
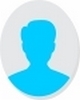
- Open Access
- Authors : Adebola Oluwafunmilayo, Ibikunle, Samuel Talabi
- Paper ID : IJERTV13IS050293
- Volume & Issue : Volume 13, Issue 05 (May 2024)
- Published (First Online): 28-06-2024
- ISSN (Online) : 2278-0181
- Publisher Name : IJERT
- License:
This work is licensed under a Creative Commons Attribution 4.0 International License
Tesla’s Supply Chain Management Model: A Lesson for Smart Manufacturing
Adebola Oluwafunmilayo, IBIKUNLE
C.T. Bauer College of Business University of Houston
Samuel TALABI
Department of Mechanical Engineering University of Texas at Tyler
Abstract- This paper explores Tesla's Supply Chain Management, which serves as a strategic cornerstone driving the company's growth and resilience. By integrating advanced technologies, strategic supplier relationships, adopting a vertically integrated manufacturing model, and emphasizing sustainability, Tesla has developed an efficient, robust, and environmentally aligned supply chain. Vertical integration allows Tesla to control production processes, reduce dependency on external suppliers, and innovate rapidly. The use of advanced technologies such as AI and blockchain optimize operations enhances transparency and predicts market needs more accurately. Strategic supplier relationships, like the partnership with Panasonic for battery production, ensure flexibility and innovation. Tesla's commitment to sustainability is evident in its use of clean energy and ethical sourcing of raw materials, minimizing environmental impact and promoting responsible practices among its suppliers. Tesla's SCM model offers valuable lessons for modern manufacturing, highlighting the importance of agility, technology integration, and sustainable practices. This study comprehensively analyzes Tesla's Supply Chain Management, presenting a compelling blueprint for smart manufacturing in the 21st century.
-
INTRODUCTION
In the rapidly evolving landscape of the electric car industry, Tesla Inc. has emerged as a beacon of innovation and sustainability. Founded in 2003, Tesla's mission to accelerate the world's transition to sustainable energy has driven its ascent to the forefront of electric vehicle (EV) production and clean energy solutions. Beyond its groundbreaking products, such as the Model S, Model 3, and its solar energy offerings, Tesla has also distinguished itself through its cutting-edge supply chain management (SCM) practices (Musk, 2013).
The company's approach to SCM is not merely a support function but a strategic cornerstone that has enabled Tesla to achieve remarkable growth and resilience in a highly competitive market. By integrating advanced technologies, strategic supplier relationships, adopting a vertically integrated manufacturing model, and emphasizing sustainability, Tesla has crafted a supply chain that is not only efficient and robust but also aligned with its overarching mission of environmental stewardship (Hawkins et al., 2017).
In an era where disruptions and uncertainties in global supply chains have become commonplace, Tesla's innovative SCM strategies offer valuable insights and lessons for manufacturers worldwide. The company's success in managing supply chain complexities underscores the importance of agility, technology
integration, and sustainable practices in modern manufacturing (Boudette, 2020).
This article delves into the intricacies of Tesla's supply chain management model, exploring the key strategies that underpin its effectiveness. We will examine how Tesla's unique approach to vertical integration, technological adoption, supplier relationship management, and sustainability initiatives contribute to its operational excellence. Additionally, we will discuss the broader implications and lessons that other manufacturers can draw from Tesla's experience to enhance their own supply chain resilience and efficiency in an increasingly dynamic and demanding market landscape (Shahan, 2019).
By understanding and applying these lessons, manufacturers will not only improve their supply chain operations but also contribute to a more sustainable and resilient industrial ecosystem. Tesla's journey offers a compelling blueprint for smart manufacturing, demonstrating that with the right strategies and innovations, it is possible to navigate and thrive amidst the complexities of the global supply chain (Matousek, 2021).
-
OVERVIEW OF TESLAS SUPPLY CHAIN
MANAGEMENT
Tesla Inc. has redefined the electric car industry not only through its cutting-edge electric vehicles but also through its innovative supply chain management (SCM) practices. Teslas SCM is characterized by a high degree of vertical integration, advanced technology adoption, strategic supplier relationships and a strong commitment to sustainability. These elements collectively contribute to its operational efficiency, cost-effectiveness, and resilience in a volatile global market.
-
Vertical Integration
Teslas approach to vertical integration sets it apart from traditional electric car manufacturers. Unlike most automakers who rely heavily on third-party suppliers for key components, Tesla manufactures a significant portion of its parts in-house. This strategy enables Tesla to maintain greater control over its production processes, reduce dependency on external suppliers, and enhance its ability to innovate (Liu, 2020). For example, Tesla produces its batteries through its Gigafactories, which not only lowers costs but also ensures a steady supply of this critical component (Wakabayashi & Ramsey, 2021).
-
Advanced Technology Adoption
Technology is at the heart of Teslas SCM. The company leverages advanced analytics, artificial intelligence (AI), and machine learning to optimize its supply chain operations. For instance, Teslas use of AI in demand forecasting allows it to predict market needs more accurately and adjust production schedules accordingly (Hollinger, 2021). Additionally, the implementation of blockchain technology in its supply chain enhances transparency and traceability, reducing the risk of fraud and ensuring the authenticity of components (Alladi et al., 2019).
-
Strategic Supplier Relationship Management
Despite its high level of vertical integration, Tesla maintains strategic relationships with key suppliers to ensure flexibility and innovation. The company collaborates closely with its suppliers to drive quality improvements and technological advancements. This collaborative approach is exemplified in Teslas partnership with Panasonic for battery production, which has been crucial in enhancing battery performance and reducing costs (Stringer, 2020).
-
Sustainability Initiatives
Teslas commitment to sustainability extends to its supply chain management practices. The company prioritizes the use of clean energy in its manufacturing processes and seeks to minimize its environmental footprint. For example, Teslas Gigafactories are designed to be powered by clean energy sources, reducing the carbon footprint associated with battery production (Irle, 2020). Moreover, Teslas focus on ethical sourcing of raw materials, such as cobalt and lithium, underscores its dedication to responsible environmental and social practices (Childs, 2021).
-
-
CHALLENGES AND ADAPTATIONS
Despite its successes, Teslas SCM is not without challenges. The company has faced production bottlenecks, supply shortages, and geopolitical risks. However, Teslas agile and adaptive approach to supply chain management has enabled it to navigate these challenges effectively. For instance, during the global semiconductor shortage, Tesla swiftly adapted by rewriting its software to support alternative chips, showcasing its abiliy to respond to supply chain disruptions (Higgins, 2021).
-
LESSONS FOR SMART MANUFACTURING IN TESLAS SUPPLY CHAIN
MANAGEMENT
The transformation of Tesla from a niche electric vehicle (EV) manufacturer to a global leader in sustainable energy solutions is not just a story of technological innovation but also a testament to its pioneering supply chain management (SCM) practices. Tesla's SCM model provides critical insights into how modern manufacturing can leverage advanced technologies, strategic integrations, and sustainable practices to achieve operational excellence. This essay explores the key lessons from Tesla's SCM that can be applied to smart manufacturing.
-
Vertical Integration: Control and Efficiency
One of the most striking aspects of Tesla's supply chain strategy is its emphasis on vertical integration. Unlike many traditional automakers who rely heavily on a network of third-party suppliers, Tesla has taken significant steps to control various stages of its production process. This strategy includes everything from battery production to vehicle assembly. Vertical integration offers several advantages. Firstly, it allows for greater control of product quality and consistency of critical components. For example, Tesla's acquisition of Maxwell Technologies and Hibar Systems aimed to enhance its battery production capabilities (Anderson, 2020). By bringing these processes in-house, Tesla can ensure the quality of its batteries, which are crucial to the performance and safety of its EVs.
Moreover, vertical integration helps Tesla to innovate rapidly. The close coordination between different production stages allows for quicker implementation of new technologies and design changes. This agility is particularly beneficial in the fast- evolving EV market, where technological advancements can quickly render existing models obsolete (Lambert, 2019).
-
Technological Adoption: Data-driven Decision Making Tesla's supply chain is also notable for its extensive use of advanced technologies. The company leverages big data analytics, artificial intelligence (AI), and the Internet of Things (IoT) to optimize its supply chain operations. For instance, Tesla's factories are equipped with a multitude of sensors and IoT devices that continuously collect data on various aspects of the production process. This data is then analyzed using AI algorithms to identify inefficiencies and predict potential issues before they become critical (Vynck, 2021).
Such a data-driven approach enables Tesla to maintain high levels of efficiency and productivity. Predictive maintenance, for example, helps reduce downtime by ensuring that machinery and equipment are serviced before failures occur. Additionally, real-time data analytics allows Tesla to make informed business decisions and respond swiftly to the market, minimizing delays and reducing costs (Chokshi, 2020).
-
Strategic Supplier Relationship Management: Collaboration and Reliability
Strategic supplier relationship management is another cornerstone of Tesla's SCM. The company has cultivated strong partnerships with key suppliers to ensure a reliable supply of essential materials and components. This collaborative approach is particularly evident in Tesla's relationship with Panasonic, its long-term partner in battery production (Kane, 2021).
Tesla and Panasonic have jointly invested in the Gigafactory in Nevada, which produces lithium-ion batteries for Tesla's vehicles. This partnership has not only secured a steady supply of batteries but also facilitated joint innovation efforts to improve battery technology and reduce costs. Such strategic collaborations enable Tesla to mitigate supply risks and enhance its competitive advantage (Lombrana, 2019).
-
Sustainability Initiatives: Aligning Operations with Mission Sustainability is at the heart of Tesla's mission, and this commitment extends to its supply chain practices. Tesla strives to minimize its environmental impact through various initiatives, such as sourcing materials responsibly, reducing waste, and using clean energy in its manufacturing processes. For instance, Tesla has made significant efforts to source cobalt, a critical component of lithium-ion batteries, from suppliers who adhere to ethical and environmentally responsible practices. The company conducts rigorous audits to ensure compliance with its standards, thereby promoting sustainable mining practices (Tesla, 2020).
Furthermore, Tesla's Gigafactories are designed to be highly energy-efficient and are powered by clean energy sources. The Gigafactory in Nevada, for example, aims to operate entirely on clean energy, significantly reducing the carbon footprint of Tesla's battery production (Boudette, 2021).
-
-
IMPLICATIONS FOR SMART MANUFACTURING
Tesla's supply chain management offers several valuable lessons for smart manufacturing:
-
Embrace Vertical Integration: Controlling more stages of the production process can lead to improved quality, greater innovation, and enhanced agility. Manufacturers should consider integrating critical processes to gain more control and efficiency.
-
Leverage Advanced Technologies: The use of big data, AI, and IoT can transform supply chain operations, enabling predictive maintenance, real-time analytics, and data-driven decision-making. Investing in these technologies is crucial for maintaining competitiveness in the modern manufacturing landscape.
-
Foster Strategic Partnerships: Building strong, collaborative relationships with suppliers can ensure reliability and foster joint innovation. Manufacturers should seek partnerships that align with their strategic goals and promote mutual growth.
-
Commit to Sustainability: Aligning supply chain practices with sustainability goals not only helps protect the environment but also enhances brand reputation and meets the growing consumer demand for ethical products. Manufacturers should prioritize sustainable practices in their supply chain management.
REFERENCES
-
Alladi, T., Chamola, V., Parizi, R. M., & Choo, K.-K. R. (2019). Blockchain applications for industry 4.0 and industrial IoT: A review. Journal of Network and Computer Applications, 144, 102965. https://doi.org/10.1016/j.jnca.2019.102965
-
Anderson, M. (2020). Tesla acquires Maxwell Technologies for battery innovations. TechCrunch. Retrieved from https://techcrunch.com
-
Boudette, N. E. (2021). How Teslas Gigafactory is redefining manufacturing. The New York Times. Retrieved from https://www.nytimes.com
-
Childs, M. (2021). Ethical sourcing in the electric vehicle industry: Addressing challenges in the supply chain. Sustainable Materials and Technologies, 28, e00256. https://doi.org/10.1016/j.susmat.2021.e00256
-
Chokshi, N. (2020). Teslas use of artificial intelligence in manufacturing.
The Wall Street Journal. Retrieved from https://www.wsj.com
-
Higgins, T. (2021, August 6). Teslas master of coin reflects on the global chip shortage. The Wall Street Journal. Retrieved from https://www.wsj.com/
-
Hollinger, P. (2021, April 14). Teslas AI strategy to dominate the electric
car market. Financial Times. Retrieved from https://www.ft.com/
-
Irle, R. (2020). Tesla Gigafactory: Building the future of manufacturing. Clean Energy World. Retrieved from https://www.cleanenergyworld.com/
-
Kane, M. (2021). Tesla and Panasonics partnership: A decade of attery
innovations. InsideEVs. Retrieved from https://insideevs.com
-
Lambert, F. (2019). Teslas approach to vertical integration and its impact
on the EV market. Electrek. Retrieved from https://electrek.co
-
Liu, W. (2020). Vertical integration in the electric car industry: A case study of Tesla. International Journal of Production Research, 58(14), 4321-4336. https://doi.org/10.1080/00207543.2020.1720887
-
Lombrana, L. M. (2019). The strategic partnership between Tesla and Panasonic. Bloomberg. Retrieved from https://www.bloomberg.com
-
Stringer, D. (2020, December 8). Tesla and Panasonics evolving partnership in battery technology. Bloomberg. Retrieved from https://www.bloomberg.com/
-
Tesla. (2020). Teslas 2020 impact report. Retrieved from
https://www.tesla.com
-
Vynck, G. (2021). Inside Teslas data-driven supply chain. The Washington Post. Retrieved from https://www.washingtonpost.com
-
Tesla maintains greater control over its production processes through vertical integration (Liu, 2020).
-
The use of AI in demand forecasting allows Tesla to predict market needs more accurately (Hollinger, 2021).
-
Teslas collaboration with Panasonic has been crucial in enhancing
battery performance and reducing costs (Stringer, 2020).
-
Teslas Gigafactories are designed to be powered by clean energy sources, reducing the carbon footprint associated with battery production (Irle, 2020).
-
Teslas agile approach to supply chain management enabled it to adapt
swiftly during the global semiconductor shortage (Higgins, 2021).
-
-
CONCLUSION
Tesla's supply chain management is a model of efficiency, innovation, relationship, and sustainability. By embracing vertical integration, leveraging advanced technologies, fostering strong supplier relationships, and committing to sustainable practices, Tesla has built a resilient and agile supply chain that supports its mission of accelerating the world's transition to sustainable energy. These lessons offer a roadmap for other manufacturers seeking to enhance their operations and adapt to the demands of smart manufacturing in the 21st century.
IJERTV13IS050293
(This work is licensed under a Creative Commons Attribution 4.0 International License.)