. The average crystalline size was obtain 70.17nm calculated by Deye- Scherrer formula
D = Kcos (1)
Where, D is the crystallite size, K is the shape factor, which can be assigned a value of 0.98 if the shape is unknown, is the diffraction angle at maximum peak intensity, and is the full width at half maximum of diffraction angle in radian.
Fig. 3(a) XRD of pristine MgO
As shown in figure 3(b). Spectra, main peak, in case of pure CuO, is observed at 2=39.97° and 2=35.56° that can be ascribed to the planes (002) and (11-1) reflection of the CuO phase while; the other peaks are lying at planes (20-2), (11-3) of CuO. All the peaks in diffraction pattern show monoclinic structure of CuO and no any other peaks are observed. The sharp diffraction peaks were clearly seen and they perfectly match with crystal structure of CuO, therefore, we get perfectly crystallinity of CuO particles. The calculated crystallographic parameters are a = 4.6837 (Å), b = 3.4226 (Å) and c = 5.1288 (Å).The pattern is also match with JCPDS file No. [7212242].The average crystallite size calculated by using Scherrer formula and is found to be is approximately 72.37 nm.
Fig. 3(b) XRD of pristine CuO
Fig.3(c). XRD of composite MgO:CuO
From table 3, it is seen that the sample average of crystallite size of samples are found to be less than the 150 nm range and it is satisfactory. The sample C3 (70 MgO 30 CuO) has lowest crystallite size in the order of 51.47 nm.
Table 3.Average Crystallite size of composite MgO:CuO
Sr.No.
Sample Code
Chemical Composition of MgO- CuO (mole %)
Crystallite size (nm)
1
C1
90 MgO -10 CuO
121.11
2
C3
70 MgO -30 CuO
51.47
3
C5
50 MgO – 50 CuO
129.74
4
C7
30 MgO – 70 CuO
137.82
5
C9
10 MgO 90 CuO
137.78
-
Scanning electron microscopy (SEM) Analysis
From SEM picture (figure 4 (a) to (d)), it is observed that all the samples viz. MgO, CuO are porous in nature. Porosity varies with sample to sample and among these material, MgO showed more porosity (small size ~ 60 to 80 nm). Due to small pores size, its surface area is more [16-17] and it shows more sensing nature. Some portion of SEM picture shows some rods with fine voids over them which helps to increase sensing properties. The surface morphology of pure MgO and CuO nano materials were studied by SEM and its picture is shown in the Fig. 4 (a to d)
Fig. 4 (a) SEM picture of MgO and CuO
Fig.4(b) SEM picture of composite A1 and A3
Fig.4(d) SEM picture of composite A9
Fig.4(c) SEM picture of composite A5 and A7
The figures 4(a to d) As shown in the SEM pictures, some pores are in the form of rods, some are the form of circles and some are in conical shapes [18].
Table 4. shows the average diameter and number of pores per inch of pure MgO and CuO, and their dopings.
CONCLUSION
From the SEM pictures (table 4), it is observed that, Sample Code C3 i.e. (70MgO-30CuO), have more pores per inch (calculated for x 2,000 magnification for each composition) than other sensors. Thus, these sensors have more active surface areas and exhibit more sensing nature [19]. It is also found that average diameter of pore in case of Sample Code C3 i.e. (70MgO-30CuO) are small as compared to other doping. This also tends to exhibit large surface area and exhibited high response of the samples
Sample Code |
Pure sample and their dopings (mole %) |
Average diameterof pore (nm) |
Number of pores per inch(in x 2000 magnification) |
PM |
MgO |
80 |
154 |
PC |
CuO |
73 |
172 |
C1 |
90MgO-10CuO |
79 |
158 |
C3 |
70MgO-30CuO |
53 |
228 |
C5 |
50MgO-50CuO |
62 |
143 |
C7 |
30MgO-70CuO |
1 |
193 |
C9 |
10MgO-90CuO |
78 |
120 |
REFERENCES
-
Maier J,Holziger M and Sitte W,Solid State Ionics,Volume 74, Issue 5,(1994)
-
Yahiro H and Katayama S-I, Denki Kagaku,Volume 61, Issue 451,(1993)
-
Ishihara T and Kometani K,Sens Actuators B,Volume 28, Issue 49,(1995)
-
Ishihara T.Kometani K.Mizuhara Y and Takita Y.J Am Ceram Soc,Volume 75,613,(1992)
-
Liao B,Ph.D.Thesis,Central south University of Technology,(1997)
-
Sanjay Srivastava, Mahendra kumar, Arvind Agrawal and Sudhanshu Kumar Dwivedi, Synthesis and Characterisation of Copper Oxide nanoparticles, IOSR Journal of Applied Physics (IOSR-JAP) Volume 5, Issue 4 PP: 61-65, (2013)
-
S. M. Sathiya, G. S. Okram, M. A. Jothi Rajan, Structural, optical and electrical properties of copper oxide nanoparticles prepared through microwave assistance, Advanced Materials Proceedings, Volume 2,Issue 6, pp:371- 377, (2017), DOI: 10.5185/amp.2017/605
-
R. Chopra, N. Kashyap, Amit Kumar, D. Banerjee, Chemical synthesis of copper oxide nanoparticles study of its optical and electrical properties, International Journal of Engineering Research &Technology (IJERT) ISSN: 2278-0181, Vol. 9,
Issue 01, (2020), IJERTV9IS010160
-
S. Thamaraiselvi, G. Thenmozhi, Synthesis of CuO Nanoparticles by using Simple Precipitation Method, International Journal of Science and Research (IJSR) ISSN: 2319-7064, Volume 11, Issue 4, (2022), DOI: 10.21275/SR22425202059
-
Nataly Silva, Sara RamÃrez, Isaac DÃaz, Andreina Garcia and Natalia Hassan, Easy, Quick, and Reproducible Sonochemical Synthesis of CuO Nanoparticles, Materials, Volume 12, Issue 804; (2019), DOI:10.3390/ma12050804
-
Kailash R. Nemade and Sandeep A. Waghuley, Optical and Gas Sensing Properties of CuO Nanoparticles Grown by Spray Pyrolysis of Cupric Nitrate Solution, International Journal of Materials Science and Engineering Vol. 2, No. 1, (2014),
DOI: 10.12720/ijmse.2.1.63-66
-
Panya Khaenamkaew ,Dhonluck Manop, Chaileok Tanghengjaroen and Worasit Palakawong Na Ayuthaya, Crystal structure, lattice strain, morphology, and Electrical Properties of CuO nanoparticles induced by low calcination temperature, Advances in Materials Science and Engineering,
Article ID 3852421, (2020), DOI:10.1155/2020/3852421
-
K. B. Raulkar, Study on sensitivity of nano SnO2 -ZnO composites with and without PPy layer for sensing CO2 gas, Materials Today: Proceedings 15, 6046,(2019)
-
Dmitry Bokov, Abduladheem Turki Jalil, Supat Chupradit, Wanich Suksatan, Mohammad Javed Ansari, 6 Iman H. Shewael, Gabdrakhman H. Valiev, and Ehsan Kianfar, Review Article, Nanomaterial by Sol-Gel Method: Synthesis and Application, Advances in Materials Science and Engineering Volume 6, (2021),DOI:10.1155/2021/5102014
-
Zahrah Alhalili, Review Metal Oxides Nanoparticles: General Structural Description, Chemical, Physical, and Biological Synthesis Methods, Role in Pesticides and Heavy Metal Removal through Wastewater Treatment, Molecules,Volume 28, 3086, (2023), DOI:10.3390/molecules28073086
-
Fang Peng, Yan Sun, Weiwei Yu, Yue Lu, Jiaming Hao, Rui Cong Jichao Shi, Meiying Ge and Ning Dai,2020, Gas Sensing Performance and Mechanism of CuO(p)- WO3(n) Composites to H2S Gas. Nanomaterials, Volume 10, 1162; DOI:10.3390/nano10061162
-
Quentin Simon, Davide Barreca, Alberto Gasparotto, Chiara Maccato, Eugenio Tondello, Cinzia Sada, Elisabetta Comini, Giorgio Sberveglieri, Manish Banerjee, Ke Xu, Anjana Devi, and Roland A. Fischer, CuO/ZnO Nanocomposite Gas Sensors Developed by a Plasma-Assisted Route, ChemPhysChem, pp:18, DOI:10.1002/cphc.201101062
-
Yalu Chen, Zhurui Shen, Qianqian Jia, Jiang Zhao, Zhe Zhao, Huiming Ji, 2013, A CuO-ZnO Nanostructured p-n Junction Sensor for Enhanced N-butanol Detection, The Royal Society of Chemistry, DOI: 10.1039/x0xx00000x
-
Raulkar K.B, Wasnik T.S, Joat R.V., Wadatkar A.S. Agrawal,
R.M. and Lamdhade G.T., Study on DC Conductivity of PPy- ZnO Nanocomposites, Materials today Proceedings,Volume 15, Issue (3), 595-603, (2019).