
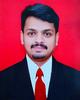
- Open Access
- Authors : Mr. Shubham R. Awale, Dr. Subim N. Khan, Dr. Pavankumar R. Sonawane
- Paper ID : IJERTV13IS050196
- Volume & Issue : Volume 13, Issue 05 (May 2024)
- Published (First Online): 30-05-2024
- ISSN (Online) : 2278-0181
- Publisher Name : IJERT
- License:
This work is licensed under a Creative Commons Attribution 4.0 International License
Design, Development, and Analysis of a Stroke Adjustor Mechanism in Variable Displacement Pumps
Mr. Shubham R. Awale, PG Student
Dept. of Mechanical, JSPMs Rajarshi Shahu College of Engineering, Tathawade, Pune, India
Dr. Subim N. Khan, Professor,.
Dept. of Mechanical, JSPMs Rajarshi Shahu College of Engineering, Tathawade, Pune, India
Dr. Pavankumar R. Sonawane, Associate Professor,.
Dept. of Mechanical, JSPMs Rajarshi Shahu College of Engineering, Tathawade, Pune, India.
Abstract
This article provides an overview of the innovation, which includes the design, development, and analysis of a stroke adjuster mechanism for a variable displacement pump. The inefficiencies associated with invariable displacement un typical hydraulic systems create operating limits, resulting in energy waste. Our solution employs a unique linking mechanism that alters stroke length to tailor fluid production to real-time requirements, therefore increasing operational flexibility and system efficiency. The core component of the design is an eccentrically mounted slotted crank link to the piston, which allows for changeable stroke lengths ranging from 0 to 7mm. This immediately correlates to a volumetric output of 0 to 0.791784cc per stroke. This mechanism is critical because it addresses all of the disadvantages of traditional ones by offering precise control over the discharged volume while reducing operational energy consumption and expenses. Comprehensive study using ANSYS Workbench 2023 R1 simulation assisted in determining the mechanical integrity of the design under varying operational situations. Experimental testing concentrated on the pump's volumetric efficiency at various speeds (200 to 600 rpm) and stroke settings. It revealed that the volumetric efficiency is at its greatest at 400 rpm, which equals 78.55%. Such maximum performance highlights the adjuster's human capacity to reduce internal leakages and inefficiencies that arise with greater speeds. The design's adaptability was also demonstrated in a comparison of theoretical and real flow rates, which were quite similar, demonstrating the accuracy of our prediction models. The stroke adjuster mechanism adjusts fluctuating flow rates in industrial applications while simultaneously improving energy economy and operational safety, making it a vital addition to current hydraulic systems. Keywords: Variable Displacement Pump, Stroke Adjuster Mechanism, Slotted Crank Link, Energy Efficiency, Volumetric Efficiency.
-
INTRODUCTION
The stroke adjustor mechanism of the variable displacement pump is designed to address a number of significant issues common to conventional hydraulic systems. The axial type piston pump has been found to be useful in a variety of applications due to its ability to manage flow rates through pressure modification; nevertheless, it generates a large back pressure. Furthermore, the backpressure may cause further vibrations and, in certain cases, a complete shutdown of the hydraulic system, posing a risk to both the system's integrity and its safety during operation. The bent-axis, swash-type piston pumps are extremely effective, but uneconomical for smaller-scale applications, since the average price of this model is often 20-30% more than that of its axial cousin. Adding to these problems is the necessity for a new mechanism that can change the pump discharge with adequate efficiency while maintaining system pressure and overall efficiency. However, the concept addresses the shortcomings of previous systems by introducing an affordable, adaptive, and efficient stroke adjustor mechanism that can be changed to meet operational needs, providing a versatile solution for a wide range of industrial applications. This is further increased by the use of current simulation and analysis tools, such as ANSYS, to evaluate the strength of the part, as well as CAD software for accurate design, to guarantee that each of the identified parts outperforms the specified requirements. [1]
The Minimum Quantity Lubrication System (MQL) has several advantages over traditional techniques of hand lubrication. Greasing or oiling the machine while it is in operation ensures that the lubricant is evenly distributed across the bearings. To ensure safe functioning, essential components should be oiled appropriately. Longer component life, fewer malfunctions, less downtime, cheaper replacement costs, and lower maintenance costs due to reduced component wear. Access to numerous locations ensures safety because there is no climbing around hazardous
machinery. Thus, employing a MQL system increases overall productivity and machine availability, as well as the possibility of reducing downtime owing to fewer general maintenance and failures. [2]
A typical lubrication system consists of a flow controller, pump and reservoir, supply lines, metering valves, and feed lines. Regardless of the system type or manufacturer, all automated lubrication systems have these five critical components: [2]
1.2 Concept and Working of Mechanism of stroke adjustor:
-
Flow Controller activates components to supply or distribute lubricant throughout the system.
-
Pump and reservoir: store and supply oil to the system.
-
Line of Supply: The lubricant is distributed through this. It is also a line that links the metering valves to the pump.
-
Metering Valves or Injectors: These components monitor the amount of oil at their position.
-
Feed lines connect the application site to injectors/metering valves. This is filled with lubrication.
As a result, it is apparent that the Pump is an important component of the MQL system, hence it is vital to develop a cost-effective automatic control variable flow pump.
Pump and
Reservoir
Stroke Adjustor
Mechanism
Electric motor
Figure 1. 3D Model of Prototype
Push Rod for Piston
Piston Rod
Connecting Rod
Slotted Crank Link
Arrangement of Eccentricity Variation
Figure 2. Stroke Changing Mechanism
Figure 1 depicts the 3D model of the fabricated prototype, whereas Figure 2 depicts the suggested mechanism for stroke variation, which converts the crank's rotating motion to a reciprocating one for output linkage. Because of the Eccentric Element, the output linkage will move in a reciprocal manner. Because of the worm and worm gear configuration, eccentricity may be altered, as provided by the Stroke adjustor mechanism. Adjust the location of the eccentric element to vary the stroke length. We can achieve maximum stability and reduced vibration in performance by adopting this mechanism, which employs UCP type bearings to provide steady and maximal support to the driving element. Additional mountings for connecting rods, piston rods, and push rods for pistons provide stability and with this stable motion can be obtained.
Recent literature on the enhancement of hydraulic pumps and systems illustrates a variety of perspectives and innovative ideas aimed at addressing some of the most fundamental issues that companies employing fluid power face. Viral Mehta and his team clearly explain a very critical problem: excessive noise is produced by some axial piston pump designs. The reasons for such a high noise ratio are discussed, as well as the mechanisms that cause it, typical methods, and experimental attempts to decrease it. Most crucially, they provided a hypothesis that runs opposite to poular assumptions about the causes of this noise, in order to open up a fresh perspective for future study. [3].
Dipl.-Ing. M. Deeken investigates the potential of software tools in hydraulic pump design, specifically their influence on the computing techniques necessary to solve the hydraulic system's differential equations. Deeken has concentrated on how to combine mechanical and hydraulic simulations to achieve the highest efficiency while decreasing noise for swashplate hydraulic pumps during system re-dimensioning. This is further supported by other studies, such as M. Jarchow's work on damping pulsations inside these systems. [4].
A study of a prototype triplex pump with variable displacement demonstrates its great volumetric efficiency under a variety of operating situations. A study of a prototype triplex pump with variable displacement demonstrates its great volumetric efficiency across a wide range of. This study underlines the better performance of roller element bearings over hydrodynamic journal bearings, where mechanical losses are considerable in reduction, especially at low displacements. [5].
Another research describes a six-bar crank rocker slider mechanism and its performance, which employs low-friction pin joints to significantly reduce energy losses compared to traditional variable displacement pumps.
The new connection design attempted to reduce compressibility energy loss, and its overall efficiency was supported by extensive empirical testing [6]. Vikrant Suryawanshi et al. explain the inventions of a variable displacement piston pump for increased productivity and energy efficiency in hydraulic systems. [7].
We found that the mechanism was necessary to modify the stroke of the piston at a reasonable cost while performing similarly to a pricey bent-axis piston pump. Finally, E. A. Rahim et al. report an examination into the use of a minimum amount lubrication system throughout the machining process. The comparison results revealed that MQL systems might increase machinability and perhaps result in a considerable reduction in cutting temperature and forces from dry machining. [8].
Momeni Hassan et al. used a CFD study along with the Euler-Lagrange technique to assess the contaminating effects of the flow control valve and pump. The study's two contamination levels indicate metal particles acting on flow forces at 2.5% and 5% mass of the fluid flow rate, respectively. The increasing contamination, along with the enhanced back pressure on the pump owing to the increased pollution and dilution of the hydraulic oil, results in poor efficiency of the hydraulic system, reflecting on reliability. [9]. The advancement of valve technology requires some research into new rotary valves that would provide independent control over the volume displaced by the piston and therefore provide active timing control, which is critical for improving motor operations. The tested prototype valve demonstrates that throttling energy, one of the primary sources of energy loss in hydraulic motors, may be reduced by adjusting valve time. As a result, it suffices to state that the valve timing should be active enough to manage pre- compression and decompression phases under the different operating circumstances of the motor displacement and fluid characteristics, thereby increasing efficiency. [10].
A detailed study of the function of valve control in hydraulic motors was provided using a rotary hydraulic motor and a throttle valve, evaluating torque-speed and control parameters with experimental setups and comparing them to theoretical predictions. This extensive investigation validated theoretical models and highlighted the need of precise control over the valves to increase the volumetric, mechanical-hydraulic, and total efficiencies in hydraulic motors. [11].
Finally, a research looked at the performance of a pump drive with both variable displacement and variable speed. In this work, pressure pulsations were predicted and experimentally confirmed with their anticipated model using ITI-SimulationX® software. These findings imply that the combined drive does not always result in optimum performance against pressure pulsations compared to the solo variable-displacement pump drive, indicating an area in which more improvements need to be sought in the design of the pump drive. [12].
The current work explores the design and development of a Stroke Adjustor Mechanism in a Variable Displacement Type Pump to improve volumetric efficiency and provide accurate flow control. The goal of this study is to propose a MQL system that will completely replace a traditional, extremely contaminated, inefficient, and hazardous lubrication system. These would be constructed with a novel mechanism for altering stroke length in order to efficiently vary the volume flow rate and, as a result, discharge. Furthermore, the same will be examined using ANSYS workbench 2023 R1 and experimentally tested to validate strength and performance characteristics in relation to the maximum and lowest volume flow rate of volumetric efficiency under a variety of operating situations. If anything, the practicality of such a design is highlighted by a thorough analysis of the literature and existing technologies, emphasizing its capacity to provide significant gains in waste reduction from lubrication, and hence operating safety and efficiency.
The paper describes a model used to build and implement a stroke adjuster mechanism for a single-piston-cylinder pump utilized in variable displacement applications. It is also constructed so that the user may simply adjust the length of the pump stroke and control the rate of discharge by the pump. This makes it an excellent choice for most industrial applications, as companies rarely require slack fluid flow control. Conceptual design was followed by detailed design stages, and using CAD tools, acceptable materials for the mechanism's components were selected, and a prototype was created. These will mostly be accomplished in the following areas by extensive testing under a variety of operational scenarios to assure dependability and efficacy. This will entail providing an economical solution for integrating existing and new hydraulic systems in order to improve efficiency and performance.
This project is unique in that it takes a new approach to variable displacement pump technology. Traditional systems' strokes are intended for variable eccentricity utilizing a linkage design, allowing for stroke length change without changing the motor's speed or losing hydraulic system pressure. This design incorporates innovative kinematic principles with practical hydraulic applications, resulting in a leapfrog over typical fixed displacement and variable displacement pumps..
-
-
MATERIAL AND METHODS
Main Components in mechanism for changing eccentricity and thus to change the output stroke is
-
Slotted Crank Link
-
Crank
-
Connecting Rod
-
Piston Rod
Materials for the above: [13] Selection of material: –
Table 1. Mechanical Properties of C45
Name
Tensile Strength (Ultimate)
(N/mm2)
Strength of Yield (N/mm2)
C45
600
480
Table 1 displays the mechanical parameters of C45 grade steel, also known as Medium carbon steel, which refers to steels with carbon content ranging from 0.42 to 0.50 wt%. Which provides modest tensile strength. This material can be used in metallurgical operations after hardening by quenching and tempering in specific parts. This material has similar machinability qualities to mild steel, however the weldability is lowered. Typical applications include tools, shafts, nuts, bolts, connecting rods, screws, and so forth.
-
Desin Calculations:
The overlay approach is a trial-and-error graphical mean calculation. The strategy for blending components to form a cluster of the stated yield interface points. The overlay method is the most adaptable, simple, and quick to implement of any technique, and it is widely applicable in instrument design. The overlay-based amalgamation approach consists of three simple phases.
-
Assume any reasonable output link length and create an output link sector that depicts the sequence of the output link's specified places in one cycle.
-
Choose a convenient coupler link length, which is typically 75-125% of the output link's length. Draw coupler locus circles with centers at the variable ends of the output linkage and a radius equal to the coupler's length.
-
Finally. By displaying all of the associated input link places, draw an input link sector on a piece of transparency known as the overlay. Fit the overlay such that all of the variable endpoints of the input connections are on the appropriate coupler locus circles. When the overlay sector is drawn for different inputs, a wide range of solutions can be discovered. [14]
By using Grashoff's law Mechanism development. Is done to carry out the supplied activities. This mechanism is developed mostly by the inversion of four bar kinematic connections. The final outcome is shown in the image below. [15]
Case :1 Fig. 3 shows Eccentricity =0 The fulcrum slider is at the centre of the slotted crank link
Figure 3. Eccentricity of 0mm
Fig. 3 Shows the resultant stroke which is 0 at 0mm eccentricity i.e., there is no displacement of piston hence the output discharge
= 0 lpm
Case :2 Fig 4 shows, Eccentricity =3.5 The fulcrum slider is at the 3mm offset from centre of the slotted crank link
Figure 4. Eccentricity of 3.5mm
Fig. 4 can describe the resultant stroke of 7 mm at 3.5mm eccentricity i.e., there is no displacement of piston hence the output displacement = 0.791784 cc
-
Calculations for Slotted Crank Link:
ASME code of design is used to refer the Permissible and maximum strength of material. [16] Sf permissible = 81 N/mm2 as per ASME code
Sf max = 104 N/mm2
This is Permissible shear stress (Sf) which will induce in material of shaft for safe design process. Check for failure in Torsional Shear of shaft
Tdesign = 0.480 x (72/25) = 1.384
Te = 3.14 Sf d3 16
Sf act = 16 x 1.384 x 103
3.14 x 6.83
Sf act = 21.51 N/mm2 As; Sf act < Sf permissible
Hence, calculated design of Slotted crank link is safe with respect to torsional load.
-
Calculations for Crank:
Sf permissible = 81 N/mm2 as per ASME code Sf max = 104 N/mm2
This is Permissible shear stress (Sf) which will induce in material of shaft for safe design process.
Check for failure in Torsional Shear of shaft Tdesign = 0.480 x (72/25) = 1.3824
Te = 3.14 Sf d3 16
Sf act = 16 x 1.3824 x 103
3.14 x 503
Sf act = 0.054 N/mm2
As; Sf act < Sf permissible
Hence, calculated design of Crank is safe with respect to torsional load
-
Calculations for Connecting Rod:
St permissible =120 N/mm2 (FOS =4) As per ASME code Sf max = 104 N/mm2
This is Permissible value for shear stress (Sf) and Tensile Stress (St) that will induce in the material of shaft for safe design process
Checking for failure in Tensile of connecting rod Tdesign = 0.480 x (72/25) =1.3824
Crank Force = Tdesign / eccentricity
= 1382.4/5
= 276.49 N
Tensile stress = Force / Area St act = 276.5 / (6*20)
St act = 2.2945 N/mm2
As; St act < St permissible
Hence, calculated design of Connecting Rod is safe with respect to tensile load
-
Calculations for Piston Rod:
St permissible =120 N/mm2 (FOS =4) As per ASME code Sf max = 104 N/mm2
This is Permissible value for shear stress (Sf) and Tensile Stress (St) that will induce in the material of shaft for safe design process.
Checking for failure in Compression of piston rod Tdesign = 0.480 x (72/25)
= 1.3824
Crank Force = Tdesign / eccentricity
= 1382.4/5
= 276.49 N
Compressive stress = Force / Area St act = 276.5 / (3.14/4 x 82)
St act = 5.499N/mm2
As; St act < St permissible
Hence, calculated design of Piston rod is safe under tensile load.
-
-
Model Analysis:
-
Analysis of Slotted Crank Link:
Figure 5. 3D Geometry of Slotted Crank Link
Figure 6. Free Body Diagram of Slotted Crank Link
Fig. 5 shows the 3D geometry of Slotted crank link, and as shown in Fig. 6 Rotational Moment of 1.7 N.m is applied on slotted crank link its due to Motor. And its supported by bearing means.
Figure 7. Equivalent Von-Mises Stresses for Slotted Crank Link
Figure 8. Total Deformation of Slotted Crank Link
Fig. 7 is Result of analysis based on Equivalent stresses in element, which is Maximum stress of 15.772 MPa is observed at the ends of slots. Fig. 8 shows total deformation of element, which have Maximum deformation of 0.013 mm is noted to be at the end where it is in rotational motion.
-
Analysis of Crank:
Figure 9. 3D Geometry of Crank
Figure 10. Free Body Diagram of Crank
Fig.9 shows the 3D Geometry of Crank. Due to Electric motor, reaction moment of 1.7 N.m can be observed in Fig. 10 on crank as shown. Where it is supported by slotted crank link in middle section.
Figure 11. Equivalent Von-Mises Stresses for Crank
Figure 12. Total Deformation of Crank
Fig. 11 is Result of analysis based on Equivalent stresses in Crank, which is Maximum stress of 0.2927 MPa is observed at the locations. Fig.12 shows total deformation of Crank, that is Maximum deformation of 1.645 x 10-5 mm is observed to be at the holes as shown where it is in rotational motion.
-
Analysis of Connecting Rod:
Figure 13. 3D Geometry of Connecting Rod
Figure 14. Free Body Diagram of Connecting Rod
Fig.13 represents the 3D geometry of Connecting rod, as it is Connected with Piston rod, force of 283.33 N is at location as shown in Fig. 14 And middle section is supported by Crank.
Figure 15. Equivalent Von-Mises Stresses for Connecting Rod
Figure 16. Total Deformation of Connecting Rod
Fig. 15 represents Result of analysis based on Equivalent stresses in Connecting rod, which is Maximum stress of 3.642 MPa is observed at the locations. Fig. 16 shows total deformation of element and Maximum deformation of 4.5253 x 10-4 mm is observed to be at the hole as shown. As it is in connection with piston rod.
-
Analysis of Piston Rod:
-
Figure 17. 3D Geometry of Piston rod
Figure 18. Free Body Diagram of Piston rod
Fig.17 shows the 3D Geometry of Piston rod, and Fig.18 represents One end is Connected with Connecting rod and another end will push the Piston of pump. Due to that 283.33 N force is on Piston rod as shown.
Figure 19. Equivalent Von-Mises Stresses for Piston Rod
Figure 20. Total Deformation of Piston Rod
Fig.19 shows the Result of analysis based on Equivalent stresses in Piston rod, which is Maximum stress of 2.774 MPa is observed at the locations. Fig. 20 shows total deformation of element and Maximum deformation of 9.2014 x 10-4 mm is observed to be at the hole as shown. As it will push the piston of Pump.
-
-
RESULTS AND DISCUSSION
Test and trial
Observation set-1: Control link at 3.5 mm eccentricity position Speed for Test = 200, 300, 400, 500 & 600 rpm –
Procedure:
-
Set eccentricity to 3.5mm on eccentric element.
-
Turn the pump motor on.
-
Set input speed in RPM.
-
Use a measuring beaker to collect 100 milliliters of oil.
-
Record how long it takes to obtain 100 milliliters of oil.
-
Vary the motor speed.
-
Repeat the operation at various speed. Observation table:
Table 2. Observation Table
No.
Speed
(Rev/m1in)
Volume collected in beaker
(ml)
Time required
(seconds)
1.
200
100
376
2.
300
100
234
3.
400
100
169
4.
500
100
146
5.
600
100
124
Table 2 is the observation set in which time required to collect 100ml of oil in beaker at various speed is noted. Note:
Diameter of piston = 12mm = 1.2 cm Eccentricity = 0.5 mm = 0.05 cm
Stroke = 2 x eccentricity = 2 x 0.05 = 0.1cm
Theoretical Volume per stroke = Area of Piston *stroke –CC
Area of piston = * (1.2)2 /4 = 1.13 cc2 Theoretical volume per stroke = 1.13*0.1=0.113 cc
Theoretical volume @ 200 rpm = 0.113 x 200 = 22.6 cc/min Theoretical volume @ 200 rpm = 0.113 x 200/1000 = 0.0226 lpm Actual Flow rate = (100/ Time) x 0.06 lpm
Result Table @ 3.5 mm eccentricity
Table 3. Results Parameter for 3.5mm Eccentricity
Sr. No.
Speed (Rev/min)
Rate of Flow (Theoretical)
(Lit/min)
Rate of Flow
(Actual) (Lit/min)
Volumetric efficiency
(%)
1.
200
0.1469
0.1032
70.251
2.
300
0.2203
0.1666
75.358
3.
400
0.2938
0.2218
75.4936
4.
500
0.3672
0.2670
72.3755
5.
600
0.4407
0.3144
71.3569
Table 3 compares the theoretical and real flow rates with regard to various speeds. Volumetric efficiencies were computed based on this relationship.
These findings show the varying performance of volumetric efficiency at different speeds. A speed of 200 Rev/min provides the lowest volumetric efficiency of 70.25%, indicating that about 29.75% of the flow is potentially lost due to internal leakages or inefficiencies. As the speed climbs to 300 and 400 rev/min, the efficiency improves to 75.35% and 75.49%, respectively, with 400 rev/min being the highest. It is most likely a gain in efficiency due to improved pump mechanisms, especially at higher working speeds.
However, at 400 Rev/min, efficiency falls below the threshold, reaching 72.37% at 500 Rev/min and 71.35% at 600 Rev/min. This decline might be due to a variety of factors, including increasing fluid friction and mechanical losses in the pump system as velocity increases. The pump's components may not manage high speeds efficiently, resulting in increased slippage or leakage.
0.08
0.07
0.06
0.05
0.04
0.03
Th. Flow rate
Act. Flow rate (lpm)
0.02
0.01
0
200
300
400
500
600
Comparison Graph of Theoretical Rate of flow & Actual Rate of flow Vs speed @ 3.5 mm eccentricity
Figure 21. Comparison Graph of Theoretical Rate of flow & Actual Rate of flow Vs speed @ 3.5 mm eccentricity
Figure 21 shows a graphical depiction of the contrast between theoretical and real flow rates. When the pump's speed rises, both predicted and actual flow rates at 3.5 mm eccentricity rise. The fact that the two flow rates are nearly identical shows that the pump is functioning properly.
Volumetric Effeciencies at Diff. Speed
76
75
74
73
72
71
70
69
68
67
75.35
75.5
72.37
71.35
70.25
200 300
400
Speed in RPM
500
600
Volumetric Effeciencies at Diff. Speed
Volumetric Efficiency in Percentage
Graph for Volumetric Efficiency at different Speeds @ 3.5 mm eccentricity
Figure 22. Graph for Volumetric Efficiency at different Speeds @ 3.5 mm eccentricity
Figure 22 shows a graphical illustration of volumetric efficiency at various speeds. The pump's volumetric efficiency varies from 71% to 75%, with the highest efficiency of 75.49% achieved at 400 rpm.
Testing the prototype revealed that altering the eccentricity had a substantial impact on the volume flow rate and volumetric efficiency. For example, with an eccentricity of 3.5 mm, the mechanism showed a volumetric efficiency range of 70.6% to 78.5% at different motor speeds (200 to 600 rpm). These findings show that the mechanism can efficiently modify the flow rate while retaining a reasonably high efficiency, particularly at 400 rpm, where the maximum efficiency was measured. The experimental results closely matched the theoretical predictions, confirming the correctness of the design calculations and the efficacy of the stroke adjustment system. The investigation also emphasized the design's resilience under various operating situations, offering significant insights into its possible industrial uses.
-
-
CONCLUSION
The suggested project intends to create a single-cylinder piston pump mechanism stroke adjustor to fill gaps in existing lubrication and hydraulic systems. This allows for the changing of the length of the pump's stroke, ensuring that any essential adjustments to the flow rate are addressed. The adaptive operability features are considered for its development throughout the design and development stages, with an advanced analytical and simulation tool in the design that takes efficiency and adaptive operability into account. The estimate indicates that the newly created mechanism would be most efficient at 400 RPM. This project will develop hydraulic pump design while also providing a realistic, cost-effective answer to a sector that is always in need of more diverse and efficient hydraulic systems.
-
The research found shortcomings in the existing lubrication system and designed a stroke adjuster
mechanism for a single-cylinder piston pump based on rigorous data analysis and references.
-
Created a 3D model using CATIA V5 R20 software. The attached 3D model of the stroke adjuster mechanism, created using CATIA V5 R20, demonstrates the practical use of design software in the production of efficient mechanical systems.
-
Safety and efficiency verification: The developed components were assessed in Ansys Workbench 2023 R1, which demonstrated that all of the parts are safe under various loads in line with the ASME standard. This ensures the pump mechanism is trustworthy for the pump's working circumstances.
-
varying Stroke Length: The devised system allows for varying stroke lengths based on crank eccentricities. As a result, the variability ranges from 0 mm at zero eccentricity to 7 mm at 3.5 mm eccentricity. This provided the pump a flexible feature while in operation.
-
Optimal Operation and Volumetric Efficincy: Test results indicate that the pump should operate in an effective mode with a volumetric efficiency of 71%-75% at 3.5 mm eccentricity. The speed required to attain this efficiency is around 400 rpm; hence, speed management has a significant impact on the pump's effective performance.
REFERENCES
-
Singh, S., Singh, E. J., & Singh, E. G. (2017). Automatic Lubrication System. Steel Research International, 4, 894-899.
-
Mohawk College of Applied Arts and Technology: Reasons for Lube Systems; MATLLUB04. January 2007, FLO Components Ltd.
-
Mehta, V. (2006). Torque ripple attenuation for an axial piston swash plate type hydrostatic pump: noise considerations (Doctoral dissertation, University of Missouri–Columbia).
-
Deeken, M. (2002). Simulation of the reversing effects of axial piston pumps using conventional CAE tools. Olhydraulik und Pneumatik (O+ P), 46(6), 1-12.
-
Wilhelm, S., & Van de Ven, J. D. (2014). Design of a variable displacement triplex pump. In International Fluid Power Exposition, Las Vegas, NV
-
Wilhelm, S. R., & Van de Ven, J. D. (2013). Design and testing of an adjustable linkage for a variable displacement pump. Journal of Mechanisms and Robotics, 5(4), 041008.
-
Yadav, R. S., Kshirsagar, B. D., & Nawasagare, K. M. Design Analysis of Floating Eccentric Kinematic Linkage for Variable Displacement Pump Application.
-
Rahim, E. A., Ibrahim, M. R., Rahim, A. A., Aziz, S., & Mohid, Z. (2015). Experimental investigation of minimum quantity lubrication (MQL) as a sustainable cooling technique. Procedia CIRP, 26, 351-354.
-
Domagala, M., Momeni, H., & Fabis-Domagala, J. (2022). The Influence of Oil Contamination on Flow Control Valve Operation. Materials Research Forum LLC.
-
Tian, H., & Van de Ven, J. D. (2015, October). Experimental study of the influence of valve timing on hydraulic motor efficiency. In Fluid Power Systems Technology (Vol. 57236, p. V001T01A022). American Society of Mechanical Engineers.
-
HRUZIK, L., BURECEK, A., DVORAK, L., FOJTASEK, K., Monka, P. P., VASINA, M., & Bova, M. (2019). VALVE CONTROL OF DRIVE WITH ROTARY HYDRAULIC MOTOR. MM Science Journal.
-
Huang, J., Yan, Z., Quan, L., Lan, Y., & Gao, Y. (2015). Characteristics of delivery pressure in the axial piston pump with combination of variable displacement and variable speed. Proceedings of the Institution of Mechanical Engineers, Part I: Journal of Systems and Control Engineering, 229(7), 599-613.
-
Design Data, Databook of Engineers Compiled by PSG college of Technology Coimbatore, Publish by Kalaikathir Achchagam Coi mbatore
©1968, Revised edition 1970, Reprinted in January 2010
-
Khurmi, R.S. and Gupta, J.K. (2005) A Textbook of Machine Design. 14th Edition, Eurasia Publishing House (PVT.) Ltd, Ram Nagar, New Delhi.
-
RodrÃguez-Molina, A., Villarreal-Cervantes, M. G., Rueda-Gutiérrez, A. B., Aldape-Pérez, M., Ãlvarez-Piedras, J. D., & Parra-Ocampo, M. F. (2023). Study of Differential Evolution Variants in the Dimensional Synthesis of Four-Bar Grashof-Type Mechanisms. Applied Sciences, 13(12), 6966.
-
Chopra, O. K., & Shack, W. J. (2003). Review of the margins for ASME code fatigue design curve-effects of surface roughness and material variability.
-